摘要:滚动导轨是很多制造设备的重要组成,尤其是在数控机床的工作台进给系统上应用广泛。滚动导轨因为沿导轨运动方向无约束,使得已有的固定结合部模型无法真实反映其运动情况。本文基于滚动导轨结合部的各个节点之间的位移及动力学关系,考虑将每个节点沿着导轨运动方向的自由度释放,提取各模态参数矩阵,并结合最小二乘法的误差辨识,所建立的可动结合部模型与导轨的实际运动及受力情况相吻合。该模型结构相对简单,应用计算机运算容易,方便企业应用。最后,围绕所构建的模型,以机床上常用的LGS20H常规型滚动导轨为例,搭建实验平台,综合实验和理论计算,验证了模态参数辨识模型的可靠性,结论证明,模型误差控制率良好。
关键词:滚动导轨;动力学参数辨识;可动结合部模型
滚动直线导轨是直线导轨的一种,与传统滑动导轨相比,滚动直线导轨优势明显,正逐步取代滑动导轨[1]。滚动直线导轨的组成一般分为如图1中标识的几个部分[2]。滚动直线导轨动、静摩擦力之差很小,刚性可调,随动性好; 同时,滚动直线导轨副具有误差均化效应,标准化程度高[3-5]。
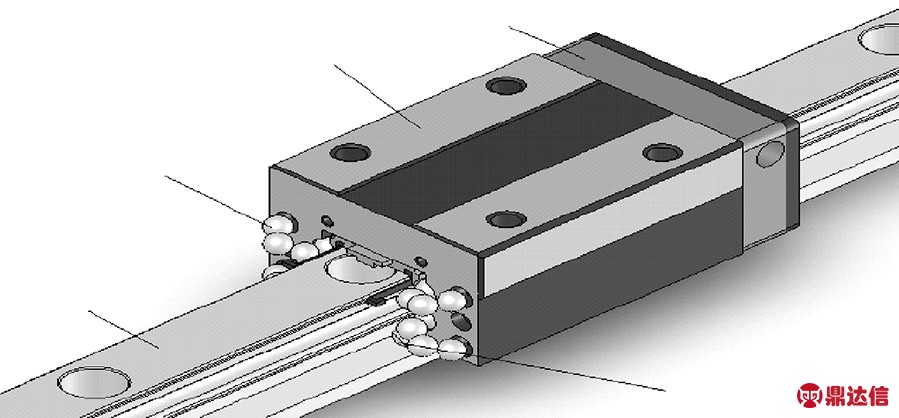
图1 滚动直线导轨组成
滚动导轨作为制造设备的重要组成部分,尤其是在数控机床的工作台进给系统上应用广泛。滚动导轨的滑块与导轨之间的部分因为存在相对运动,而往往与机械固定结合部相区分。研究表明,机床滚动导轨可动结合部的特性是机床进给运动性能的重要体现,对产品的加工效率及加工精度影响深远。