摘要:为研究内爆载荷作用下双层复合材料爆炸圆筒的变形与内外层相互作用的规律,将多层缠绕纤维复合材料等效成一层材料,并将内爆载荷通过载荷曲线的形式施加,提出一个简化的数值计算模型。在模型校核的基础上,利用LS-DYNA软件对同一双层圆筒、不同药量下以及不同内外层厚度比例圆筒在内爆载荷下的变形特征进行分析。结果表明:双层爆炸圆筒壳体在小药量炸药爆炸作用下以弹性呼吸振动为主,随药量增加,金属内衬与外层复合材料会发生分离,外层复合材料在振动过程中会强烈压缩金属内衬,内衬会发生不规则变形,在大药量条件下内衬会被压溃而失去承载能力;相同壳体面密度条件下,过薄的金属内衬在外层复合材料强作用下会过早被压溃,从而失去承载能力,过厚的金属会使得壳体的环向形变增大。研究结果可为双层复合材料爆炸圆筒的设计提供数据参考。
关键词:复合材料爆炸圆筒;爆炸载荷;双层壳体;变形与破坏
0 引言
爆炸容器是一种用来限制内部爆炸物爆炸对周围人员和设备造成伤害的特殊容器,广泛应用于科学研究、爆炸加工、公共安全等领域[1-3],常用的是圆柱形容器。复合材料由于其轻质高强的特性,广泛用于爆炸容器,相对于金属容器,复合材料爆炸容器的变形与破坏更为复杂,其动力学响应问题是该领域研究的热点与难点。
柱形整体容器结构较为复杂,因此变形特征研究常以两端开口圆筒为对象。早期,Tsypkin等[4]对玻璃纤维增强复合材料爆炸圆筒失效进行研究时发现,小当量炸药爆炸单次加载条件下当爆心截面环向应变在2.5%左右时,容器即在后续的振动周期中发生破坏。该应变值小于纤维的极限应变,究其原因是容器的呼吸振动模态向弯曲振动模态转变,导致其环向应变发生应变增长,研究发现该增长倍数可达到2倍甚至更高[5-6]。后来发现通过在玻璃纤维壳内加入一定厚度的薄钢板层,可以有效阻止这种现象发生,从而提高容器的承载能力[7-8]。胡洋[9]采用固连失效接触模型(Tie-Break Contacts)和内聚准则研究了复合材料容器中复合材料层在爆炸载荷作用下的分层破坏。Dong等[10-11]通过实验得到了玻璃纤维复合材料爆炸圆筒和碳纤维爆炸圆筒的破坏模式,其中玻璃纤维复合材料爆炸圆筒在内爆条件下的两种破坏模式,一是内衬可能发生动态屈曲,导致外玻璃纤维壳体分层断裂,限制了玻璃纤维爆炸容器的抗爆炸载荷能力,二是内衬明显的圆形塑性膨胀和外纤维壳纤维断裂。
目前的研究多为实验研究,受测试的限制,获得数据有限,对双层壳体变形过程和变形机制的研究不充分。本文将多层缠绕的复合材料简化成一层正交各向异性材料,通过LS-DYNA软件来探究内爆条件下爆炸圆筒内外层的相互作用规律,以及改变容器的内外层厚度比对容器承载能力的影响。
1 数值模拟模型简化及校核
1.1 模型简化
本文主要研究玻璃纤维复合材料爆炸圆筒在内爆条件下的动态响应。在内爆条件下,复合材料爆炸圆筒柱形段的变形长度不超过直径的2倍[12],爆心截面是最容易破坏的位置。因此,本文将玻璃纤维复合材料爆心截面代替容器的筒身作为研究对象。
