摘要:以流量控制阀调节下的闭式液体静压导轨为对象,建立了导轨系统的运动学方程和流量方程,推导并线性化处理了外载荷与油膜厚度、油腔压力的微分方程组,利用Laplace变换获得了传递函数,推导了导轨动态性能的数学表达式。以现场调试为基础,绘制了油膜厚度与动力黏度、油腔压力与初始开口度的关系曲线,分析了系统的幅频、相频特性。分析了动力黏度、初始开口度对时域、频域内导轨动态性能的影响,研究结果可为工程调试提供理论基础。
关键词:流量控制阀;闭式静压导轨;非线性微分方程;动态特性
0 引言
流量控制阀能够根据工作负载需要而灵活地调整输出流量,设定后的输出流量抗干扰能力强、刚度大,因此在静压支承中得到了广泛的应用。近年来,国内外较多的学者对其进行了研究。吕琳等[1]以精冲机滑块的高精度导向为要求,计算了静压导轨承载能力及油膜刚度,研究了静压导轨油膜厚度的控制方式。左旭芬[2]根据数控凸轮磨床结构的特点,确定了矩形静压导轨的结构参数对与磨床性能的影响关系。罗恕燕等[3]对大型数控滚齿机工作台的二级承载液体静压导轨副的动静态性能进行了定性和定量的计算。张亮等[4]建立了静压导轨自适应供油系统的数学模型,对其进行了动态仿真研究。李志红等[5]以调速阀进口节流调速系统为例,得到了液压缸无杆腔压力超调量的变化规律,并对理论推导和分析进行了试验验证。刘恒丽等[6]利用功率键合图法建立了键图模型和数学模型,用MATLAB软件进行了仿真,对调速阀的性能进行了分析。
流量控制阀-静压导轨支承系统属于非线性系统,计算和分析都比较困难。国内外很多学者都致力于静压支承系统的性能研究,但流量控制阀-静压导轨支承系统的动态特性的研究报道较少,因此笔者试图采用线性化处理及Laplace变换的方法获得导轨系统的传递函数,对其进行动态特性分析。
1 导轨系统的状态分析
导轨系统主要包括对置静压油腔、流量控制阀、液压泵及溢流阀等,如图1所示。流量控制阀选用的是2FRM型二通流量控制阀,由旋钮1、节流体2、节流口3、阀体4、弹簧5、压力补偿器6、节流孔7组成。节流口3为流量阀主要的压力设定元件,压力补偿器6为流量阀的压力自动调节元件。
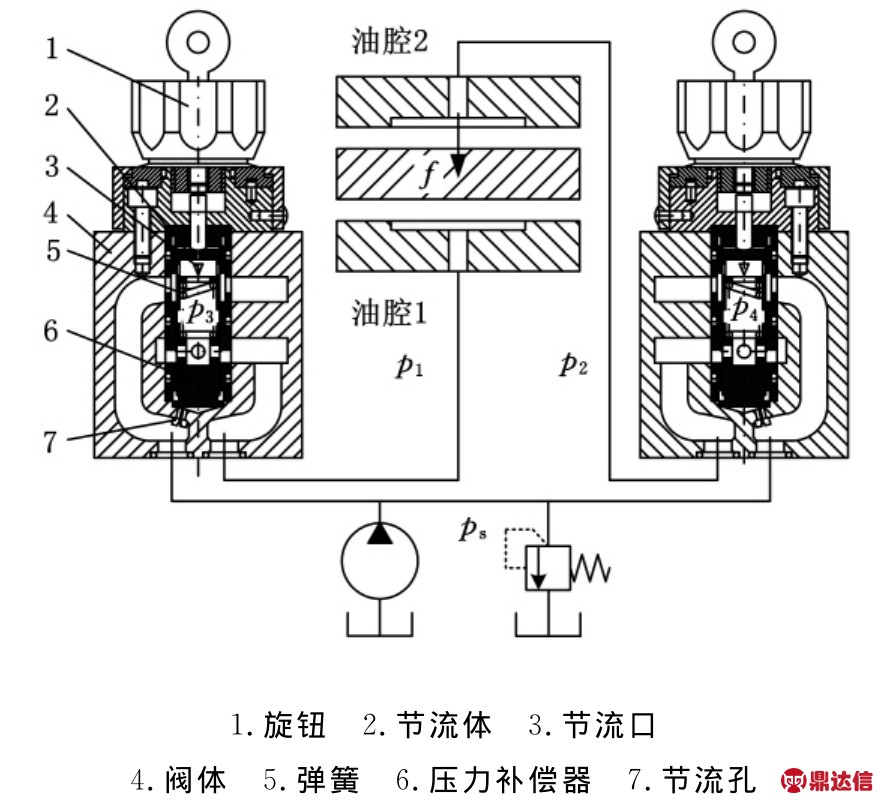
图1 导轨静压支承系统的结构示意图
导轨系统的对置油腔组由2个形式相同、尺寸相等的矩形油腔组成,如图2所示。
1.1 导轨系统的初始状态
导轨处于初始状态时,导轨质量为m,油腔尺寸确定,供油系统的泵压为ps,油膜厚度为h0。

