摘要:运用统计学规律对滑动导轨副在实际运行工况下的磨损特征与精度衰减进行了分析,从而建立了滑动导轨副的精度保持性模型,该模型反映了导轨副的精度保持性能与导轨副工况参数、运行参数、材料属性以及磨损状况的定量关系。利用自主研制的导轨副精度保持性实验台进行了导轨副试样的磨损精度实验,验证了理论模型的有效性。该理论模型既可以预测导轨副的精度保持寿命,也可以指导导轨副的耐磨设计及精度保持性设计。
关键词:滑动导轨副 机床 磨损 精度保持性 数学模型 台架实验
引言
国内生产制造的高精度机床的精度已能达到国际同类水平,但精度保持性与国外仍有较大差距,精度保持性已成为制约我国高精度机床研发的技术瓶颈之一。滑动导轨副是常用的机床进给系统的核心部件,对机床加工精度起着决定性作用。
影响导轨副精度保持性的因素有很多,如导轨自身的几何加工精度、导轨材料的弹性变形和热变形、切削力的不稳定性、机床的振动以及导轨的磨损等。磨损是影响导轨副精度保持性的最重要因素。导轨副表面磨损会逐渐改变导轨副的几何精度,从而影响导轨副在进给过程中的直线性,最终影响机床加工工件的几何精度和表面质量。国内外学者主要研究新材料或者表面涂层对滑动导轨副表面耐磨性的影响[1-6],而导轨表面的磨损机制及磨损计算则少有研究[7-8],目前还未能建立合理的磨损模型对滑动导轨副的实际磨损进行准确预测。此外,国内外学者研究了导轨的几何精度及接触变形等因素对导轨运动精度的影响[9-13],但是关于磨损引起导轨副精度衰减方面的研究还鲜见报道[14-15]。本文将结合机床滑动导轨副的运行工况特征,建立导轨副直线度衰减与表面磨损的映射关系以及导轨副的精度保持性预测模型。
1 滑动导轨副精度保持性的理论建模
1.1 滑动导轨副的工作过程及磨损特点
