摘 要:齿轴外圆在变速箱中与轴承相连接,随着对变速箱性能要求的不断提高,锥度外圆设计随之出现,是提升变速箱寿命、传动精度、稳定性的重要因素;本文以DCT250 变速箱输出轴一为研究对象,分析了加工中的技术难点,阐述了QUICKPOINT 3000 磨床的加工原理,加工方案及验收标准.结果表明:使用加工方案后计算产品Major 特性的初始过程能力满足加工要求≥1.33;粗糙度、圆度、傅里叶分析等要求均能够满足所要求的性能要求,为进一步研究、开发提供依据。
关键词:锥面齿轴 QUICKPOINT 3000磨床 加工能力
变速箱中齿轴锥面外圆的设计是优化传动稳定性的重要改善方法,直接影响变速箱的质量、寿命。齿轴锥角外圆在加工中的稳定性、高效性是保证锥角外圆设计能在得到广泛的应用在整车中并发挥该设计益处的重要前提。
1 加工原理分析
QUICKPOINT3000 机床是采用点接触式进行的高速磨削法,采用仅几毫米宽,不易磨损的立方氮化硼工作;借助砂轮前段斜角设计与水平夹紧的工件之间的倾斜产生一个后角,使砂轮与工件件的主要接触区域从线接触变化为点接触,达到快速精磨切削的目的;编辑工件程序,使砂轮刃类似车刀走程序,适应不同外径,不同轴长,不同形状的外圆加工,达到工件上不同外圆使用同一砂轮的万能磨削目的。
针对带有锥度的齿轴外圆,需单独建立相匹配的砂轮主参数,砂轮主参数中依据工件锥度外圆大小增加砂轮摆角角度参数,砂轮加工的路线同样依据工件锥度外圆大小设置成带锥度的加工路线。
2 加工程序拟定
针对DCT250 轴一的锥度外圆,进行该锥度外圆的程序编辑,如下:
(1)在确定了的加工中针对Φ35.5(+0.028,+0.012)(距端面7mm 位置)单独建立外圆砂轮的的砂轮主参数,注意砂轮摆角的设置成0.07°。
(2)常规设置加工进刀安全起点后,依据外圆直径与工件锥度换算设置切削起点与切削终点的位置坐标,通过加工起 点(X:35.116,Z:192.48)与 终 点(X:35.524,Z:209.18)的X、Z 体现。
复核程序中加工路线的角度设置,
加工路线角度=arctan(35.524/2-35.116/2)/(209.18-192.48)
=arctan0.0122
=0.07°(与砂轮角度和工件角度相符,复核通过)
(3)常规设置往复光整程序及退刀安全点,进行空运行检测程序无异常后进行试切加工。
3 试切结果分析
试切的锥度外圆的产品特性要求及试切3 件结果如下:
(1)锥角=0.07°(+0.015°,-0.02°);实测0.0671°、0.0669°、0.0698°。
(2)外 圆 直 径Φ35.5(+0.028,+0.012)(距端面7mm 位置),且为Major 特性;实测Φ35.521、Φ35.518、Φ35.520。
(3) 粗 糙 度:Rz1.5-1.9,Rmax2.6-3.0,RPK0.13-0.16,RK0.21-0.26,RVK0.2-0.24,Mr1.6-1.8。
(4)圆度0.004,直线度0.004,中凹0.001;实测:圆度0.0023-0.0033,直线度0.0024-0.0035,中凹0.0004-0.0008。
(5)傅 里 叶 短 波 分 析5~300 阶 次,n0=0.7,K=0.6,R=3;实测5-50 阶次合格;50-300 阶次合格。
4 初始过程能力分析
按照GETRAG 的GCG_803007 标准建立分析样本,分析锥度外圆直径Φ35.5(+0.028,+0.012),连续加工200 件,加工中不允许调整机床,只可以进行自动或手动的补偿,样本容量n=3,样本数量k=25,得到以下75 组数据(见表1):
使用qs-STAT 分析初始过程能力:
每个样本平均值分布以及样本内极差值分布,样本容量内数据分布符合正态及瑞利分布,初始过程能力PP、PPK 合格(图1)。
5 结 语
(1)采用QUICKPOINT3000 磨床可以实现锥度外圆的磨削加工。
(2)设计的加工方案能满足产品特性的要求,能有效的提升变速箱质量、寿命。
(3)验证表面:初始过程能力PP=1.94,PPK=1.80,可用于批量生产,可作为进一步设计的参考。
表1
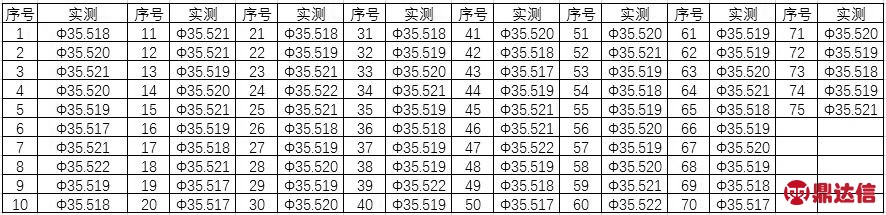

图1