玻璃纤维复合材料由纤维和基体组成,表现为正交各向异性力学性能,表1为单向纤维复合材料板的力学性能参数。
表1 复合材料性能参数
Tab.1 Performance parameters of composite materials
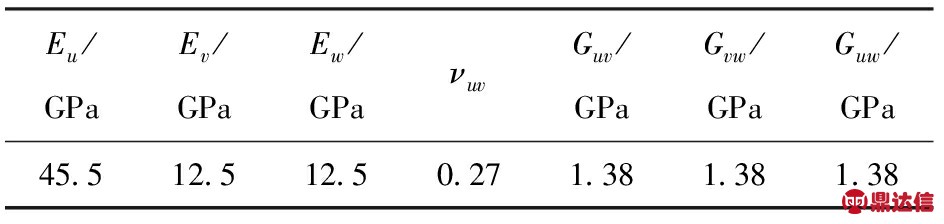
注:Eu、Ev和Ew表示材料的弹性模量,νuv为材料的泊松比,Guv、Gvw和Guw为材料的剪切模量,u、v、w分别表示复合材料坐标系的轴向、环向和径向。
本文主要研究容器内外层之间的相互作用,对复合材料内各铺层之间的相互作用与分离不作考虑,因此将12层不同铺层角度的复合材料简化成一层正交各向异性材料,等效后的材料参数可以通过理论计算得到。
爆炸圆筒玻璃纤维绕外壳的坐标关系如图1所示。图1中,α为纤维纵向与环向坐标轴之间的夹角,z、θ、r分别表示整体坐标系的轴向、环向和径向。由于纤维复合材料每一层的材料坐标系与整体的结构坐标系不同。先通过转换公式[13],将每一个单向纤维缠绕层本构关系表示在整体坐标系上:
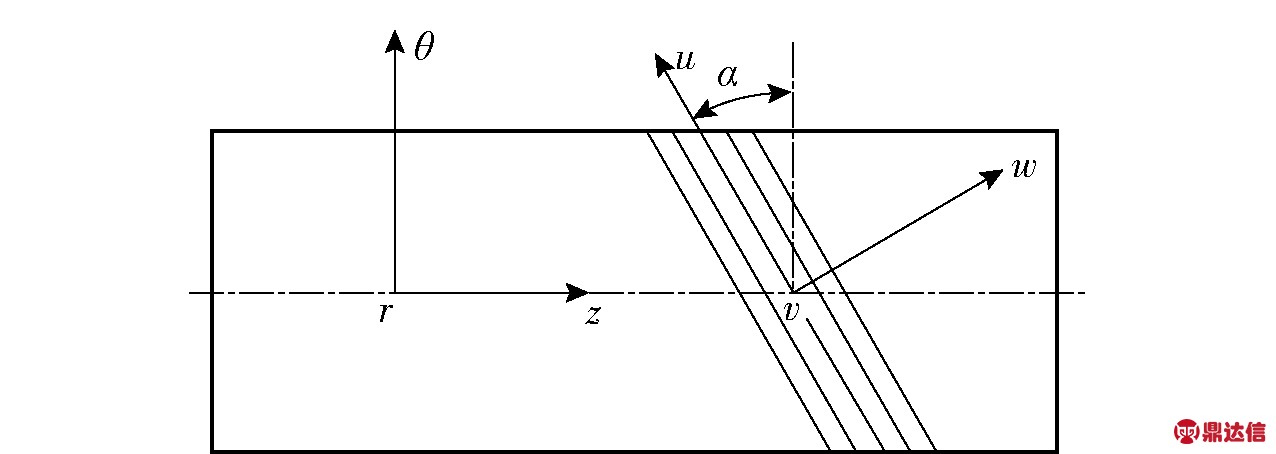
图1 爆炸圆筒玻璃纤维缠绕外壳的坐标关系
Fig.1 Coordinate relationship of glass fiber-wound shell of explosive cylinder
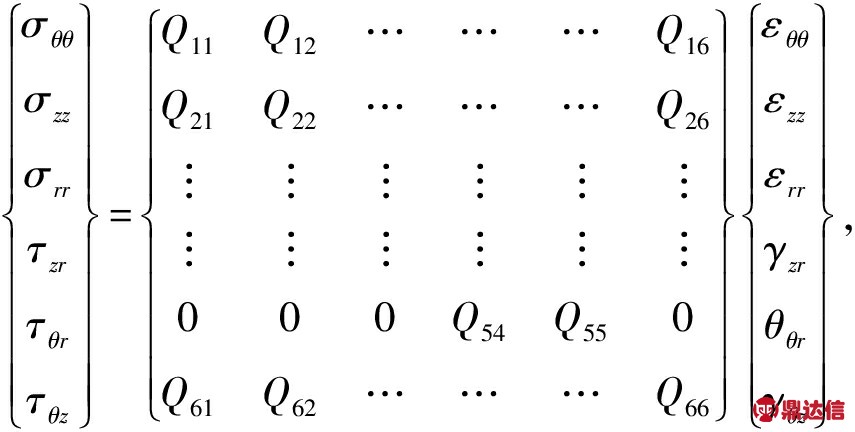
(1)
式中:Qij(i、j=1,2,…,6)为弹性常数;σθθ、σzz、σrr表示正应力;τzr、τθr、τθz表示切应力;εθθ、εzz、εrr表示正应变;γzr、γθr、γθz表示切应变。
通过一系列简化[14],最后得到材料的径向、轴向和环向等效弹性模量关系式如下:
(2)
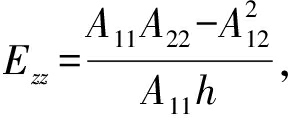
(3)
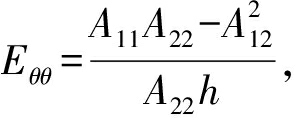
(4)
式中:Err为等效径向弹性模量;Ezz为等效轴向弹性模量;Eθθ为等效环向弹性模量;为外层复合材料缠绕总层数的一半,tk为第k层缠绕层的厚度;
为复合材料缠绕层总厚度;J23=
由文献[9]可知,柱形圆筒爆心截面的径向位移主要与材料的环向模量相关[15],因此根据玻璃纤维复合材料的参数,可以计算出等效后正交各向异性层的环向模量。
1.2 载荷简化
本文中的复合材料爆炸圆筒是两端开口的,爆炸载荷不会在容器内反复聚集、对容器产生进一步的破坏,选取的研究对象仅为爆心截面,计算发现爆炸载荷第1个脉冲的反射冲量对容器壳体的响应影响最大,后续脉动的压力基本可以忽略。通过LS-DYNA软件中的流体与固体耦合任意Lagrange-Euler算法(ALE)计算出各药量在容器内壁附近的反射压力曲线,提取的载荷冲量与霍宏发等[16]、张德志等[17]和刘文祥等[18]实验中测量得到的结果一致。再将得到的曲线加载容器的内壁上,可以避免重复使用ALE算法,加快计算效率。
