摘 要:针对传统液压泵的不足,研制了一种新型非对称式凸轮转子型双定子叶片泵.该泵将凸轮转子型叶片泵的结构和双定子的思想相结合,在泵的壳体内设置了内外两个定子和一个转子,其中转子内外凸起数不同,使该泵可输出多级定流量,也能够同时对多个系统供油.阐述了泵的工作原理与特点,通过非对称式凸轮转子型双定子叶片泵内部结构的分析,归纳出凸轮转子在不同转角下内外泵的理论流量,进而得到泵在不同工作方式下的瞬时流量.搭建了非对称式凸轮转子型双定子叶片泵试验平台,试验结果表明:与传统的对称式双凸起凸轮转子型叶片泵相比,非对称式凸轮转子型叶片泵的流量脉动更小,大约降低了2%左右,试验结果与理论分析基本一致,验证了理论分析的正确性.
关键词:非对称式;双定子泵;凸轮转子;流量脉动;不均匀系数
近年来,我国制造业高速发展,液压技术也与纳米技术、微电子技术、材料科学等技术相结合得到了广泛的发展[1],同时,液压传动也以其工作平稳、能驱动大负载、结构紧凑、体积小等优点,被广泛应用于工程、建筑、农业、国防技术等领域[2-4],其应用和发展与我国的工业进程息息相关[5].
在国内最早于1982年研制成额定工作压力为16 MPa的凸轮转子型叶片泵;广州机床研究所的王忠楗等研制了TYB系列凸轮转子型叶片泵[6];湖北液压件厂的张或定提出两种凸轮转子型叶片泵的基本类型[7];福州大学的林信彰等主要提出了几种提高凸轮转子型叶片泵工作寿命的措施[8-10];北京机械学院的邱永榴等分别对两凸起、四凸起以及六凸起凸轮的凸轮转子型叶片泵的流量与马达的转矩进行了详细的计算[11].
传统单个凸轮的双凸起凸轮转子型叶片泵有流量脉动不平稳,噪声大等缺点,本文所研究的是一种新型原理泵,其特点与意义在于:该泵是一个内外凸起数不同的凸轮转子轴对应内外两个定子,可输出多级定流量,可进行多级压力调节,也能够同时对多个系统供油.通过对过渡曲线、叶片数量、轮廓线对应角度等参数的合理设计,使得这种新型泵的流量脉动减小,降低了噪声,提高了比功率,延长了寿命,体现了液压传动的特点[12-13],但该泵要求加工精度高,泄露比一般的叶片泵要大.这种新型结构的提出可在一定程度上增加液压泵的使用场合和种类.
1 结构与工作原理
1.1 结构
图1为非对称式凸轮转子型双定子叶片泵结构示意图.从图中可以看出,该泵内有两个定子和一个转子,转子内轮廓与内定子形成内泵,转子外轮廓与外定子形成外泵.转子的外轮廓为三凸起,内轮廓为两凸起,叶片在转子内外表面可光滑平稳地运动.由于转子内外凸起数不等,内外结构不对称,故称为非对称式双定子泵[14-17].
1.2 工作原理
图2为非对称式凸轮转子型双定子叶片泵的原理简图.1、2、3、4 分别对应内泵的工作容腔;5、6、7、8分别对应外泵的工作容腔.随着转子顺时针旋转,容腔2、4、6、8的空间增大,形成局部真空,吸入液压油;容腔1、3、5、7的空间减小,压力升高,排出液压油.图中连接内外泵压油口的沟槽与叶片槽根部相通,其目的是将高压油引入叶片根部,使高压油压力和弹簧弹力共同作用于叶片根部,既保证了初始密封,又保证了动态密封,同时也降低了弹簧的疲劳损坏.转子每旋转一周,每个工作空间要完成两次吸排油,故该泵可划归为双作用叶片泵.内外泵输出流量不等的油液,各泵既可单独工作输出油液,也可联合工作输出油液;既可形成多个子系统,又可形成多级流量、多级压力的单个系统[14].

图1 非对称式凸轮转子型双定子叶片泵结构
Fig.1 Structure of asymmetrical cam-rotor double-stator vane pump

图2 非对称式凸轮转子型双定子叶片泵原理
Fig.2 Simplified schematic diagram of asymmetric camrotor double-stator vane pump
2 转子轮廓曲线设计
在过渡区,叶片沿径向从小半径圆弧走到大半径圆弧路程的方式可能是多种多样的,设计中要综合考虑过渡曲线所产生的冲击及加工的难易程度等因素,在设计样机时最终确定采用等加速等减速曲线作为过渡曲线,从而使得叶片在运动过程中不会产生硬性冲击、串压或撞击等不良影响[18].
在非对称式凸轮转子型双定子叶片泵的设计中,由于转子的内外轮廓是非对称的结构,所以其轮廓曲线应分别设计.图3为凸轮转子截面轮廓,其中,转子外轮廓是由3段大半径圆弧、3段小半径圆弧以及连接大圆弧与小圆弧的6段过渡曲线所组成;转子内轮廓是由2段大半径圆弧、2段小半径圆弧以及连接大圆弧与小圆弧的4段过渡曲线所组成[19-22].图3中:、
为转子外、内轮廓过渡曲线包角;
、
为转子外、内轮廓大(小)圆弧包角;
、
为转子外、内轮廓大圆弧半径;
、
为转子外、内轮廓小圆弧半径.

