摘要:本文分析了摩擦盘式电磁制动器的工作原理与磁路结构,推导了电磁制动器电磁吸力的解析计算公式,定义了电磁吸力密度的概念,提出了一种最大电磁吸力密度的结构优化方法。通过优化内外吸力环中磁密,使两者相等,实现电磁吸力密度的最大化。为验证解析计算结果的准确性与优化方案的有效性,以一台6 N·m电磁制动器为仿真与优化对象,进行二维与三维有限元分析。仿真验证了电磁吸力解析计算结果的准确性以及最大电磁吸力密度结构优化方法的有效性。
关键词:电磁制动器;磁路计算;电磁场仿真;优化设计;电磁吸力密度
引言
电磁制动器(electromagnetic brakes, EB)自上个世纪中叶问世以来,由于其结构简单、制动可靠、耐用性强、环境适应性好等特点,可以很好地满足工业生产要求,因此被广泛应用于印刷业、纺织工业、军工、工业自动化、医疗等行业[1]。电磁制动器在通电时电磁吸力抵消弹簧弹力从而使摩擦盘悬空,断电时弹簧弹力使摩擦盘与制动板产生摩擦转矩,完成断电制动。
早期的电磁制动器借鉴了螺线管的电磁建模方式,通过对螺线管的电磁性能分析研究尝试建模电磁制动器[2~3]。转矩由摩擦力产生,通电时由电磁吸力抵消摩擦力,转矩控制方法在文献 [4] 中进行讨论。气隙是产生电磁吸力的关键,因此需要对气隙的表面效应与瞬态磁化过程进行分析[5]。在通电、断电瞬间,线圈中会产生涡流,而涡流在制动中会产生热量,文献 [6] 对此进行了分析讨论。