摘 要:基于环形叶栅理论将二维叶片叶型转化为三维叶片,建立了叶轮叶片的三维模型。根据流体流动规律列出了叶轮连续方程、动量方程,使用FLUENT软件对方程进行了计算分析,数值模拟了叶轮三维湍流流场,获得了叶片表面压力云图、速度矢量图、叶片进出口边附近压力分布图和叶片安放角压力变化曲线。通过图形分析知,空蚀最严重位置出现在叶轮轮毂背面出口边附近。以效率最大、空化空蚀量最小建立目标函数,在MATLAB中进行计算求解,优化了叶轮进出口直径、进出口安放角。利用这种方法能够达到提高叶片泵的效率、降低叶片空蚀影响的目的。
关键词:叶片泵;叶片;三维模型;FLUENT;湍流流场;MATLAB
1 引言
液压传动是以油或水作为中间介质,通过液体的压力实现能量的传递。这种传动方式可实现大吨位传动,并且具有传动平稳、操作方便、易于控制等优点,能在大范围内实现无级调速,便于实现复杂动作[1-2]。液压泵是液压传动系统的动力元件,而叶片泵是液压泵很普遍的一种存在形式。近年来,叶片泵正朝着空化空蚀小、效率高的方向发展[3-7]。叶轮是叶片泵的重要组成部件,叶轮的核心零件是叶片,所以叶片的设计与分析是降低叶片泵空化、空蚀和提高叶片泵性能的重点。
随着CFD技术的快速发展,借助FLUENT软件的强大功能,对叶片泵叶轮叶片的三维流场进行分析,可提高达到预期目标的效率与质量。EbrahimiMojtaba[8]等研究发现通过改变定子内表面的特性曲线能够提高叶片密封性,进而提高叶片的寿命。文献[9]等基于流体分析软件对轴流泵叶片水力矩三维紊流进行了流场分析,绘制了泵的流量与水力矩的关系曲线。本模型在环形叶栅理论基础上设计了叶片泵叶片,对叶片泵叶轮流场进行了数值模拟,将获得的叶片云图进行分析。建立了叶片泵效率、空蚀最大最小的目标函数,对其参数进行优化求解,其仿真优化过程和结果为今后叶片泵叶轮的设计与研究提供了重要的参考。
