摘 要: 核电汽轮机润滑油对机组运行安全起着至关重要的作用,其清洁度对轴承润滑性能有直接的影响。阐述了核电汽轮机润滑油的主油箱滤网设计特点,根据现有核电项目油系统现场冲洗、反复用油对滤网的冲击情况,对主油箱滤网进行了相关结构优化研究,保证了后续机组滤网的耐久安全,从而保证机组轴承用油的可靠性。研究成果可为同类型机组的润滑油滤网设计提供参考。
关键词: 核电汽轮机; 润滑油; 滤网; 优化
从岭澳二期3号机组开始,东方汽轮机有限公司负责核电汽轮机润滑油系统的自主化设计,并对主油箱内部进行详细设计,以满足润滑油供油条件及保证润滑油清洁。由于润滑油循环经过了轴转动加热、压力平衡调节等过程,再回到主油箱的润滑油品质已明显较低。所以需要设置滤网,用于过滤润滑油内部颗粒杂质,它是有效保证润滑油清洁度及品质的重要组件。润滑油滤网要求过滤精度高,滤网网孔尺寸就需要很小,这样滤网本身强度等性能就会较差,严重时会造成回油滤网被冲破从而导致滤网过滤功能丧失的情况。核电汽轮机润滑油油量很大且运行可靠性要求较高,回油滤网在保证核电汽轮机机组润滑油洁净度中起着关键作用,是核电主油箱设计的关键和重点。
1 核电主油箱滤网设计介绍
1.1 主油箱滤网的功能及要求
在主油箱结构设计中,润滑油从汽轮机机组轴承回油至主油箱接口处,主油箱内部设计了回油滤网。主油箱内部所装的油的杂质颗粒情况主要由主油箱回油滤网的性能决定。
回油滤网承受的来油方式主要有润滑油传输系统注油至油箱、所有轴承润滑油回油至油箱、润滑油系统设备回油至油箱,以及油处理系统处理后回油至油箱。
上述需经过滤网的来油方式或多或少都带有杂质,且核电汽轮机润滑油量较火电机组高出3~5倍,这就要求滤网不仅能较好地过滤杂质,还需具有较强的抗冲击强度。滤网功能及位置简易图如图1所示。
