摘要: 基于RNG k- ε紊流模型和雷诺时均N- S方程,运用流体计算CFD软件对钟型进水流道的轴流泵装置进行三维流动数值模拟以及水力性能的优化设计。通过先局部后整体的方法先单独对钟型进水流道进行优化,然后在整体泵装置内对弯管式出水流道进行优化,对进、出水流道进行三维参数化建模,进水流道以出口断面速度均匀度和水力损失为目标函数,出水流道以泵装置效率为目标函数,针对设计流量工况点,分别对进水流道和出水流道各控制参数方案进行数值模拟计算,分析不同控制尺寸对进、出水流道水力性能的影响。最后通过模型试验对优化方案数值计算结果进行可靠性验证。数值模拟和模型试验结果表明,优化后钟型进水流道的水力损失由0.348 m降低到0.148 m,钟型进水流道出口流速均匀度由54.59%提高到93.35%;弯管式出水流道的水力损失由0.464 m降低到0.415 m,通过优化流态得到了改善。模型泵装置试验在叶片安放角0°时,设计工况下泵装置效率达到74%,泵装置最高效率为76.47%,高效区运行范围较宽;进出水流道无漩涡产生,流态均匀,数值模拟和模型试验外特性曲线误差在5%以内,进水流道水力损失曲线趋势相同。运用数值模拟优化计算钟型进水流道的轴流泵装置,缩短了试验周期,节约了成本,可为同类泵站的设计和安全运行提供参考。
关键词: 钟型进水流道; 轴流泵装置; 数值优化; 模型试验
0 引言
轴流泵是一种大流量、低扬程泵,在平原地区灌溉排涝及城市供排水、排污等方面被广泛使用[1],钟型进水流道纵向高度低,减少了泵站的挖方深度,可以节约工程投资[2-3]。但钟型进水流道往往难以设计钟型的形状,设计不好将导致叶轮进水条件不好,轻则影响泵装置的运行效率,重则导致水泵发生汽蚀,产生噪声、振动等不利于机组运行的状况[4],对机组的高效、稳定、安全运行是极大的威胁,故需要在设计阶段对泵装置进行三维流动的预测、研究和必要的优化。
杨帆等[5-6]通过数值模拟对大型轴流泵装置进行了计算。汤方平等[7]以模型试验为主配合CFD分析泵装置,认为能够比较全面地得出泵装置的水动力性能。陶海坤等[8-9]通过数值模拟的方法对半圆形和蜗形两种钟型进水流道吸水室内部流动进行了研究,并在流场数值模拟的基础上对这两种吸水室的后壁距进行了分析。何钟宁等[10]采用雷诺方程(RANS)和标准湍流模型,计算了钟型进水流道6种不同喇叭管悬空高度和4种不同流量方案下的流道内流场,分析了钟型进水流道关键部位的流态特征,揭示了流道特征断面的速度分布规律。陈松山等[11]设计了一个钟型出水流道模型,测试了流道的水力损失,观测到流道内的流态。杨帆等[12]基于三维不可压缩流体的雷诺平均Navier- Stokes方程和RNG k- ε湍流模型,应用有限体积法计算了双隔墩钟型进水流道内流场,预测了流道的水力损失并揭示了水力损失规律。葛强等[13]对钟型箱涵流道过流特性及流态进行了试验分析,提出了改善流态的有效措施。李彦军等[14]在肘型进水流道和虹吸出水流道型线数学模型基础上,开发了基于流道设计参数的优化设计软件。陆林广等[15-16]、孙东坡等[17]、梁金栋等[18]、颜红勤等[19]、周正富等[20]、齐学义等[21]也分别利用数值模拟进行了相关的研究工作。