结合大量早期电磁阀模型的知识, 文献 [7]对摩擦盘式电磁失电制动器精确模型的等效磁路与瞬态特性进行了仿真分析与实验验证,现在常见的电磁制动器沿用的一般都是这个模型的变体。
近几十年,全世界的学者在电磁制动器方面开展了丰富的研究。涡流型电磁制动器具有低噪声、低摩擦损耗、易于控制和低电流的特性,在文献 [8] 中提出了一种新的设计方法可以更加凸显其特性,在文献 [9] 中则基于一种自行车用涡流型电磁制动器对其特性进行了全面的定量计算与仿真分析。在文献 [10] 中,一种新型的电磁制动器结构被提出,应用其快速制动的特性作传动装置的紧急制动器用。文献 [11] 提出了一种利用一张在不同转速和定子阻抗下的电容值分布表的三维图表辅助可再生电磁制动器设计的方法。文献 [12] 提出了一种基于电磁制动器的新型的辅助机器人导管插入系统的从机械手,可实现快速响应和无损夹紧。文献 [13] 和 [14] 提出了一种由励磁电流和永磁体混合励磁的电磁制动器以获得更好的控制性能。
目前国内外学者的研究主要集中在电磁制动器拓扑结构与工作原理的创新,但对电磁制动器的设计优化较少。本文通过对摩擦盘式电磁制动器(下文简称电磁制动器)的磁路进行结构分析与解析计算,进而优化磁路实现电磁吸力密度最大化。
