摘要: 为避免车辆轮胎因扎刺或弹片侵彻等引起的爆胎问题,设计一种非充气型全金属网面车轮结构。建立关于轮胎的垂向刚度预测、垂向振动的理论分析模型;结合三维建模软件Pro/E、有限元前处理软件ANSA和有限元仿真软件Abaqus建立轮胎仿真模型;制作与235/70 R16型号充气轮胎同尺寸的轮胎样机,开展轮胎静力学压板试验和车辆平顺性试验。仿真结果表明,该金属轮胎在各向力作用下不会产生塑性变形,满足轮胎使用的强度条件;通过垂向刚度试验,验证了仿真过程的准确性和轮胎较强的承载能力;平顺性试验表明,金属轮胎在减振性能上略差于充气轮胎,但具有更好的抓地特性。
关键词: 金属轮胎; 全金属网面; 充气轮胎; 垂向刚度; 结构设计; 仿真与试验
0 引言
全金属网面车轮能有效防止因轮胎扎刺、爆胎等问题引起的安全事故。在军事领域,当车辆经过复杂地形、雷区或交火区域时,轮胎将不会因为弹片等损坏部分胎体或者卡入内部而影响正常机动;在航空航天领域,该车轮能在月球、火星等存在极大温差和高真空的极端环境中正常工作。目前,全金属车轮主要应用于星球探测车,从结构上可分为刚性车轮和弹性车轮[1],刚性轮胎如前苏联的Lunokhod探测车车轮[2],弹性轮胎如载人月球车(LRV)的金属丝编织轮[3];从结构外形上可分为圆柱轮、圆锥轮、鼓形轮、螺旋轮和筛网轮等,如Marsokhod型火星车Lama车轮[4-5]采用了圆柱和圆锥两种触地结构;用于星球探测和南极科考的轮式机器人自动越野车Nomad采用了鼓型全金属车轮[6];美国Grumman公司研发的移动测试站(MTA) MOLAB概念车采用了螺旋金属弹性车轮[7]。
与网面车轮具有近似结构的弹性车轮,除了上文提到的金属丝编织轮[3],还有由美国航空航天局和固特异公司联合研发的Spring Tire轮胎[8],已经成功运用于“悍马”车,但其相关参数目前还处于保密状态。
总之,由于弹性金属轮的承载能力差,而刚性金属轮的减振性能不好,使得国内暂时还没有类似的全金属车轮结构应用于军用或民用轮式车辆的报道。另一方面,载人星球车作为星球登陆的主要工具,对车轮承载和减振等性能都有很高要求,相关全金属车轮的理论、仿真及研制已十分必要[9-11]。
因此,本文创新性地设计一种非充气型全金属轮胎结构,通过对组成金属网面的单根主弹簧圈做受力分析,结合实际的金属丝编织工艺,确定了主、辅弹簧的丝径等结构参数;基于轮胎压板试验,建立了单根及3根主弹簧圈受压变形时的垂向刚度预测模型,并结合实验室3轴6×6无人车较简单的底盘结构,对金属轮胎的垂向振动特性做了理论分析;针对金属网面接触点多、隐式计算收敛性差的问题,结合三维建模软件Pro/E、有限元前处理软件ANSA和有限元仿真软件Abaqus,通过弹簧预弯计算、胎体整体建模、应力导入和隐式回弹计算等过程建立了具有较高精度的有限元模型,对其各向刚度做了仿真分析;最后通过开展轮胎刚度试验验证了理论和仿真模型的精度,通过平顺性试验对两种同尺寸轮胎的垂向振动特性做了对比分析。
1 全金属网面车轮结构设计
1.1 结构组成
在文献[12-13]的基础上,本文提出一种以金属网面结构为主支撑的非充气车轮,外层胎体可以通过包覆橡胶或履带等减振层构成多种车轮总成。图1(a)所示全金属结构可用于星球车、消防车等橡胶轮胎无法使用的真空、高温环境;图1(b)所示包覆橡胶层结构可用于普通铺装路面;图1(c)和图1(d)所示安装履带结构可以实现轮履复合推进,以适应各种越野路面。
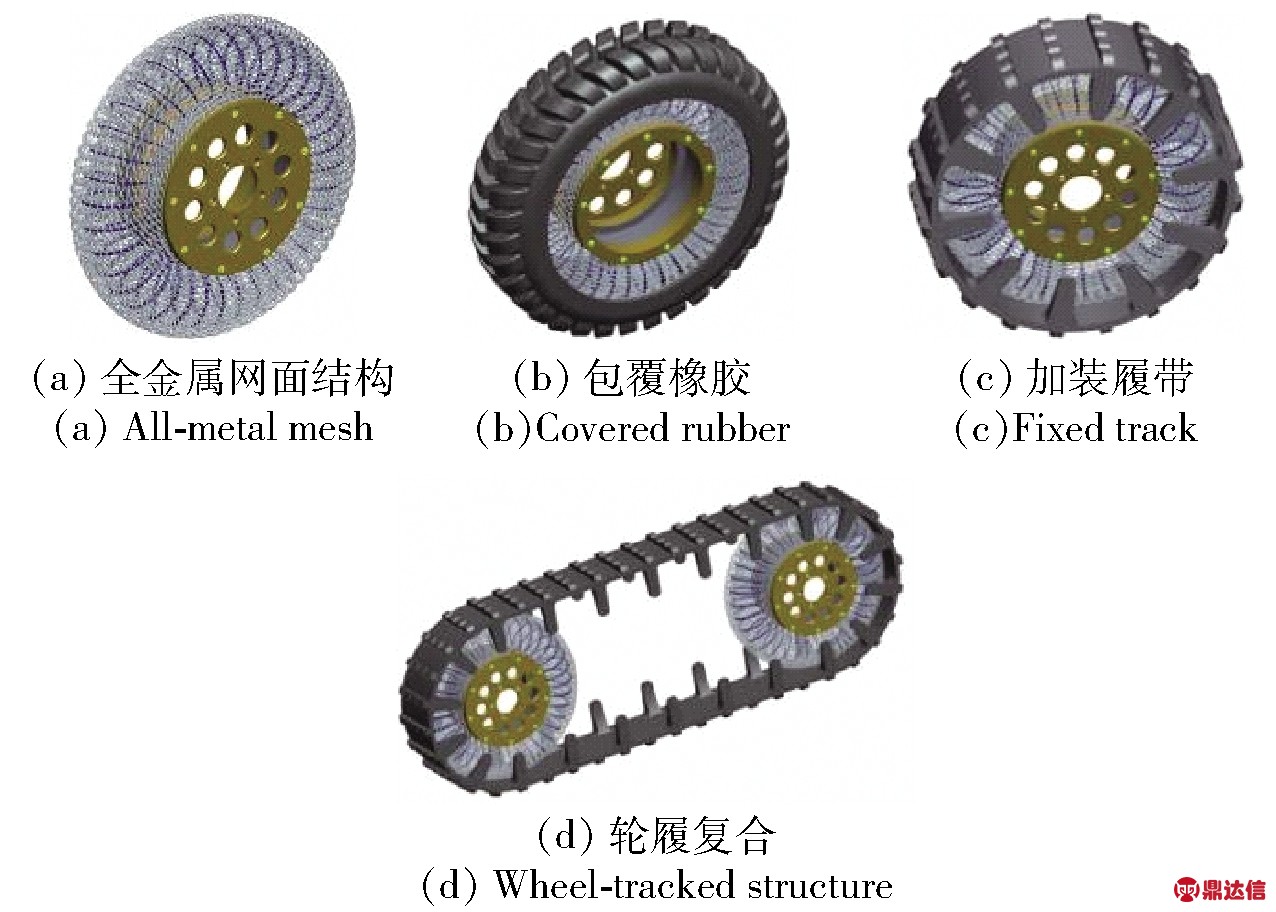
图1 基于金属弹簧内支撑的各种车轮总成
Fig.1 Wheel assemblies based on support of metal springs
图1所示车轮结构在保持与充气橡胶轮胎相近的承载、减振、牵引特性的同时,具有抗穿刺、免充气、使用温度范围广、绿色环保等优点。
本文以该类型车轮的基本结构即全金属网面车轮为研究对象开展相关研究,车轮组成如图2所示,胎体主要由主弹簧(蓝色)、辅弹簧网面(灰色)、固定带(亮黄色)、两侧卡盘(暗黄色)、具有螺旋凹槽的轮辋(黑色)组成。主弹簧由1根较粗的螺旋弹簧首尾相接形成内支撑体,多根旋向相同、螺距相等的辅弹簧相互勾连、形成辅弹簧网面,部分辅弹簧穿过主弹簧丝,保证主、辅弹簧结构一体性。主弹簧卡入轮辋表面的螺旋凹槽内,通过固定带和螺栓紧固。使用螺栓将辅弹簧网面固定在轮辋两侧,并通过卡盘上的U型孔限位。主弹簧承受大部分载重和力矩,辅弹簧网面承受部分载荷并增强胎体稳定性和地面附着性。
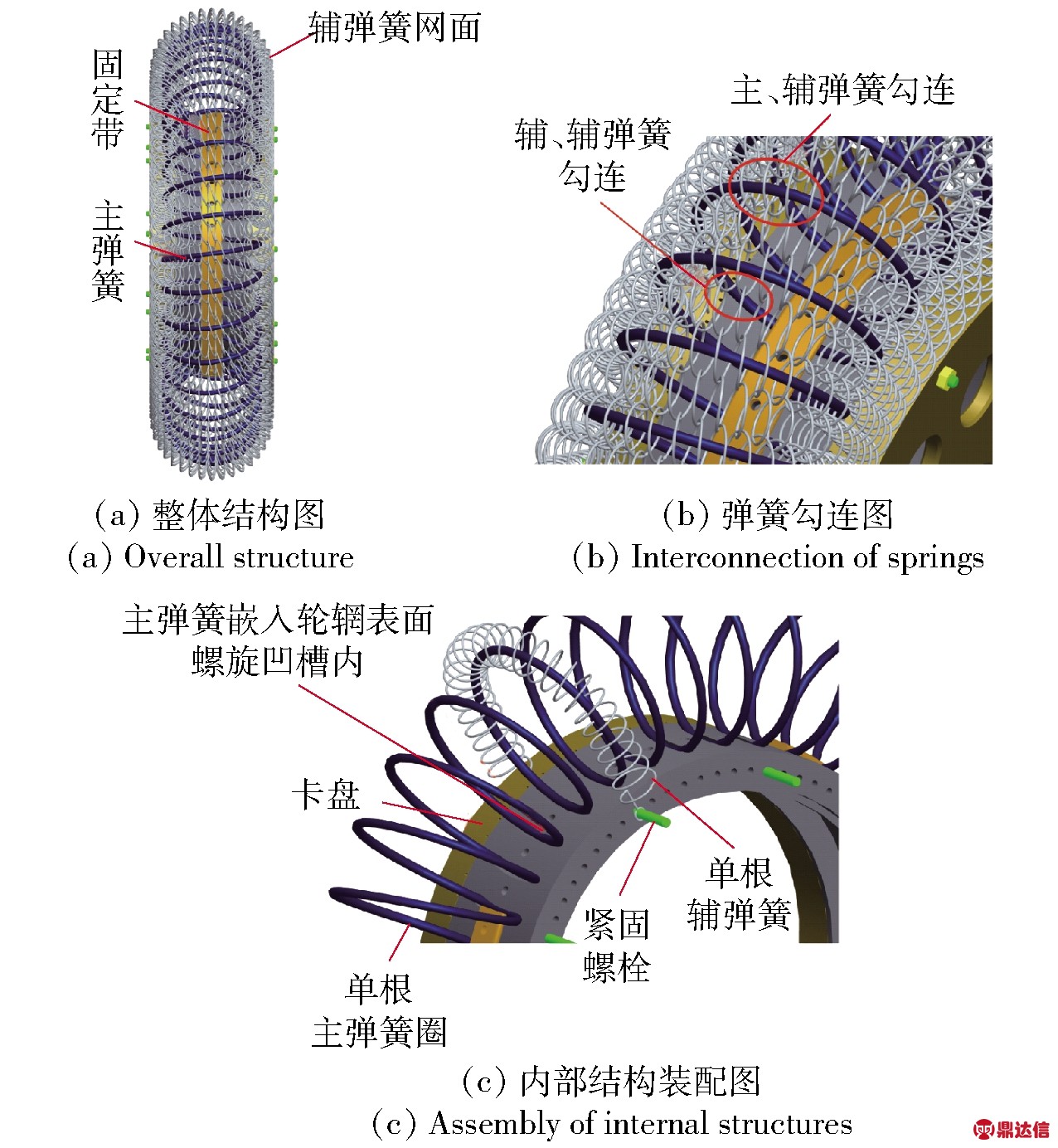
图2 金属车轮组成
Fig.2 Parts of all-metal wheel
1.2 接地状态分析
由于轮胎主弹簧由36根弹簧圈组成,与地面接触的簧圈与过轮心垂线之间的夹角决定了轮胎不同的初始受力状态,本文定义该角度为接地角α(0°≤α≤5°),如图3所示。

图3 接地角
Fig.3 Grounded angle
1.3 主、辅弹簧丝径设计
参照佳通轮胎(中国)制造商LT 235/70R16 104/101型充气橡胶轮胎制作试验样机,首先确定金属车轮的整体尺寸及载重要求,即车轮直径为735.4 mm,轮胎高度为164.5 mm,单胎载重为900 kg,进而设计主弹簧中径为150 mm,辅弹簧中径为30 mm.