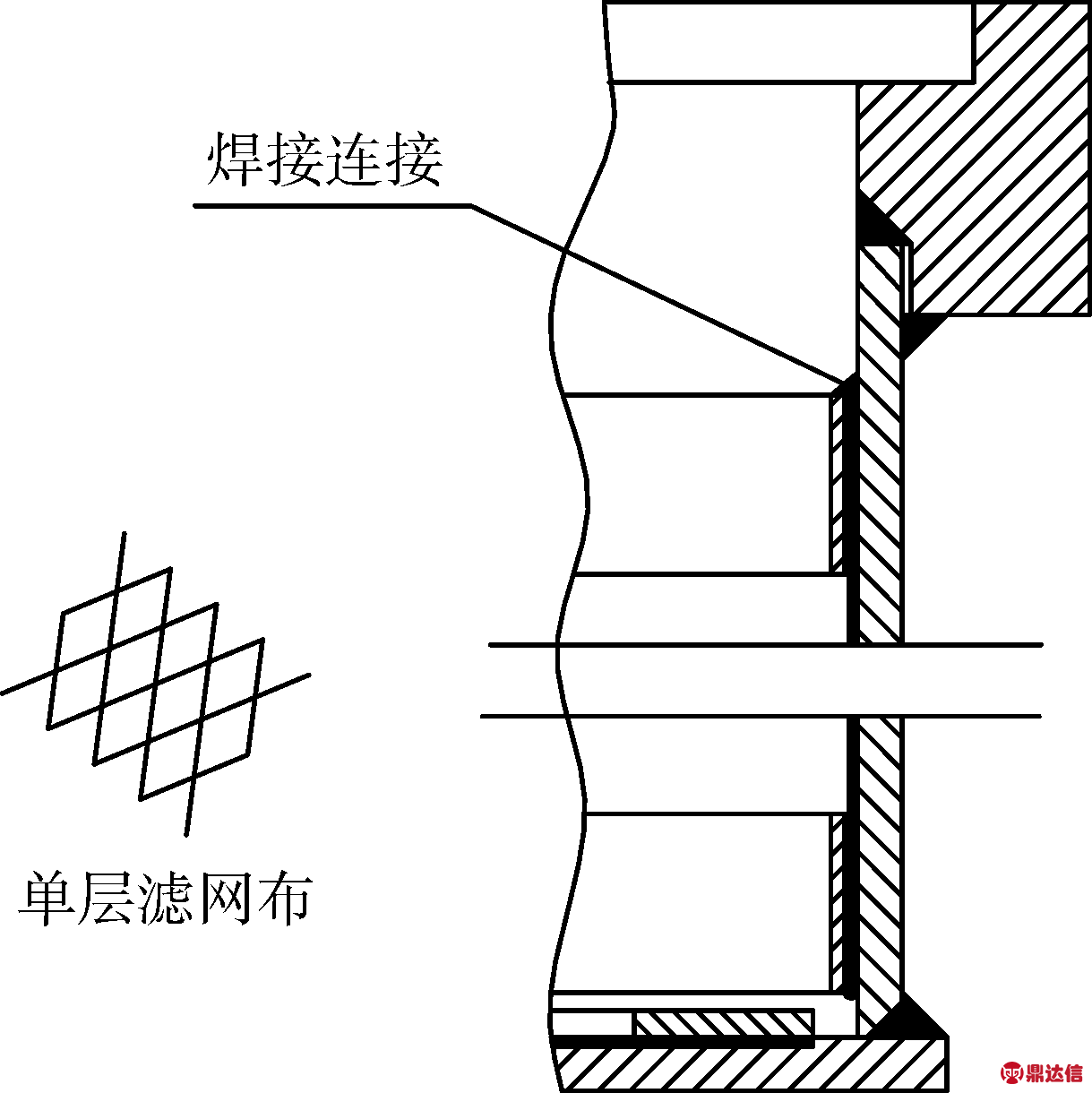
图1 润滑油循环流程中主油箱滤网位置示意图
1.2 主油箱滤网的设计
1.2.1 润滑油特性
一般核电用汽轮机润滑油采用的是ISO VG46,在注入润滑油系统前,其油品的基本性能均满足ISO或SAE标准中的统一要求[1]。但经过轴承润滑、温度变化及管道通流,润滑油品质会有所变化,回油滤网主要对大颗粒杂质进行过滤,另外主油箱内部还设有润滑油处理系统,处理润滑油的杂质及水分。
1.2.2 回油滤网的结构设计
回油滤网选型要点主要在于金属网孔尺寸和金属丝丝径的选择。根据国家标准工业用金属丝编织方孔筛网(GB/T5330-2003)和火电润滑油滤网方面的信息,核电汽轮机用的回油滤网尺寸依旧采用粗滤网(孔径380 μm )、细滤网(孔径250 μm )结合,但结构形式和位置不一样。