导轨副的整个运行过程,如图1所示,包括对刀、进给和退刀过程,其中进给属于主要工作过程,在此过程中实现了工件的加工;对刀和退刀属于辅助的运动过程,主要用于实现刀具的准确定位和复位。尽管在整个运行过程中摩擦表面都会发生磨损,但由于进给过程中载荷相对较高且运行时间长,而对刀和退刀过程中载荷相对较低且运行时间短,即2个过程的磨损状况和磨损程度不同。进给过程中的磨损占整个运行过程中磨损的绝大部分,而且进给区域也是精度衰减最严重的区域。因此,为了便于分析,本文考虑导轨面进给区域的磨损对导轨精度的影响,而且认为该区域内进给过程和退刀过程的磨损作用相当。
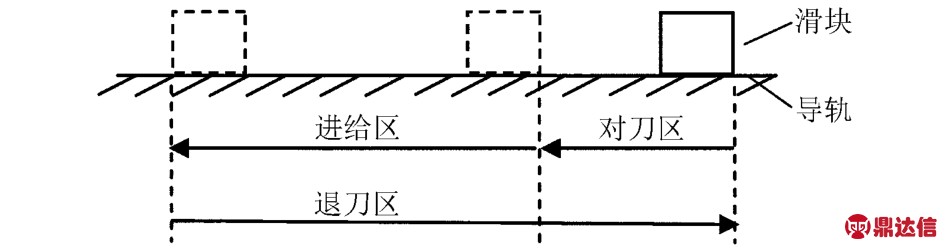
图1 导轨副的运行过程示意图
Fig.1 Schematic diagram of working process of slide guide
导轨副的磨损主要影响导轨表面的直线度和平面度,导轨直线度(尤其是垂直面上的直线度)的改变将对加工工件的尺寸精度和表面质量产生明显影响,而导轨平面度的改变对加工工件的影响相对较小,而且导轨平面度的改变与直线度的改变也具有一定的相关性。所以本文主要研究磨损对导轨垂直面内直线度的影响,如图2a所示。理论上常用的评定直线度的方法有最小区域法,如图2b所示,即用2条宽度最小的平行线来包络导轨表面与水平垂直面的外形截线,该区域内截线的最大偏差,即为直线度。从图2b中可见,导轨直线度的改变与导轨面的磨损深度密切相关,最大的磨损深度决定了导轨的直线度。
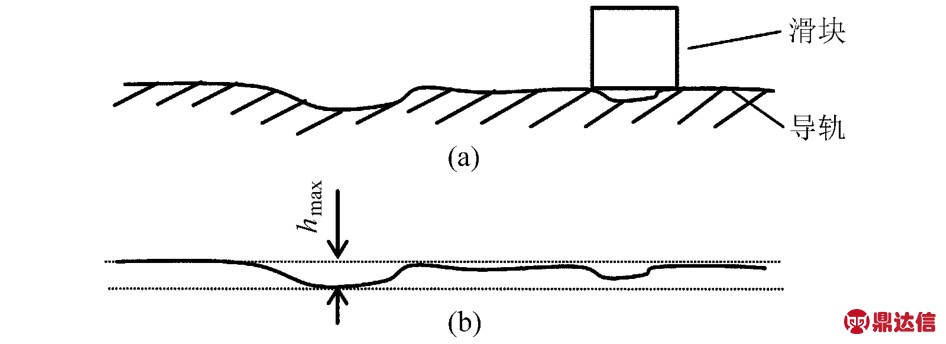
图2 导轨表面的磨损与直线度变化
Fig.2 Wear and straightness attenuation of guide way
(a)导轨表面磨损 (b)导轨表面直线度评定
1.2 导轨精度衰减与导轨磨损的关系模型

图3 滑块的进给与导轨面的磨损
Fig.3 Wear of slide guide in feeding process