图2 静压油腔的结构示意图
(1)导轨的运动学分析。对初始状态时的导轨进行分析,建立力平衡方程:

式中,p1,0、p2,0 分别为油腔1和油腔2的压力;Ae,1、Ae,2 分别为油腔1和油腔2的有效承载面积,Ai、Bi分别为矩形油腔的长和宽;ai、bi分别为在长、宽方向上的封油边宽度。
(2)油腔的流量分析。导轨系统的流量可表示为

式中,μ为液压油的动力黏度为流量系数。
(3)流量控制阀的运动学分析。流量控制阀中的压力补偿器处于平衡状态,列出力平衡方程:

式中,FT,i 为流量控制阀的弹簧力;pi+2,0 为压力补偿器的前部初始压力;AF,i为压力补偿器的有效作用面积;FW,i为压力补偿器的稳态液动力;Cv为流速系数;Cd为流量系数;di为压力补偿器的直径;xi,0为压力补偿器的初始开口度;θ为压力补偿器的液流角,θ=69°。
(4)流量控制阀的流量分析。对流量控制阀中的节流口、压力补偿器处的流量进行计算,列出控制阀流量qF,i,0 的表达式:

式中,AJ,i为节流口的通流面积;ρ为油液密度。流量控制阀内部有节流口与压力补偿器两个节流位置,因此式中存在两个流量计算公式。
(5)导轨系统的流量分析。导轨系统处于稳定状态时,流量控制阀与油腔的流量相等:

1.2 导轨系统的过渡状态
导轨处于过渡状态时,油腔压力p、油膜厚度h、压力补偿器的开口度x、前部压力pi+2均随着外载荷F的变化而变化。
(1)导轨的运动学分析。在外载荷F的作用下,导轨在对置两油腔连线方向上的位移与油膜的厚度变化值e相等。对过渡状态时的导轨进行分析,建立力平衡方程:

(2)油腔的流量分析。导轨在外载荷的作用下,对置两油腔的油膜厚度分别为h1、h2,h1=h0-e,h2=h0+e,则油腔的瞬时流量可表示为

(3)流量控制阀的运动学分析。过渡状态下,流量控制阀中压力补偿器的开口度为xi,列出力平衡方程:

其中,弹簧力FT,i与开口度x有关,调节过程中开口度变化较小,因此FT,i认定为恒值。
FW,i的数学表达式为
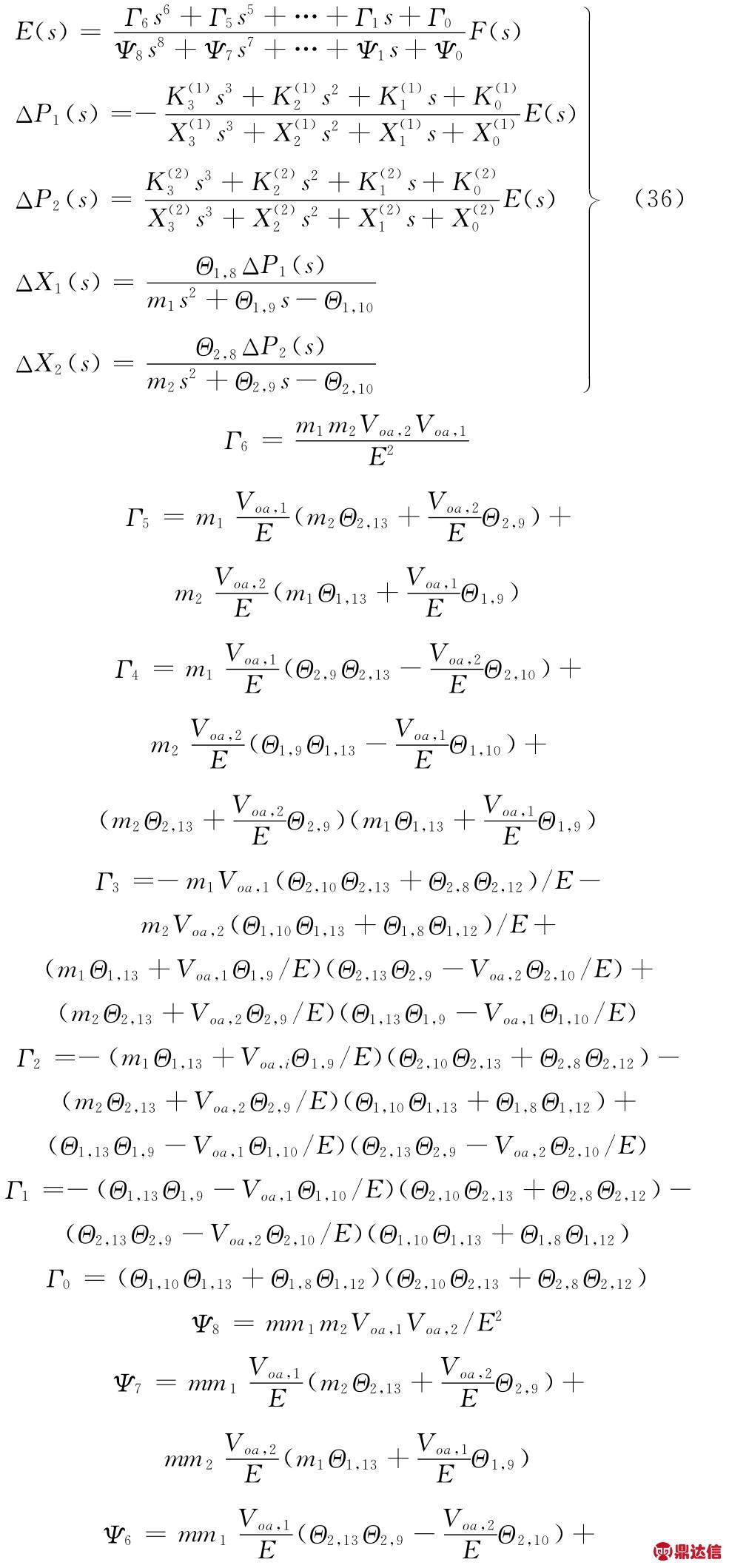
压力补偿器的瞬态液动力FS,i的数学表达式为
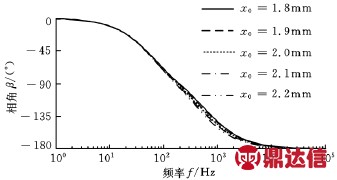
式中,Li为压力补偿器内液体轴向流动距离。
(4)流量控制阀的流量分析。对流量控制阀的节流口、压力补偿器的流量进行计算,流量控制阀的输出流量为
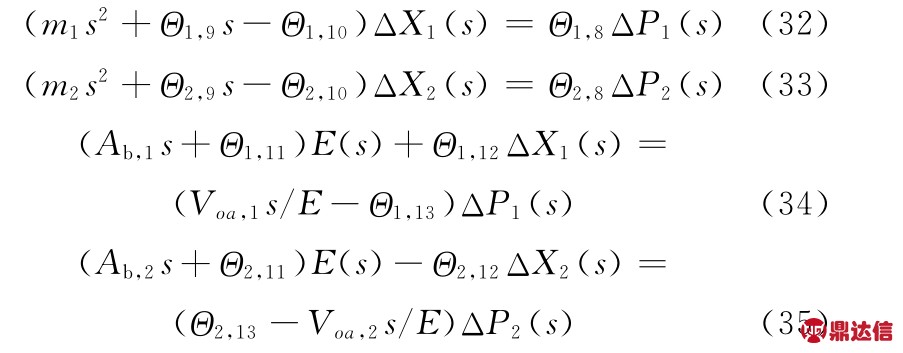
流量控制阀内部有节流口与压力补偿器两个节流位置,因此式(12)中存在两个流量计算公式。
(5)导轨系统的流量分析。导轨系统处于过渡状态时,流量控制阀与油腔的瞬时流量不相同,流量关系为

