摘 要:从试验检测角度分析了试验设备、试验方法对轴向橡胶垫产品刚度试验检测结果的影响,分析了不同试验工装板厚对橡胶层应力水平的影响。同时,对既有技术标准的修订工作提出了建议。
关键词:轴向橡胶垫;试验方法;刚度试验
轴向橡胶垫是我国铁路货车交叉支撑式转向架重要的弹性元件,成对安装在交叉支撑装置端部,为转向架提供合理的抗菱刚度,在转K2型、转K6型、DZ1型等多型号转向架中广泛应用。
自1998年引进侧架弹性下交叉技术以来,国内学者对交叉支撑装置进行了大量的研究与改进[1-4]。本文以交叉支撑装置轴向橡胶垫产品为研究对象,从试验角度出发,研究分析不同试验设备、不同试验方法对轴向橡胶垫产品刚度试验检测结果的影响,以及不同试验工装对橡胶层应力水平的影响,并对既有技术标准的修订工作提出建议。
1 试验内容
目前,对轴向橡胶垫的考核主要依据Q/CR 548.1—2017《铁道货车转向架 第1部分:交叉支撑式转向架》和TJ/CL 264—2013《轴向橡胶垫技术条件》进行,型式试验项点包括单件常温刚度试验、-40 ℃低温刚度试验、50 ℃高温刚度试验、组合件常温刚度试验、疲劳试验以及强化疲劳试验。其中,单件常温刚度试验的试验方法是将单件轴向橡胶垫安装在特定的试验工装上,以2~4 mm/min的速度加载至50 kN,加载3次,记录第3次加载过程中的力-位移曲线,分别计算在35 kN时的轴向刚度值。组合件常温刚度试验的试验方法是将一对轴向橡胶垫安装在特定的试验工装上,施加大小为675 N·m的扭矩,以2~4 mm/min的速度加载至40 kN,加载3次,记录第3次加载过程中的力-位移曲线,分别计算在10 kN、20 kN、30 kN时的轴向刚度值。-40 ℃低温刚度试验、50 ℃高温刚度试验在刚度测试方法上与单件常温刚度试验完全相同,在此不再赘述。
