摘要:以工业机器人自动化生产线为研究对象,针对轨迹规划和生产现场调试难度大的问题,提出采用机器人仿真软件对工业机器人生产线进行三维实体建模。通过设置端拾器、冲床、皮带线Smart组件的属性连接,创建机器人I/O信号及连接方式,并设定机器人、端拾器、机器人、机床、皮带机之间工作站逻辑关系,完成工作站的离线编程和仿真。最后仿真验证自动化生产线验证其合理性。该方法可显著提高自动化生产线的调试效率,缩短调试周期,降低调试过程中的人力成本。
关键词:机器人;自动化生产线;仿真软件
随着工业自动化发展的需求,制造业也向自动化生产转型,采用机器人生产线的用户不断增加。传统生产线产品的搬运采用人工操作,不仅生产效率低下,还有安全风险的存在。因此工业机器人自动化生产线成套设备已成为未来发展主流[1-2]。通过机器人虚拟仿真对生产线中生产过程进行模拟,可有效降低生产成本、规避安全风险。
目前机器人生产线过程仿真软件种类繁多,各有优劣[3]。本文中讨论的冲压自动化生产线采用的是ABB公司的工业机器人作为自动上下料设备,为此,选择三维软件对自动化生产线过程进行仿真,便于在软件模型库中调用与实际一致的工业机器人及外部设备。通过仿真软件的应用,可以实现机器人安装前的离线编程,提高编程效率,改善编程环境,同时可以实现生产布局的方案设计、机器人到达能力检测、碰撞检测、离线编程等功能。
1 自动化生产线三维布局的建立
生产线的三维布局是机器人自动化冲压线的前提与基础,而三维建模的准确性直接关系到仿真结果的可靠性。为加快建模速度,本文利用SolidWorks建立机床、拆垛小车、对中台等生产设备的三维模型,并转换为STEP或者X-T格式进行软件间模型的传输。