式中,qJ,i 为 油膜 厚度变 化而 排挤的 油液 流量;qR,i 为 控 制阀与油腔的容积效应流量。
由于油膜厚度变化而排挤的油液的挤压面积为

油腔的挤压流量为

油液中较容易混有未溶解的空气,因此需考虑容积效应[7]。容积效应一般与油液的压缩性有关,与流量控制阀出口到油腔之间的所有油液体积(一般称为敏感油路体积Voa,i)有关,其数学表达式为

式中,τ为油液的压缩性系数;E为油液的弹性模量。
2 导轨系统的线性化及传递函数推导
2.1 导轨系统的方程推导
(1)初始状态。根据导轨系统的设计,只要确定导轨质量m、油腔尺寸、油膜初始厚度hi,0、油腔初始流量qi,0,则油腔压力pi,0、前部压力pi+2,0、初始开口度xi,0均可计算出。
根据式(5),pi+2,0 可由xi,0 表示:

将式(4)、式(17)代入式(3)中,得到
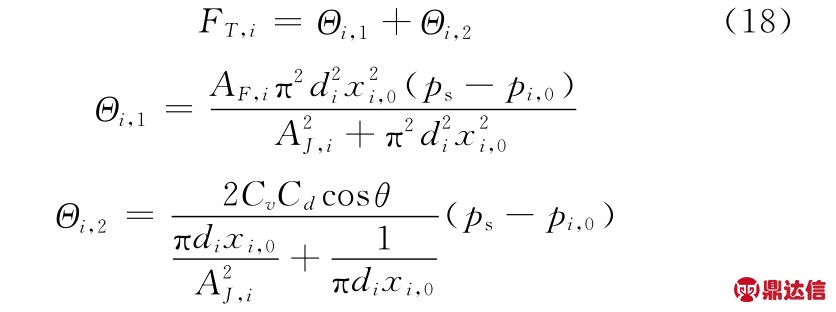
将式(2)、式(5)、式(17)代入式(6)中,得到
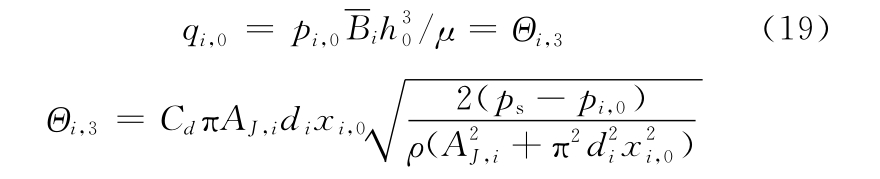
(2)过渡状态。根据静压导轨的设计,只要确定导轨质量m、油腔尺寸、初始油膜厚度hi,0、油腔流量qi,0、外载荷F,则油腔压力pi、油膜厚度hi、前部压力pi+2、开口度xi均可计算。
根据式(12),pi+2 可由xi 表示:

将式(10)、式(11)、式(20)代入式(9)中,得到
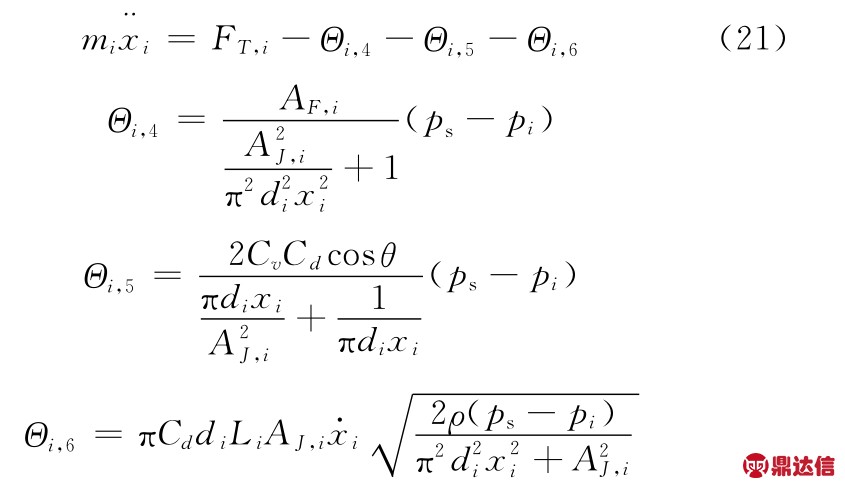
将式(20)代入式(12)中,得到

将式(15)、式(16)、式(22)代入式(13)中,得到

2.2 导轨系统的线性化
导轨系统的关键参数为油膜厚度变化值e、油腔压力pi、压力补偿器开口度xi,因此基于这些参数对方程进行变换。
式(7)减去式(1),得到


式(21)减去式(18),得到

式(23)减去式(19),得到

式(25)为非线性微分方程,对其进行求解非常困难,因此有必要对其进行线性化处理。
在实际应用中,导轨系统的油腔压力pi、压力补偿器开口度xi变化很小,因此将式(25)中的某部分设定为常数值:

将式(25)变换成Taylor级数的形式,去掉高阶项,得到导轨系统的线性化方程:
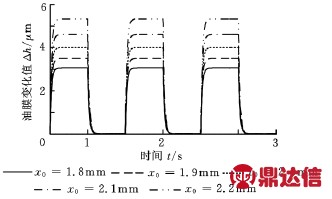
同理,将式(26)变换成Taylor级数的形式,去掉高阶项,得到导轨系统的线性化方程:

2.3 导轨系统的传递函数推导
对式(24)进行Laplace变换[8],得到

代入边界条件,e(0+)=0,e(1)(0+)=0,则式(30)可简化为

同理,对式(28)、式(29)进行 Laplace变换,代入 边 界 条 件,Δxi(0+)= 0,Δx(1)i (0+)=0,Δpi(0+)=0,e(0+)=0。
将式(28)、式(29)代入式(31)中,得到
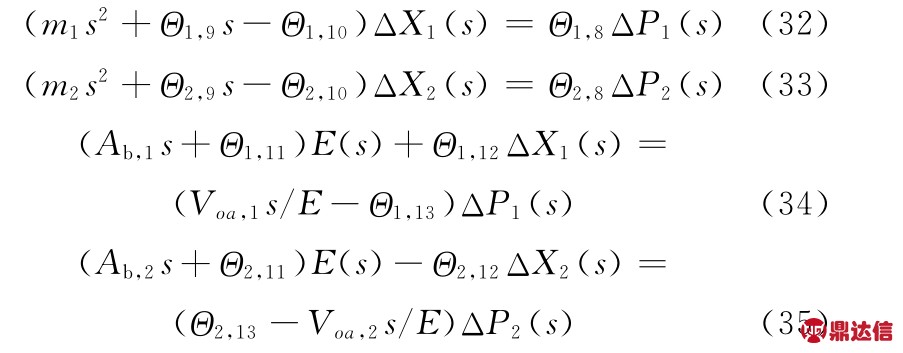
根据式(31)、式(32),计算出油膜厚度变化值e,油腔压力pi压力补偿器的开口度xi:
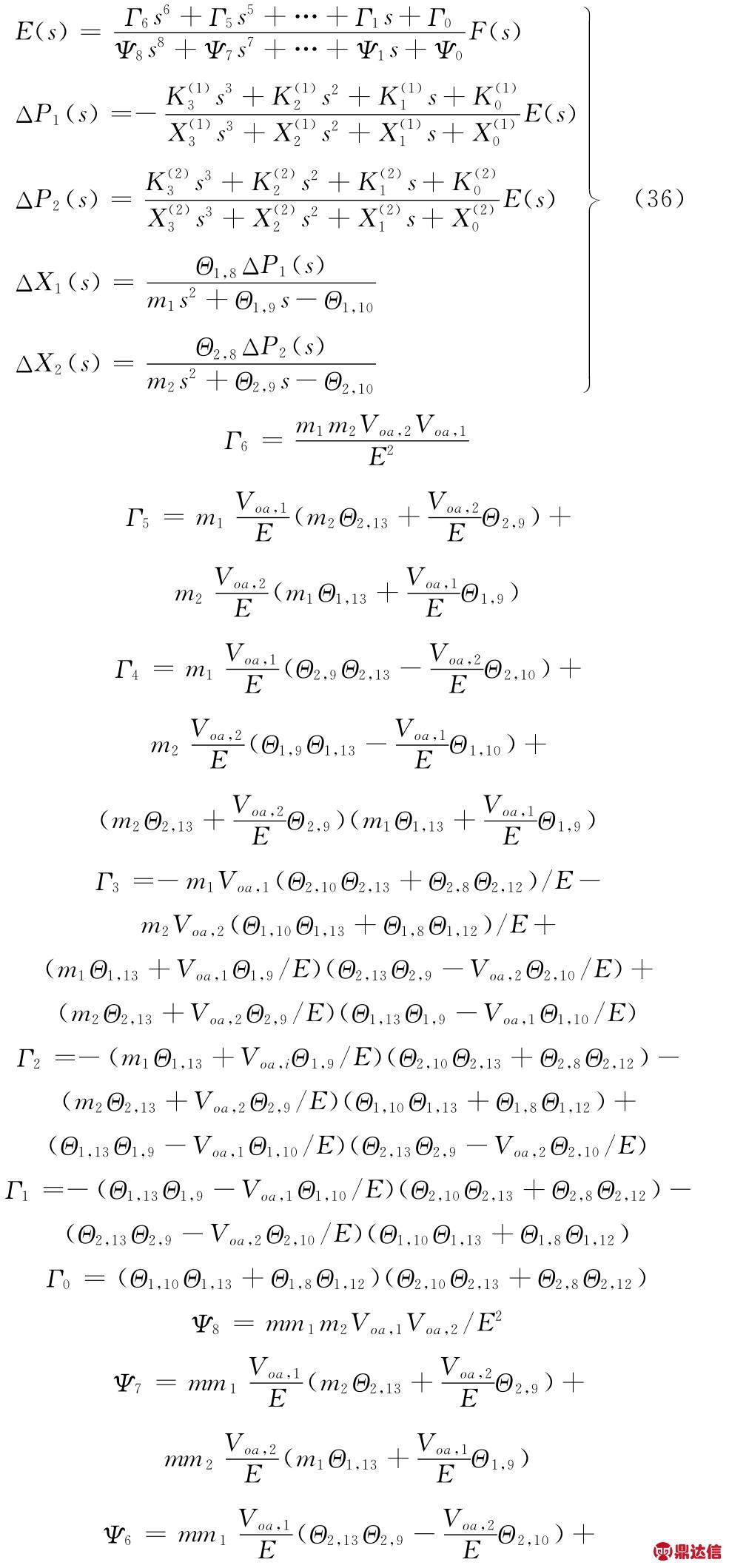
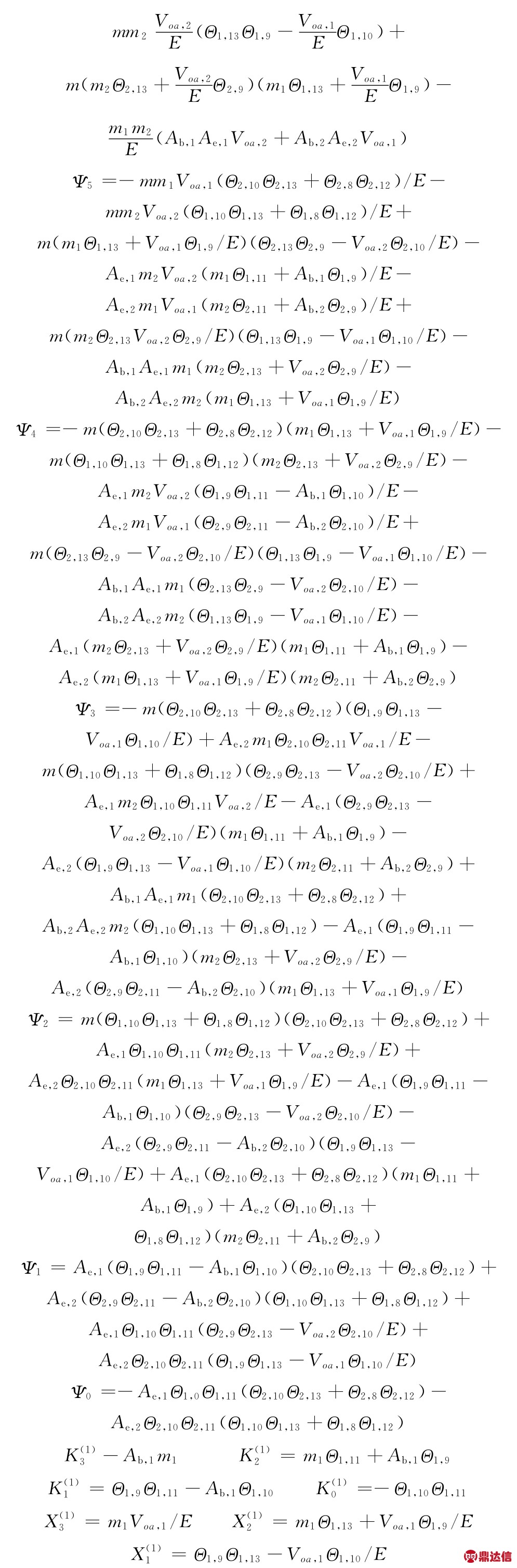
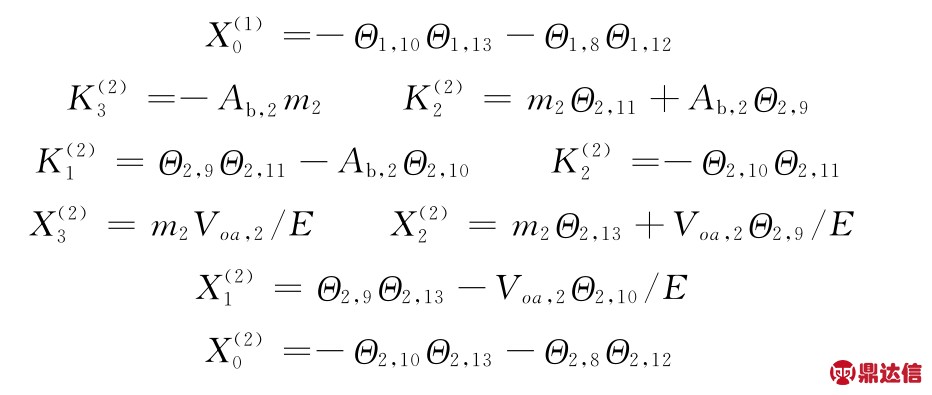
3 导轨系统的动态特性分析
3.1 导轨系统的参数
导轨系统主要由导轨、油腔、流量控制阀、液压泵、溢流阀等组成。导轨的参数如表1所示。
表1 静压导轨的参数
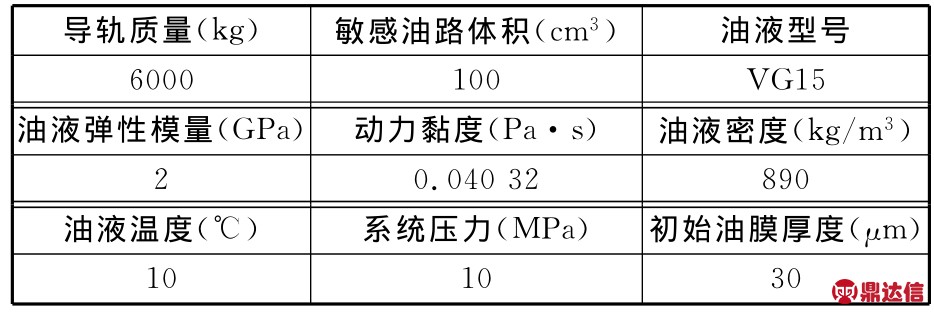
导轨系统有10对相同尺寸的对置静压油腔(即B1=B2,b1=b2,A1=A2,a1=a2),参数如表2所示。
表2 对置油腔的参数
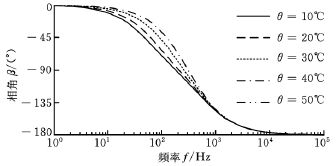
流量控制阀(2FRM型二通流量控制阀)的数量为20,其参数如表3所示。
表3 流量控制阀的参数
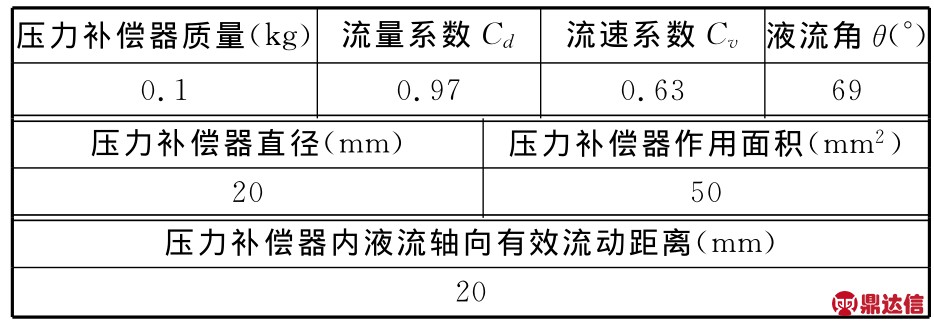
外载荷信号为阶跃载荷F1(kN)、脉冲载荷F2(kN),其数学表达式分别为
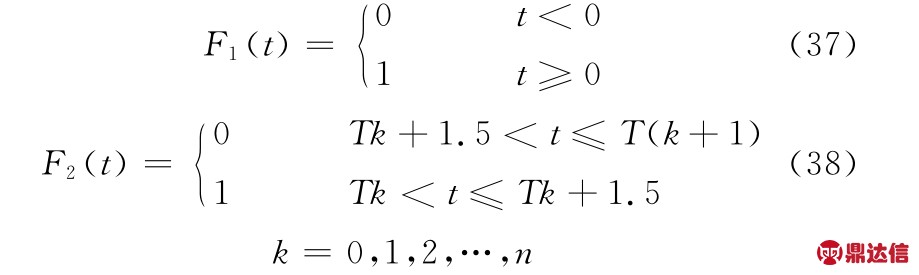
式中,t为时间变量;T=3。
3.2 导轨传递函数的简化