同时,建立高精度的滚动导轨可动结合部力学模型是建立机床整机动力学模型的前提和基础,因此要提高机床的加工效率及加工精度,就必须对机床可动结合部的特性进行深入研究。相对于机械可动结合部的动力学分析及参数识别,机械固定结合部的相关研究开展更早。与固定结合部的研究不同之处在于,可动结合部有更多的自由度,动力学的分析需要兼顾更多的维度,如果简单的引入固定结合部的研究方法,往往会导致结合部动力学参数辨识精度的缺失。
目前对滚动直线导轨副可动结合部进行动力学研究,比较常见的方法是构建弹簧-阻尼单元动态模拟可动结合部运动特性,进而辨识其动力学参数。该方法考虑一系列的孤立弹簧-阻尼单元模拟导轨与滑块的连接,从而构建动力学模型。等参数接触单元法因为精度更高、更为通用为多国学者重视,该方法的研究主要集中在六结点等参单元和八结点等参接触单元的简化,进而表征其静态接触刚度以及其动态接触刚度[6-7]。
基于上述研究基础,本文通过对滚动直线导轨可动结合部的动力学模型分析,求解系统输出的频响函数矩阵,以此辨识滚动导轨可动结合部模型的动力学特征参数,并完成其动力学模态特征的分析。
1 滚动直线导轨可动结合部动力学分析
滚动直线导轨运动副沿导轨方向的运动不受约束,参照有限元分析中的“八节点六面体”模型,将滚动导轨的可动结合部单元表征为如图2所示的单元形式,其中Ⅲ为滚动导轨与螺母之间的结合部单元,在模型的动力学分析过程中,不考虑结合部单元的质量属性。
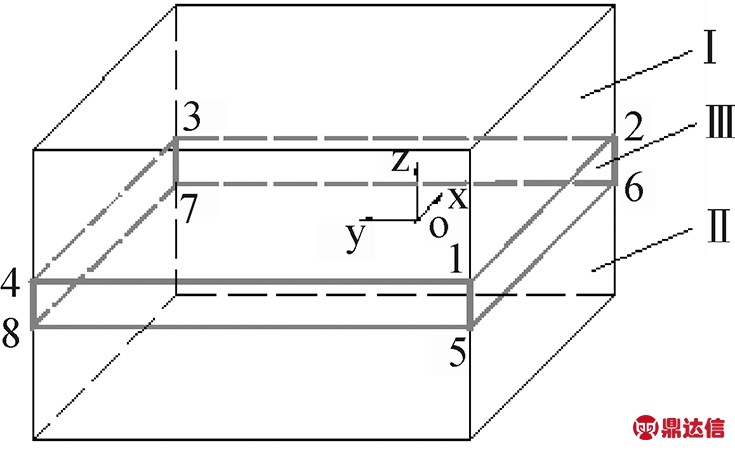
图2 “八节点六面体”结合面单元