在机床布局过程中,为保证冲压机操作台处于机器人工作空间的可达范围内,可将机器人拖拽到压机的磨具上抓取物料,检测是否处在机器人覆盖半径内,是否有干涉,是否能流畅的完成动作,最后确定冲床间距及机器人位置坐标。通过在三维仿真环境中依次载入四台机床、拆垛小车、重力对中台、皮带线的三维模型,并调用IRB6700机器人模型,设计出自动化生产线整体布局,如图1所示。
2 自动化生产线仿真过程的实现
在三维仿真环境中,可以客观的对机器人自动冲压线的完整过程进行实时模拟,以便更加合理的进行生产线的布局与生产资源的配置。同时,在仿真环境中对机器人冲压生产线的设计方案进行验证分析,如机器人的可达性、机器人驱动程序的正确性、碰撞检测、奇异点规避等。
2.1 仿真生产线流程设计
为保证仿真效果,自动化生产线的仿真流程应与实际工作情况一一对应。仿真开始后,拆垛小车进入工作区域,机器人1得到位信号后拾取拆垛,放在重力对中台,机器人2得到放置结束信号后拾取对中台上的板料放入第一压机中,压机冲压,机器人3等待冲压完成信号发出后拾取板料送入第二台压机中,压机冲压,机器人4等待冲压完成信号发出后拾取板料送入第三台压机中,压机冲压,机器人5等待冲压完成信号发出后拾取板料送入第四台压机中,压机冲压,机器人6等待冲压完成信号发出后拾取板料放置于皮带线,皮带线将产品输送至末端,仿真结束。
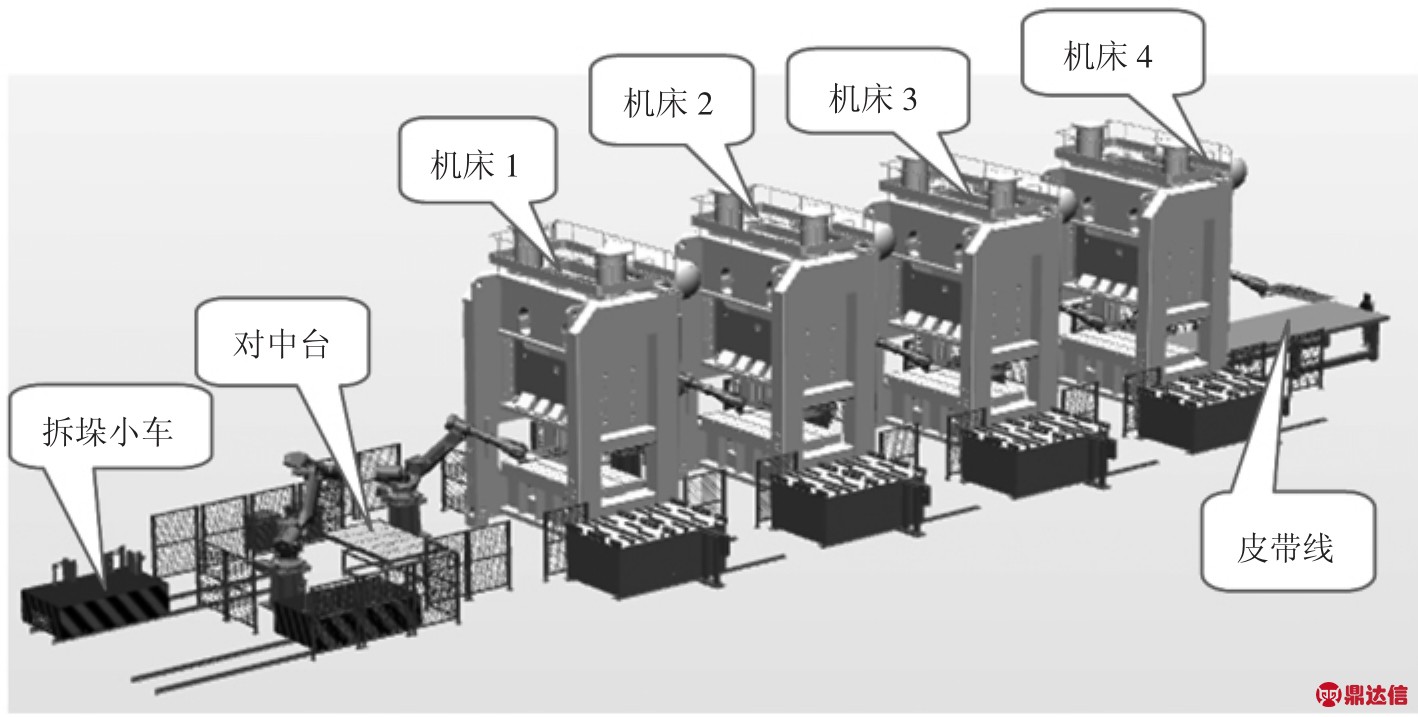