以光轴工件的加工为例,由于各个工件的加工长度可能不同,决定了导轨副每次进给的距离可能不同。如图3所示,在导轨的进给区域内,水平线条为滑块的进给距离,尽管各次的进给距离可能会有差异,但是每次进给都会滑过同一区域,因此这一区域将成为严重磨损区,其余区域可看作是轻微磨损区。令加工的光轴工件总量为N,每个工件一次加工完成,即滑块的总进给次数为N。令加工工件的长度范围为lmin~lmax,则滑块的最小和最大进给距离分别为lmin和lmax。结合图3,可以得出导轨工作区域(进给区域)的长度Lf=lmax;严重磨损区长度Ls=lmin。令 j为长度系数,0≤j≤1,j是一个随机变量,用来衡量各个工件的长度差异。因此单个工件的长度L,即滑块的单次进给距离L,可表示为
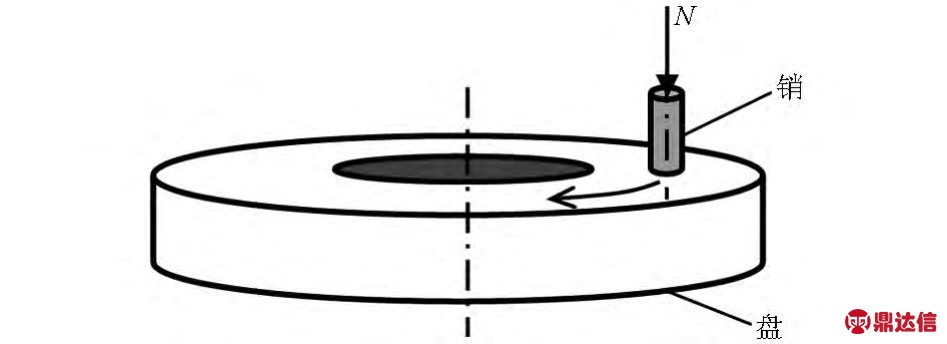
滑块总的进给行程S可以表示为

其中滑块在严重磨损区的总行程可表示为

令导轨表面总的体积磨损量为V,而在严重磨损区的体积磨损量为Vs,由于磨损量与滑动行程呈正比,因此Vs可以表示为

工程应用上可将j看作是一个服从正态分布的随机变量,如图4a所示,即加工工件中长度最大和长度最小的工件数占工件总量的比例最少,而长度适中的工件数占工件总量的比例最大。式(4)中Nj实际上表示的是图4b中矩形斜线阴影部分的面积,而该部分面积与图4b中虚线三角形部分的面积相等,该三角形面积为,因此式(4)中的Nj可以表达为
。式(4)可以变换为
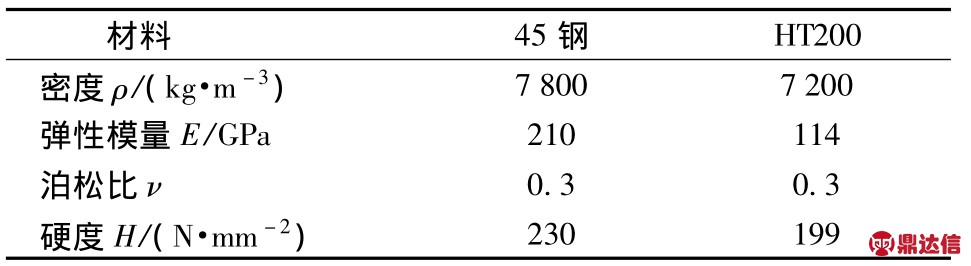
令严重磨损区的磨损深度为hmax,即导轨的直线度A=hmax;令严重磨损区的宽度为b,则严重磨损区的体积磨损量Vs可以表示为

将式(6)代入式(5)中可得

式(7)反映了导轨副的体积磨损V与导轨副的直线度A之间的数学关系。
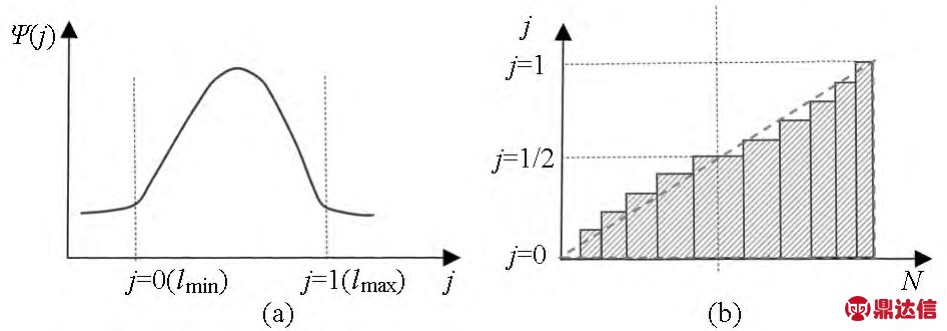
图4 随机变量j(工件长度系数)的统计学分析(正态分布)Fig.4 Statistical analysis of length factor j