对钟型进水流道优化设计鲜有报道,本文通过CFD数值模拟对某大型泵站立式轴流泵装置内部的三维湍流流动和水力性能进行优化计算,采用ANSYS软件的DM模块[22]建立进、出水流道参数化模型,应用CFX对立式轴流模型泵装置进行数值计算及优化,优化过程按照先局部后整体的优化思路,先优化钟型进水流道,然后通过整体泵装置进行数值模拟,对弯管式出水流道进行优化,分析比较不同方案立式轴流泵装置内部的三维湍流流动和水力性能,预测泵装置性能,最后通过泵装置模型试验验证数值优化的准确性。
1 泵站工程概况
泵站规划单机设计抽排流量13.1 m3/s,设计静扬程5.67 m,水泵叶轮直径1 720 mm,泵站进水流道采用钟型进水流道,出水钢制弯管、扩散管接混凝土流道进压力水箱。根据泵站所选定的水泵水力模型,水泵结构采用标准泵段,根据已有研究成果,确定了泵站主要结构尺寸,比如叶轮安装高程,进、出水流道长度,进水流道底部高程,出水流道顶部高程,进、出水流道出口宽度等。
考虑到泵装置CFD三维流动数值计算需要通过模型试验进行验证,所以本次优化针对模型泵装置展开。根据文献[1],对原型泵装置到模型泵装置进行等nD(n表示叶轮旋转速度,D表示叶轮直径)值相似换算,换算后扬程参数保持不变,设计流量变为398.5 L/s,水泵叶轮直径变为300 mm。
2 三维建模及网格剖分
2.1 计算模型
立式轴流泵模型泵装置采用钟型进水流道、弯管出水流道、进出水流道接进足够长的压力水箱。本文采用ANSYS软件的DM模块对钟型进水流道、弯管出水流道模型按照模型泵装置的流道尺寸(模型泵与原型泵几何尺寸比为0.174)进行参数化建模。图1为钟型进水流道计算模型,图2为弯管出水流道计算模型。
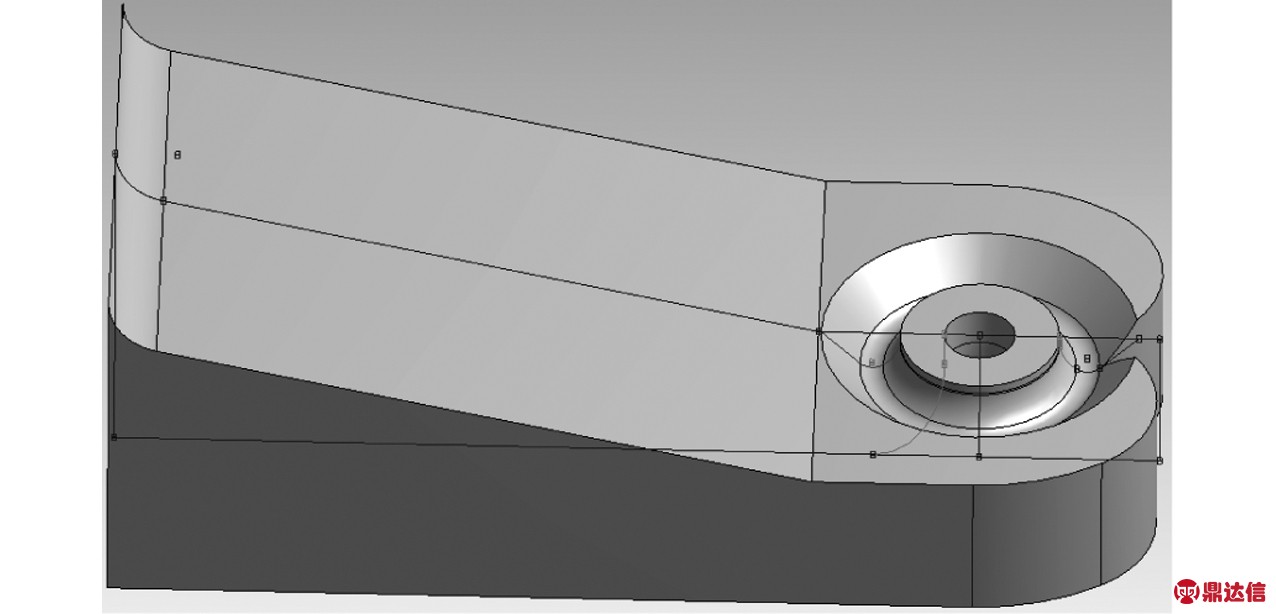
图1 钟型进水流道计算模型
Fig.1 Numerical model of bell-type inlet runner
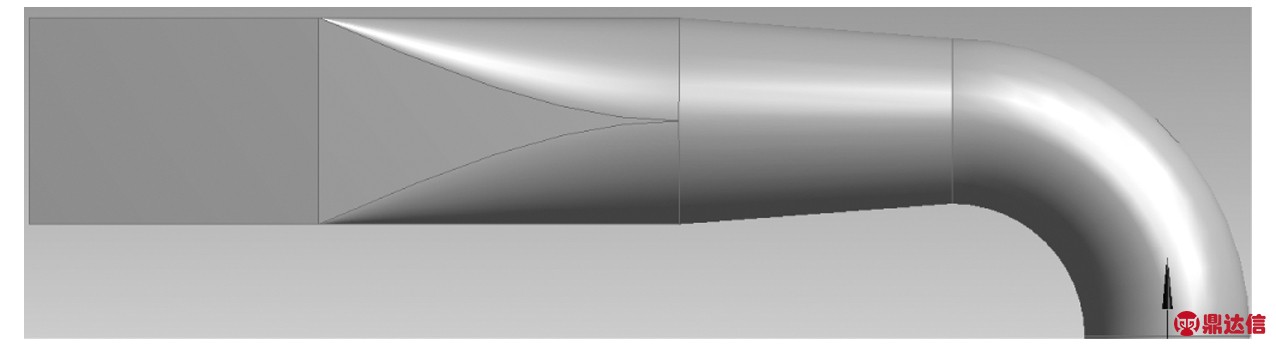
图2 弯管出水流道计算模型
Fig.2 Numerical model of runner of elbow
2.2 网格划分
在ANSYS ICEM软件下对建好的模型进行网格剖分。图3为钟型进水流道采用ICEM生成的自适应能力较好的非结构化四面体网格,对边界层及局部进行加密处理。图4为弯管出水流道由ICEM生成的正六面体结构化网格,对边界层进行局部加密处理,进、出水流道网格节点数和网格数见表1,网格质量均大于0.3。
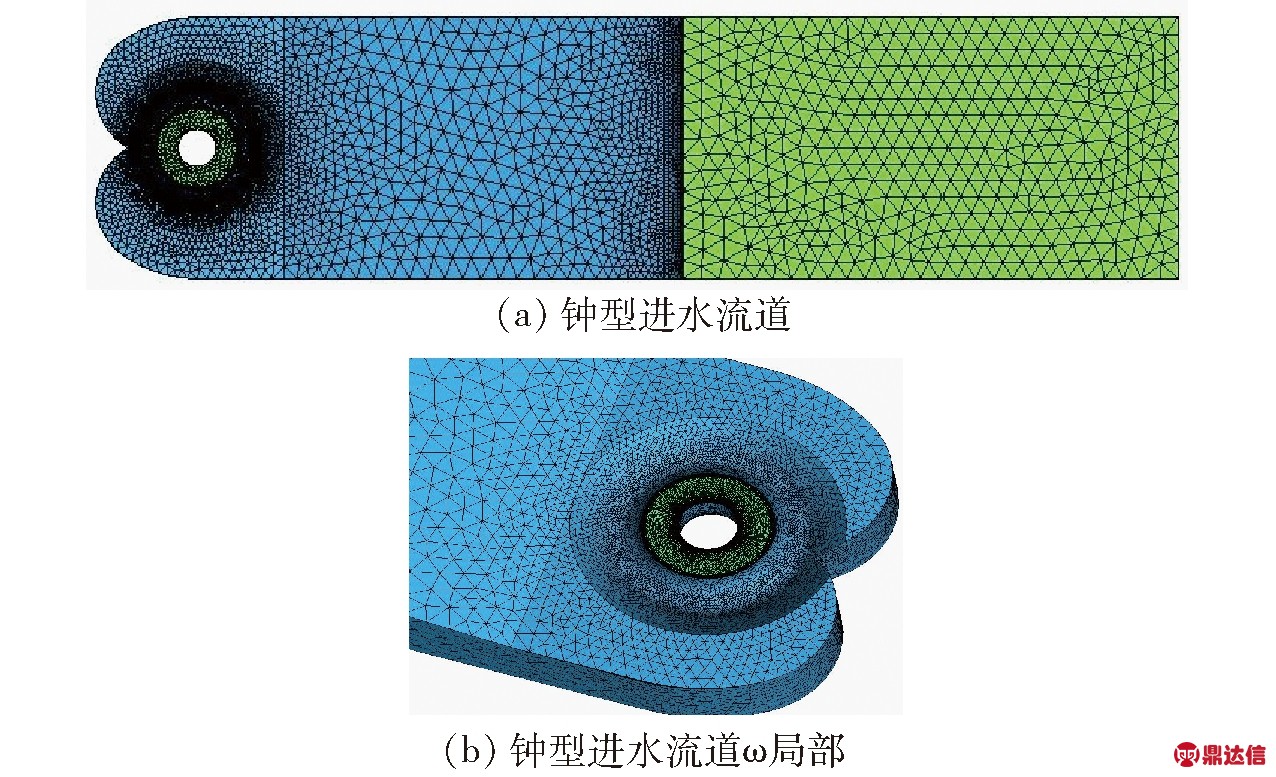
图3 钟型进水流道非结构化网格
Fig.3 Bell-type inlet channel unstructured grid
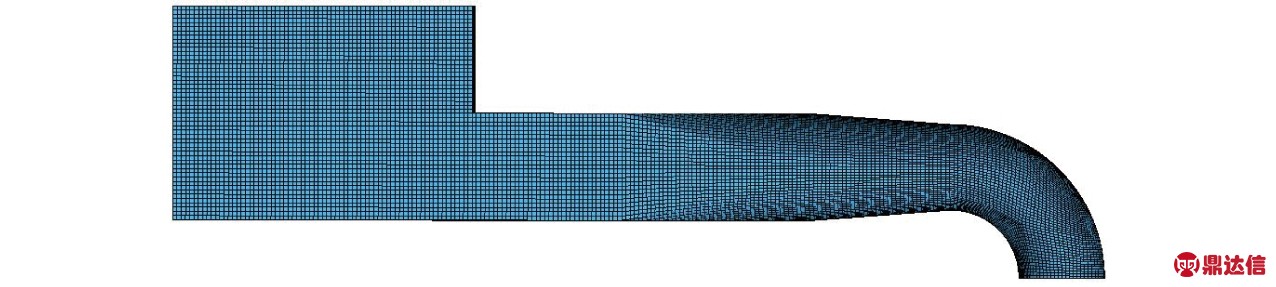
图4 弯管出水流道结构化网格
Fig.4 Structure of elbow outlet channel
