摘要: 导叶式离心泵应用范围越来越广泛,迫切需对其稳定性运行及内部非稳态流动机理等相关问题进行探讨与研究。结合数值软件ANSYS-CFX与试验方法,基于SST k -ω湍流模型对导叶式离心泵内部非定常流场进行数值分析,并采用试验方法对其压力脉动特性进行研究,探讨不同流量工况下,压力脉动特性与非稳态流场分布规律。结果表明:导叶进口处压力脉动高于导叶出口处,而蜗壳隔舌处脉动强度小于其出口处;叶轮内压力分布主要受叶轮-导叶动静干涉作用影响;导叶内压力分布同时受动静干涉作用和蜗壳不对称几何形状影响;因叶轮出口尾迹流-射流影响,叶片出口附近出现吸力面静压大于压力面;由于导叶前缘与叶轮尾缘的影响,导叶叶片进口处压力分布极其复杂,规律性较差。
关键词: 导叶式离心泵; 压力脉动; 非稳态流场; 数值模拟
引言
导叶是离心泵中重要的过流部件,广泛应用于多级或单级离心泵中,其中在多级离心泵中导叶主要起压力回收及引流作用,而在单级离心泵中,除上述作用外,导叶还可降低作用于叶轮上径向力。随着社会进步和科学技术的发展,导叶式离心泵的水力性能、运行稳定性及可靠性越来越受重视。
因导叶结构因素,与普通离心泵相比,尤其在偏离设计工况时,导叶式离心泵中叶轮、导叶及蜗壳内均会出现剧烈的湍流流动,并对水泵的水力性能产生较大的影响[1-3]。在较小流量工况时,导叶式离心泵扬程曲线易出现驼峰,且进一步减小流量时,由于叶轮进口处剧烈的非定常湍流流动,可能导致叶轮进口前盖板附近区域出现旋转汽蚀现象,此现象会随着流量逐渐降低而加剧,且逐渐向靠近叶轮进口处的轮毂附近迁移,同时,旋转汽蚀位置的移动会导致泵内能量变化,进而使流量扬程曲线在此处出现正斜率,即部分载荷旋流[4-5]。因此认识导叶式离心泵内部非稳态流动机理有利于离心泵的稳定可靠运行。
目前国内外许多学者主要集中于离心泵导叶结构的研究,尤其针对多级离心泵[6-11],而对于单级离心泵中导叶形式或多级离心泵末级导叶结构及导叶内部非定常流动研究较少。桂绍波等[12]、张永学等[13]研究前置导叶对混流泵水力性能与空化性能的影响,结果表明通过适当的调整前置导叶预选角可提高离心泵的水力性能与空化性能。随后曹树良等[14]提出一种三维前置导叶水力设计方法,改进了传统二维翼型前置导叶的不足。周邵萍等[14]基于DES数值模拟方法对多级离心泵导叶内部流动损失进行分析,并在此基础上运用叶轮设计方法对反导叶进行重新设计。曹卫东等[15]、李红等[16]、徐磊等[17]运用数值模拟预测了离心泵中关键点的压力脉动幅值与频率,表明叶轮与导叶的动静干扰使叶轮出口流场产生压力脉动。李伟等[18]、施卫东等[19]、周岭等[20]结合试验与数值模拟方法对多级离心泵轴向力进行预测,表明数值模拟方法可较准确地预测泵中轴向力分布。一些学者运用数值模拟与试验方法分析时序效应对导叶式离心泵性能影响[21-23]。
