摘要:着重介绍CP7620多刀车床刀架导轨进行自动润滑系统的改造,来减少操作员工的劳动强度,减少机床刀架导轨的磨损或破坏,降低机床设备故障率和保证产品加工精度,达到提高生产效率和降低生产成本的目的。
关键词:缸套;刀架;自动润滑
1 CP7620多刀车床刀架导轨改造原因
2005 年以前在气缸套行业中CP7620多刀车床作为主要关键设备之一,其主要特点之一该机床的主传动采用双速电机驱动,可根据加工工件的不同直径,在一次自动循环中前、后刀架可得到两种不同的合理切削速度,操作简单实用。主要用于加工缸套长短、外圆、水槽封、大台等部位。随着数控机床的不断普及,逐步退出关键设备的历史舞台,被数控机床所替代。但是,目前在气缸套生产过程中,CP7620多刀车床主要用于修车等工序,进行加工气缸套的长度、大台外径及厚度、裙部等部位几何尺寸相关余量,其加工尺寸稳定,加工时间短,生产效率较高等特点。
由于CP7620多刀车床刀架导轨采用人工润滑,操作员工每天都要在班前、班中对前后刀架导轨进行两次人工润滑,存在很多的动作浪费或人为因素影响设备加工性能等现象。在现实工作中存在有的操作人员不能遵守定时润滑的动作,或有润滑动作可是润滑不到位,可造成导轨损伤;或润滑油使用过多造成润滑油浪费等现象。因导轨润滑不良而引起的导轨磨损、拉伤、振纹、两端面平行度不好、加工外圆尺寸锥度大等设备故障率较高。同时,一次维修刀架导轨时需磨刀架、配键、刮研等工作时间1-2天,每次维修费用在3000元左右,若刀架导轨磨损严重造成整体刀架报废,维修成本会更高,且影响产品质量及生产效率。所以,随着科技的进步,机械行业向自动化、智能化方向发展,气缸套行业精益生产的推行,设备自动化改造,减少操作员工的劳动强度等方面的改善,我们对CP7620多刀车床前后刀架导轨进行自动润滑改造。
2 CP7620多刀车床刀架自动润滑系统设计及改造
为实现CP7620多刀车床刀架导轨定时定量自动润滑,刀架导轨配合面处于均匀油膜的良好状态,减少磨损故障率,降低设备维修成本,降低员工劳动强度。我们参考数控机床自动润滑化原理对CP7620多刀车床刀架导轨进行自动润滑系统设计及改造。
CP7620多刀车床刀架导轨自动润滑系统原理图如图1所示,包括自动润滑油泵,分支器和油管,自动润滑油泵固定在设备上,自动润滑油泵加满润滑油,通上电源,自动润滑油泵润滑油出口通过油管与分支器连接,分支器出口分别通过油管与前横刀架导轨、前纵刀架导轨、后横刀架导轨、后纵刀架导轨的配合处注油口固定好。保证前刀架和后刀架在运行过程的平稳和导轨有均匀有油膜,处于良好的润滑状态,降低导轨的划伤或磨损。
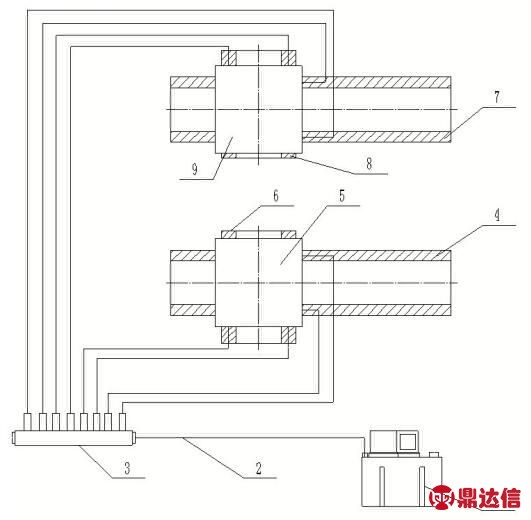
图1
1、自动润滑油泵;2、油管;3、分支器;4、前刀横架导轨;5、前刀架;6、前纵刀架导轨;7、后横刀架导轨;8、后纵刀架导轨;9、后刀架
使用自动润滑油泵作为动力源主要优点是能够定时、定量地自动加注润滑油到各导轨润滑点,使各导轨在刀架的移动工作中总是处于良好的润滑状态。通过分支器调节旋钮可以对各导轨润滑点所需润滑油量进行调整,保证各刀架导轨润滑油量地均匀性。
3 CP7620多刀车床刀架自动润滑系统改造效果
3.1 降低员工劳动强度:未改造前员工每班进行二次(班前和班中)手动对刀架导轨进行润滑,其润滑效果一致性较差,存在润滑不良的现象。每次润滑需要将导轨防护取下,润滑后重新安装好,上下4个刀架防护全部要进行安取一次,每次需要15分钟左右,每班2次,需要30分钟左右。改造后至今运行正常,员工只需要将机床进行预热和空运行就可以,只操心保证工件的质量就可以了,大大降低了员工的劳动和操心强度。
3.2 降低成本:未改造前刀架导轨大约每年需要维修一次,每次维修刀架时磨刀架、配键、刮研刀架导轨等工作,一次维修费用在3000元左右,维修成本高,维修周期长,且影响产品质量及生产效率,同时每台设备需要配置1个压力油枪。改造后至今运行正常,未发现因润滑不良而引起的导轨磨损、拉伤、平行度不好等故障,降低了设备故障率,降低了影响产品质量因素和维修成本,解放修理工们的重复劳动时间。
3.3 提高生产效率:未改造前每台设备每班需要润滑时间30分钟,若发生故障时维修需要三个维修人员进行更换调整工作4小时左右生产线才能正常运行,造成很大的窝工现象。改造后实现对CP7620多刀机床刀架定时定量自动润滑,刀架导轨配合面处于油膜良好均匀,减少刀架导轨因缺油磨损故障率,员工劳动量的降低,设备故障率降低、加工精度稳定,产品质量得到了保证,生产效率有极大的提高。
4 结束语
对CP7620多刀车床刀架自动润滑系统改造,经过一年多的实践应用,至今未发现刀架导轨故障,提高设备自动化程度,润滑油使用均匀合理且性能好,有效地减少人为因素影响设备性能目的,解放员工的多余劳动强度,降低了设备故障率和维修成本,提高产品质量、设备利用率和生产效率。