2 CFD模型的建立
在广东韶关泵厂使用了伏因特西门子试验机对大型叶片泵模型进行叶片形状测绘实验,通过该实验装置采集到了叶轮叶片不同扇形角度φ值处所对应叶片工作正面叶型型值坐标Z1值和叶片非工作面坐标Z2值。实验获得的部分数据,如表1所示。其中叶型两端的数据(φ=-30°和φ=40°)使用插值法细化数据组合,Z1、Z2数据中小数部分根据绘图后叶片的光滑情况给与调整。使用表1中修正后的数据可以绘制成的叶型曲线,如图1所示。图1中的叶型曲线可以认为是某条环形叶栅线切割三个叶片形成的,基于这种理论将多个二维叶型图形转化成了三维叶片图形,如图2所示。由于形成的三维叶片图形的光滑性将影响流场流线分布性,所以要对三维叶片图形进行曲率检查,对不平滑的叶片部分微调型值点的大小进行修复,最后得到完整的叶片。叶片以外的叶轮零件图由厂家提供。在Pro/E中装配得到叶片泵叶轮段三维模型。
表1 叶片叶型型值点
Tab.1 Leaf Blade Type Value Point
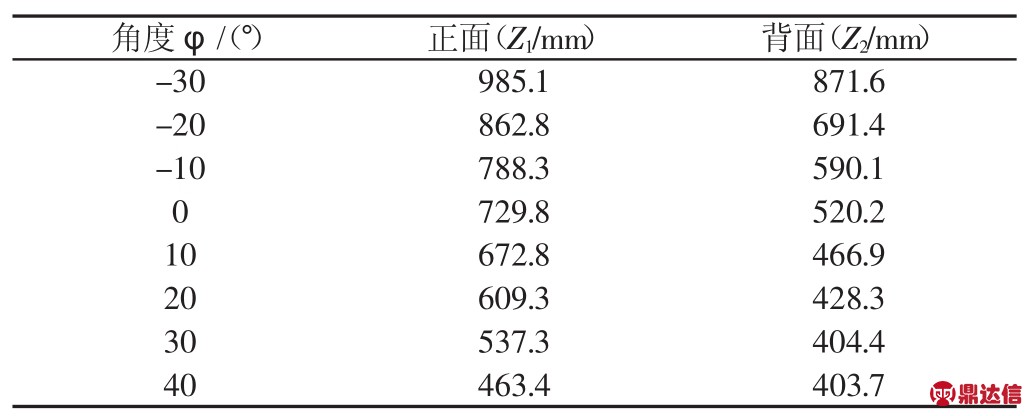
将形成的三维叶片泵叶轮段模型导入ICEM软件中,由于模型所含有的叶片径向尺寸与轴向尺寸比大,叶片是扭曲复杂的曲面体,因此在ICEM软件中采用能够适应这种复杂形状的非结构网格对其各零件进行了网格划分。泵体、泵球形轴、叶片计算网格数分别为81716、60085、255032个单元,叶片泵叶轮流场计算域,如图1所示。叶型线,如图2所示。叶轮计算区域,如图3所示。
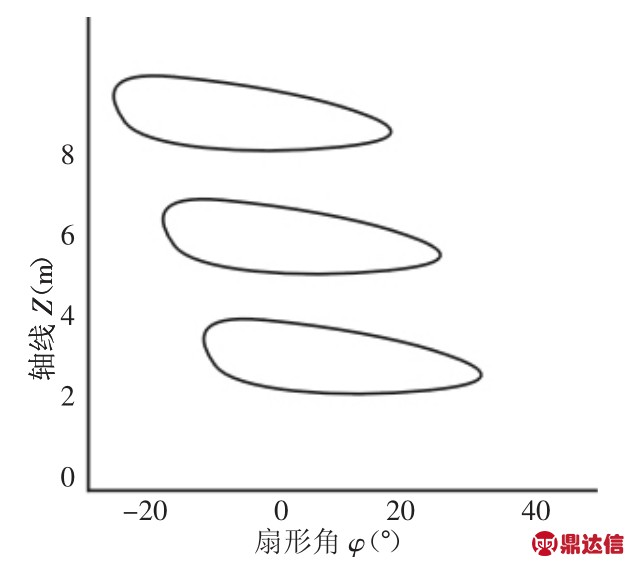
图1 叶型线
Fig.1 Leaf Type Curve
