摘 要:借助计算流体动力学(CFD)软件对影响机械密封环密封性能的因素进行分析,研究表明,转速的变化对动环、静环及端面液膜温升影响较大,随转速的增大,摩擦热增加,温升明显。另一方面,压差对动环、静环及端面液膜温升的影响程度则较小。
关键词:机械密封环 温度场 计算流体动力学 影响分析
机械在运转过程中,密封环相互贴合并相对转动,从而产生摩擦热,导致密封端面温度升高,由此带来一系列问题。如:密封端面温度升高,使液膜汽化,导致端面间润滑失效;密封端面温度不均匀,形成温度梯度,从而产生热压力,易使密封环变形。因此,为了保证机械密封环的密封性能,对机械密封环的温度场影响因素进行分析是非常必要的。彭旭东等[1-3]采用有限元分析软件求解机械密封环在流体介质压力及摩擦热作用下的形变量,并探讨了影响机械密封环形变的主要因素。孙泽刚等[4-6]对机械密封环腔内压力场和温度场进行了模拟分析,得出机械密封环的温度、压力在不同速度下的分布情况。郝本明等[7-8]在不同工况下对机械密封环温度场及压力场进行了计算,得出密封环端面温度及压力的变化状况。笔者借助计算流体动力学(CFD)软件对影响机械密封环性能的因素进行了计算分析,为实际工程应用提供了数值参考依据[9-10]。
1 密封环温度场模拟分析的基本假设
由于机械密封装置在实际运行中的复杂性及多变性,因此需对机械密封环模拟分析进行合理的简化,假设:①机械密封结构模型及温度场均为轴对称;②机械密封环正常工作时温度场为稳态;③机械密封环材质热物理性能恒定。
2 网格划分
在进行网格划分时,既要考虑计算的精确性,又要考虑计算量。因此,该模型分3个区域进行网格划分。动环、静环厚度方向网格尺寸设为1,液膜厚度方向网格尺寸设为0.5,从而保证液膜厚度方向的计算精度,更好地反应温度场的分布情况。最后,对网格划分质量进行相应的检查。具体网格划分如图1所示。
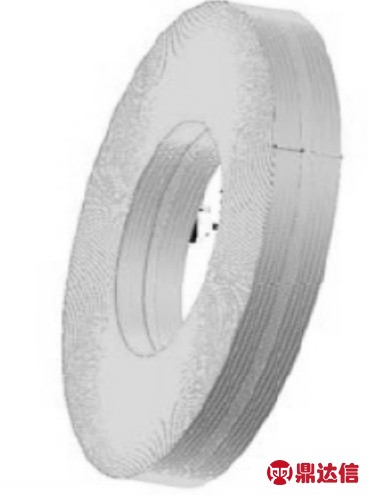
▲图1 网格划分结构示意图
3 边界条件
3.1 密封环及密封流体的物理参数
动、静环材料为碳化硅与石墨材料的组合,密封介质为水,其具体物理参数见表1。
表1 密封环及密封流体的物理参数