图3 凸轮转子截面轮廓
Fig.3 Cross-section profile of cam rotor
为了保证泵输出流量的均匀性,通常将大圆弧与小圆弧所包围的弧度角设置为相等的值.下面分别对转子的内外轮廓曲线公式进行介绍.
对于外轮廓与内轮廓,分别设线1与线2为基准线,转子顺时针转动.设转子相对于基准线1转过的角度为 ,转子外轮廓的曲线半径为
,转子相对于基准线2转过的角度为
,转子内轮廓曲线半径为
则在任意一点的表达式为

由于凸轮转子的对称性,式(1)仅为转子转过120°外轮廓曲线半径的表达式,式(2)仅为转子转过180°内轮廓曲线半径的表达式.
3 泵理论流量计算
图4为非对称式凸轮转子型双定子叶片泵内部结构主要几何参数.

图4 泵内部结构主要几何参数
Fig.4 Main structural parameters of the pump internal structer
由图4可以看出,泵的排量与叶片扫过的面积有关,当转子旋转一周,对于单个外泵叶片所扫过的面积是曲线abcdega所包围面积的3倍;对于单个内泵叶片所扫过的面积是曲线hijklmh所包围面积的2倍[23].这两个面积是由圆弧和过渡曲线间的空隙形成的扇形,故可以用高等数学中扇形面积的积分来计算此区域的排量,即下面分别对非对称式凸轮转子型双定子叶片泵内外泵的排量及理论流量进行计算分析.
在外泵中,以图4中基准线1为起始位置,逆时针转过角度为φ1,由于扇形的对称性结构,可得其中,
和
分别为

将 表达式分别代入式(3)中,且 α1 + β1 =
/3,可得:

在内泵中,以图4中基准线2为起始位置,顺时针转过角度为φ2,同样由于扇形的对称性结构,可得其中,
和
分别为
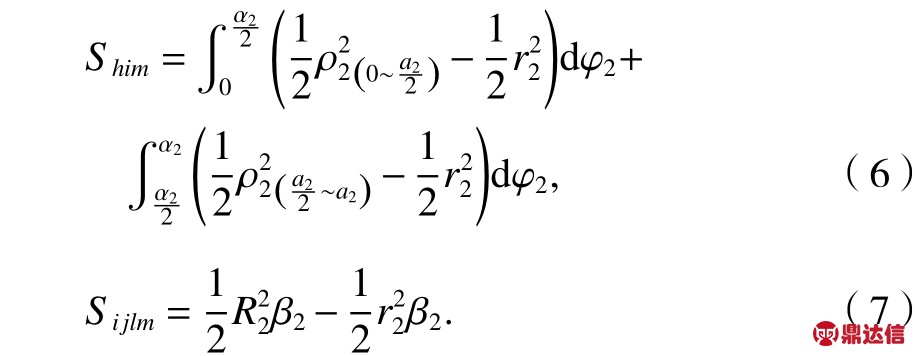
将 表达式分别代入式(6)中,且 α2 + β2 =
/2,可得

根据传统叶片泵中排量的计算公式,可知当凸轮转子转过一周时,外泵排量q1、内泵排量q2分别为


式中:、
为外、内泵叶片个数,
= 2,
= 2;
、
为为凸轮外、内轮廓凸起数
B为叶片宽度.
根据非对称式凸轮转子型双定子叶片泵的结构参数计算出q1 = 56.55 mL/r,q2 = 21.92 mL/r.液压泵的理论流量Qt的计算公式为

式中:n为电机的工作转速.
取转速为1500 r/min的电机,可计算得到外泵理论流量Qt1 = 84.825 L/min,内泵理论流量Qt2 =32.880 L/min.
4 泵流量脉动分析
随着凸轮转子的转动,液压泵的密闭容积会发生瞬时变化,为了计算非对称式凸轮转子型双定子叶片泵的流量波动性,应首先对其瞬时流量进行分析.设凸轮轴旋转的角速度为 ,非对称式凸轮转子型双定子叶片泵的外泵中单个叶片所扫过的瞬时流量计算公式为

非对称式凸轮转子型双定子叶片泵的内泵中单个叶片所扫过的瞬时流量计算公式为

下面分别对内外泵在不同转角下单个叶片所扫过的瞬时流量进行计算.
对于外泵:

同理,对于内泵:
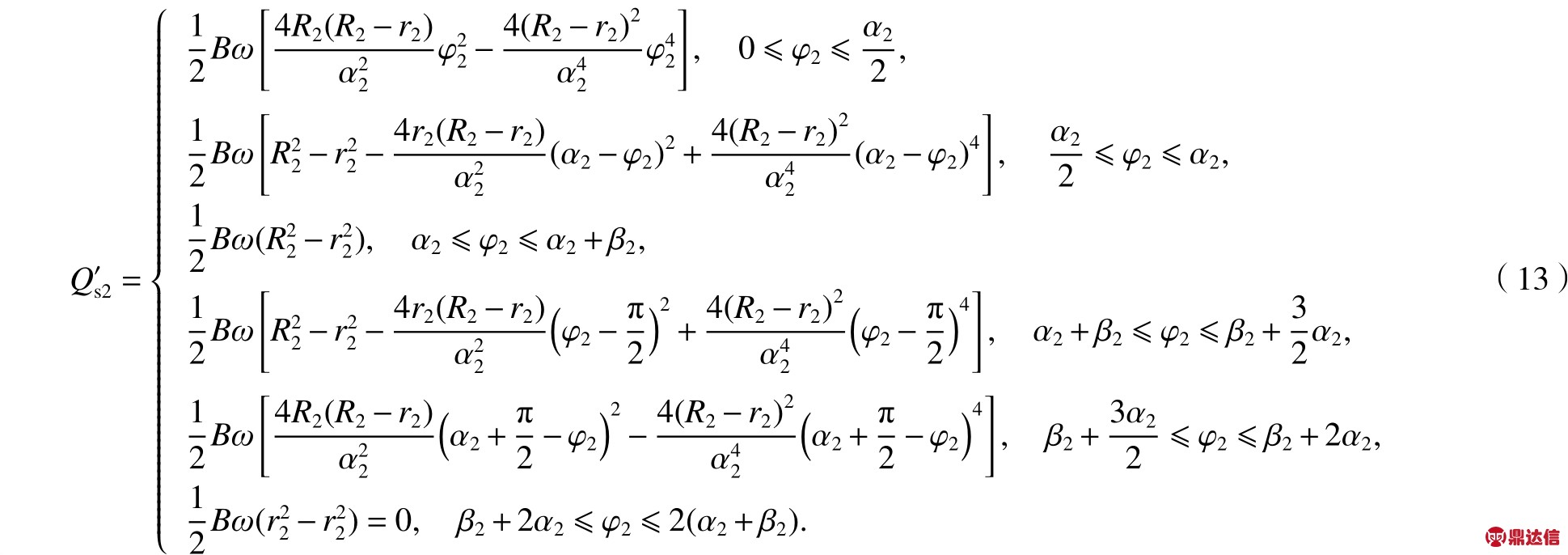
由式(12)与式(13)可得出单个外泵与单个内泵瞬时流量的输出特性曲线,如图5所示.从图5中可以看到,无论是单个外泵或是单个内泵,在其单独工作时瞬时流量的波动性都非常大,而过大的流量脉动会引起压力的脉动,使管道、液压阀等元件产生振动和噪声,不利于整个系统的工作.
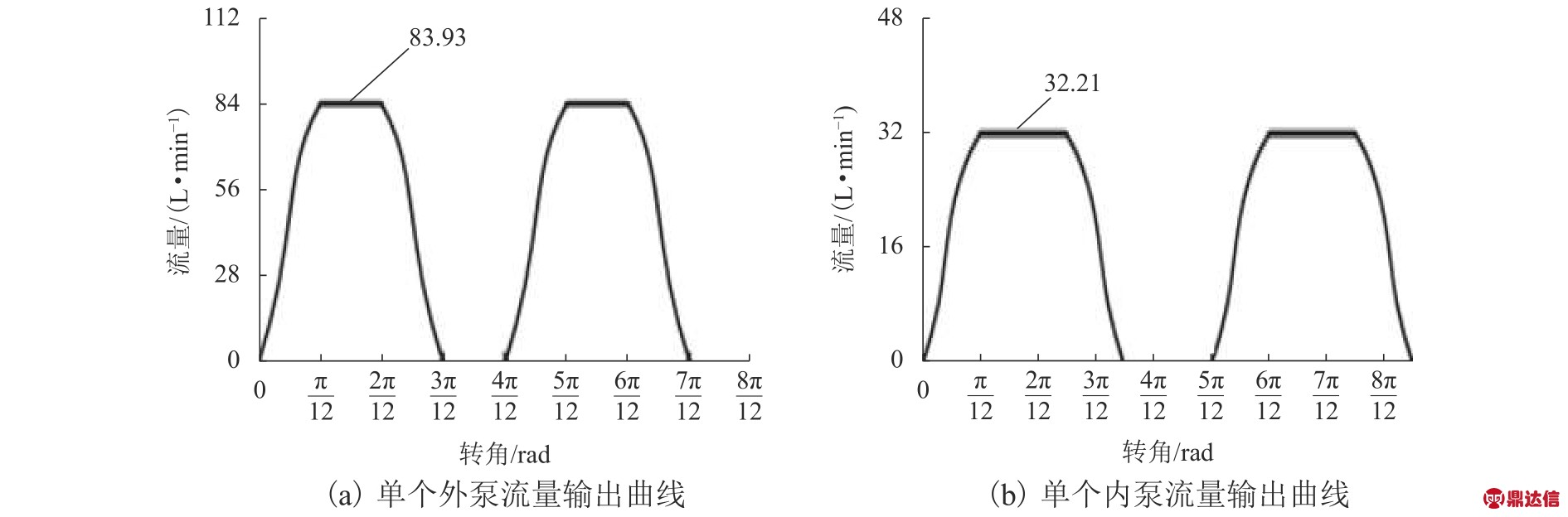
图5 内、外泵流量输出曲线
Fig.5 Flow output curves of external and internal pumps
在传统的双凸起凸轮转子型叶片泵中,单个凸轮的流量脉动亦呈现图5中的情况,为了减小流量的脉动,其做法是采用两个相差90° 的凸轮转子并排布置,如图6所示,两转子用同一转轴带动.

