摘要:基于等效单自由度模型自主研发了滑动结合面动态特性参数识别试验台,对不同类型的滑动结合面进行参数识别试验,得到了结合面的动刚度,并分析了滑动速度、面压、介质等因素对刚度的影响规律。分析结果表明:滑动速度的增大会降低结合面的动刚度;适当增大面压可提高结合面的动刚度,且能降低速度增大对动刚度的影响;添加润滑油能使结合面的动刚度提高20%左右;贴塑导轨比普通金属导轨能更好地维持结合面动刚度的稳定性,其动刚度随速度的变化在25%左右。
关键词:滑动导轨;结合面;动刚度;动压润滑
0 引言
机床中各类结合面的动态特性对整机动力学性能都有着重要影响[1-2],动载荷下抵抗变形的能力称为动刚度,结合面的存在会降低结构的局部刚度,直接影响结构的机械性能。随着先进制造技术的发展,结合面间的动态特性及参数识别研究越来越受到各国学者的重视。目前,国内外对固定结合面[3-5]和滚动结合面[6-7]动态特性的理论和试验研究比较多,而对滑动结合面的研究较少。滑动导轨作为机床上使用最广泛的导轨,其结合面动态特性参数的研究对提升高精度数控机床的设计水平和制造水平具有重要意义。
为了研究不同条件下滑动导轨结合面的动力学特性,本文分析了影响滑动结合面动态特性的因素,并在自主研发的滑动结合面动态特性测试系统上以各种滑动导轨为测试对象进行了大量试验,获取了多种滑动结合面的动态特性参数,分析了滑动结合面动态特性参数随其影响因素的变化规律,为高精度数控机床的设计提供了依据。
1 试验原理与方法
1.1 试验原理
典型的滑动导轨结合面构成如图1所示,滑块和固定导轨配合形成滑动结合面,导轨与基础之间为螺栓连接。滑动结合面的接触刚度相对于固定结构(基础)的刚度较低,振动时结合面的变形远大于固定结构自身的变形,因此可以将固定结构近似为刚体,滑块看作质量块,滑动结合面便可等效为刚度为k、阻尼为c的弹簧阻尼器。
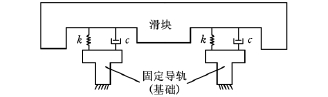
图1 滑动导轨结合面示意图
由于结合面本身存在一定的几何形状误差及微观不平度,而且结合面间可能存在介质等,所以当受到外加复杂动载荷作用时,结合面间会产生微小的相对位移或转动,使结合面既存储能量又消耗能量,表现出既有弹性又有阻尼的特性,这就是等效动刚度和阻尼。
假设滑块的质量为m,k和c分别为滑动导轨结合面的等效动刚度和阻尼,x(t)和y(t)分别是滑块和基础的位移,p(t)为滑块所受外力,基础位移影响弹簧和阻尼器的受力状况,为了消除基础位移的影响,根据单自由度系统理论,其振动方程可以表示为

对式(1)作以下变换构成单自由度振动方程:

在简谐激振力作用下,p(t)、x(t)和y(t)可表示为p(t)=Pejωt,x(t)=Xejωt,y(t)=Yejωt。将以上三项代入式(2)可得

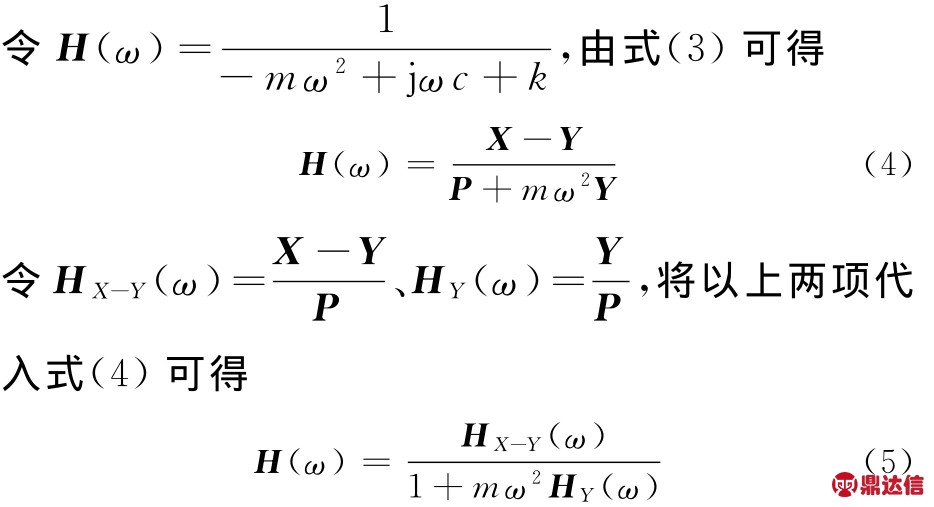
其中,HX-Y(ω)为运动部件频响函数与基础频响函数矢量差,HY(ω)为基础频响函数,二者可由实测数据计算得到。
由以上推导过程易知,H(ω)是一个等效单自由度系统的频响函数。在单自由度系统的固有频率处,质量块的振幅达到峰值,相位由0°变到-180°,激励与响应间的相位差为90°。由测量所得的频响函数曲线可识别出系统的固有频率ωn,然后根据k=mω2n求出滑动导轨结合面的动刚度。这种识别方法消除了基础位移对试验的影响,更符合实际,识别出的参数精度高且具有理论依据。
日本学者Yoshimura等[8]在对机床动力学特性的研究文献中提出:在结合条件相同的情况下,只要平均接触压力相同,结合面单位面积的动态特性参数是相同的。为了使数据具有通用性,求出单位面积的动刚度ke=k/s,其中,s为滑动结合面的接触面积。
1.2 试验装置及方法
本文主要通过单因素试验分析滑动速度、面压、润滑油黏度、是否贴塑等各因素对滑动结合面动刚度的影响规律,各影响因素的取值情况见表1。
表1 滑动结合面动态特性的影响因素
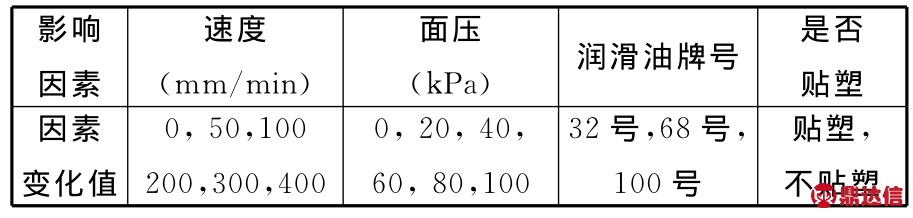
滑动导轨结合面动态特性参数的识别试验是在自主研发的测试系统上进行的,试验装置构成如图2所示。测试装置采用直流可调速电机驱动滚珠丝杠,丝杠螺母连接滑块,通过直流调试器改变电机转速以调节滑动速度,激振器连接在滑块支架上对系统进行激振。
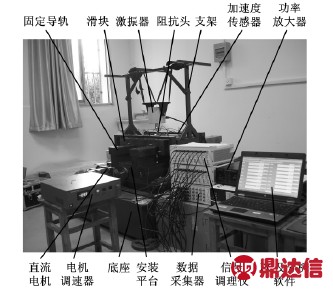
图2 测试装置实物图
试验过程中,采用M18螺栓对滑块进行法向加载,扭矩由扭矩扳手测量。图2中,数据采集器发出的扫频信号经功率放大器放大后作用于激振器,激振器连接阻抗头并对试验台激励。力信号由阻抗头拾取,加速度信号由加速度传感器测得,两者经电荷放大器转变为适量大小的电压信号,并由数据采集器采集。计算机最终得到的是经数据采集器模数转换后的力和加速度,通过模态分析软件进行傅里叶变换后即可得各测点频响函数,然后根据MATLAB程序可计算出结合面的单位面积等效动刚度。
图3所示为MATLAB程序识别过程中的幅值和相位曲线,在振动幅值最大处,激励和响应相位差为90°。
2 试验结果与分析
2.1 滑动速度对滑动结合面动刚度的影响