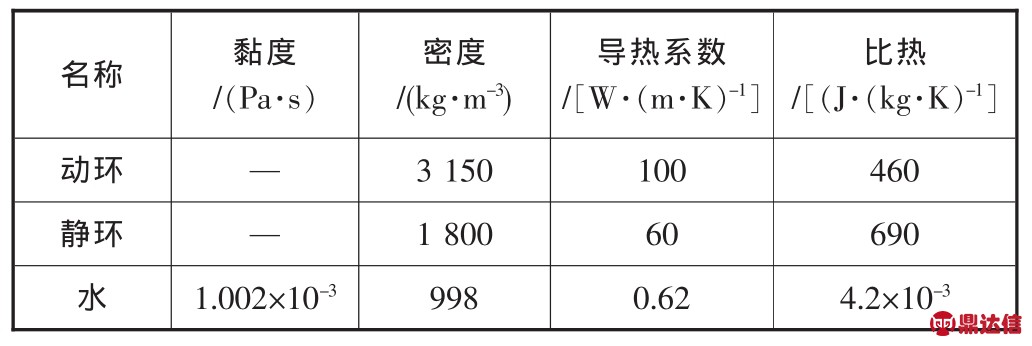
3.2 边界条件
动、静环端面与液膜设定为流固耦合热边界条件,静环圆周与周围空气设定为对流边界条件,静环内径与流体介质设定为对流换热边界条件,动环内径与流体介质设定为对流边界,动环外径壁面与周围流体介质也设为对流边界,静环背面和动环背面均设为绝热边界。
4 结果与分析
4.1 转速对温度场的影响
分别模拟分析了不同工况参数对机械密封动环、静环及液膜温度场的影响规律,图2所示为压差在0.2 MPa条件下,机械密封动环、静环及液膜的温升随转速的变化趋势。
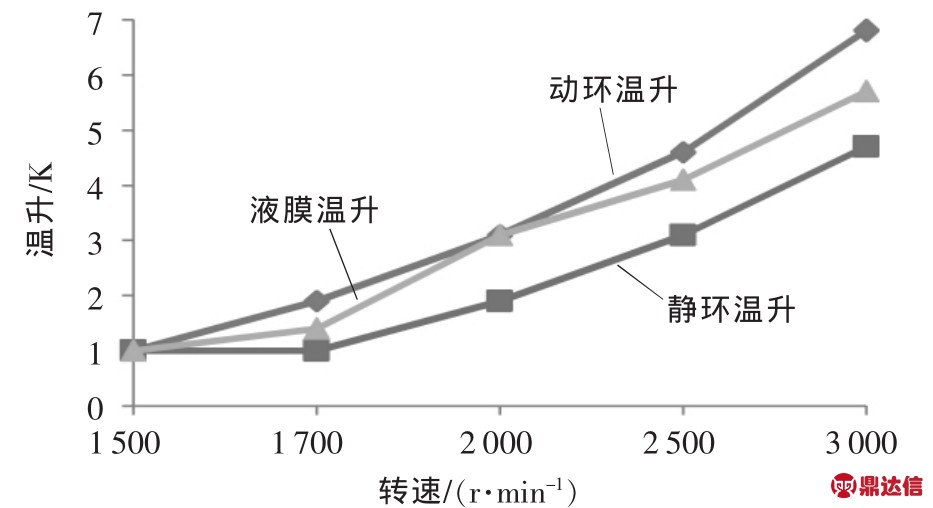
▲图2 动环、静环及液膜温升随转速的变化趋势
从图2中可见,在不同的转速下,动环、静环及液膜有着不同的温升,转速越高,温升越大。因此,转速对动环、静环及液膜温升的影响较为显著。随着转速的加快,机械密封环与液膜两者之间的摩擦热也逐步增大,从而使动环、静环的温度变化更明显。如转速在2 000 r/min时,动环温升为3.1 K,静环温升为1.9 K;转速在3 000 r/min时,动环温升达到6.8 K,静环温升为4.7 K。同样,密封端面液膜温度也随转速的加快而升高,原因主要是散热速度小于热量增大的速度,从而导致密封端面液膜温升增大。如转速在2 000 r/min时,液膜温升为3.1 K;转速在3 000 r/min时,液膜温升达到5.7 K。
4.2 压差对温度场的影响
图3为转速在2 000 r/min的条件下机械密封动环、静环及液膜的温升随压差的变化趋势。
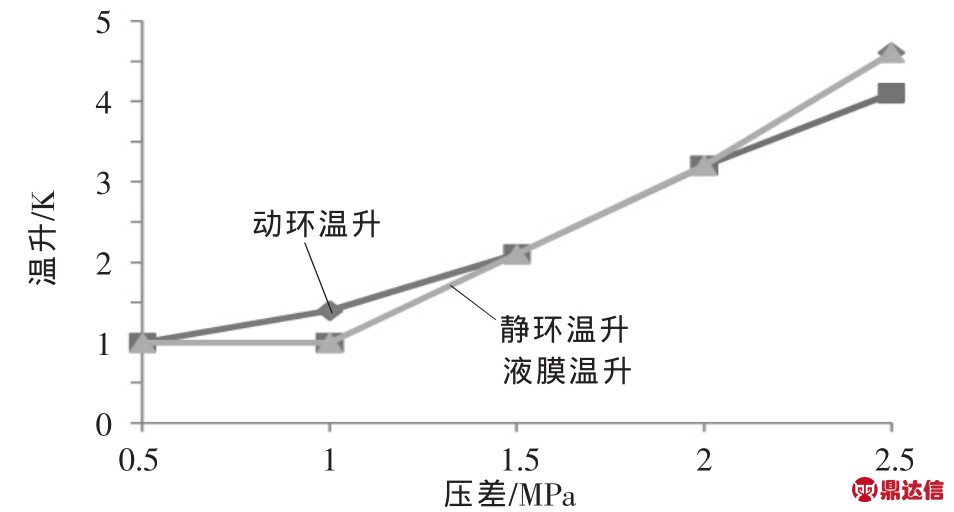
▲图3 动环、静环及液膜温升随压差的变化趋势
由图3可见,在不同的压差下,动环、静环及液膜有着不同的温升,但其增大趋势不如转速加快所带来的变化趋势那么明显,主要是由于压差增大,密封环端面所受载荷也增大,虽然也使密封环端面的摩擦热增加,但增加的幅度较小。
5 结论
(1)在不同的转速下,动、静环及液膜有着不同的温升,转速的影响较明显,温升幅度较显著。
(2)动、静环及液膜温升随压差增大而增大,但相对转速而言,增幅并不明显。