本文首先给出电磁制动器基于转矩需求的磁路计算过程,然后有限元仿真分析与解析计算结果进行比对验证其准确性。通过有限元仿真对电磁制动器磁路结构进行分析,系统研究了电磁制动器体积不变的情况下,电磁吸力受内外环中气隙平均磁密比值的影响,提出当内圆环气隙与外圆环气隙的平均磁密比值为1时,电磁吸力可以达到最大值的结构优化原则,有限元仿真验证了结构优化原则的有效性。
1 电磁吸力解析计算
1.1 原理分析
如图1所示,电磁制动器主要由磁轭、衔铁、线圈、摩擦片、盖板和弹簧构成。通电时制动器电磁吸力大于弹簧力使衔铁吸附在磁轭上,摩擦片悬空并通过六角套与转子固定随电机转动;断电时衔铁被弹簧顶压到摩擦片上,摩擦片与衔铁面和盖板面摩擦而产生制动转矩,从而使转子实现快速制动。
制动转矩是电磁制动器的主要性能,制动转矩由摩擦片与衔铁、盖板之间的压力和摩擦系数产生,压力由弹簧弹力提供。参见图2,制动转矩可表达为

式中µ为摩擦片与衔铁、盖板之间的摩擦系数,f为弹簧弹力。
材料及加工精度一定,则摩擦系数确定,制动转矩取决于弹簧弹力与摩擦片尺寸。若摩擦片尺寸保持不变,弹簧弹力越大则制动转矩越大。在线圈通电时,衔铁与磁轭之间的气隙产生电磁吸力抵消弹簧弹力,为使摩擦片悬空,要求:
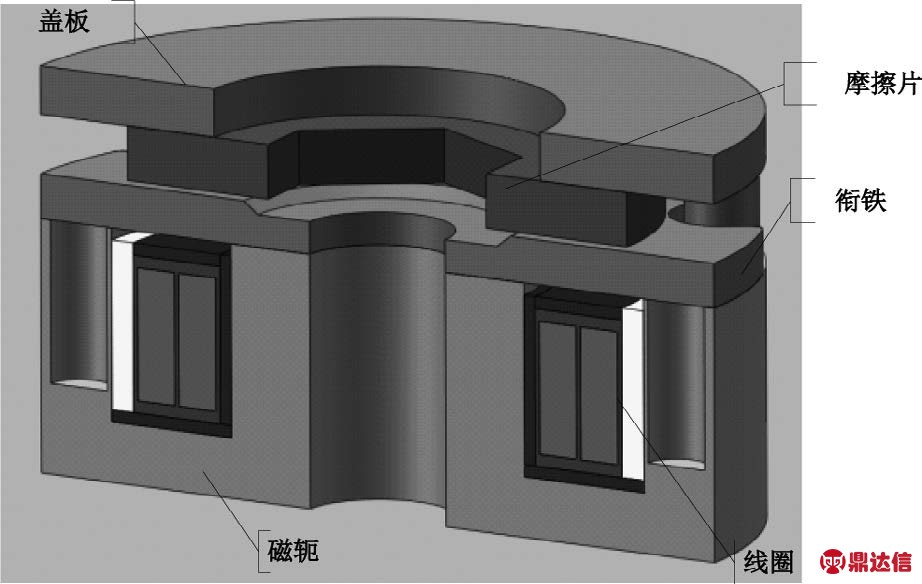
图1 电磁制动器结构示意图
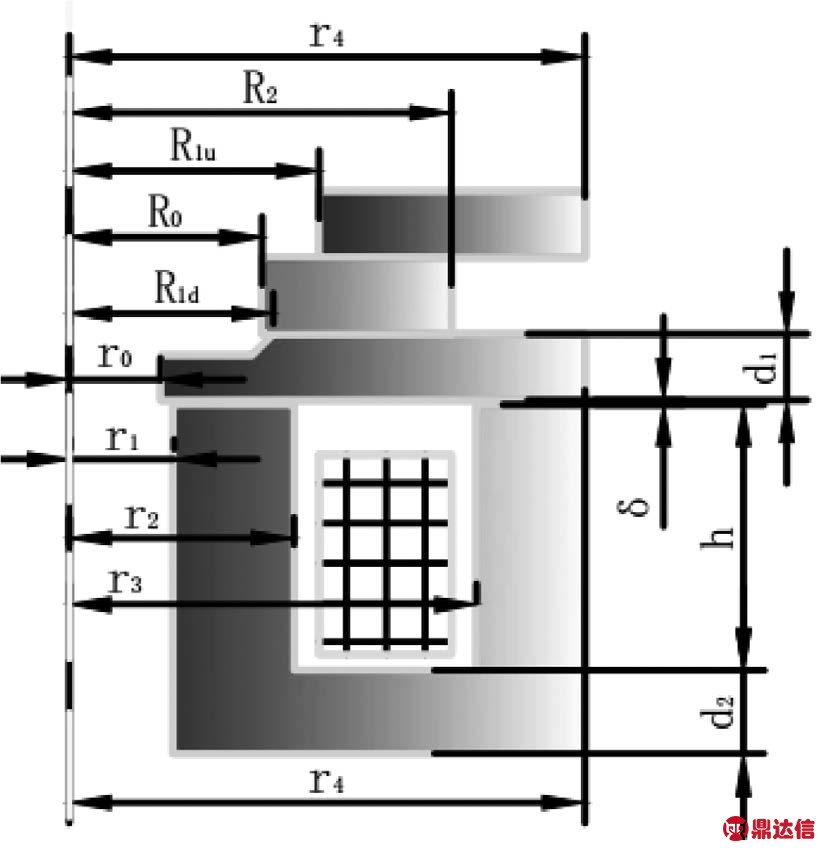