2 试验设备对检测结果的影响
2.1 试验准备
为了对比不同试验设备对轴向橡胶垫刚度试验检测结果的影响,选取5件轴向橡胶垫产品,分别在3台不同型号的试验设备(表1)上进行单件常温刚度试验。为了避免环境温度、加载工装、加载方法等对试验检测结果产生影响,3组试验环境温度均为(23±2) ℃,不同试验设备测试时间均至少间隔1天。
表1 试验设备信息
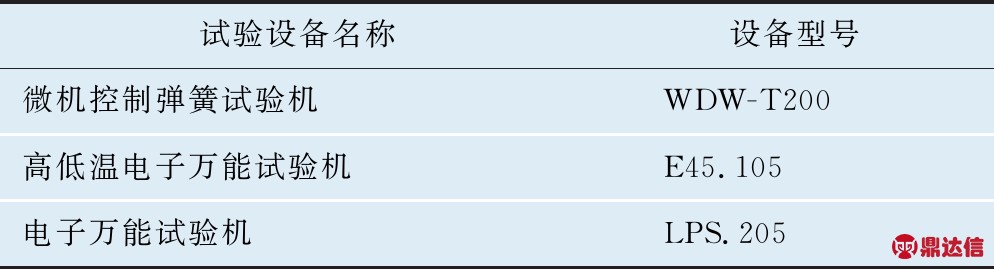
2.2 试验结果分析
5件轴向橡胶垫产品在35 kN载荷下的单件常温刚度试验结果见表2。从表2中可以看出,对于同一轴向橡胶垫产品,不同的试验设备所测得的刚度值存在一定的差异。
表2 单件常温刚度试验结果 kN/mm
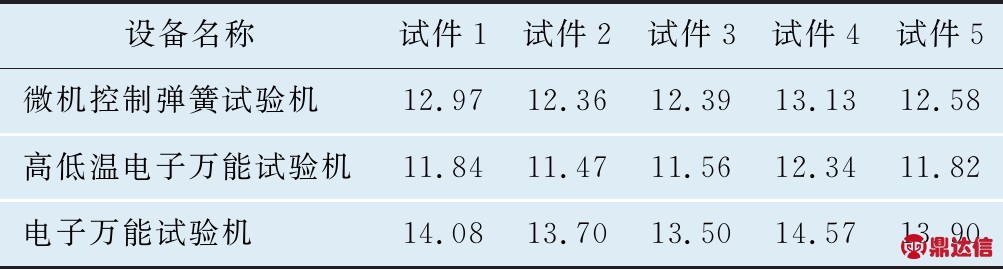
3组试验的环境温度、加载工装、加载方法均相同,数据也均由试验设备自动采集,可以排除上述因素对于试验检测结果的影响。加载工装划对角线,加载中心划中心圆,可以排除加载偏心对试验检测结果的影响。由此可以判断,试验检测结果的差异是由试验设备自身刚度和精度造成的。经分析,试验设备测得的载荷值即为施加在轴向橡胶垫上的载荷值,而试验设备测得的位移量不仅包含轴向橡胶垫的变形量,还包含加载横梁变形量、加载工装变形量、作动器连接间隙、横梁提升螺杆间隙等。试验设备所测得的位移量往往大于轴向橡胶垫的实际变形量。
分别以空白试验和引伸计测量2种方式来分析试验设备自身刚度和精度对轴向橡胶垫单件常温刚度试验检测结果的影响。
(1) 分别在3个试验设备上进行空白试验,通过计算得到试验过程中轴向橡胶垫的实际变形量,进而计算轴向橡胶垫单件常温刚度值,结果见表3。