1.3 数值模拟校核
经过1.1节的简化模型,建立的数值模拟模型如图2所示。复合材料爆炸圆筒的内衬是不锈钢,内径为216 mm,厚度为1.5 mm,圆周方向网格尺寸为2 mm×2 mm,径向划分为5个网格,共有5 100个网格。采用*MAT_KINETIC_PLASTIC关键字进行模拟,该关键字使用Cowper-Symonds本构方程描述内衬的变形和应变率效应,其关系式为
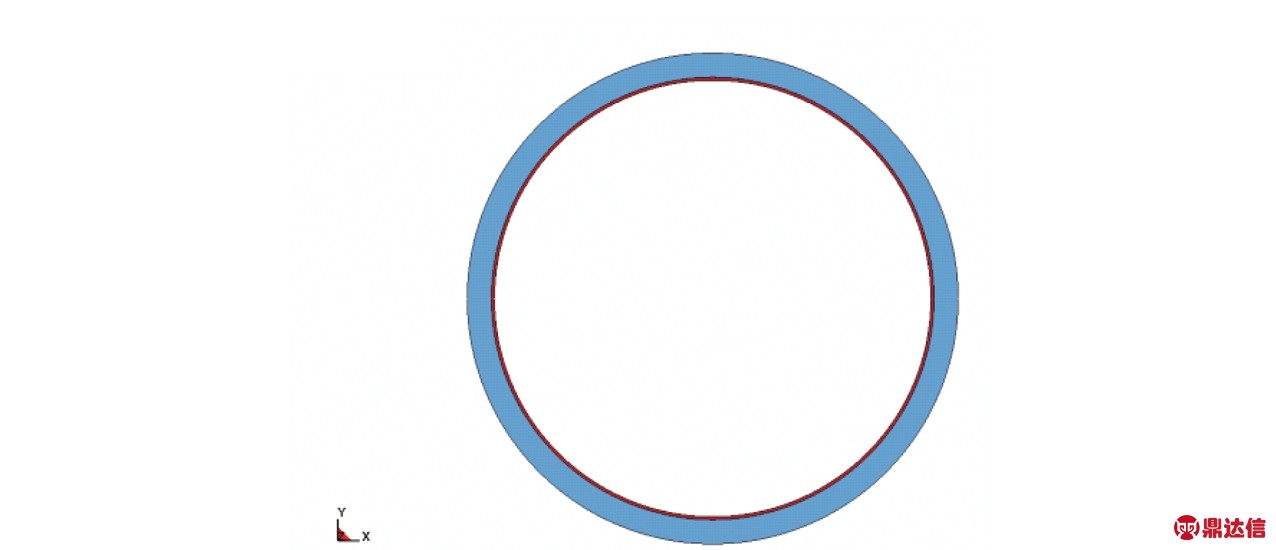
图2 爆炸圆筒的数值模拟模型
Fig.2 Numerical simulation model of explosive cylinder
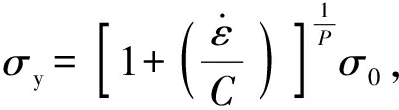
(5)
式中:σ0、σy分别为内衬准静态屈服应力和动态屈服应力;为应变率;C和P为应变率参数。表2为内衬各参数取值。
表2 不锈钢内衬的材料参数
Tab.2 Material parameters of stainless steel lining

注:E为不锈钢内衬的弹性模量,ν为泊松比,ρ为材料密度,σs为材料屈服强度,β为硬化系数,fs为单元的有效塑性应变。
外层复合材料内径为219 mm,厚度为12 mm,圆周方向网格尺寸为2 mm×2 mm,径向划分成12个网格,总共有13 968个网格。采用*MAT_ENHANCED_COMPOSITE_DAMAGE关键字进行模拟,该关键字考虑了复合材料的失效,比较符合材料在实验过程中真实的失效状态。经过1.1节的简化,铺层为45°/-45°/90°(由3个缠绕循环构成,每个缠绕循环交错和环向缠绕厚度分别为1 mm、1 mm、2 mm,即厚度比为1∶1∶2)的玻璃纤维复合材料参数如表3所示。由于壳体的变形速率不太高,复合材料没有考虑其应变率效应。
表3 复合材料性能参数
Tab.3 Performance parameters of composite materials
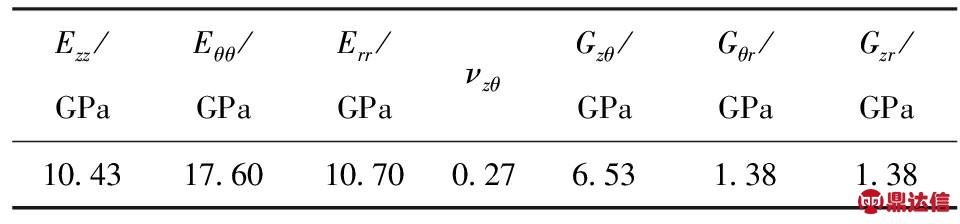
注:νzθ为泊松比,Gzθ、Gθr和Gzr为复合材料层等效的剪切模量。
玻璃纤维缠绕爆炸圆筒外层复合材料缠绕在内衬上,通过面-面接触来定义,即*CONTACT_AUTOMATIC_SURFACE_TO_SURFACE关键字。
甘云丹[19]在60 g药量內爆作用的实验中,通过三维数字相关图像方法(3D-DIC)取出爆炸圆筒最外层点上的径向位移曲线,如图3中带方块的线。本文在相同条件下进行数值模拟计算,以爆炸圆筒的圆心为坐标原点,取圆筒与x轴正向相交最外层的点为参考点,得到该点的位移时程曲线,如图3中带圆形的线。由图3可以看出,通过简化模型计算得到的位移时程曲线与文献[19]实验得到的曲线基本一致,从而表明本文的数值模拟计算参数设置合理、结果有效。