立式轴流泵装置数值计算的水力模型叶片数为4,导叶体叶片数为7。采用ANSYS Turbo Grid软件对叶轮和导叶体进行实体建模与网格剖分,图5a为叶轮和导叶模型,图5b~5e为叶轮和导叶网格。叶轮、导叶结构化网格数见表1,建模时按标准模型泵叶轮直径D=300 mm建立,设置单边叶顶间隙为0.2 mm。
表1 网格结点与网格数
Tab.1 Grid node and grid number
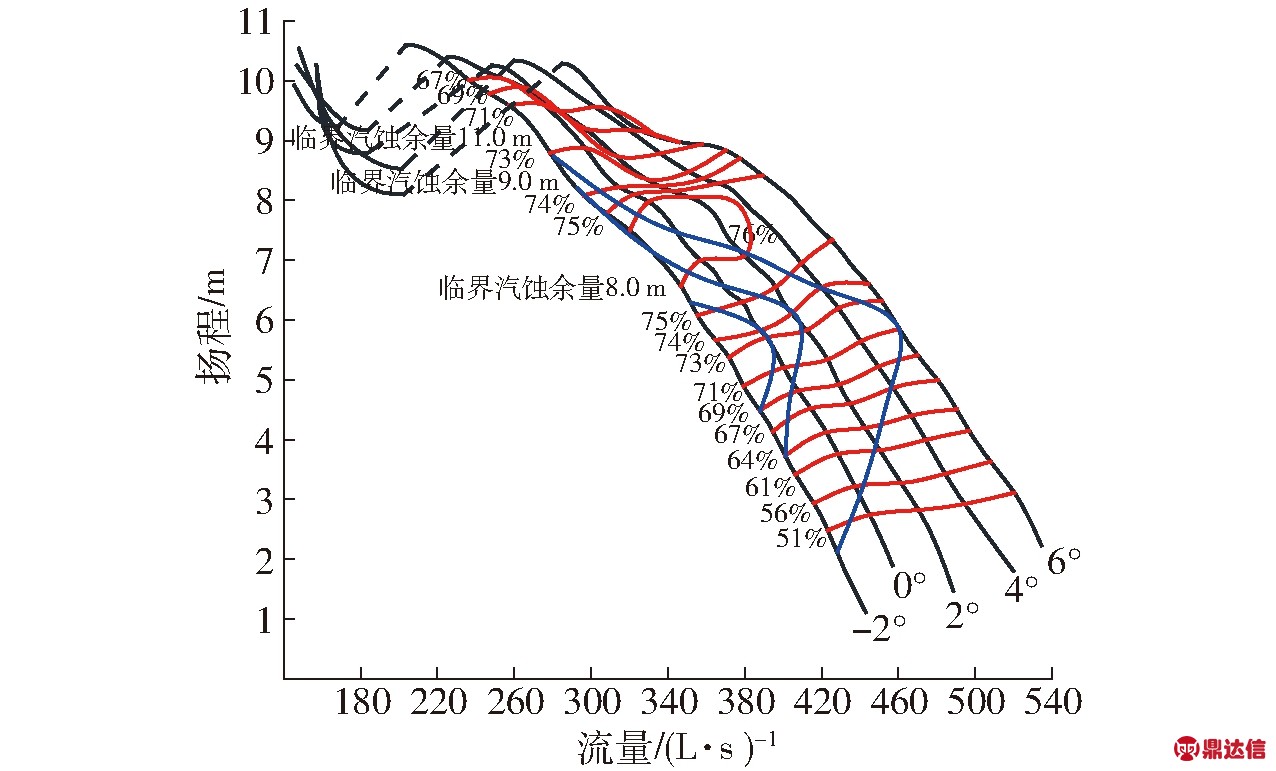
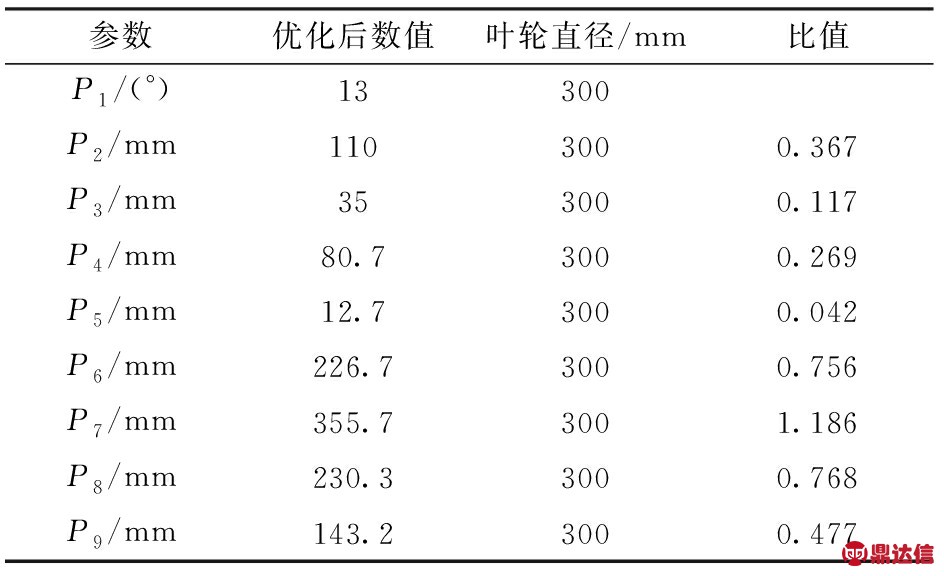
图5 叶轮、导叶模型和网格
Fig.5 Impeller, vane model and grid
根据文献[23],在满足网格无关性要求时,本文不断改变网格数量并对不同网格数量的泵装置效率进行计算,发现当网格增加到一定数量时,泵装置效率趋于稳定,不再随着网格数量的增加而增加。在满足网格无关性要求下,取泵装置叶轮网格数为887 720,导叶网格数为555 513,整个泵装置网格数为2 385 400。
2.3 边界条件与控制方程
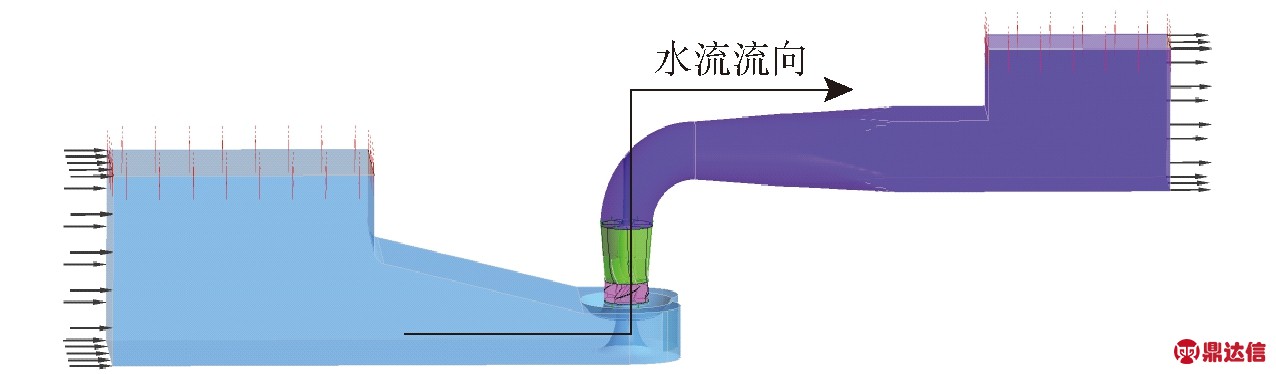
图6 立式轴流泵泵装置运行示意图
Fig.6 Schematic diagram of vertical axial pump operation
导入各分段的网格模型到CFX- Pre中,组装各段模型形成模型泵装置,如图6所示。
设定额定转速1 433 r/min,进口设置为质量流量进口,优化设计时设计工况进口流量设置为398.5 L/s,出口断面采用总压出口,出口总压设置为101 325 Pa。进水前池和出水池的水面为自由液面,将自由表面的速度和紊动能均按对称面处理。立式轴流泵模型泵装置的进出水流道壁面、叶轮的轮毂壁面、外壳及导叶体壁面均设置为静止壁面,应用无滑移条件,近壁区采用标准壁面函数边界条件,对进出水流道表面取无滑移壁面。
动静交界面不考虑旋转叶轮与导叶相对位置不同的影响,采用“Stage”交界面处理叶轮与导叶体之间动静耦合流动的参数传递,控制方程的离散采用基于有限元的有限体积法。扩散项和压力梯度采用有限元函数表示,对流项采用高分辨率格式。泵装置内部采用雷诺平均N- S方程,紊流模型采用考虑了平均流动中的旋转及旋转流动情况的RNG k- ε紊流模型,能更好地处理高应变率及流线弯曲程度大的流动。
在前处理器中写出泵装置进出口断面的压力增量及效率的表达式,作为辅助监控点,在计算过程中实时观察。收敛条件设置残差值为1×10-5,同时监控泵装置进出口断面的压力增量和效率直到稳定为止。
2.4 计算公式
2.4.1 进出水流道水力损失
根据伯努利能量方程引入水力损失hf概念,采用CFD 数值计算得到的流速场和压力场预测过流部件的水力损失,计算公式为

(1)
式中 p1、p2——流道进、出口处的静压,Pa
Z1、Z2——流道进、出口的高度,m
u1、u2——泵装置进、出水流道断面各点流速,m/s
ρ——水流密度,kg/m3
g——重力加速度,m/s2