主弹簧在承载中起主要支撑作用,其丝径决定了主弹簧的刚度大小,刚度越大,载重越大,但同时会导致车辆平顺性变差。
当接地角α=0°时,与地面接触的主弹簧圈将受到最大垂向力作用,此时将弹簧圈简化为一个规则的圆环,建立如图4所示的1/2受力模型。图4中:R为主弹簧圈半径,P为弹簧圈所受到的集中力,即轮胎总径向力的一半。
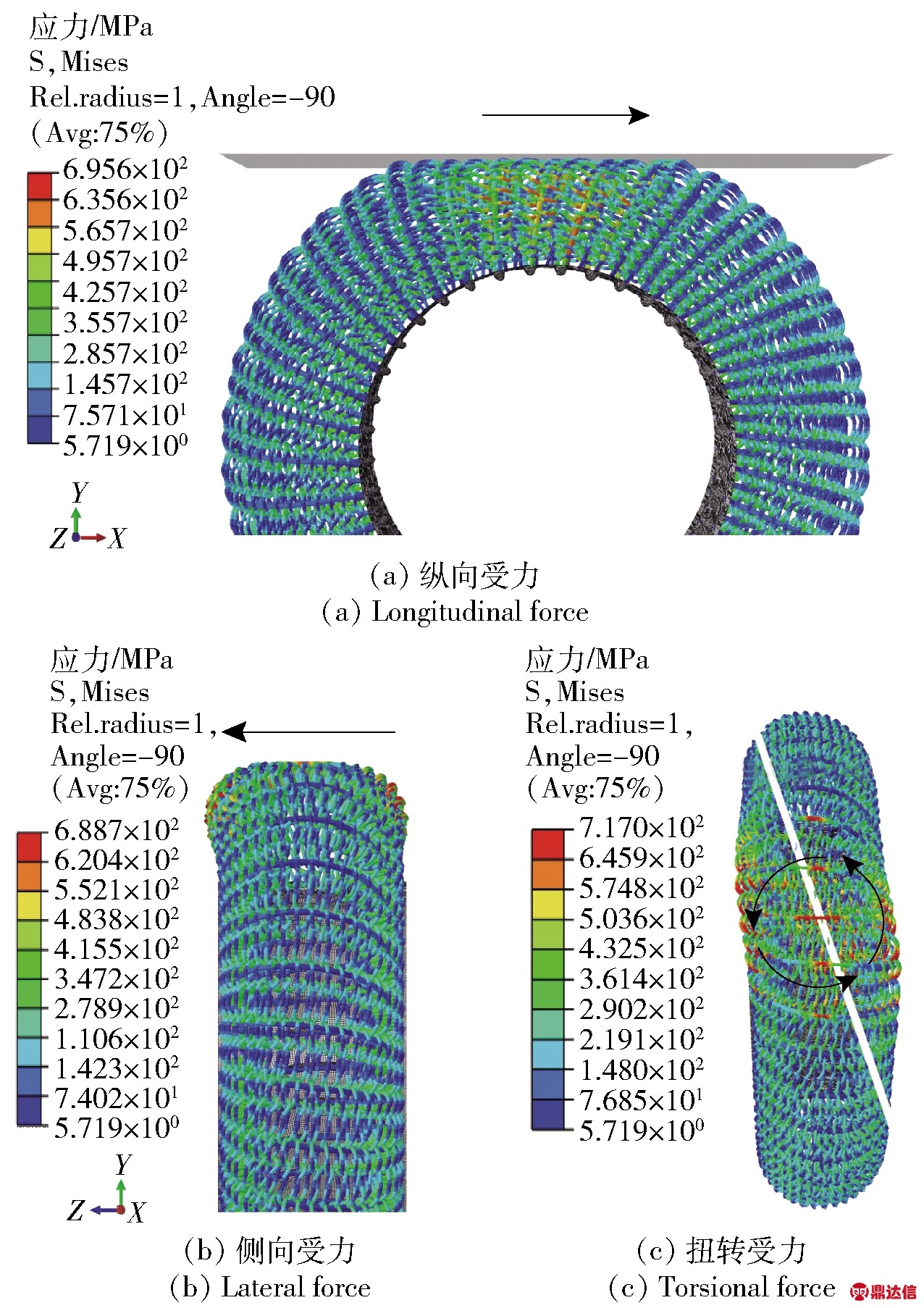
图4 主弹簧圈1/2受力模型
Fig.4 1/2 force model of main spring coil
此时危险截面处的压缩正应力为
σ1=P/(πr2)=4P/(πd2),
(1)
式中:d为主弹簧丝径;r为主弹簧圈簧丝的半径。
弯曲最大压应力为
σmax =M/ωn=PR/[πd3/32]=32PR/(πd3),
(2)
σ=σ1+σmax ,
(3)
式中:M为截面弯矩;ωn为抗弯截面系数;σ为截面总应力。
集中力P取额定载荷(8 820 N)的一半,根据选取的弹簧钢材料许用应力[σ]≥σ,求解得到许用丝径[d]≤d. 考虑实际中弹簧螺旋角、辅弹簧网面勾连及地面切向摩擦力的作用,弹簧圈会更易产生变形,故在求解得到的丝径值基础上给予一定裕值,取主弹簧丝径dm=8 mm.
辅弹簧线径决定了辅弹簧网面的刚度大小,但其刚度值要比主弹簧小的多。因此,为了保证由辅弹簧网面受力到主弹簧受力过程的平滑过渡,应尽量增加辅弹簧线径,以提高其刚度。但这无疑大大增加了辅弹簧与主弹簧的装配难度。因此,根据实际组装时的工程经验,确定辅弹簧丝径为da=4 mm.
2 力学特性分析
2.1 垂向刚度预测
为了便于预估轮胎刚度、简化理论建模过程,这里同样仅考虑主弹簧受力。
2.1.1 单根主弹簧承重
建立如图5所示的金属圆环受力模型。图5中, Pe为自由端水平载荷,φ为任意一截面与车轮垂直面之间的夹角,该截面处的轴向力和切向力分别为N和Q.
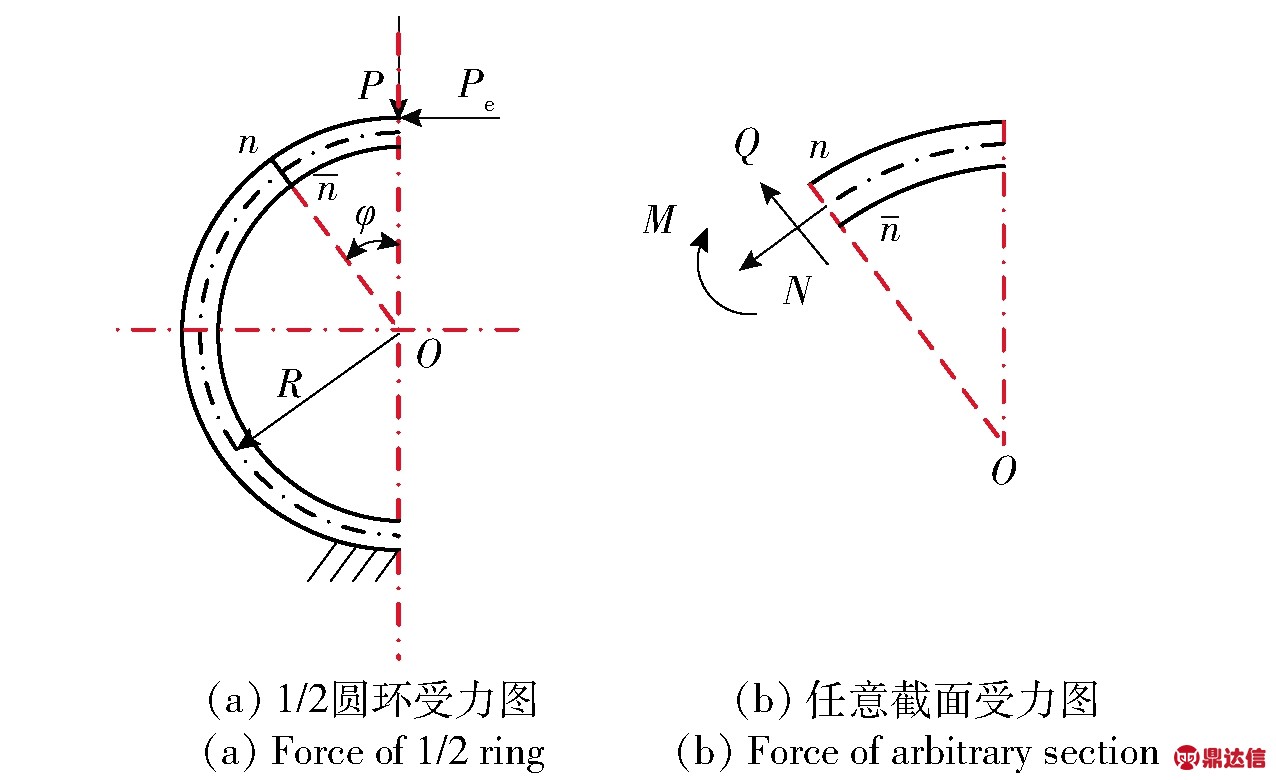
图5 金属环受力模型
Fig.5 Simplified stress model
则曲梁任一截面处的弯曲力矩为
M=PRsin φ+PeR(1-cos φ),
(4)
圆环在全长内的弯曲弹性位能为

(5)
式中:EI为抗弯刚度,表示为材料的弹性模量E与圆环横截面绕其中性轴惯性矩I的乘积。
由(5)式可得圆环的垂向变形量fy为
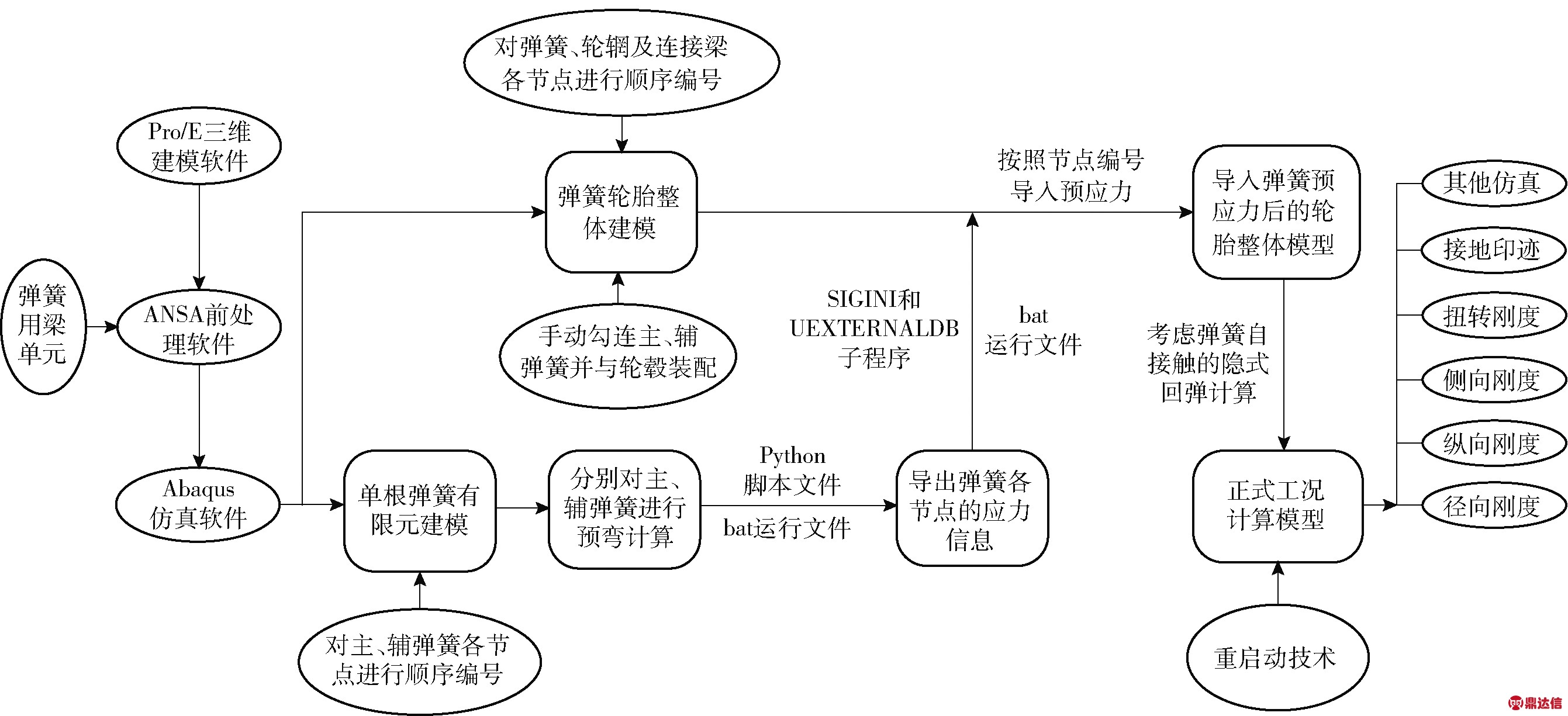
(6)
因此,单个圆环的垂向刚度C为
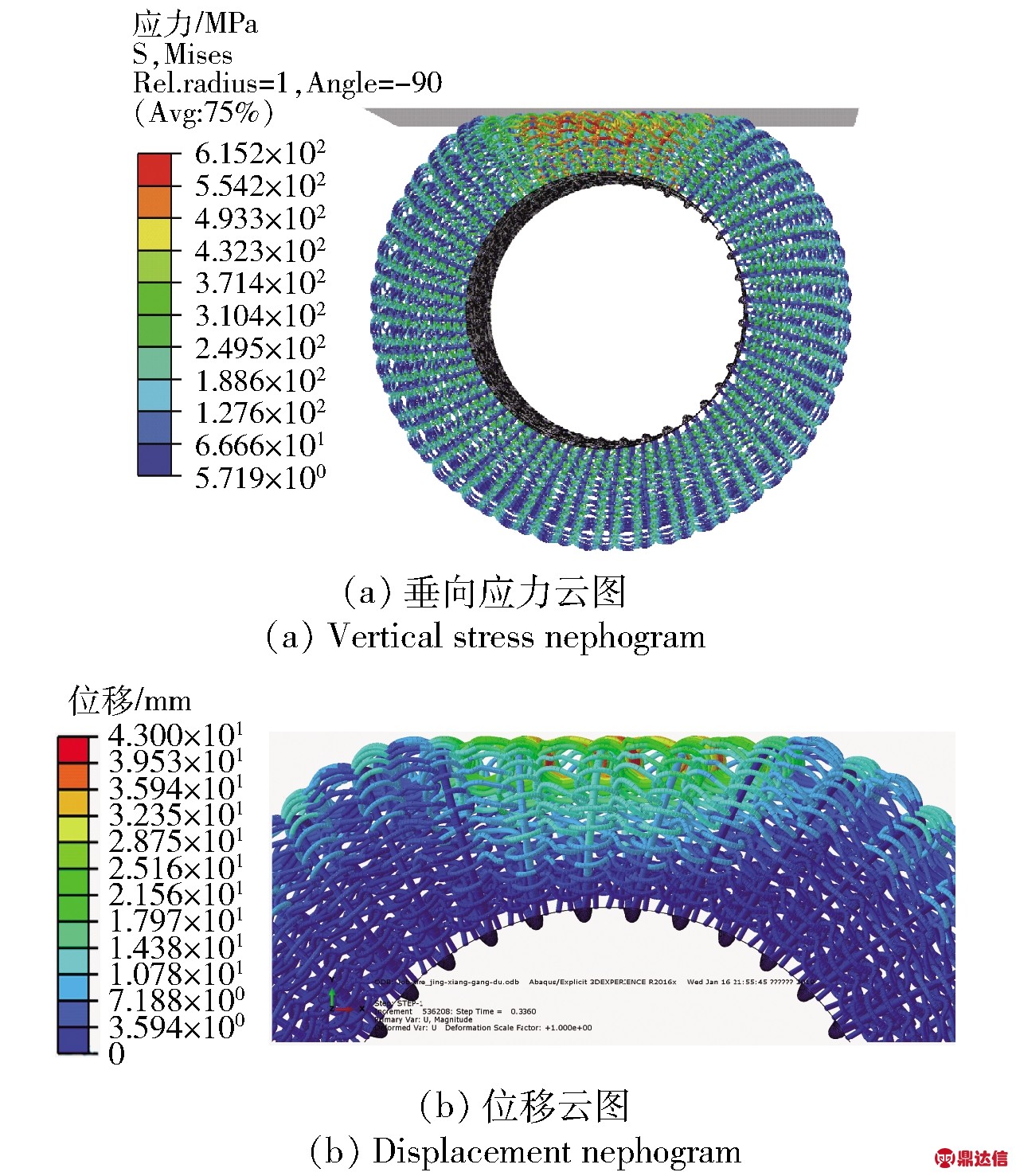
(7)
引入修正系数K(K>1)来消除螺旋角、辅弹簧网面刚度、弹簧圈受压扭转变形等带来的计算误差,得到主弹簧的垂向刚度为