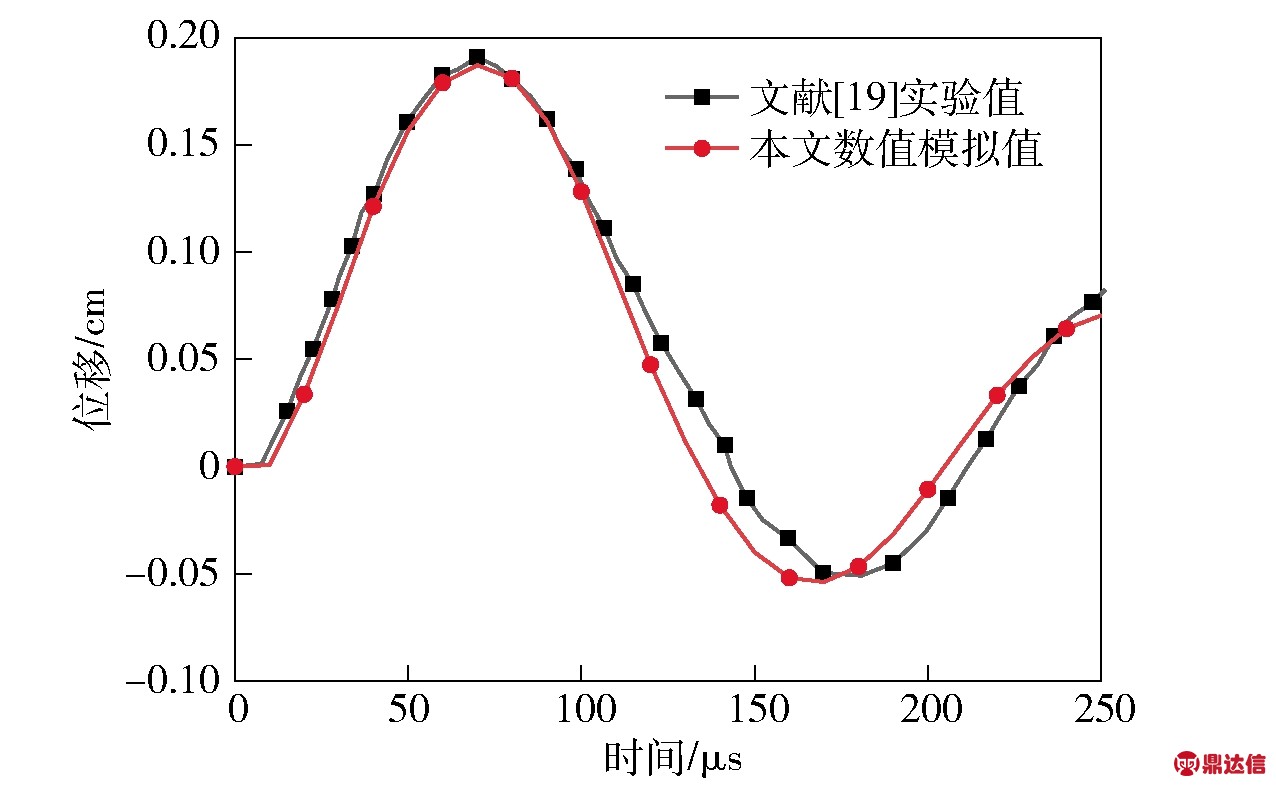
图3 60 g药量下数值模拟与文献[19]实验结果的对比
Fig.3 Comparison of numerically simulated and experimental results in Ref.[19]under the action of 60 g dose
2 不同药量内爆作用下爆炸圆筒的变形特征
采用验证后的计算参数,利用LS-DYNA软件进行数值模拟,研究复合材料爆炸圆筒在不同药量內爆作用下的变形特征。采用的数值模拟模型内径为216 mm,内衬厚度为1.5 mm,外层复合材料厚度为12 mm.通过改变内爆的药量得到位移时程曲线,来观察结构的变形特点。以爆炸圆筒的圆心为坐标原点,取圆筒与x轴正向相交为0°,下文中位移时程曲线中的内衬曲线所取的点是0°上内衬最外层的点,外层运动曲线所取的点是0°上外层复合材料最内层的点。
2.1 小药量内爆作用下壳体的变形特征
在30 g药量內爆作用下,通过图4中的位移时程曲线可以看出,结构基本处于弹性振动,没有发生内衬和外层复合材料分离的现象,结构在振动后期振动频率发生了一定的改变。将位移时程曲线进行快速傅里叶变换(FFT),得到结构的振动频谱图(见图4(b)),可以看出结构的振动频率主要有两种,一种是结构的呼吸振动模态(5.79 kHz,0.150 4),另一种是结构的第5阶弯曲模态(2.99 kHz,0.004 39)(见图5)。由此可见,从呼吸模态向弯曲模态的转变是导致结构后期振动曲线发生改变的原因。
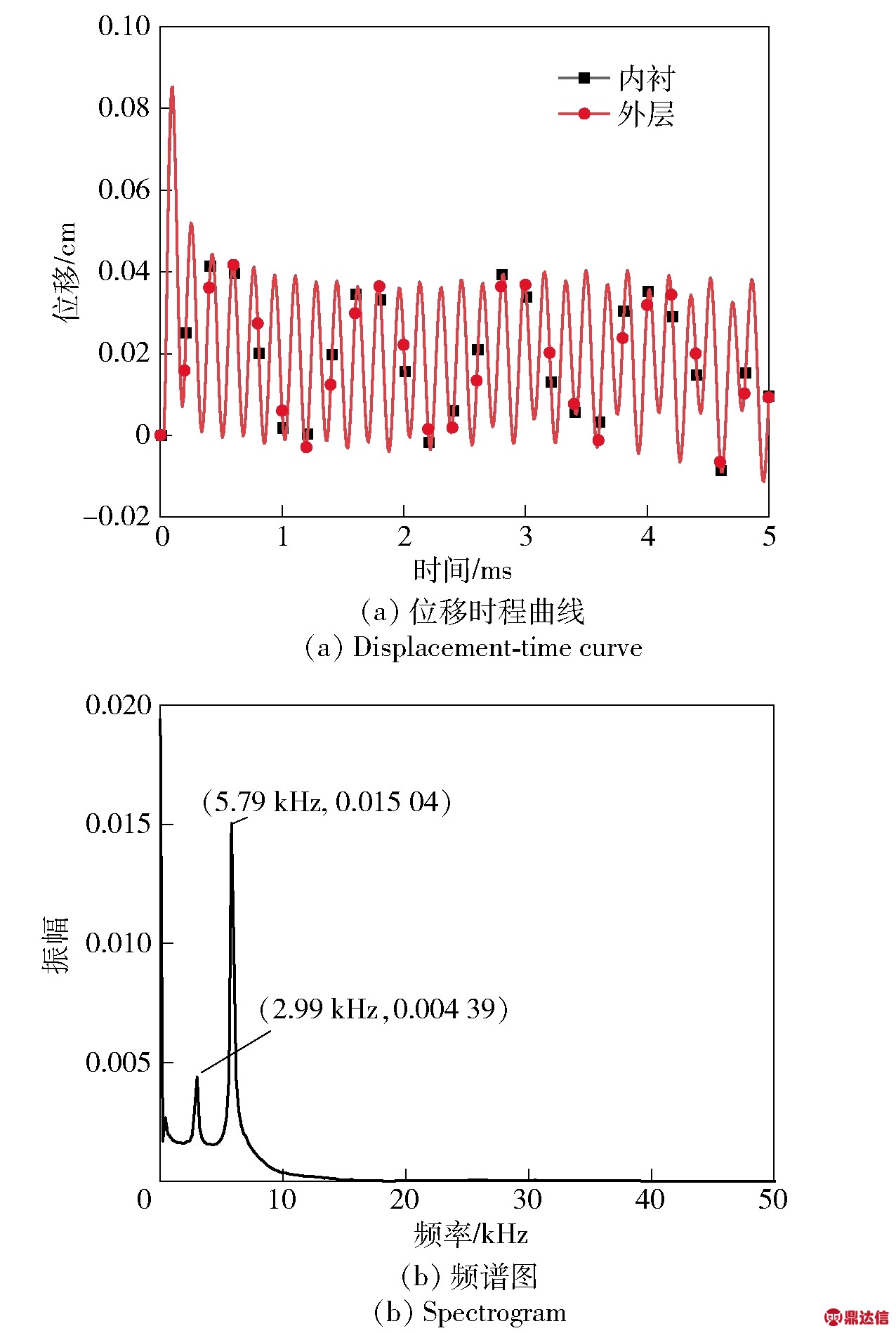
图4 30 g药量作用下结构的位移时程曲线以及频谱图
Fig.4 Displacement-time curve and spectrogram of structure under the action of 30 g dose
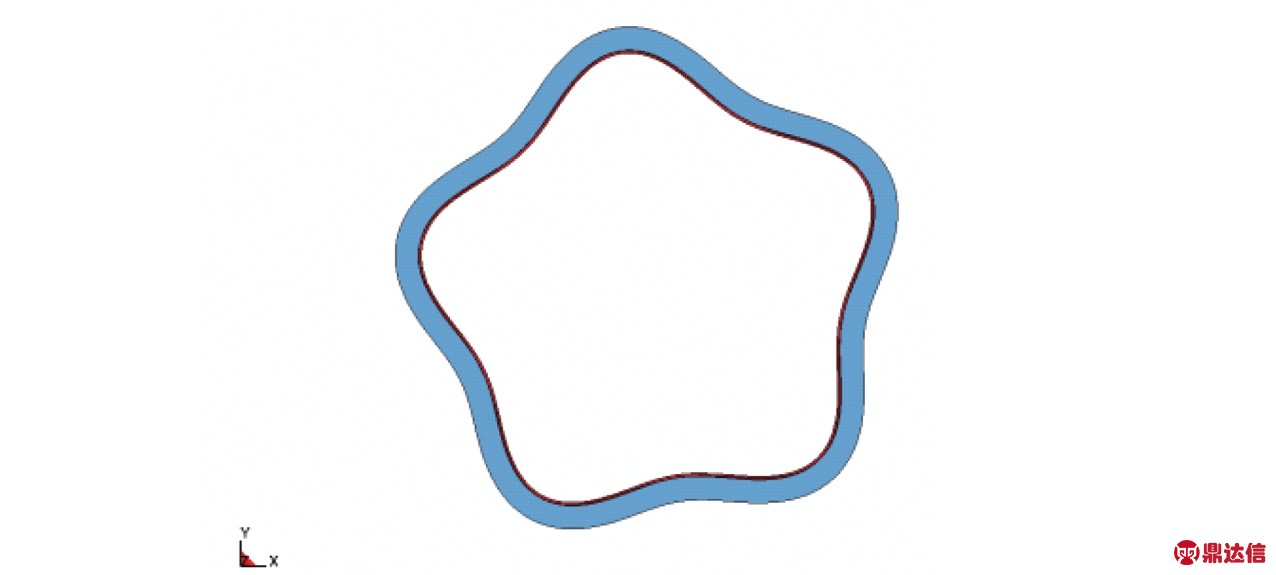
图5 爆炸圆筒的第5阶弯曲模态(2.99 kHz)
Fig.5 Fifth-order bending mode of explosive cylinder(2.99 kHz)
2.2 中等药量内爆作用下壳体的变形特征
当内爆药量增加至50 g时,结构出现了内衬和外层复合材料分离的现象。从图6中可以看出,结构在0.24 ms时内外层的速度开始不一致,此时已经第2次过了平衡点,在0.27 ms时,发生内外层分离,在第2个周期的后半程中,外层复合材料向内运动时与内衬发生了较强的相互作用,但是由于相互作用力较小,没有对内衬造成较大的变形,但能量被耗散掉了,并且在随后的相互作用中继续消耗能量。
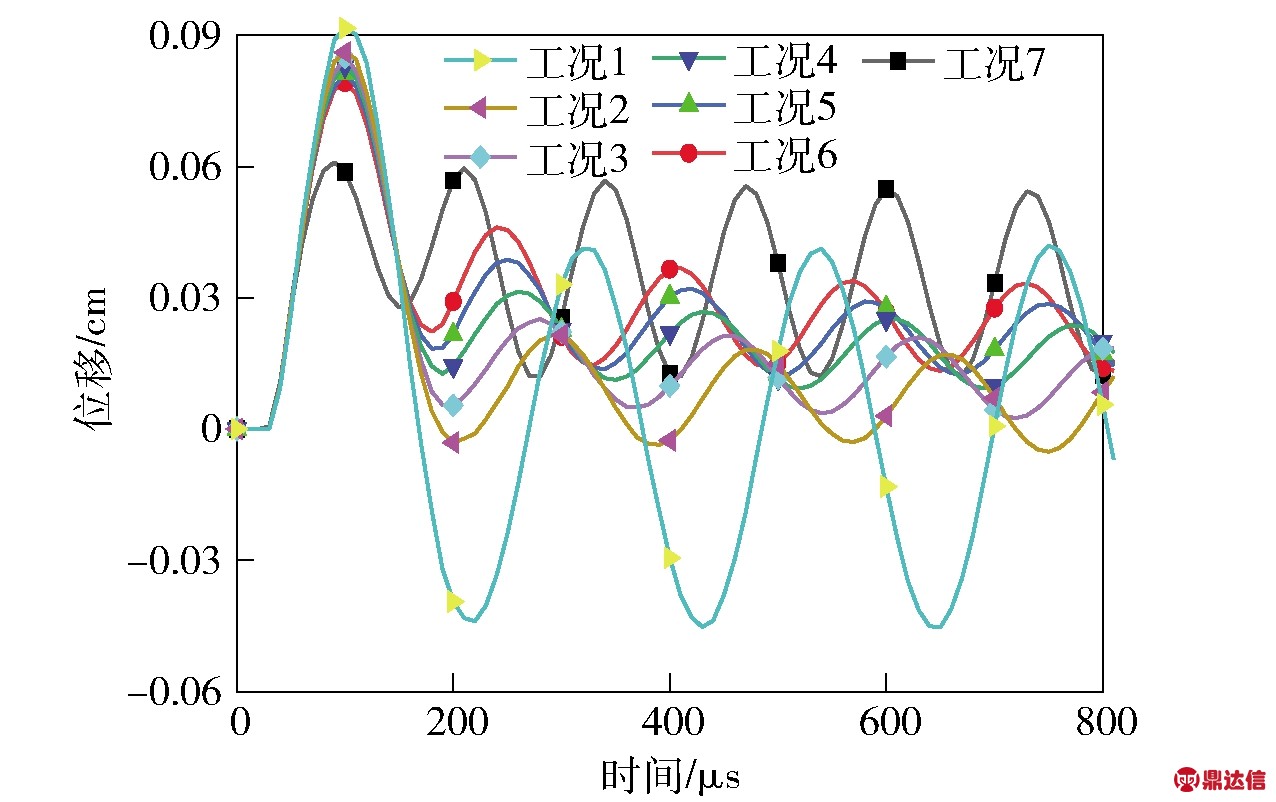
图6 50 g药量作用下爆炸圆筒径向运动曲线