(a)j的概率密度分布函数 (b)工件总量N与j的分布关系
1.3 滑动导轨副的磨损模型
许多学者建立了磨损的经验公式和理论模型[16-18]。对于滑动导轨副来说,其实际的磨损状况很复杂,因此很难利用单一的磨损理论及其磨损模型来预测导轨副的磨损。通过考察多个基本的理论磨损模型,包括Holm的磨粒磨损模型,Achard的粘着磨损模型,Suh的剥层疲劳磨损模型等[19],发现这些模型均可以转换为

式中 W——载荷 H——材料硬度
σs——材料屈服强度
K——导轨副的磨损系数,不同的磨损理论模型中,K的物理意义、影响因素及具体的表达形式各不相同
基于上述分析,导轨表面的磨损量为

导轨副的磨损系数K可通过与导轨副相同工况下的标准磨损实验来获得。考虑到用于制造导轨的脆性金属材料(如灰铸铁)没有明显的屈服强度,因此式(9)中引入硬度H而不是屈服强度σs作为参数。
1.4 滑动导轨副的精度保持性模型
式(9)通过变形可得

式中 v——滑动速度 t——滑动时间
将式(10)代入式(7)中可得到导轨直线度A随时间t衰减的数学关系,即
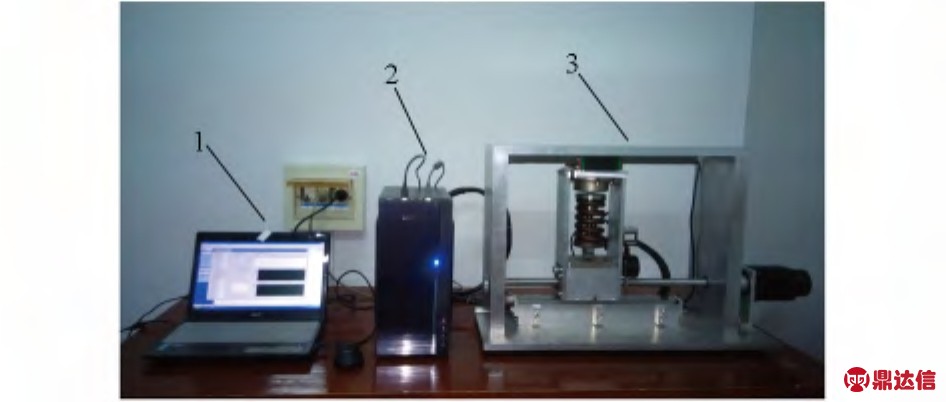
若导轨副的允许直线度为Amax,要求运行过程中导轨副的直线度变化A不能超过Amax,若超过Amax,则导轨副的精度失效。导轨副保持有效精度的时间(寿命)可以表示为

利用式(11)可以计算导轨副在运行过程中由磨损带来的精度衰减,利用式(12)可以预测导轨副保持有效精度的寿命。
2 实验验证
通常研究为滑动导轨副配对材料45钢和灰铁200的磨损精度衰减规律,这2种材料的属性见表1。首先利用标准的销盘磨损实验来获得45钢和HT200在边界润滑条件下的磨损系数K,然后利用自主设计的滑动导轨副精度保持性实验台架来研究45钢-HT200的导轨副在随机运行工况下的磨损精度并验证理论模型。
表1 材料属性参数
Tab.1 Parameters of material property
