摘 要:汽车座椅导轨在不确定外载荷作用下,导轨内的滚珠和导轨之间不断发生压紧和分离的交替运动,若对滚珠的预压量不当,则在汽车行驶的过程中会产生异响。为了确定合理的预压量,基于Hyperworks仿真软件,将内外导轨和滚珠的接触关系用弹簧-阻尼单元代替。对导轨施加一定激励,可得到该单元节点处的相对位移,在此基础上对位移的大小进行统计学研究,最终得出合理的导轨预压量为0.21 。
关键词:汽车座椅导轨;弹簧-阻尼单元;相对位移;统计学;预压量
随着人们对于汽车乘坐舒适性要求的提高,汽车座椅导轨作为座椅与车身之间的连接部件,其异响问题受到各大汽车厂商的重视。座椅内外轨之间存在4条沟槽,沟槽内由保持架固定若干滚珠,内外导轨同时承载着座椅与乘客的重量和车身传给它的路面随机激励,因此导轨内滚珠与内外轨之间的结合部位将是振动噪声产生的主要来源。
一直以来,人们对汽车座椅导轨异响问题进行了大量研究,文献[1]采用振动传递路径分析方法对座椅导轨的振动问题进行了研究,文献[2]利用测试手段和动态仿真相结合的方法,对