润滑油流动方向上,细滤网在前,粗滤网在后,且呈圆筒状,分布在主油箱整个回油区域,回油滤网结构如图2所示。
核电汽轮机主油箱粗细滤网的顺序相比于常规的粗滤网在前,细滤网在后有其自身优势,如果按粗在前、细在后设计,杂质颗粒会在内外滤网网格之间存留, 容易在内外滤网之间堆积而形成堵塞,清洗时需要同时提出内外滤网,不够方便。如果将内部细滤网放在前面,则可直接提出,清洗杂质,不需要将外部滤网取出。
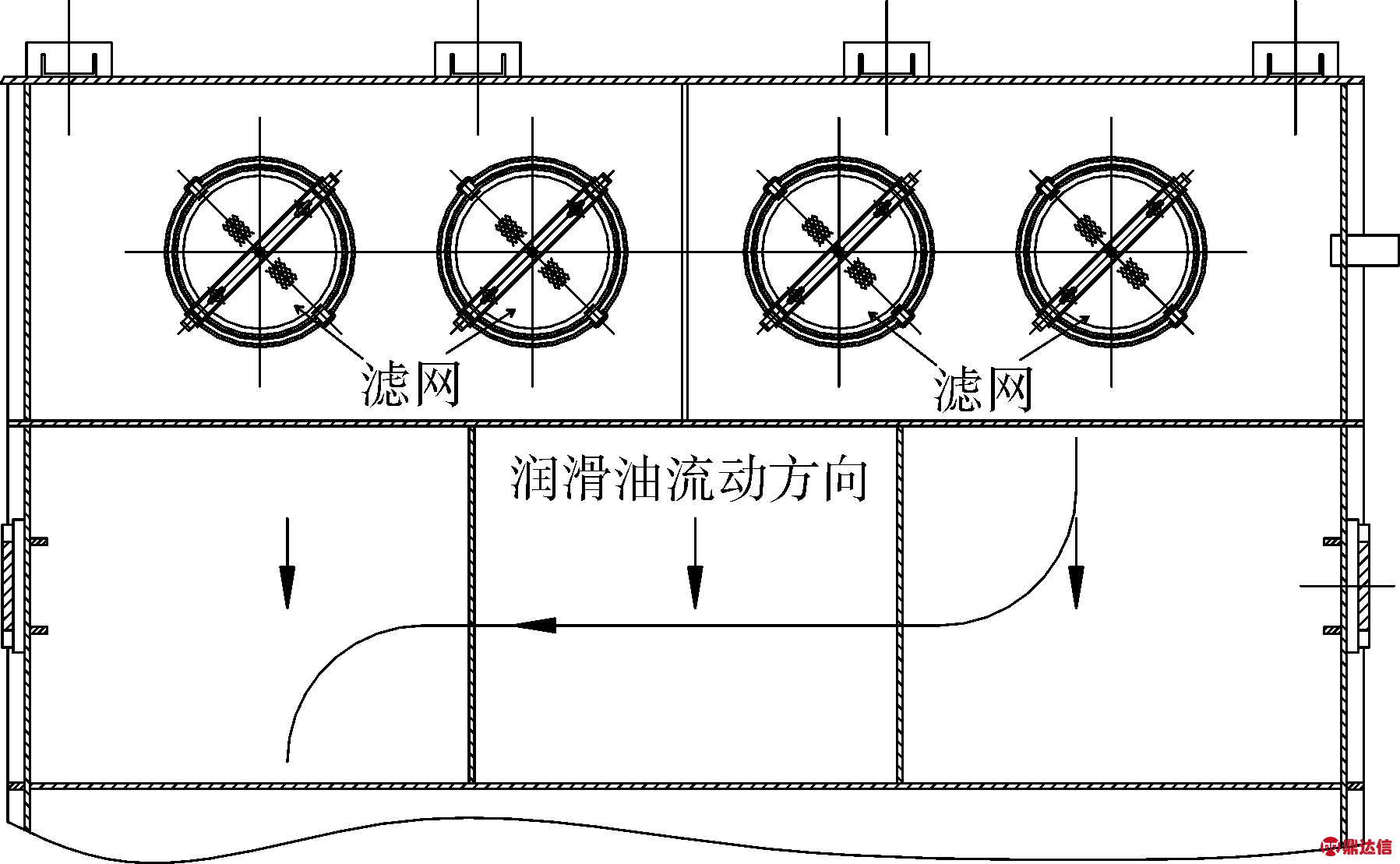
图2 核电汽轮机润滑油回油滤网结构(俯视)
核电汽轮机采用的回油滤网的金属丝网状结构为:粗滤网孔径380 μm ,不锈钢丝丝径0.224 mm;细滤网孔径250 μm ,不锈钢丝丝径0.16 mm。
回油滤网对应的网孔尺寸及通流面积大小如表1所示。