图1 自动化生产线布局
2.2 Smart组件的设计
Smart组件是三维仿真软件的一种受信号与属性控制的动作组件,本文用Smart组件功能依次创建动态机床上下冲压组件,端拾器真空系统吸料和放料组件、皮带线输送链组件,Smart组件具体参数如图2所示。通过以上参数设置,可以实现机床冲压动态效果,包含机床中滑块向下运动的动作,停止动作、滑块向上移动动作、再次向下运动依次顺序循环;端拾器吸料放料动作,包括端拾器上传感器遇到料片产生吸附动作、端拾器到达目的地产生放料动作,端拾器再次移动有料处吸附动作,按照此顺序依次循环;皮带输送链向前移动,到达末端消失依次循环。
2.3 逻辑工作站的连接
三维仿真过程的核心就是建立控制信号间的逻辑关系,该自动化生产线包括4个冲压单元,6个机器人传送单元、1个输送系统单元,根据单元间的控制需求,添加相应的I/O信号,在逻辑工作站中把信号逻辑关系建立起来。
其中机器人I/O信号,将Smart组件的输入输出信号和机器人端的输入输出端信号关联,这是工作站逻辑站的设定,Smart组件的输出信号作为机器人端的输入信号,机器人端的输出信号作为Smart组件的输入信号,机器人的输出信号可以作为下一台机器人的输入信号,这样Smart组件就可以和工业机器人进行I/O通信。本自动化生产线建立的逻辑站参数关系如图3所示。
2.4 冲压机器人轨迹的规划