2.4.2 进水流道出口断面轴向流速分布均匀度
进水流道的设计在兼顾水力损失较小的同时也应为叶轮提供均匀的流速分布和压力分布进水条件。进水流道的出口就是叶轮室的进口,其轴向流速分布均匀度Vu反映了进水流道设计的优劣,Vu越接近100%,表明进水流道出口水流的轴向流速分布越均匀,进入叶轮的水流越均匀同向,其计算公式为
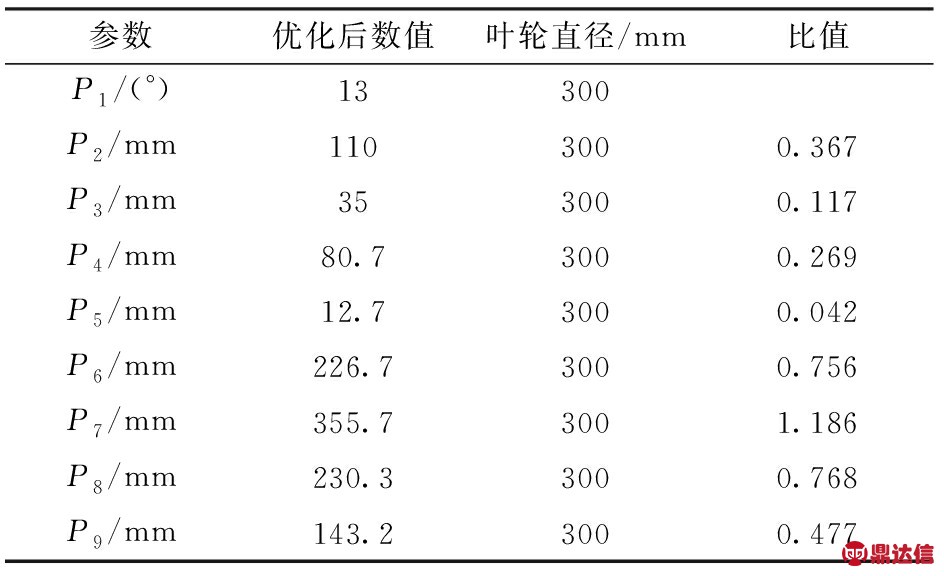
(2)
式中 Vu ——流道出口断面轴向流速分布均匀度,%
流道出口断面轴向流速算术平均值,m/s
vai ——流道出口断面各计算单元的轴向流速,m/s
n ——出口断面上的计算单元个数
2.4.3 泵装置能量性能
根据伯努利能量方程计算泵装置扬程,由计算得到的速度场和压力场以及作用在叶轮上的扭矩预测泵装置的水力性能。泵装置扬程计算公式为
(3)
式中 H1、H2——泵装置进、出水断面高程,m
S1、S2——泵装置进、出水断面面积,m2
ut1、ut2——泵装置进、出水流道断面各点流速法向分量,m/s
Q ——泵装置流量,L/s
泵装置效率计算公式为
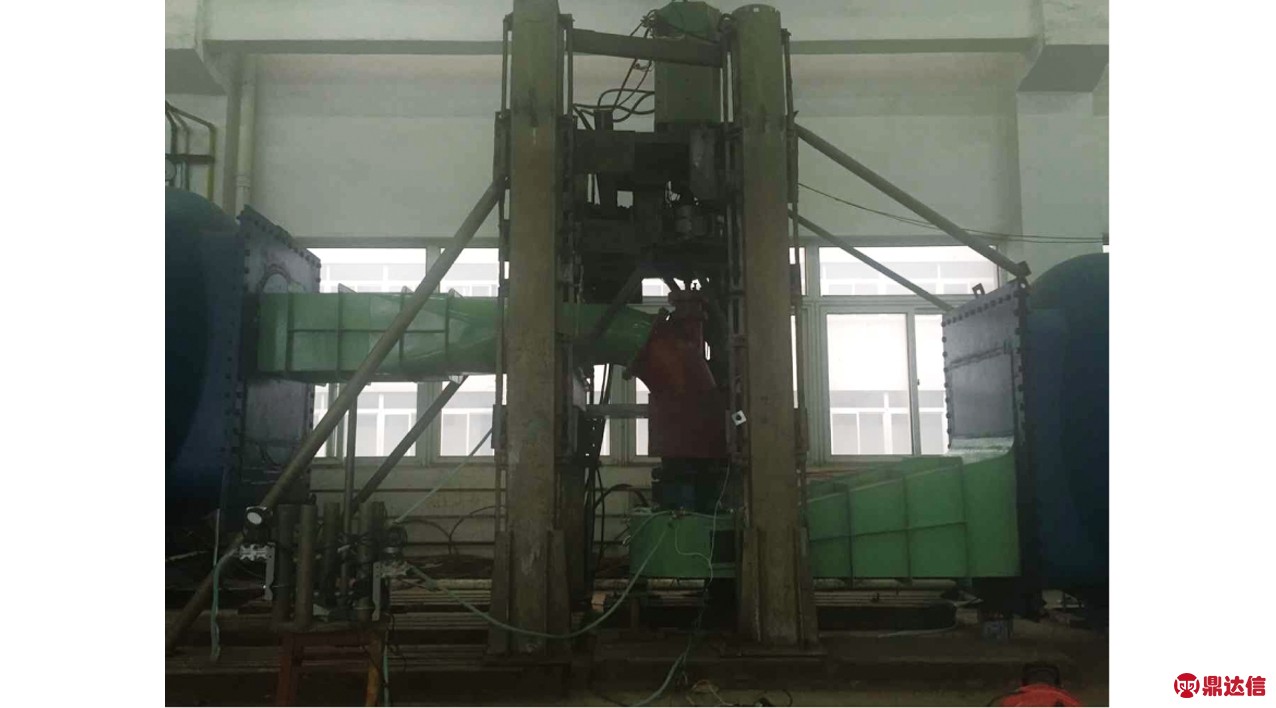
(4)
式中 Tp——扭矩,N·m
ω ——叶轮旋转角速度,rad/s
3 进出水流道优化
3.1 钟型进水流道的优化
通过对初始钟型进水流道进行初步数值计算,发现钟型进水流道在前半部逐渐收缩,流态较好,而在靠近进水流道出口处因流线转向过急,易形成涡带,为防止涡带的形成,需减少钟型后侧低速区,将凹槽处参数以及流体拐角曲率作为9个控制参数作为优化变量进行优化,其中P1为1- 1断面至2- 2断面倾角,P2为凹角直线段长度,P3为凹角远叶轮圆弧半径,P4为凹角近叶轮圆弧半径,P5为ω型后壁圆弧圆心与中心线距离,P6为ω型后壁圆弧半径,P7为后壁与中心线距离,P8为导水锥椭圆长半轴长,P9为导水锥椭圆短半轴长,其示意图如图7所示,以钟型进水流道的水力损失及出口流速均匀度作为优化的目标函数。优化设计方案的选择是在上一个控制单变量最优的条件下进行的,同时变量的变化范围考虑结构尺寸的约束,以探求钟型进水流道控制参数对其水力特性的敏感度。
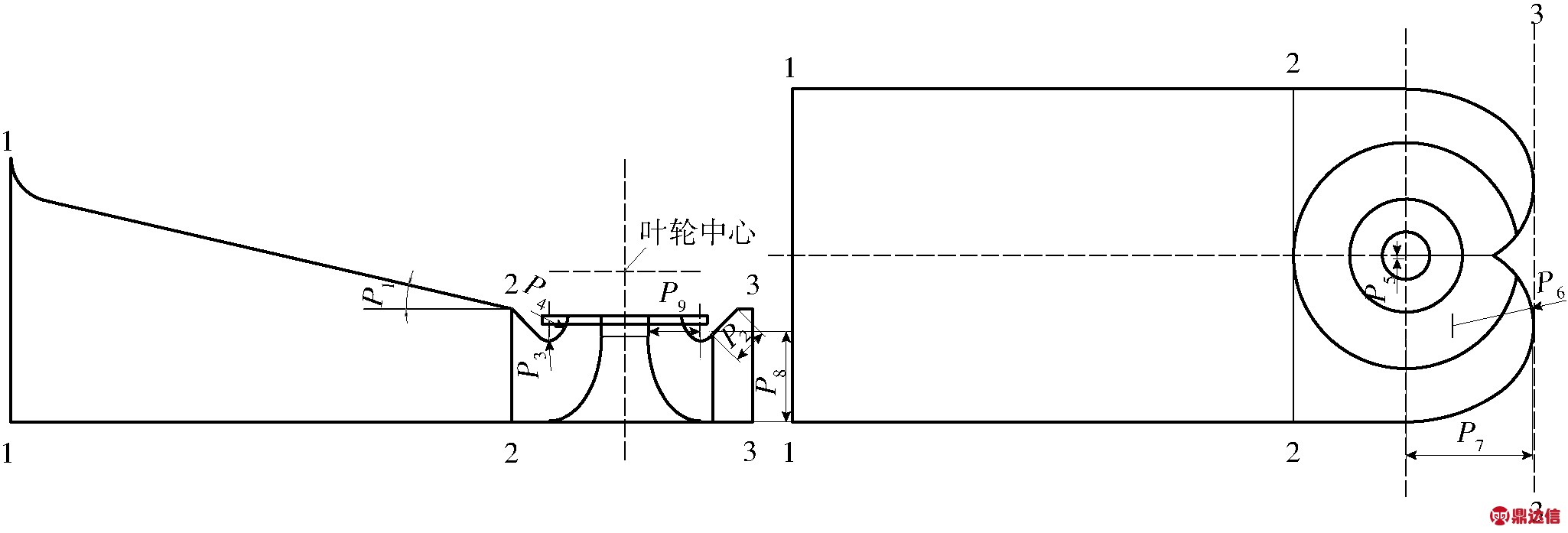
图7 优化参数示意图
Fig.7 Schematic diagram of optimization parameters
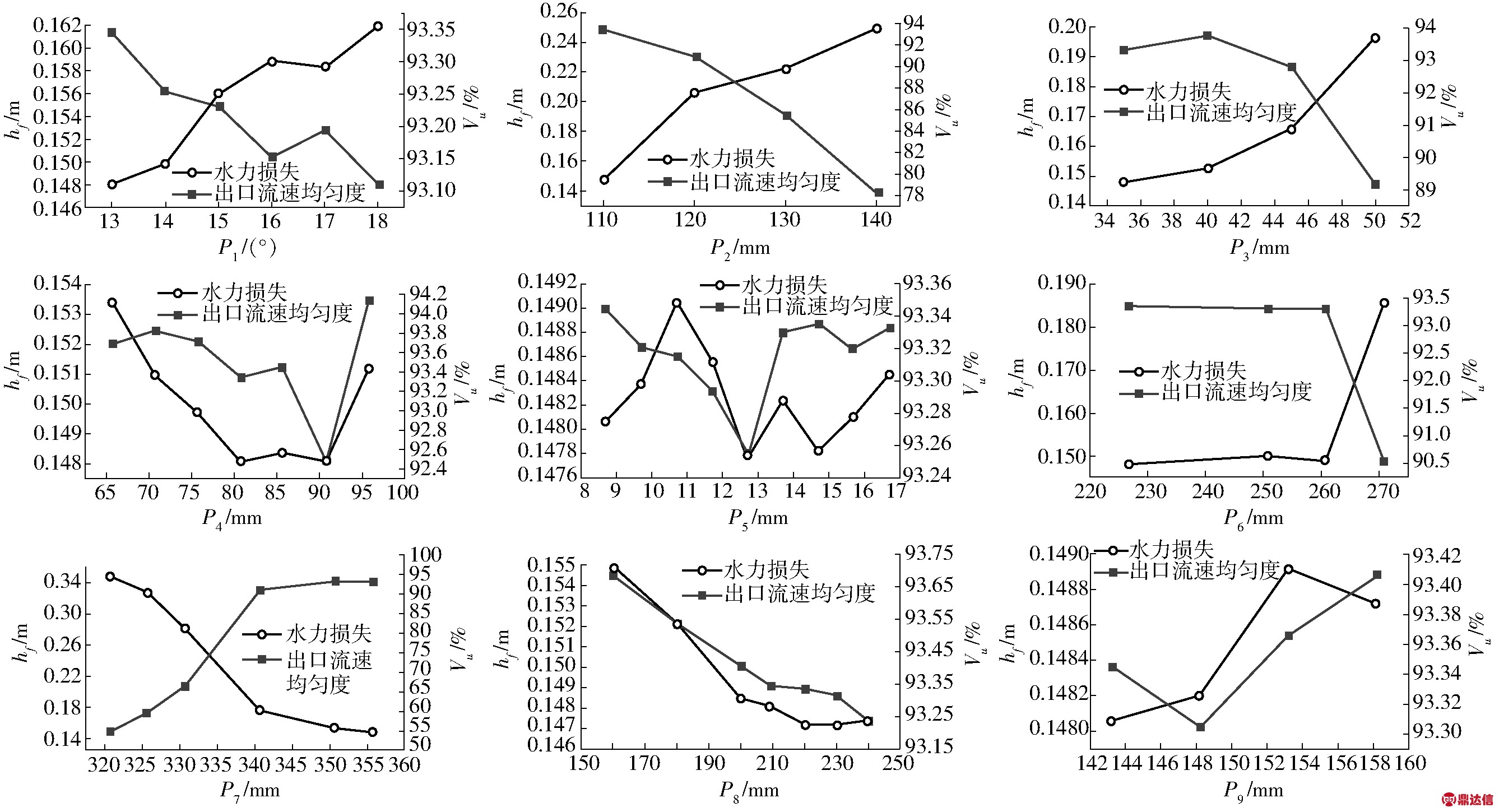
图8 钟型进水流道数值优化水力性能结果
Fig.8 Numerical results of bell-type inlet runner numerical optimization
对于钟型进水流道设计参数的优化是在参数可变区间内,采用控制变量法。钟型进水流道采用参数化建模,模型、网格的更新和数值计算在ANSYS Workbench中自动进行,方案生成和计算较快,极大地节约了优化时间。优化时按照P1~P9参数的顺序,当前一个参数达到最优时进行下一个参数的优化,旨在探究在参数可变范围内最优的数值方案,具体优化方案如表2所示。