导叶式离心泵结构相对比较复杂,一方面难以通过试验对各过流部件内的流场压力进行测量,另一方面影响导叶式离心泵内部压力脉动特性的因素,如叶轮、导叶、蜗壳等多重因素,与涡壳式离心泵相比,其内部非定常受力特性研究总体并不充分。本文采用试验与ANSYS-CFX数值模拟方法对导叶式离心泵内部非稳态流动特性进行分析,重点试验分析导叶与蜗壳内的压力脉动特性、数值分析各过流部件内部非定常流场,以期为导叶式离心泵运行稳定性与设计提供理论依据与参考。
1 基本参数与数值模型
导叶式离心泵基本参数:流量Q=40 m3/h,扬程H=60 m,转速n=2 900 r/min,比转数Ns=53。设计参数:叶轮外径D2=223 mm,叶轮叶片出口宽度b2=8 mm,叶轮叶片数Z1 =6;导叶进口直径D3=228 mm,导叶叶片宽度b3=10 mm,导叶出口直径D4=283 mm,导叶叶片数Z2=5;蜗壳基圆直径D5=284 mm,蜗壳进口宽度b4=19 mm。
采用ICEM对模型泵进行前处理得到结构化网格,如图1所示,其中叶轮、导叶与蜗壳网格单元数分别为448 761、385 337、531 295。湍流模型采用SST k-ω模型,稳态数值计算边界条件采用压力进口,质量流量出口边界条件,壁面无滑移边界条件。以稳态计算作为瞬态数值计算的初始条件,叶轮每转过3°为一时间步,其时间步长0.000 172 414 s,1个周期迭代120步,迭代6个周期,选最后一周期进行流场分析。
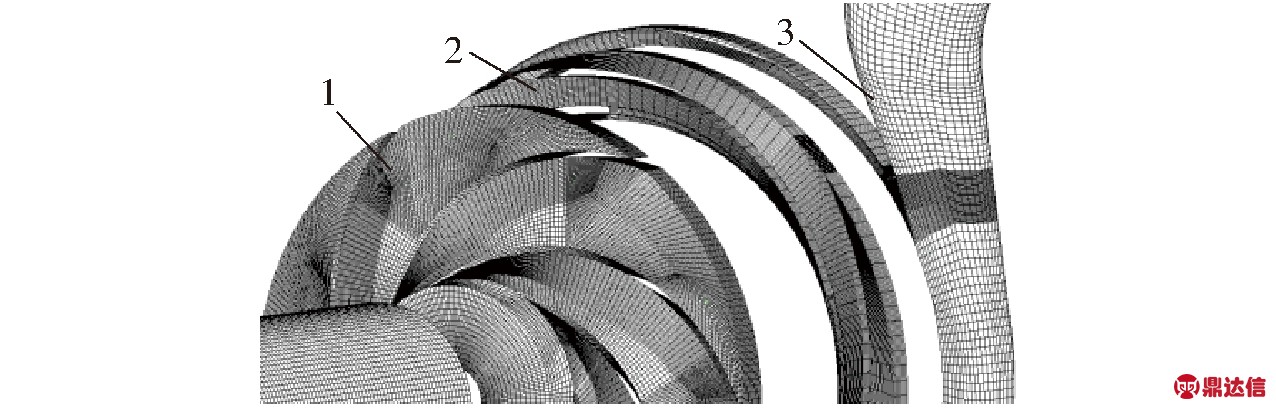
图1 计算域网格
Fig.1 Grids of computation domain
1.叶轮 2.导叶 3.蜗壳
2 试验
图2给出了试验模型泵几何结构与压力脉动监测点布置。试验模型泵中叶轮、导叶、蜗壳采用有机玻璃3D打印技术加工制造,导叶采用6个销钉均匀固定在支架上。考虑有机玻璃材料强度因素,所有所需测试参数(扬程、功率、效率、压力脉动等)都在转速1 450 r/min下进行测试。采用JN338 型扭矩传感器(北京三晶有限公司)对扭矩进行测量,其误差为±0.2%;运用日本横河AE215型流量计测量试验回路流量,测量误差为±0.5%;采用日本横河EJA510A 型压力传感器对模型泵进出口压力进行测量,测量误差为±0.075%。
