摘 要:500 kV某变电站35 kV电容器自投运以来,发生了多起因电容器故障造成的电容器组不平衡电流保护动作跳闸事故。通过对历史故障情况及故障现象进行统计分析,从操作过电压、合闸涌流、谐波、电容器产品质量等方面分析电容器故障损坏的可能性,通过对故障电容器进行解体检查,发现电容器生产工艺不满足技术要求,电容器的内部芯子与汇流母线断线是造成电容器故障的根本原因。最后对电容器的产品质量及运维提出了意见和相应的运维控制措施。
关键词:电容器;过电压;合闸涌流;谐波
电容器是电力系统中大量使用的一种设备,它的合理应用关系着整个电网的安全,同时在保证输电质量的情况下,它的无功补偿性质可有效降低能量损耗、改善电能质量、增强输电、配电能力等,其可用率对于电网电压调节和降损节能有着重要作用。除相关国家标准和行业标准外,《预防电容器装置事故的技术措施》《中国南方电网公司反事故措施》中均有防止装置发生事故的措施要求。因此,为了保障电网的安全和稳定运行,有必要采取有效措施来减少电容器的故障问题,从而提高电容器的工作效率和延长使用寿命。
1 概述
某变电站35 kV #1号、#2号电容器于2005年正式投入运行,电容器型号为TBB35-60120/334-BLW;两组电容器为户外三相式,采用双星型接线方式,带不平衡电流保护;每组单台电容器为180台,单台容量为334 kVar,总容量为60 120 kVar,保护配置有电流速断、过电流、不平衡电流、过电压及低电压保护。本文通过对#2号电容器组的多起电容器故障原因进行分析,得出电容器生产制造的工艺质量是引起电容器故障的根本原因,并提出了相应的改进建议和运维措施,从根本上降低了电容器故障的发生率,提高电容器组的可用率。
2 故障经过及故障现象
2.1 故障前设备情况
根据“南方电网公司反事故措施”的要求,35 kV #2号并联电容器组于2010年取消外熔丝结构。电容器的投切由区域控制中心AVC自动投切装置根据总调下发的电压调整曲线进行自动投切。
2.2 故障现象
取消外熔丝前后,#2号电容器组在投入运行过程中,电容器组不平衡电流保护动作跳开S312开关,现场检查电容器组外熔丝熔断;取消外熔丝后,在#2号电容器组投入过程中,电容器组不平衡电流保护动作,跳开S312开关,现场检查电容器外观正常,进一步检查发现其中一桥臂上单体电容器电容明显小于铭牌电容值。
故障情况统计如表1所示。
表1 电容器组故障情况统计表

3 故障原因初步分析
3.1 操作过电压
现场检查电容器组避雷器的计数器显示次数,A相12次、B相13次、C相13次,与以往记录相同。
避雷器放电计数器无动作,表明每一次操作过电压没超过施加到避雷器端子间的最大允许工频电压有效值,不存在操作过电压的可能。
3.2 合闸涌流
并联电容器装置的合闸涌流限值,宜取电容器组额定电流的20倍;当超过时,应采用装设串联电抗器予以限制。
单组电容器投入,通常合闸涌流不大。实际上,只要装设有抑制谐波的串联电抗器,合闸涌流均不会超过电容器组额定电流的20倍。S312电容器组安装有12%电抗率的串联电抗器,可不考虑合闸涌流影响。
3.3 电网谐波
大量的研究表明,谐波电流通过并联电容器时会使其过负荷,甚至烧毁并联电容器,为了防止谐波对电容器影响,目前最有效的方式是在并联电容器支路中串联电抗器[4],其简化电路如图1所示。
