目前,高速自动化冲压线的应用正处于普及阶段,但受成本影响,很多企业仍在使用较为传统的冲压设备,虽配备了机械手、端拾器等自动化设施,减少了人员投入,但生产效率的提升却不是很显著。本文主要围绕压机、模具、机械手三要素对冲压自动线效率提升的途径进行介绍。
随着市场对汽车需求量的不断增加,对冲压件的需求也在同步增加,但由于生产前准备、模具调试时间长、机械手与压机运行匹配不协调、端拾器结构缺陷等,致使生产效率不能有明显提升。因此,缩短换模时间、优化压机与机械手动作匹配、改善端拾器结构等方法就显得格外重要。下文以采用人工换模的传统机械压力机+六轴机械手所组成的冲压生产线为例进行介绍。
缩短换模时间
该压力机换模过程包括:①工作台开出→②顶杆更换→③模具定位安装→④下模夹紧→⑤工作台开入→⑥滑块下行、微调至下死点→⑦上模夹紧→⑧调整生产参数→⑨试压、复检夹紧→⑩正式生产。
通过以上分析可发现,换模过程中用时较长的工序主要为②、③、⑥、⑧。解决方案如下:
针对工序②的问题,多数冲压厂普遍采购外协模具进行生产,为方便生产使用,顶杆与拉伸垫都是分体结构,哪个位置需要顶杆就在哪个位置上安装,每次更换都需要耗费较多时间;如果车间所使用冲压模具均为自行开发,将顶杆与拉伸垫做成一体结构或工作台上插满顶杆,模具上仅需做避空即可,此举可大大缩短更换顶杆的时间。
针对工序③的问题,可在模具本体同侧增加两个定位结构(V形+平面定位或2个V形定位),方便模具安装时仅用力一推便可完成定位工作,类似结构如图1所示。此结构在使用时需确保设备工作台面上有定位销插入的销孔,如台面无销孔,可对台面进行改造。
针对工序⑥、⑧问题,可通过编制现场工艺卡对所需参数(如装模高度、闭合高度、平衡器风压、气垫压力等)及操作规范进行详细要求,并对所有生产参数进行监控,观察参数变化并及时做出调整。