图6 相差90°的双凸轮凸轮转子型叶片泵
Fig.6 Dual-cam rotor vane pump with 90 °difference of cams
这样,两端输出油液的瞬时流量相差半个周期,起到了互补的目的,从而减小了脉动.而单个凸轮的三凸起式凸轮转子型叶片泵,则是采用两相对叶片布置,这样,当一个叶片处于缩回状态时,另一叶片便处于伸出状态,两输出油液的瞬时流量叠加值亦可起到减小脉动、提高稳定性的效果.
在非对称式凸轮转子型双定子叶片泵中,对于外泵,其形式类似于传统单个凸轮的三凸起凸轮转子型叶片泵,两泵的瞬时流量正好处于互补状态,故其外泵总的瞬时流量曲线(即两外泵瞬时流量的叠加)如图7(a)所示,从图中可以看到,外泵叠加后其瞬时流量脉动性较小.对于内泵,其形式类似于传统单个凸轮的双凸起凸轮转子型叶片泵,如果简单地将两内泵的瞬时流量叠加,形成的瞬时流量与图5(b)相类似,这种叠加不仅没有减少流量的脉动性,反而加剧了瞬时流量最大与最小值的差值,为了减小流量脉动,可将两内泵流道距汇流点的位置错开转过/2 rad的整数倍的转角时间,这样内泵总的瞬时流量(即两内泵瞬时流量的叠加)如图7(b)所示,可实现瞬时流量的稳定.
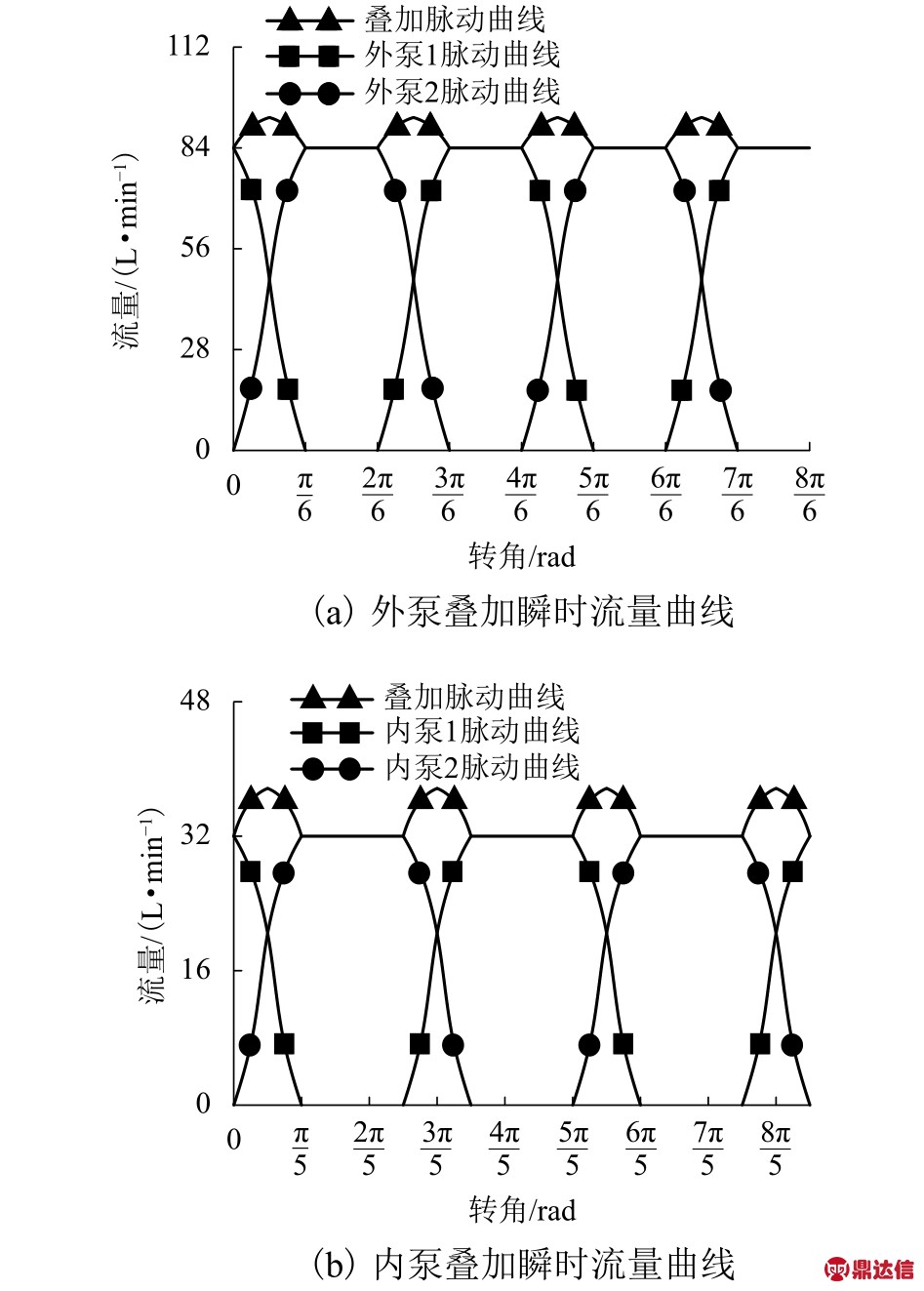
图7 瞬时流量曲线
Fig.7 Instantaneous flow curve
叶片泵的瞬时流量品质可由流量脉动频率fq和流量不均匀系数δq来分析.其中fq为每秒钟发生叠加流量曲线一个周期的次数,即