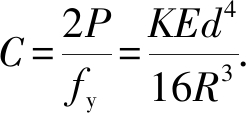
(8)
2.1.2 3根主弹簧承重
3根主弹簧圈承重时的受力简图如图6所示。图6中:β为相邻主弹簧圈之间的间距,β=10°;N1、N2和N3分别为产生变形的主弹簧圈标号;ΔL1、ΔL2和ΔL3分别为主弹簧圈产生的变形量;F为轮胎总的径向力。
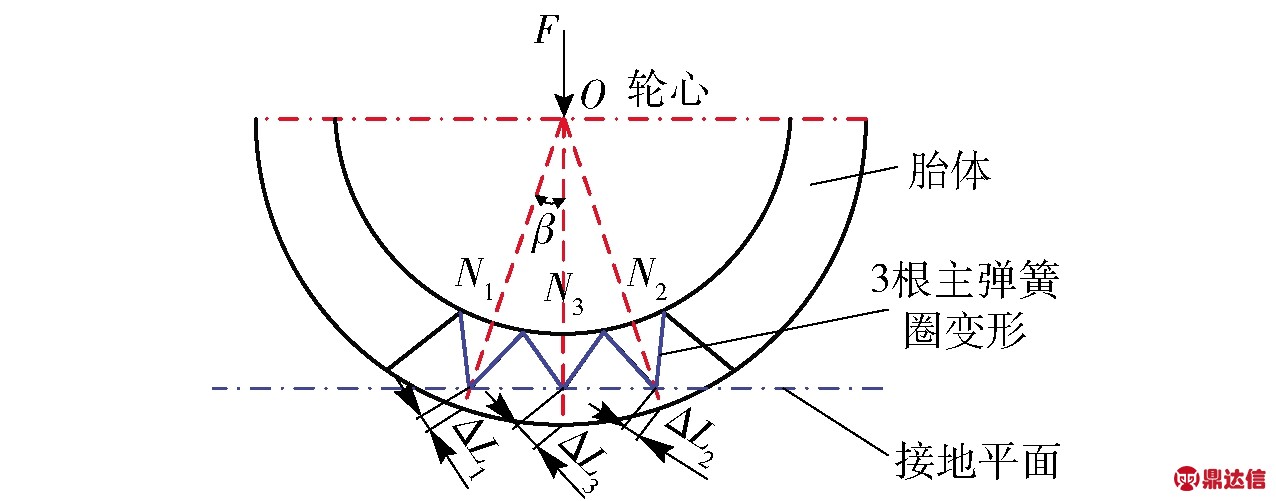
图6 3根主弹簧承重
Fig.6 Load-bearing of three main spring wires
根据3杆受力静平衡方程,可得
∑Fh=0,N1sin β-N2sin β=0,
(9)
∑Fv=0,N1cos β+N2cos β+N3=F,
(10)
式中:Fh和Fv分别表示投影到水平和垂直方向上的受力大小。
由弹簧圈关于y轴产生对称变形,可得变形协调方程为
(R-ΔL1)cos β=R-ΔL3.
(11)
将(8)式代入(11)式,可得

(12)
结合平衡方程(9)式和(10)式,可得

(13)
将相关结构参数E=207 GPa、d=8 mm、R=60 mm代入(13)式,得到垂向刚度的预测值为
2.2 垂向振动分析
实验室现有的3轴6×6无人车,底盘构成比较简单,没有悬挂系统、减速器等零部件,能直接反映路面通过车轮传递后对车体的振动情况,结合该无人车建立如图7所示的1/2车辆振动模型。图7中:kt和ct分别为轮胎刚度和阻尼,qf、qm和qr分别为前、中、后轮的路面激励,mv为整车质量。

图7 车辆1/2振动模型
Fig.7 1/2 vibration model of vehicle
车辆在行进过程中仅通过轮胎进行减振,包括车体、雷达等在内的整个车身均为轮上质量,因此可以得到分析车身垂直振动最简单的单质量系统模型,如图8所示。图8中:m、k和c分别为轮上质量、轮胎等效刚度和等效黏性阻尼比,q为路面不平度函数。
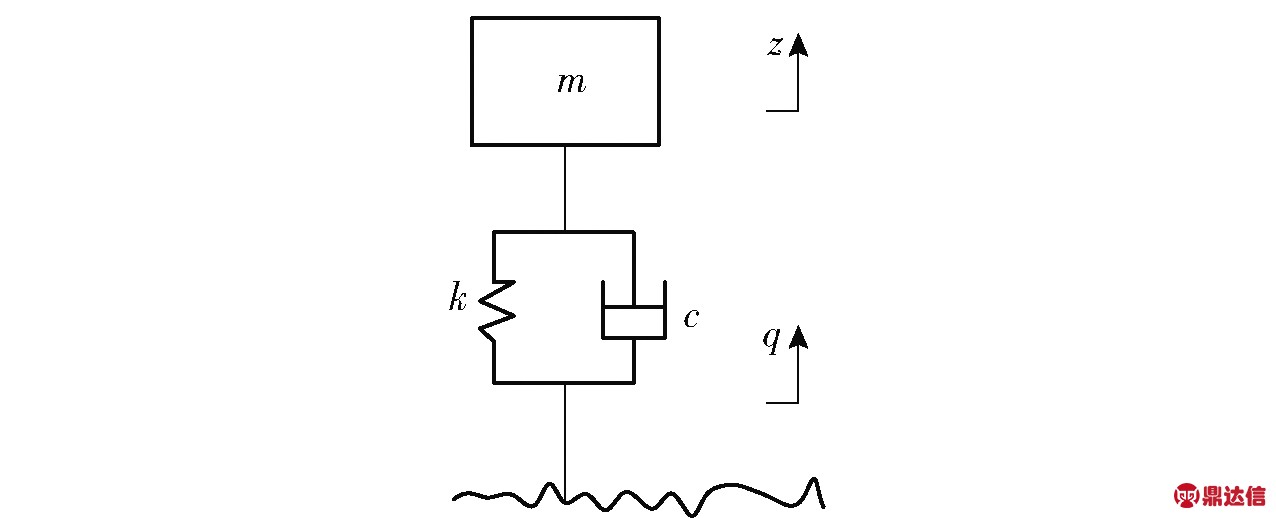
图8 单质量系统模型
Fig.8 Single mass system model
不考虑阻尼的影响,轮上共振的频率近似由(14)式计算:
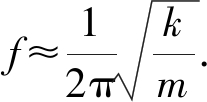
(14)
若要减小轮上振动程度,需要有效减小轮上振动的固有频率,由(14)式可知,可通过减小车轮的刚度或者增加轮上质量实现。
3 力学仿真研究
3.1 有限元建模与参数设置
建模过程中因主、辅弹簧接触部位较多,隐式计算收敛性较差,计算量非常巨大,因此将主、辅弹簧简化成梁元进行计算,这样既可以有效减少计算量又能保证计算精度。仿真实验的基本流程如图9所示[14-16]。
3.1.1 主、辅弹簧预弯计算