表3 对试验设备进行空白试验后的单件常温刚度试验结果 kN/mm
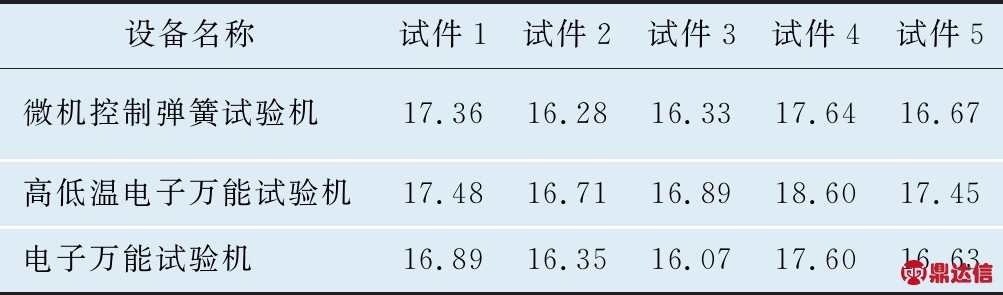
通过空白试验消除了加载横梁变形、加载工装变形、作动器连接间隙、横梁提升螺杆间隙等因素的影响,经过计算得出了轴向橡胶垫的实际变形量。对照表2、表3数据可知,消除上述因素影响后,轴向橡胶垫的刚度普遍变大。同时,不同试验设备测得的同一轴向橡胶垫的刚度结果离散度变小。
(2) 利用电子万能试验机自带的引伸计直接测量轴向橡胶垫产品的实际变形量(工装变形量忽略不计),消除加载横梁变形、横梁提升螺杆间隙等因素的影响。引伸计测得的位移数据为设备自动读取,避免了人工读数所造成的误差。
表4为不同测试方法测得的单件常温刚度试验结果对比。如表4所示,增加引伸计测量后所测得的刚度试验结果比原始试验所测得的试验结果大12.7%~15.5%。同时,增加引伸计测量后所测得的刚度试验结果与增加空白试验测量后所测得的试验结果差别不大(图1),最大相差2.1%。
表4 不同测试方法测得的单件常温刚度试验结果对比 kN/mm
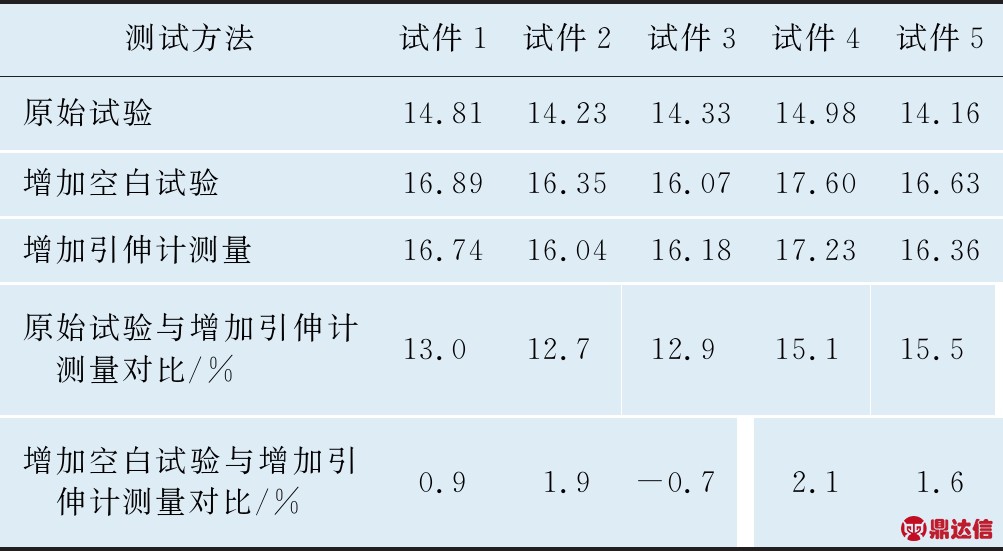
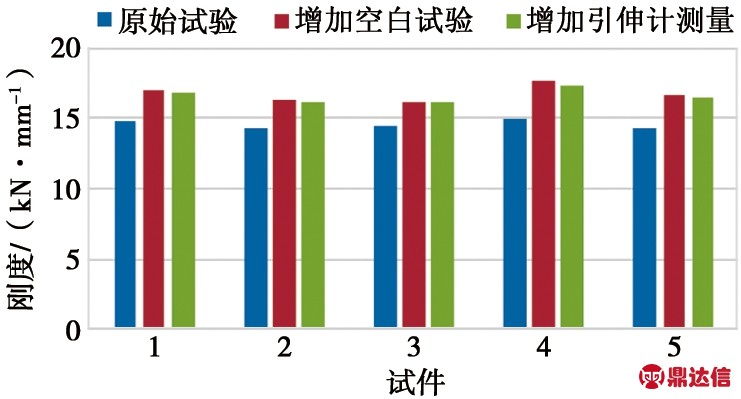
图1 不同测试方法的刚度试验结果对比图
轴向橡胶垫产品在35 kN载荷下,变形量为2.5~3.5 mm,变形量较小。此时,不能忽略试验台加载横梁变形、横梁提升螺杆间隙、作动器连接间隙等因素的影响。采用空白试验或者引伸计测量的方法可以相对精确地计算或者直接测得轴向橡胶垫在试验过程中的变形量,有效避免上述因素对刚度试验结果的影响。因此,对于小位移量的刚度试验,为了保证试验结果的精确性,应采用增加空白试验或者增加引伸计测量的方法。
