摘要:本文对平板闸阀的整体结构和密封原理进行了介绍。对几种阀座组件结构进行了对比,分析了高压平板闸阀全压差开启时阀座经常损坏的原因,对高压平板闸阀阀座组件结构进行了优化。有效解决了高压平板闸阀全压差开启时阀座破坏的问题,能满足高压平板闸阀的全压差开启要求,使其符合API 6D 对管线平板闸阀的规定,保证高压平板闸阀的密封性能和使用寿命。
关键词:高压平板闸阀;阀座组件;全压差开启;密封性能;平衡孔
1 概述
平板闸阀有密封可靠、结构简单、开关扭矩小和便于操作等优点,是石油化工和天然气管线工程等领域中管路上常用阀种。随着石油化工装置和石油天然气管线工程的大型化,与其配套的平板闸阀的口径也越来越大,压力越来越高。当运行压力达到10MPa 及以上,在进行全压差开启时,经常发生阀座损坏并产生泄漏的现象,由此给管道工程带来安全隐患。本文介绍了一种新的阀座组件结构,有效解决了高压平板闸阀全压差开启时阀座破坏的问题,能满足高压平板闸阀全压差开启要求,使其符合API 6D 对管线平板闸阀的规定,保证平板闸阀的密封性能和使用寿命。
2 平板闸阀密封原理
平板闸阀的主要部件有阀体、阀盖、阀杆、闸板和阀座组件等,见图1。两个阀座组件采用单活塞结构, 闸板与阀杆间采用T 形连接,闸板可以沿介质方向浮动,两阀座组件以闸板为中心对称分布,与闸板形成一套浮动组合件,通过闸板升降来实现流体的截断和流通。一般情况闸板上升为开启,下降为关闭。当闸板向下关闭后,两端阀座组件在尾部预紧弹簧的作用下使之抱紧闸板形成初始密封,介质推动上游阀座贴紧闸板,形成自紧密封,介质压力越高密封力越大。当上游密封发生破坏后,闸板可浮动,在介质作用下,闸板可以与下游阀座形成第二道自紧密封。由于闸板是浮动的,无论是上游阀座密封还是下游阀座密封,巨大的介质推力均由下游阀座承受。
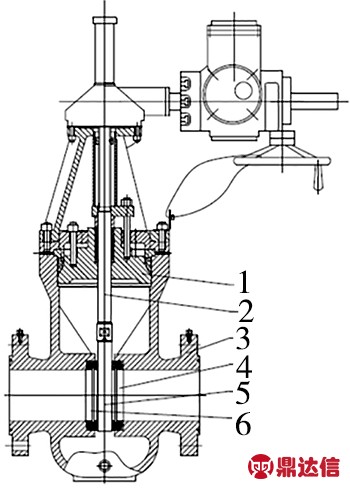
图1 平板闸阀示意图
1.阀盖 2.阀杆 3.阀体 4.阀座1 5.闸板6 阀座2
3 阀座损伤现象与损伤原因分析
3.1 阀座损伤现象
阀座组件由阀座支撑环、阀座和O 形圈等组成,阀座为密封件,通常选择为增强四氟等非金属材料,阀座支撑环是用于固定和支撑阀座的金属部件,阀座支撑环上设计有阀座固定槽,阀座安装于其中。当阀门组装后进行全压差开启试验时,一端进压,另一端无压力,对阀门进行开启,底部阀座(面对流道6 点钟位置)突起(图2),当闸板关闭时,突起部分被剪切形成缺口(图3),造成阀门泄漏。
3.2 损伤原因分析
当阀门关闭时,闸板自上而下运动,将阀座与阀座固定槽底部间空气大部分挤压到阀座支撑环底部(面对流道6 点钟位置)。阀门单端进压进行全压差开启时,下游阀座承受全部介质推力,下游阀座与环槽底部间的空气被压缩到非常高的压力,阀门进行开启时,闸板与阀座开始脱离,当闸板下边缘到达阀座内侧边缘即将脱离时,阀门还未泄压,但下游阀座已有部分已与闸板脱离,局部受力失去平衡,阀座会被环槽底部压缩空气推出,形成局部凸起,造成破坏。
4 当前结构及工艺处理缺点
当前高压平板闸阀的阀座组件设计,各个制造工厂存在一定差别。有的工厂的阀门在5MPa 的压差下开启,阀座即被破坏;有的工厂的阀门在10MPa 的压差下开启,阀座即被破坏。为了满足API 6D 中全压差开启的要求,制造工厂对阀座支撑环或阀座进行了改进,常见方式如下。
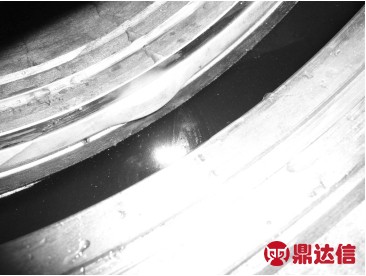
图2 阀座凸起
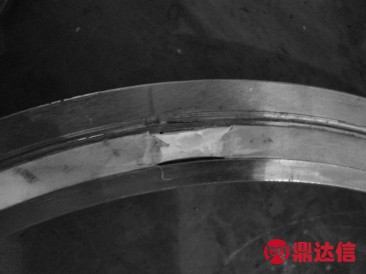
图3 阀座被闸板剪切
(1)采用强度和硬度高的阀座材料。这一方式虽然能够满足全压差开启的要求,但低压密封困难,要求加工精度高,阀门压力试验返修率高。
(2)采用硬度较高的阀座材料,用强力粘接剂将阀座与阀座支撑环粘接。这种方式一般可以承受一至三次的全压差开启,满足出厂要求,但在实际使用中多次启闭后,阀座又被破坏或变形,造成阀门内漏,影响管线运行。
(3)采取组合式阀座支撑环,阀座支撑环分成两部分,将阀座卡在组合阀座支撑环中。但这一方式加大了内件尺寸,从而需要加大阀体尺寸,组合阀座支撑环加工形状较复杂,精度要求高,增加了制造成本。