某汽车的悬置系统进行了改进,以减少座椅导轨的异响,文献[3]提出了从舒适性角度对座椅的振动噪声进行评价的几种方法,这些研究工作虽在一定程度上减少了噪声的产生,但没有从根本上解决导轨的异响问题。目前,诸多座椅厂均是采用对导轨进行预压的方法,来减少导轨的异响,但预压量却往往是依靠经验数据,且由于滚珠位置处于导轨内部,难以用实验测量的方法精确获取导轨结合部滚珠的变形量,异响问题仍未从根本上得到解决。
本文采用弹簧—阻尼单元来代替导轨内滚珠与内外轨的接触关系,以该单元两端点之间的相对位移来近似模拟导轨内部滚珠的挤压和分离状态,并利用Hyperworks软件进行动力学仿真分析,获取导轨内的所有弹簧—阻尼单元的相对位移并进行统计学分析,最后根据导轨与滚珠的间隙分布情况,确定合理的预压值,进而从根本上减少导轨异响问题。
1 导轨结构及计算机建模
1.1 导轨结构
导轨的结构由外轨、内轨(滑块)、滚珠、滚珠保持架、卡位装置等组成,如图1所示。内轨通过导轨沟槽内的滚珠安装在外轨上;保持架用于固定各滚珠之间的相对位置,也用于保证内轨滑动过程中滚珠有序滑动,同时也能防止滚珠从沟槽内滑出;内外轨两端都有凸起限位结构,防止内外轨错位严重保持架滑出沟槽。
从宏观上看,内外导轨和滚珠的结合面是光滑的。但实际上,其表面却是凹凸不平的,在正压力下,表面上这些凹凸体中,峰顶较高的率先发生接触,产生弹性变形,当压力增大时,较低的峰点便开始相互接触,原来已经发生弹性变形的峰点随着变形量的加大,会继续发生塑性变形,这样结合面始终表现为弹性变形和塑性变形混合交织的状态[4],从而使结合面表现出既有刚度又有阻尼[5],这为本文采用弹簧—阻尼单元来替代滚珠与导轨的连接关系奠定了理论基础。
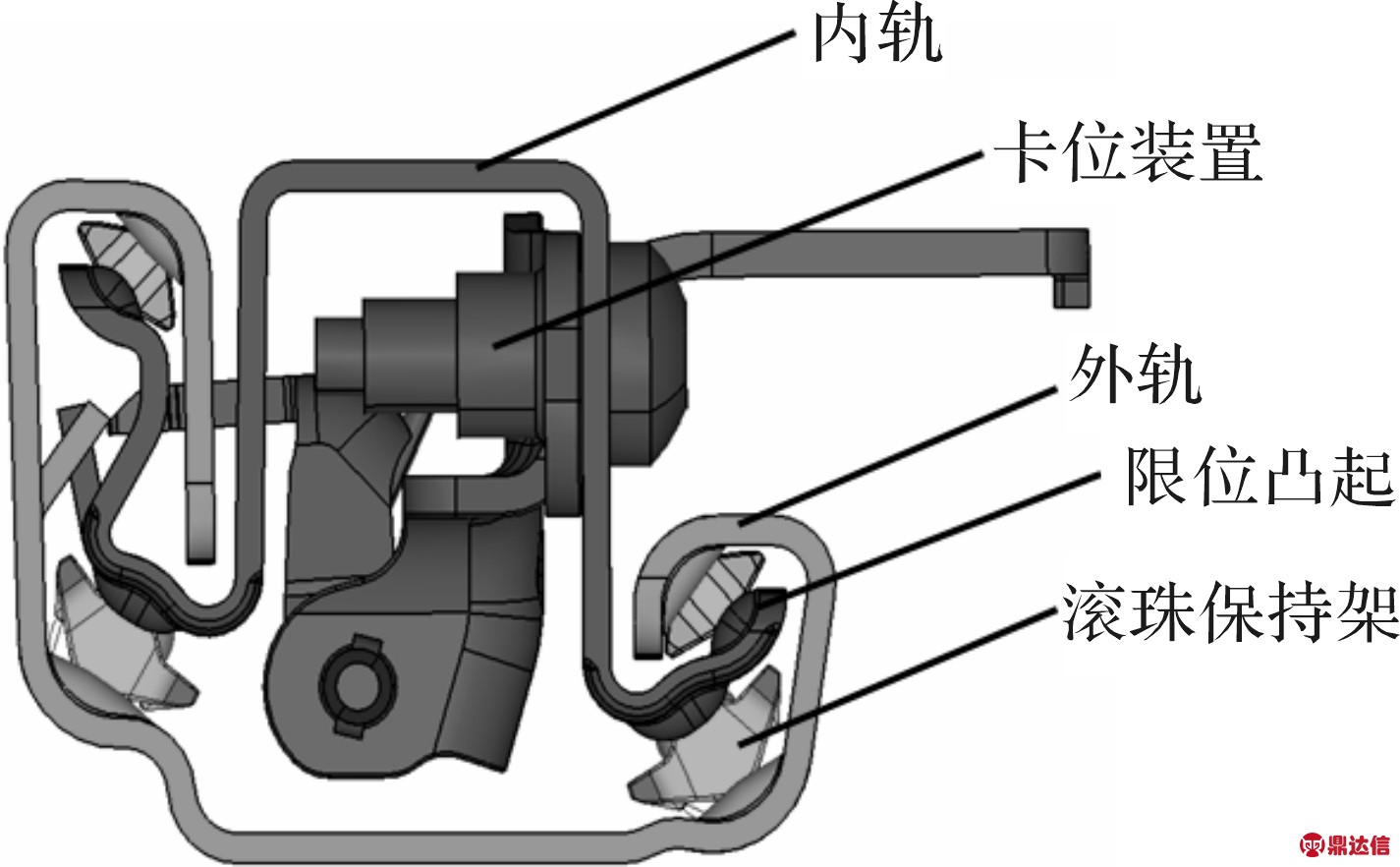
图1 汽车座椅导轨剖面图
1.2 导轨有限元模型
汽车座椅导轨有限元模型利用计算机软件Hyperworks[6]进行创建,导轨整体采用CQUAD4单元进行建模,导轨模型的相关材料和尺寸如表1所示。
表1 导轨模型尺寸和材料参数