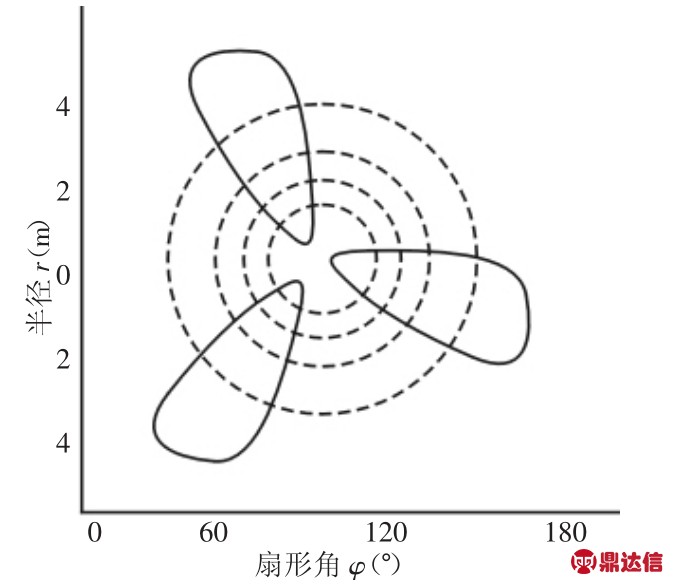
图2 叶片环形叶栅
Fig.2 Annular Cascade Curve of the Blade
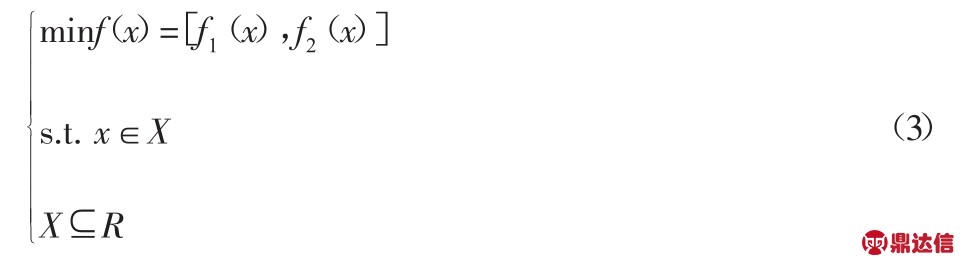
图3 叶轮计算区域Fig.3 The Calculation Area
3 模型的计算与结果分析
模型采用ANSYS和FLUENT软件对计算域进行求解。求解前边界条件设置为:近壁采用标准壁面函数,给定质量流量的进口,给定相对大气压为0Pa出口,设定最大残差小于10-3的收敛精度。壁面边界条件采用非滑移边界条件,使用多参考系模型MRF处理叶轮区域的转动,转动速度为叶片泵的额定转速。求解前求解的参数设定为:压力、速度耦合方式采用SIMPLEC算法,压力、动量等参数采用一级迎风格式。模型采用描述流体流动规律的连续性方程、动量守恒方程作为求解方程。
连续性方程:

动量方程:

式中:ui、uj—各轴平均速度;
p*—等效压力;
ρ—流体的密度;
με—流体的黏度。
目前有多种湍流模型用于不同湍流运动的模拟,在叶片泵CFD流场模拟中能量表现为热传导。水流是不可压缩流体且热交换量很小,标准k-ε湍流模正好能够表征流动的这种特点,且在边界层流动、管内流动、剪切流动等较大的范围内应用具有足够的精度,所以本模型采用标准k-ε湍流模型进行计算域流动特性的模拟。在FLUENT软件中对方程求解时监视压力速度迭代残差过程,如图4所示。图4中虚线表示压力残差迭代过程,实线表示速度残差迭代过程,两曲线迭代步数n大于40以后,均方根残差δ小于0.001,此时计算达到稳定状态。
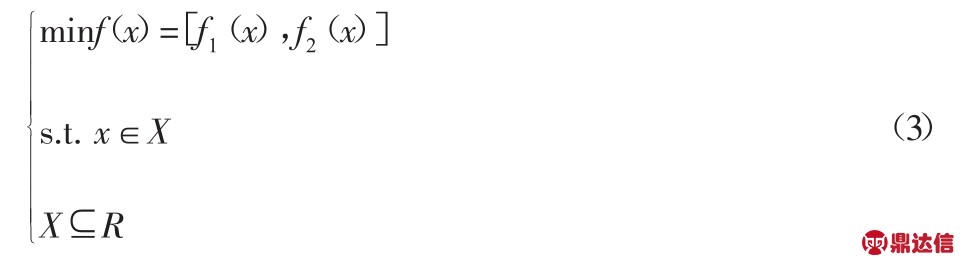