Fig.6 Radial motion curve of explosive cylinder under the action of 50 g dose
当药量增加到70 g时,爆炸圆筒在0.27 ms时刻发生了内外层分离,随后内外两层均以自身的频率各自振动,且在相互碰撞3次后,外层复合材料发生层内单元失效破坏(见图7)。在相互作用过程中,内衬形状有不规则的变形,这主要是因为内外层的相互作用激发了各种不同频率振动模态的耦合,其中内衬的呼吸模态频率为7.78 kHz,幅值为0.001 84;外层复合材料的呼吸模态频率为4.87 kHz,幅值为0.010 24(见图8),但是内外层相互作用力不是很大,内衬的形状最终并没有发生改变(见图7和图8)。
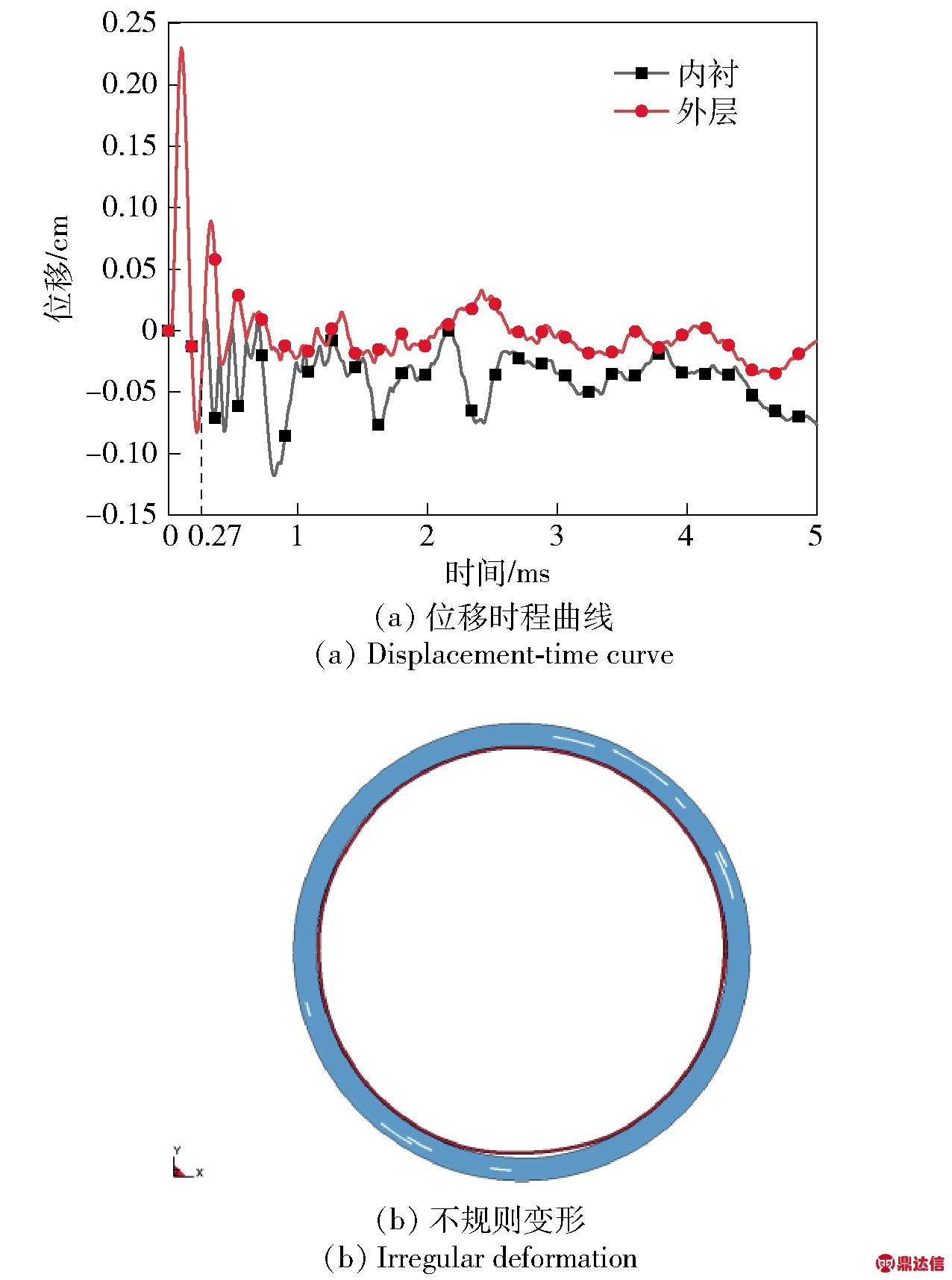
图7 70 g药量作用下爆炸圆筒径向运动曲线和内衬不规则变形截面图
Fig.7 Radial motion curve of explosive cylinder and irregular deformation section of lining under the action of 70 g dose
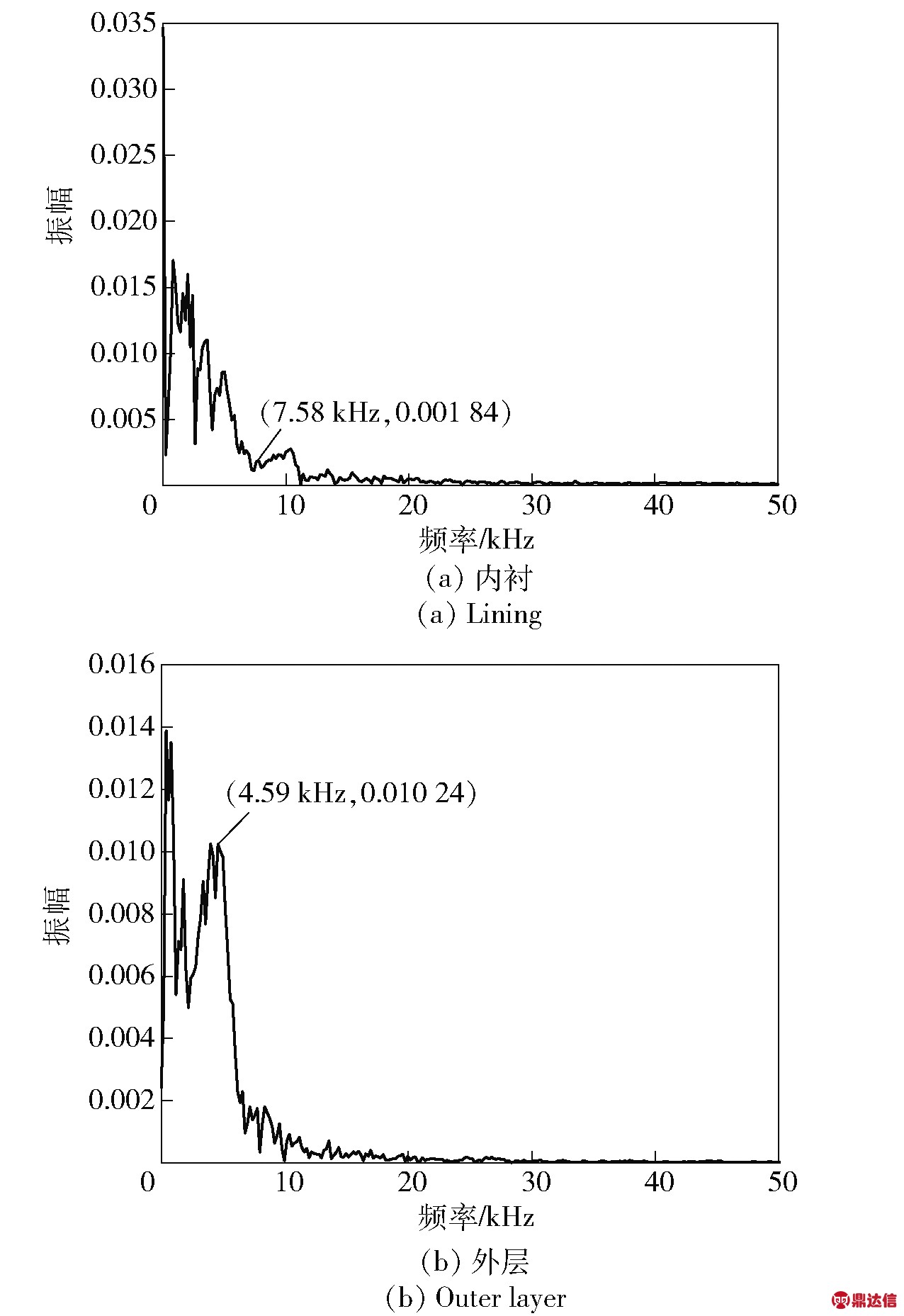
图8 70 g药量作用下爆炸圆筒内外层的频谱图
Fig.8 Spectrogram of inner and outer layers of explosive cylinder under the action of 70 g dose
在80 g药量內爆作用下,爆炸圆筒也发生了外层复合材料的层内单元破坏失效,相比于70 g药量內爆作用下的结构,外层复合材料层内失效的单元减少,但是内衬形状发生了很大变化。从图9中可以看出:70 g药量作用下,内衬经过外层复合材料的第1次挤压后基本处于稳定状态;80 g药量下,外层复合材料多次挤压内衬,使内衬有了较大的塑性变形,吸收了更多的能量。
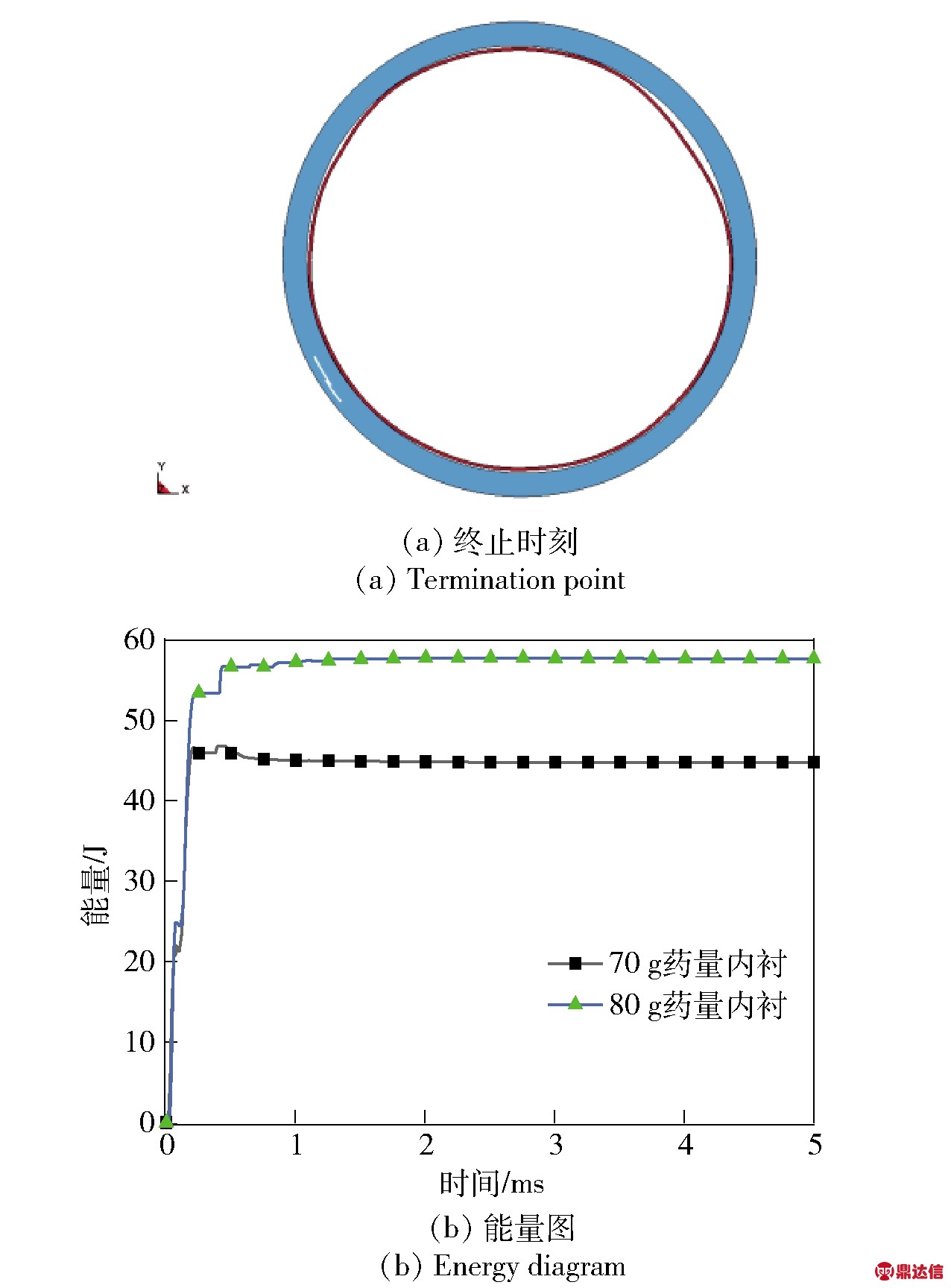
图9 80 g药量下的截面图和爆炸圆筒金属内衬的总能量图
Fig.9 Sectional diagram at 80 g dose and total energy diagram of each material in the explosive cylinder
2.3 大药量内爆作用下壳体的变形特征
100 g药量作用下,爆炸圆筒更早地发生了内外层分离,外层复合材料也发生了层内失效分离,且内衬形状也变成了不规则形状(见图10)。
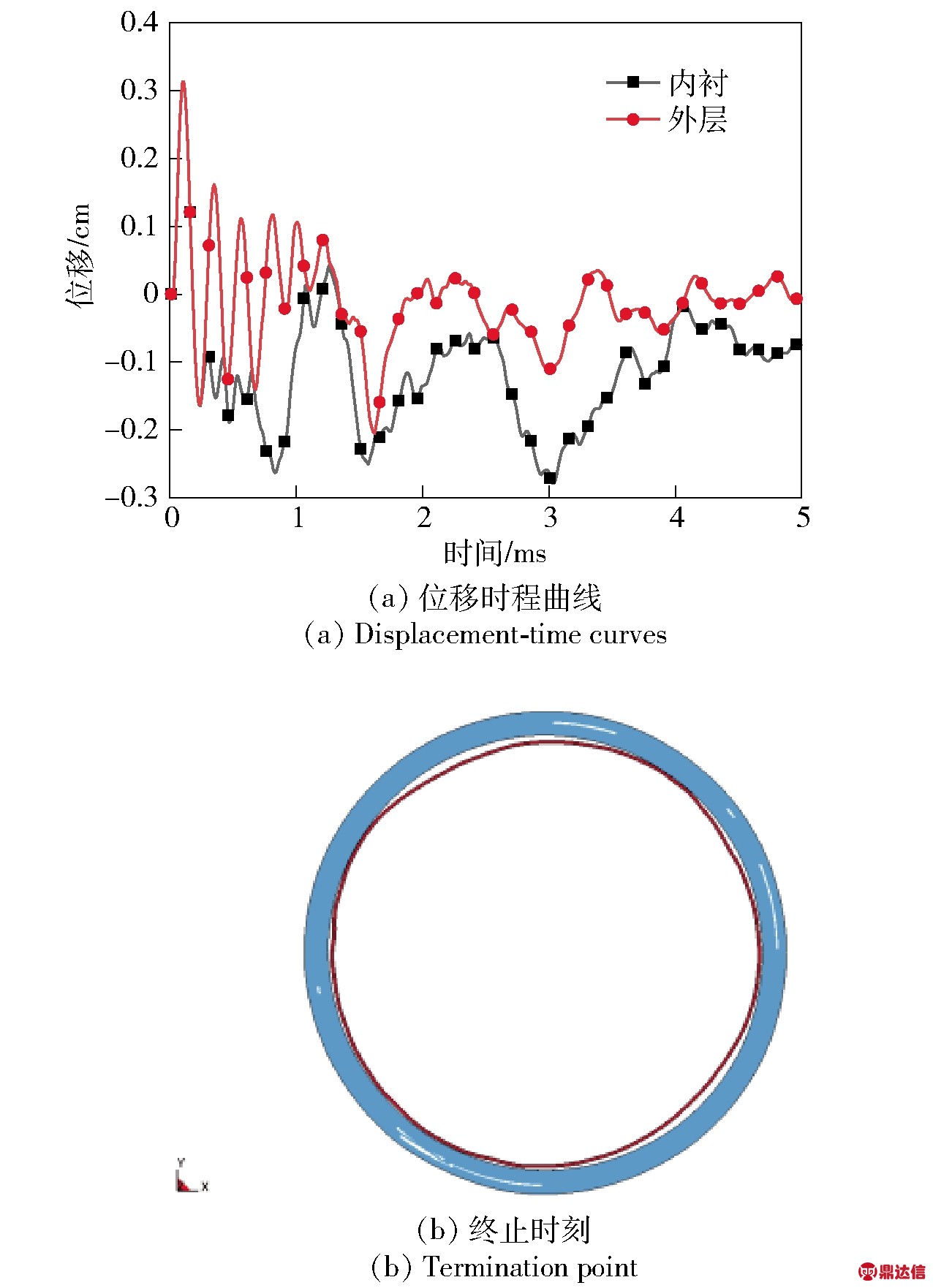
图10 100 g药量作用下爆炸圆筒径向运动曲线和圆筒截面图
Fig.10 Radial motion curve and cross section of explosive cylinder under the action of100 g dose