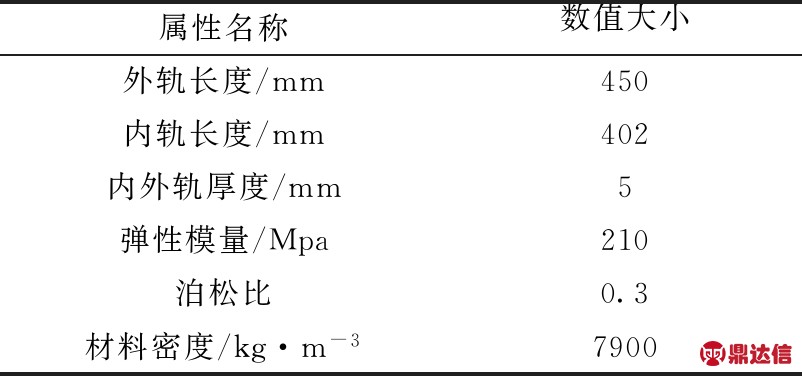
根据滚珠在导轨中的位置,可将其分为4组,根据导轨中各组内实际的滚珠数目,在创建模型的过程中,在导轨模型第1组和第4组的相应位置分别嵌入6个弹簧-阻尼单元,第2组和第3组位置分别嵌入4个弹簧-阻尼单元,如图2所示。
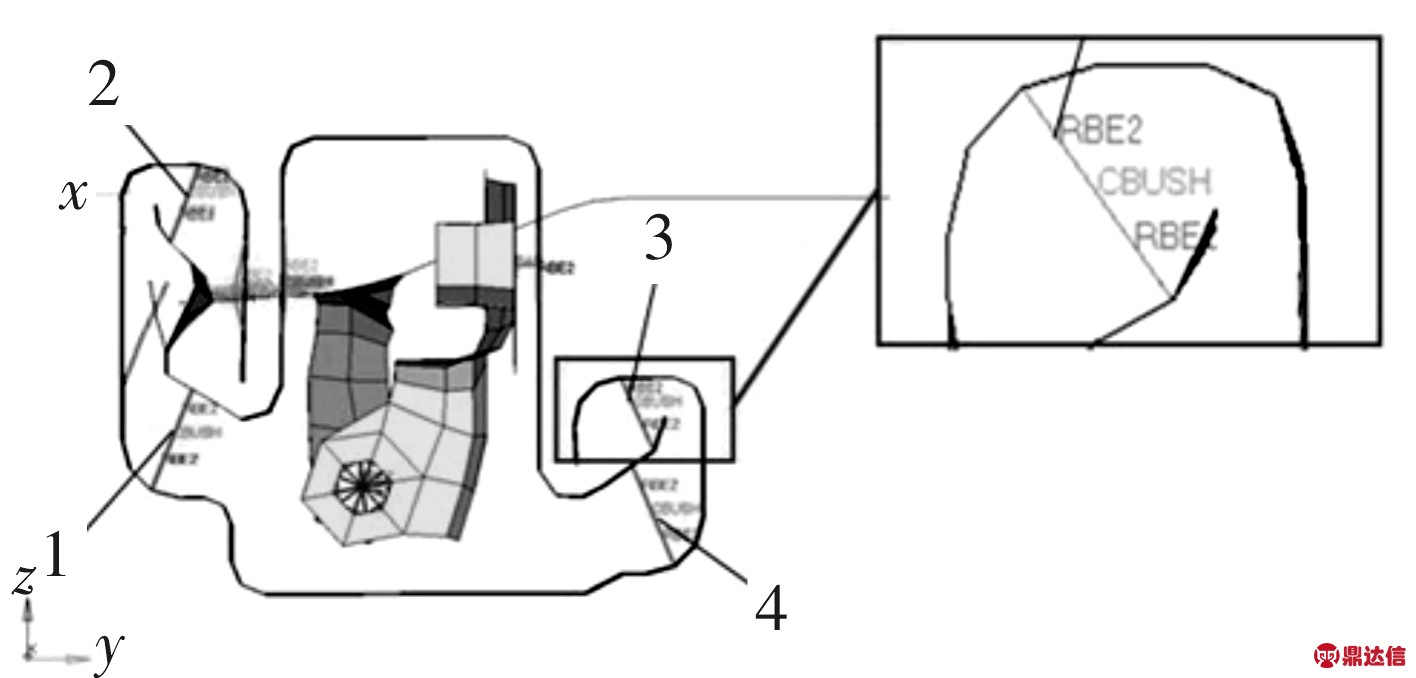
图2 导轨模型内部滚珠位置示意图
1.3 刚度和阻尼参数的获取
导轨接触部位的刚度和阻尼值对导轨整体刚度和变形有较大影响。采用文献[7]的方法,对某型号汽车座椅导轨截面滚珠接触部位的动力学参数刚度和阻尼进行识别,结果如表2和表3所示。并将得到的刚度和阻尼参数赋给相应位置的4组弹簧-阻尼单元。
表2 弹簧-阻尼单元的刚度识别结果 /N·m-1
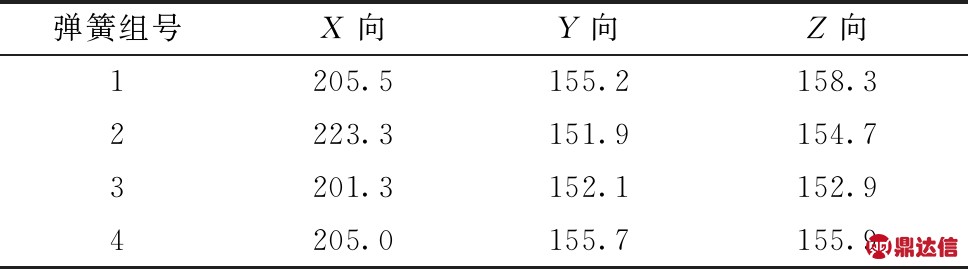
表3 弹簧-阻尼单元阻尼识别结果 /N·m-1
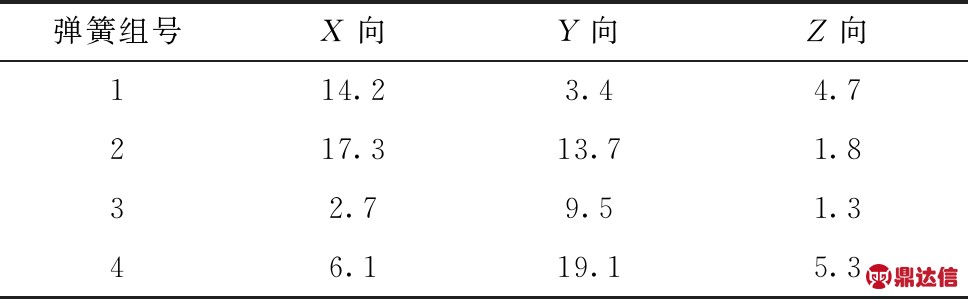