在Pro/E软件中分别建立主、辅弹簧模型,模型尺寸如图10和图11所示。再在ANSA软件中将模型抽取中线转换成梁单元。
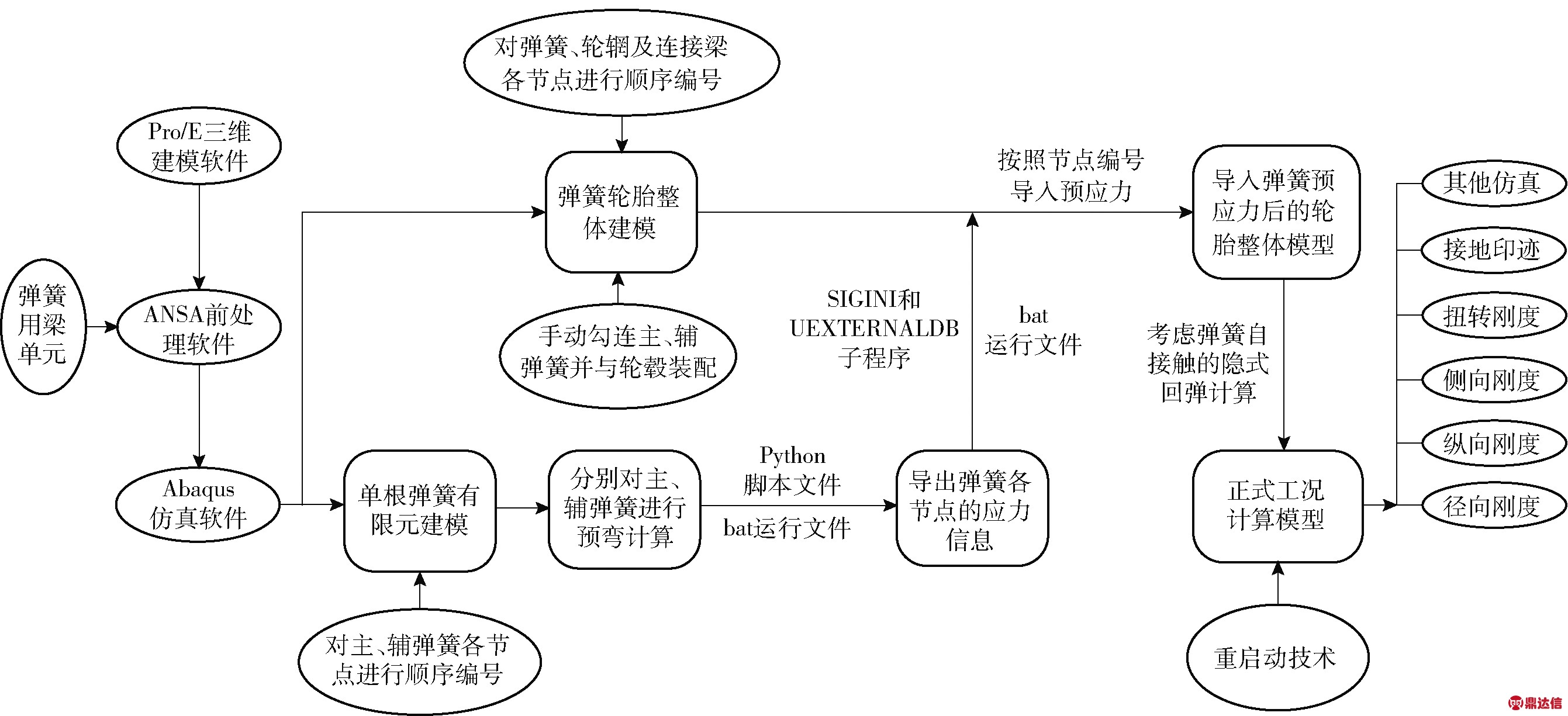
图9 仿真流程图
Fig.9 Modeling flow chart
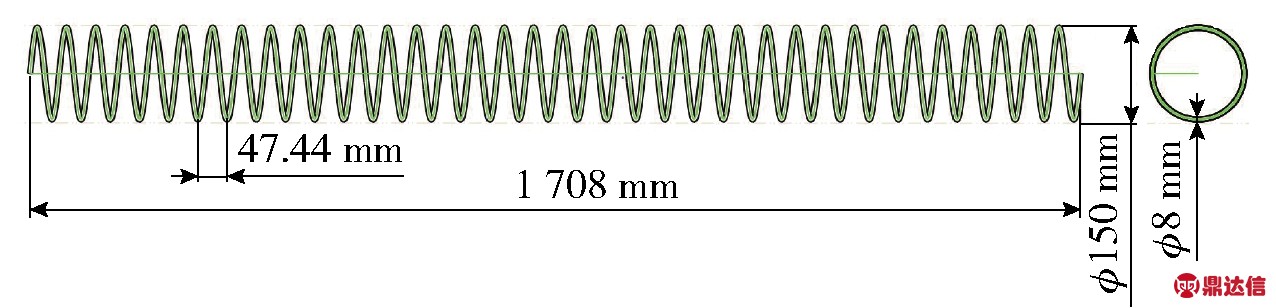
图10 主弹簧结构示意图
Fig.10 Structure diagram of main spring
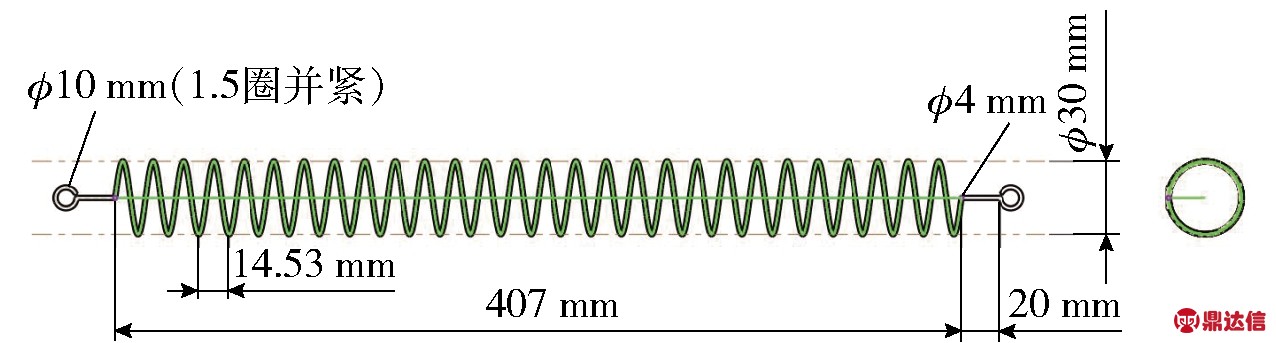
图11 辅弹簧结构示意图
Fig.11 Structure diagram of auxiliary spring
主、辅弹簧材料牌号为65Mn,参数如表1所示。
表1 材料特性参数
Tab.1 Material parameters
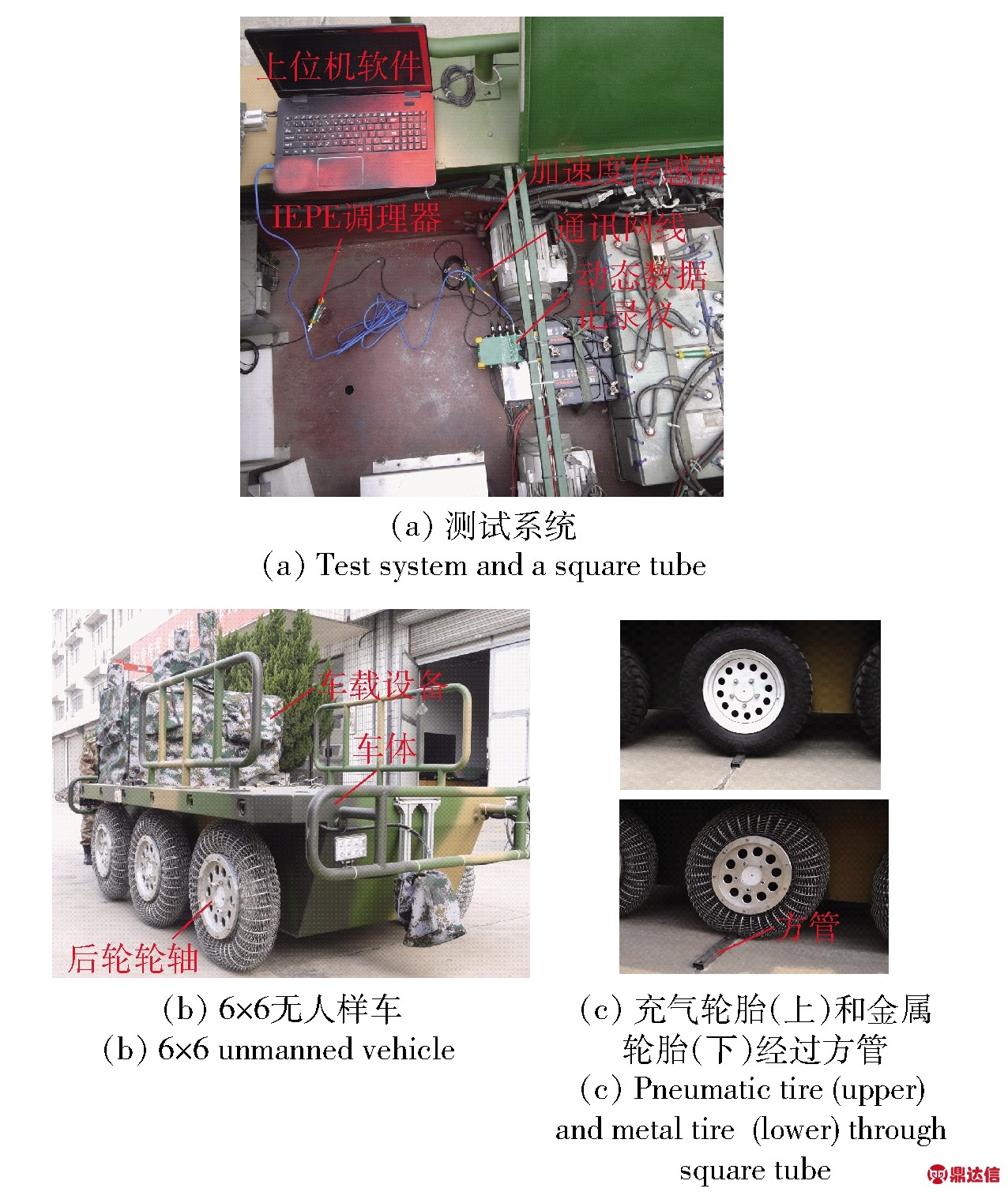
之后在Abaqus软件中,将主、辅弹簧弯曲成实际的安装状态,弯曲状态通过约束弹簧一端,在另一端施加角位移实现,其中主弹簧预弯角度为360°、辅弹簧约为270°,如图12所示。弹簧预弯计算得到的预弯应力将作为后续轮胎整体应力初始化的应力数据来源。

图12 预弯计算应力云图
Fig.12 Pre-bending stress nephogram
3.1.2 轮胎整体建模
整体建模时,为了简化计算提高分析效率,忽略图2中的卡盘、紧固螺旋和固定带等结构对轮胎刚度的影响,保留主弹簧、辅弹簧和轮辋。其中主弹簧1个、辅弹簧72个,同样先在Pro/E软件中建立三维模型,再在ANSA软件中将模型抽取中线转换成梁单元,轮辋采用刚体壳单元进行模拟,壳单元与主弹簧进行绑定连接。
在ANSA软件中通过Morphing Tools工具,采用移动单元节点的方法实现辅弹簧与主弹簧以及辅弹簧之间的相互勾连,确保模型不会产生相互干涉、穿透等,如图13所示。

图13 ANSA中无应力整胎模型
Fig.13 Stressless tire model in ANSA
3.1.3 应力初始化
为了更加准确地模拟实际,需要将初始应力导入建好的轮胎模型中。根据3.1.1节中的预弯计算得到的主、辅弹簧应力数据,通过编写SIGINI和UEXTERNALDB子程序实现应力初始化,前者主要用于弹簧轮胎主、辅弹簧单元截面点的应力初始化,后者用于Abaqus子程序与外部数据进行通讯。轮胎施加预应力后的应力分布图如图14所示,此时最大应力与辅弹簧预弯时的应力值相同。
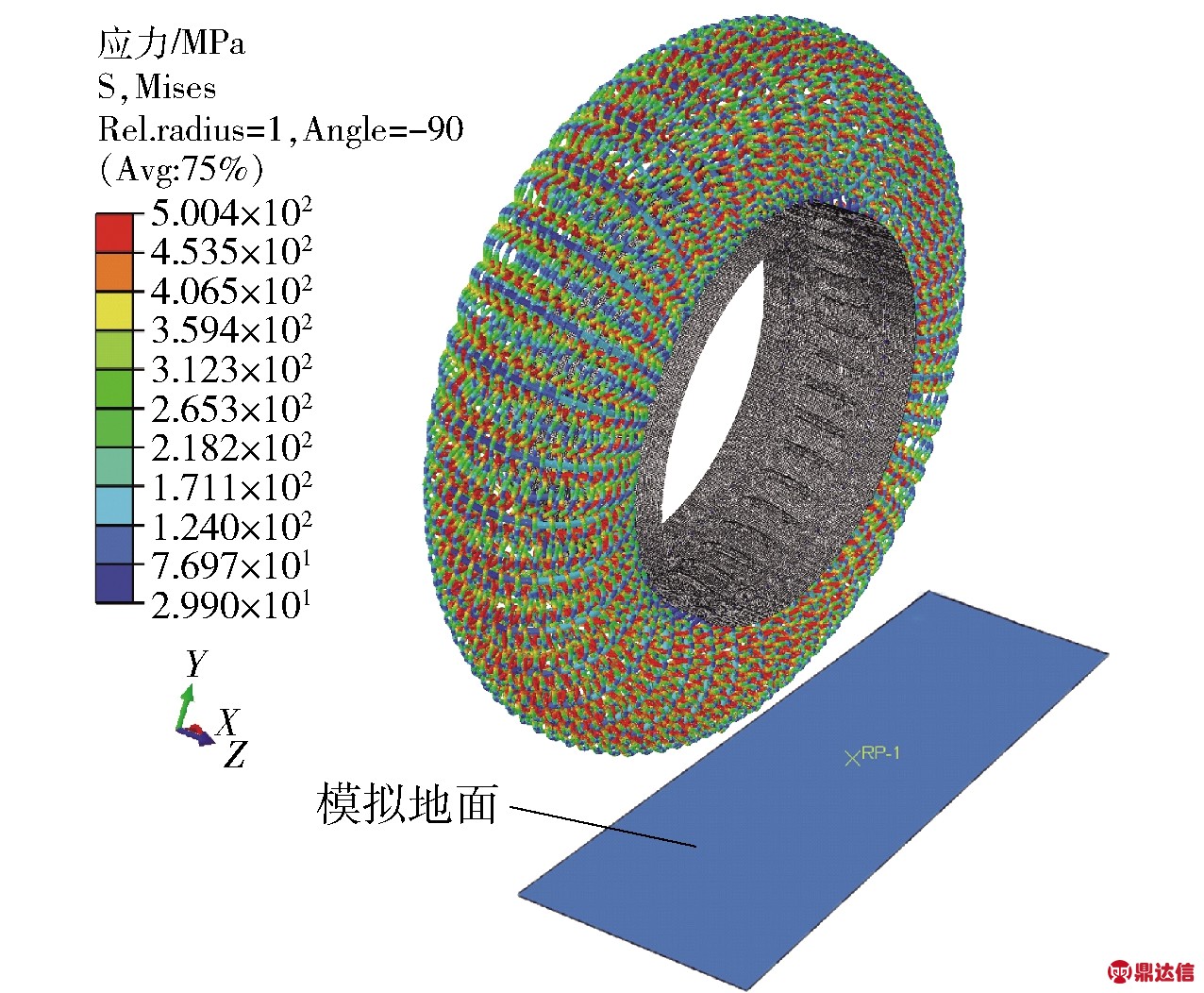
图14 加载预应力
Fig.14 Loading prestress
3.1.4 回弹计算