图2 主要尺寸示意图

式中,fel为电磁吸力,由图2尺寸可得电磁吸力表达式为

式中为真空磁导率,Brin为内气隙磁密,Brout为外气隙磁密。
由公式(1)-(3)可在确定制动转矩与基本尺寸参数的前提下,得到电磁吸力的需求值。电磁吸力由气隙磁密与气隙面积决定,气隙磁密由线圈提供的总磁动势与磁路决定,因此电磁吸力解析计算的关键是对电磁制动器磁路的精确计算。
1.2 磁路计算
由图1可见,电磁制动器的磁路是轴对称结构,由衔铁、磁轭、气隙组成,磁动势由线圈产生,如图3所示。
电磁制动器有内外两个气隙,主磁路磁通与内外两个气隙中磁动势分别为:

式中φ为主磁路磁通,Rin为内气隙磁阻,Rout为外气隙磁阻,Fin为内气隙磁动势,Fout为外气隙磁动势。
在区域1与区域3中,可认为磁密均匀分布,由图2尺寸可得到如下关系式:


图3 电磁制动器磁路

式中S1、S3分别为区域1与区域3的截面积,B1、B3分别为区域1与区域3的磁密,H1、H3分别为B1与B3对应的磁场强度,F1、F3分别为区域1与区域3的磁动势。
区域2与区域4中磁密不是均匀分布,磁密随着半径的增大而降低,因此本文将这两块区域划分成十个等宽圆环,认为每个圆环中磁密均匀分布,由图2尺寸可得如下表达式:
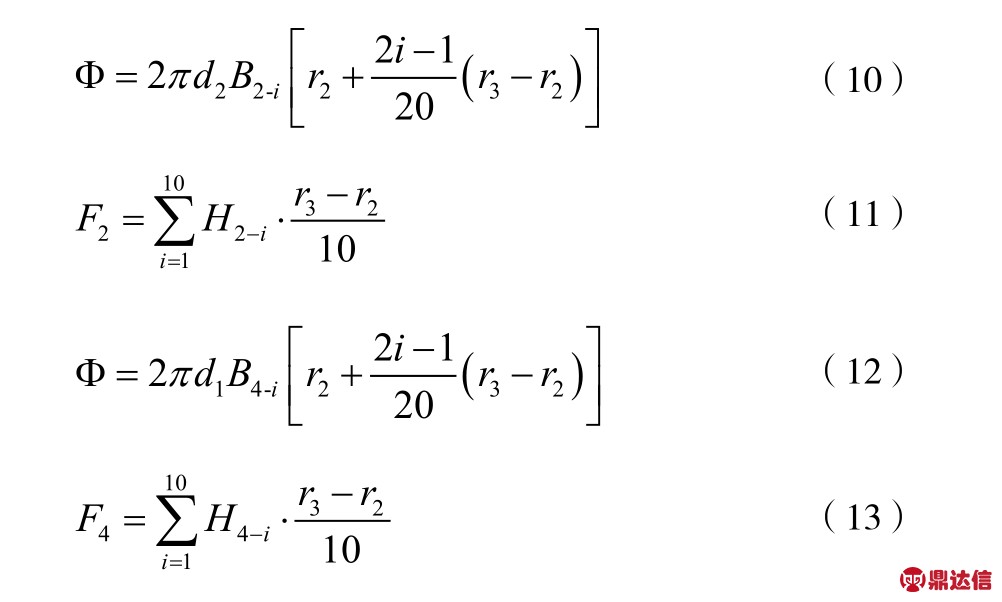