通过图8可以看出,各参数水力损失与流速均匀度基本呈现负相关。水力损失最小处,流速均匀度最大,P4、P5、P6、P8和P9在可变范围内对钟型进水流道水力损失和流速均匀度的影响较小,参数P2和P7对钟型进水流道水力损失和流速均匀度的影响最大,对钟型进水流道的优化应该重点关注。优化后得出各最优参数与叶轮直径的比值关系如表3所示。
表2 钟型进水流道模型优化方案
Tab.2 Model optimization scheme of bell-type inlet flow
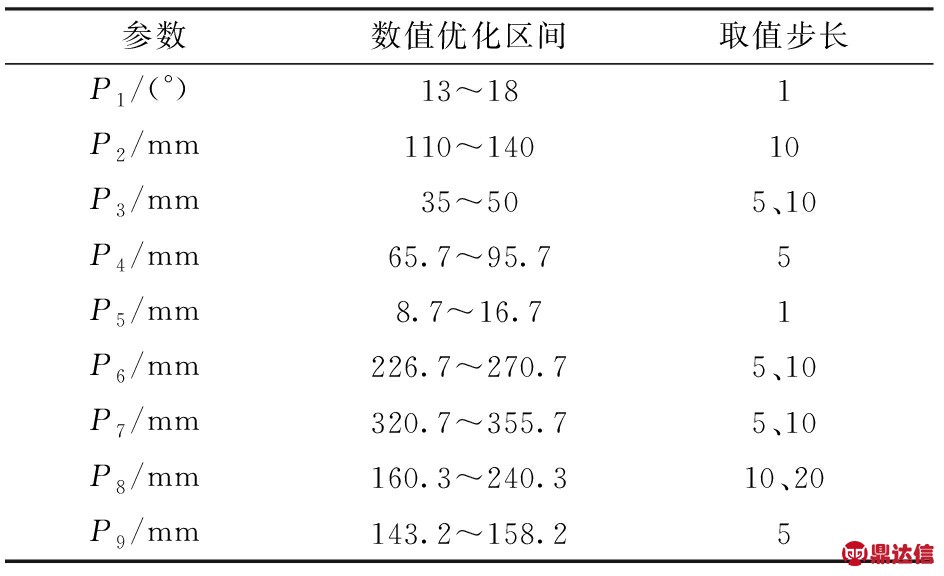
不同方案比较得:最大水力损失时,进水流道水力损失为0.348 m,流速均匀度54.59%,进水条件不好。通过图9可以看出,叶轮进口处轴向流速分布不均匀,且流道左右两部分的流态不对称,叶轮进水条件不好。通过图10可以看出,优化后进水流道出口断面流速分布均匀,对称性较好,为叶轮提供了良好的进水条件,进水流道水力损失降到0.148 m,流速均匀度93.35%,水力损失降低为原来的42.5%,叶轮进口流速均匀度提升为原来的171%,优化后性能得到了较大的提升。
表3 钟型进水流道模型最优参数
Tab.3 Optimal parameters for bell-type inletrunner model
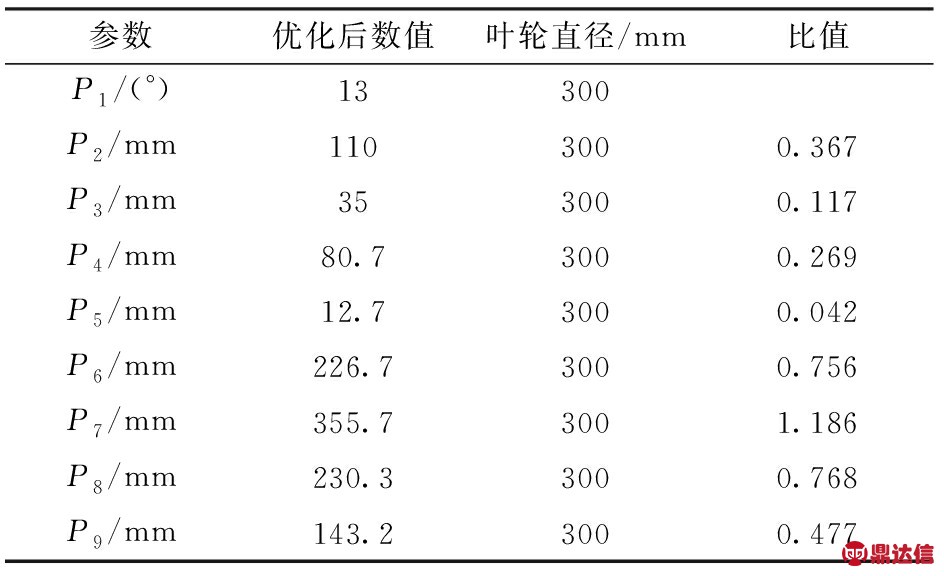
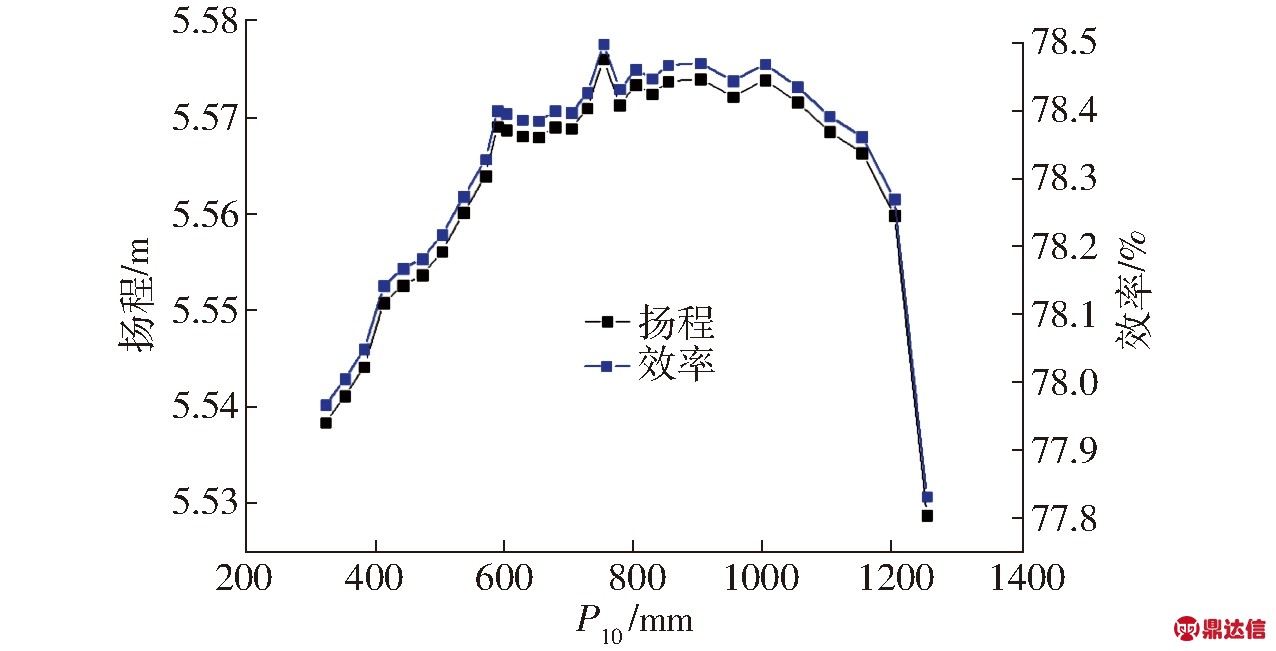
图9 优化前出口断面轴向流速分布云图
Fig.9 Axial flow velocity profile for outlet cross section before optimization
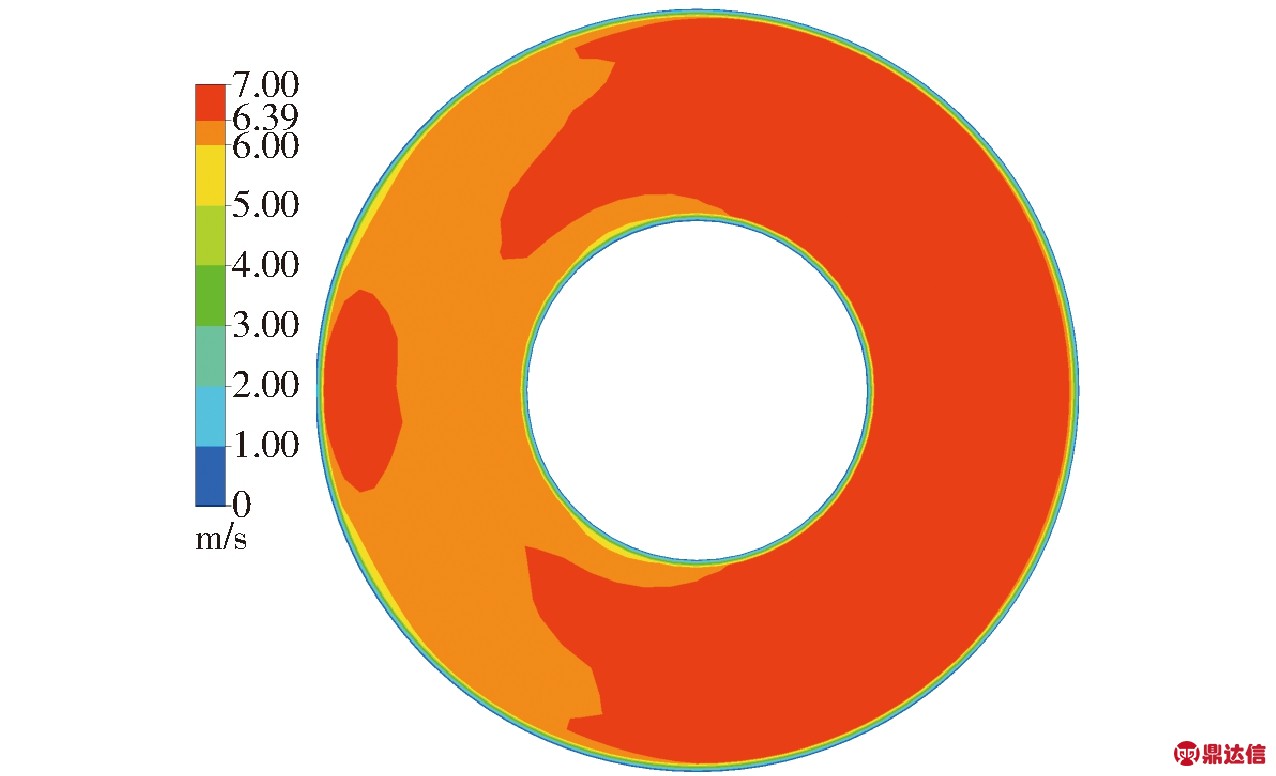
图10 优化后出口断面轴向流速分布云图
Fig.10 Axial flow velocity profile for outlet cross section after optimization
顺序改变进水流道参数P1~ P9,经数值计算分析得到各优化参数下进水流道平均水力损失所占百分比和平均流速均匀度与100%的差值所占百分比分别为(10.24%,7.99%)、(13.75%,15.90%)、(11.03%,9.32%)、(9.83%,7.63%)、(9.73%,7.86%)、(10.42%,8.74%)、(15.48%,26.97%)、(9.78%,7.77%)、(9.75%,7.81%),从中可以看出,参数P2和P7对钟型进水流道水力特性的影响最为敏感,这两个参数与钟型进水流道的水力特性呈现强相关,P1和P3两个参数对钟型进水流道的水力特性呈现中度相关,其余的参数对钟型进水流道的水力特性相关程度较为平均,呈现一般性的相关。
3.2 弯管出水流道的优化