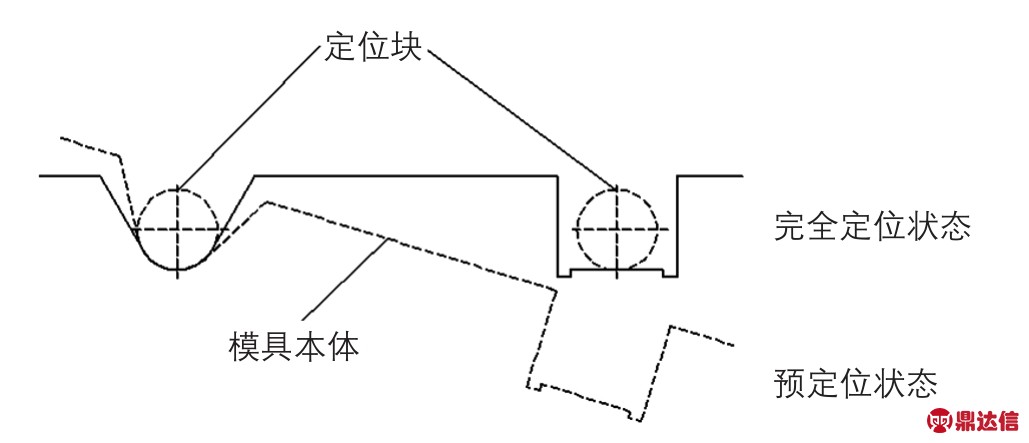
图1 模具定位结构示意图
压机、机械手、端拾器的优化
压机与机械手的运动都是通过模具上安装的接近开关输出的信号来驱动的,但受模具结构、压机结构、PLC程序、端拾器结构、机械手偏转角度及运行轨迹等的综合影响。为提升生产节拍,需从以下几个方面着手。
增大上、下模间的安全距离
上、下模间的安全距离即将工序件从模具型面提升至可平移出下模的位置与上模最低点位置间的距离,如图2所示。增大安全距离有利于机械手提前进入模具抓取制件。
通常情况下,由于滑块行程受设备结构所限,仅能通过优化模具结构的方法来实现。以图2翻整模为例,上模F面有一把插刀用于驱动下模滑车机构运动,为增大安全距离,可考虑将插刀位置移动到侧面且避开机械手运动轨迹的位置。
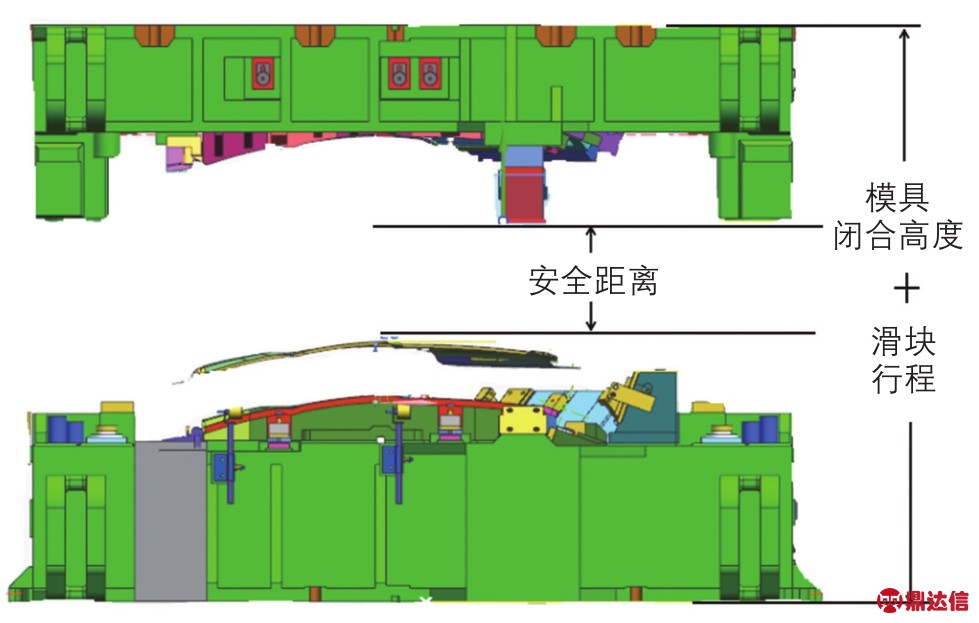
图2 上、下模间安全距离示意图
统一全序下模型面高度
在机械手运动速度最大的情况下,各工序间下模型面高度基本保持一致,可节省相邻工序间的制件搬运时间。通常在模具开发时,可对此处做出要求,且尽量将下模高度做低;如已是量产模具,当工序间下模型面高度差偏大时,可对较低模具增加垫板。
减小各工序间冲压角度的变化
冲压角度的变化直接影响机械手运动轨迹的变化,通常情况下相邻两工序间冲压角度越接近,机械手在取送料过程中,各轴的协同配合动作就越少,运行也越流畅。如制件为左右对称件,各工序间冲压角度变化均较大时,可考虑左右件合模开发。
优化端拾器结构
为方便端拾器在模具间活动,端拾器结构在满足抓取件的条件下,主杆需靠近制件、主杆两侧的辅杆所成的夹角需尽量大;为确保抓取制件可靠,可再适量增加吸盘数量及加强杆。
缩短离合器启动等待时间