在自动化生产线控制程序编写前,需要对机器人进行轨迹的规划及目标点的示教。自动化生产线中机器人分为三类:拆垛机器人、传送机器人和下料机器人。拆垛机器人共有3个示教点,分别是机器人拾起板料点、中间过渡点home点、机器人放置点;传送机器人共有5个示教点,分别是机器人拾取点、机器人在机床1等待点,机器人中间过渡点、机器人在机床2等待点、机器人放置点;下料机器人共有4个示教点,分别是机床中拾取板料点、机床外等待点、过渡点、机器人放置点。目标点示教后同步至rapid程序中,进行程序的编程。
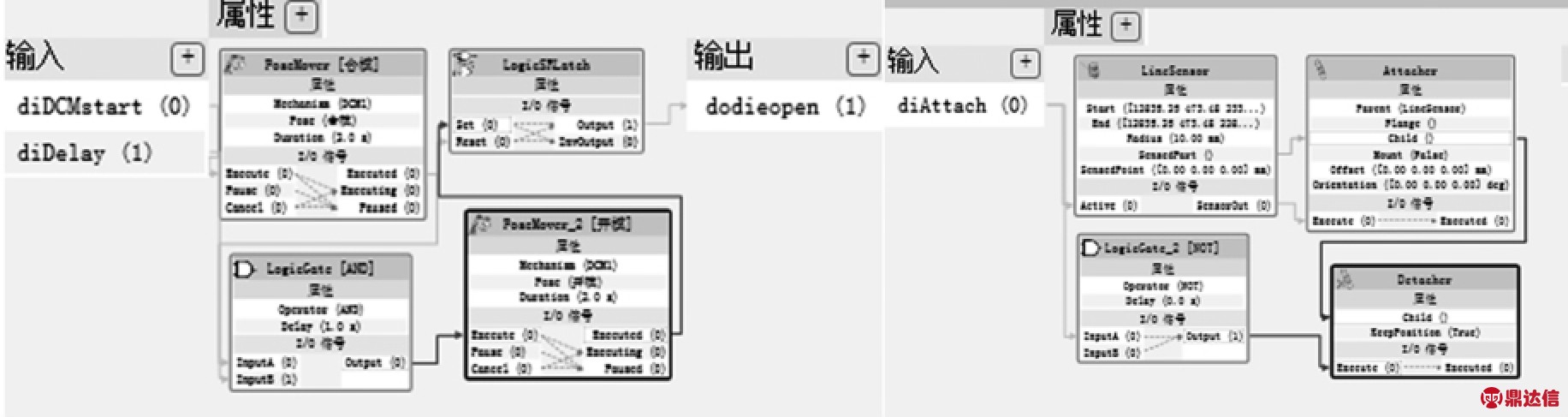
图2 Smart组件的连接
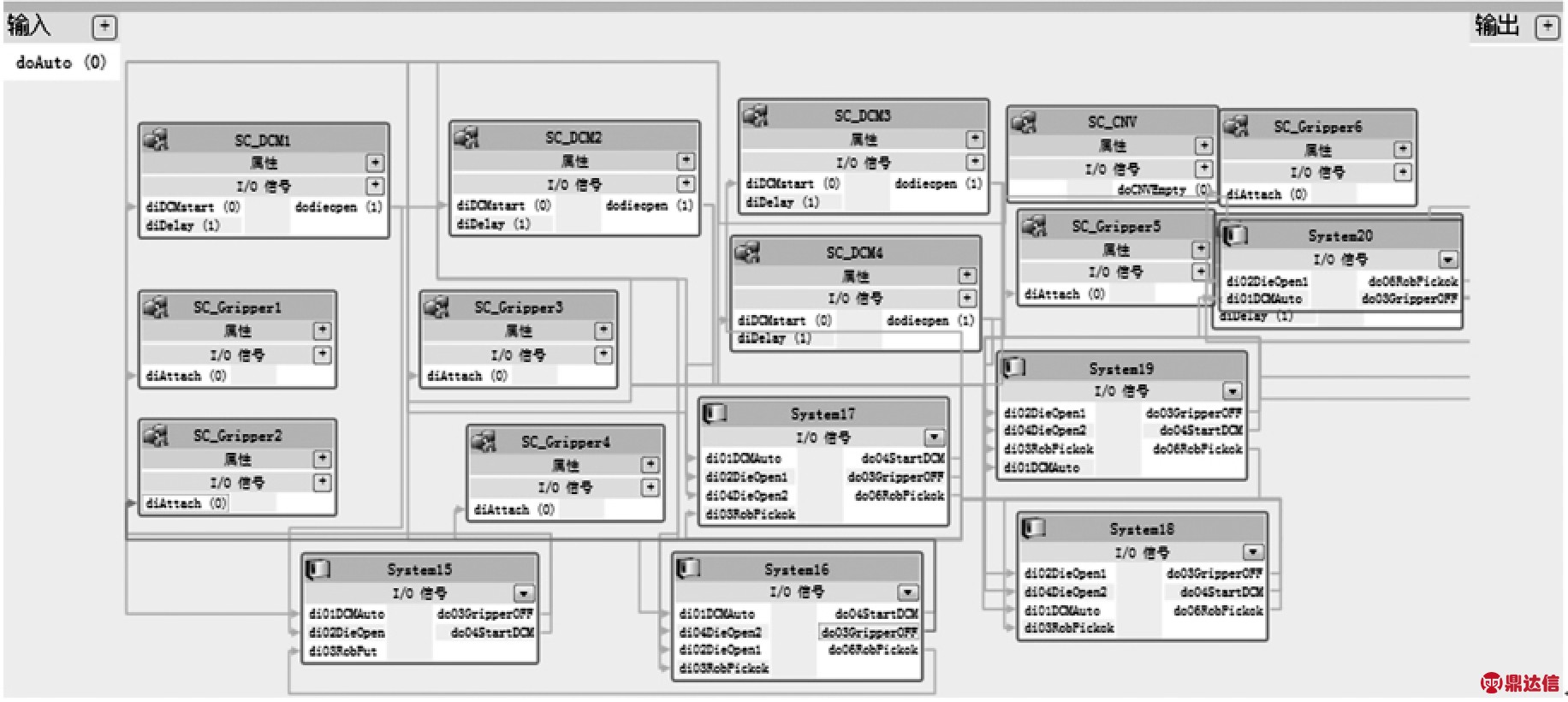
图3 自动化生产线逻辑工作站
3 结语
本文搭建的机器人仿真工作站,在保证Smart组件创建的正确性、逻辑关系连接的正确性、机器人控制程序的正确性的前提下,经调试优化后,该工作站能正常运行,前后动作衔接合理,符合生产实际。模型调试过程发现,建立自动化生产线工作站有两大难点:①Smart组件和逻辑工作站在创建时要注意I/O信号的连接关系,一一对应,逻辑清晰;②在编程时要按照生产实际顺序,层层递进,使程序更易理解[5]。
本文建立的自动化生产线仿真模型,可以实现对整个生产线的直观展示,通过在仿真环境下的试运行,提前解决在生产线布置中产生的问题,对生产的预期效果有个准确定位,有效节省设计到投入生产所需时间。基于该仿真模型设计的门壳自动化生产线,已成功应用于实际并开始生产运行,大大缩短了生产线的设计周期,降低了调试过程中的经济损失,对制造业自动化生产线有重要的参考意义。