当药量增大至120 g时,从图11中的位移时程曲线可以看出,爆炸圆筒在第1个周期的波谷时就发生了内外层的分离,随后内外层依据自身的频率各自振动,经历两次碰撞之后内衬发生了较大的塑性变形,出现了屈曲失稳的状态,结构的承载力大大下降。
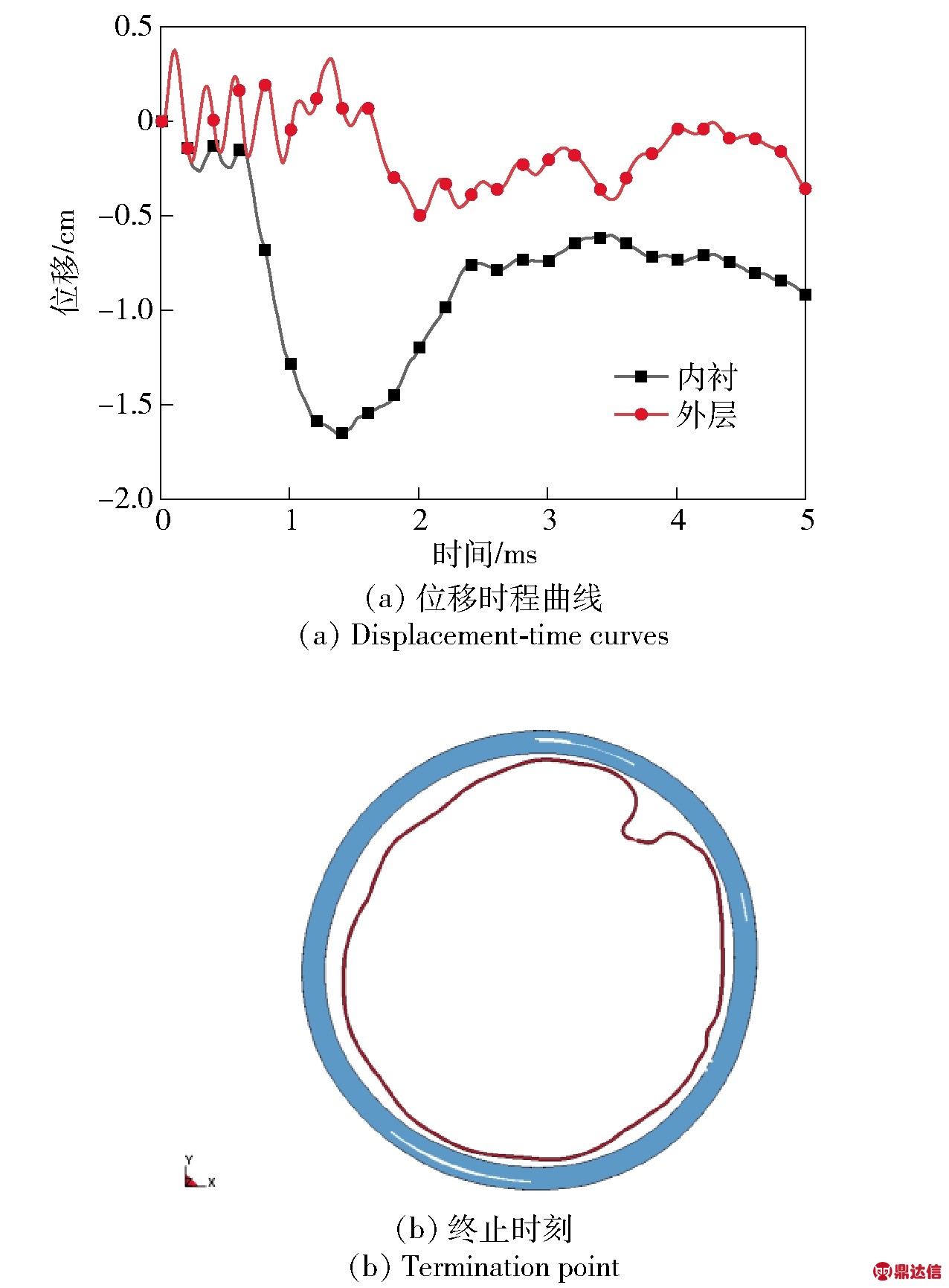
图11 120 g药量作用下爆炸圆筒径向运动曲线和圆筒截面图
Fig.11 Radial motion curve and cross section of explosive cylinder under the action of 120 g dose
160 g药量作用下,由于能量太大,结构在160 μs时,外层复合材料就出现了破坏断裂。由于选取的参考点均在0°上,从图12的位移时程曲线中可以看出,内衬在达到平衡位置时与外层复合材料发生完全分离。此时内衬发生了严重的塑性变形,外层复合材料也发生了破坏断裂,结构已不具备承载能力。
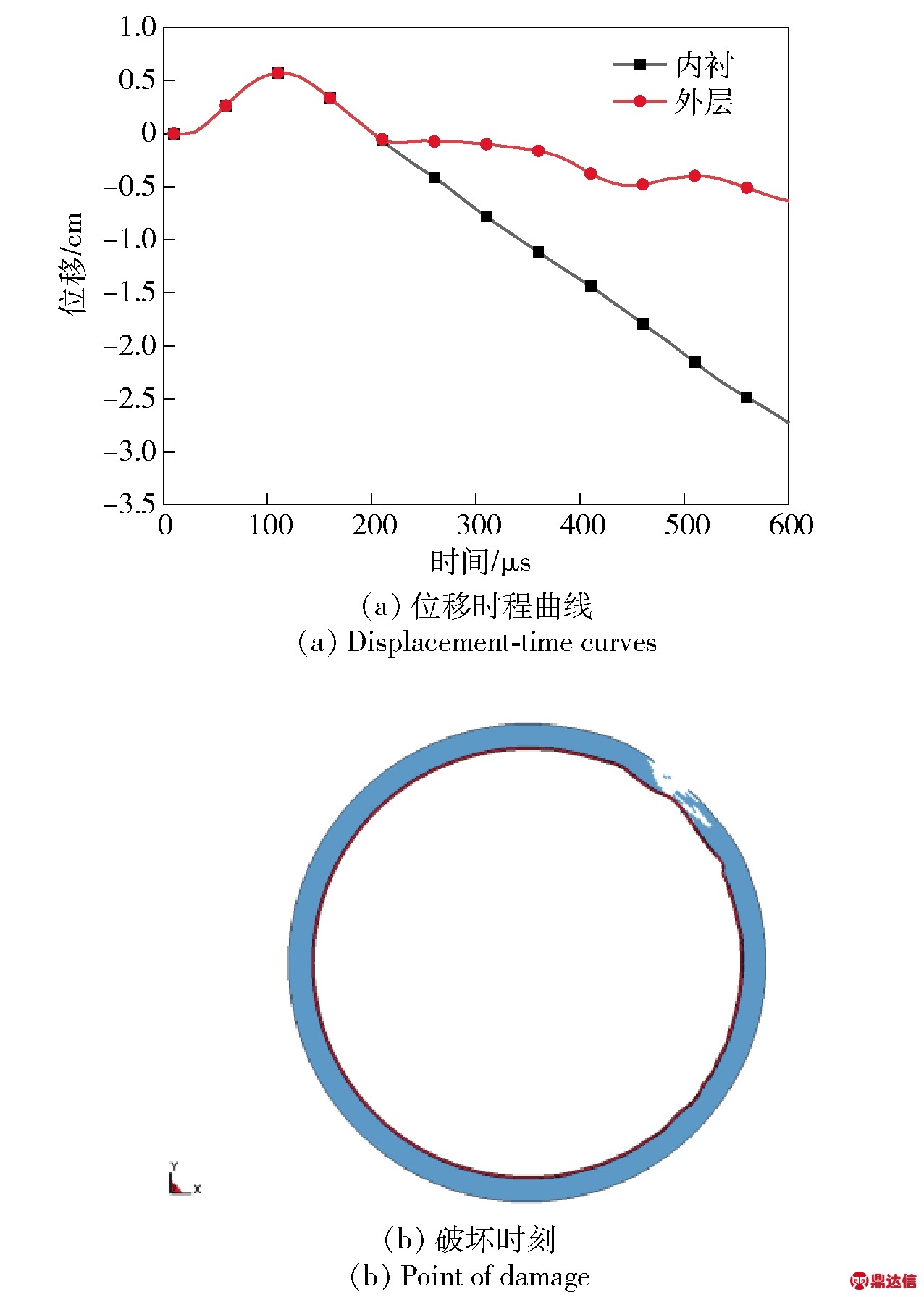
图12 160 g药量作用下爆炸圆筒径向运动曲线和圆筒截面图
Fig.12 Radial motion curve and cross section of explosive cylinder under the action of 160 g dose
综上所述可以看出,在小药量内爆载荷作用下,爆炸圆筒基本只发生弹性振动。随着药量的增加,圆筒先发生内外层的分离,再发生内外层相互作用,但是由于相互作用力较小,内衬形状基本保持圆形。当药量继续增加时,内外层的相互作用力逐渐变大,内衬形状由圆形变为不规则形状,以至于发生失稳破坏。直至药量增加到160 g时,外层复合材料在第1个周期内就发生了完全破坏。
3 不同厚度比复合材料爆炸圆筒的变形特征
为了能够有效优化结构尺寸,进一步研究复合材料爆炸圆筒内衬与外层复合材料厚度比对容器承载能力的影响。本文在保证面密度相等的情况下,通过改变内衬与外层复合材料的厚度比,建立了7种不同厚度比的模型,具体模型尺寸如表4所示。
表4 不同厚度比结构尺寸
Tab.4 Structure sizes of models with different thickness ratios
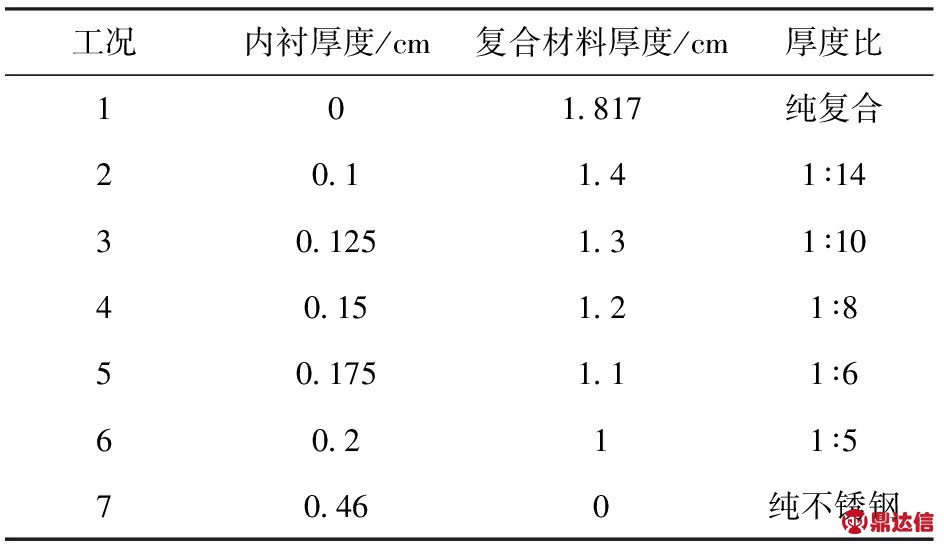
对7种不同厚度比的模型分别进行30 g、60 g、80 g和100 g药量的数值模拟,针对其中的位移和能量进行分析,以圆筒圆心为坐标原点,圆筒最外层与x轴正向相交的点为位移时程曲线所取的参考点。
3.1 壳体动态响应分析
在30 g药量作用下,爆炸圆筒结构中复合材料比重越大,圆筒径向第1次到达的最大拉伸位移也会越大,圆筒第1次向内回缩的位移也越大。除1号工况外,其余工况都发生了微小的塑性,但是没有发生内外层分离的情况,也没有出现外层复合材料层内单元失效破坏的情况(见图13)。