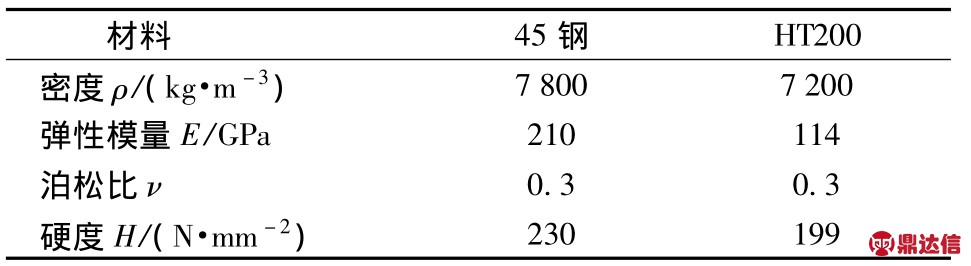
2.1 销盘磨损实验
利用MMW-1型立式万能摩擦磨损试验机进行销盘实验,如图5所示,其中销的尺寸Φ6 mm×13 mm,材料为45钢;盘尺寸为Φ31.7 mm×10 mm,材料为HT200,销和盘的接触面积为28.26 mm2,两接触表面的粗糙度Ra均为0.8 μm。根据常用滑动导轨副的典型载荷和速度,设计了如表2所示的8组工况条件下的边界润滑磨损实验。实验中使用的润滑油为68号导轨油,其特性参数见表3。研究表明边界润滑状态下表面吸附膜和化学反应膜的厚度是表面粗糙度的~
,结合销盘的接触面积以及转速,可估算出实验中的用油量为0.02 mL/h[20]。每组实验的磨损时间为1 h,实验开始时利用移液管在摩擦面上滴入润滑油0.02 mL,之后不再添加润滑油。利用精度为0.1 mg的电子天平测量盘(HT200)在实验前后的失重,并转换为体积磨损率作为研究指标,每组参数重复实验3次,取其平均值作为最终的实验结果,各组实验的磨损率如表2所示。
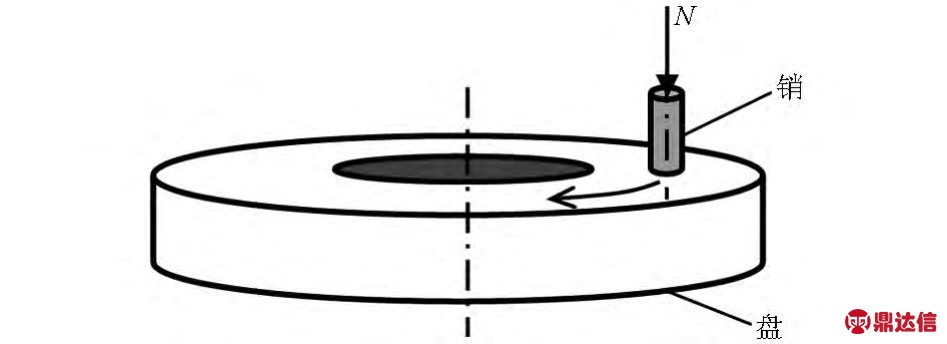
图5 销盘磨损实验示意图
Fig.5 Sketch map of pin-on-disc wear test
表2 销盘磨损实验设计及实验结果
Tab.2 Experimental design and results of pin-on-disc wear tests
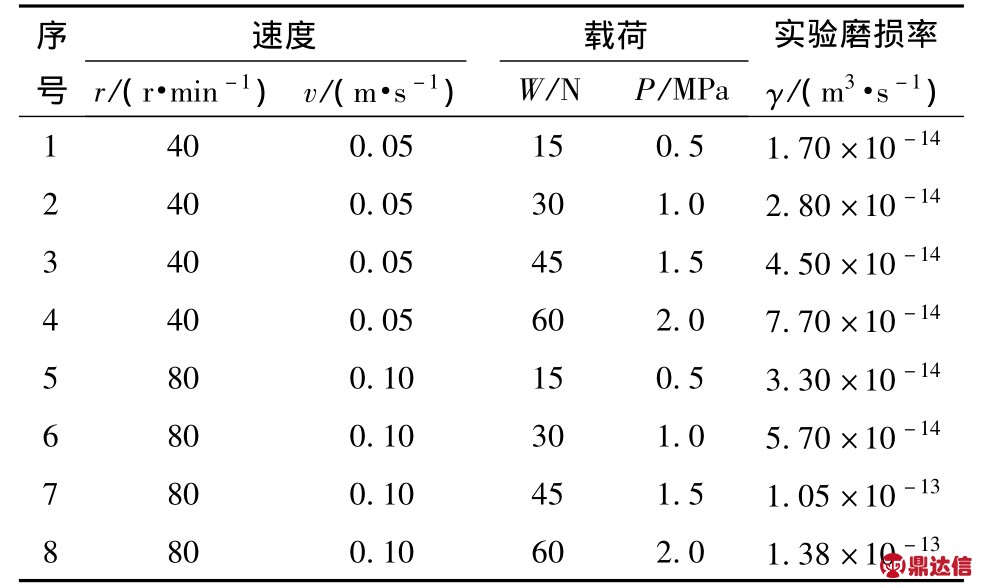
对表2中各组实验磨损率数据进行二元非线性回归分析,如图6所示,其拟合结果为

表3 68号导轨油的特性参数
Tab.3 Characteristic parameters of 68#rail oil
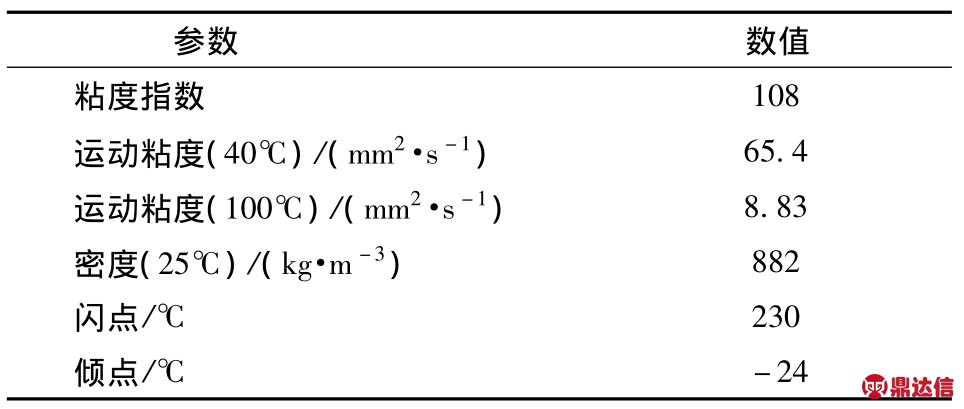