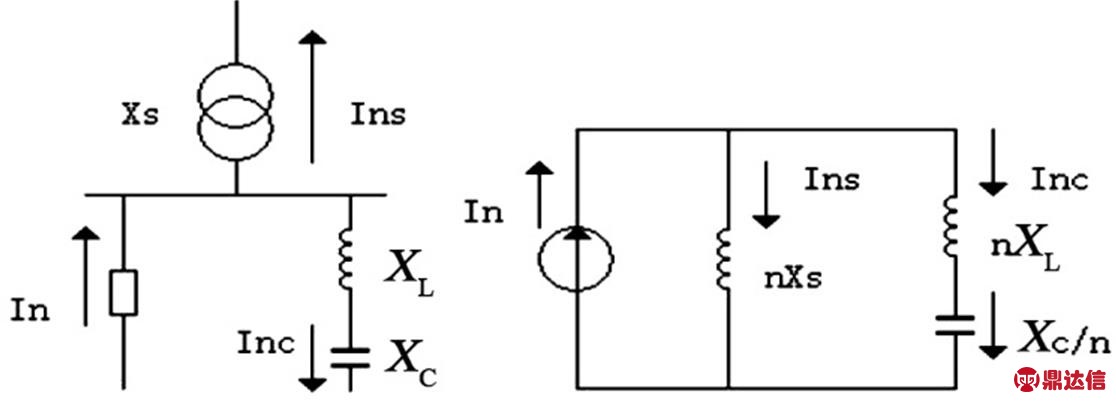
(a)串联电抗器 (b)串联电抗器n次系统图
图1 谐波电流等效电路
为了使抑制3次谐波串联电抗率为12%,Xc的电抗为3XL-(Xc/3)=3×0.12Xc-(Xc/3)=0.02,Xc>0。
这就说明在并联电容器支路中串联电抗率为12%的电抗器时,对3次谐波和3次以上的各次谐波,该支路均呈现感抗,因而有效地抑制了谐波对并联电容器的影响(在《并联电容器装置设计规范》GB 50227—95中推荐:抑制3次谐波的串联电抗器的电抗率为0.12Xc)。
4 故障电容器解体检查情况
4.1 解体检查情况
对故障电容器解体检查,取出电容器芯子后,除发现第一串段的第二个元件引线片焊接处脱落,其他无异常,如图2所示。同时,测量3个串段的电容值,第二、三串段的电容分别为90.3 μF和91 μF,第一个串段在第二个元件引线片联接和断开时分别测得电容值为84.3 μF和7.5 μF。
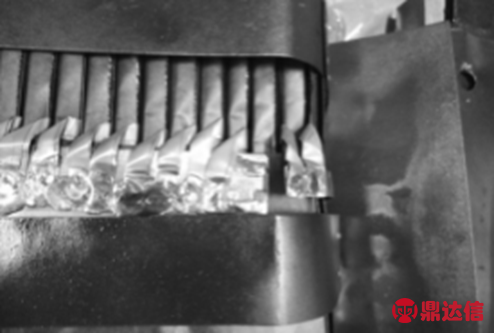
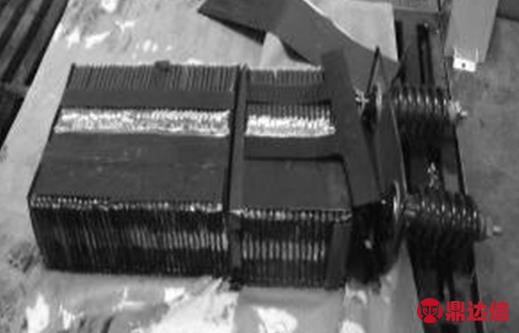
图2 电容器内部芯子及芯子引流排断裂情况
根据测量结果计算故障电容器的电容值:
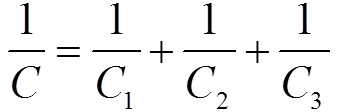
基本与故障情况相符。
据此可判断电容器组在投切过程中,电容器芯子汇流排断裂导致电容器故障,最终导致不平衡保护动作。
4.2 故障原因分析
电容器单元引出线与元件汇流排在焊接时导流接触面之间没放焊锡,未能有效地将单元引出线与汇流排熔焊在一起。同时,电容器单元引出线压接相邻元件引线片上,引出线与汇流排之间存在间隙,导流截面明显变小,如图3所示。在电动力累积作用下,引出线焊接点逐渐受损,最终造成引出线与汇流排断裂。
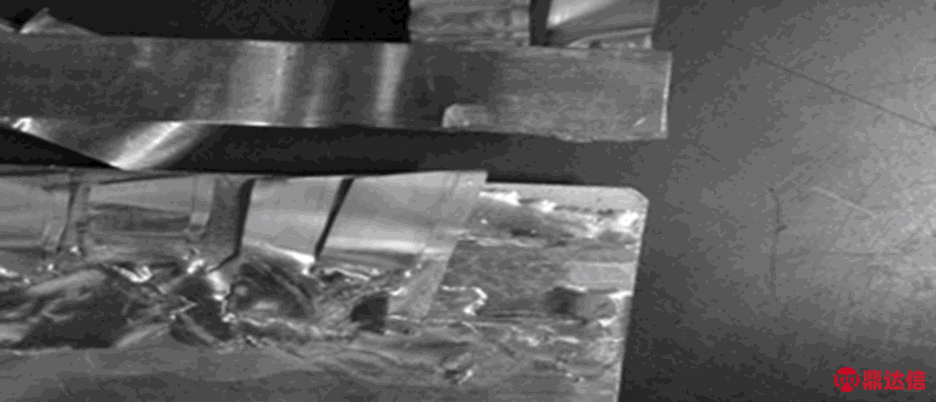
图3 引出线与汇流排连接情况
5 控制措施和建议
5.1 开展技术培训,提高生产人员技能
由于电容器在生产过程中,电容单元的连接需通过一线工人的人工焊接,电烙铁的温度控制、连接汇流接触面的平整度及焊锡在接触面的覆盖面积都是影响焊接质量的因素。电烙铁温度过低,焊锡溶解不完全,造成接触不牢固;接触面不平整,焊接时易存在虚焊和空隙;接触面间未放焊锡进行焊接,连接处面积减小。为此,电容器制造单位因改善生产工艺,对生产人员进行有关焊接工艺要求的培训,保障设备工艺满足要求。
5.2 加强技术监督,做好预试定检的数据分析
针对目前运行中的同批次生产的电容器,可能存在同样的生产缺陷,为减少同类故障的发生,加强对电容器电容量的检测工作,并做好试验数据结果的分析和对比。如果发现电容器电容量与铭牌及历史数据偏差较大时,应及时更换电容器。
6 结论
通过对故障电容器故障原因分析及故障电容器解体检查可以发现,电容器生产工艺不满足技术要求,内部电容芯子与汇流板间焊接不良而脱落,造成单体电容器故障,流过不平衡CT的电流增大造成保护动作是此类电容器故障发生的主要原因。
为此,做好产品生产工艺质量控制、现场运维及产品技术监督工作是延长电容器使用寿命的有效措施。