式中:α为过渡曲线对应夹角;β为大小圆弧对应夹角.
计算可得,外泵脉动频率fq1 = 150 Hz,内泵脉动频率fq2 = 100 Hz(这里取转速为1500 r/min的电机).
由图7可以看出,外泵的最大瞬时流量发生在转角 φ1 = α1/2 处,最小瞬时流量发生在 α1 ≤ φ1 ≤ α1 +β1时;内泵的最大瞬时流量发生在转角φ2 = α2/2处,最小瞬时流量发生在 α2 ≤ φ2 ≤ α2 + β2时.经计算可得外泵瞬时流量叠加值的最大值Qs1max、最小值Qs1min,以及内泵瞬时流量叠加值的最大值Qs2max、最小值Qs2min的计算公式分别为
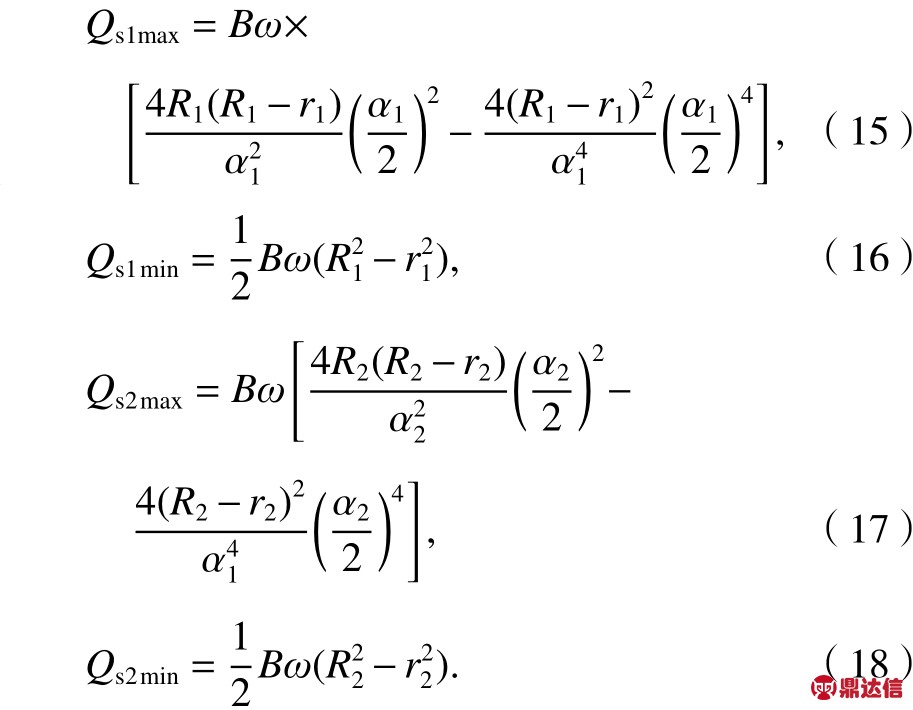
取转速为1500 r/min的电机,计算可得Qs1max =87.75 L/min,Qs1min = 83.93 L/min,Qs2max = 33.91 L/min,Qs2min = 32.21 L/min.流量不均匀系数δq可定义为瞬时流量最大值Qs max 和最小值Qs min之差与理论平均流量Qt的比值,即