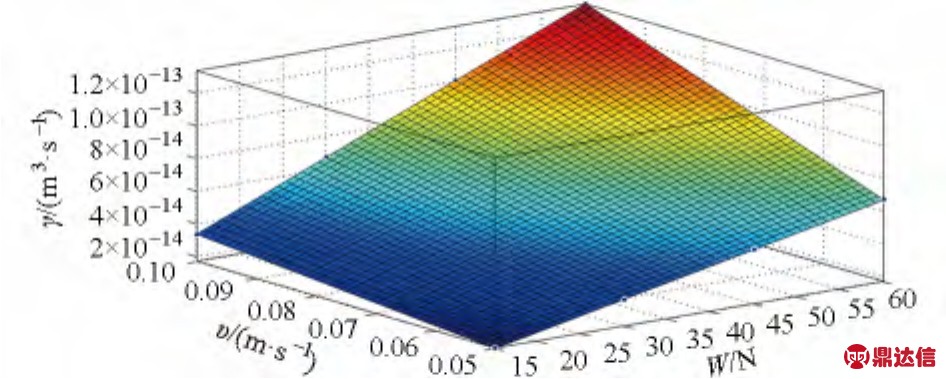
图6 销盘磨损实验数据的二元非线性回归分析
Fig.6 Dual nonlinear regression analysis of pin-on-disc wear test results
拟合结果的决定系数R2为0.997 3,非常接近1,因此通过拟合优度检验,认为式(13)是合理的。比较式(10)和式(13),并将 H=199 N/mm2代入式(10)中,可求得HT200在边界润滑条件下的磨损系数 K 为4.42×10-6。
2.2 滑动导轨副的精度保持性实验
实验在自行研制的滑动导轨副精度保持性实验台架上进行,如图7所示,实验台架主要包括机械装置和控制部件。图8为该实验台架的主要机械结构组成。该台架的设计载荷为0~6 000 N(0~1.5 MPa),运行速度为0~0.15 m/s,设计的载荷和速度参数与机床滑动导轨副的表面承载范围和进给速度范围基本相当。该实验台架能模拟导轨副的实际运行工况,实现等距、非等距(滑动长度服从一定的随机分布)滑动。该实验台架不仅能实时测量导轨副试样的摩擦力和摩擦因数,而且能自动在线测量导轨副在磨损过程中的直线度衰减并自动处理和实时显示实验数据。
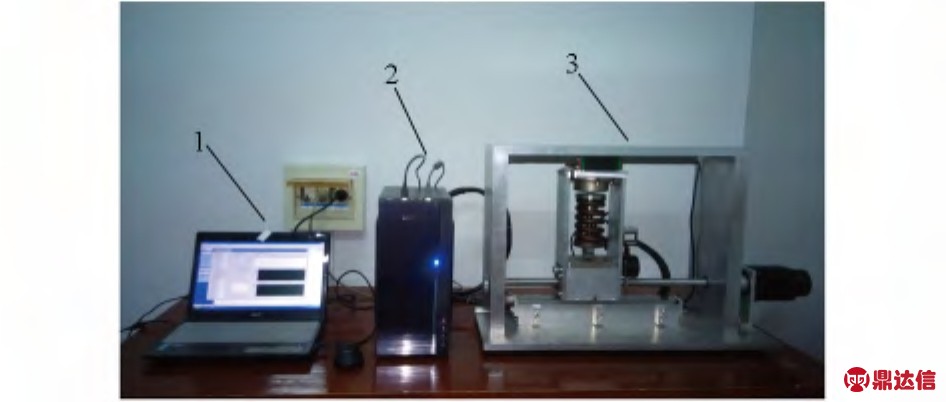
图7 滑动导轨副精度保持性实验台架
Fig.7 Test bench of precision retaining ability for slide guide
1.上位机 2.下位机 3.机械装置
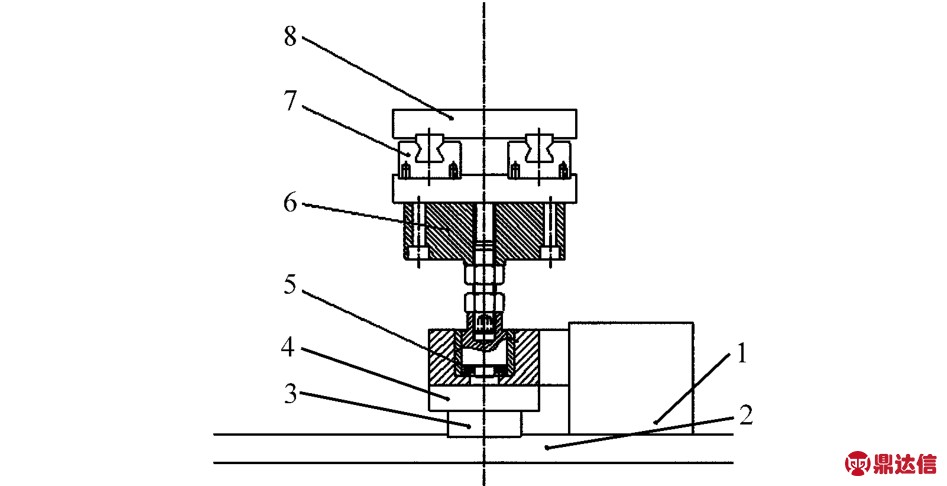
图8 导轨副精度保持性台架系统的主要机构组成
Fig.8 Mechanical constitution of test bench of precision retaining ability for slide guide