出水流道的优化不同于进水流道,出水流道导叶出口环量存在,水流不能完全垂直出水流道进口断面进入,对出水流道的优化应以泵装置进水流道、叶轮和导叶的三维流场作为基础才更为准确。在优化钟型进水流道的基础上,出水流道为方便施工,不改变90°弯头、流道总长和出口断面尺寸等结构上的限制尺寸,在优中选P11为倒圆角起始控制断面直径、P10为控制断面距90°弯头出口的距离为控制参数,以达到控制出水流道型线的目的,优化目标为泵装置整体效率最高,水流充分扩散平稳,压力梯度变化小,优化参数示意图见图11。
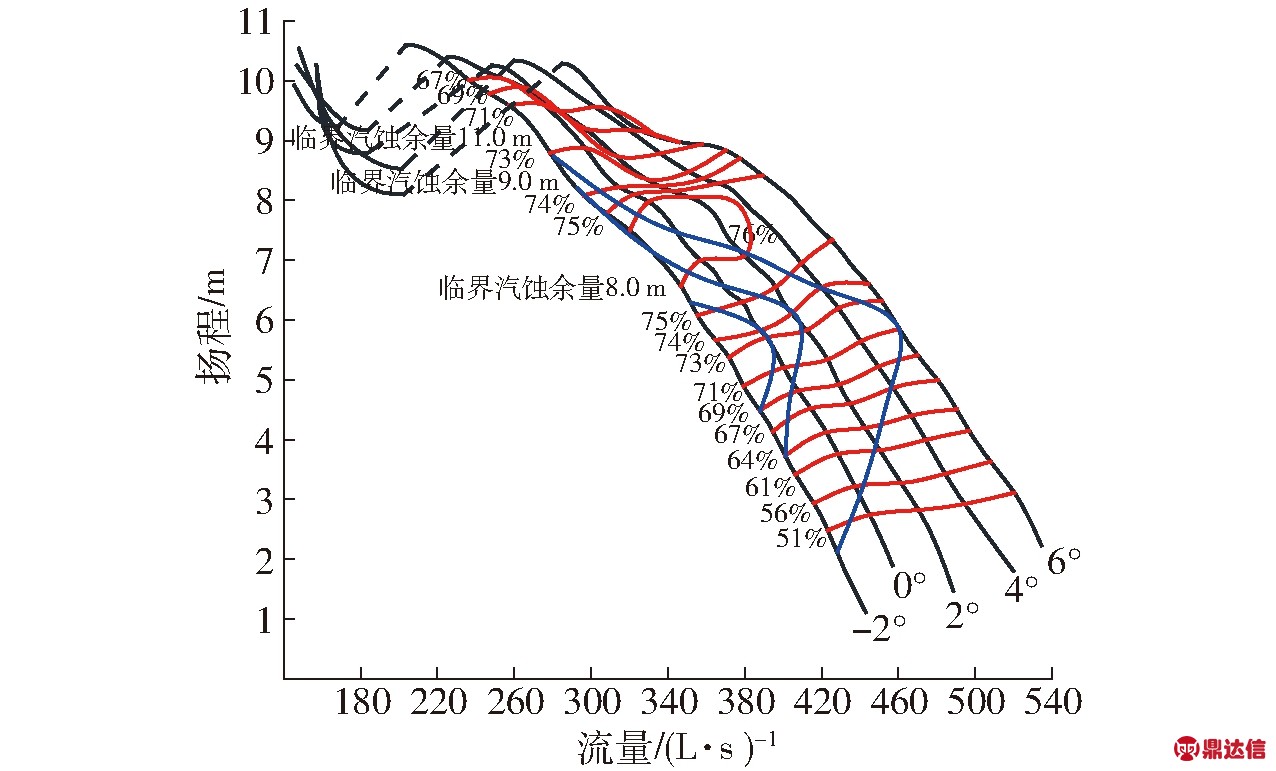
图11 出水流道优化参数示意图
Fig.11 Schematic diagram of optimization parameters for runner
考虑导叶出口速度环量对出水流道性能的影响,对弯管出水流道的优化是在整体泵装置的基础上进行的。设计参数P10和P11的选取,采用控制变量的方法,按照先优化对出水流道性能影响较大的参数P10,当P10达到最优时再优化P11,优化方案见表4。通过对弯管出水流道参数化的建模,在ANSYS Workbench中对模型及网格可以实现更新,自动数值计算,节省了优化的时间,可以探究更多的优化方案。通过优化旨在探究P10、P11与弯管出口直径的最佳比值。
表4 弯管出水流道模型优化方案
Tab.4 Model optimization of outlet runner model of bend

通过图12和图13可以得出,泵装置扬程变化趋势与效率变化趋势相同。圆变方起始断面参数P10和P11均存在一个最优的位置,大于或小于这个位置,泵装置性能均不理想,通过优化出水流道,泵装置整体效率提升了0.8%,从常年运行来看,可以为泵站节约较多的能源,优化效果明显。
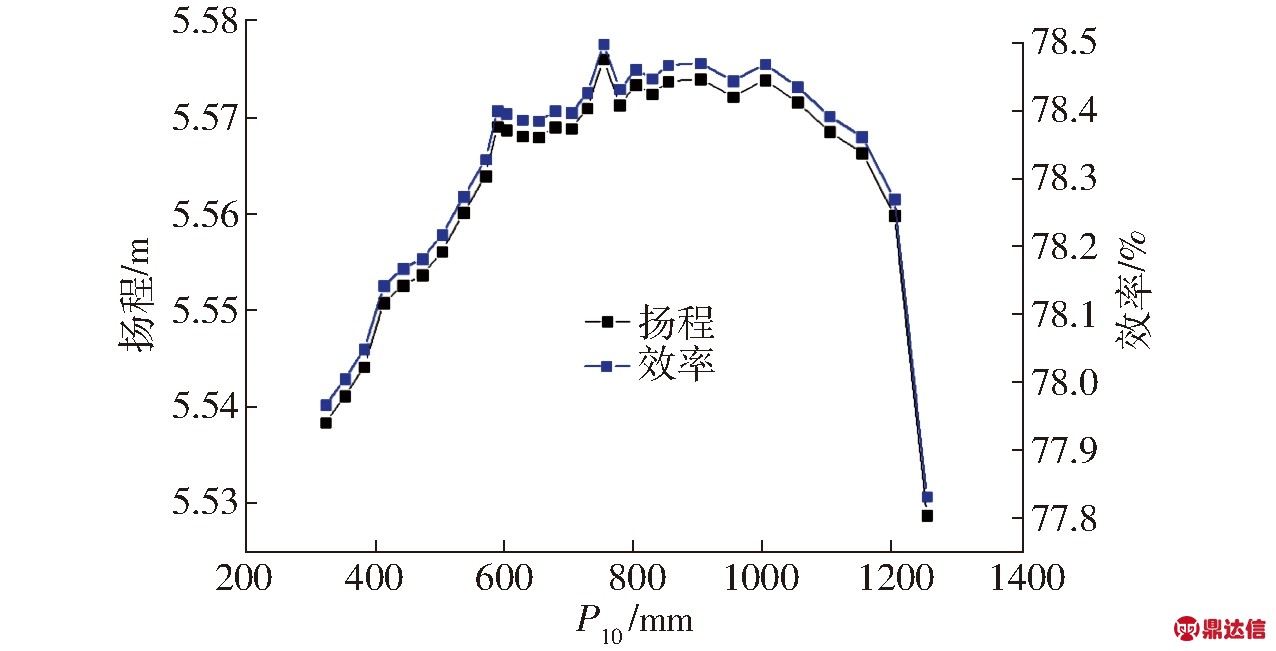
图12 出水流道P10不同方案下外特性曲线
Fig.12 Out of water flow channel P10 under different programs outside characteristic curve
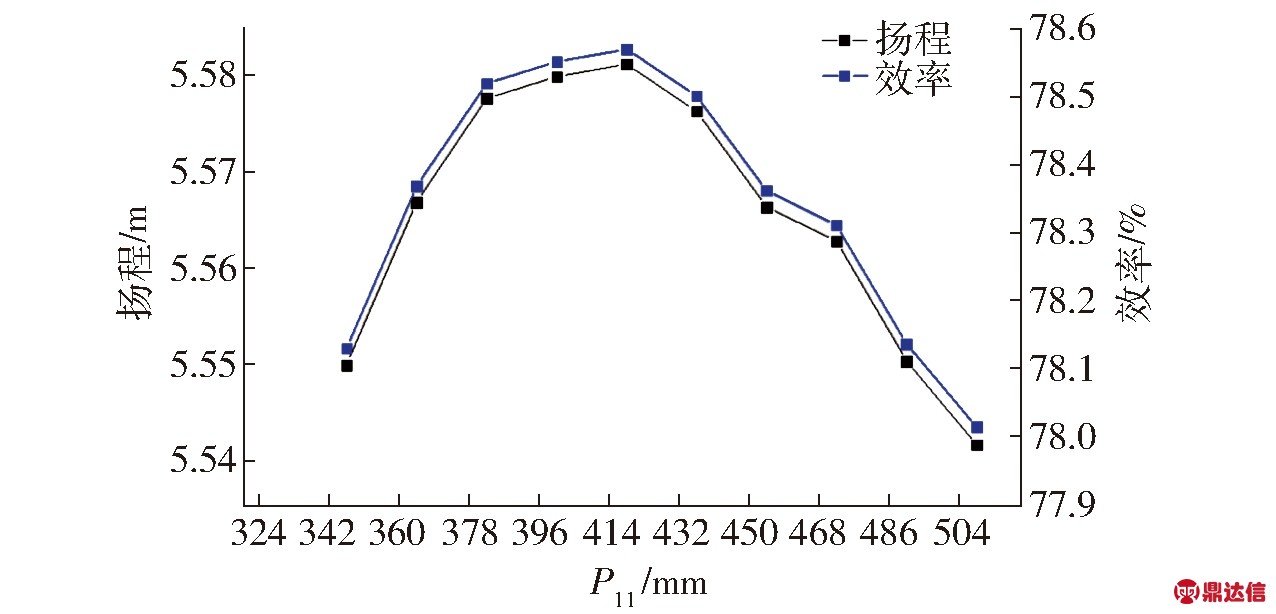
图13 出水流道P11不同方案下外特性曲线
Fig.13 Out of water flow channel P11 under different schemes outside characteristic curve
选取效率最低方案和最高方案的两个方案,在CFX- POST中提取出出水流道静压分布云图,如图14所示。
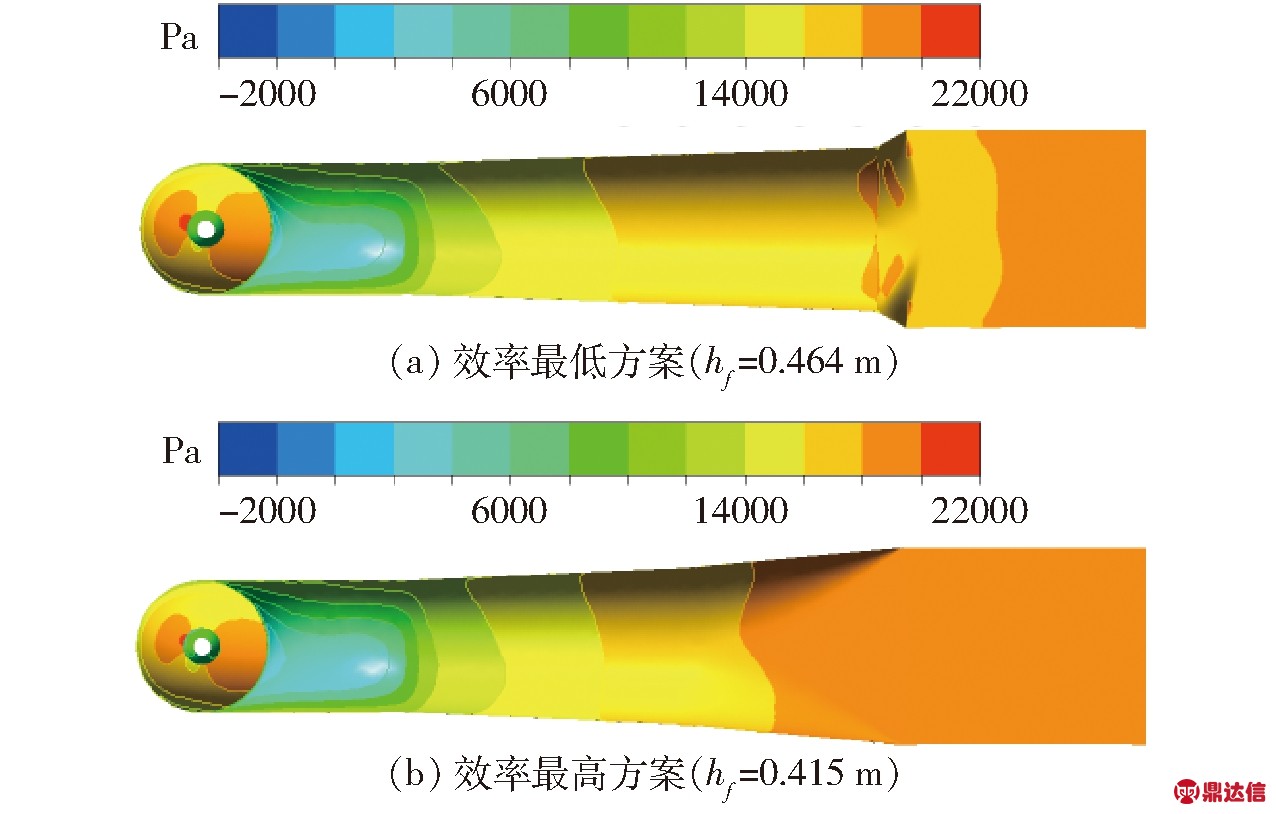
图14 出水流道静压分布云图
Fig.14 Static distribution of water flow distribution
对比分析得出,立式轴流泵泵装置最优方案在设计流量工况下运行时,叶轮、导叶与进、出水流道配合较好,此方案出水流道压力梯度递变均匀,局部的高压区和低压区面积较小。采用扩散管出水形式,有利于导叶出口能量的回收,动压转化为静压,出水流道水力损失较小。