滑动导轨低速运行时易产生爬行现象,而提高滑动速度可避免这一现象,且导轨在不同的滑动速度下稳定性也不同,因此滑动速度是影响结合面动态性能的重要因素之一。图4表明了滑动速度对结合面动刚度的影响规律。
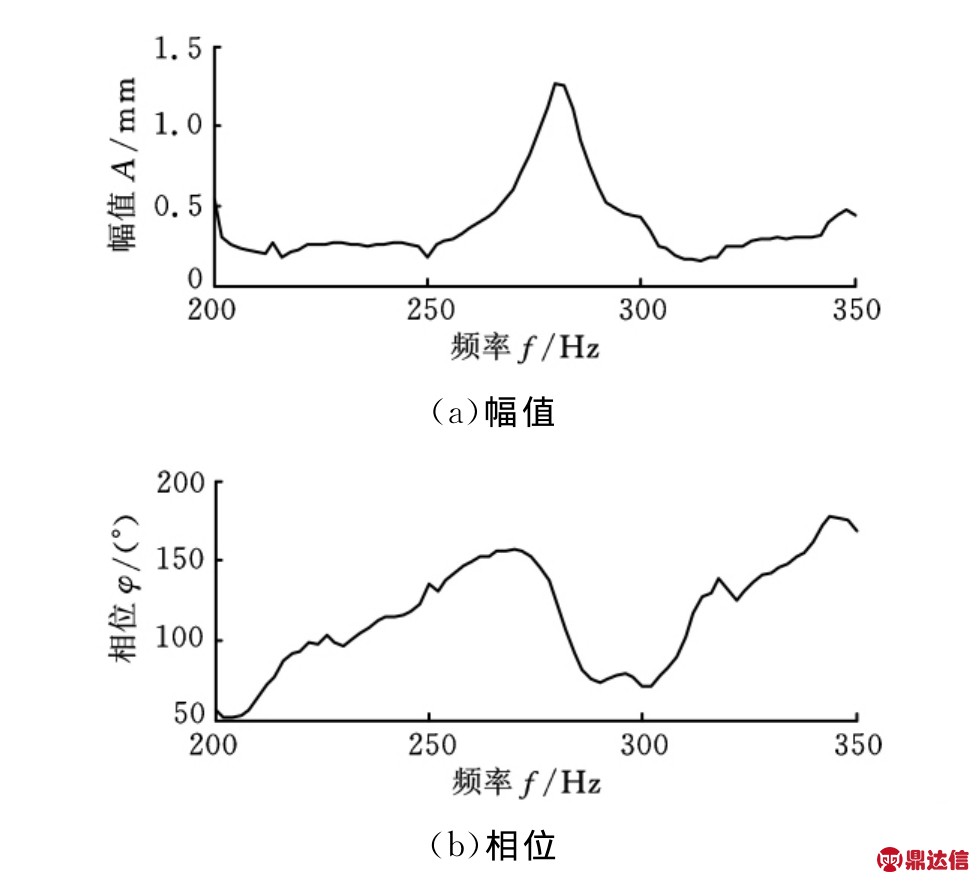
图3 MATLAB识别曲线
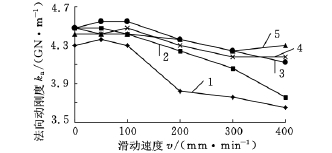
图4 滑动速度对结合面动刚度的影响
1.p=0 2.p=40kPa 3.p=60kPa 4.p=80kPa 5.p=100kPa
从图4可以得出,滑动结合面的动刚度随着速度的增大而减小,面压p不同,其降低幅度也不同。当速度从0增大到400mm/min,面压为0时,结合面动刚度下降14%,而面压为100kPa时的结合面动刚度仅下降6%。另外,当面压较大时,速度达到300mm/min以后结合面动刚度还略有增大。
滑动导轨表面实际上是粗糙不平的,滑动结合面在静止状态下的接触实际上是两个粗糙表面微凸体的接触,粗糙表面上的微凸体是随机分布的,只要结合面的面积确定,则实际接触面积也就确定且不随着滑块位置的改变而改变。当滑块运动时,两接触表面上的微凸体形成新的接触对,同时破坏旧的接触对。在形成接触对的过程中,两微凸体接触的面积是逐渐增大的,而当破坏接触对时,接触面积是逐渐减小的,因此在形成接触对和破坏接触对同时进行时,其接触面积比原来相对减小,即运动的滑动结合面在单位时间内实际接触面积比静止状态小。滑动速度越大,形成和破坏接触对的过程越剧烈,其动刚度也越小。所以当图4中面压较大,速度达到300mm/min以上时,结合面动刚度略有增大,这是由于结合面间出现动压润滑状态,形成了润滑油膜。
2.2 面压对滑动结合面动刚度的影响
对机床而言,安装在导轨上的运动部件重量各异,而且加工工件重量及切削力也会发生变化,因此滑动导轨结合面所受的外加载荷是不断变化的,分析面压对滑动结合面动态特性的影响具有重要意义。图5所示为结合面动刚度随面压的变化规律曲线。
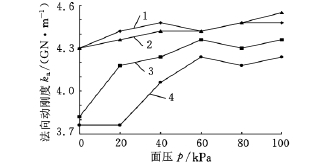
图5 面压对结合面动刚度的影响
1.v=0 2.v=100mm/min 3.v=200mm/min 4.v=300mm/min
从图5可以看出,滑动结合面的动刚度随着面压的增大而增大,且当面压增大到60kPa以后,面压的增大对动刚度的变化影响变小。另外,滑动速度越大,面压对动刚度的影响越大,滑动速度为0和100mm/min时,动刚度变化在5%左右,而速度增大到300mm/min后,动刚度变化达到15%。