式中B2-1~B2-10、B4-1~B4-10分别为区域 2 与区域 4中十个等宽圆环内磁密,H2-1~H2-10、H4-1~H4-10分别为B2-1~B2-10 与B4-1~B4-10对应的磁场强度。
由公式(4)-(13)可以得到线圈内磁动势为:

式中I为绕组内电流,N为线圈匝数,F0为总磁动势。
由公式(4)-(14),在确定线圈总磁动势与制动器主要尺寸参数的前提下,即可计算出气隙磁密,代入公式(3)可解析计算得到电磁吸力。
1.3 仿真验证
表1为一台6N·m电磁制动器的主要参数。
基于表1所给尺寸构建电磁制动器三维有限元仿真模型,在ANSYS Maxwell中进行分析,电磁场仿真结果如图4所示。
对图4有限元模型进行电磁吸力计算,仿真计算结果与本文解析计算结果具有良好的一致性,如表2所示。
2 设计优化
本文引入电磁吸力密度概念以评测电磁制动器结构设计的优劣。电磁吸力密度γel定义为电磁制动器单位体积所产生的电磁吸力,如下所示:

式中Vmag表示包含总磁路的最小密封体,定义如下:

对于电磁吸力,由公式(3)不难看出,电磁吸力的大小由内外两个气隙的磁密与面积决定。对公式(3)进行进一步化简可以得到电磁吸力与气隙平均磁密、主磁路磁通的关系式为:

式中、 r o ut分别为内气隙与外气隙的平均磁密,定义如下:
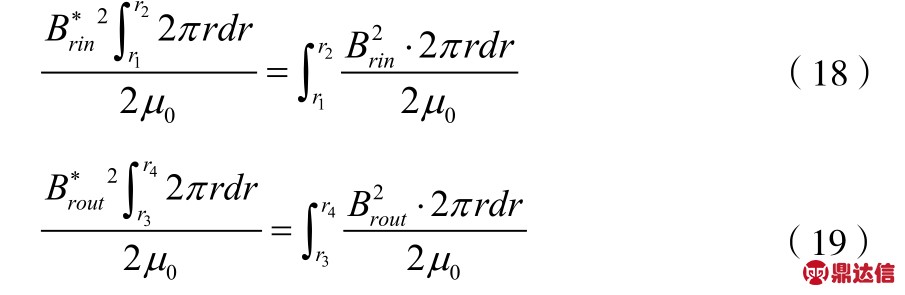