表1 滤网网孔参数[2]

滤网丝布柔软,需要刚度较大的支撑筒作为紧固架,便于固定及安装。图3简单说明了滤网和支撑筒的关系,支撑筒由钢板钻孔后卷制而成,保证一定通流能力的同时能固定回油滤网。
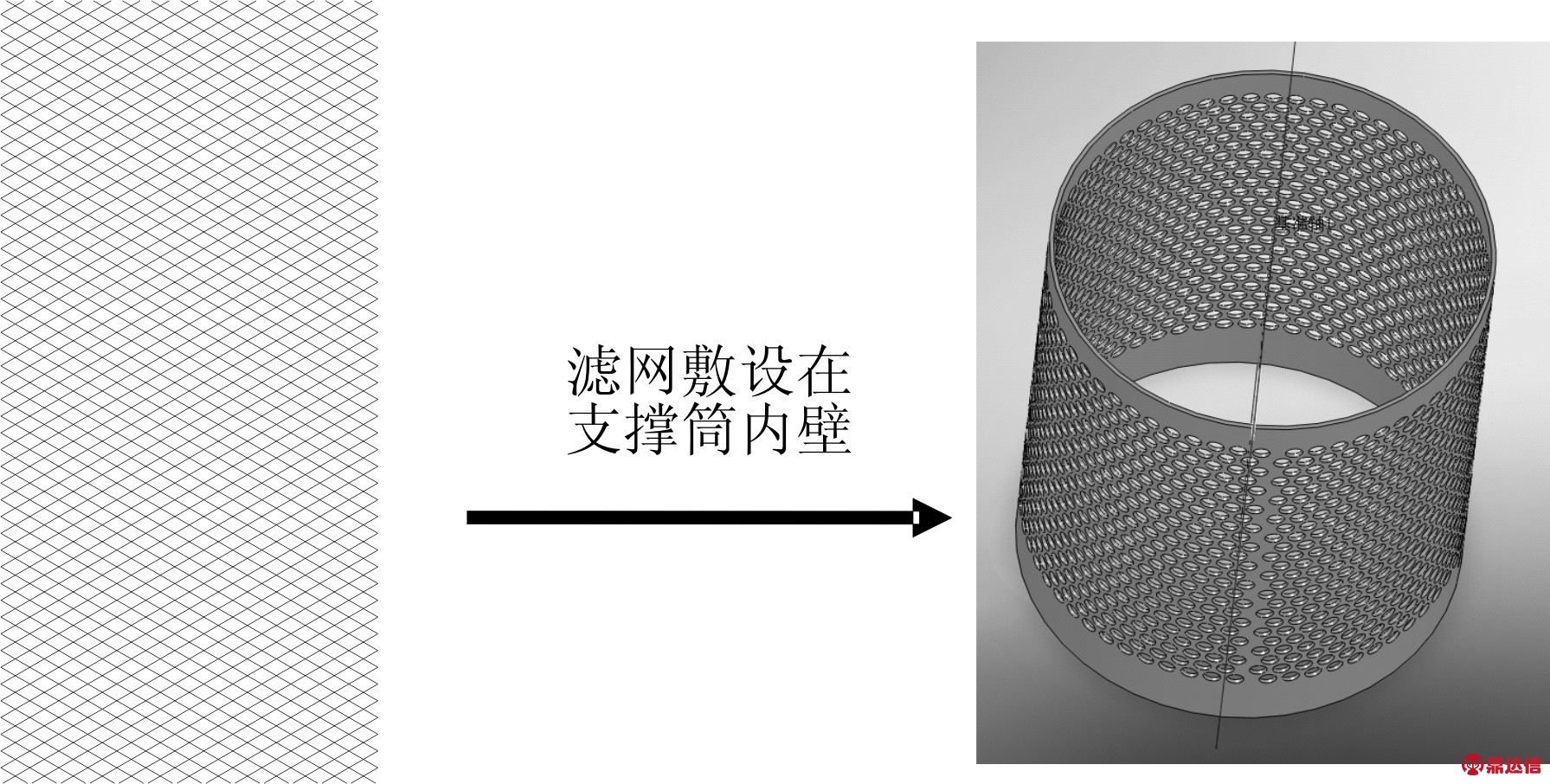
图3 核电汽轮机润滑油回油滤网固定
根据核电润滑油滤网设计规范,为减少通流阻力及避免产生过多油泡,润滑油通流速度不能超过0.2m/s。核电汽轮机所用润滑油流量的大小直接决定润滑油滤网及其支撑筒的选型设计,计算公式如下:
V=n×Sp×Vo
式中:V为润滑油流量;n为滤网数量;Sp为考虑金属丝网通流及支撑筒通流能力的综合通流面积;Vo为润滑油通流速度,不大于0.2 m/s。
在已知润滑油流量、流速要求等情况下,可合理选取润滑油滤网及其数量,并设计支撑筒直径及其通流孔数。