5 阀座组件结构改进方案、工作原理及试验验证
5.1 阀座组件结构改进方案
针对现有技术所存在的不足之处,在不影响原阀门整体尺寸的基础上,对阀座组件结构进行了改进,成功的解决了全压差开启阀座损伤的问题,保证了平板闸阀的密封性能和使用寿命。具体结构如下(见图4)。
(1)在阀座支撑环放置阀座的环槽底部均布一定数的排气孔,孔直径为2.5 ~4mm,在不与其他加工尺寸干涉时,尽量取大值。排气孔中心线与环槽底部面重合,使环槽底部与阀座支撑环外环面贯通。DN400 及以下均布4 个,DN500-DN900 均 布6 个,DN1000-DN1600 至少均布8 个。
(2)在环槽开口位置外侧设计一个突出1mm 左右的止口。
(3)在环槽底部,最先与闸板脱离位置,设计平衡孔(见图5)。平衡孔的大小、间距和数量的确定准则:L:闸板与阀座脱离时,闸板下边缘与阀座支撑环环槽外圆两交点的距离;N:设计需要的至少平衡孔数量;n:平衡孔计算数量;d:平衡孔直径(d 一般取2.5 ~4mm,在不与其他加工尺寸干涉时,尽量取大值);l:平衡孔中心距离,l=3d。


图4 阀座组件局部图
1.阀座 2.止口 3.气孔4.平衡孔 5.阀座支撑环
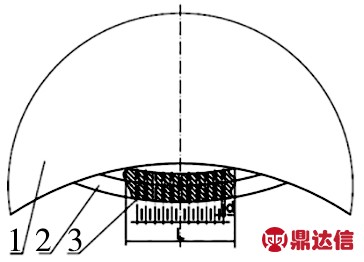
图5 闸板即将脱离底部阀座
1.闸板 2.阀座组件3.平衡孔
当n 有小数时,直接进一位圆整;当n 为奇数时,N=n;当n 为偶数时,N=n+1。
L、l 和d 见示意图5。
以上公式适用于DN25 以上的平板闸阀,DN25 及以下的平板阀只需要设计一个平衡孔(N=1),及将其中一个排气孔安装到阀门流到底部(面对流道6 点钟位置)即可。
5.2 改进后阀座组件结构的工作原理
阀座安装在阀座支撑环的环槽中之后,在高压设备压紧时,阀座底部与环槽之间的空气通过均布的排气孔排除,阀座发生冷流,以此填满整个环槽,止口处也会完全贴合,再完成阀座密封面的加工即可组装。阀门组装后进行全压差开启试验时,阀门关闭,闸板向下运动,使阀座底部与环槽间的空气向底部(面对流道6 点钟位置)挤压,均会通过底部平衡孔排出;闸板关闭到位,上游进压,介质将闸板推向下游阀座,下游阀座承受巨大的推力,阀座底部与环槽底部间残留的空气再次从平衡孔中排出,防止积压。当阀门进行开启时,闸板与阀座开始脱离,当闸板下边缘到达阀座内侧边缘时,此处阀座前后压力平衡,阀座不会发生破坏。即使有少量残留空气使阀座有向外推出的趋势,也会被环槽顶部的止口挡住,从而防止阀座破坏。
5.3 改进后阀座组件结构的试验验证
针对改进后的阀座组件结构,采用了DN50 PN150、DN100 PN150、DN350 PN150、DN600 PN150 和DN800 PN100 共5 个规格的平板闸阀各一台进行验证试验,每个阀座进行20 次(每台阀门共进行40 次)全压差开启试验,PN150 阀门的试验压差为不低于15MPa,PN100 阀门的试验压差为不低于10MPa。试验前按照 API 6D 要求对阀座进行了高压水密封试验,均合格,然后每5 次全压差开启试验后对阀座进行表面检查,并按照 API 6D 要求进行一次高压水密封试验。完成所有试验后再次对阀座组件进行检查,阀座高压水密封试验合格,阀座表面无损伤。
试验结果表明安装改进后阀座组件的高压平板闸阀能够满足全压差开启要求,且性能稳定,使用改进后阀座组件高压平板闸阀将极大的降低管道工程阀门内漏的可能性。
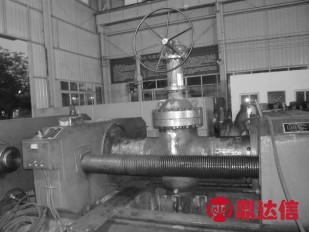
图6 DN350 PN150 规格试验
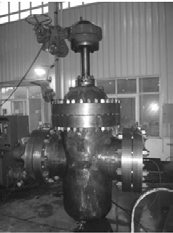
图7 DN600 PN150 规格试验
6 结语
本文对高压平板闸阀全压差开启时的状态进行了分析,提出了一种新的阀座组件结构设计,并通过试验验证,从原理上彻底解决了高压平板闸阀全压差开启时阀座破坏的问题。新阀座组件结构设计几乎不影响原阀门整体尺寸,基本不增加阀门生产总成本,又满足高压平板闸阀全压差开启要求,符合API 6D 规定,可保证高压平板闸阀的密封性能和使用寿命。