设各节点位移为xij,各节点所受的力为fij,i =1,2,…,7,8;j=1,2(这里申明j=1代表X方向的平动,j=2代表Z方向的平动,下同)。首先推导结合面有限单元的刚度矩阵。结合面的运动特性需要考虑相互关联的不同节点之间的相对运动,如节点1和节点5;节点2和节点6等等,其运动位移可描述如下:
x1j-x5j,x2j-x6j,x3j-x7j,x4j-x8j,j=1,2。
根据刚度影响系数法,则有

(1)
其中,为刚度影响系数,i,m=1、2、3、4,表示节点号;n,j=1、2,表示方向。
刚度是重要的动力学参数,阻尼多自由度线性振动系统的运动微分方程的描述如下:

(2)
应用傅里叶变换后,不妨定义系统动刚度矩阵为[Z(w)]=[K]+jw[C]-w2[M],则式(2)可记为
[Z(w)]{X(w)}={F(w)} 。
(3)
频响函数与系统的输入、输出相关,而对于线性定常系统,频响函数能够准确表征系统输出与输入的固有关系。
本文对频响函数的描述如下:
Hij(w):表示自由度j方向上施加激励信号,而自由度i方向上予以信号的测量,其中j方向上的信号为输入信号,而i方向上为输出信号;当i,j全面取值时,根据排列组合的相关知识,推测一共存在n2种情况,他们构成一个n×n的频响函数矩阵,
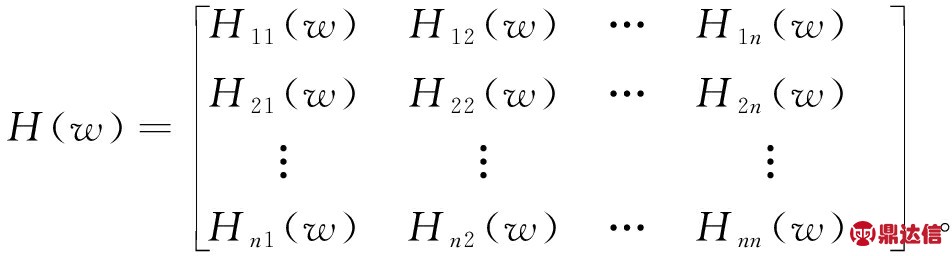
从动刚度矩阵的表达式可以看出,动刚度矩阵[Z(w)]与m,c,k有关,则[H(w)]也与m,c,k有关,它是反映系统固有特性的量,是以外界激励频率w为参变量的非参数模型,可以通过锤击实验测得,这是锤击法进行模态实验的理论基础。