根据式(33),采用表1~表3中的导轨系统的工作参数,利用MATLAB软件计算出传递函数中各系数的数值,Γ0 =6.6460×10-8,Γ1 =2.6131 × 10-11,Γ2 = 3.4828 × 10-14,Γ3 =3.7639×10-18,Γ4 = 3.4077 × 10-21,Γ5 =-7.0699×10-25,Γ6 = 2.5000 × 10-29,Ψ0 =11.4599,Ψ1 =0.2273,Ψ2 =3.4853×10-4,Ψ3 =4.2313 × 10-7,Ψ4 = 1.3933 × 10-10,Ψ5 =7.0386×10-14,Ψ6 = -3.8054×10-18,Ψ7 =-3.7540×10-22,Ψ8 =1.5000×10-26。
流量控制阀调节下的闭式静压导轨系统的传递函数存在6个零点、8个极点,表达式复杂、分析困难。由于Γ6、Γ5、Γ4、Γ3、Γ2、Γ1、Ψ8、Ψ7、Ψ6、Ψ5、Ψ4、Ψ3相对于Γ0、Ψ1、Ψ0 小若干个数量级,使得系统中相应极点在s平面左半部远离虚轴,留数非常小,衰减指数非常大,对系统的影响较小[8]。
闭式静压导轨系统的传递函数G(s)非常复杂,在实际的工程设计、调试及维护过程中,设计人员很难以此为依据,对导轨系统进行设计分析。因此需抓住主要矛盾,忽略次要因素,进行化简,真正为工程设计人员提供理论依据,被工程设计人员灵活应用。
因此对导轨系统进行简化,用惯性环节代替:
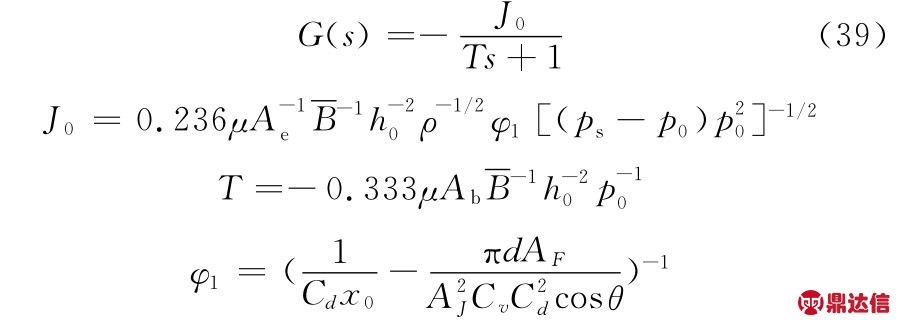
3.3 影响导轨动态性能的参数
根据式(35)可知,导轨的动态性能与油液参数ρ、μ,油腔参数Ae、Ab、B,油膜厚度h0,油压参数ps、p0,流量控制阀参数d、AF、AJ、x0 有关。
导轨系统的较多参数均对动态性能有重要影响。在实际设计、维护中,能够调整且对动态性能有影响的参数有油膜厚度h0、油腔压力p0、流量控制阀初始开口度x0及油液动力黏度η。
为了直观描述各参数对导轨动态性能的影响,依次改变动力黏度μ、初始开口度x0,绘制动态性能与动力黏度、初始开口度之间的关系。
初始开口度x0的变化范围如表4所示。油液牌号为VG15,工作温度为10℃~50℃,黏温特性(动力黏度η和运动黏度ν的变化范围如表5所示。
表4 初始开口度的变化范围