为了分析导叶流道及蜗壳隔舌不稳定流场与压力脉动之间的关系,分别在导叶流道内设置2个监测点、在蜗壳隔舌附近设置2个监测点,共取4个监测点,分别为P1~P4,其中P1、P2分别位于导叶流道中段附近、导叶出口附近,P3、P4分别位于蜗壳隔舌、蜗壳出口附近,如图2所示。
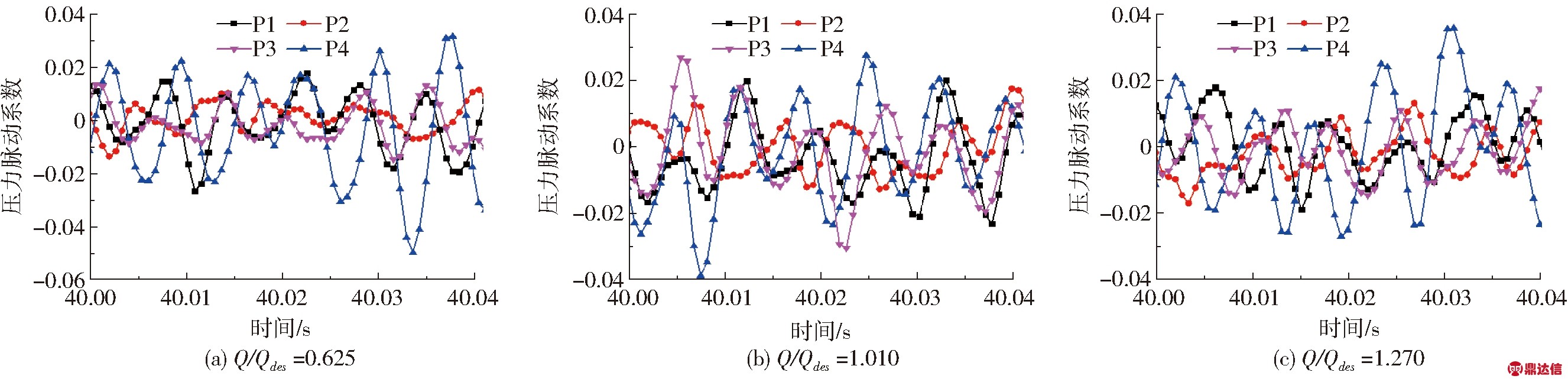
图2 试验模型泵几何结构与压力脉动监测点布置
Fig.2 Geometrical structure of test pump and layout of pressure fluctuation monitoring points
1.叶轮 2.导叶 3.销钉 4.支架 5.蜗壳
图3(Qdes表示设计流量)给出了不同流量工况下不同监测点压力脉动时域分布。由图3可知,1个叶轮旋转周期内(T=0.041 s),各监测点压力脉动波动均呈现出周期性,即6个明显的波峰与波谷。由监测点P1、P2压力脉动对比可知,监测点P1压力脉动周期性规律较差,压力脉动幅值较高,波动较剧烈,产生此现象主要原因可能由于导叶前缘与叶轮尾缘影响,即叶轮尾迹流-射流影响,使导叶进口处流场不均匀,存在局部回流等流动不稳定现象,从而导致监测点P1压力脉动幅值较大。由监测点P3、P4压力脉动对比可知,位于蜗壳隔舌附近监测点P3压力脉动周期性规律较好,压力脉动幅值较小,主要原因可能由于蜗壳隔舌存在扰流作用,尽管蜗壳较小过流断面处回流流体与导叶出口流体在蜗壳隔舌附近相互撞击,但由于隔舌扰流因素,使蜗壳下游,尤其位于蜗壳出口壁面附近区域可能存在较大旋涡,出现流动不稳定等现象,从而导致监测点P4压力脉动幅值较大。
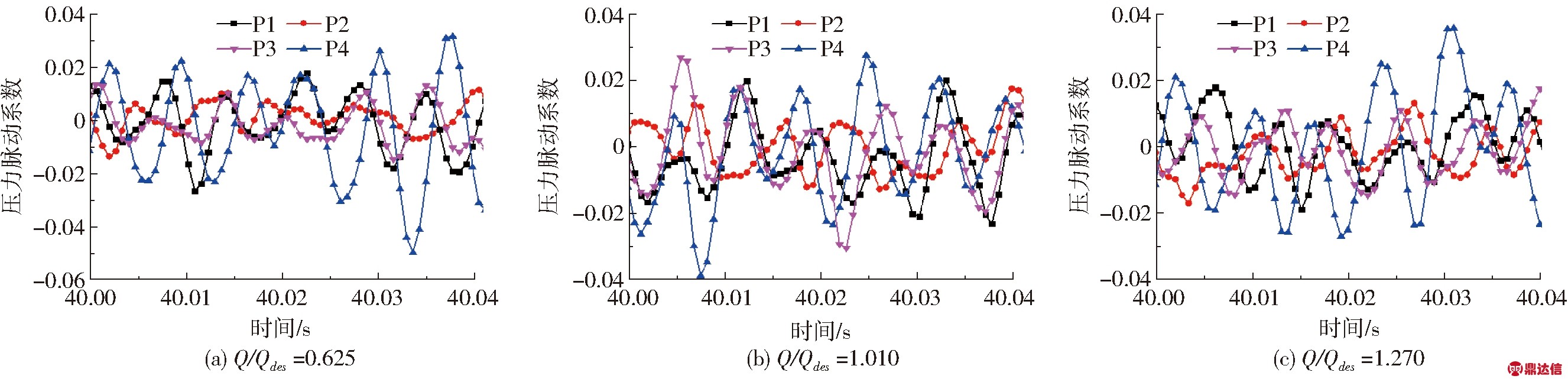
图3 不同流量工况下不同监测点压力脉动时域分布
Fig.3 Pressure fluctuations of different monitoring points under different flow conditions