对式(19)进行计算,可得到两外泵和两内泵流量不均匀系数分别为δq1 = 4.5%,δq2 = 5.2%.可见,内泵的流量不均系数更大一些.
5 实验研究
由于所设计的非对称式凸轮转子型叶片泵具有新型的结构,所以有必要对其进行原理性实验分析,图8(a)为泵样机,图8(b)为实验现场,图8(c)为实验系统图,通过换向阀的换向使泵实现3种不同的工作方式.
根据前面的分析,本次实验所制造的非对称式凸轮转子型叶片泵样机的外泵排量为56.55 mL/r,内泵排量为21.92 mL/r,转子外圈大圆弧半径为36 mm,转子外圈小圆弧半径为30 mm,转子内圈大圆弧半径为21 mm,转子内圈小圆弧半径为17 mm,外泵过渡曲线夹角为/6 rad,内泵过渡曲线夹角为
/5 rad,外泵圆弧夹角为
/6 rad,内泵圆弧夹角为3
/10 rad.
本次实验采用雷诺公司生产的CHPM型液压测试仪及SR-CT150-B-B-6型CT涡轮流量传感器测量泵工作过程中的瞬时流量值,设定采样周期为50 ms,选取马达稳定运转后 1 s内实验数据,并整理出瞬时流量的曲线.实验中选用电机的转速是1440 r/min.
受加工条件的影响,泵样机的加工精度较低,在测定泵的容积效率时,过高的压力会使测得的容积效率误差偏大,因此实验过程中选取的压力范围较小.进一步提高泵的压力范围需要更高的加工精度.对负载压力进行调节,分别在 1、2、3、4、5、6 MPa时对泵的输出流量进行测量,实验数据如表1~3所示,3种工况下泵的理论流量与实际流量均存在误差,原因是在工作中油液温度较高使得油液黏度较低;测量仪器存在误差;零件的加工精度存在一定误差,实际的密封配合精度较低;实验中如叶片、凸轮转子等运动部件出现磨损,造成更大的泄漏;其它人为因素等.
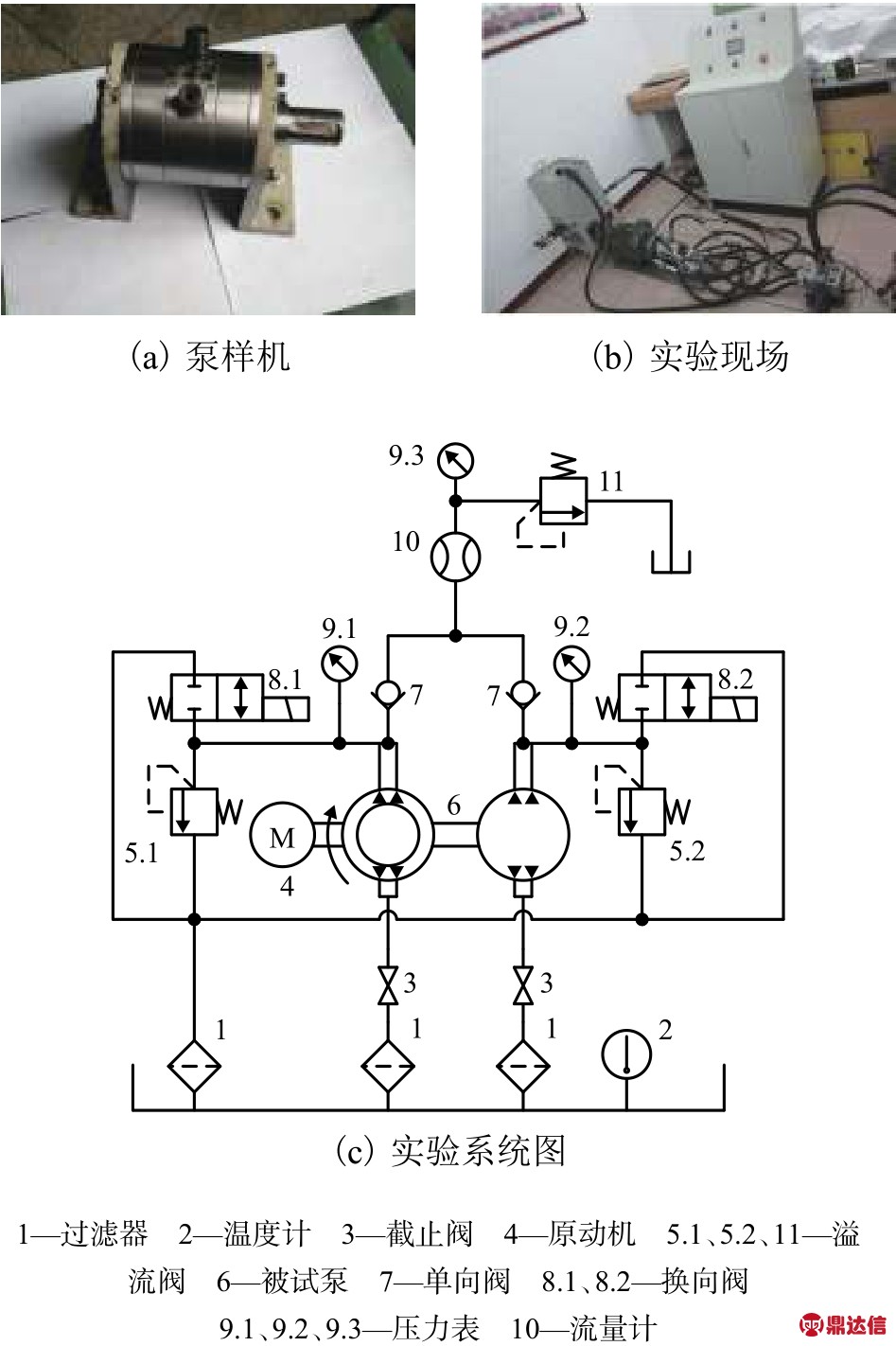