1.3 主油箱回油滤网的安装特性
回油滤网的设计安装需考虑多方面的要求,主要包括拆卸方便、固定容易、避免振动偏移。分别设计了压紧螺母和锁紧卡片,在竖直和旋转方向上都对滤网进行了固定。
回油滤网安装结构简图如图4所示,在安装回油滤网时,先将外滤网对应的扶手外缘对准支撑板上卡片固定处的空隙,放入支撑平台,然后再将内滤网放入并和外滤网一起整体旋转90°,让内滤网的锁紧卡片(L型)和滤网平台的卡片固定孔配合卡住,保证滤网在旋转方向上的固定[3]。竖直方向上顶部压紧螺母和滤网上方的盖板压杆接触,保证整个运行过程中滤网在竖直方向的固定。
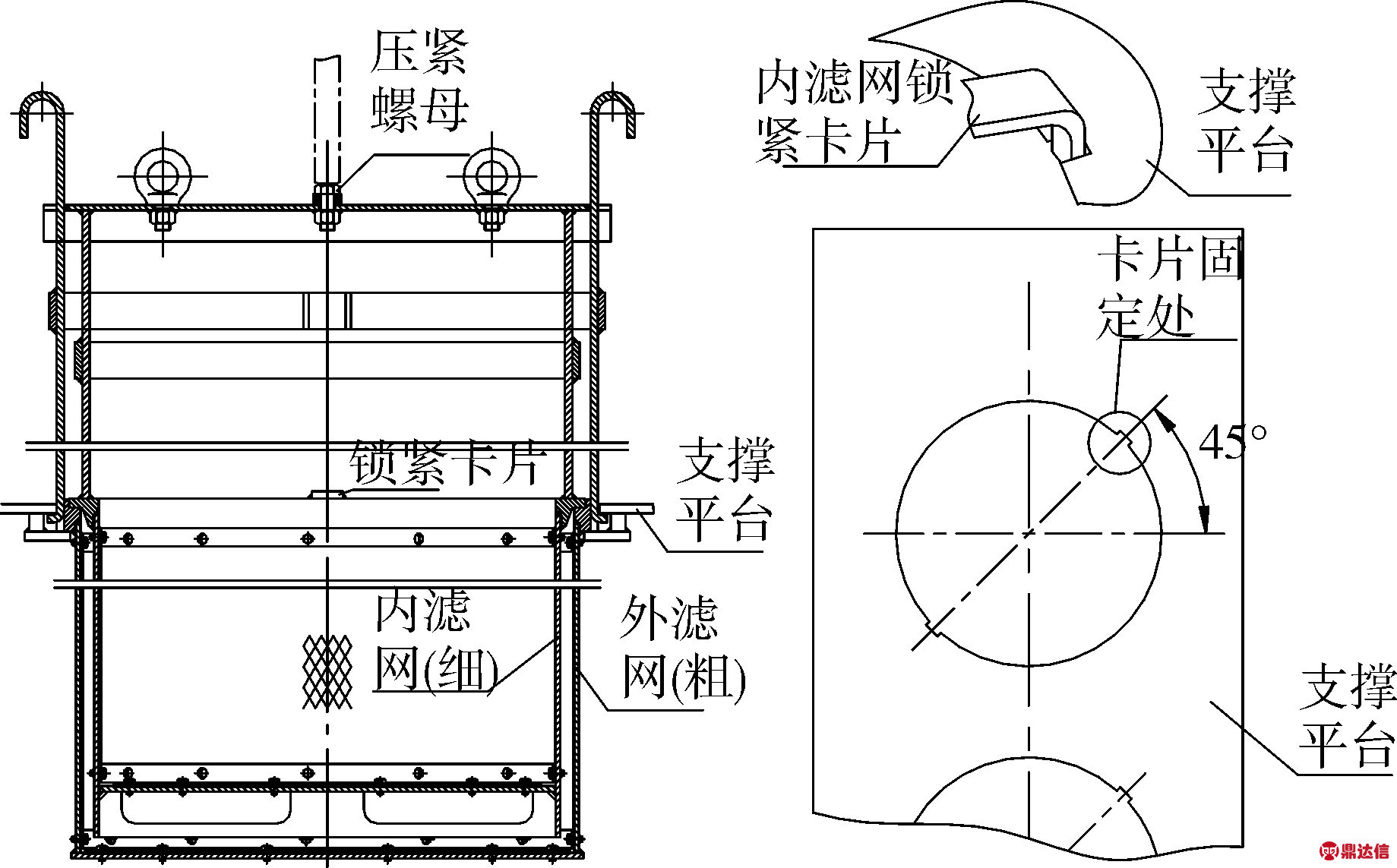
图4 回油滤网安装结构简图
2 核电站现场回油滤网运行情况