图4给出了不同流量工况下不同监测点压力脉动频谱分析。由图4可知,导叶内监测点P1与蜗壳内各监测点P3、P4在各流量工况下压力脉动的主频率均为叶片通过频率(144.6 Hz);导叶出口附近监测点P3高阶谐波幅值很小,且压力脉动的主频为轴频(24.1 Hz)。由监测点P1、P2对比可知,P1叶频与轴频处压力脉动幅值大于P2的相应值,而蜗壳内监测点P3叶频与轴频处压力脉动幅值小于P4相应值。导叶内各监测点P1、P2压力脉动幅值随着流量增加而降低,但蜗壳内各监测点P3、P4在0.625倍设计流量工况与1.270倍设计流量工况附近时压力脉动幅值最大,在设计流量工况附近时幅值最小,产生此类现象主要原因可能为当偏离设计工况时,蜗壳隔舌附近区域液流角发生变化,沿着隔舌扩散段方向会因此出现分离旋涡,此分离旋涡可能导致压力脉动幅值增加。
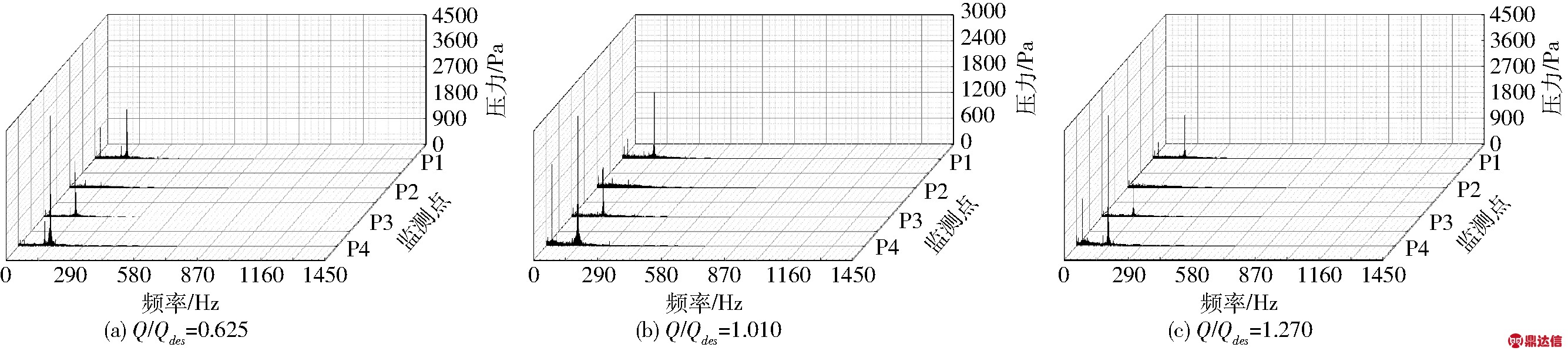
图4 不同流量工况下不同监测点压力脉动频谱分布
Fig.4 Frequency spectra distributions of pressure fluctuation under different flow conditions
图5给出了不同流量工况不同监测点轴频与叶频处压力脉动幅值。由图5可知,导叶内监测点P1、P2与蜗壳内监测点P3在叶频处压力脉动幅值随着流量的增加而几乎不变,蜗壳内监测点P4叶频处压力脉动幅值在偏离设计工况(Q/Qdes=0.625、Q/Qdes=1.270)时较大,在设计工况附近时脉动幅值最小,产生此类现象主要原因可能为当偏离设计工况时,蜗壳隔舌附近液流角发生变化,从而导致隔舌下游即蜗壳扩散段区域出现旋涡,进而促进压力脉动增加。监测点P1、P3、P4叶频处压力脉动幅值明显高于轴频处脉动幅值,即主频为叶频,而监测点P2处主频为轴频。
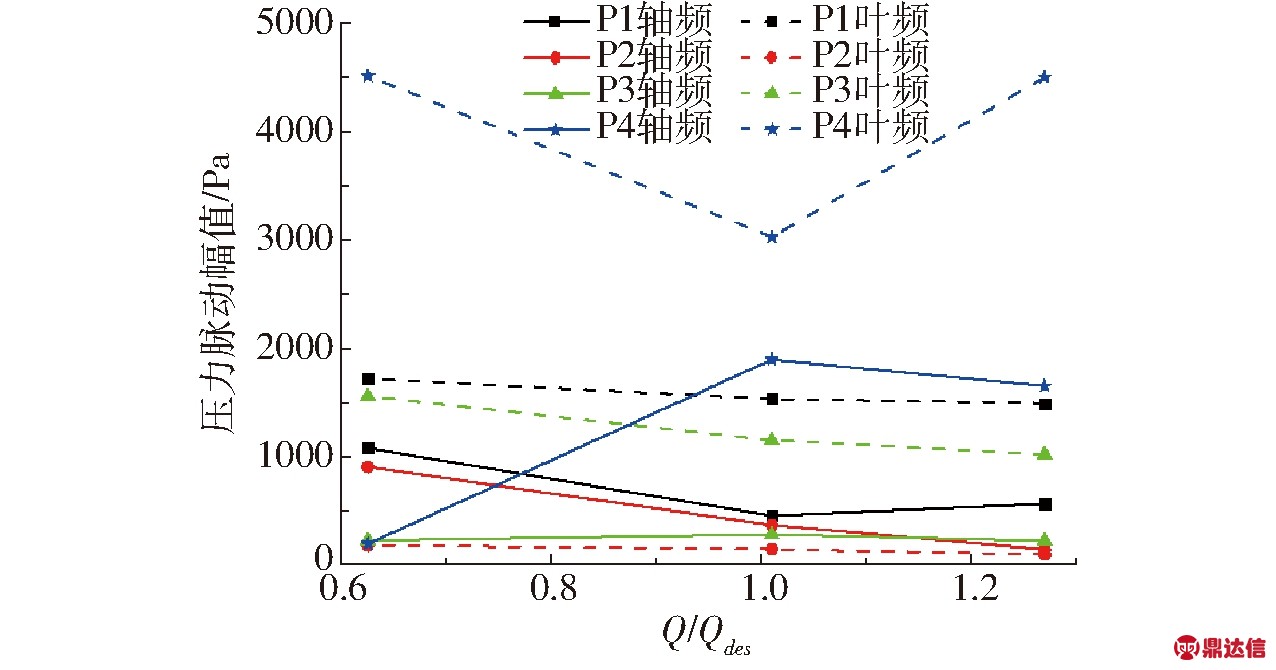
图5 不同工况监测点轴频与叶频处压力脉动幅值
Fig.5 Pressure fluctuation of monitoring points at shaft-frequency and blade-frequency under different conditions
3 数值模拟结果分析
3.1 数值分析验证
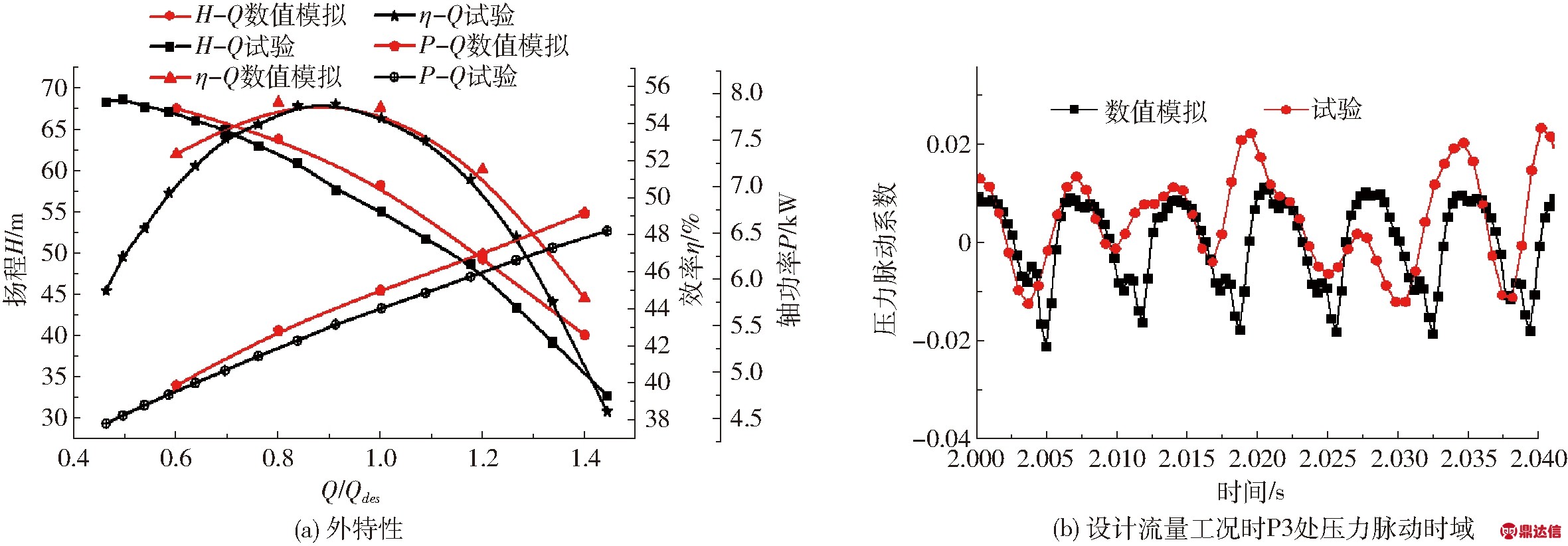
图6 导叶式模型离心泵数值模拟与试验对比
Fig.6 Comparison of numerical and experimental results