图8 泵样机及实验系统
Fig.8 Pump prototype and experimental system
表1 内泵单独工作时容积效率实验测量数据
Tab.1 Test data of volumetric efficiency with single operation of internal pump
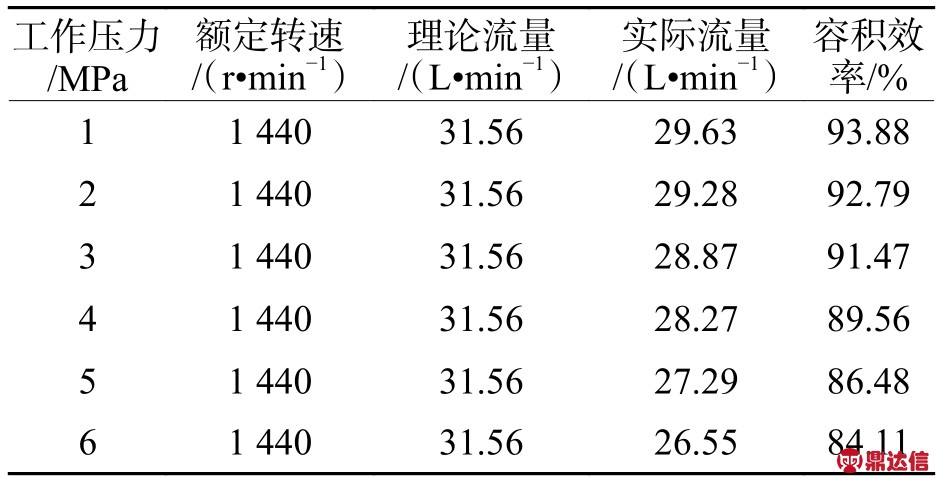
表2 外泵单独工作时容积效率实验测量数据
Tab.2 Test data of volumetric efficiency with single operation of external pump
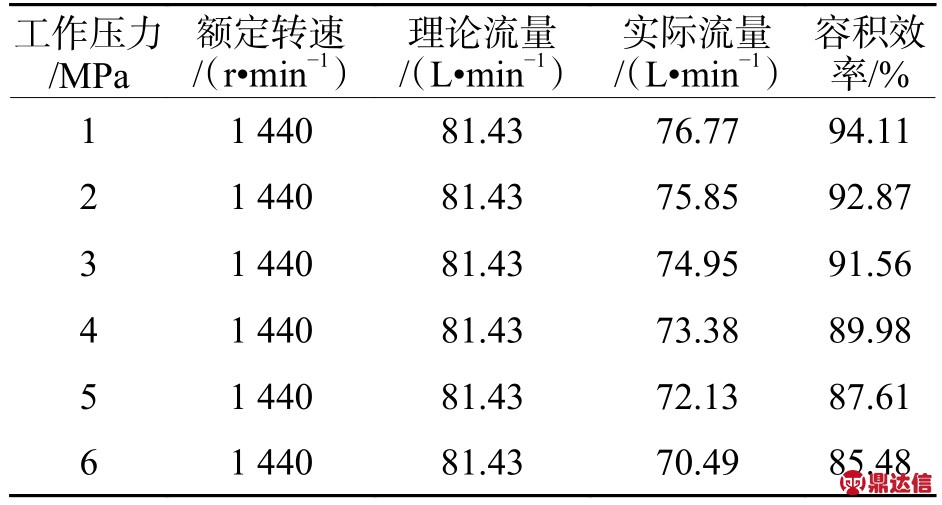
表3 内外泵联合工作时容积效率实验测量数据
Tab.3 Test data of volumetric efficiency with joint operation of internal and external pumps
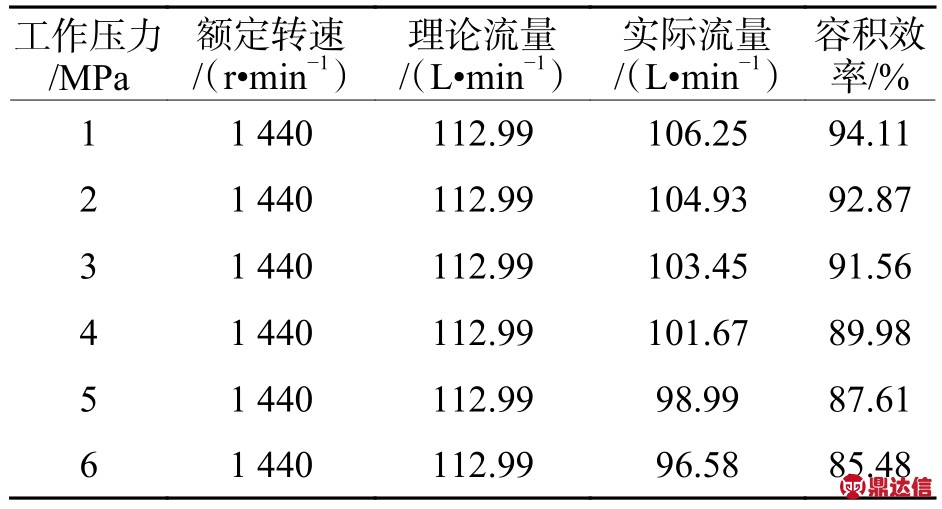
通过实验分析并对测量数据进行记录,得到上述3种泵在不同工作方式下的瞬时流量,如图9所示.从图9可以看出外泵单独工作时的流量脉动较小,内泵单独工作时流量脉动较大,内、外泵共同工作时的流量脉动较大.因为外泵采用单个凸轮的三凸起式凸轮转子,两相对叶片布置,这样,当一个叶片处于缩回状态时,另一叶片便处于伸出状态,两输出油液的瞬时流量叠加值亦可起到减小脉动、提高稳定性的效果.内泵为了减小流量脉动,将两内泵的流道距汇流点的位置错开/2 rad的整数倍的转角.从图10可以得知,在相同负载压力下工作时,内泵的容积效率最低,内外泵联合工作时次之,外泵的容积效率最高,主要是因为内泵在工作时的泄露更严重.