通过隐式回弹计算,得到轮胎在初始应力场作用下发生回弹、接触的真实应力状态,可知总体应力值变小,如图15所示,此状态为后续其他工况的初始计算状态。
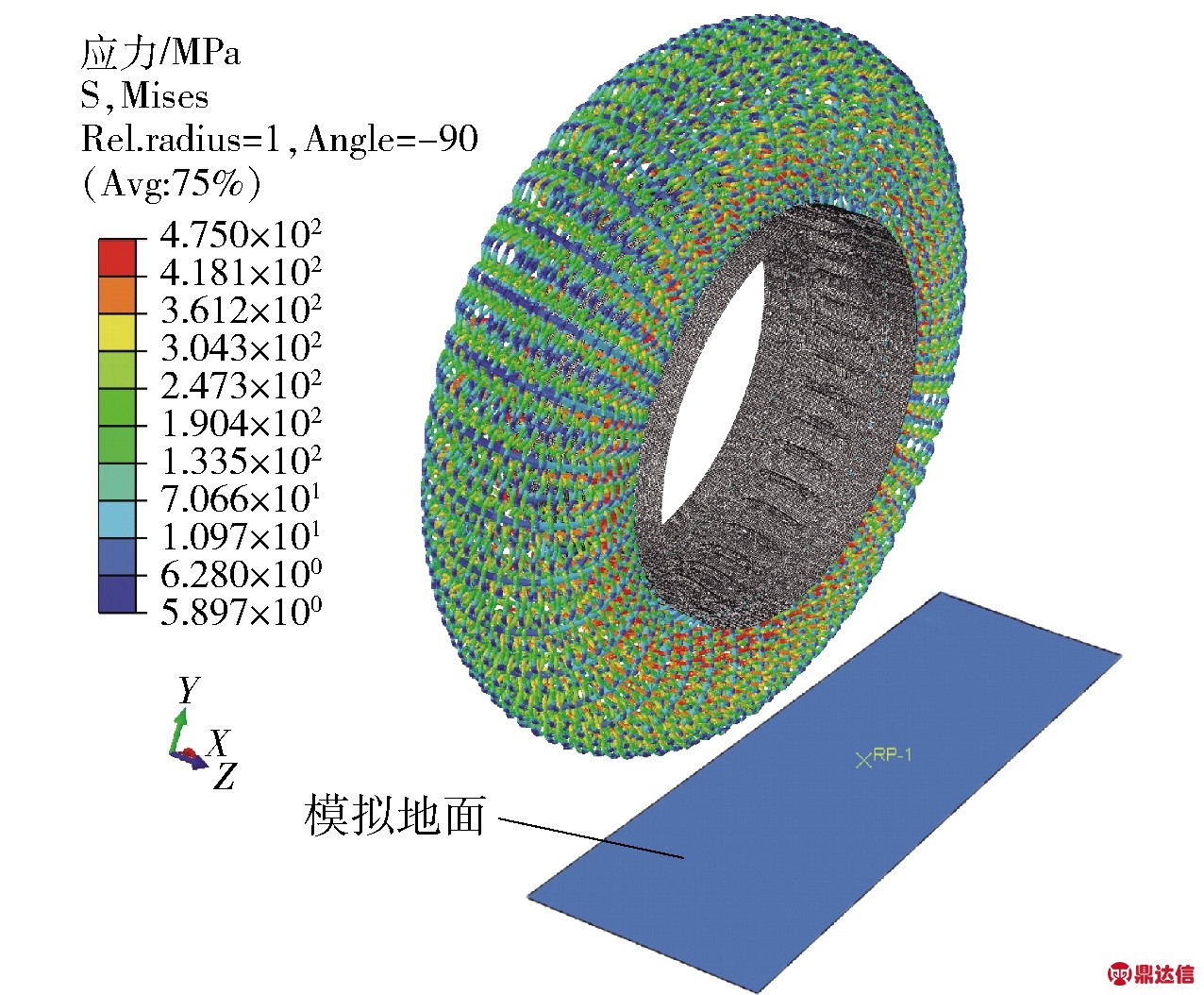
图15 隐式回弹计算
Fig.15 Implicit rebound calculation
3.1.5 各部分接触的定义
模型中的接触主要包括主弹簧、辅弹簧、轮辋、压板之间的相互接触,以及部分自接触。其中,模拟地面定义为刚体,地面与弹簧之间定义为通用接触(general contact)类型,为避免二者过度滑移,摩擦系数设置为0.3;轮辋与主弹簧之间采用绑定约束tie处理;主弹簧与辅弹簧、辅弹簧与辅弹簧以及弹簧丝间的自接触均为梁- 梁接触,同样采用通用接触,并考虑梁元截面的偏置接触,参照钢材之间的接触情况,自接触摩擦系数设置为0.1.
3.2 刚度仿真分析
轮胎垂向、纵向、侧向和扭转刚度的仿真工况如图16(a)~图16(d)所示,箭头所指方向为路面移动方向,在轮心O处施加全约束边界条件[14]。
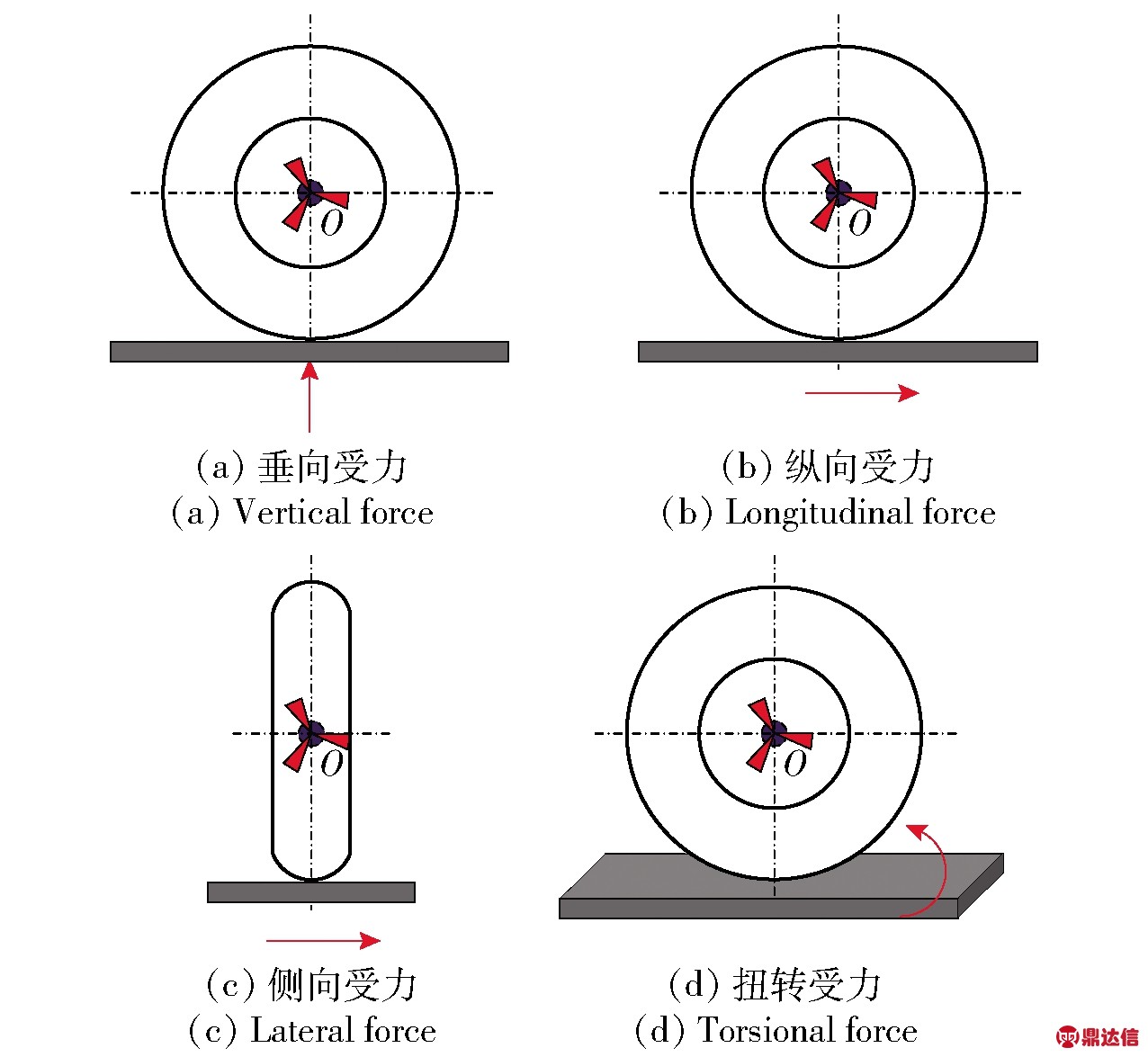
图16 各向刚度仿真工况
Fig.16 Simulation conditions of each directional stiffness
各向刚度分别体现了轮胎不同的力学特性[17],垂向刚度决定了轮胎的减振和稳定特性;纵向刚度直接影响轮胎的纵向振动、牵引及制动能力;侧向刚度常用于判定轮胎的侧偏特性,对车辆的操纵稳定性有较大影响[18];扭转刚度反映了轮胎的回正特性,影响车辆的转向能力。
3.2.1 垂向刚度仿真
在轮胎预应力状态下,固定轮毂中心耦合点,沿轮胎径向进行位移加载[16],最大压缩量取43 mm,应力和位移云图如图17所示。
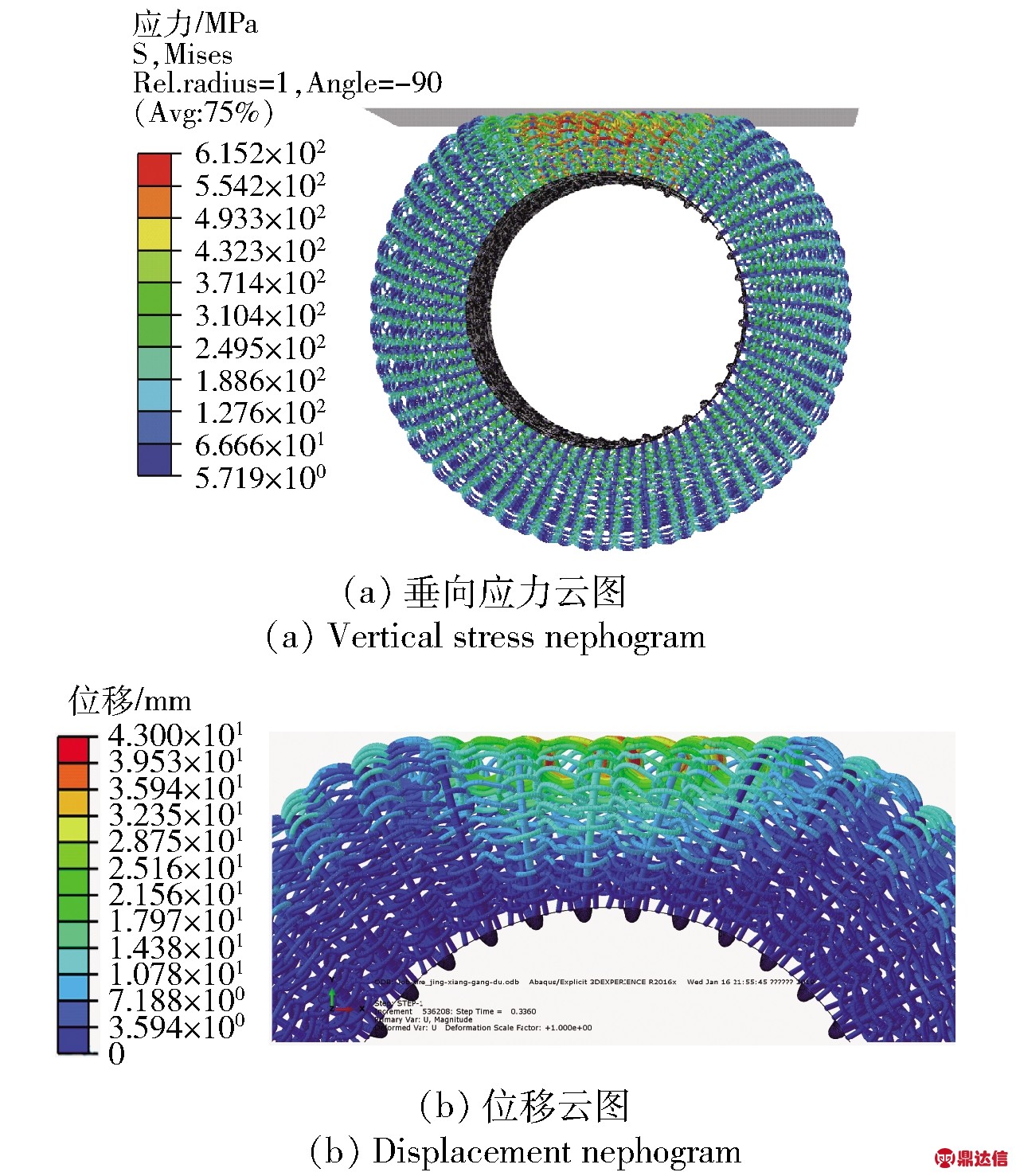
图17 垂向应力和位移云图
Fig.17 Vertical stress and displacement nephograms
由图17(a)可知,最大等效应力为615 MPa,数值小于表1中材料的屈服极限,满足强度要求;由图17(b)可知,当最大位移为43 mm时有3根主弹簧产生变形。对比图18中不同接地角下的轮胎刚度曲线可知,接地角对垂向刚度的影响不大,但会使刚度曲线产生不同程度的偏移。

图18 不同接地角下垂向刚度曲线
Fig.18 Vertical stiffness curves at different grounded angles
3.2.2 其他各向刚度仿真
在垂向刚度仿真的基础上做轮胎其他刚度仿真,即首先对轮胎做垂向压缩(取满载工况,垂向载荷为8 820 N),然后对地面施加不同方向的位移载荷,研究轮胎受各向力时是否满足设计要求[19]。得到的各向应力云图如图19所示,纵向、侧向和扭转时的最大应力分别为695 MPa、688 MPa和717 MPa,满足强度要求。
