摘 要:汽车变速箱垫片的选取方式是影响变速箱装配质量和效率的关键,传统的选垫方法已经不能满足现代化生产的要求,为此作者研制了一种新型的汽车变速箱垫片自动选配系统.该系统采用相对测量原理,由工业计算机控制,控制部分以Visual C++ 6.0为主要开发工具完成界面和控制工作,提高了变速箱装配的质量和效率.
关键词:变速箱; 垫片自动选配系统; VC++; 计算机控制
0 引 言
汽车变速箱装配质量的影响因素很多,其中一个最重要的因素是如何选取垫片厚度的问题[1].传统的选垫方法是手工选垫,不仅精度不高而且浪费时间,选垫效率低下,返工率高.随着我国汽车工业的发展,对汽车变速箱质量和数量的要求不断提高,传统的手工选垫方法已经不能满足现代化生产的要求[4].而本课题为深圳比亚迪汽车有限公司研制的汽车变速箱垫片自动选配机采用相对测量原理,由工业计算机智能控制,采用Visual C++ 6.0编程语言和Access数据库相结合的方式完成界面和控制工作,操作简便,选垫准确性高,提高了变速箱装配的质量和效率.
1 设计思想
汽车变速箱分为前壳体和后壳体两大部分,其中前壳体由主轴承孔、副轴承孔、差速器轴承孔3部分组成,后壳体由主轴承、副轴承、差速器轴承3部分组成[3].
以H1、H2、H3分别表示主轴承孔、副轴承孔及差速器轴承孔的高度,用h1、h2、h3分别表示主轴承、副轴承及差速器轴承的高度,δ表示预留间隙,k表示调整间隙,其中δ、k是可以设定的常量.则主轴承应选垫片厚度m1=H1-h1+δ+k,副轴承应选垫片厚度m2=H2-h2+δ+k,差速器轴承应选垫片厚度m3=H3-h3+δ+k.
只要测量出H1、H2、H3及h1、h2、h3的值,就可以得出3类轴承应选垫片的厚度.但是,通过直接测量的方法很难测量出H1、H2、H3及h1、h2、h3的值,为此我们通过相对测量的方法对H1、H2、H3及h1、h2、h3进行测量.我们采用标准件作为测量的基准来进行相对测量.以主轴承为例说明如下:H1=L1+x1,h1=L2+x2,其中L1、L2为对应于H1、h1的基准参数,由测量前的校正操作获得;x1、x2为对应于H1、h1的位移传感器的测量值,其值都在-1~+1 mm范围内[2].
对变速箱前壳体的3个测量值H1、H2、H3进行判断,如果H1、H2、H3均在各自设定的上、下限之间,则前壳体为合格产品;对变速箱后壳体的3个测量值h1、h2、h3进行判断,如果h1、h2、h3均在各自设定的上、下限之间,则后壳体为合格产品;变速箱前、后壳体均为合格产品时,才可进行下一步垫片选配.
根据垫片厚度不同,共分为40组垫片.其中主、副轴承共用20组垫片,垫片组号1~20;差速器轴承单独用20组垫片,垫片组号1~20.以主轴承为例,给出选垫片组号公式如下:
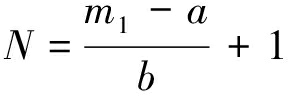
其中m1为主轴承应选垫片厚度,a为主轴承分组下限,b为主轴承分组间隔.
2 硬件组成及数据处理
2.1 硬件组成
该设备主要由前壳体测量台、后壳体测量台、垫片选配台及电气控制部分等组成.
前壳体测量台的测量对象是主轴承孔、副轴承孔及差速器轴承孔的高度.该测量台由载物平台和传感器安装架等组成.要测量的前壳体放置在载物平台上,测量时由气缸压紧被测件.传感器安装架上安装有7支传感器,其中4支传感器用于被测件定位测量,如果其最大值和最小值的差不大于定位精度(定位精度是可设定的值),则认为被测件放平,否则检查定位情况,另外3只传感器用于测量主轴承孔、副轴承孔及差速器轴承孔高度.
后壳体测量台的测量对象是主轴承、副轴承及差速器轴承的高度.该测量台由机械台身、载物平台和测量装置等组成.要测量的后壳体放置在载物平台上,测量时依靠气缸拉下测量装置.测量装置上安装有7支传感器,其中4支传感器用于被测件定位测量,如果其最大值和最小值的差不大于定位精度,则认为被测件放平,否则检查定位情况,另外3只传感器用于测量主轴承、副轴承及差速器轴承高度.
垫片选配台上有一个报警器及40组垫片放置槽,每个放置槽上安装有一个光电传感器,一个绿色指示灯,选配时按绿灯显示取走相应的垫片,误取时报警器响.