滑动结合面的实际接触是两个粗糙表面上微凸体的接触,其实际接触面积的大小取决于发生接触微凸体的数目和接触点的面积大小。当面压较小时,滑动结合面间的接触仅仅发生在少数较高的微凸体顶端之间,此时相互接触的微凸体数目较少,而且各接触点的面积也较小,所以结合面的实际接触面积较小,其抵抗法向变形的能力较弱,即结合面动刚度较小。随着面压的增大,发生接触的微凸体数目增加,已接触的微凸体也会进一步变形,结合面的实际接触面积增大,从而其抵抗变形的能力增强,即结合面的动刚度增大。当面压增大到一定值时,两结合表面的微凸体已达到一定程度的形变,继续增大面压对微凸体的接触状态改变不大,故此时面压的增大对结合面动刚度的影响较小,动刚度变化曲线也就如图5所示趋于平缓。
2.3 润滑介质对滑动结合面动刚度的影响
滑动导轨工作过程中,滑块相对导轨往复滑动,润滑油是不可或缺的。润滑油在导轨和滑块之间形成油膜,把两者隔开可大大减小摩擦力。另外,润滑油还具有抗氧化、抗腐蚀、防锈及防爬性能。试验中测试了不同黏度的导轨润滑油对滑动结合面动刚度的影响规律,如图6所示。
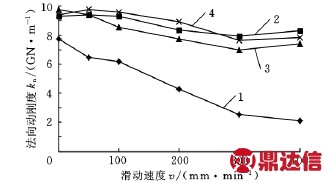
图6 润滑油黏度对结合面动刚度的影响
1.无介质 2.32号导轨油 3.68号导轨油 4.100号导轨油
由图6可知,当其他条件相同时,润滑状态下的结合面动刚度比干摩擦状态下的动刚度大,可提高20%左右,而且在润滑状态下,滑动速度对动刚度的影响比干摩擦时小。当速度由0增大到400mm/min时,干摩擦结合面的动刚度下降约70%,而润滑状态的结合面动刚度仅下降20%左右,这说明润滑油能够有效地维持结合面动刚度的稳定。比较图6中32号、68号、100号不同黏度润滑油对结合面动刚度的影响,其变化规律基本一致,这说明润滑油黏度对结合面动刚度的影响较小。
从润滑机理分析,存在润滑油的滑动结合面会形成两种性质不同的吸附膜:一种是物理吸附膜,即润滑油中的极性分子在范德华力的作用下吸附到导轨表面,形成定向排列的分子层吸附膜;另一种是化学吸附膜,主要靠润滑油中极性分子的有价电子与导轨表面的金属电子发生交换而产生化学结合力。从微观上分析,滑动结合面的接触表面并不是光滑的平面,凹凸不平的接触面内会储存润滑油,当滑块滑动且达到一定速度时,必然会产生微观动压润滑现象。微观动压润滑形成的油膜隔开了滑动导轨上下表面,避免了导轨与滑块的直接接触,物理吸附膜、化学吸附膜则提高了润滑油膜的承载能力,从而增大了导轨结合面的动刚度。
2.4 贴塑对滑动结合面动刚度的影响