为确保滑块下行时与机械手不发生碰撞,在压机的PLC程序内,一般会在模具传输上料信号给压机,促使离合器启动前,增加500~1000ms的延时。通过现场尝试,逐步缩短延时时间。
调整设备安全参数
机械手控制端拾器在模具内“进”和“出”时,与设备参数“下料角度”、“模具保护角度”有联系。当滑块回程至“下料角度”后,压机传输给机械手信号,使其进入模具内进行下料操作;当滑块由上死点运行至“模具保护角度”,但机械手还未移出模具时,迫使压机离合器进行紧急制动。
结合现场观察,可通过逐步减小“下料角度”、增大“模具保护角度”数值,让压机、机械手提前运行,缩短压机和机械手单次运行周期。
机械手自动线为确保运行安全,多个机械手在系统坐标内运行时,会设置防碰撞安全保护程序,通过修改机械手程序,促使机械手提前运行。
自动线生产节拍的估算
当模具设计完成后,为初步评估自动线生产节拍,可通过以下方式进行估算,具体做法如下:
⑴利用模具间安全距离X1、端拾器最高点到制件距离X2、滑块行程X3,计算出端拾器抓取件后不与下模干涉且恰好可从模具内平移出时,滑块的位移量Y=X3-(X1-X2)(以滑块下死点为基准数值0)。
⑵利用计算出来的Y值,分别在每台设备滑块运行曲线图上做一条直线与曲线相交,交点在横轴上取得数值W1和W2(可作为“下料角度”和“模具保护角度”的参考数值)。
⑶通过计算每台设备W2减W1的差值U,取一个相同的倍数V可将U值整除;并利用倍数V值,将每台设备滑块运行曲线图的横轴进行等分,如图3和图4所示。
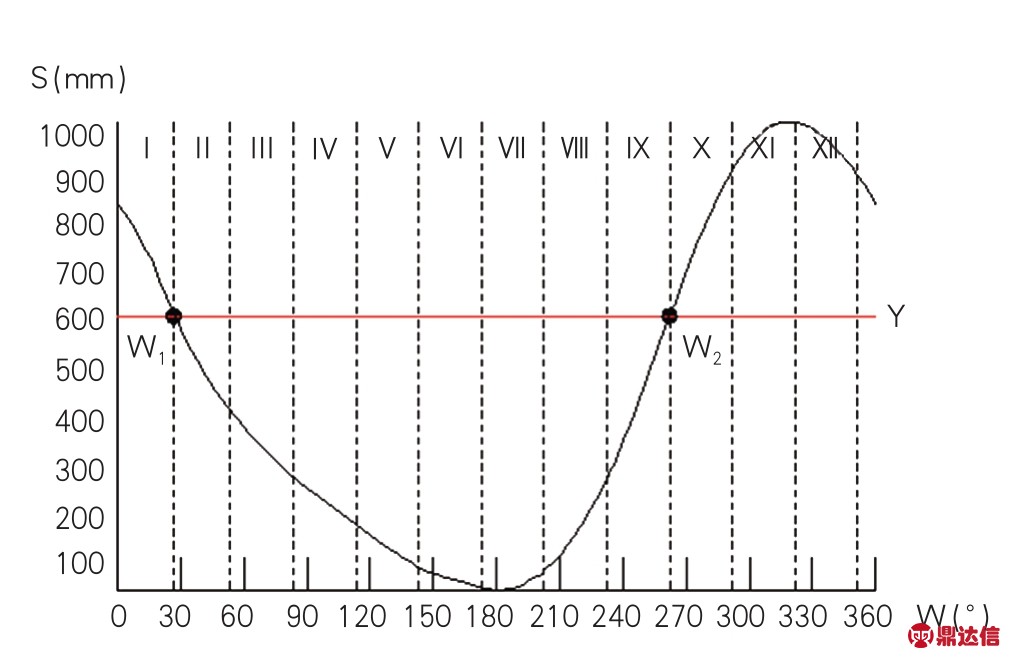
图3 2250t压机滑块行程曲线图
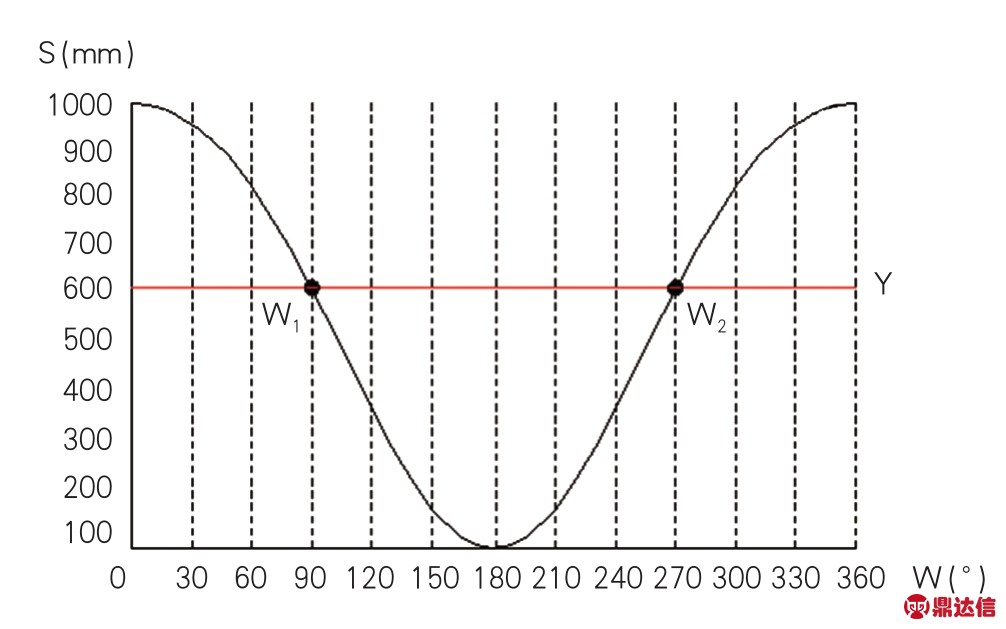
图4 1000t压机滑块行程曲线图