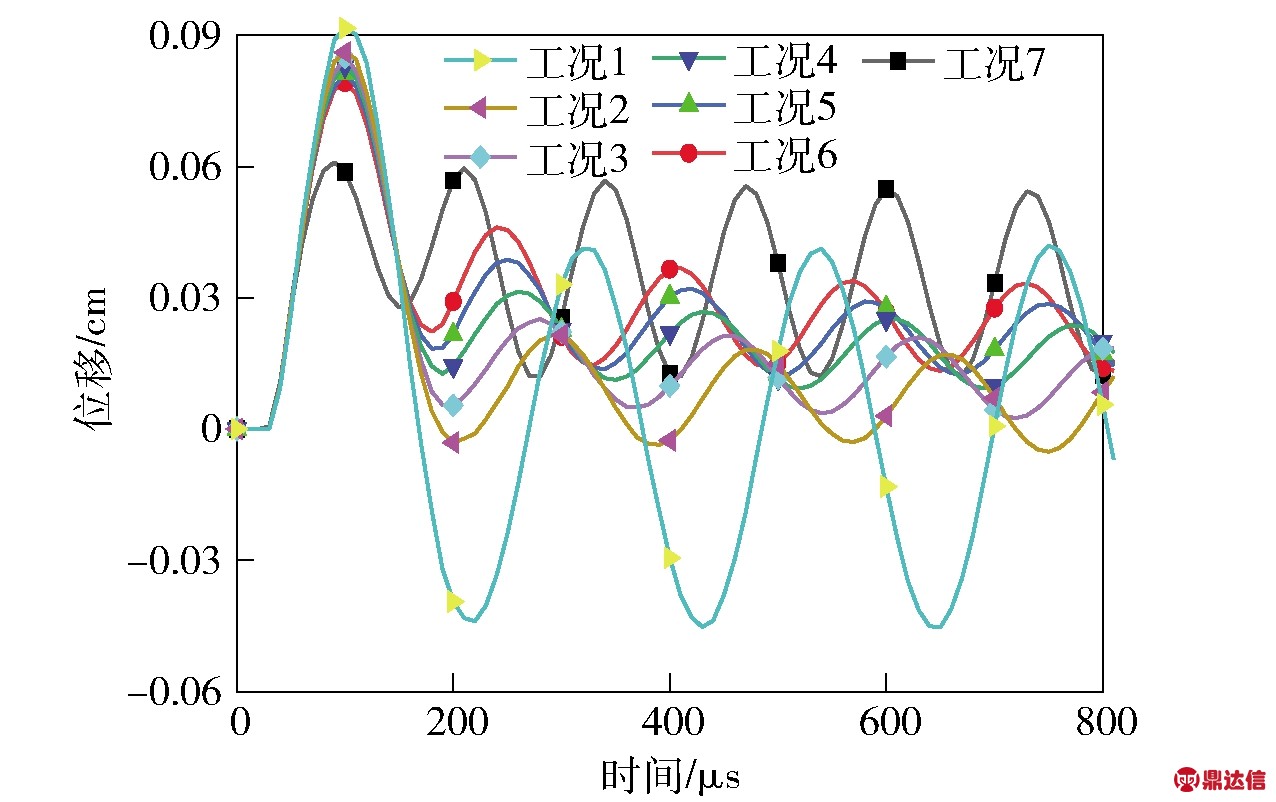
图13 30 g药量各工况下爆炸圆筒的径向位移时程曲线
Fig.13 Time history curve of radial displacement of 30 g explosive cylinder under various conditions
在60 g药量作用下,爆炸圆筒结构中复合材料比重越大,圆筒径向第1次达到的最大拉伸位移越低。出现了与30 g药量內爆作用下相反的规律。只有工况1发生了应变增长,导致结构发生破坏,其余不同厚度比的爆炸圆筒只发生了内外层分离、没有发生破坏。由于爆炸圆筒的内外层发生分离后会按照自身频率开始振动,外层复合材料属于弹性振动,而内衬已经发生了塑性应变,因此在振动过程中内外层会发生相互碰撞,每次碰撞都会加大内衬的塑性,随着复合材料所占比重的增加,内衬所吸收的能量在逐渐减少(见图14)。
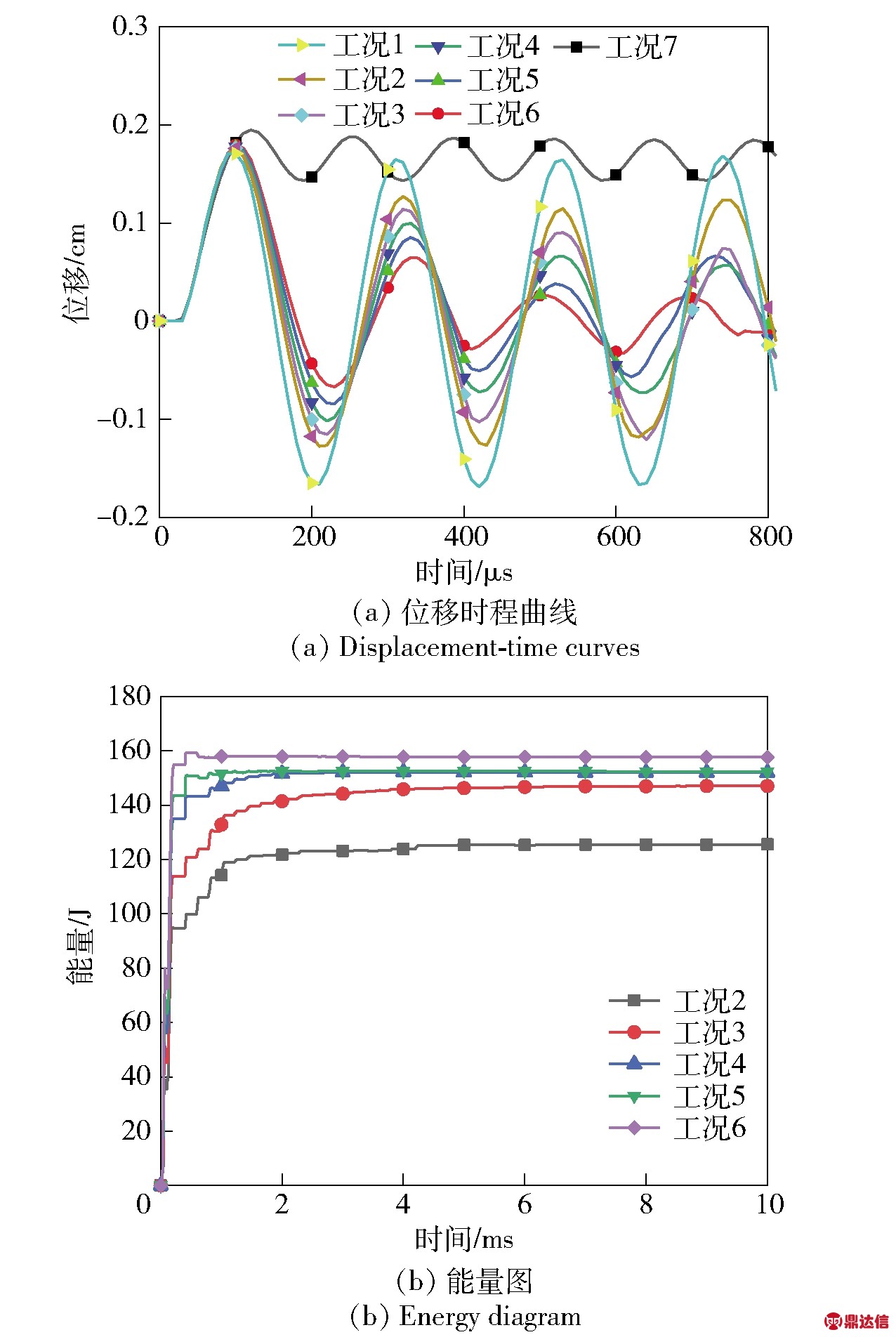
图14 60 g药量各工况下爆炸圆筒的径向运动曲线和材料能量图
Fig.14 Radial motion curves and material energy diagram of 60 g explosive cylinder under various working conditions
在80 g药量作用下,爆炸圆筒径向位移的规律与60 g药量作用下相同,即爆炸圆筒第1次达到的最大拉伸位移会随着复合材料比重的增大而减小。从图15中可以看出,在保证壳体面密度相等的情况下,随着复合材料所占比重的增加,内衬所吸收的能量在逐渐减小。在该药量内爆条件下,1、2和3这3种工况,外层复合材料会完全发生破坏,而4、5和6这3种工况,内衬和外层复合材料发生分离,外层复合材料出现层内单元失效分离现象,但是并没有发生完全破坏。

图15 80 g药量各工况下爆炸圆筒的径向运动曲线和材料能量图
Fig.15 Radial motion curves and material energy diagram of 80 g explosive cylinder under various working conditions
在100 g药量作用下,爆炸圆筒径向最大拉伸位移的规律也与60 g药量作用下相同。内爆条件下,工况1、工况2、工况3、和工况4下,外层复合材料发生完全破坏,在工况5和工况6下,内衬和外层复合材料发生分离,且出现层内失效分离的现象。从图16中可以看出,工况2、工况3和工况4下内衬只经过两次上升就不再改变,表明内衬已经被压溃,随后没有继续发生相互作用。整体来看仍然符合60 g药量作用下得到的能量规律,即随着复合材料所占比重的增加,内衬所能吸收的能量越少。
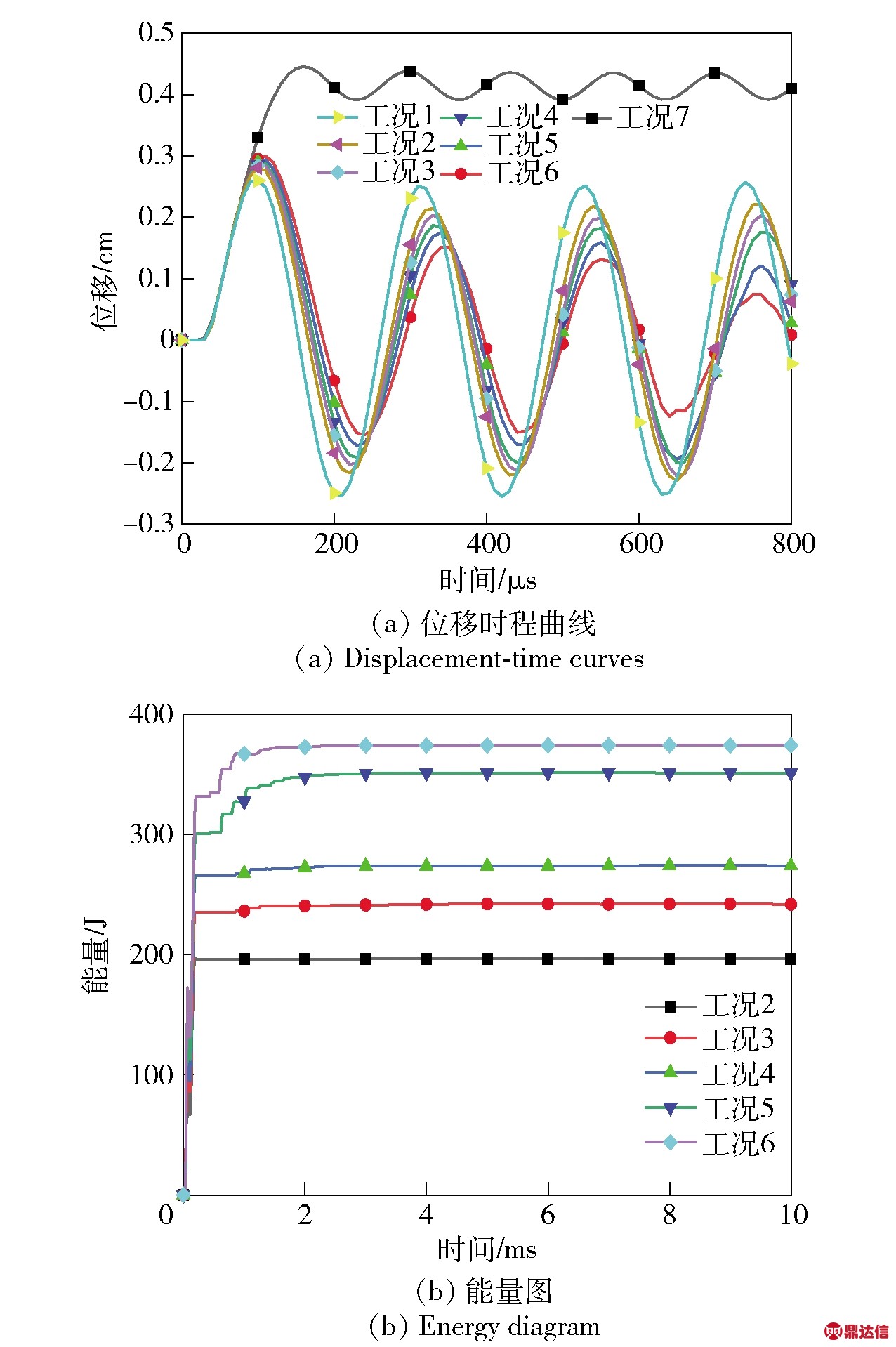
图16 100 g药量各工况下爆炸圆筒的径向运动曲线和材料能量图