图6给出了模型泵数值模拟与试验结果对比。由于试验在1 450 r/min转速下进行,故在进行数值模拟结果验证时,对其数值模拟也在1 450 r/min条件下进行。由图6a可知,模型泵最高效率并不在设计工况点,而处于0.95倍流量工况,由此可知,导叶喉部面积可能偏小,导致最高效率向较小流量偏移。数值模拟外特性曲线与试验曲线吻合较好,尤其在设计流量工况附近,数值模拟中扬程及效率与试验误差在5%以内,表明数值模拟存在一定的准确性,但在0.6倍流量工况及1.4倍流量工况时,数值模拟与试验值误差偏大,产生此类现象主要原因可能为:远偏离设计工况时,离心泵存在剧烈的湍流、回流等现象及湍流模型在局部区域存在剧烈湍流评估等。由图6b可知,数值模拟压力脉动时域曲线分布趋势与试验类似,即因动静干涉作用影响,压力脉动系数呈现出周期性波动,且其数值模拟结果略低于试验值,表明监测点P3压力脉动时域分布与试验值吻合较好,由此进一步说明数值分析的准确性。
3.2 内部流场分析
图7分别给出了设计流量工况时不同时刻叶轮、导叶及蜗壳中截面静压分布,其中1~6表示叶轮叶片,a~e表示导叶叶片,t1时刻叶轮叶片1的尾缘位于导叶叶片a的前缘,t2时刻叶轮叶片2的尾缘位于导叶叶片b的前缘,t3时刻叶轮叶片3的尾缘位于导叶叶片c的前缘。由图7a可知,因动静干涉作用,不同时刻各叶轮流道静压分布不同,当叶轮叶片靠近导叶前缘时,对应的此叶轮流道出口静压最大且高压区较宽。因导叶前缘影响,靠近叶轮流道出口压力面区域出现较大静压,梯度变化较大,吸力面处静压较小,分布均匀,说明叶轮压力面受动静干涉作用影响较大,叶片出口压力面与吸力面存在较大压差,可能使叶轮承受较大作用力而导致叶轮振动变大。
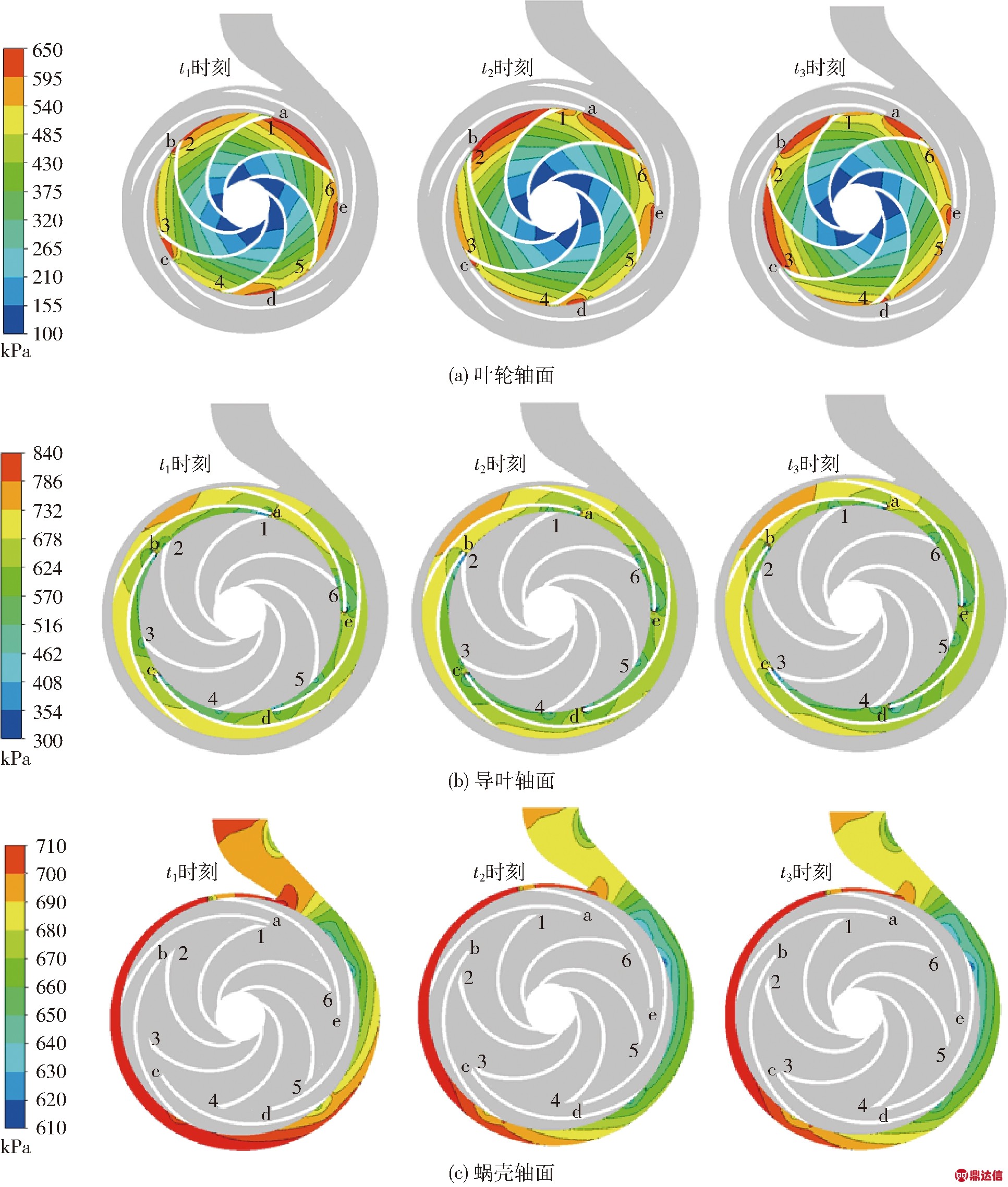
图7 设计流量工况时不同时刻过流部件中截面静压分布
Fig.7 Static pressure distributions in flow passage components under design conditions
由图7b可知,在离心泵中导叶主要起扩压作用,导叶进口处出现低压区,出口呈现高压区。由于受蜗壳几何形状不对称的影响,导叶各流道静压沿叶轮旋转方向逐渐降低,从而导致叶轮各流道出口压力分布不对称,由此可能导致叶轮径向力的产生。在整个导叶流道中,因受导叶前缘与叶轮尾缘的共同影响,导叶进口处压力分布最复杂:靠近导叶前缘吸力面与叶轮尾缘压力面区域出现局部低压,梯度变化较大,说明导叶前缘吸力面与叶轮尾缘压力面对导叶进口段压力分布影响较明显。