对于如图3所示的导轨结合部,其结合面的动力学参数m,c,k未知,便可基于上述频域内模态参数识别方法进行参数识别。
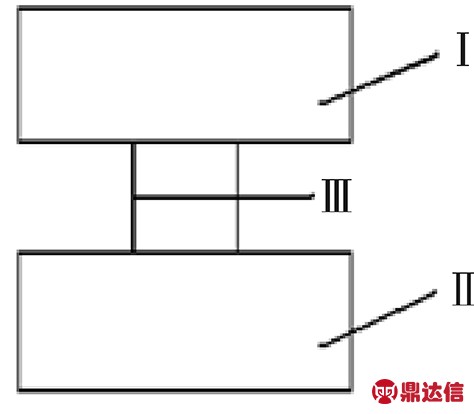
图3 导轨可动结合部
设Ⅰ、Ⅱ子结构的动力学方程为:

(4)
包含导轨可动结合部全结构的动力学方程描述为:

(5)
其中,子结构Ⅰ、Ⅱ的整体质量矩阵(已知量); 子结构Ⅰ、Ⅱ的整体阻尼矩阵(已知量); 子结构Ⅰ、Ⅱ的整体刚度矩阵(已知量);
[Mj],[Cj],[Kj]分别表示可动结合部的质量、阻尼及刚度特征参数,其中[Cj]=α[Mj]+β[Kj]。
综合方程(4)及方程(5)的描述,可得如下动力学方程:

(6)
此处不考虑子结构本身的阻尼Cs以及结合面的质量,则[Cj]=β[Kj]。进一步转化方程得到,
(-w2[Ms]+jwβ[Kj]+[Ks+Kj]){H(w)}=[I] 。
(7)
对于各子结构,有限元模态分析能够得到其质量矩阵,刚度矩阵,阻尼矩阵(此处比例阻尼,可忽略);对于结合面,结合公式(7),其刚度矩阵Kj和阻尼矩阵Cj未知,是模型需要求解结合面动力学参数。
基于单点激振,多点拾振方法,对应于w取不同的值,便得到不同的方程,也即
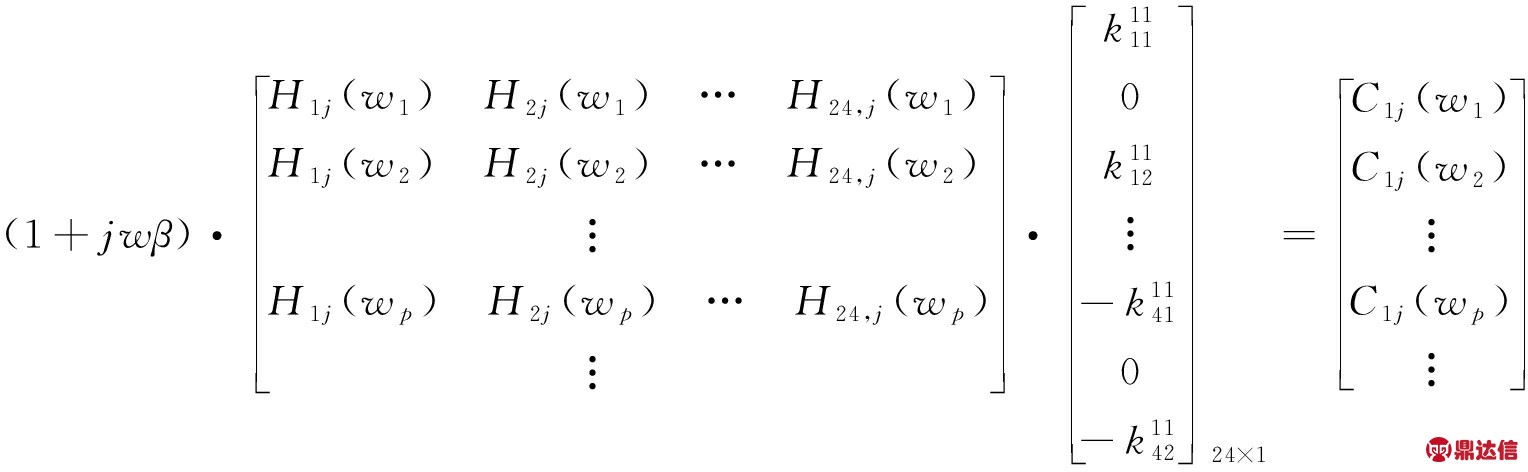
,
(8)
其中,p为w(方程)的个数;上式含有9个未知数,分别是和β。
采用最小二乘法思想,定义函数