图4 压力速度迭代残差曲线
Fig.4 Iterative Residual Cure of Stress and Speed
基于FLUENT软件对设计叶片进行了数值模拟,模拟时采用的介质为水,在给定流量为290m3/s的情况下,获得了叶片工作面压力云图、背压面压力云图、进出口边速度矢量分布图、叶片不同安放角时压力变化曲线、叶片矢量图以及模拟图形,如图5~图9所示。
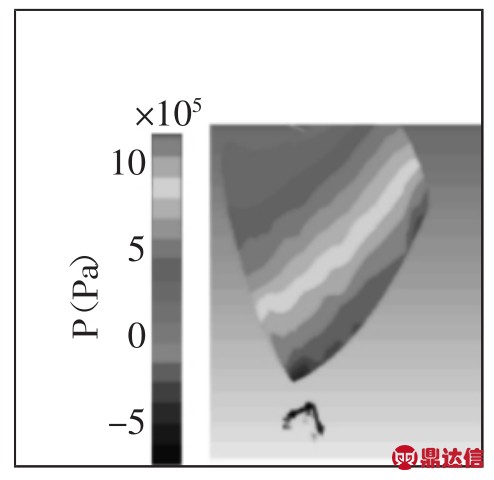
图5 叶片工作面压力云图
Fig.5 Stress Nephogram of Blade Stress
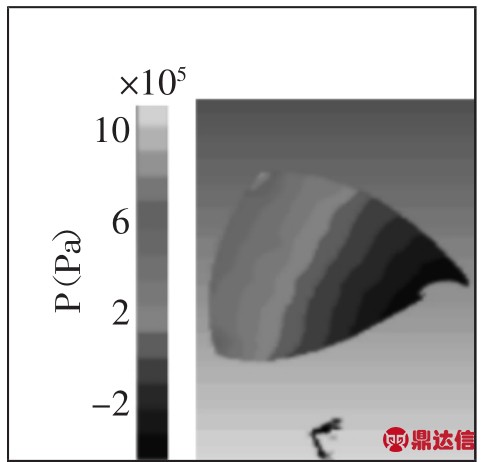
图6 叶片背压面压力云图
Fig.6 Stress Nephogram of Blade Back Surface Pressure
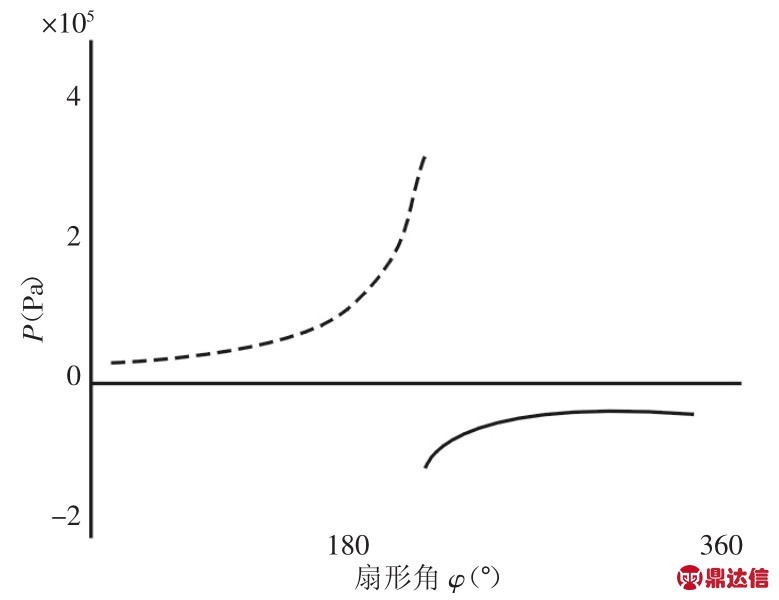
图7 叶片进出口边压力分布图
Fig.7 Distribution Chart of import and Export Blade Side Pressure
叶轮叶片工作面压力云图,如图5所示。从轮毂至轮缘压力逐渐变大,在叶轮轮毂处出现最低压力,在轮缘处出现最高压力,靠近轮缘处具有更大力臂,轮缘处较大的压力有利于叶片输出更大的功率,这些与实际情况相符。
叶片背压面的压力云图,如图6所示。背压面整体压力比工作面压力小,并且由轮缘到轮毂逐渐变小。由于叶片头部具有较大叶片包角,叶片面积增加,单位负荷减小,在靠近轮毂附近出现压力最小值,此处区域空化、空蚀最严重。
