摘 要 针对传统射流式和射吸式液动锤在坚硬岩层中施工近水平孔或仰孔时效率低下的情况,根据普通液动锤的工作原理,设计了一种阀控式双作用液动锤。结合液动锤的结构特点,利用牛顿第二定律,建立了液动锤的活塞的动力学模型,编制了Matlab软件的M文件,对液动锤的活塞在回程和冲程阶段的启动性能进行了仿真分析;研制了1台φ89 mm液动锤样机,进行了试验室和井下工业性试验,验证了液动锤的冲击性能与设计的合理性,为煤矿井下及隧道坚硬岩层的近水平孔或仰孔施工提供了一种可供借鉴的方法。同时,通过试验发现液动锤的配流元件容易出现划伤、变形等快速磨损问题,为液动锤的可靠性研究提出了新的方向。
关键词 液动锤 射流式 射吸式 双作用 阀控式 仿真
早在19世纪末,人们便开始致力于液动冲击回转钻进技术的研究工作,但直到20世纪60年代,美国、日本、德国、苏联等发达国家才成功研制出了适合工程应用的液动锤[1]。中国地质科学院勘探技术研究所与吉林大学(原长春地质学院)是最早从事液动锤研究的单位,分别研制出了射吸式和射流式液动锤,在地质钻探、金矿等行业得到了大量的推广应用[2-3]。随着液动锤钻进工艺技术发展的需要,黄雪琴[4]、张海平[5]、赵建军[6]等分别对双作用液动锤、射流式冲击器和高频液动锤进行了设计与优化研究,并对其性能进行了台架试验验证,取得了一定的研究成果;曹学斌[7]、赵铁峰[8]、卢予北[9]等将液动锤与绳索取心钻进工艺相结合,应用于金矿复杂地层、坚硬致密“打滑”地层的钻进工作,取得了较好效果。液动锤在施工垂直下行孔时取得了较好效果,但在煤矿井下硬岩钻进施工上行孔或近水平孔(岩石坚固性系数f=8~12,施工角度为+5°),却表现出冲击功小、钻进速度慢等缺点。为解决煤矿井下硬岩钻进的施工难题,本文研制了一种新型双作用阀控式液动锤,以达到井下或隧道快速施工上行或近水平硬岩孔的目的。
1 双作用阀控式液动锤的工作原理
由于气动冲击钻进在施工过程中存在较大的粉尘与噪音污染,且针对射流式和射吸式液动锤在施工近水平孔或上行孔时效率低、冲击功小等不足,本文结合液压凿岩冲击器的结构特点,在对无簧阀式双作用液动锤结构分析的基础上,结合水力凿岩冲击器的工作原理[10-11],设计了一种新型双作用阀式液动锤,其结构原理见图1。高压水进入液动锤后,分别进入活阀(类似于先导阀)的环状间隙、活塞的前后腔,同时控制流体由活塞前腔引入到活阀前腔,由于活阀前腔作用面积大于后腔作用面积,促使活阀快速左移回程,当活阀上的泄压口与排液口连通时,活塞后腔压力迅速下降(近似为零),远低于其前腔压力,从而促使活塞快速回程。当活阀回程到上死点时,由于活阀环状间隙中2个台肩面积不等,使活阀换向右移,其泄压口又逐渐被关闭,同时活塞后腔与高压水连通,形成水击现象,活塞回程结束,在水击压力作用下,活塞实现快速冲程,冲击钻头尾部,在旋转的配合下,实现硬岩层的快速钻进。