电气控制部分以研华公司生产的工业控制计算机为核心,配有PCL813、1754及1758u数据采集卡,外围各数据或开关信号通过此卡由计算机采集或控制[6].
2.2 数据处理
用以测量定位信号、前壳体H1、H2、H3及后壳体h1、h2、h3的14支传感器由输力强公司生产,其测量范围为-1~+1 mm,转换为电压信号后的放大输出为-2.5~+2.5 V[2].
3 软件设计
考虑到Visual C++ 6.0对人机界面设计的快速、简单及便于维护等优点,本课题研制的汽车变速箱垫片自动选配机的软件部分采用Visual C++ 6.0编程语言和Access数据库相结合的方式,在Windows XP操作系统下来编制[5].
本系统有4种主要工作状态:测量及选配、标准件校正、参数设置和数据统计.由于工业计算机和新的开发软件的使用,使得该设备具有较高的控制灵活性和直观的人机界面.
3.1 标准件校正
当系统进入标准件校正状态时,工业计算机显示标准件校正界面.校正操作用于对前、后壳体H1、H2、H3及h1、h2、h3的基准参数进行校正.以主轴承为例说明如下:此时校正操作用于对H1、h1的基准参数L1、L2进行校正,有L1=P1+x1,L2=P2+x2. 其中,P1、P2为对应于H1、h1测量而特制的标准件的高度,P1、P2作为系统参数,在系统的“参数设置”状态下由人工输入.
标准件校正操作为前、后壳体H1、H2、H3及h1、h2、h3的实际测量提供基准参数,消除系统误差,提高测量准确性[5].因此要求操作者每天开机后进行一次标准件校正.系统校正界面如图1所示.
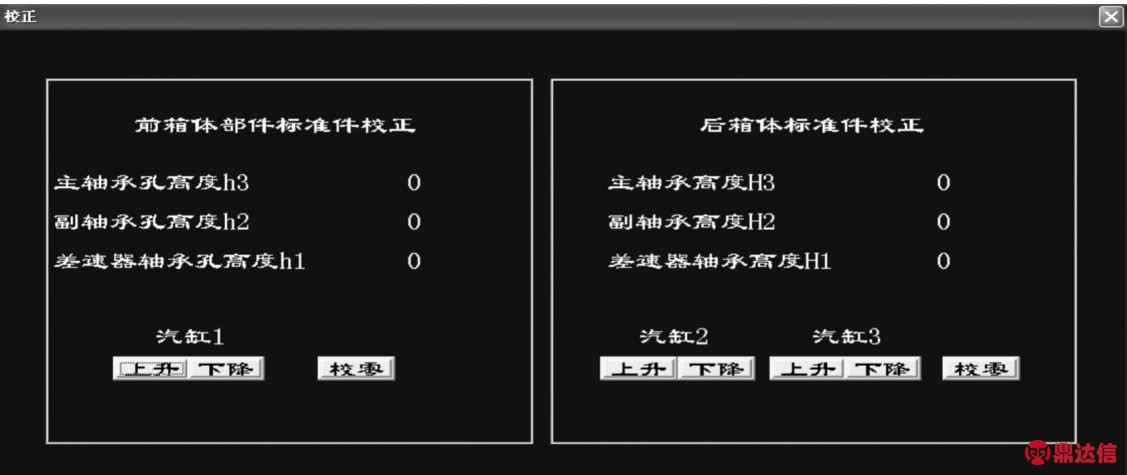
图1 校正界面
3.2 参数设置
本设备需要设置的参数主要有4类:前壳体参数、后壳体参数、垫片分组参数及被测件定位精度.其中,前壳体参数包括主轴承孔、副轴承孔及差速器轴承孔的名义值、上下限值及标准件值;后壳体参数包括主轴承、副轴承及差速器轴承的名义值、上限值及标准件值;垫片分组参数包括主轴承垫片、副轴承垫片及差速器轴承垫片的分组下限、分组间隔、调整间隙及预留间隙.这些参数均按照生产的实际要求进行设置.参数设置界面如图2所示.