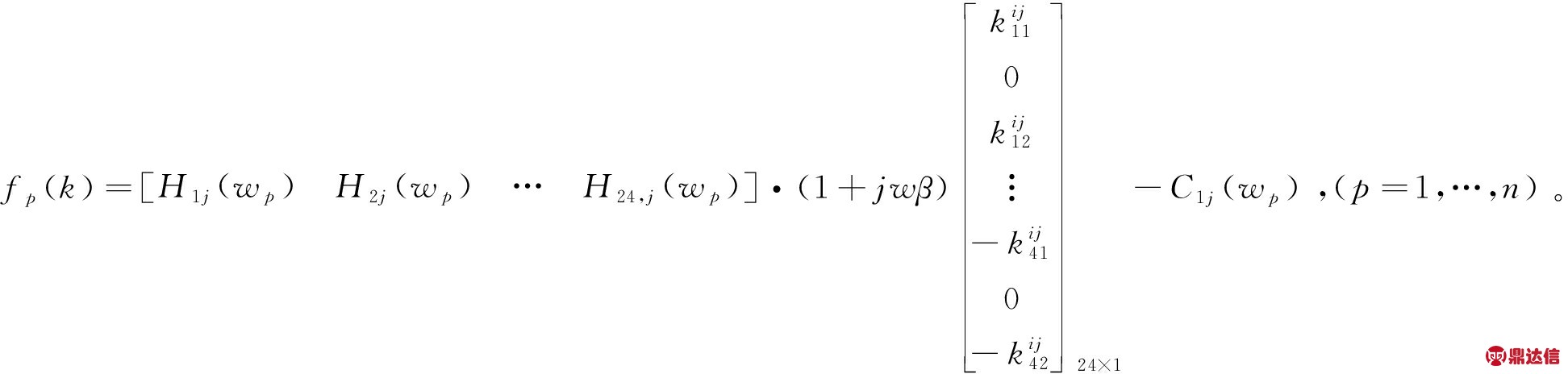
(9)
上式显示, fp(k)为非线性函数,自变量为p及wp。在参数求解时,选择非线性最小二乘法求解未知动力学参数。其中,
f(k)=[abs(f1(k))·abs(f2(k))·abs(f3(k))…abs(fp(k))]T 。
当利用MATLAB非线性最小二乘法求解f(k)时,目标函数可以表示为

其中,k为未知列向量,f(k)为函数列向量。
至此,参数识别得到了导轨可动结合部单元刚度矩阵和阻尼矩阵,从而建立了导轨可动结合部单元的动力学模型。
2 实验分析
实验以机床上常用的LGS20H常规型滑块直线导轨为研究对象,借助LMS软件的强大功能,展开滚动导轨的模态分析。测试系统需要在导轨及其配重块布置测点56个,滑块及其配重块布置测点48个。LMS中测试点模型如图4所示:
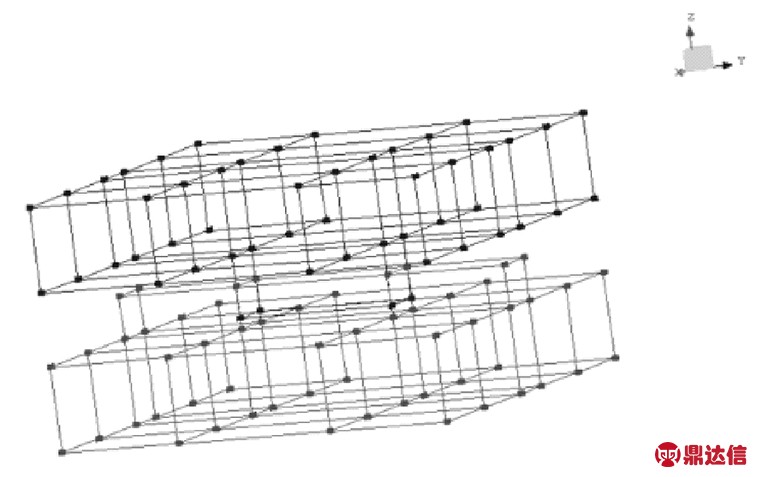
图4 LMS中的测点模型
实验边界条件考虑自由状态,试验采取的是两个方向的激振,即X轴负方向和Z轴负方向,测试现场如图5所示:
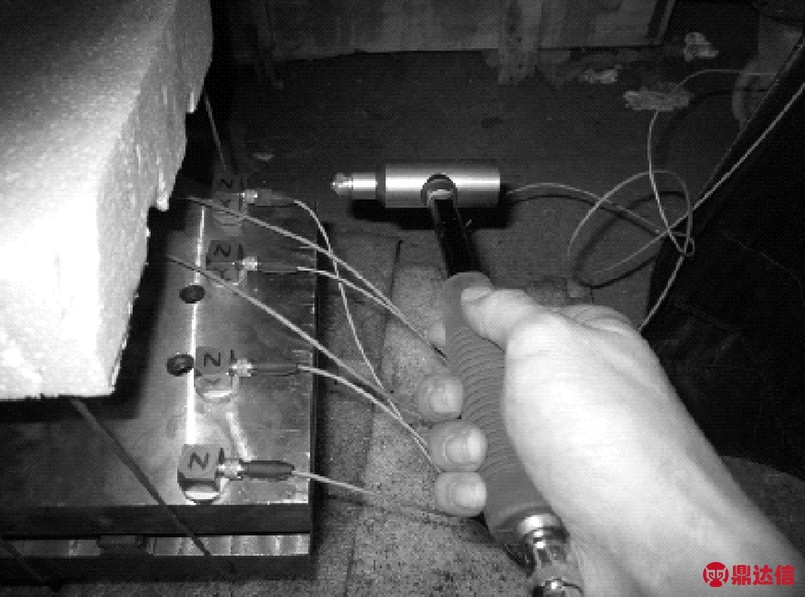
图5 导轨动态测试现场
实验的激励方式为力锤冲击激励,锤击激励设置简单,实验周期短,不会影响试件的动态特性。本次实验激励的敲击点选择在立柱的顶部body1∶31号测点上。敲击方向沿着Z轴负方向和X轴负方向。实验时,取带宽fmax=1 600 Hz,采样频率即为fs=2fmax=3 200 Hz。