贴塑导轨是一种金属对塑料摩擦接触形式的导轨,一个滑动面贴有一层抗磨软带,通常是PTFE(聚四氟乙烯),另一个滑动面是金属面。贴塑导轨具有良好的摩擦特性,可保证较高的重复定位精度,满足微量进给时无爬行的要求。与普通滑动导轨相比 ,它还具有寿命长、结构简单、成本低、使用方便、吸振性好等优点,因此越来越广泛地应用于实际生产中。图7表明了贴塑结合面的动刚度与金属结合面动刚度的变化规律。
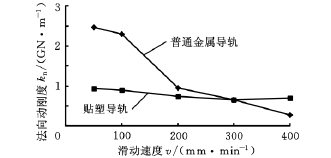
图7 贴塑对结合面动刚度的影响
从图7可以看出,在滑动速度较小的情况下,贴塑结合面的动刚度比金属结合面的动刚度要小得多,随着滑动速度的增大,两种结合面的动刚度都逐渐减小,但贴塑结合面的动刚度变化幅度要比金属结合面动刚度变化幅度小。当滑动速度由50mm/min变化到300mm/min时,金属结合面动刚度减小了将近80%,而贴塑结合面动刚度仅减小了25%左右。当滑动速度增大到400mm/min时,金属结合面的动刚度继续减小,而贴塑结合面的动刚度略有增大,这说明贴塑结合面在400mm/min的速度下已形成动压润滑状态。
之所以出现上述情形,是因为贴塑导轨表面的PTFE软带受压时,弹性变形较大,导致其动刚度比金属结合面动刚度低,但PTFE软带能更容易地将承受的负荷均匀地分布于受压表面,增大结合面的真实接触面积。PTFE软带质地较软,能吸收金属微粒,从而保护配对金属表面,改善导轨因受力变形引起的局部过压状况,使导轨磨损均匀,结合面的动刚度变化也比较稳定。此外,贴塑导轨结合面更容易形成动压润滑状态,这对于高速工作下的滑动导轨动态性能的稳定有很大帮助,因此贴塑导轨越来越广泛地应用于数控机床中。
3 结论
(1)滑动速度的增大会降低滑动结合面的动刚度。当面压较大或结合面间存在润滑油时,该变化趋势比较平缓,而结合面处于低面压或干摩擦状态时,该变化则比较明显。
(2)适当增大面压有助于提高滑动结合面的动刚度,但当面压增大到一定程度时,动刚度的变化便趋于稳定。
(3)结合面间存在润滑油可有效改善其动刚度的稳定性,且滑动速度越大,润滑油的改善效果越明显。当速度由0增大到400mm/min时,干摩擦状态的结合面动刚度下降70%,而润滑状态的结合面动刚度仅下降20%左右。
(4)贴塑导轨结合面的动刚度比金属副导轨结合面的动刚度小,但贴塑导轨具有更稳定的动态特性,且更容易形成动压润滑状态。当滑动速度由50mm/min变化到300mm/min时,金属结合面的动刚度比原来减小了将近80%,而贴塑结合面动刚度仅减小了25%左右。