表5 油液的黏温特性表


3.4 导轨动态性能的时域分析
3.4.1 时域内油温对动态性能的影响
令油温由10℃变化至50℃,绘制了不同温度下油膜厚度及油腔压力的阶跃响应曲线,如图3、图4所示。
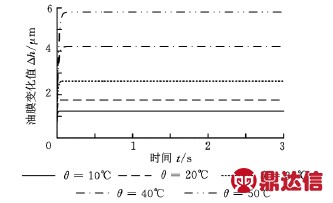
图3 油膜的阶跃响应曲线
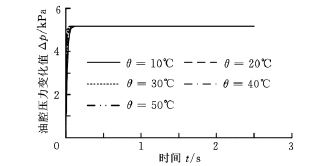
图4 油腔压力变化的阶跃响应曲线
由图3看出,油温为10℃时(对应的油液的动力黏度为40.32×10-3 Pa·s),响应时间为0.02s,油膜的稳态变化值 Δh=1.23μm;油温升高至50℃时(对应的油液的动力黏度降至8.46×10-3Pa·s),响应时间为0.1s,油膜的稳态变化值Δh=5.80μm。随着油温逐渐升高,动力黏度μ逐渐降低,油膜的响应时间延长,稳态变化值Δh增大。
图4所示为不同温度下油腔压力的阶跃响应曲线。由图4看出,当油液温度为10℃时(对应的油液的动力黏度为40.32×10-3 Pa·s),响应时间为0.03s,油腔压力的稳态变化值Δp=5.169kPa;油温升高至50℃时(对应的油液的动力黏度降至8.46×10-3 Pa·s),响应时间为0.1s,油腔压力Δp=5.168kPa。
随着温度逐渐升高,油液动力黏度μ降低,油膜变化值Δh依次增大。动力黏度μ与油膜变化值Δh相互影响,如下式所示:

但二者相互影响,相互作用,反而使得对油腔压力的影响很小,基本可以忽略,因此油腔压力的稳态值基本保持恒定,如图4中曲线所示。
3.4.2 时域内初始开口度对动态性能的影响
调整流量控制阀的初始开口度x0,绘制了不同初始开口度下油膜厚度的脉冲响应曲线,如图5所示。
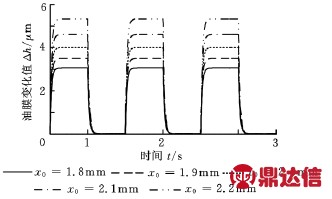
图5 油膜变化值的脉冲响应曲线
由图5看出,当初始开口度x0=1.8mm时,响应时间为0.1s,油膜稳态变化值Δh=3μm;初始开口度为2.2mm时,响应时间为0.1s,油膜稳态变化值Δh=5μm。
根据导轨油膜的数学模型(式(36)),在本范例中流量控制阀初始开口度x0的变化范围内,开口度x0逐渐增大时,φ1增大,增益系数J0逐渐增大,因此油膜变化值Δh逐渐增大。
如图5所示,逐渐增大对置两油腔的流量控制阀初始开口度x0,初始状态下导轨上下油腔油膜越接近等间隙状态,油腔液阻的变化越小,因此油膜变化值Δh随控制阀初始开口度x0增大而增大。
3.5 导轨动态性能的频域分析
3.5.1 频域内油温对动态性能的影响
令油温由10℃变化至50℃,绘制了不同温度下导轨的幅频、相频特性曲线,如图6、图7所示。
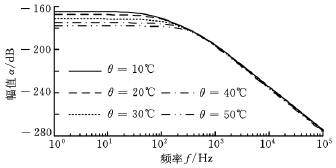
图6 不同温度下导轨的幅频曲线
从图6、图7看出,随着油温升高,导轨的幅值在100~102 Hz范围内逐渐变小,在102~105 Hz范围内变化不大;相角在100~103 Hz范围内逐渐增大,稳定性变好,在103~105 Hz范围内变化不大。
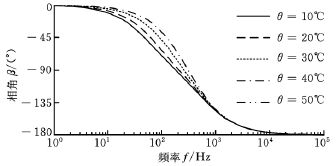
图7 不同温度下导轨的相频曲线
随着油温的升高,动力黏度μ逐渐减小,导轨系统出现幅值减小、相角增大的趋势。
3.5.2 频域内初始开口度对动态性能的影响
调整流量控制阀的初始开口度x0,绘制了不同初始开口度下导轨的幅频、相频曲线,如图8、图9所示。
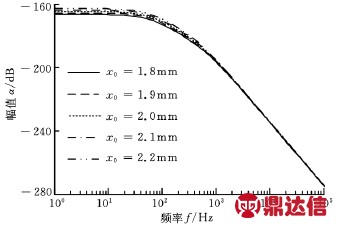
图8 不同初始开口度下导轨的幅频曲线
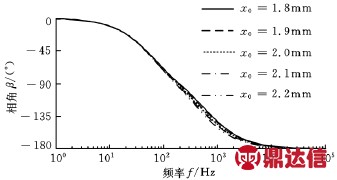
图9 不同初始开口度下导轨的相频曲线
从图8、图9看出,随着流量控制阀的初始开口度x0逐渐增大,导轨的幅值在100~103 Hz范围内变大,在103~105 Hz范围内变小,但变化程度很小;相角在100~102 Hz范围内变化不大,在102~104 Hz范围内减小。
4 结论
(1)液体静压导轨系统可简化为惯性环节,列出了传递函数与各参数的表达式。对动态性能有较大影响的参数有油膜厚度h0、油腔压力p0、流量控制阀初始开口度x0及油液动力黏度μ。
(2)随着油温升高,动力黏度降低,油膜厚度变化值增大,但油腔压力基本恒定;导轨幅值变小,相角变大。因此在油液的工作温度范围内,油温越低,导轨的动态性能越好。
(3)在本文流量控制阀开口度的调节范围内,开口度增大,油膜厚度变化值变大;导轨幅值出现先增大后减小,相角变小的趋势。
(4)综合考虑油温、流量控制阀开口度对导轨动态性能的影响,在实际设计、维护过程中,油温越低,导轨的动态性能越好;改变流量控制阀的初始开口度,可以很好地调整导轨的动态特性。