3 试验工装对橡胶层应力水平的影响
Q/CR 548.1—2017和TJ/CL 264—2013标准要求轴向橡胶垫在疲劳试验前后均需进行组合件常温刚度试验,试验加载示意图见图2,要求刚度变化率不得大于10%。
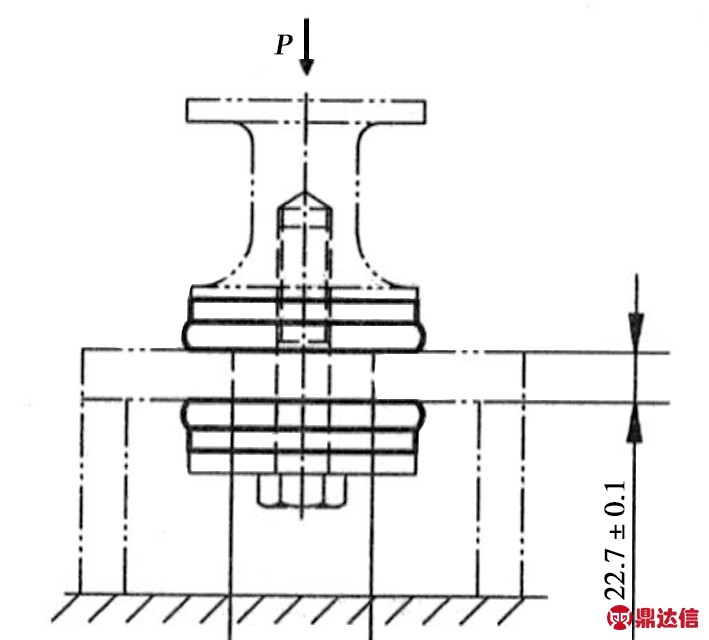
图2 组合件常温刚度试验加载示意图
显然,在轴向橡胶垫组装示意图(图3)中,高度H(由总高度(35.6±1.0) mm减去有效高度(24.6±0.8) mm)在9.2~12.8 mm区间均合格。同时,Q/CR 548.1—2017和TJ/CL 264—2013标准建议加载工装板厚为(22.7±0.1) mm。当2件符合技术图纸尺寸要求的轴向橡胶垫产品按照图3进行组装时,在未施加扭矩情况下,2件产品的A面会存在贴合或未贴合2种情况。
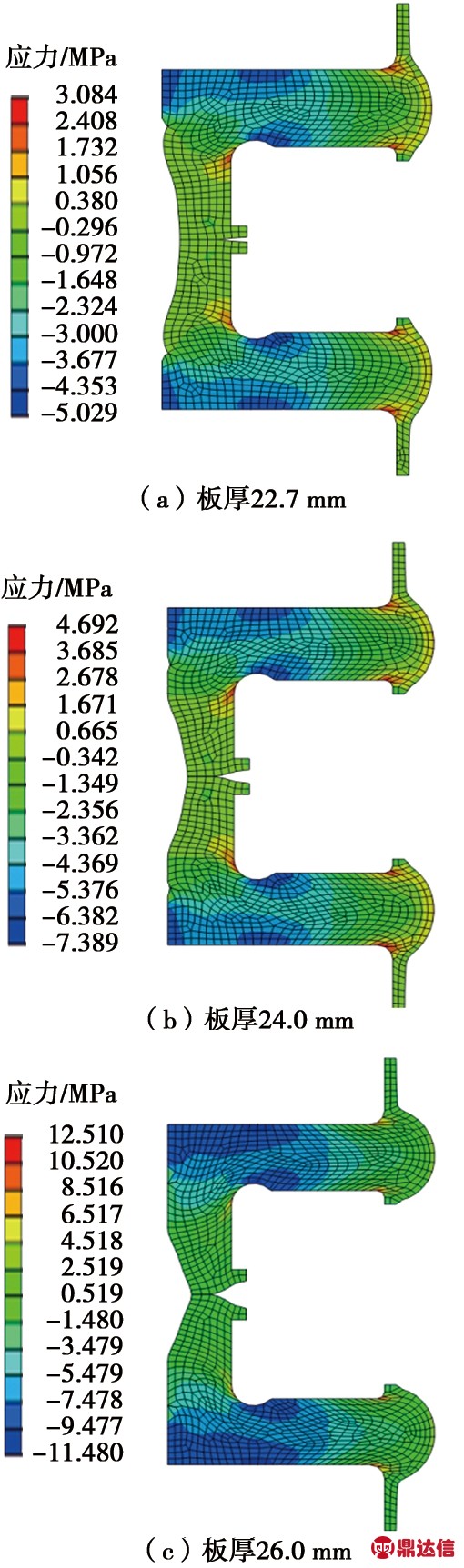
图3 轴向橡胶垫组装示意图
经分析,在施加675 N·m扭矩后,2件符合技术图纸尺寸要求的轴向橡胶垫产品按照图3组装时,2件产品的A面均会贴合,不同高度H的轴向橡胶垫产品的橡胶层压缩量不同,橡胶层的应力水平不同。同理,当产品尺寸H一定时,不同试验工装板厚对轴向橡胶垫橡胶层的应力水平也会有一定影响。由于试验手段很难测得橡胶层的应力,故借助ABAQUS软件进行仿真分析。分别计算了试验工装板厚为22.7 mm、24.0 mm、26.0 mm时,轴向橡胶垫产品(H=11 mm)在施加了675 N·m扭矩下橡胶层的应力水平,如图4所示。
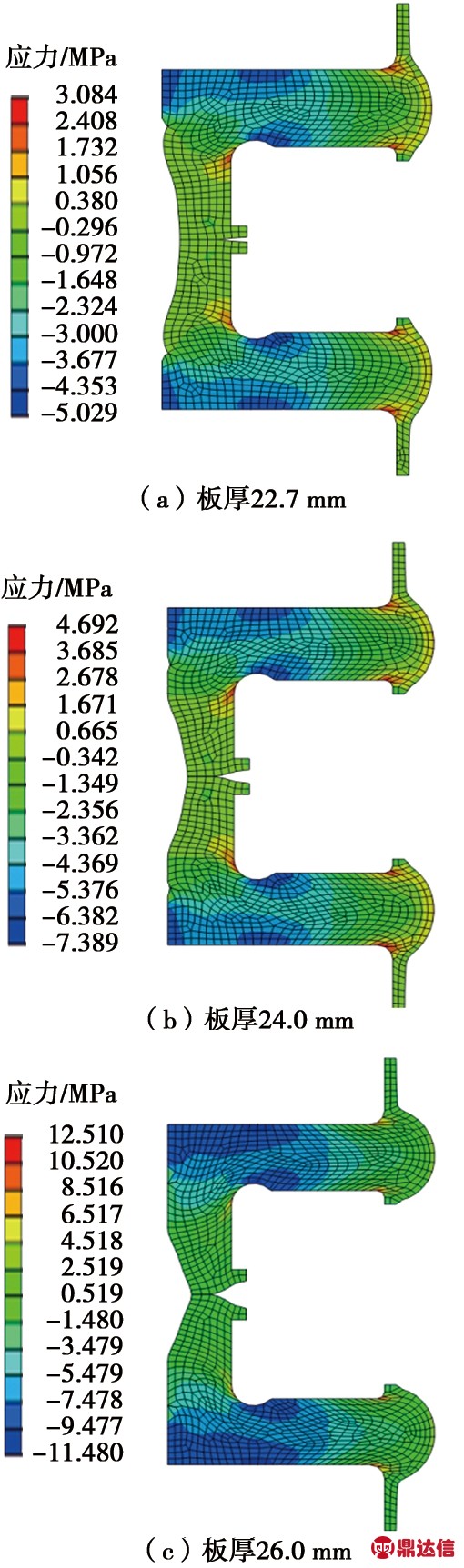