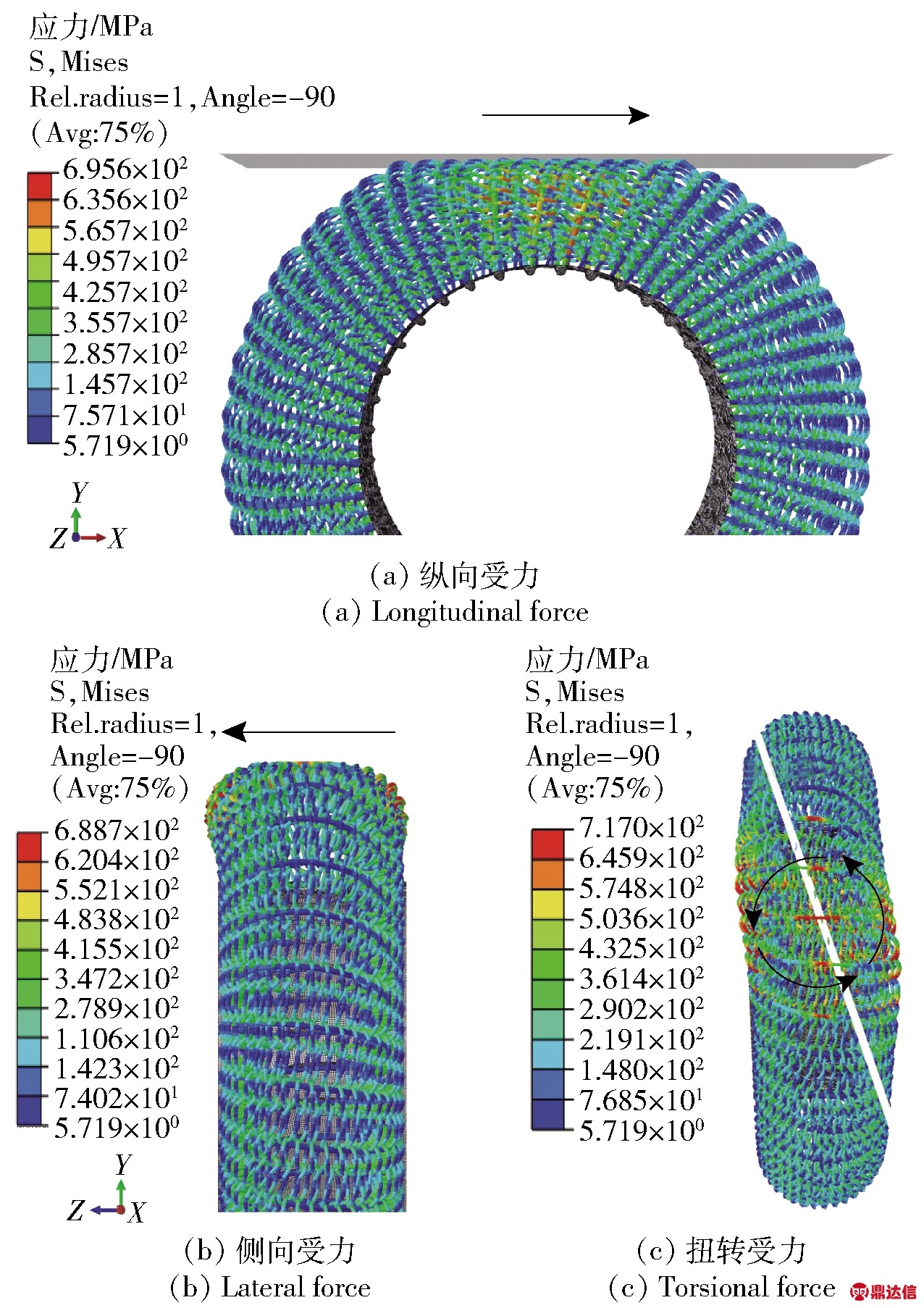
图19 各向应力云图
Fig.19 Other directional stress nephograms
对如图20(a)和图20(b)中的曲线进行最小二乘拟合,得到纵向刚度和侧向刚度分别为kz=104 N/mm,kce=146 N/mm. 根据图20(c)所示曲线可知,当扭转角较小时扭转刚度较大,随着扭转角变大,扭转刚度变小,OA段和AB段的扭转刚度分别为knA=3.27×106 N·mm/°,knB=5.77×105 N·mm/°.
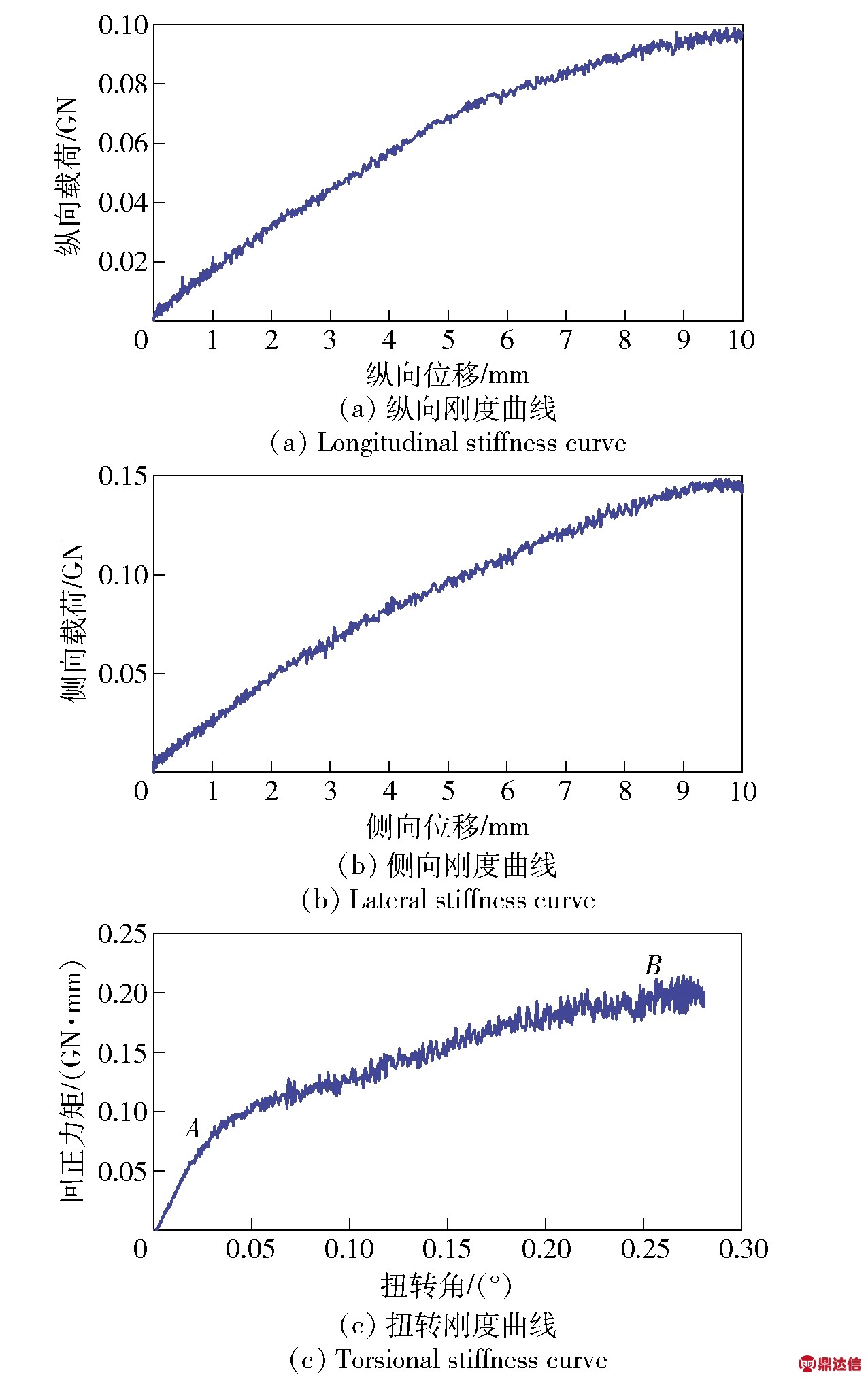
图20 其他各向刚度曲线
Fig.20 Other directional stiffness curves
4 垂向刚度试验
通过图21所示材料拉压试验机测试轮胎的垂向刚度,使用固定工装将轮胎底部悬空放置,通过控制试验机压头压缩胎体,模拟轮胎安装在实车上时与地面间的相互作用。
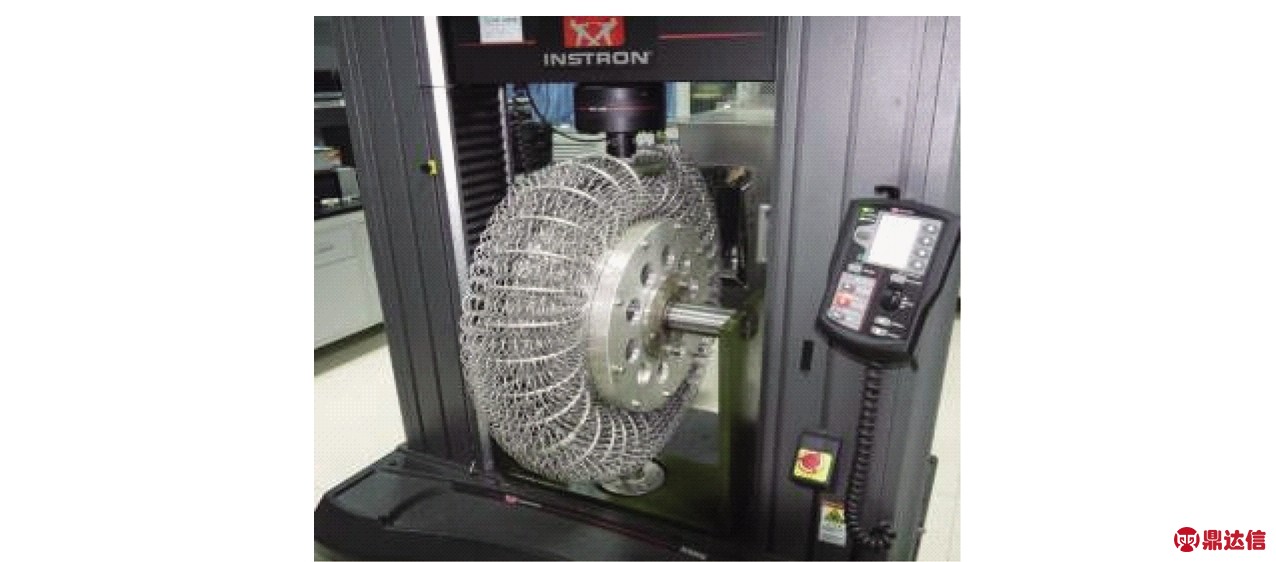
图21 垂向刚度试验台架
Fig.21 Test bench for vertical stiffness
试验中采用两种不同尺寸和形状的压板,如图22(a)所示的圆形压板和如图22(b)所示的长矩形压板,分别对应2.1节中轮胎单根和多根主弹簧受力时的情况。
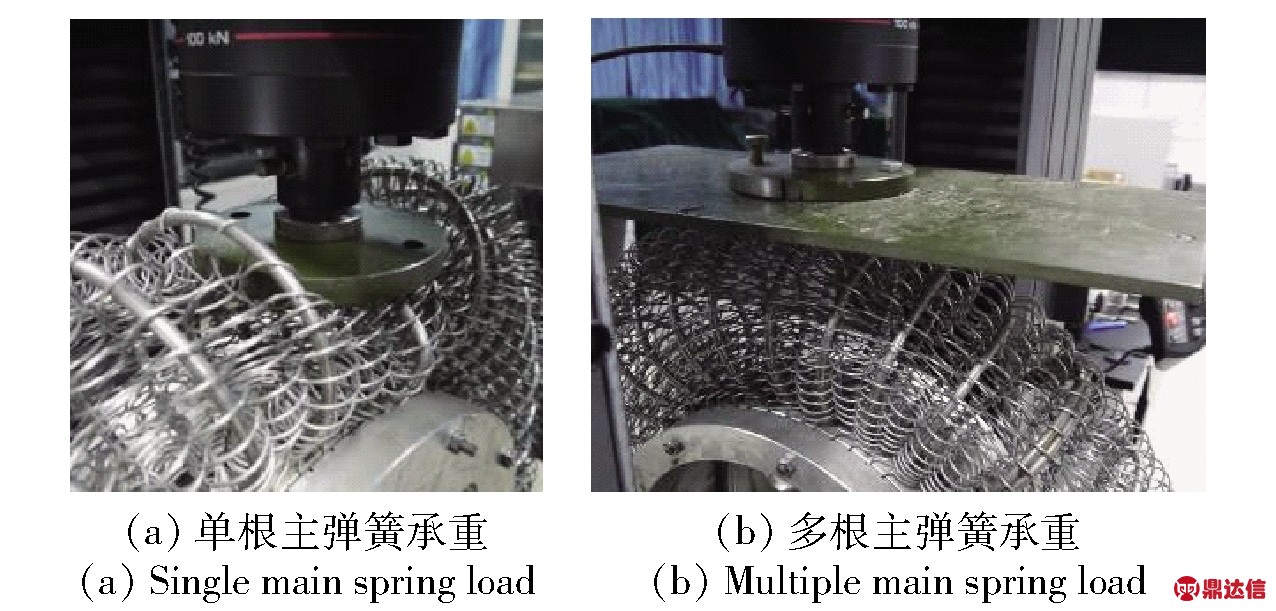
图22 轮胎垂向压板试验
Fig.22 Vertical plate loading test of tire
4.1 单根主弹簧受力分析
单根主弹簧受压可以模拟轮胎受到路面凸台等障碍、产生包覆内吞时的的受力情况。此时得到的轮胎垂向刚度曲线如图23所示,由图23可知:OA段曲线比较平直,此时仅辅弹簧网面受压变形,表明其刚度值很小;AB段载荷值逐渐增加,即主弹簧开始承重,但由于辅弹簧网面张紧力及弹簧圈之间摩擦力的作用,曲线产生了非线性变化;BB′段曲线呈现为线性,此时辅弹簧与主弹簧紧密贴合,主要产生线弹性变形,是轮胎主要的受力范围;B′之后轮胎刚度变小,开始产生塑性变形。
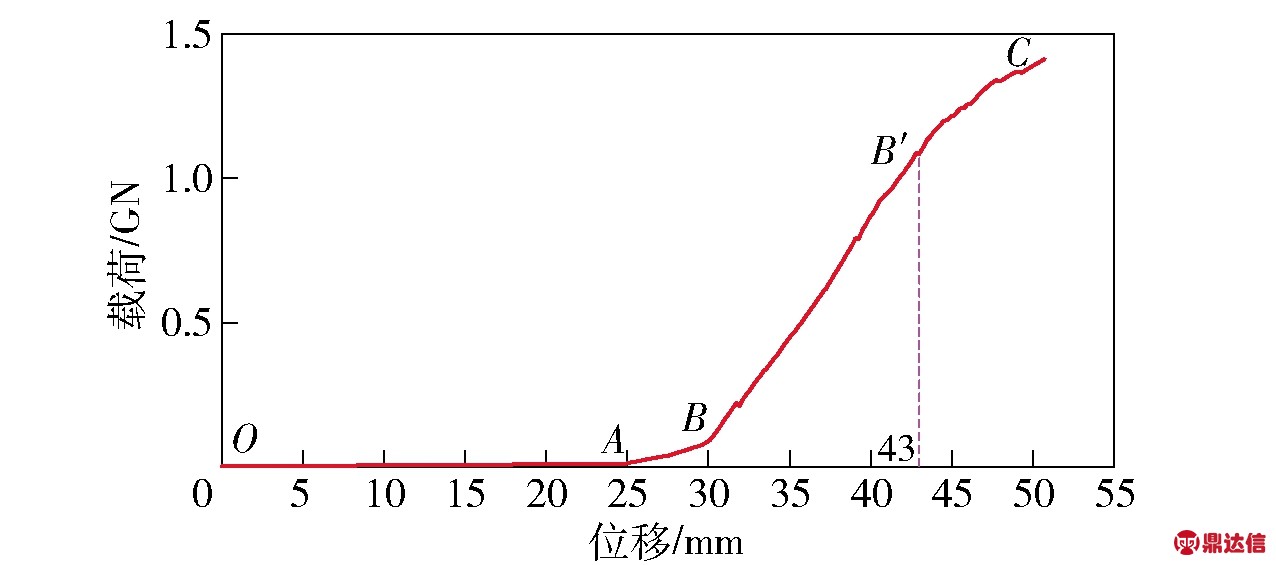
图23 单主弹簧承重时的垂向刚度曲线
Fig.23 Vertical stiffness curve for load-bearing of a single main spring