通过优化可知,出水流道的圆变方的起始断面与弯管出口的水平距离P10为弯管出口直径的2.14倍较为理想,圆变方起始断面的直径P11为弯管出口直径的1.19倍较为理想。弯管式出水流道的水力损失由0.464 m降低到0.415 m,泵装置效率由77.8%提升到78.6%,通过优化出水流道流态得到了改善。
4 模型泵装置试验
4.1 试验系统
根据模型泵装置数值模拟结果,将优化后泵装置的叶轮、导叶和进、出水流道模型加工出来进行泵装置试验研究。泵装置试验在扬州大学测试中心的高精度水力机械试验台上进行。试验台为立式封闭循环系统。在该试验台上对本文针对性设计出的水泵水力模型进行了泵装置能量性能试验和汽蚀性能试验。试验台如图15所示。
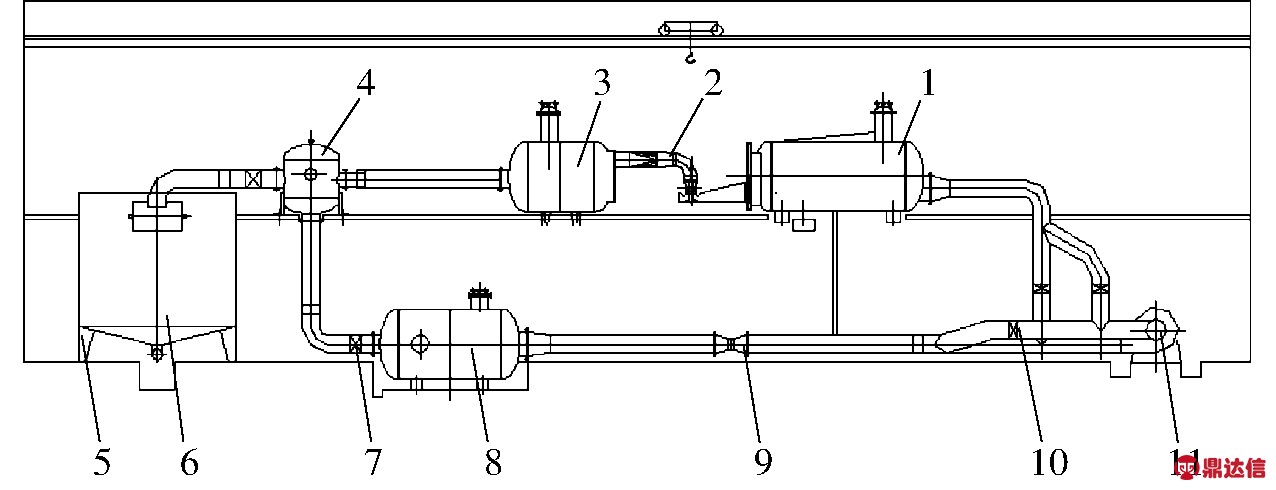
图15 高精度水力机械试验台
Fig.15 High-precision hydraulic machinery test bed
1.进水箱 2.受试泵装置及驱动电动机 3.压力出水箱 4.分叉水箱 5.流量原位标定压力传感器 6.流量原位标定装置 7.工况调节闸阀 8.稳压整流筒 9.电磁流量计 10.系统正反向运行控制闸阀 11.辅助泵机组
模型泵名义叶轮直径300 mm,实际叶轮直径299.8 mm。叶轮轮毂比为0.483,叶片数为4,用黄铜材料经数控加工成型。导叶叶片数为7,用钢质材料焊接成型。进出水流道采用钢板焊接制作,模型泵叶轮室开有观察窗,便于观测叶片处的水流和汽蚀,模型泵装置安装检查,导叶体与叶轮室定位面轴向跳动0.10 mm,叶轮轮毂外表面径向跳动0.08 mm,叶顶间隙控制在0.20 mm以内。模型泵叶轮如图16a所示,模型泵导叶如图16b所示,模型泵装置如图17所示。
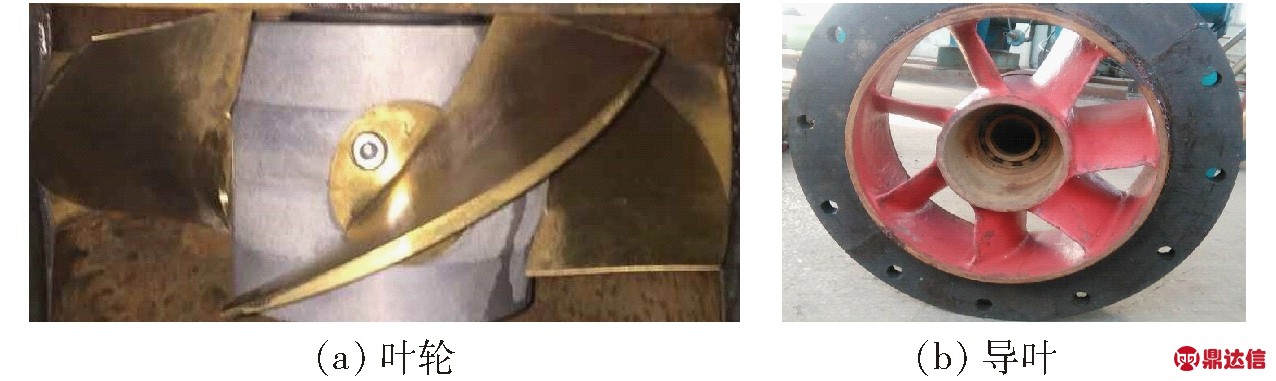
图16 模型叶轮和导叶实物图
Fig.16 Model impeller and guide vane physical map
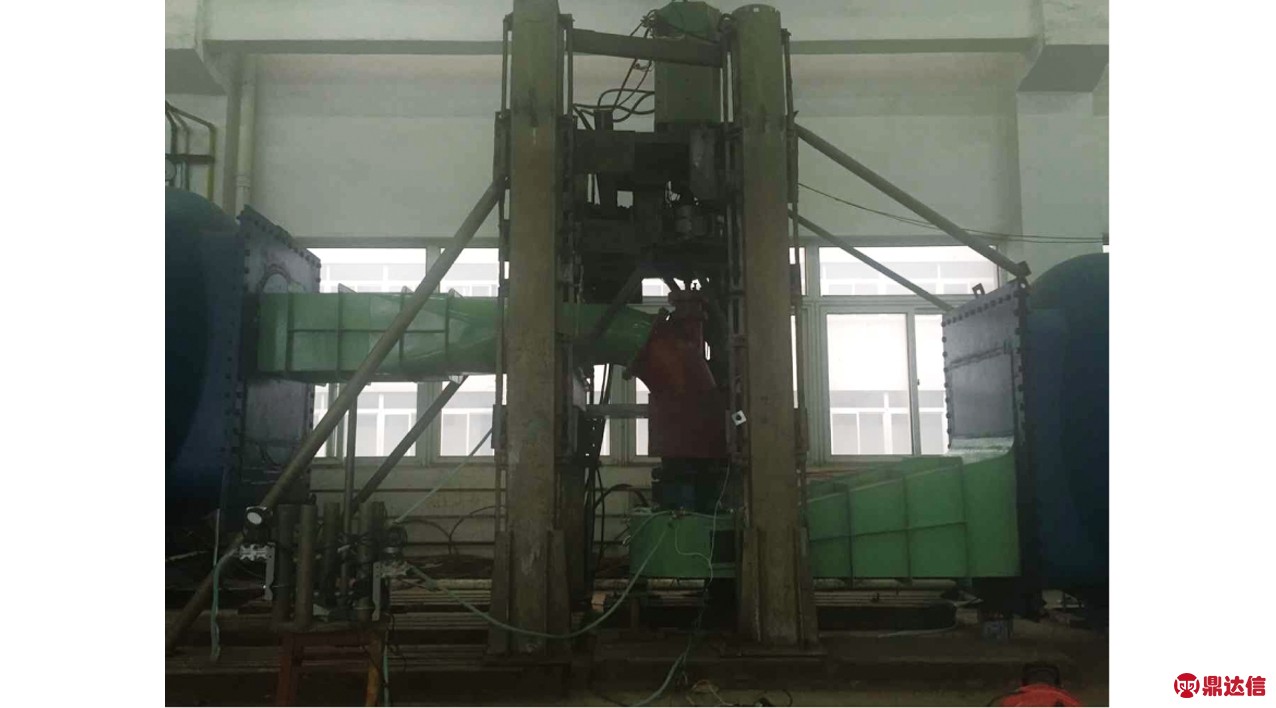
图17 模型泵装置实物图
Fig.17 Model pump device physical map
4.2 测试方法
模型泵装置试验测试内容包括各叶片安放角下模型泵装置能量性能试验和0°叶片安放角下模型泵装置进水流道水力损失试验。试验执行《离心泵、混流泵和轴流泵水力性能试验规范(精密级)》(GB/T 18149—2000)和《水泵模型及装置模型验收试验规程》(SL 140—2006)标准,每个叶片安放角的性能试验点不少于18点,临界汽蚀余量的确定按流量保持常数,改变有效汽蚀余量至效率下降1%时确定。
4.3 测试结果
模型泵段试验测试了5个叶片安放角度(-2°、0°、2°、4°、6°)的能量性能和各叶片角度下不同流量点的汽蚀性能,将结果数据整理成水泵水力模型综合特性曲线,如图18所示。
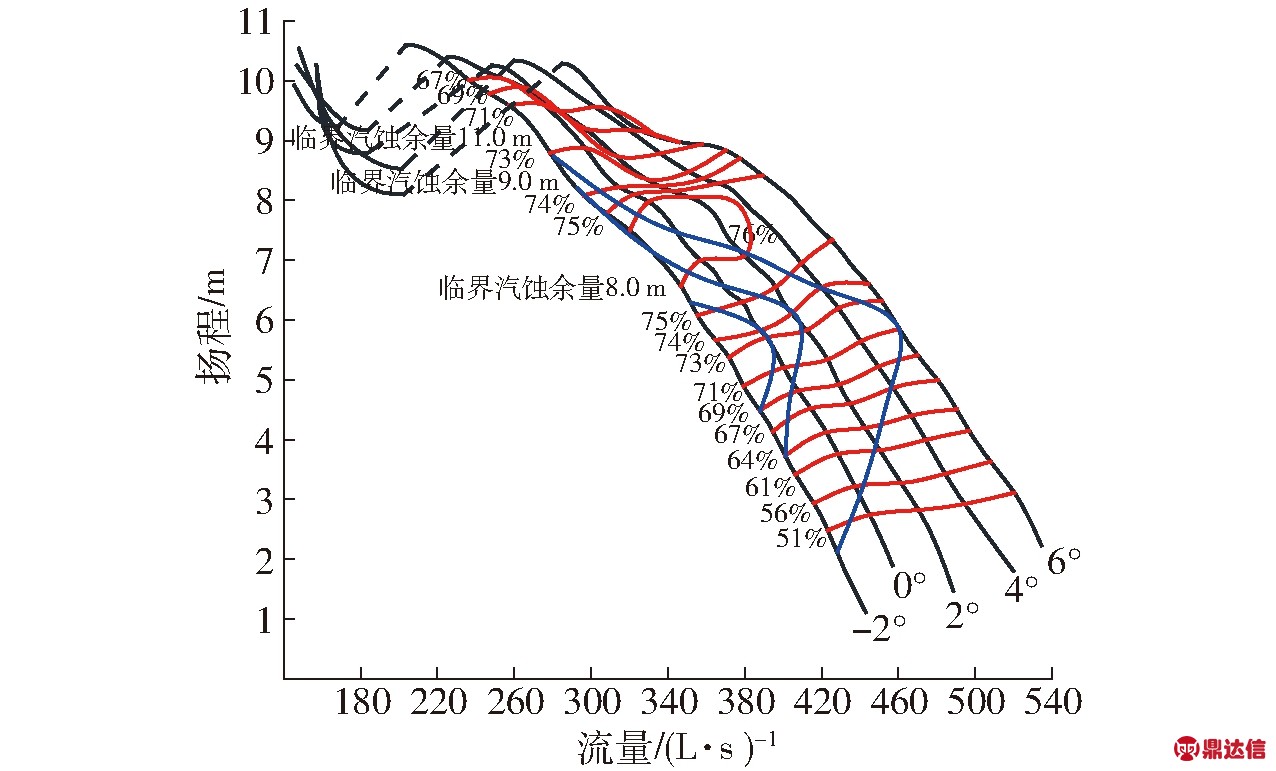
图18 水泵水力模型综合特性曲线
Fig.18 Pump water hydraulic model comprehensive characteristic curves