由图7c可知,当叶轮叶片逐渐靠近蜗壳隔舌时,位于蜗壳隔舌附近高压区在逐渐增大,说明尽管蜗壳隔舌远离叶轮,蜗壳内流场不仅受叶轮-导叶动静干涉作用影响,而且叶轮-蜗壳隔舌动静干涉作用对蜗壳隔舌附近流场存在一定影响。蜗壳隔舌附近与较小过流断面处静压最大、分布均匀,蜗壳较大过流断面处静压最小、梯度变化较大。位于导叶尾缘压力面区域出现局部低压,梯度变化较大,因此导叶尾缘压力面对蜗壳进口局部压力影响大于吸力面。
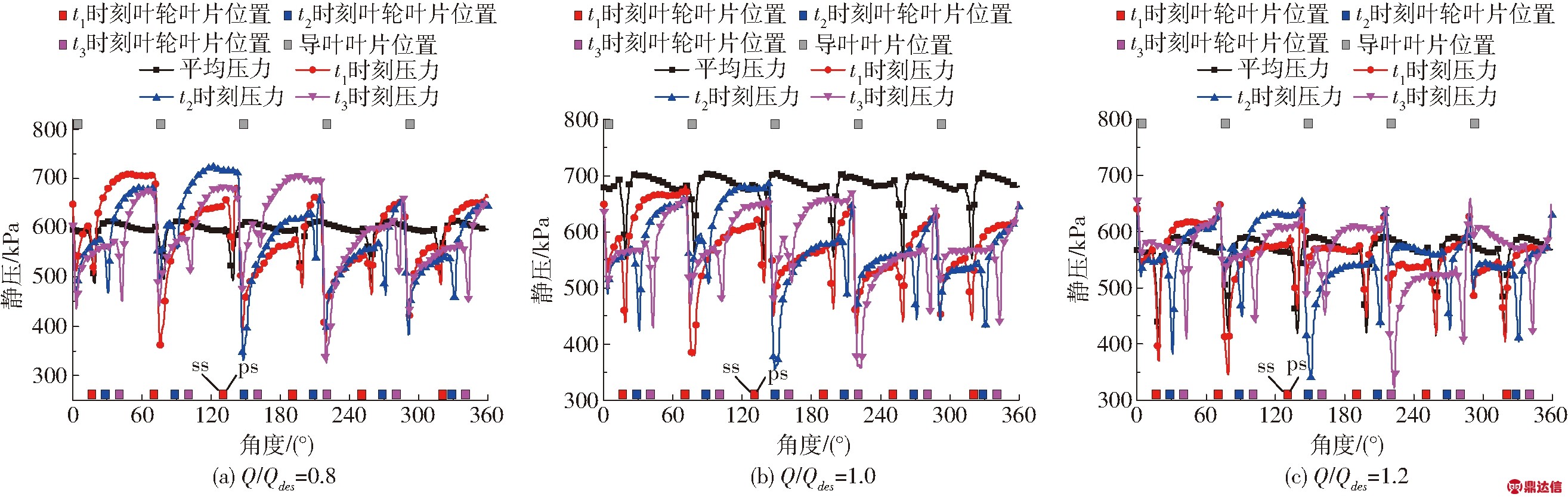
图8 不同流量工况下叶轮出口中截面沿圆周方向的瞬时与平均压力分布
Fig.8 Instantaneous and average pressures distributions of impeller outlet under different flow conditions
图8给出了不同流量工况下不同时刻叶轮出口中截面沿圆周方向的瞬时压力、平均压力分布。由图8可知,不同流量工况、同一时刻叶轮出口瞬时压力随着流量增加而减小,且叶轮各流道压力对称性分布逐渐趋于稳定,由此可说明叶轮各流道压力不对称现象是导致叶轮径向力产生的主要原因,且随着流量增加,作用于叶轮上径向力可能降低。相同流量工况、不同时刻瞬时压力分布趋势类似:由于动静干涉作用影响,压力波峰位于导叶前缘压力面,波谷位于导叶前缘吸力面;叶轮尾缘压力面出现局部低压,吸力面呈现局部高压,因此导叶前缘吸力面与叶轮尾缘压力面对叶轮出口静压分布影响较大,受动静干涉作用影响较明显。
不同流量时,平均压力分布均匀,各流道压力呈现较好对称性,但叶轮各流道瞬时压力对称性较差,由此可明确说明叶轮出口压力分布主要受叶轮-导叶动静干涉作用影响,从而使其叶轮出口压力时刻改变,各流道压力不对称,说明叶轮-导叶动静干涉作用是叶轮径向力产生的主要因素,而蜗壳不对称几何形状是次要因素。
图9给出了不同流量工况下不同时刻导叶进口中截面沿圆周方向的瞬时压力、平均压力分布。由图9可知,同一时刻,随着流量增加,导叶各流道压力分布逐渐趋于对称。导叶进口圆周方向压力共同受动静干涉作用与蜗壳几何形状影响:同一流量工况、不同时刻瞬时静压波谷位于导叶前缘吸力面,波峰位于导叶前缘压力面,由此可知导叶吸力面受动静干涉影响较明显;位于叶轮叶片尾缘压力面区域出现局部低压,且随着叶轮旋转而向前移动,表明叶轮叶片压力面对导叶进口区域静压影响大于吸力面。
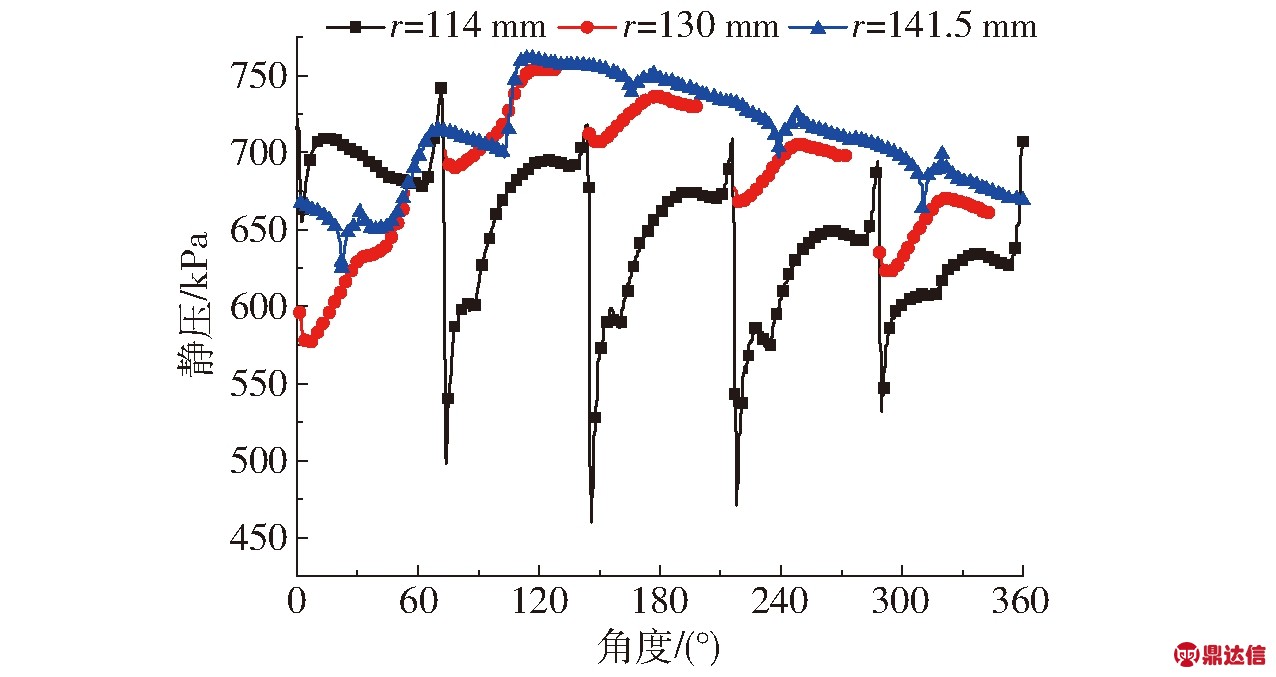