由公式(17)可以看到,在磁通不变的条件下,内外气隙平均磁密总和越高则电磁吸力越大。受公式(4)与内径外径尺寸约束,内外环一个气隙平均磁密升高必然会导致另一个气隙平均磁密降低,因此当内外环气隙平均磁密相等时有可能获得电磁吸力的最大值,此时有
表1 电磁制动器主要参数
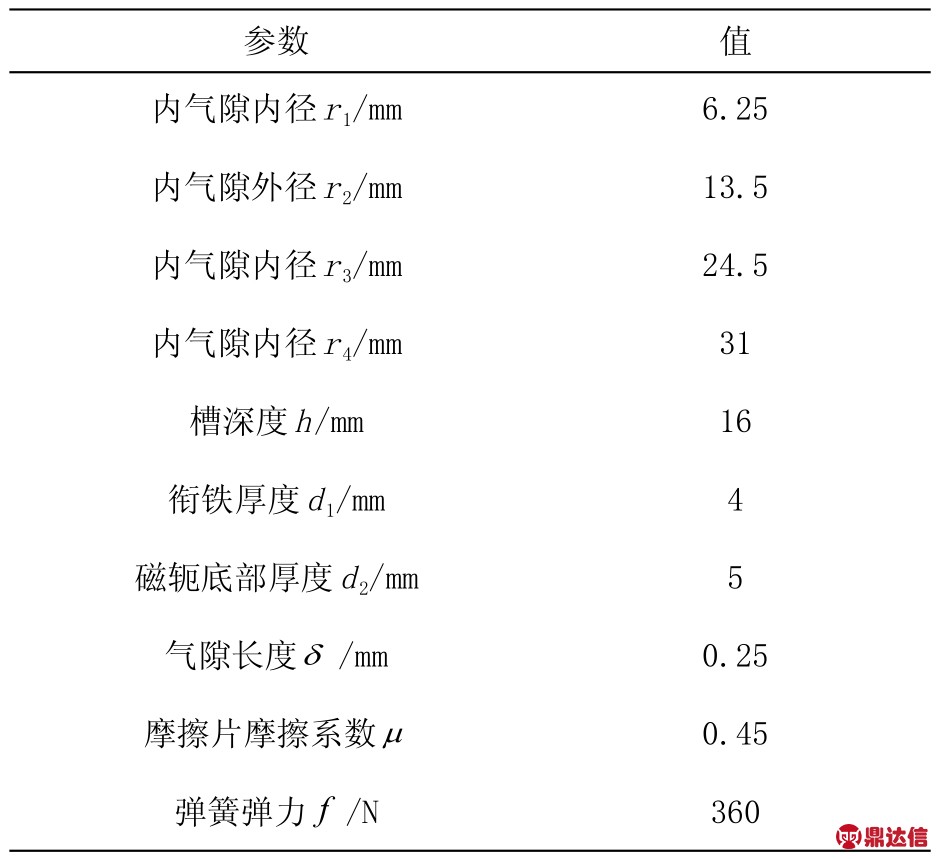
表2 电磁吸力仿真值与解析计算值对比
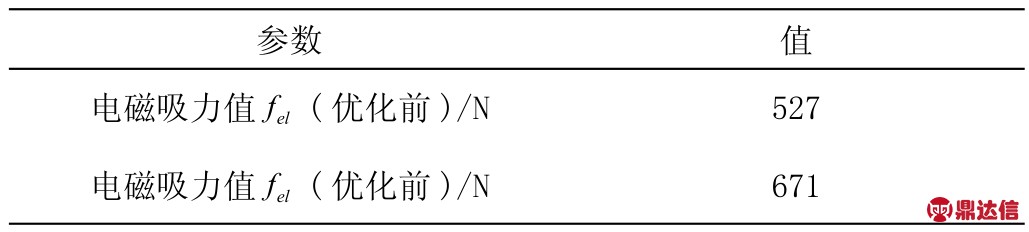
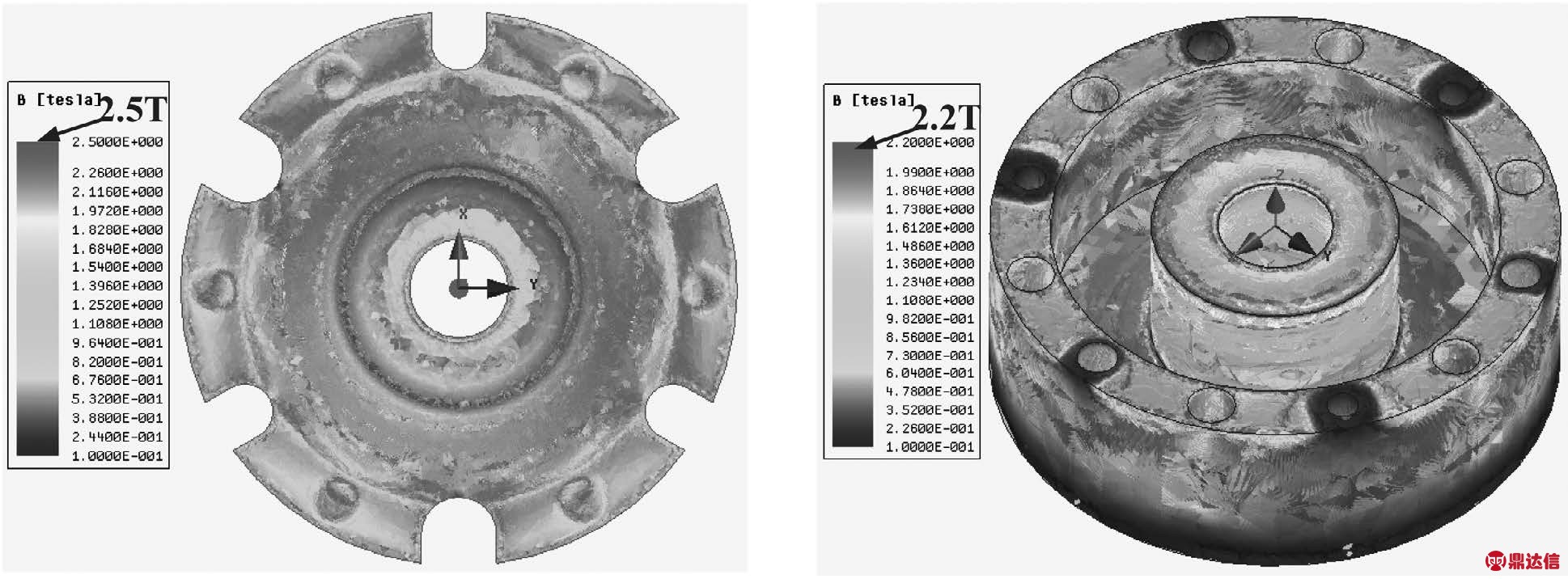
图4 电磁制动器磁场仿真结果

本文利用有限元仿真对公式(20)进行了验证。由于三维模型的仿真速度较慢,结构更改涉及的参数较多,总体效率较低,因此本文使用去除所有弹簧孔、螺纹孔与凹槽设计的简化二维模型进行讨论。简化二维模型的电磁吸力仿真结果与三维模型存在一定偏差,但是不会改变电磁吸力特性的变化趋势。在二维有限元仿真时保持模型的槽截面积、槽满率、线圈磁动势与r0、r1、r4不变,仅调整r2、r3使得内外吸力环中的平均磁密的比值发生变化,对电磁制动器模型进行仿真分析,得到结果如图6所示。
