摘 要:主要论述解决薄壁锥套的加工难题,通过对零件结构进行分析,定制加工路线、确定工艺加工方法、选择装夹加方式及定位基准、优化加工方法等,确定最优加工方案。
关键词:薄壁锥套;加工方法;工艺优化
1 概述
薄壁锥套是采煤机械设备上常用的一种连接件,此锥套内锥为1:4需与同锥度的外锥配合使用,且应具有互换性,由于零件自身结构的特殊性以及矿井下使用工况条件较差,该零件加工精度等级要求较高。因此,选择合理的加工工艺流程,以保证加工质量稳定尤为重要。
2 工艺路线的编制
根据设计图纸(如图1所示)零件材料及技术要求制定整个零件的加工路线。此例零件材料为40CrNiMoA,图纸技术要求整体淬火,硬度HRC38-42。由于是薄壁类零件,所以加工过程分为粗、半精、精加工。根据以上条件,工艺路线制定为:锻-热(正火)-车(粗车)-车(半精车)-热(整体淬火)-车(精车)-钻(螺纹孔)-线切割(3处1.5宽槽)。
3 工艺编制,根据图纸要求及工艺路线编制加工工艺
3.1 工艺基准的选择(如图1所示)。以外圆Φ125f7为加工基准,1:4内锥相对外圆基准A的跳动为0.02,因此外圆、内锥要一刀下,且允差小于0.02,考虑这几点要求,装夹位置选择在零件的右端。
3.2 刀具的选择。由于设计结构、精度等级、光洁度、加工方法的限制,此零件的内孔、外圆均在热处理淬火之后进行最后一道精加工,且此锥套内孔带有凸台,结构特殊,整体硬度高于普通的调质零件,一般的内孔车刀大小、硬度均无法满足加工,选择只针对此零件的内孔专用车刀,外圆车刀也选择更适合加工此硬度的专用车刀。
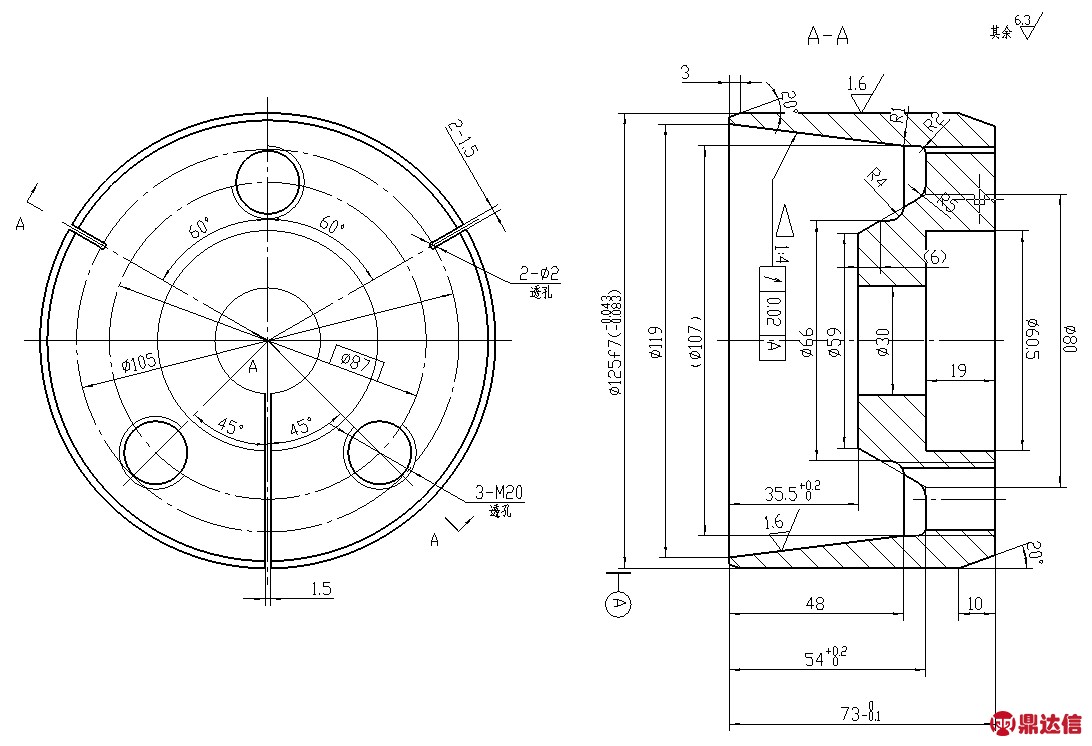
图1
4 加工过程切削量的选择。
为提高加工精度,满足图纸光洁度的要求,采用高转速、小进给,分层多次车削。此零件经过在现场多次试验,精加工车削工序最终选择转速 s=200~300 r/min,进给量 f=0.1~0.14mm/r,背车刀量ap=0.2~0.3 mm。
5 工艺加工方法的优化选择。
此零件加工的方法的选择主要体现在内孔与外圆加工的区别。
方法一:内孔、外圆均采用磨削,以保证图纸要求,但是1:4内锥是与同锥度的外锥配合使用,外锥轴零件是采用车削加工出来的,所以在磨削内锥时要和外锥配磨来保证使用时接触面积大于80%,这样以来就相当于轴和套的配合只能是一对一,没有互换性,一损俱损,给使用者带来了经济性和便捷性的双重负担。
方法二:内孔、外圆均采用车削加工,依靠同一数控车床的精准加工来保证1:4锥度要求。经试验一批30件,内、外锥度1:4均采用数控车削加工,完工后在格林森三坐标检测仪检测出来的结果,1:4锥度及其他参数均符合图纸要求。
结束语
薄壁套类零件加工是车削加工的难点之一,主要由于装夹应力及车削热应力的影响,在加工过程中容易引起变形,有的甚至是加工完在机床上检测是合格的,一但卸下来后放置一段时间自然冷却就会放生变形。所以加工薄壁套类零件时要注意以下几点a.装夹方式的选择,尽量选择使用较小的夹紧力或者做专用工装进行装夹。b.车削时分层车削,小背吃刀量、小进给量,高转速。c.冷却要及时。