图9 不同流量工况下导叶进口中截面沿圆周方向的瞬时与平均压力分布
Fig.9 Instantaneous and average pressures distributions of diffuser inlet under different flow conditions
导叶各流道进口平均压力分布较对称,但对称性劣于叶轮各流道压力对称性;导叶各流道压力沿着叶轮旋转方向逐渐降低,而降低幅值较小,表明导叶进口处压力分布主要受动静干涉作用影响,而蜗壳不对称几何形状对其影响不明显。随着导叶径向距离的增加,即从导叶进口至出口,导叶各流道平均压力极其不对称,受蜗壳不对称几何形状影响越来越明显,其各流道静压沿着蜗壳流道方向逐渐降低(如图10所示,其中r表示半径)。
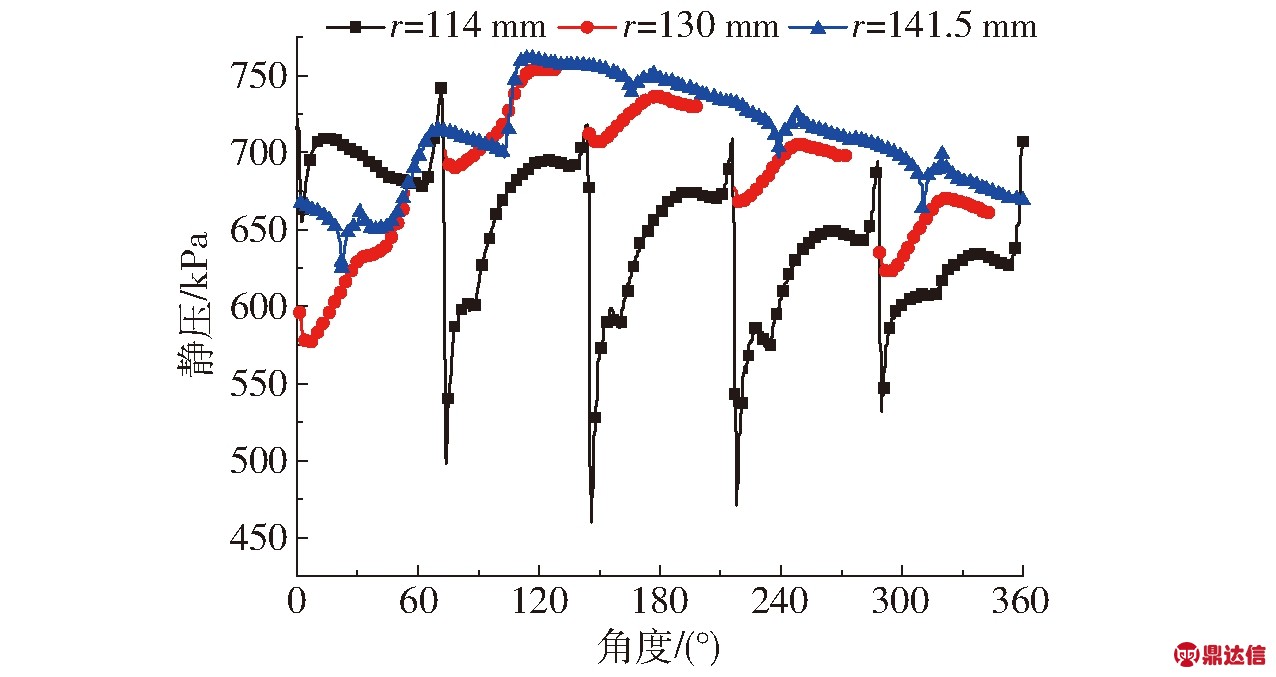
图10 设计流量工况t1时刻不同半径时导叶中截面
沿圆周方向的平均压力分布
Fig.10 Average pressure of diffuser at t1 with different radius under design flow rate
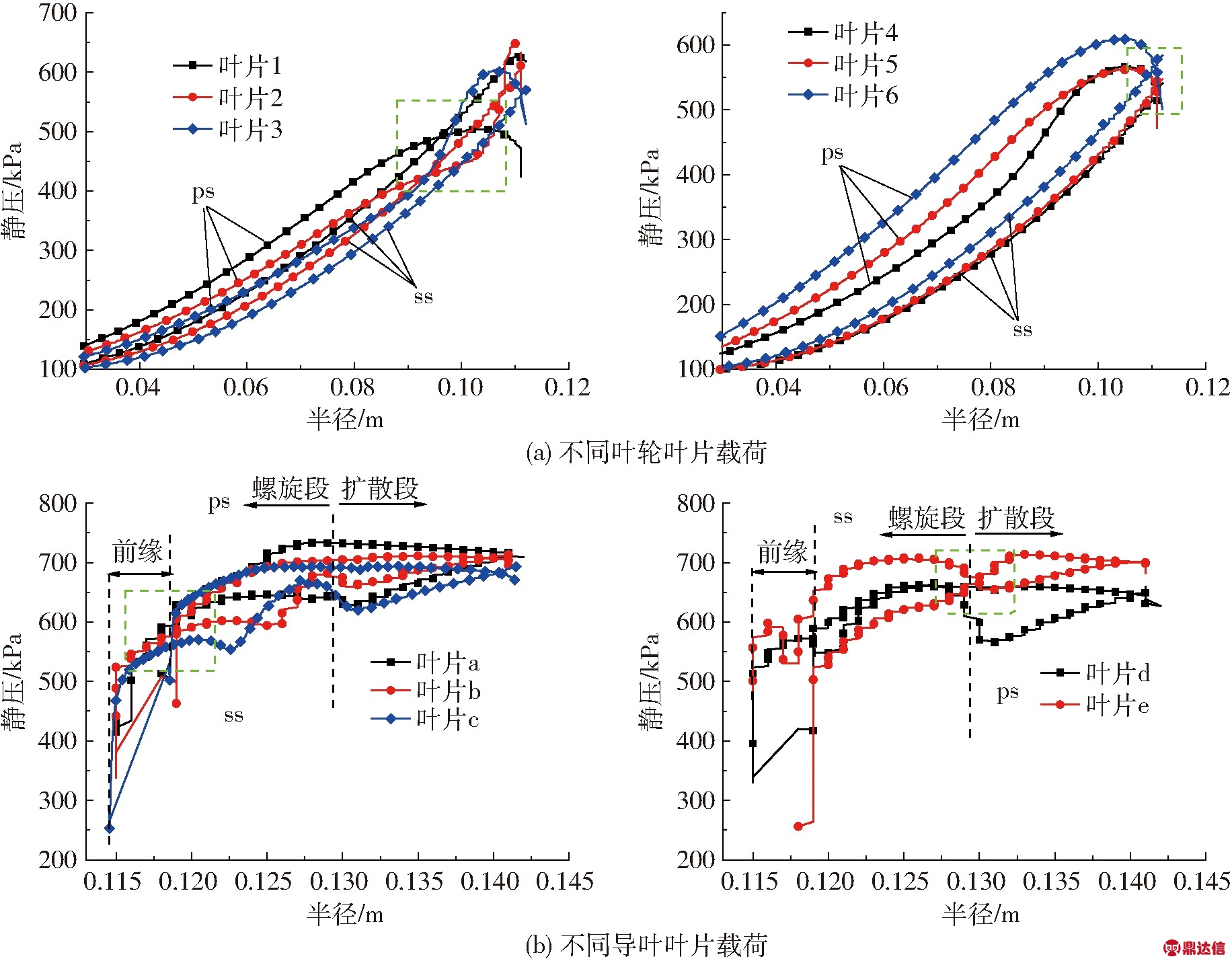
图11 设计流量工况下t1时刻不同叶片载荷
Fig.11 Different blade loadings at t1 under design flow rate
图11给出了设计流量工况下t1时刻叶轮与导叶各叶片载荷分布。由图11可知,叶轮中各叶片静压分布相似,叶片吸力面静压均小于压力面。因动静干涉作用与导叶前缘影响,叶轮叶片逐渐靠近导叶前缘时,叶轮表面压力逐渐增加,即叶片做功增大,压力面与吸力面静压差值逐渐减小(如叶片1、2、3),说明叶片在流体中受力减小,振动降低,而叶片逐渐远离导叶前缘时,其差值增加(如叶片4、5、6),因此叶轮尾缘逐渐远离导叶前缘时,叶轮内流动逐渐不稳定,振动较大。叶轮叶片逐渐远离导叶前缘时,叶片出口吸力面大于压力面静压的位置逐渐向出口移动,当叶片1、2位于导叶叶片a、b前缘附近时,其吸力面大于压力面静压的位置位于叶轮半径r=0.09 m附近,而叶片3、4、5、6位于叶轮出口,说明叶轮尾缘逐渐靠近导叶前缘时,叶轮出口处流场受射流-尾迹流影响更明显。