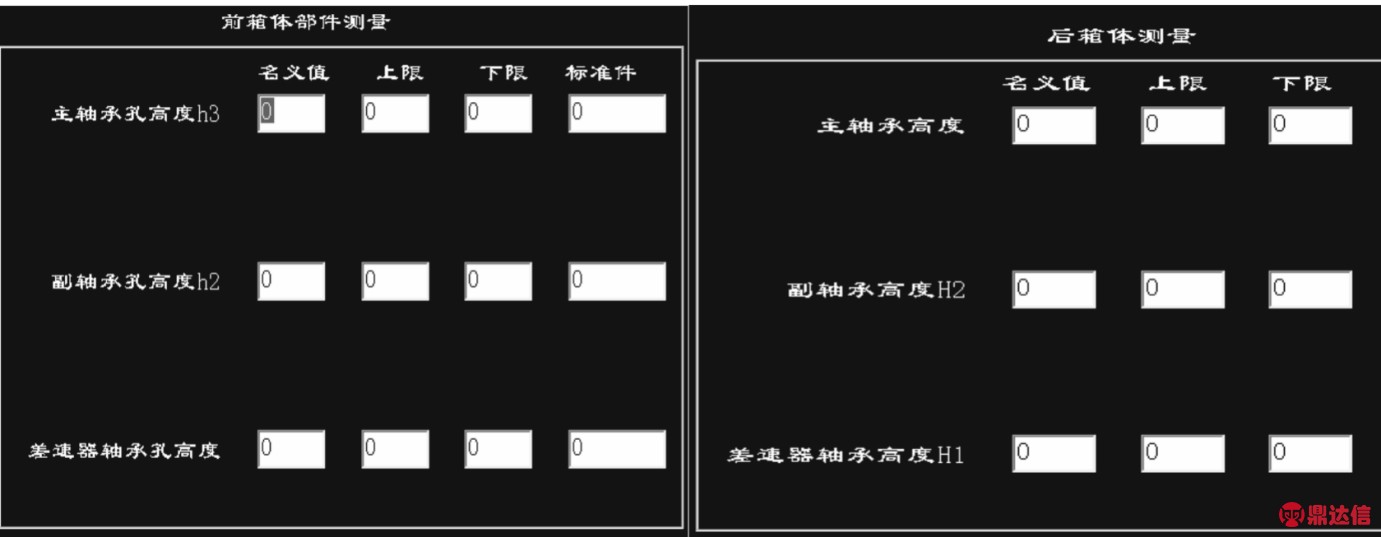
图2 参数设置界面
3.3 测量及选配
测量及选配状态设备的正式工作状态.测量和选配过程如下:
前壳体测量:静止时气缸回位——手工放入标准件——按下校对键——气缸带压紧装置下压到位延时3秒——气缸自动回位,校正结束——先用扫描枪扫描工件条码,然后将前壳体放入测量位置——按测量开关——气缸带压紧装置下压到位延时3秒(其中到位后,首先4#~7#传感器采样,如果其最大值和最小值的差不大于定位精度,则1#~3#传感器采样并得出主轴承孔、副轴承孔及差速器轴承孔高度H1、H2、H3;否则检查定位情况)——传感器采样完毕,气缸退回,取走工件.
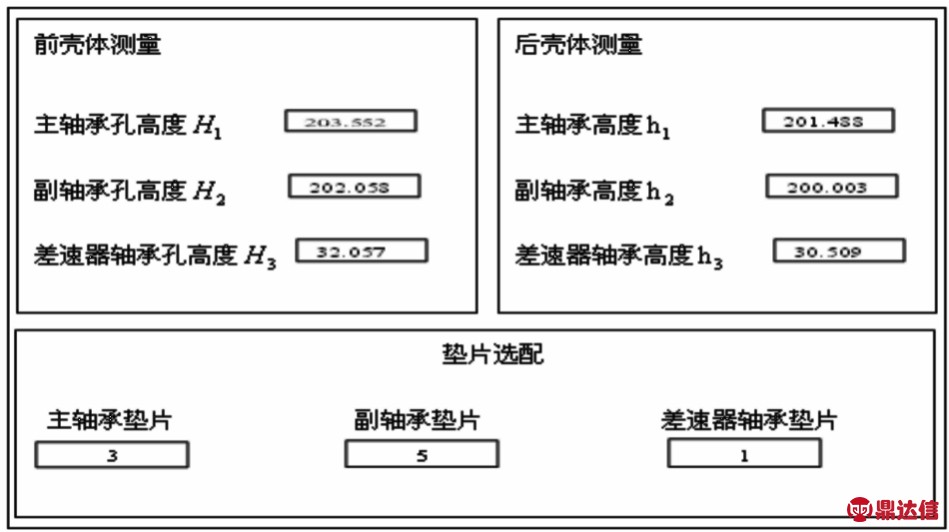
图3 测量及选配界面
后壳体测量:静止时气缸伸出——手工推入标准件到测量位置,然后将测量部件拉下并放置到位——按下校对键——气缸带测量装置下压到位延时3秒——气缸自动回位,校正结束;将标准件及测量装置复位——后壳体到位,先用扫描枪扫描条码,然后将测量部件拉下并放置到位——按测量开关——气缸带压紧装置下压到位延时3秒(其中到位后,首先4#~7#传感器采样,如果其最大值和最小值的差不大于定位精度,则1#~3#传感器开始采样并得出主轴承、副轴承及差速器轴承高度h1、h2、h3;否则检查定位情况)——传感器采样完毕,气缸松开,将测量装置复位.