图4 不同试验工装板厚下橡胶层的应力水平
由图4可知,当板厚为22.7 mm时,橡胶层的最大应力为3.084 MPa;当板厚为24.0 mm时,橡胶层的最大应力为4.692 MPa;当板厚为26.0 mm时,橡胶层的最大应力为12.510 MPa。显然,试验工装板厚不同时,轴向橡胶垫橡胶层的应力有较大差异。同理,在实际运用中,当侧架上轴向橡胶垫工装板厚一定时,由于轴向橡胶垫尺寸(H值)不同,橡胶层的应力水平也会存在较大差异。橡胶层长期处于高应力水平,会影响轴向橡胶垫产品的整体运用性能。因此,在制造加工允许的情况下,应减小轴向橡胶垫产品技术图纸中的相应尺寸公差。
另外,目前很多客车用橡胶产品疲劳试验前后刚度变化率要求不大于15%,而现行轴向橡胶垫的技术文件要求在疲劳试验前后轴向橡胶垫的组合件常温刚度变化率不得大于10%,指标定得明显偏严。建议在后期标准修订时,在不影响转向架整体抗菱刚度的前提下,该指标应适当放宽。
4 数据处理方法对检测结果的影响
4.1 刚度计算方法
单件常温刚度和组合件常温刚度中所提到的刚度均是指割线刚度,计算方法可参照TB/T 2843—2015《机车车辆用橡胶弹性元件通用技术条件》中第6.3.3条款,橡胶弹性元件刚度计算示例见图5。
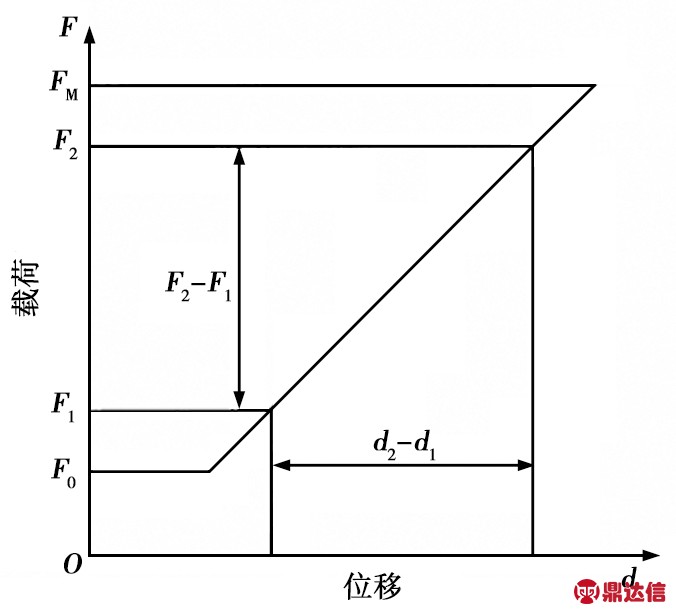
F0.试验最小加载载荷;F1.起始点载荷;F2.截止点载荷;FM.试验最大加载载荷;d1.起始点位移;d2.截止点位移。
图5 橡胶弹性元件刚度计算示例
刚度K计算公式为:
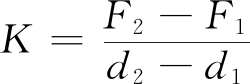
4.2 不同计算方法对刚度结果的影响
以组合件常温刚度试验为例,分析不同计算方法对刚度结果的影响。