⑷绘制机械手运行示意图,如图5所示。
⑸根据冲压生产线布局及设备参数,对相应数值进行设定,并利用同一时间轴,将压机与机械手的动作进行匹配。
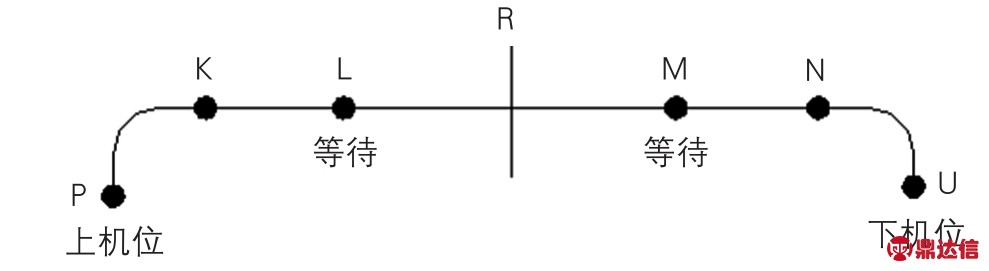
图5 机械手运行示意图
例如,冲压线布局为2250t+1000t+1000t+1000t、六轴机械手联线、压机间距7m、机械手最大运行速度为7m/s、自动线滑块行程次数最大10SPM,即可假设压机与机械手在各等分区间运行时间均约为0.5s(即I~XII每段位移用时为0.5s;KL、MN等每段位移用时为0.5s)。利用图3、图4、图5状态进行分析,则,
单件工时=压机一个冲程用时+压机在上死点等待时间=12×0.5+(6-2)×0.5=8秒/件
生产节拍=60÷8=7.5件/分钟
注:①首台设备通常为多连杆压力机,成形时运行速度较慢,且冲压生产线为联动状态,故首台设备实际生产运行一个周期所用时间即为单件生产工时;
②压机在上死点等待时间为,压机在上死点停止,至上料机器人将物料放入模具内压机开始运动时所用时间。
改善后效果
通过改善顶杆结构、定位方式及过程标准化,模具安装调试效率提升至少35%;通过优化端拾器结构、缩短离合器启动等待时间、调整设备安全参数,可实现产能提升5%左右;在模具开发阶段,通过增大模间的安全距离、统一下模型面高度、减小各工序间冲压角度的变化,可实现产能提升15%左右。
结束语
为追求更高的生产效率,行业内对模具和设备等也提出了更高的要求,比如选用高端压力机、增大压机的滑块行程和冲次、缩短压机间的布局、增加快速换模系统、将传统4工位布局调整为5工位布局、使用7轴机械手并配备更先进的端拾器等方式。伴随经济的快速发展,更多先进技术会被应用在实际生产中,共同推动冲压行业的前进。