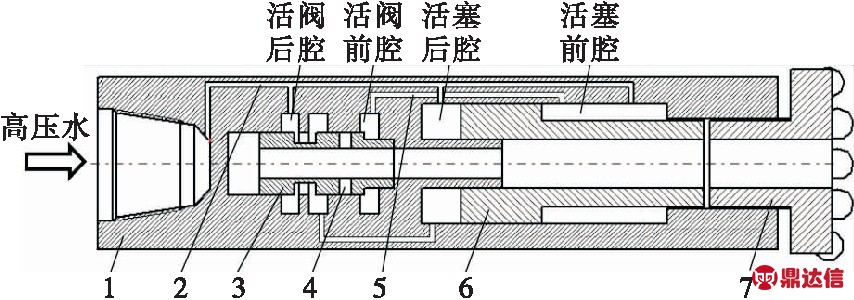
图1 新型双作用阀式液动锤结构原理
1—后接头;2—高压水通道;3—活阀;4—泄压口;
5—控制流体;6—活塞;7—钻头
2 液动锤活塞动力学模型的建立
液动锤工作时,由于活阀的泄漏油口是逐渐打开和关闭的,故活塞受力情况是相当复杂的,属于非线性动力学系统,为准确求解,需列出一系列非线性微分方程组。但这种方法求解难度较大,没有任何实际意义。为解决非线性系统动力学问题,可近似地把活塞受到的力看作是线性变化的,于是可建立活塞的动力学模型。
2.1 活塞回程时的动力学方程
活塞回程阶段示意见图2,以活塞为研究对象,根据牛顿第二定律,可建立活塞回程阶段的动力学方程:

(1)
式中,m为活塞质量,为活塞回程时的加速度,m/s2;F1为活塞回程时后腔所受到的液压力,回程时,后腔与出液口导通,水压近似为零,故F1=0 N;F2为活塞右侧受到的液体压力,N;Fs为活塞回程阶段受到的水力阻力作用,
为活塞与密封圈、活塞与滑阀套相对滑动时所受到的摩擦力,N,Ff=μπdhps[12],其中,μ为密封圈与配合面的摩擦系数,d为密封相对运动处的直径,m,h为密封圈的有效宽度,m,ps为密封圈处的工作压力,Pa。
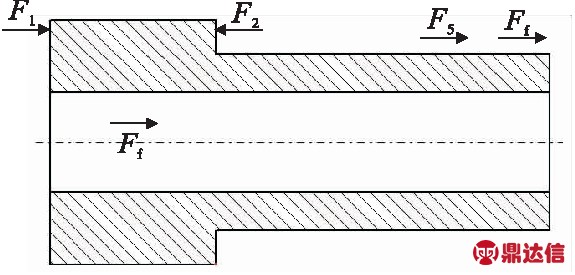
图2 活塞回程阶段的受力分析示意
2.2 活塞冲程时的动力学方程
活塞冲程阶段示意见图3,其后腔受到水击压力作用,且后腔作用面积远大于前腔作用面积,活塞快速冲程,可建立活塞回程阶段的动力学方程:

(2)
式中,m为活塞质量,为活塞冲程时的加速度,m/s2;F1为活塞冲程时后腔所受到的液压力,为泵压与活塞环状面积乘积,N;Fd为水击压力,即活阀将活塞后腔与出液口阻断,同时导通高压与前腔瞬间所产生的压力,
其中,C为水击波速,
为与管道材料相关的参数,D为通水孔内径,m,i为通水孔壁厚,m; F2为活塞冲程阶段受到的液体压力,N;Fs为活塞冲程阶段受到的水力阻力,N;Ff为活塞与密封圈、活塞与滑阀套相对滑动时所受到的摩擦力,N。
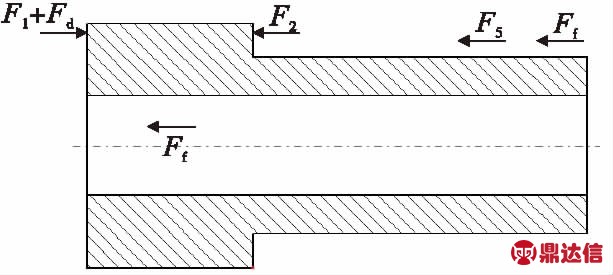
图3 活塞冲程阶段的受力分析示意
3 活塞冲击性能分析