1.4 接触部位间隙的定义
在有限元软件中,建立弹簧-阻尼单元时选择两个相互重合的节点作为该单元的两个端点,这样可更直观的考察间隙值,将弹簧两端点相对位移量在结合部公法线方向上的分量定义为间隙。若两端点反向分离则定义为出现间隙;若两端点相向重合则定义为压紧,即不出现间隙,其间隙值的计算如式(1)所示,间隙示意图如图3所示。
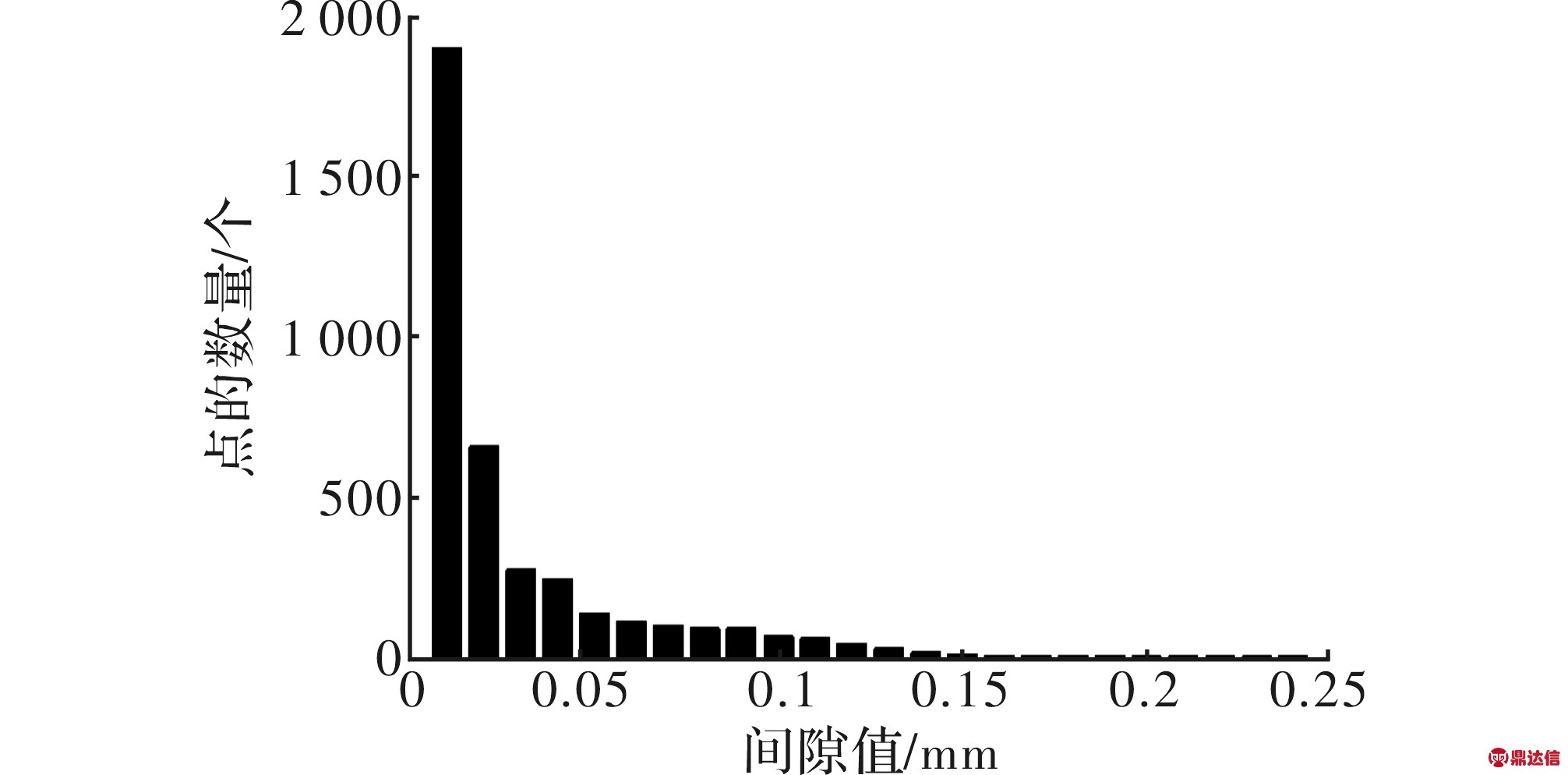
(1)
其中,分别代表CBUSH单元两端点位移量;N为CBUSH单元的个数。
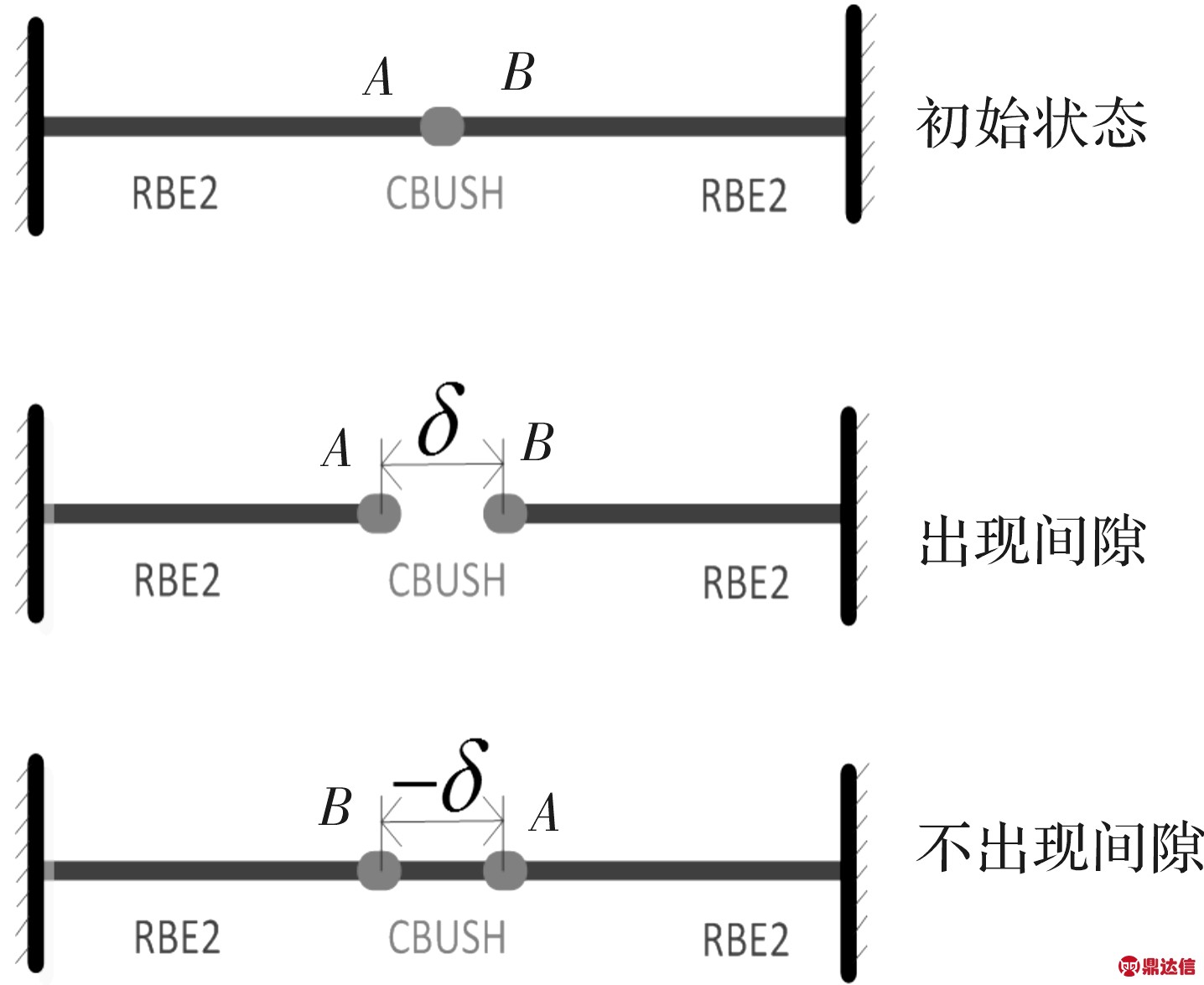
图3 间隙示意图
2 有限元仿真分析及结果评价
2.1 有限元仿真流程
为简便起见,将座椅自重和乘客的重量简化为对导轨所施加的垂向载荷,由于相位差对振幅影响很小,所以在安装点处采用相同的激励信号,未考虑激励信号相位差的影响,垂向载荷和激励的施加位置如图4所示。将采集得到的实际路谱信号作为瞬态激励信号,如图5所示。对导轨模型进行瞬态动力学仿真分析。