垫片选配:按下选配键,工业计算机自动计算出所需的组别,并按主轴承、副轴承、差速器轴承的顺序依次点亮该组别的绿灯,取出一个,接着点亮下一个垫片组的绿灯,直到一个变速箱选配完.
一组工件测量结束后,工业计算机显示测量及选配完成界面,图3为一组工件测量结束界面.
3.4 数据统计
本设备具有数据统计功能,可以检索出某一段时间内测量的数据,且能将其导出到excel表中;可以统计前、后壳体H1、H2、H3及h1、h2、h3的合格量与不合格量;可以绘制SPC图.数据统计界面如图4所示.
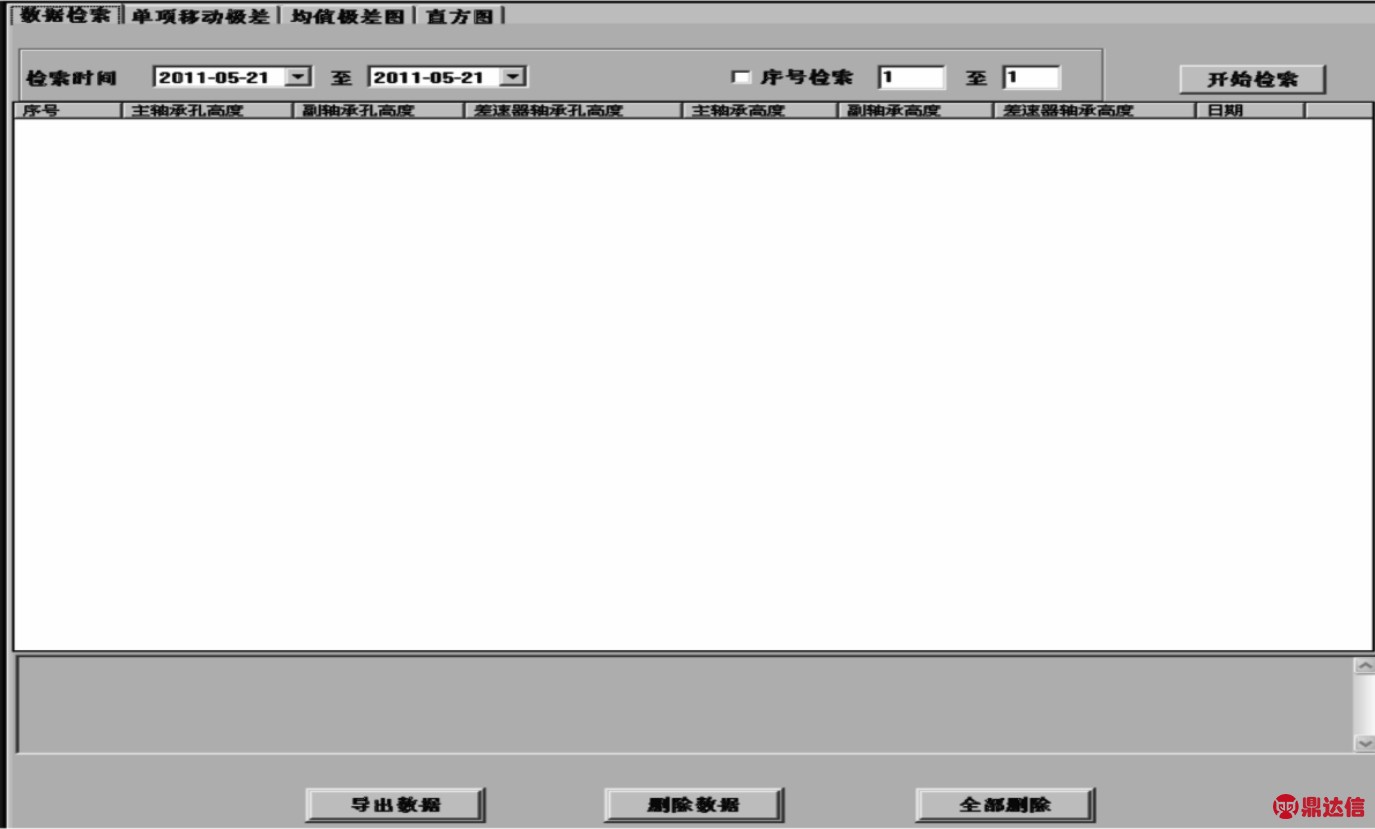
图4 数据统计界面
4 结束语
为了提高汽车变速箱选垫的准确度及速度,保证变速箱装配的质量,克服传统选垫的缺点,为此深圳比亚迪汽车有限公司研制了一款新型汽车变速箱自动选配机.本设备的研制,很大程度上提高了工人的操作效率、提高了选垫的准确性、提高了变速箱的装配质量和效率,从而大大降低了返工率.系统的人机界面友好,操作简单,具有很好的应用前景.