图9 试验泵的瞬时流量
Fig.9 Instantaneous flow of test pump
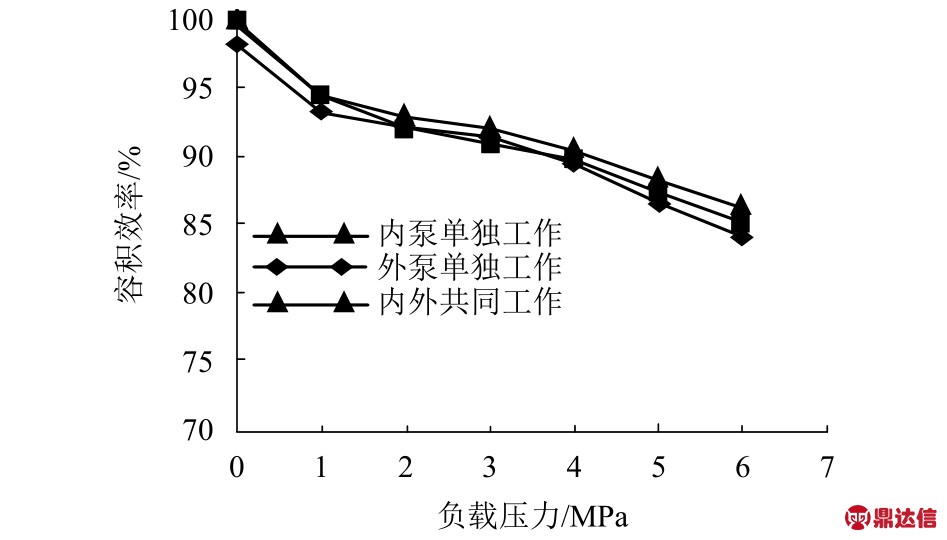
图10 试验泵样机的容积效率曲线
Fig.10 Volumetric efficiency curve of test pump prototype
6 结 论
(1) 提出了非对称式凸轮转子型双定子叶片泵,该泵壳体内设置了一个内外凸起数不同的中心转子和内外两个定子,该泵可以输出多级定流量,也能够同时对多个系统供油,对于简化回路、减少压力干扰、提高效率等方面起到一定推动作用,不仅丰富了新型液压元件,且为新型液压传动奠定了基础.
(2) 该泵共有3种不同的工作方式,分析了泵在不同工作方式下的流量脉动.其中外泵单独工作时流量脉动最为稳定,理论上几乎实现无脉动,内外泵共同工作时次之,内泵单独工作时流量脉动最差.在很大程度上提高了泵的使用寿命,减少了噪音.
(3) 通过泵样机的实验得出:非对称式凸轮转子型双定子叶片泵比传统单个凸轮的双凸起凸轮转子型叶片泵的流量脉动要平稳,为新型液压元件的设计提供参考.