根据双作用阀式液动锤的动力学模型, 利用Matlab软件编制了仿真程序,对其微分方程进行求解,可得到活塞回程和冲程阶段行程与时间的特性曲线,见图4、图5。可知,活塞回程时,活阀上的泄压口与活塞后腔迅速连通,使活塞后腔压力迅速下降为零,在压差作用下,快速启动回程;冲程阶段,当活阀泄压口与活塞后腔关闭且连通高压腔与后腔时,由于惯性作用,活塞还将往左运动微段距离,并迅速启动并完成冲程。
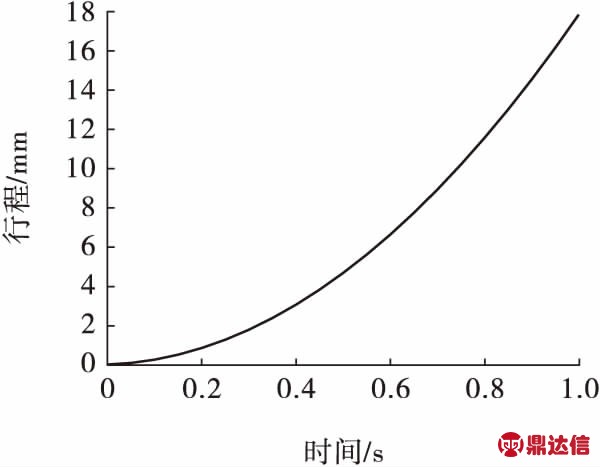
图4 回程阶段活塞行程与时间的关系
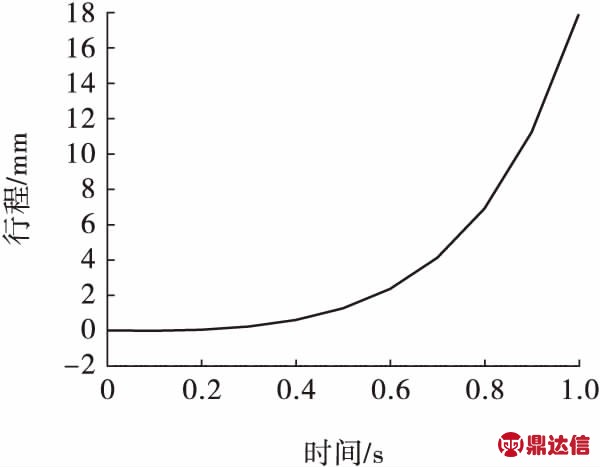
图5 冲程阶段活塞行程与时间的关系
4 液动锤样机主要技术参数
根据动力学模型,结合钻孔需要,设计并试制了1台φ89 mm双作用液动锤样机,其结构参数见表1。样机及试验室试验见图6。当泵量为200 L/min,泵压为6 MPa时,其冲击功为48.6 J,与理论计算值44.5 J基本相符。
表1 YCJQ89型新型液动冲击器的主要技术参数


图6 液动锤的试验室试验
5 现场试验
2018年12月将样机送至松藻煤矿矛口巷道的灰岩层中进行试验,岩石坚固性系数f>10,试验泵流量为200 L/min,泵压为8 MPa。灰岩中施工时,其钻进速度为0.08~0.15 m/min,比φ90 mm低风压气动冲击器略低,比普通回转钻机高2倍左右。试验共完成2个孔,孔深分别为44和53.5m。试验完成后,拆开液动锤,发现配流套磨损严重,活塞等其他零件没有发现磨损情况,见图7。
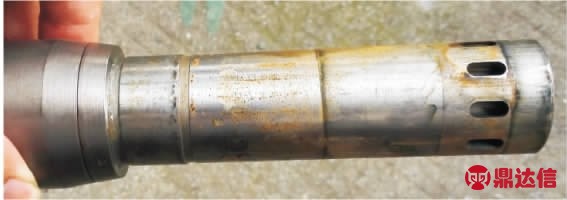
图7 试验后的液动锤配流套
6 结 论
(1)通过分析与研究液动锤工作原理,建立了液动锤的几何模型;同时为研究液动锤的冲击性能,建立了液动锤活塞的动力学模型。
(2)根据活塞的动力学模型,建立了相应动力学方程,利用matlab软件编制了M文件,对活塞的回程和冲程阶段的性能进行了仿真分析,得出了活塞回程和冲程阶段的启动性能曲线,并将其与设计样机进行性能对比,发现其冲击功与冲击性能较为吻合,说明动力学分析模型建立的正确性。
(3)通过井下工业性试验,发现液动锤的配流套磨损严重,使活塞冲击性能下降,严重影响了液动锤的冲击功、冲击频率等性能参数,后期将重点研究液动锤关键零件的可靠性方面,为液动锤的推广应用奠定基础。
(4)设计的阀控式双作用液动锤,通过试验室与井下工业性试验,验证了液动锤的冲击性能,为煤矿井下或隧道近水平或仰孔硬岩层施工提供了高效、清洁的孔底动力钻具,具有较好的推广应用前景。