由上述分析可知:该工况下辅弹簧网面变形范围为25 mm、载重130 N,承重能力较弱;胎体的线弹性变形(AB′)范围为43 mm、载重11 180 N(>8 820 N),是轮胎主要承载范围,此时求解线性段(BB′)的斜率作为轮胎垂向刚度大小,得到kc1=777 N/mm.
4.2 多根主弹簧受力分析
多根主弹簧承重是弹簧轮胎的主要使用工况,此时变形和刚度大小决定了轮胎的承载能力和减振性能。施加垂向位移载荷分别为21.0 mm、25.8 mm、28.1 mm、43.0 mm、47.7 mm、51.4 mm和56.0 mm,通过反复加载试验并做分组对比分析,测试轮胎的弹性变形范围。由于轮胎最外层辅弹簧网面的刚度较小,使得刚度曲线在前20 mm位移范围内的载荷值很小(如图23中OA段),在分组作图时将曲线3~曲线7的横坐标20 mm作为坐标原点,得到图24所示不同位移载荷下的轮胎垂向刚度曲线。
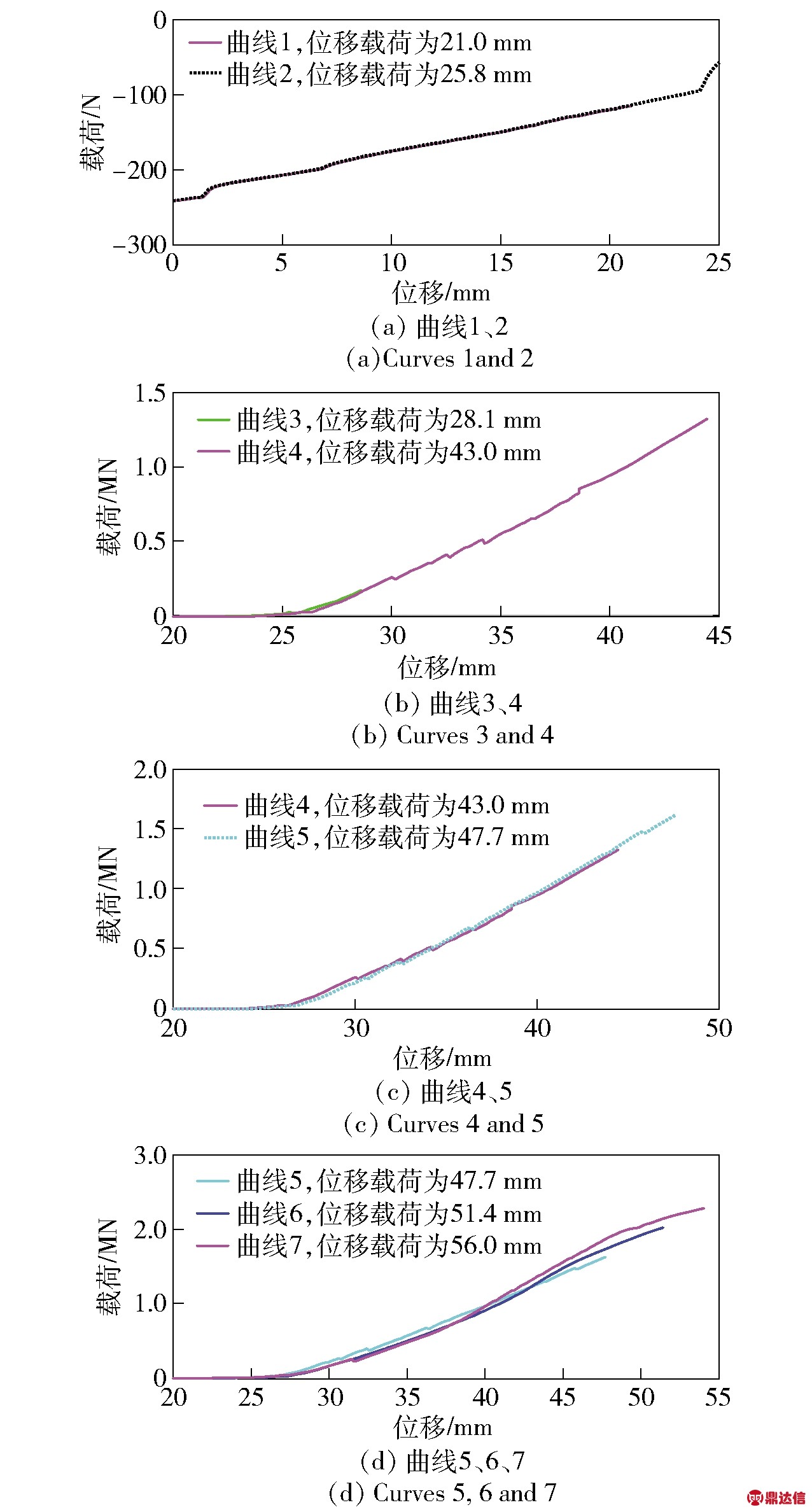
图24 多主弹簧承重时的垂向刚度曲线
Fig.24 Vertical stiffness curves for load-bearing multiple main springs
由图24可知:曲线1~曲线5基本重合,表明轮胎在前4次加载中均属弹性变形;第5次加载使弹簧产生了残余变形和残余应力,使曲线5~曲线7不再重合,斜率变大,即刚度变大。因此,轮胎的弹性变形范围要大于或等于曲线4的变形范围,此时最大垂向位移为43 mm,载荷为12 300 N. 同样求解曲线4线性段斜率作为该工况下轮胎的垂向刚度,得到kc2=827.6 N/mm,其数值要略大于理论值kc,原因在于简化的理论预测模型没有考虑主弹簧螺旋角、辅弹簧网面以及弹簧圈扭转变形等因素的影响。
由图25可知,垂向刚度的仿真与试验结果基本一致,初步证明了有限元模型和仿真过程的准确性,但由于仿真时为满足收敛条件,设置的计算增量步较多,导致仿真曲线不如试验曲线光滑。使用最小二乘法拟合仿真曲线的线性段,得到垂向刚度的仿真值kc3=851 N/mm,均大于理论值kc和实验值kc2,原因在于仿真中使用有限多个梁单元来建立弹簧模型,相连两个梁单元之间不可避免地存在一个钝角,导致弹簧的刚度变大。
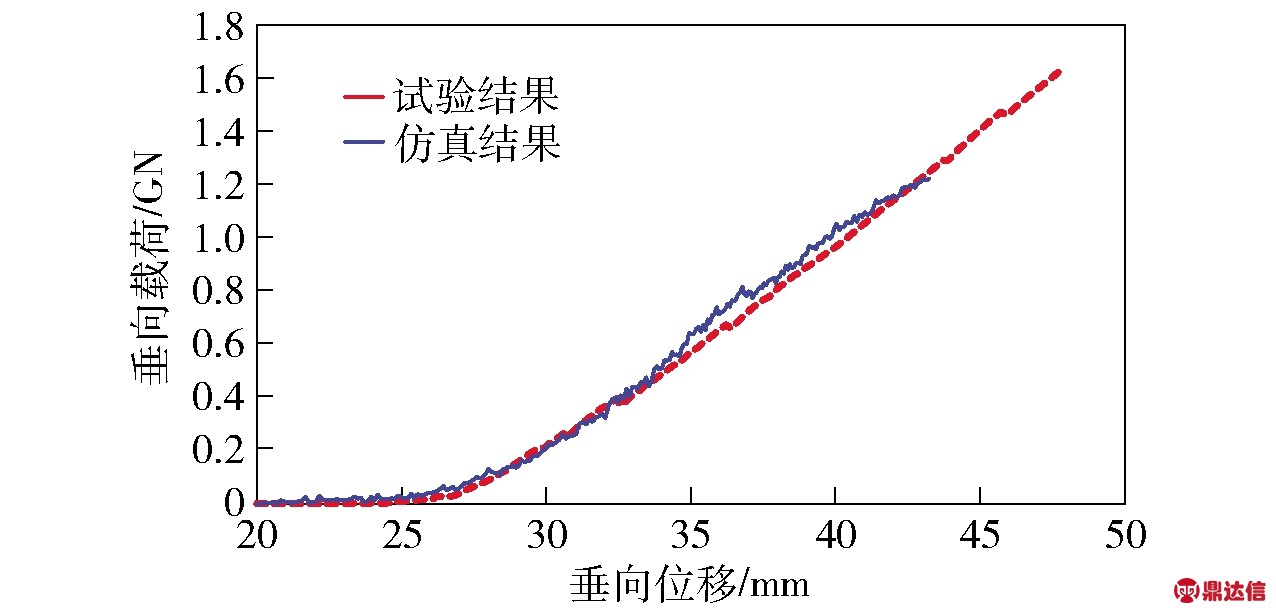
图25 垂向刚度仿真与试验曲线
Fig.25 Simulated and test vertical stiffness curves
5 垂向振动试验
搭建如图26(a)所示的测试系统进行车辆平顺性试验,加速度传感器固定放置在车体内部、车轮轮轴正上方,以准确采集轮胎的振动情况。测试中使用的6×6无人车及行驶路面如图26(b)所示,并在路面上设置尺寸为50 mm×25 mm的方管,以分别测试金属轮胎和充气轮胎受到冲击载荷时的振动情况,如图26(c)所示。