现场润滑油实际运行包括注油工作、润滑油管道大量冲洗、正常运行等,回油滤网需要经历回油冲击和油循环过程中产生固体颗粒及油泡冲击等不同条件的运行环境。
在初期设计的滤网产品中,现场润滑油冲洗及运行时主要出现的状况是:
1)滤网受冲击后,滤网端部结合处易出现金属丝断裂,在连续冲击下整个金属丝布撕开;
2)滤网拆卸更换不方便,由于设计时滤网和支撑筒之间设计了焊接连接,每当滤网损坏时拆卸不方便。
3 滤网结构优化设计
3.1 优化内容
根据现场运行情况,对润滑油回油滤网的设计优化主要从两个方面考虑:一是增加滤网刚度,防止冲刷破裂;二是设计为可拆卸结构,便于拆装清洗。
滤网网孔尺寸及丝径的选择要求在过滤固体颗粒的同时,能具备较好的滤网刚度,于是在后续设计上对滤网进行了增加保护滤网(孔径1 mm,丝径0.5 mm)的设计。为了更好地保护滤网,方便现场清洗、拆卸,后续设计将原有滤网的焊接结构优化为螺栓连接固定。滤网优化设计原理如图5所示。
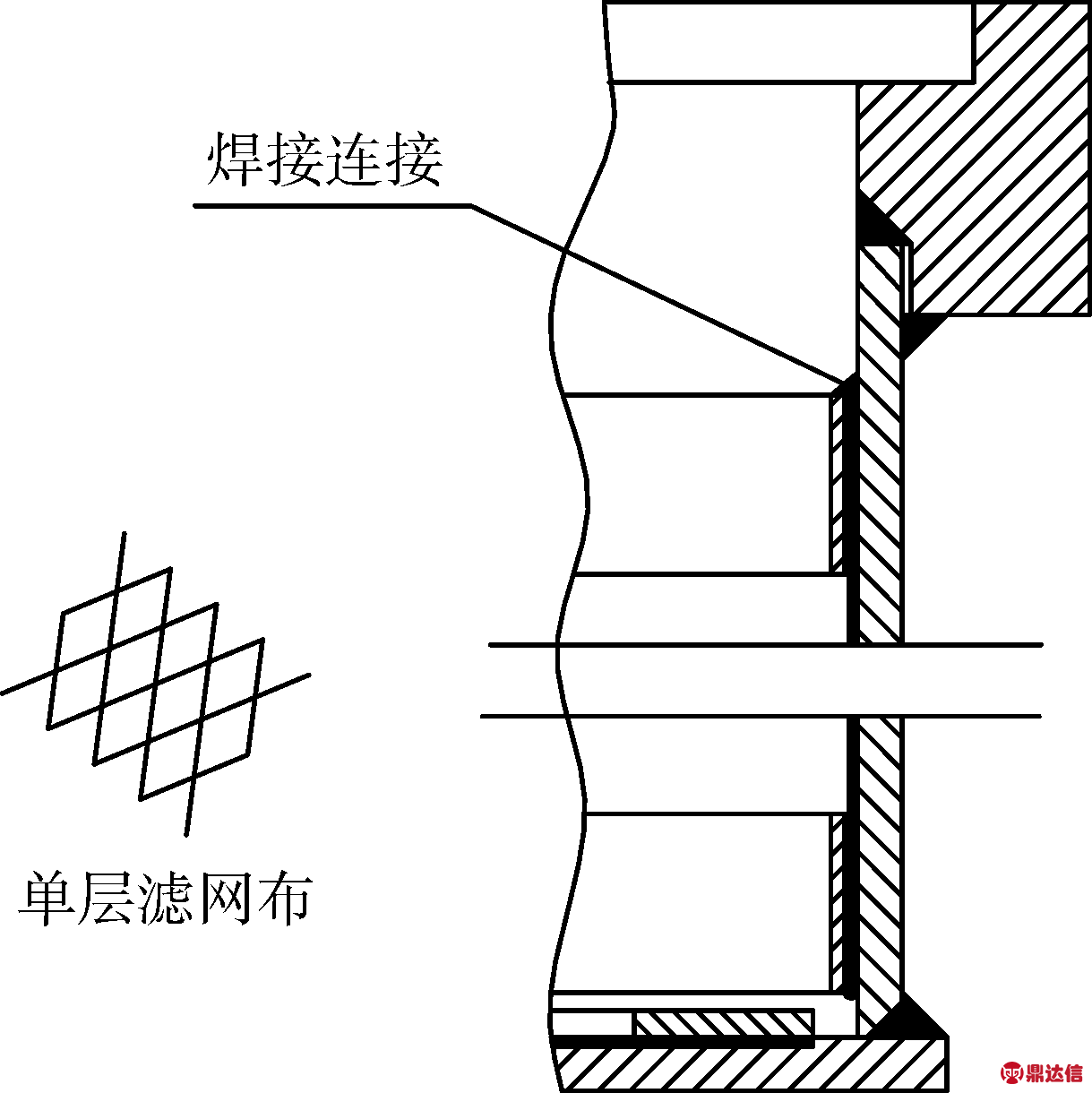
(a) 优化前的滤网结构
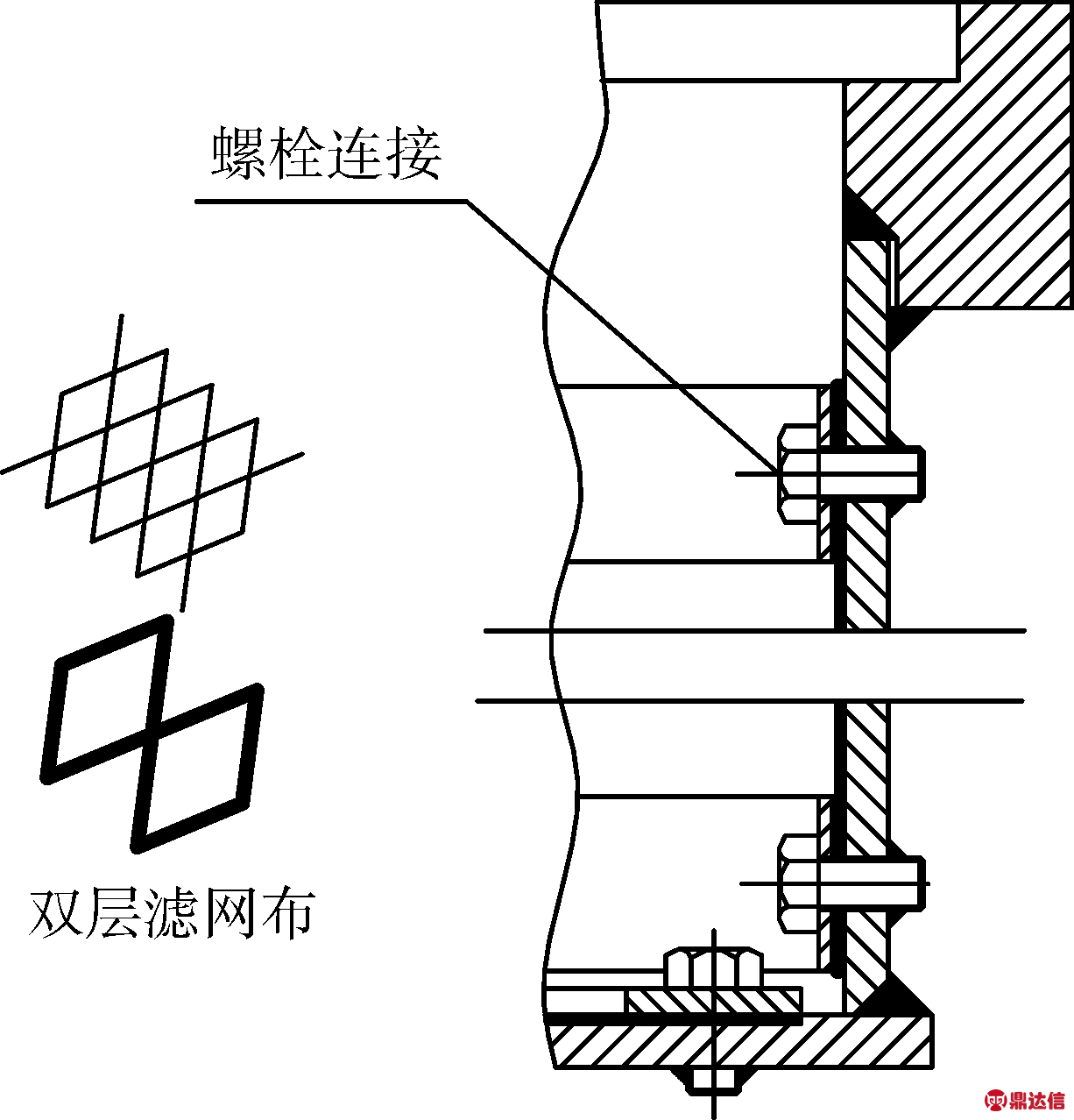
(b) 优化后的滤网结构
图5 回油滤网优化前后对比示意图
3.2 优化后特点
滤网经过上述优化,有如下特点:
1)内外粗细滤网在保护滤网的作用下,整体刚性得到了大幅提升,不易因受冲击而导致金属丝脱丝或破裂;
2)滤网清洗时,现场工具有限,设计成螺栓固定结构,方便滤网损坏后的更换工作。
4 结 论
核电机组润滑油滤网的设计对于整个润滑油品质有至关重要的影响。本文所述的滤网优化方案设计原理清晰,符合核电机组用油高洁净度、低油泡的要求。实际运行结果证明其效果良好,改进后的滤网能完全满足汽轮机长时间、大流量、高清洁度的用油要求,同时更换更为方便。