通过图6,可以观察到随着线圈磁动势从200安匝增加到1 500安匝,电磁吸力均在内外气隙平均磁密值相等时达到最大值,可认为调整内外气隙平均磁密值使其相等可实现电磁制动器结构的最优设计。磁动势较小时,整个磁路中磁密较低,磁密与磁场强度近似呈线性关系,因此优化的效果不是很明显。随着线圈磁动势的提升,在一些区域开始出现磁路饱和现象,优化结构可有效缓解磁路饱和现象,从而明显提升电磁吸力。
表1结构参数电磁制动器的气隙磁密波形如图7所示,可以观察到电磁制动器内气隙的磁密为1.5 T左右,外气隙的磁密仅为0.5 T左右,磁密分布严重不均匀。根据本文提出的优化原则,调整电磁制动器尺寸使内外气隙平均磁密相等,优化后气隙磁密波形如图7所示。
对优化前后电磁制动器的简化二维有限元仿真模型进行比较分析,电磁吸力仿真值对比如表3所示,可以观察到电磁吸力提升了27 %,由于Vmag没有发生变化,电磁吸力密度也提升了27 %。
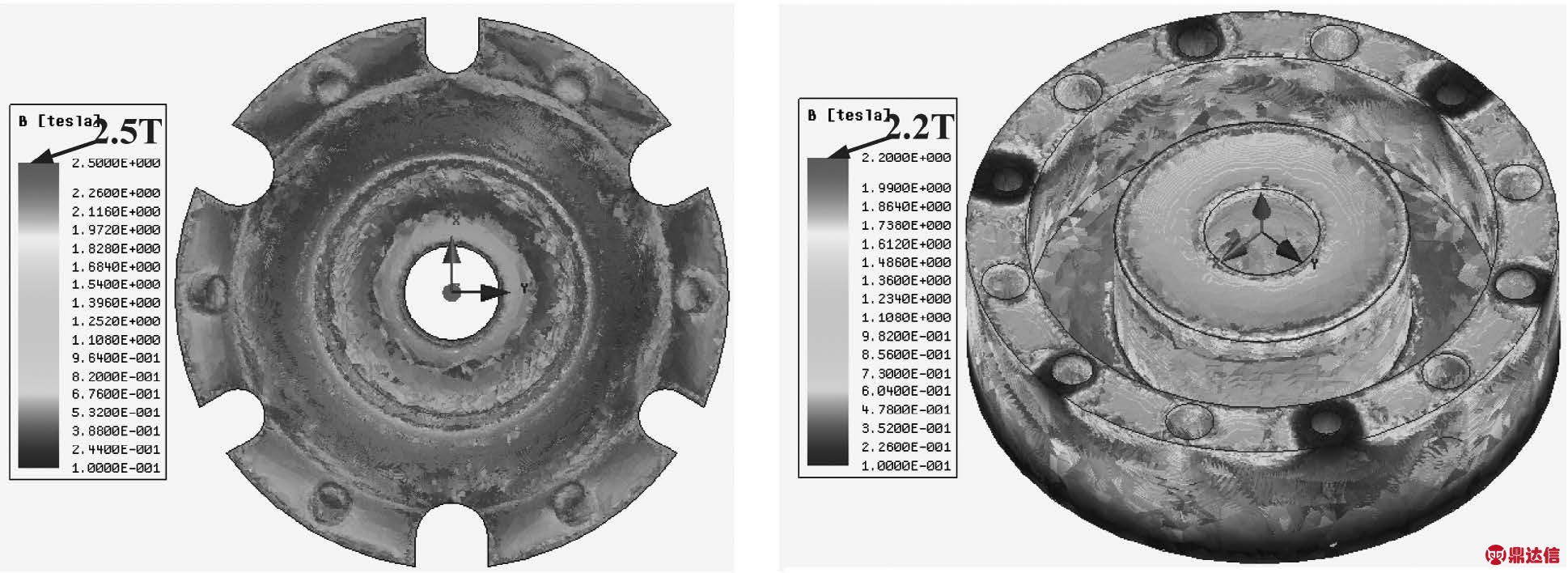
图5 电磁吸力在不同磁动势下随气隙平均磁密比变化曲线
表3 优化前后电磁吸力对比
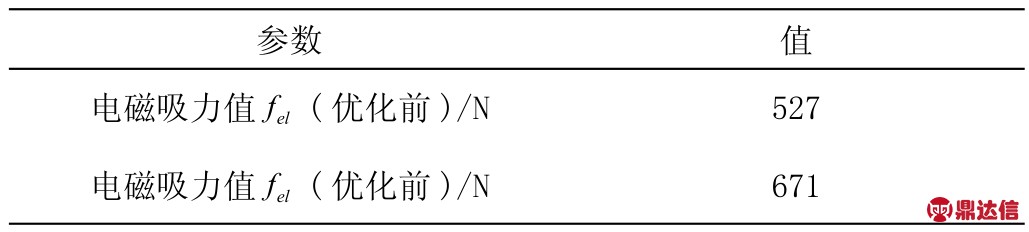
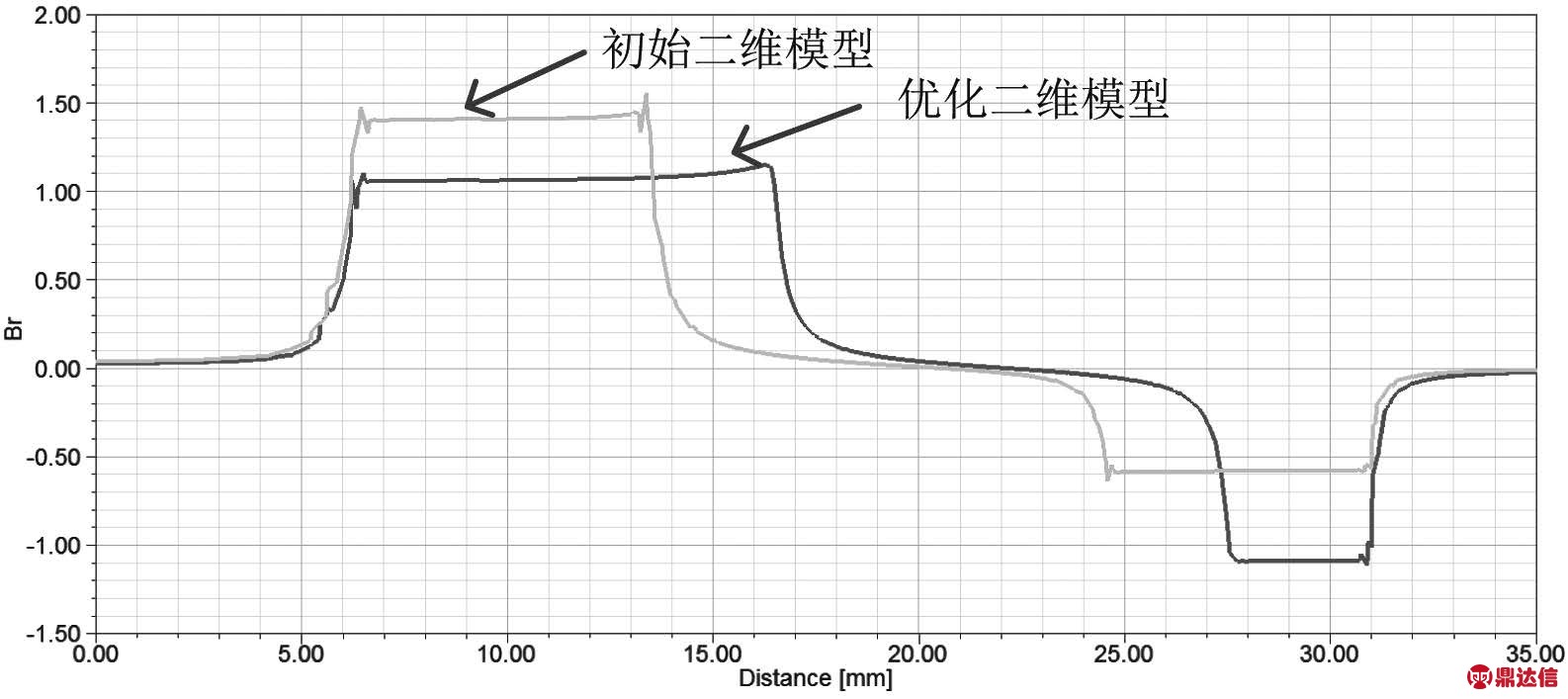
图6 优化前后气隙磁密波形
3 仿真验证
基于本文所提出的结构优化原则,构建了电磁制动器三维有限元模型,对表1电磁制动器进行了优化,调整尺寸使内气隙与外气隙平均磁密接近相等,优化前后的三维有限元仿真对比如表4所示。可以观察到制动转矩与电磁吸力均提升了约15 %,电磁吸力密度提升了约17 %。
