摘 要:一台导轨磨床工作台导轨副磨损严重,静压润滑系统老化,不能满足工作要求。决定进行改进和维修,采用开式静压导轨结构,采用恒流供油静压润滑系统,选用性能优良的多头泵;对原导轨面进行刮研处理,提高接触精度,减小平面误差。经过改进和维修,磨床工作台恢复原使用性能。改造过程投资少,方案先进,施工方便。
关键词:磨床;静压润滑;改进;维修
某公司一台老式进口导轨磨床,工作台长9 m,宽1.8 m。该机床服役多年,工作台导轨面磨损严重,液压系统零部件老化,原静压系统无法满足机床的正常工作要求。决定对机床工作台导轨副进行改进和维修,提高机床的使用性能。
该机床工作台导轨副为开式静压导轨,工作台导轨面上有12 个油腔,每个油腔对应一个单薄膜反馈节流器,用单独的节流器调整流量,控制压力,将工作台托起,形成油膜间隙。原机床工作台导轨副静压系统如图1 所示。
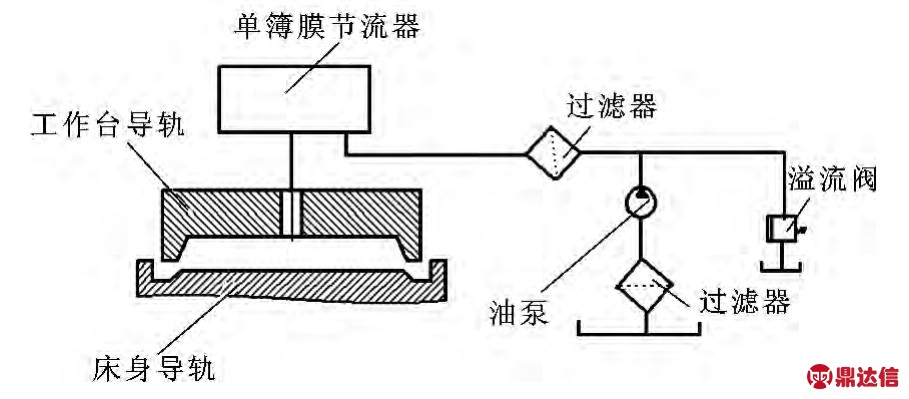
图1 原磨床工作台导轨副静压系统示意图
1 改进方案
1.1 采用开式静压导轨结构
原磨床工作台导轨副是开式静压导轨结构,是否保留这种结构,要经过充分的论证和比较。
开式静压导轨具有较好的承受正方向垂直载荷性能,而承受偏载引起的颠覆力矩的性能较差,适用于载荷比较均匀、偏载引起颠覆力矩影响较小的场合。另外这种结构简单,加工和安装比较方便。而导轨磨床工作台负载较小,载荷分布均匀,磨削量小,负载变化小。其横向颠覆力矩不会很大,而工作台纵向长度较长,可以有效抵消其在这个方向的颠覆力矩。因此决定保留原导轨副结构,采用开式静压导轨副结构。
1.2 采用恒流供油静压润滑系统
磨床工作台与床身导轨之间采用流体静压润滑系统,用油泵将润滑油送入到导轨面之间的油腔里,润滑油将工作台托起,润滑油在其间隙里形成压力油膜,使工作台和床身导轨面完全隔开,实现完全液体润滑。
该磨床原工作台导轨静压润滑系统已老化,需拆除,决定采用恒流式供油静压润滑系统。
恒流式供油静压润滑系统是润滑供油系统的油泵将润滑油供给多头泵,多头泵将润滑油定量送入工作台导轨上的油腔里,系统中没有节流器,故是全流量供油,供油压力与油腔压力一致,进入油腔里的润滑油通过导轨间隙向外流出,回到油箱。油腔里的油将工作台托起,与床身导轨之间形成油膜间隙,当载荷增大,工作台下沉,与床身导轨面间隙变小,油流出导轨间隙的阻力增大,由于是定量供油,油腔压力与油膜厚度的立方成反比,所以油腔润滑油压力又增大,工作台又浮起,直至与载荷平衡为止。图2 为恒流供油系统示意图。
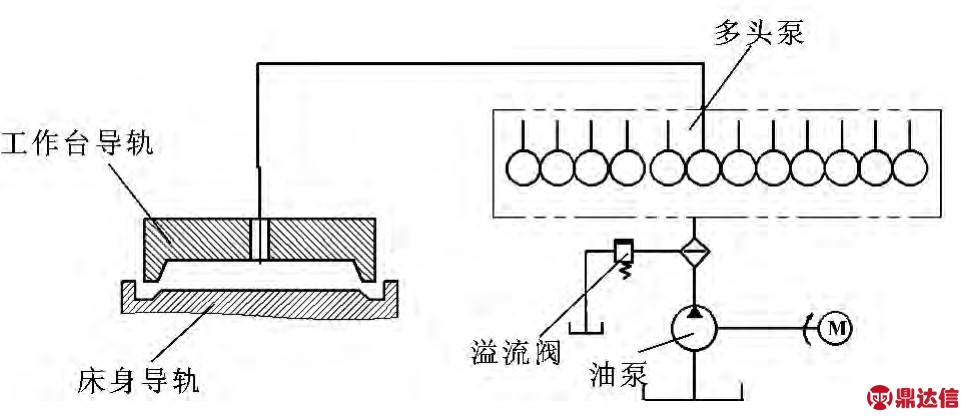
图2 恒流供油系统示意图
恒流供油静压系统是在全流量下工作,没有压力降,多头泵供油没有溢流,故温升小,有利于减小导轨的热变形;恒流供油静压系统压力储备大,过载保护能力强,系统中没有节流器,不存在节流器堵塞、使油腔失压的危险,所以工作可靠稳定。采用多头泵,实现每个油腔都用一个定量泵供油,确保供给油腔的润滑油量为一定值。因此,恒流供油静压系统导轨,不仅压力储备大,过载保护能力强,刚度高,工作可靠稳定,而且调整和维护简单方便,适用于低速重载的机床。所以该磨床工作台导轨采用恒流式供油静压系统。
1.3 多头泵的选择
多供油点的供油方式使用多供油点的油泵叫多头泵,这种供油方式和油泵已广泛应用于重型机床的导轨上,使原来所采用的单泵供油方式获得新的发展和应用。恒流供油方式,通过使用多头泵来保证每个供油点供应量一致。采用多头泵供油的静压导轨,可以保证恒定的油膜压力,随不同负载可以自动调节,因此无论零件轻重如何,均可获得稳定的加工精度。
经过计算和分析比较,决定选用多头泵型号为BCD-A12200,12 个供油点,单头流量200 mL/min。
2 导轨和油腔的维修
该磨床工作台导轨和床身导轨均存在一定的磨损,于是进行维修:
(1)对导轨接触面进行刮研处理,保证接触均匀,接触精度为大于12 点/25 mm2,刮研深度在0.006~0.01 mm 内。
(2)保证导轨平面间隙均匀,控制工作台导轨平面度误差,要求误差在0.01~0.02 mm 内,即应小于工作台浮起量。
(3)修整工作台导轨面上的油腔,刮研油腔槽,保证油腔槽的深度,强化润滑油的流动,实现较好的润滑效果。
3 结束语
通过工作台导轨副静压润滑系统的改进,采用恒流式供油方式,使工作台运行稳定可靠,加工精度得到改善。对导轨面和油腔油槽进行维修,恢复了机床零件的工作性能,使一个服役多年的机床又发挥作用。该改进项目,方案先进、可行,投资少,效果明显。