Fig.16 Radial motion curves and material energy diagram of 100 g explosive cylinder under various working conditions
3.2 壳体经向位移计算与分析
爆炸圆筒径向位移在不同药量下呈现不同规律的现象,可以由赵士达[15]对爆炸容器的理论来解释。
根据冲量设计准则,容器的最大径向位移[15]为
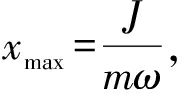
(6)
式中:J为单位面积上的冲量;ω为柱形容器的自振频率;m为单位面积的质量。
柱形容器的自振频率为
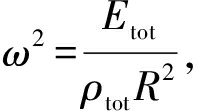
(7)
式中:ρtot为爆炸圆筒的总密度;R为容器的内径;Etot为容器的等效环向模量。
将(7)式代入(6)式,可以得到爆炸圆筒的最大径向位移:
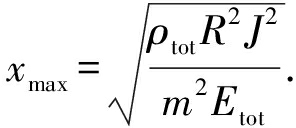
(8)
由(8)式可以看出,爆炸圆筒径向的最大拉伸位移会随着结构等效环向模量的增大而减小。因此,在小药量內爆条件下,爆炸圆筒的响应主要处于弹性阶段,等效环向模量会随着复合材料比重的增加而降低,容器的径向最大拉伸位移则会增加。在中等药量和大药量内爆情况下,爆炸圆筒的响应主要处于塑性段,此时内衬的环向模量就会低于外层复合材料的环向模量,整个结构的等效环向模量会随着复合材料比重的增加而增加,容器的最大拉伸位移则会降低。而内衬吸收能量的规律则与大小药量无关,只与内外层厚度比相关,即爆炸圆筒复合材料所占比重越大,内衬所吸收的能量越小。
4 结论
1)本文所提出的复合材料爆炸圆筒简化数值计算方法,可以提高计算效率,适用于圆筒内层金属与外层复合材料相互作用过程的数值模拟研究。
2)复合材料圆筒在不同药量下的相应特征如下:在小药量条件下,爆炸圆筒基本处于弹性状态,可用等效弹性模量描述其响应特征;随着药量的增加,内外层逐渐发生分离并相互作用,由于相互作用力不大,内衬形状还是圆形;药量继续增加,圆筒内外层分离更早,相互作用力更大,内衬的形状变得不规则,外层复合材料也发生层内单元失效分离;在大药量作用下,外层复合材料在第1个周期内就发生完全破坏。
3)复合材料圆筒在内爆载荷作用下,其金属内衬与外层复合材料存在强的相互作用,该作用是引起内衬不规则变形的主要原因。
4)相同面密度下不同内外层厚度比的爆炸圆筒在相同药量作用下的变形规律如下:小药量情况下,容器内衬的响应基本处于弹性段,容器第1次达到最大拉伸位移会随着复合材料比重的增大而增大;在大药量情况下,容器的响应基本处于塑性段,容器第1次达到最大拉伸位移会随着复合材料比重的增大而降低;内衬吸收的能量会随着复合材料比重的增加而降低。
5)过薄的金属内衬在外层复合材料作用下会过早地发生不规则变形,从而失去承载能力,会引起圆筒的承载能力下降。