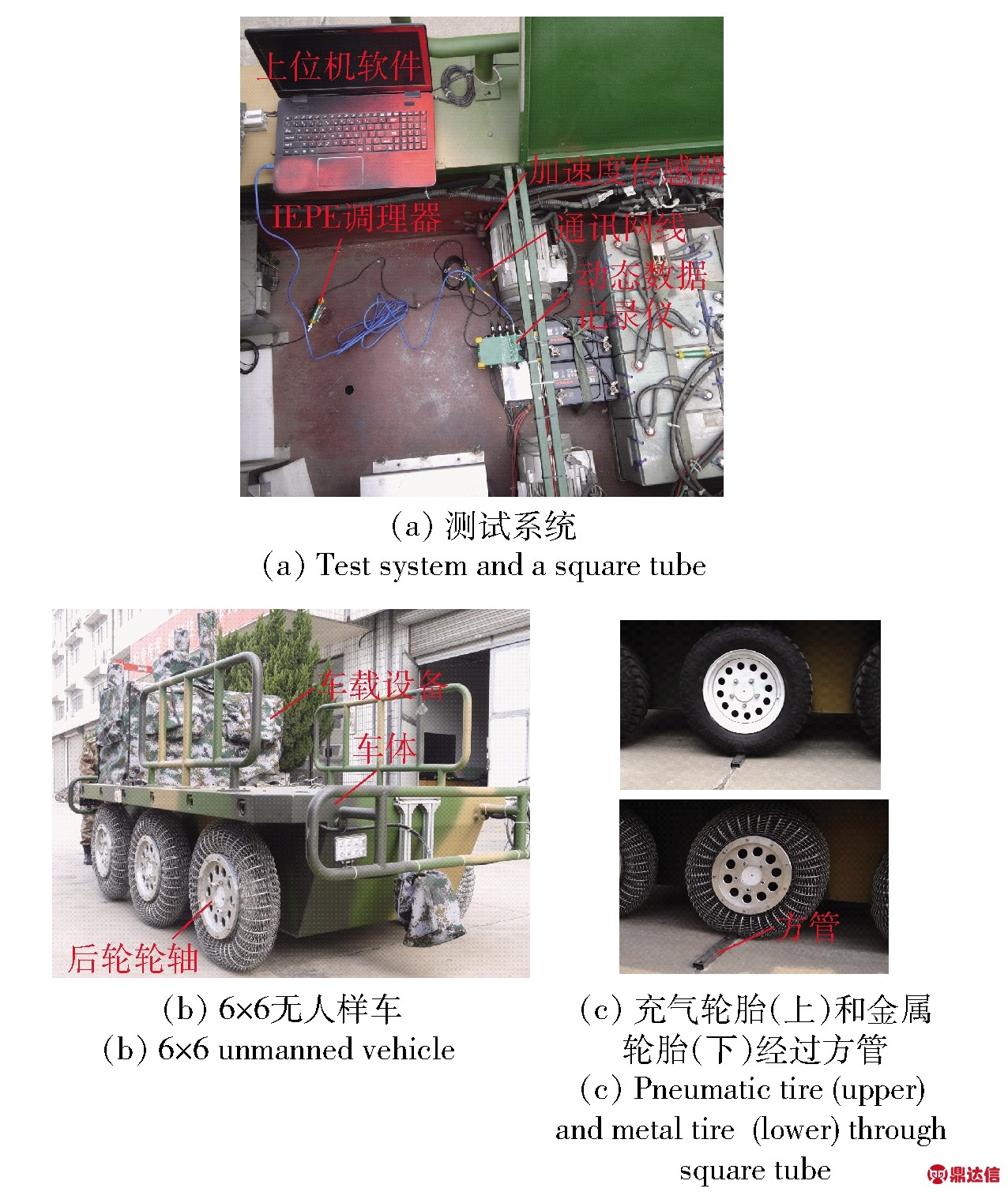
图26 平顺特性测试
Fig.26 Test of ride comfort
整体测试过程为:加速度传感器采集振动信号,经调理器调制放大后传输至数据记录仪,通过网线实时传输到笔记本电脑进行存储,最后对保存数据进行处理和分析,得到车辆不同车速、车体不同位置处的加速度信号时域曲线,如图27所示。
根据我国国家标准GB/T 4970—2009 汽车平顺性试验方法[20]中的相关内容,本文通过求算加权加速度均方根值的大小定量分析各工况下车辆的振动情况,均方根值越大,表示平顺性越差,具体求解过程如(15)式:

(15)
式中:aw为轮胎加速度均方根值;Ga(f)为功率谱密度函数,可通过频谱分析加速度时间历程获得;W(f)为频率加权函数。进而得到各工况下充气轮胎和金属轮胎的均方根如表2和表3所示。
表2 充气轮胎加权加速度均方根值
Tab.2 Root mean square value of weighted acceleration of pneumatic tire m/s2
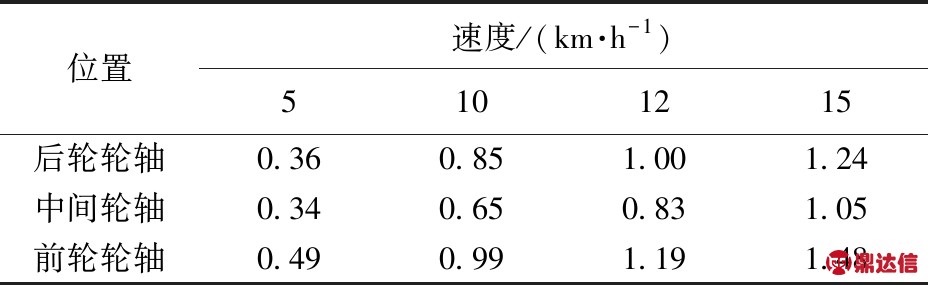
表3 金属轮胎加权加速度均方根值
Tab.3 Root mean square value of weighted acceleration of metal tire m/s2
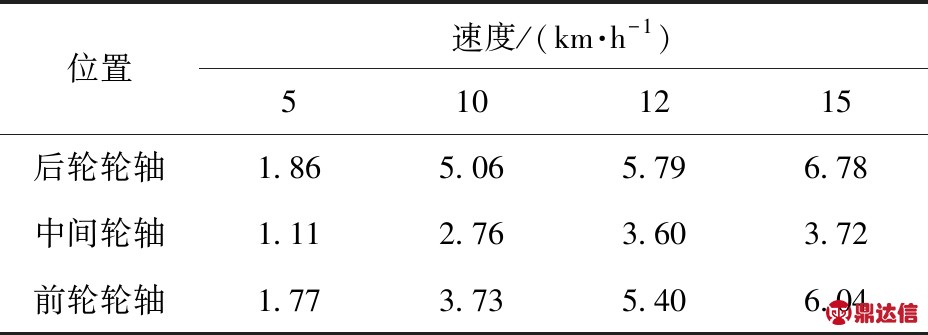
由表2和表3可知,总体来看,两种类型轮胎的平顺性均随车速的增加而变差,且均在中间位置处最好。对比来看,充气轮胎的平顺性要优于金属轮胎,但结合试验中实际观察到的现象发现,当车辆前轮通过方管时,由于充气轮胎弹性大,使车辆跃起一定高度,而金属轮胎的胎体网面则会产生较大变形,将方管包覆在内,使得金属轮胎的抓地特性要优于充气轮胎。

图27 加速度时域信号曲线
Fig.27 Acceleration signal curve in time domain
6 结论
本文通过对一种新型全金属网面车轮开展结构设计、力学分析、有限元建模、压板试验及平顺性试验,得到以下主要结论:
1)该全金属网面轮胎的垂向刚度主要受主弹簧的弹簧圈半径和丝径的影响,其尺寸值越大,垂向刚度越大,而辅弹簧的尺寸及网面胎体的接地状态对垂向刚度的影响较小。
2)单根主弹簧的承载力要小于多根主弹簧的承载力,但两种工况均能满足轮胎垂向上的承载要求。
3)仿真结果表明,当轮胎受到多向力作用时,胎体的最大应力值均能够满足强度要求。
4)轮胎的垂向振动主要受胎体质量和垂向刚度的影响,为提高安装金属轮胎车辆的平顺性,需要通过改变主、辅弹簧的中径、丝径等参数,或在胎体表面覆胶等方式来实现。