取谱线数L=3 200,此时频率分辨率△f=fmax/L=0.5 Hz。为了减少实验误差,力锤实验时选取5次锤击的频响函数均值。选择导轨和滑块上面的螺强度为8.8级,实验环境考虑相同预紧力下将滑块进行来回滑动后回位,螺栓预紧力设置为12 N·m,结合上文理论基础,用刚度影响系数进行参数识别,本组选取的螺栓预紧力为12 N·m 的试验,参数识别时程序中可调参数选择:
ex=0.95×ex; ez=2.8×ez; ey=0.59×ey;
x=1.6×(6.5/3)×(0.05/3)×2.1e11; y=0.3;
z=x×(1-y)/((1+y)×(1-2.0×y));
实验模态与计算模态的比较如图6所示:(12 N·m)。
实验结果表明,本文基于动力学建模的滚动直线导轨刚度参数辨识切实可行,各阶模态的误差控制率良好。
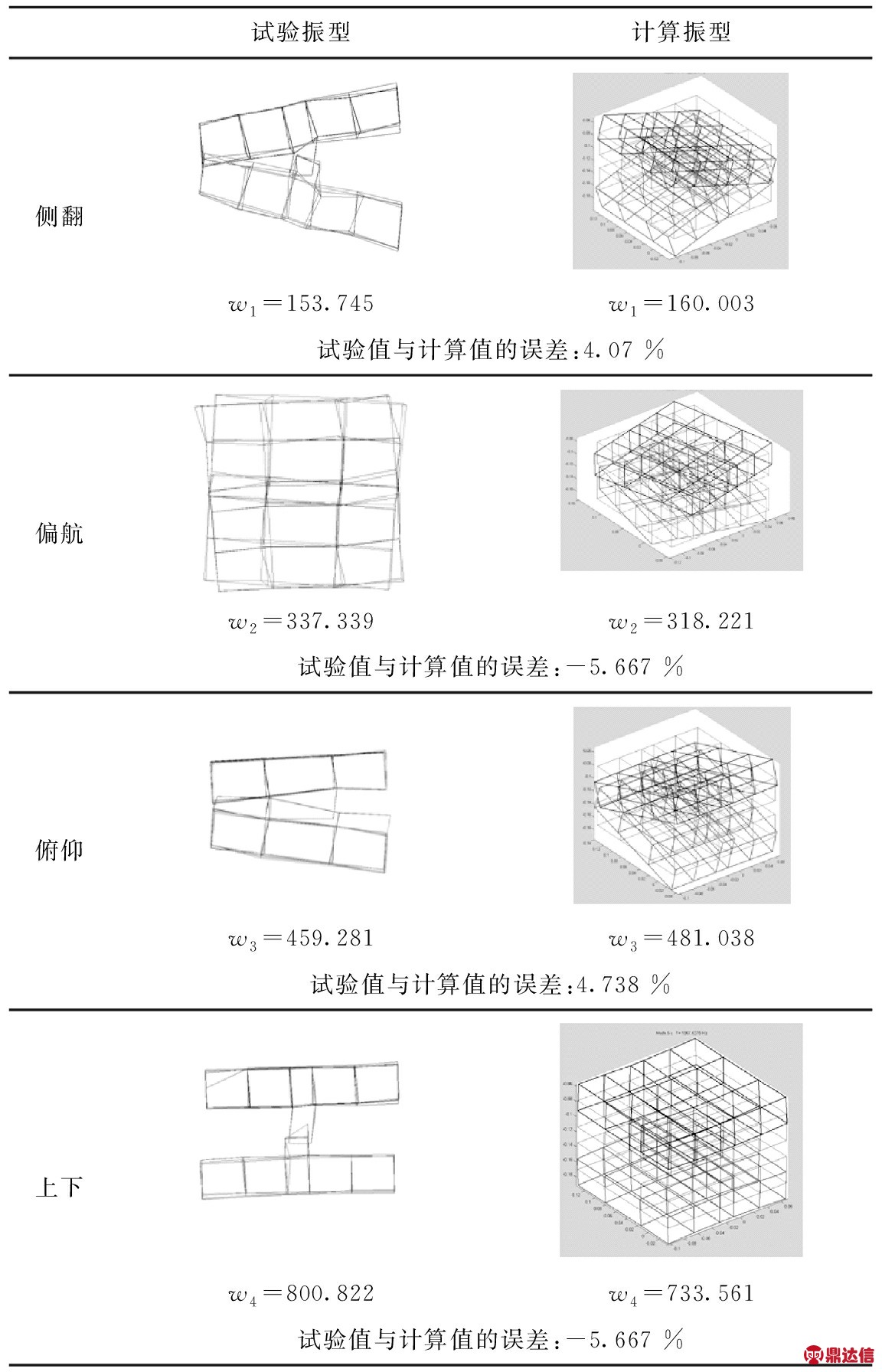
图6 实验模态与计算模态的比较
3 结语
通过对滚动导轨的结构和性能分析,针对导轨与滑块之间的可动结合部构建了多点动力学模型,该模型基于滚动导轨结合部的各个节点之间的位移及动力学关系,考虑将每个节点沿着导轨运动方向的自由度释放,并结合最小二乘法的误差辨识,最终实现了对滚动导轨可动结合部的模态参数的识别。文章最后围绕所构建的模型,以机床上常用的LGS20H常规型滚动导轨为例搭建实验平台,应用理论与实践相结合的科学方法,验证了模态参数辨识模型的可靠性,实验结果显示模型误差控制率良好。