组合件常温刚度试验的载荷-位移曲线见图6。按照割线刚度计算方法,在计算10 kN、20 kN、30 kN载荷下的组合刚度时,起始点载荷F1取值为0。由于A-B段较为平缓,F1对应的位移S1的选取易产生偏差,而当载荷值为35 kN时,位移量也不到1.2 mm,故微小的偏差会对最终结果产生较大影响。同时,对比其他铁路货车弹性元件产品的刚度计算方法,如承载鞍橡胶垫产品在计算刚度时,F1取值为5 kN;弹性旁承在计算刚度时,F1取值为0.3 kN。因此,为了降低试验误差,建议将F1取值为5 kN。
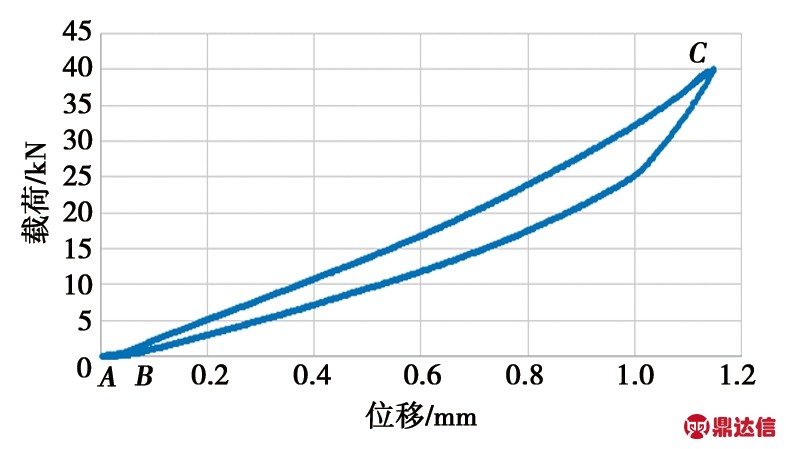
图6 组合件常温刚度试验载荷-位移曲线
5 结论与建议
(1) 同一轴向橡胶垫产品用不同的试验设备测得的刚度差别较大,用空白试验或引伸计测量的方法可消除设备自身所带来的误差。同时,为了降低载荷起始点选取所带来的误差,建议在计算刚度时,起始点载荷取值为5 kN。
(2) 轴向橡胶垫现行标准要求疲劳试验前后组合件常温刚度变化率不得大于10%,指标明显偏严,在不影响转向架整体抗菱刚度的前提下,建议对疲劳前后组合件常温刚度变化率指标适当放宽。
(3) 组合件常温刚度试验中,试验工装板厚对组合件刚度影响不大,但是对橡胶层的应力水平影响较大。在后期产品图纸或者技术标准修订时,应适当减小产品尺寸公差。
此外,《铁路货车段修规程》中规定,轴向橡胶垫产品的使用寿命为6年,满6年后需报废更换新品。而实际运用中装用轴向橡胶垫产品的敞车、棚车等车型的厂修期为9年。这样,在段修中更换的轴向橡胶垫在使用 3 年后又必须报废,不仅增加了段修的工艺难度,也造成了轴向橡胶垫的浪费。因此,建议主机厂和科研院所开展轴向橡胶垫产品延长使用寿命方面的研究。