叶片轮毂附近水流沿进出口边压力变化曲线,如图7所示。其中虚线为工作面进口边到出口边压力变化曲线,并且由进口到出口压力逐渐变小;实线为背压面出口边到进口边压力变化曲线,并且由出口到进口压力逐渐增大。比较实、虚曲线知道最小压力在叶片轮毂背面出口边附近,在此处最容易出现空化、空蚀,因此在实际叶片泵运行中要检测此处叶片小面积剥落与磨损情况。
图5~图7为叶片在特定某安放角时测得最小压力,为满足调节流量,叶片需要在不同安放角处变化。在模型相同的设置条件下,通过使叶片绕轮毂到轮缘轴线旋转不同角度,得到叶片最小压力随角度变化时的曲线,如图8所示。
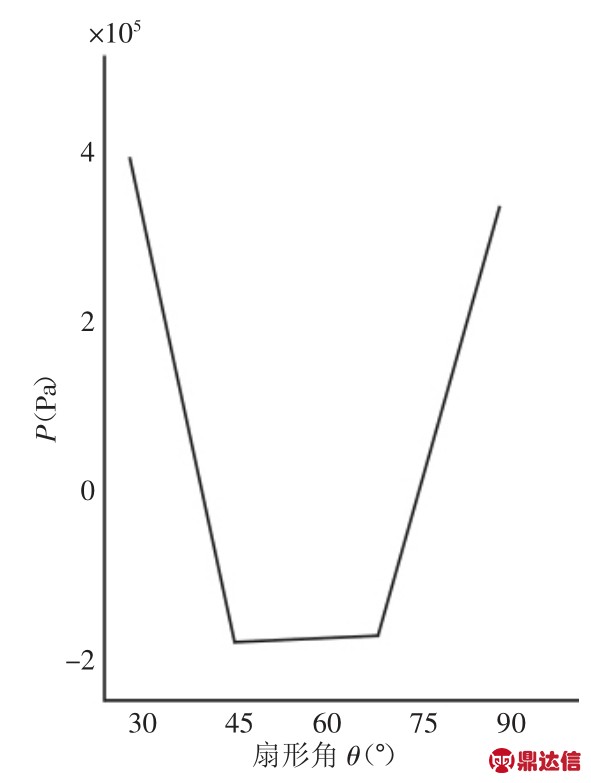
图8 叶片不同安放角压力变化曲线
Fig.8 Stress Changing Curve of Different Blade Angle
通过图8可以看出叶片安放角在之间叶片压力最小,此区间的叶片安放角是空化、空蚀最严重的的位置,从图中还可以看出叶片安放角越靠近空化、空蚀越轻。
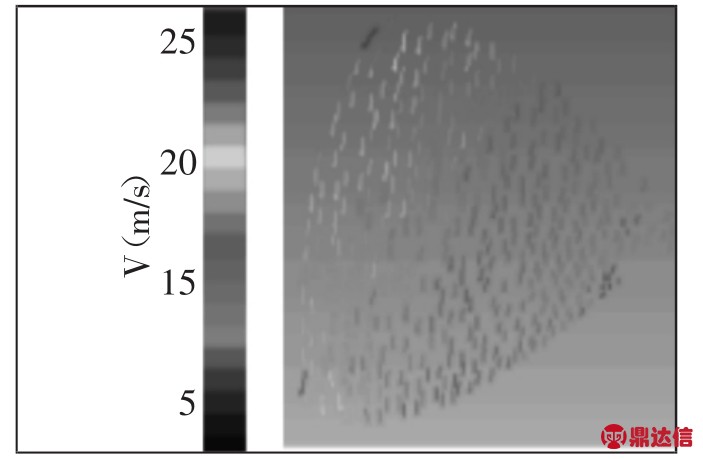
图9 叶片速度矢量图
Fig.9 Vector Diagram of Blade Velocity
叶片安放角靠近时得到叶片速度矢量图,如图9所示。由图可发现叶轮速度由轮毂到轮缘逐渐增大,速度矢量均匀过渡,但在叶片头部周围有一定的撞击,存有回流旋涡现象出现;叶轮出口存有较大径向速度,有较大程度上的能量损失,这证明此处叶片泵效率较低。
4 优化分析
在设计叶轮的参数时发现降低叶片泵空化、空蚀的条件与提升叶片泵效率的条件是相互矛盾的,单纯的追逐一方面的性能会给另一方面造成不利的结果。现以叶片泵效率为最大目标、空化空蚀为最小目标建立多目标函数,通过计算求解获得最佳叶轮的参数。该多目标函数模型表述为:
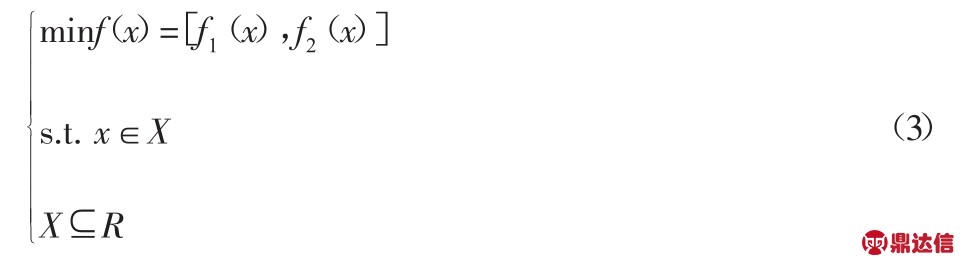
效率最大表征函数:

空化、空蚀最小表征函数:

进出口能量损失最小时叶片泵理论扬程控制方程:

为解方程补充叶片泵摩擦方程:

在计算前,对每个分目标进行分配权重,权重分配办法结合遗传算法,然后统一各分目标:

式中:HL—泵的扬程;
S—水力损失;
n—泵的转速;
ΔPd—摩擦损失;
P—轴的功率;
k、k1、k2—修正系数;
Q—流量;
ηv—容积效率;
D0—叶轮进口当量直径;
D1—叶轮进口直径;
D2—叶轮的出口直径;
μ—叶轮圆周速度;
σ—滑移系数;
β—叶轮出口角;
b—叶轮出口宽度;
φ—叶轮出口排挤系数。
将式(5)~式(8)放到MATLAB中计算,求解得到表2的优化数值。从表2中可以看出增大叶轮进口直径和叶轮进口宽度能够减小叶片的空蚀,这是因为进口水流速度减小使空蚀影响变小。通过式(4)和式(8)知道增大进口安放角、减小出口安放角能够提高叶片泵的效率。
表2 叶片泵参数优化前后比较
Tab.2 The Comparison of Before and After of Vane Pum p Parameter
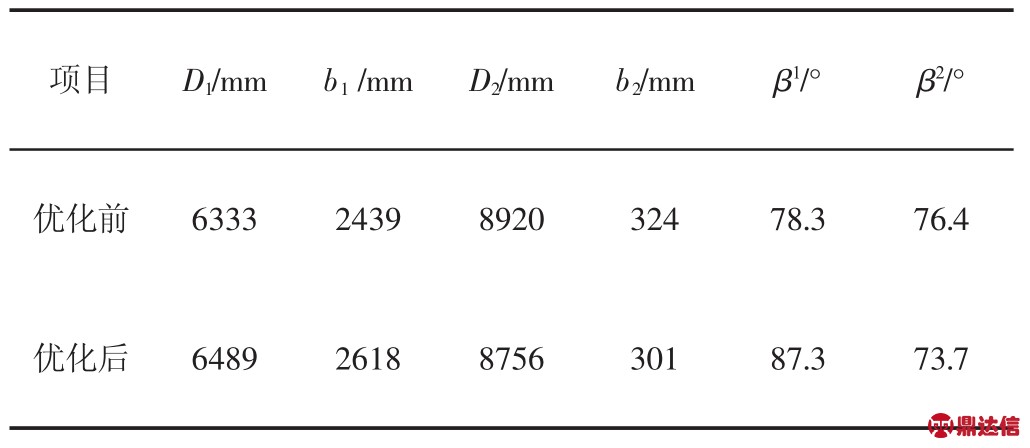
5 结语
(1)基于环形叶栅理论建立了叶片三维模型;采用FLUENT软件对含有叶片泵叶轮段进行了湍流流场分析;通过云图能够快速找到空化空蚀最严重的位置;绘制出了叶片不同安放角处压力曲线,该曲线指出了空化、空蚀最大危险安放角运行区,以上研究对泵的实际运行起到指导作用
(2)对叶片泵主要设计参数进行了优化,解决了降低泵的空蚀与提高泵的效率的矛盾问题。通过仿真优化分析降低了叶片泵研发周期,为以后的叶片设计提供了重要参考。