根据图18水力模型的综合特性曲线可知,泵装置在叶片安放角0°下,设计工况下泵装置效率达到74%,泵装置最高效率为76.47%,高效区运行范围较宽;模型泵装置最大运行扬程超过10 m,满足泵站最大运行扬程7.78 m的运行要求。模型泵装置在叶片安放角0°下,设计静扬程附近汽蚀性能最优,临界必需汽蚀余量在9.0 m以下,满足该泵站对汽蚀的运行要求。如需要考虑闸门槽、涵洞的水力损失可以在水泵水力模型综合特性曲线上保证流量相等,增加扬程来确定叶片角度。
5 数值计算结果与模型试验对比分析
将0°角的数据结果取出与数值模拟结果进行对比,如图19所示。试验测得进水流道水力损失与数值模拟计算得出的进水流道损失对比,得到对比曲线如图20所示。
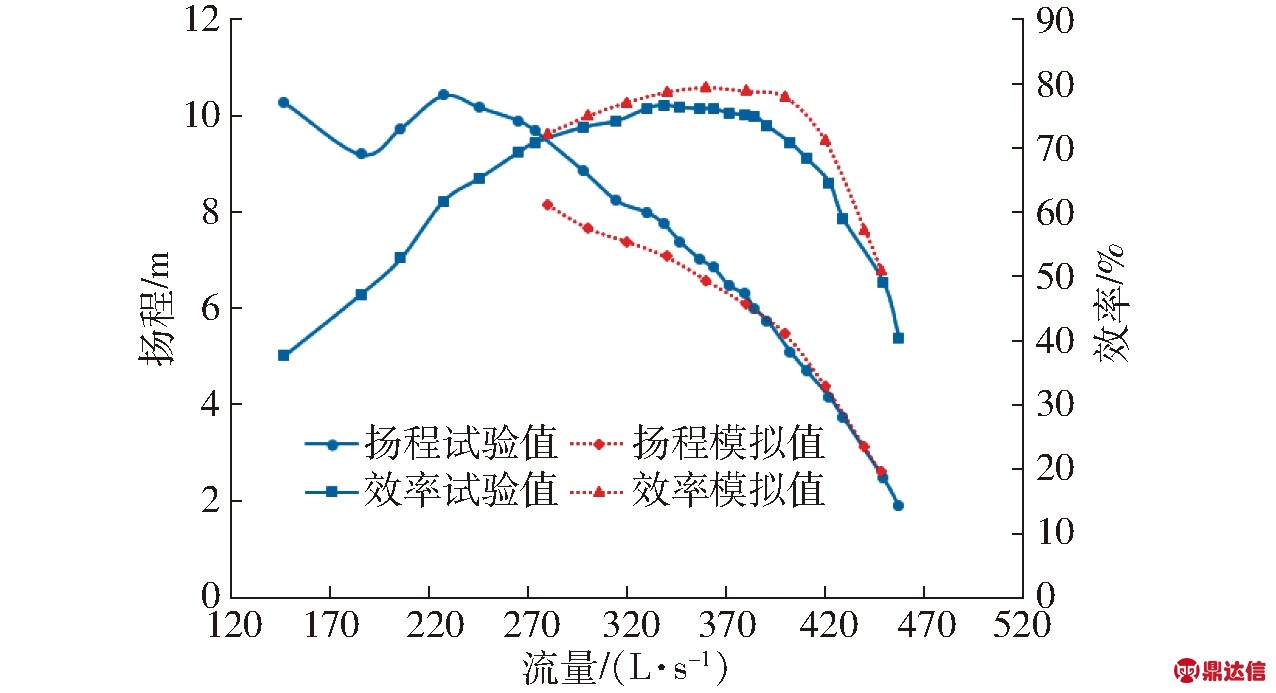
图19 试验结果与数值模拟结果对比曲线
Fig.19 Comparison of test results with numerical simulation results
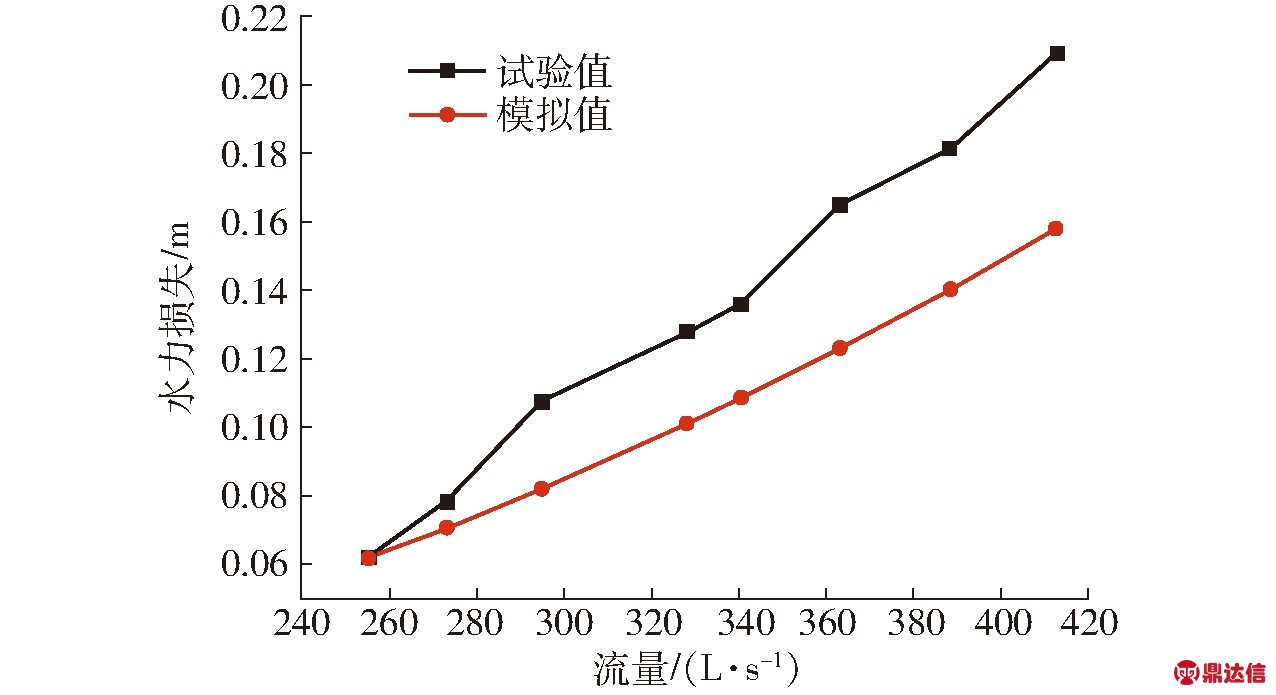
图20 进水流道水力损失试验与数值模拟对比曲线
Fig.20 Comparison of hydraulic loss test and numerical simulation of inlet channel
根据图19、20可知,针对模型泵装置的外特性和进水流道水力损失数值模拟结果与试验结果趋势相同、误差较小,说明针对模型泵装置的数值优化结果是可靠的。数值模拟结果与试验结果得到了相互验证,同时对比分析钟型进水流道内流态稳定,无漩涡产生,水泵运行平稳,说明了对立式轴流泵装置的数值优化计算是准确、可靠的。通过图中也可以看出,数值模拟在大流量和设计工况预测较为准确,在小流量工况的预测不理想,对比数值模拟和模型试验结果可以发现误差最大处不超过5%,能够满足工程的应用,同时本文的优化是基于设计工况进行的,说明数值模拟优化合理、准确、可靠。
6 结论
(1) 基于RNG k- ε紊流模型对钟型进水流道的立式轴流模型泵装置进行了数值优化计算,通过模型试验对比分析,设计扬程、预测扬程与试验扬程基本吻合,针对该泵站模型泵装置的数值优化结果是可靠的。
(2) 优化后钟型进水流道水力损失由0.348 m降低到0.148 m,钟型进水流道出口流速均匀度由54.59%提高到93.35%;弯管式出水流道的水力损失由0.464 m降低到0.415 m,通过优化性能得到了较大提升。进水流道水力损失与出水流道水力损失比较相对较小,合理的出水流道型线是泵装置性能高效的保证,出水流道的优化需要考虑泵出口的实际流场。
(3) 通过优化分析得出,钟型进水流道参数P2和P7对其水力特性的影响最为敏感,设计时应该重点关注。
(4) 设计工况下泵装置效率达到74%,泵装置最高效率为76.47%,泵站设计静扬程处在高效区附近,高效区范围较宽,能够很好地实现泵站扬程波动运行范围内的高效,降低泵站的年运行费用。按照数值模拟优化预测,模型试验验证的方法为泵站的优化设计作指导是准确、可靠的。