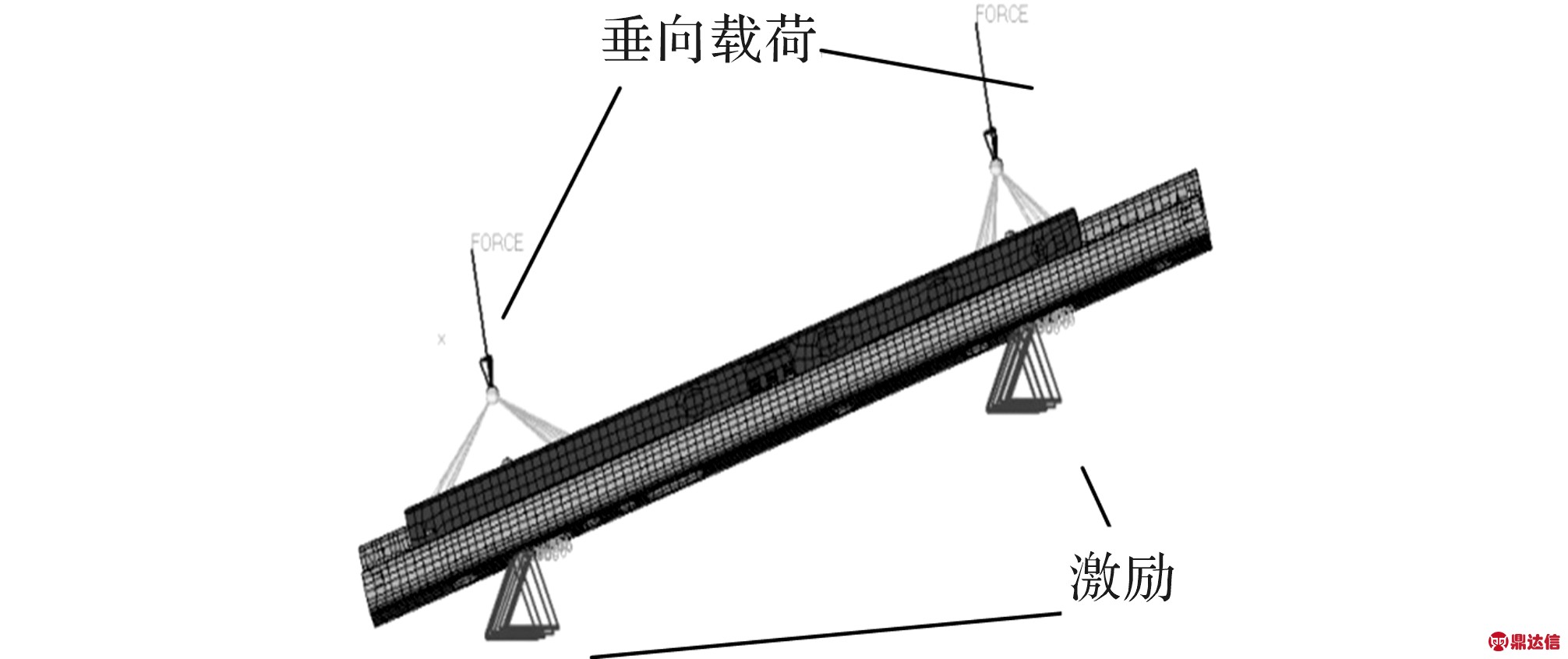
图4 垂向载荷和激励施加位置示意图
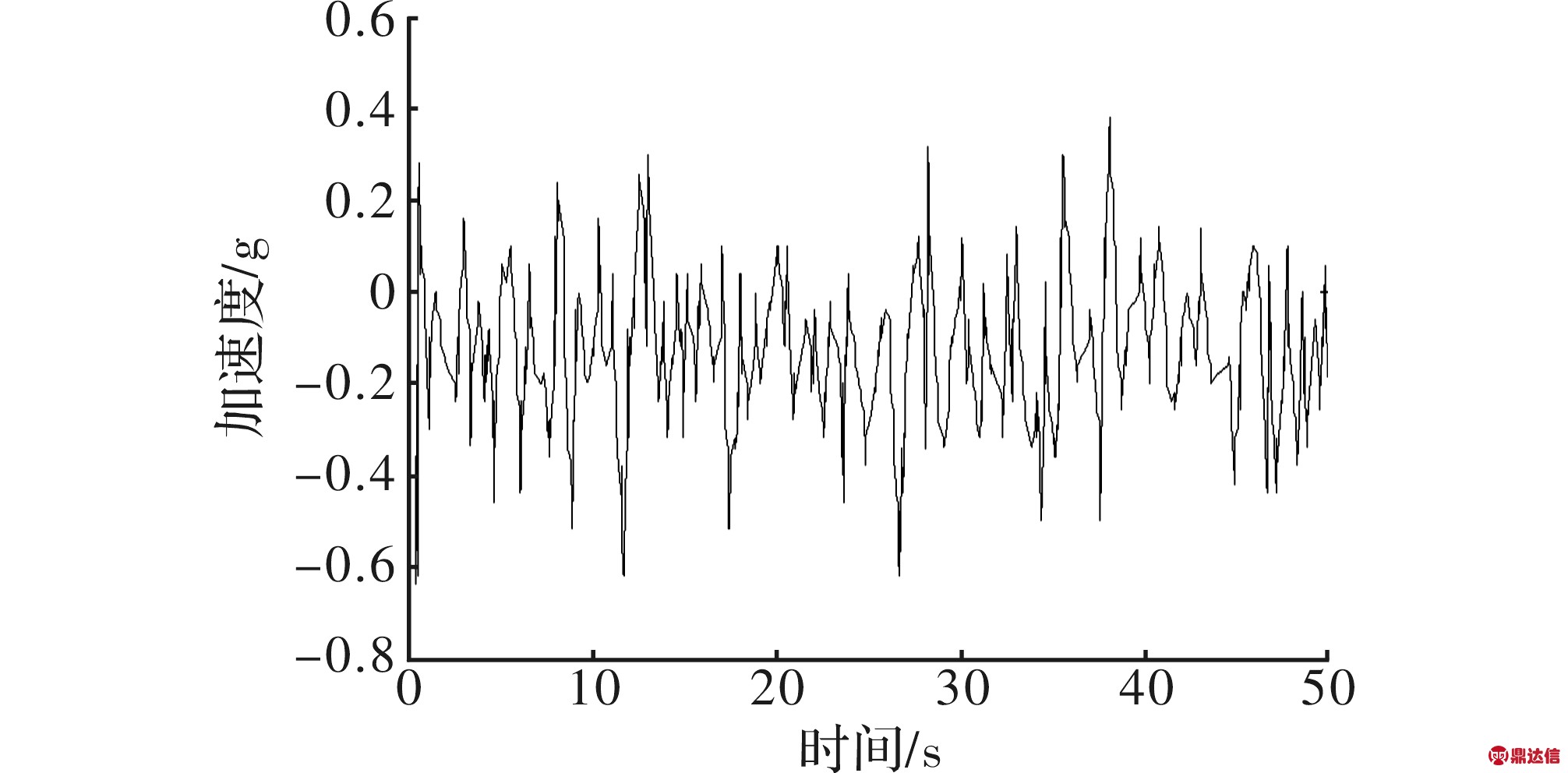
图5 时间—加速度路谱
2.2 仿真结果评价
根据上述的定义,在图5所示路谱的激励下,导轨内嵌入的20个弹簧-阻尼单元两端点必然会产生相对位移,由此可得到20个弹簧-阻尼单元两端点A、B之间的相对位移,根据分组,可以分别得到各组弹簧-阻尼单元的相对位移变化情况,如图6~图9所示;其中A点取连接内轨的单元节点,B点取连接外轨的单元节点,两节点在初始时刻相互重合。
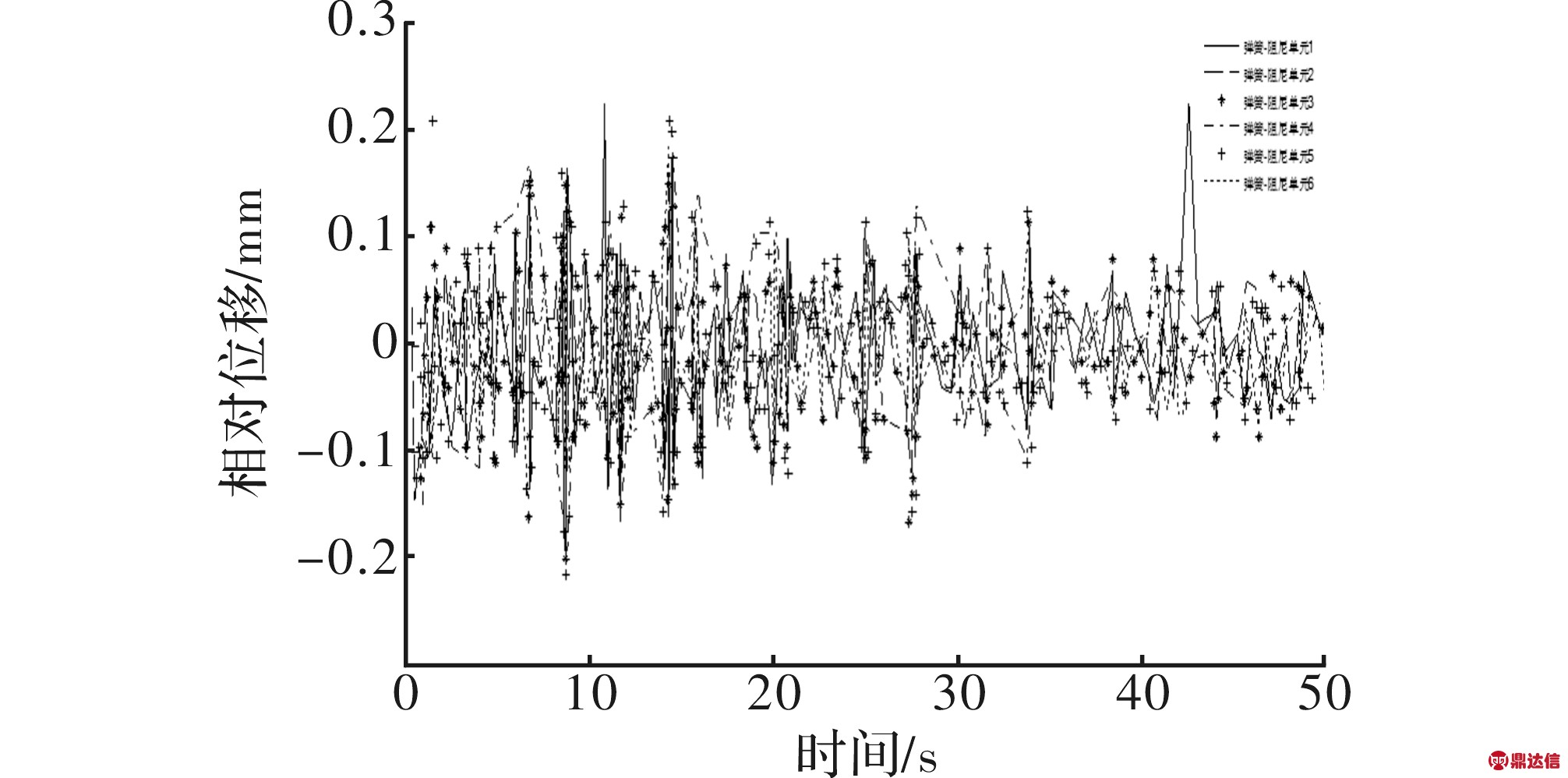
图6 第1组6个弹簧-阻尼单元的位移随时间变化曲线
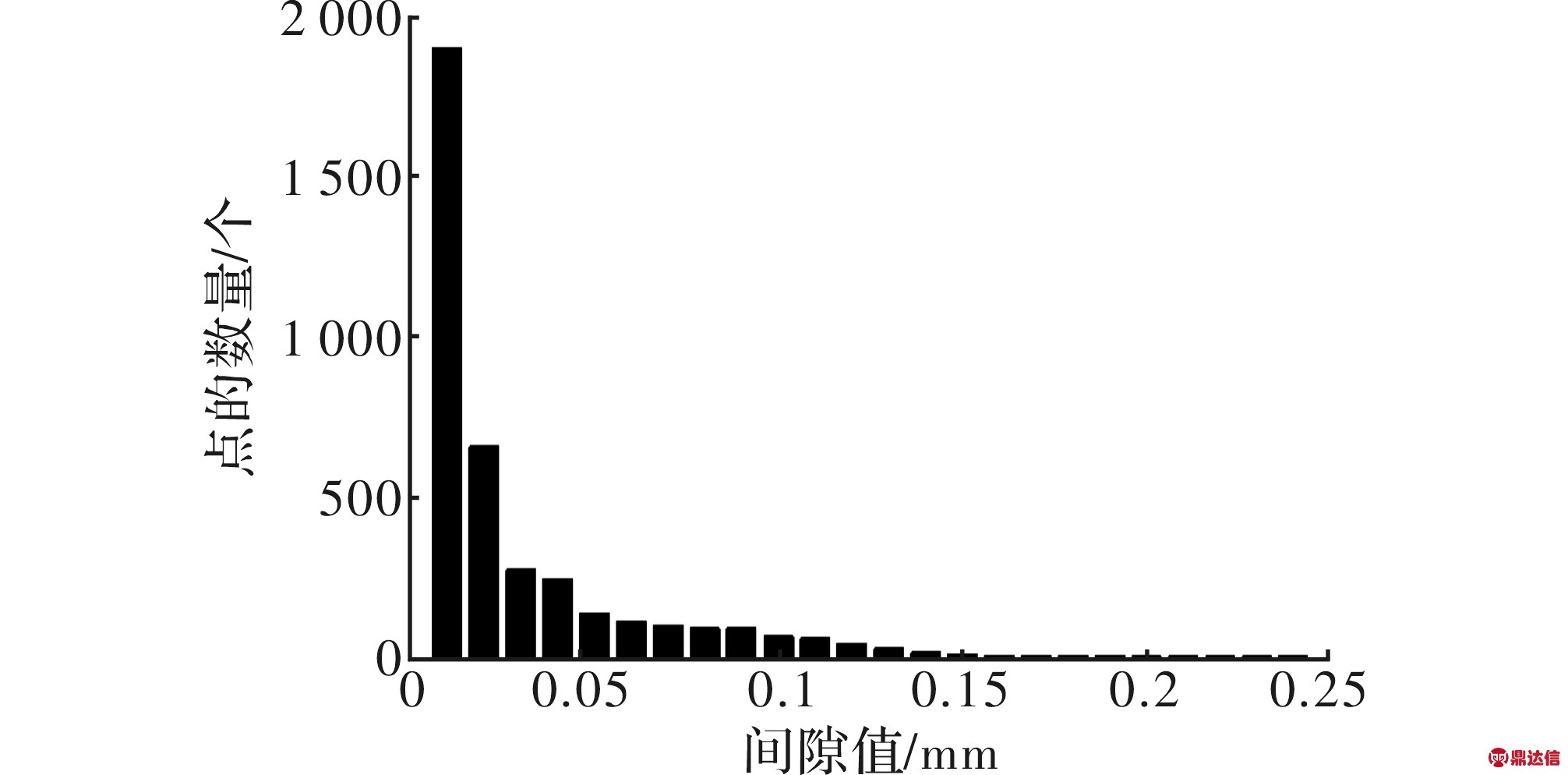
图7 第2组4个弹簧-阻尼单元的位移随时间变化曲线
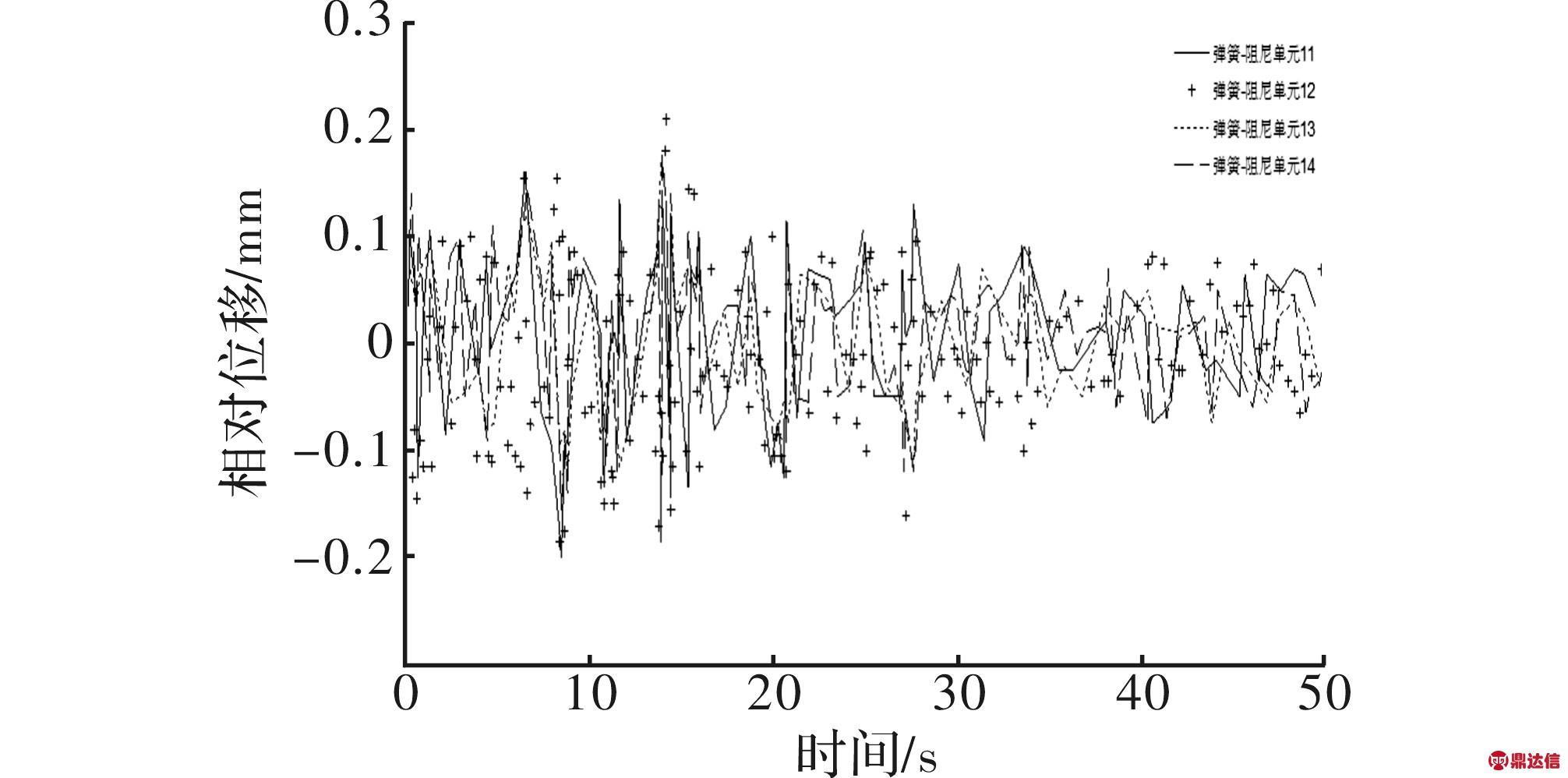