优化模型的电磁场仿真结果如图7所示。可以观察到,电磁制动器磁路中的磁密分布变得更为均匀,几乎没有磁饱和的区域。
优化模型与初始模型的温度场仿真结果如图8(a)与(b)所示。可以观察到,线圈与铁磁的材料温度几乎没有变化。
表4 电磁制动器优化前后主要参数
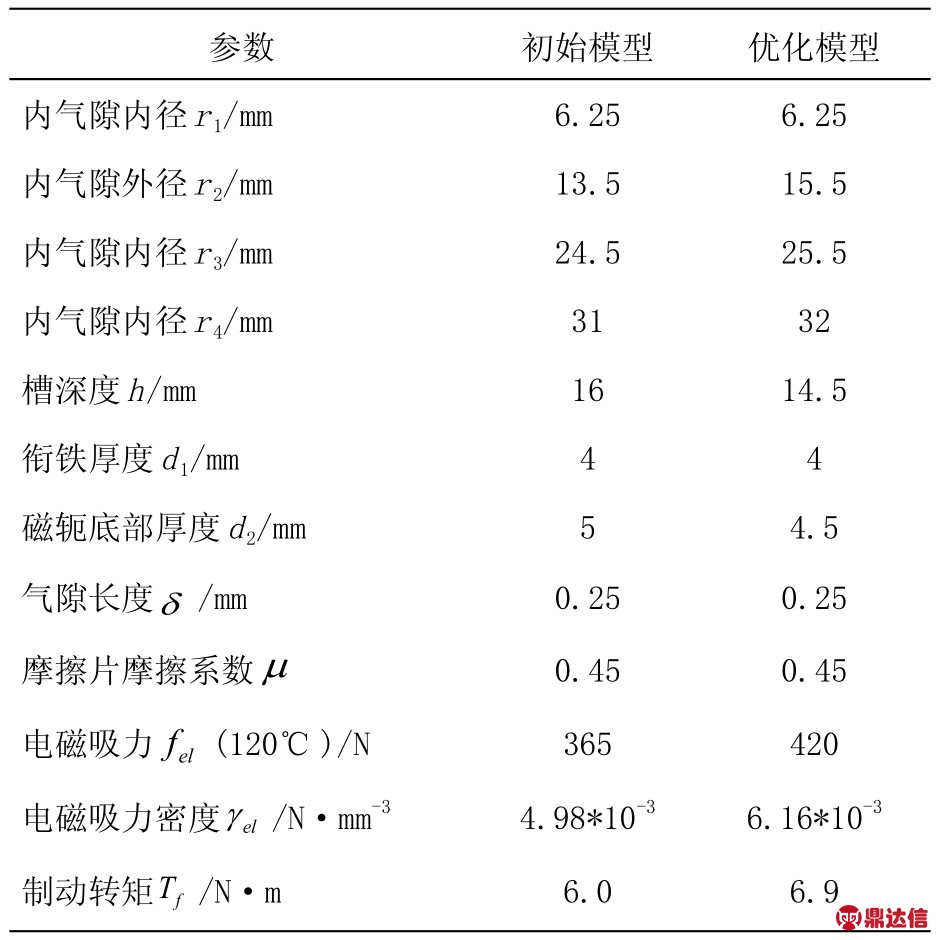
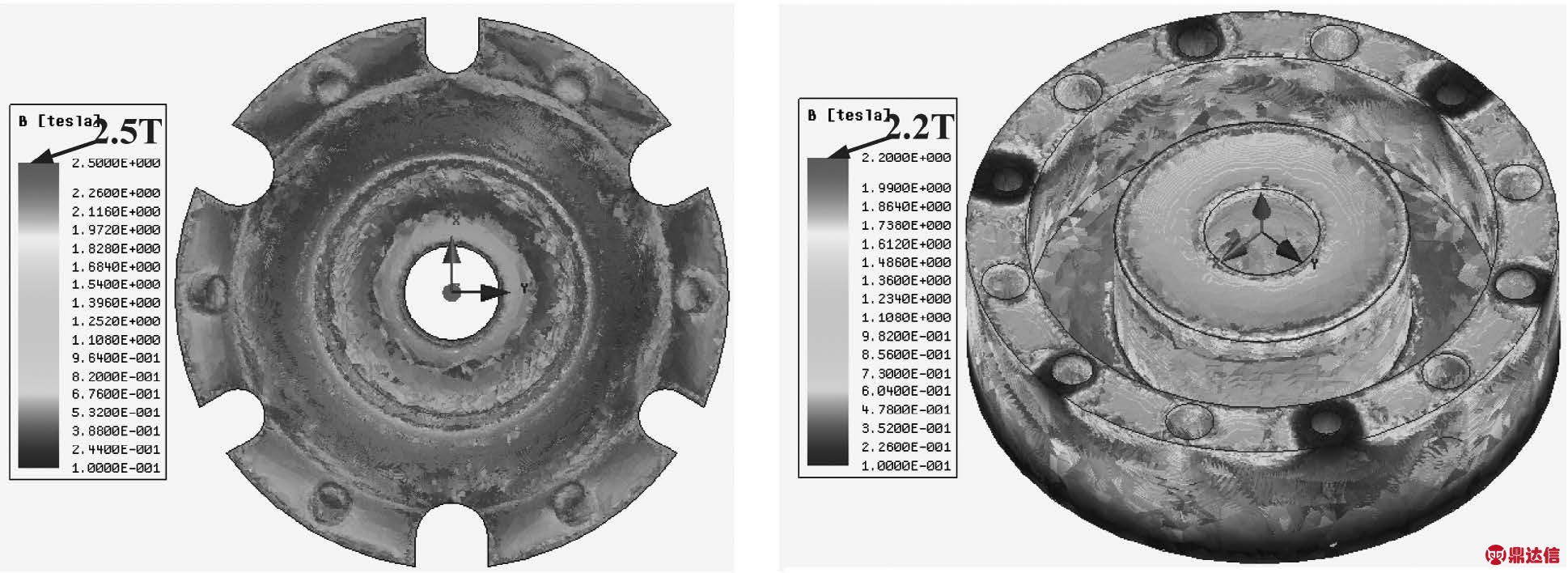
图7 优化模型磁场仿真结果
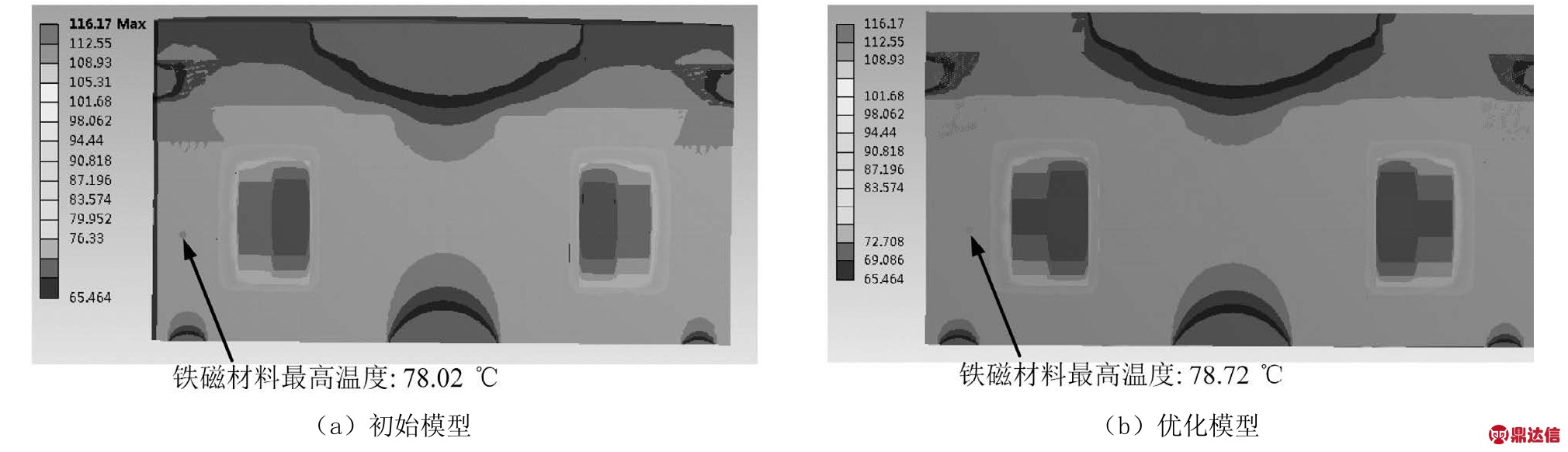
图8 温度场仿真结果
4 结论
本文基于磁路分析与解析计算,定义了电磁吸力密度的概念,针对摩擦盘式电磁制动器提出一种磁路优化原则,解决了电磁制动器磁路利用率不高、电磁吸力密度较低的问题,并进行了二维与三维有限元仿真,仿真结果表明:
1)在Vmag与Φ保持不变的前提下,电磁吸力随内外气隙平均磁密的比值而变化,当内外环平均磁密的比值为1时达到电磁吸力最大值,即电磁吸力密度最大值。
2)对于一台6 N·m电磁制动器,优化其结构参数使内外环气隙平均磁密趋于相等,有效提升了其制动转矩与电磁吸力密度,同时保持温度几乎不变,验证了所提结构优化原则的有效性。