因动静干涉、导叶前缘影响,导叶各叶片前缘与螺旋段处压力分布较复杂,局部出现吸力面静压大于压力面。蜗壳不对称几何形状及蜗壳隔舌对导叶各叶片表面压力影响较大,当导叶叶片远离蜗壳隔舌(叶片a、b、c、d),但逐渐靠近蜗壳较大过流断面(叶片c、d)时,其螺旋段处吸力面静压逐渐逼近压力面;当叶片位于蜗壳隔舌附近,且位于蜗壳较小过流断面(叶片e)时,其螺旋段处吸力面处静压大于压力面,且其位置向扩散段偏移,导致以上现象主要原因:导叶叶片尾缘刚好处于蜗壳第一断面与隔舌附近,蜗壳过流断面积较小,流出导叶的高速流体与蜗壳中低速流体碰撞而产生旋涡(图12),从而导致导叶叶片e中出现旋涡,由此可知导叶叶片与蜗壳隔舌之间的安装位置对离心泵存在一定影响;流入蜗壳过流断面的绝对速度因较小或较大蜗壳过流断面使其方向和大小发生变化,且此流体与导叶出口的流体相遇时,因速度大小和方向不同产生撞击,从而影响导叶出口附近的速度与静压分布。
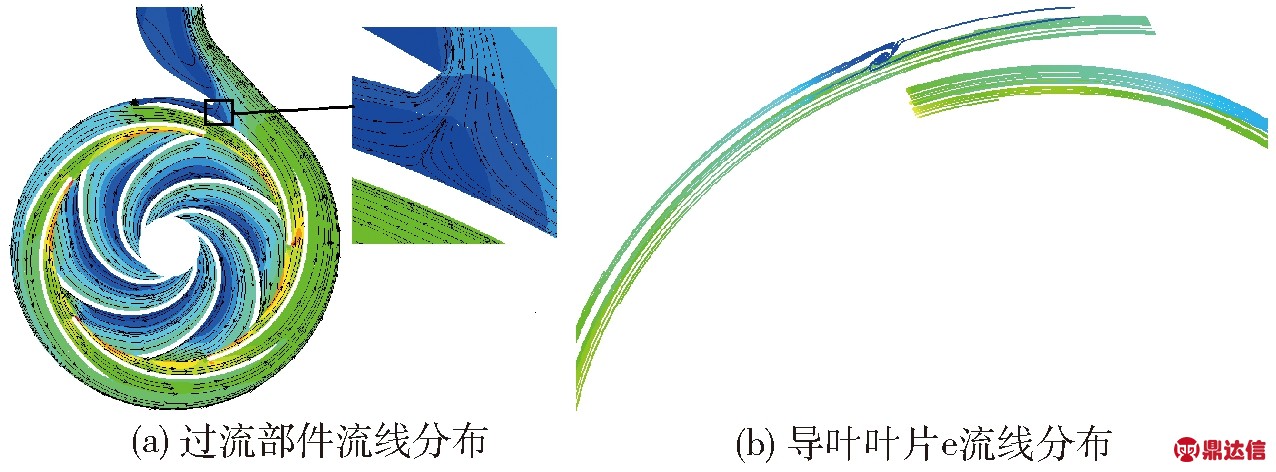
图12 设计流量工况下t1时刻速度流线分布
Fig.12 Velocity streamline distributions at t1 under design flow rate
4 结论
(1) 因动静干涉作用影响,导叶式离心泵内各监测点压力脉动均呈现周期性变化,其脉动主频均为叶片通过频率;导叶进口处压力脉动高于导叶出口处,由此说明导叶进口处流场受导叶前缘与叶轮尾缘影响及动静干涉作用影响较大,蜗壳出口处脉动强度大于隔舌附近。
(2)叶轮内压力分布主要受叶轮-导叶动静干涉作用影响;导叶内压力分布同时受动静干涉作用和蜗壳不对称几何形状影响,随着导叶径向距离增加,蜗壳不对称几何形状影响逐渐增强,叶轮-导叶动静干涉作用影响逐渐减弱;蜗壳内压力分布同时受叶轮-蜗壳隔舌动静干涉作用和导叶尾缘影响。
(3)叶轮出口中截面和导叶进口中截面沿圆周方向的压力主要受叶轮-导叶动静干涉作用影响,蜗壳不对称几何形状对其影响较小,但随着导叶径向距离的增加,蜗壳不对称几何形状对导叶内沿圆周方向压力影响逐渐明显,即各流道压力对称性变差。
(4)随着流量增加,叶轮叶片和导叶叶片表面压力在逐渐降低,说明叶轮做功逐渐减小;因叶轮出口尾迹流-射流影响,叶片出口附近出现吸力面静压大于压力面;因导叶前缘与叶轮尾缘的影响,导叶叶片进口处压力分布极其复杂,规律性较差。叶轮各叶片的静压分布明显受叶轮-导叶动静干涉作用影响,当叶片逐渐靠近导叶叶片前缘时,压力面与吸力面处的压力差值呈增大趋势;导叶各叶片的静压受蜗壳隔舌影响,使其位于隔舌附近的叶片压力分布极其复杂。