图8 第3组4个弹簧-阻尼单元的位移随时间变化曲线
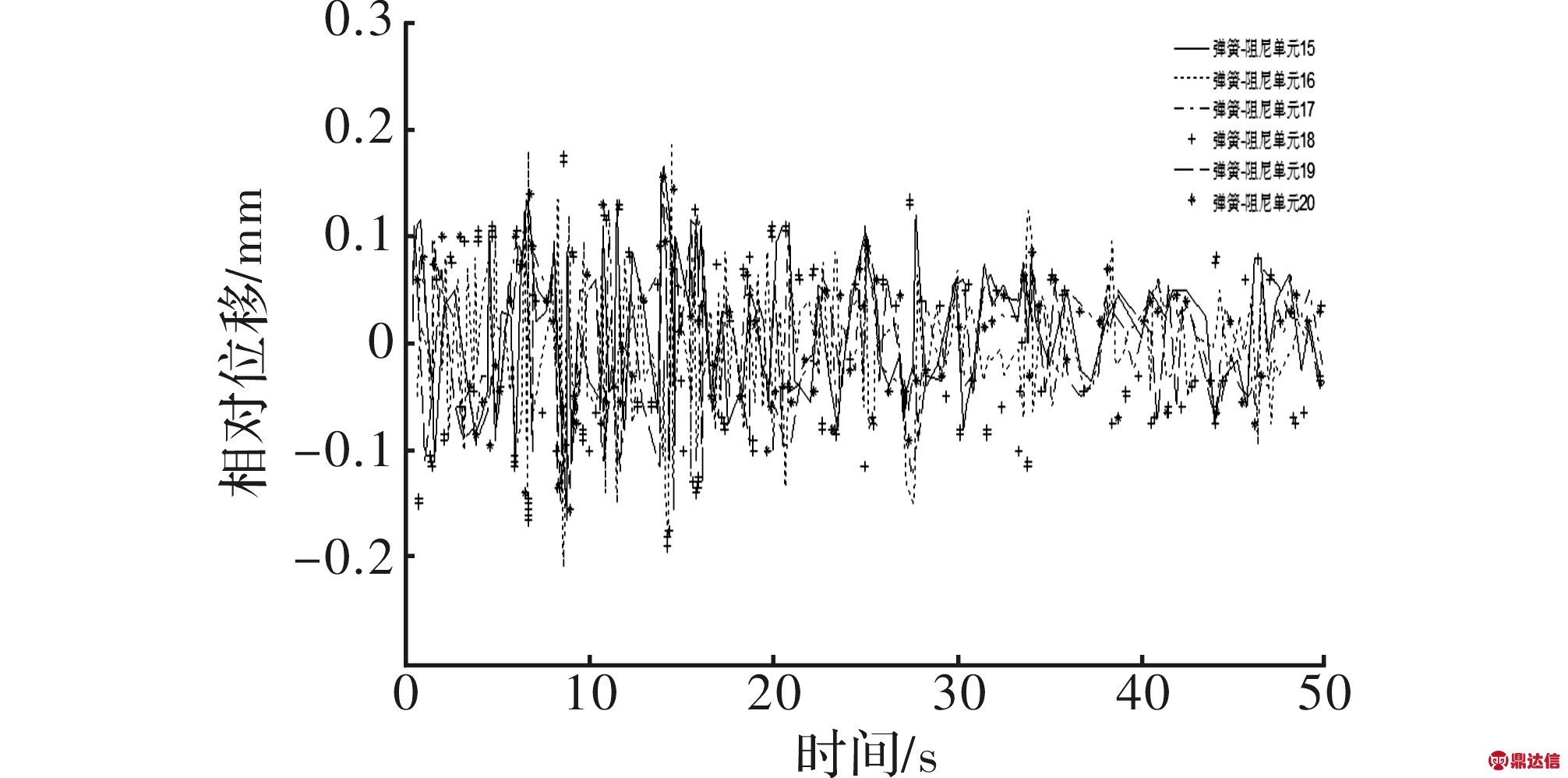
图9 第4组6个弹簧-阻尼单元的位移随时间变化曲线
由图6~图9可得,在跨度为50 s的时间历程上间隙的最大值为0.23 mm。为进一步确定座椅导轨间隙值的分布情况,对图6~图9中20个弹簧—阻尼单元两端点之间的相对位移进行了统计学分析:在每条曲线上均匀取出400个点,20条曲线的8 000个点构成了统计的样本空间,对8 000个点的纵坐标值进行了统计,根据数理统计计算得该组数据服从N(0.000 27,0.070 1)的正态分布。由于只考虑出现间隙的情况,取正态分布的右半部分,如图10所示。
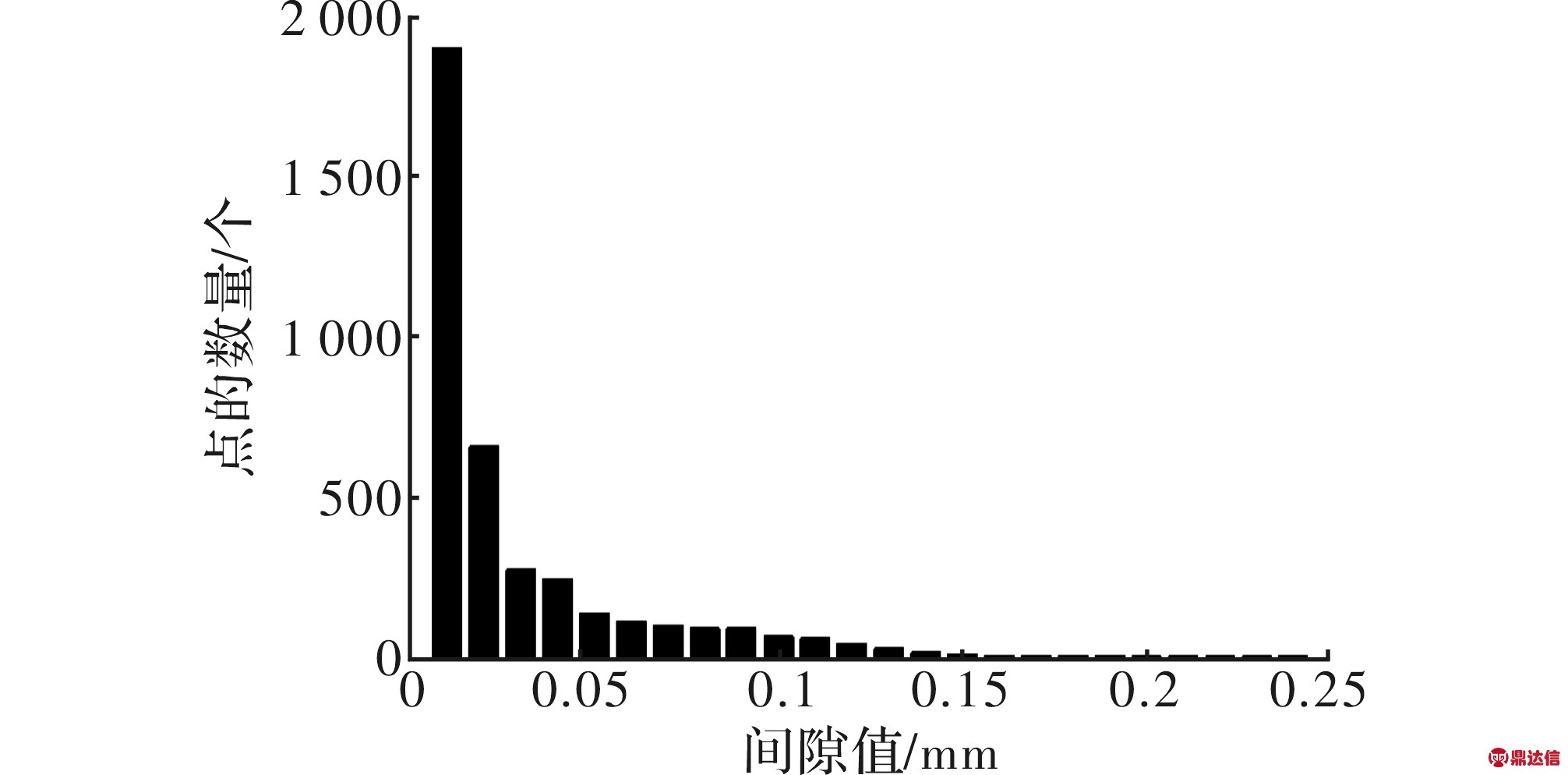
图10 间隙区间分布柱状图
容易得出该部分均值为0.028 mm,即间隙均值为0.028 mm。由数理统计[8]可知,该部分的概率密度函数是正态分布概率密度函数的两倍,且x的范围为0~+∞。根据正态分布表,可得间隙置信度表如表4所示。