1.位置、速度控制组件 2.支撑底板 3.导轨样件 4.滑块样件5.载荷加载弹簧 6.载荷传感器 7.支撑导轨 8.支撑顶板
实验使用的滑块试样尺寸为100 mm×40 mm,材料为45钢;导轨试样尺寸为400 mm×60 mm,材料为HT200。导轨副接触表面的宽度b为40 mm。本实验主要模拟导轨副在一定载荷和速度条件下进行随机进给的运行工况。为了在实验室条件下较快地获得导轨表面的精度衰减数据,设计了较大的实验载荷,其值为6 000 N(1.5 MPa);设计的滑动速度为0.05 m/s。实验中使用的润滑油为68号导轨油,其属性参数见表3。为了使滑动表面保持边界润滑状态,通过估算,可得实验中的用油量为0.2 mL/h[20],因此实验过程中每隔1 h用胶头滴管在摩擦表面滴加润滑油4滴(0.05 mL/滴)。为了实现导轨副的随机进给运动,在参数设置界面设置了一系列在100~300 mm范围内,均值为200 mm,标准偏差为47 mm的服从正态分布的随机进给位置点,利用指令控制实验台架中的伺服电动机和滚珠丝杠以驱动滑块达到指定位置。实验开始前测得导轨面的初始直线度 A0为0.015 mm(15 μm),实验过程中每隔0.5 h测量一次导轨面的直线度,实验时间约为20 h。实验过程中测得的导轨面的直线度变化如图9所示。将相关参数数值代入式(11)中,可以得到理论计算的直线度衰减曲线,如图9所示。
由图9可知,在实验的初始阶段,导轨表面的直线度会出现较大的衰减,之后会达到一个衰减较小且变化稳定的阶段。这主要是由于实验初期导轨副摩擦表面有一个磨合适应阶段,该阶段的磨损较为剧烈,因此直线度衰减变化较大;当摩擦表面达到稳定的磨损状态后(t0时刻以后),导轨副也进入稳定的工作状态,此时直线度的变化变得相对平稳。由图9可见,在导轨副稳定的磨损阶段,导轨表面直线度的理论计算曲线和实验数据曲线较为接近,二者的最大相对误差为22%,这说明本文建立的理论模型能较好地预测导轨副在稳定工作状态下的精度衰减。