表4 间隙置信度
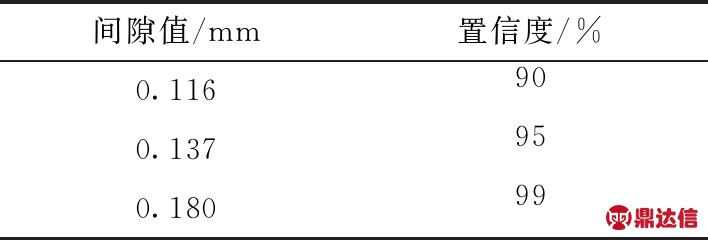
或者根据3σ准则,将有99.74%的概率保证间隙值不超过0.21 mm。即在导轨装配过程中,若在导轨与钢珠之间预压0.116 mm,则有90%的概率保证导轨与滚珠之间不出现异响;预压0.137 mm,则有95%的概率保证导轨与滚珠之间不出现异响;预压0.180 mm,则有99%的概率保证导轨与滚珠之间不出现异响;预压0.21 mm,则有99.74%的概率保证导轨与滚珠之间不出现异响。
3 结束语
通过上述建模方法可得到各个弹簧-阻尼单元两端点的相对位移量,也即导轨内间隙值的大小,并对其进行数理统计分析。根据分析结果,可得出不同的预压量,异响发生的可能性也不同,为了最大限度的减少异响现象,建议预压0.21 mm,在工程实际中,座椅制造商在解决导轨异响问题时对导轨的预压量为0.2 mm,这说明本文的研究与工程实际相吻合,为解决实际问题提供了理论依据。