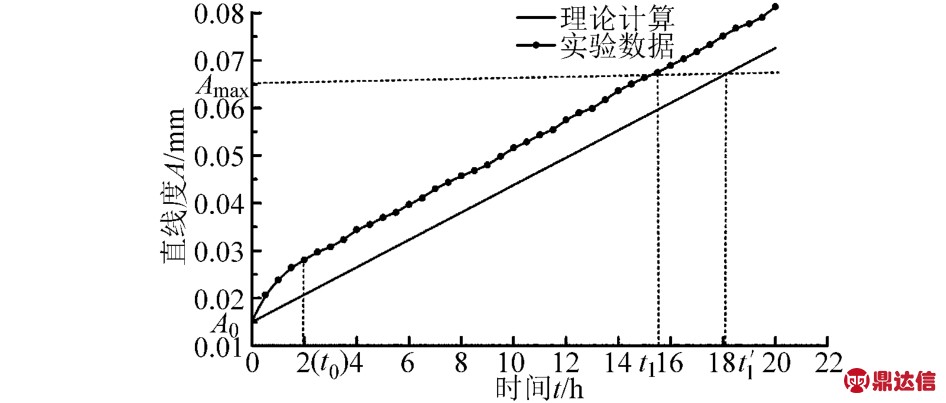
图9 导轨副服从正态分布随机进给滑动时精度衰减的实验值与计算值对比
Fig.9 Comparison between experimental and theoretical results of straightness attenuation of slide guide in random feeding process with normal distribution
此外,由图9可知,对于给定的导轨副的允许最大直线度偏差Amax,理论模型计算的精度保持时间t'1比实验测得的精度保持时间t1偏大,这表明利用理论模型可以计算得到台架实验中导轨副精度保持性能的极大值。然而台架实验和实际机床导轨副的运行工况具有一定差异。在台架实验和理论建模时,导轨副的往复运行工况相同,即认为退刀过程和进给过程中表面的磨损作用相同;而实际机床导轨副往往在退刀时比进给时的磨损作用要轻微,即实际机床导轨副的总体磨损量比台架实验和理论模型预测的磨损量低,相应地其表面精度衰减更慢,其精度保持的时间更长。据此可得,利用本文建立的精度保持性理论模型可以计算得到实际机床导轨副精度保持寿命的极小值,即导轨副实际的精度保持寿命值比理论计算值大,这可为导轨副的精度调修提供参考依据。
3 结论
(1)基于机床滑动导轨副实际运行工况下的磨损特点,推导建立了滑动导轨副的精度保持性模型,该模型表明导轨副的精度保持性能与导轨副的工况参数(表面承载及滑动速度)、运行参数(滑动进给行程)、导轨副材料属性以及表面磨损率等因素具有定量的数学关系。
(2)利用自主设计的滑动导轨副精度保持性实验台架模拟导轨副的随机运行工况并测量导轨副的直线度变化,在导轨副稳定工作阶段直线度衰减的实验值曲线和计算值曲线较为接近,二者的最大相对误差为22%,表明本文建立的精度保持性模型是合理的,能较好地预测导轨副的精度保持寿命。