摘 要:为探究轴压作用下双金属复合海底管道的组合作用与承载性能,对双金属复合海底管道进行了试验研究和理论分析。开展了不锈钢衬管材料性能试验,对比了国际主流不锈钢本构关系模型和试验结果。利用ABAQUS建立了精细化的双金属复合管道轴压试验有限元模型,系统研究了关键参数如复合工艺产生的环向复合应力、钢管初始缺陷幅值等对双金属复合管在轴压作用下力学性能的影响规律。通过对比已有轴压双金属复合管道试验结果,验证有限元模型。基于验证的有限元模型,对轴压作用下双金属复合管道的组合作用以及径厚比和材料强度对承载力的影响进行了分析。结果表明双金属复合管道的轴压极限承载力主要取决于基管的截面屈服荷载,并随着管径和材料强度的提高而增大。并依据分析结果对双金属复合海底管道的设计提出建议。
关键词:双金属复合管;轴压;组合作用;海底管道;承载性能;径厚比;材料强度
近年来,随着现代社会对能源的需求量越来越大,海洋油气资源也不断向着深海和海洋环境更加恶劣的海域进行勘探和开发。据统计,1986~2016年间在我国全海域海底管道腐蚀事故发生频率最高,主要原因是由于油气中二氧化碳或硫化氢等酸性成分含量过高[1]。对于强腐蚀性的油气,采用传统单一的防腐技术及材料,已经不能满足油气能源开发的需求[2]。目前伴随多种不锈钢结构研究的进行和材料成本的降低[3-5],以耐腐蚀合金管为内衬管与腐蚀介质接触,以碳钢管或者低碳钢作为基管承受压力复合而成的双金属复合管,其充分利用了组成材料的各自特点,提供了一种兼具力学和耐久性能,并成本可控的海底管道形式,近年来在石油化工、核电工程等行业将会有着愈加广泛的应用前景[6]。
全寿命周期作用下的海底管道,会经受如服役阶段由油气高温高压产生的较大轴力[7-8]、泥沙运动或者渔锚拖拽可能导致管道巨大的变形从而承受压—弯—剪复合受力,轴向压力往往作为最基本的受力工况,设计过程中根据规范给出的抗力系数法[9],其属于影响管道力学性能最主要的荷载,因此有必要针对双金属海底管道在轴压作用下的力学性能进行研究。目前,Focke等[10]针对两种管径的双金属复合管进行了轴压试验研究,指出管道的承载力主要取决于基管,同时在管道失效后衬管会出现向内的褶皱现象。但是对于双金属复合管的轴压性能研究还很少[11],深入了解轴压作用下双金属复合海底管道的力学性能对于实际海洋油气运输工程具有重要意义。
因此为了探究双金属复合海底管道轴压性能,确保衬管非线性材料不锈钢本构模型所选用的正确性,对双金属复合管进行了材性试验,验证了Gardner和Nethercot修正的R-O模型[12]的准确性,并使用ABAQUS有限元软件,建立了精细化的双金属复合管道轴压有限元模型,在验证模型正确性基础上,进一步分析了双金属复合管的组合作用,并对双金属复合管的径厚比和材料强度进行了参数分析研究。
1 双金属复合管材料本构关系
双金属复合管中的碳钢基管和不锈钢衬管往往通过液压胀形法[13]复合在一起,液压复合工艺是将衬管与管基管同轴装配,同时衬管和基管之间存在一定的初始间隙;通过在衬管内施加胀合液压力使得衬管沿径向扩展,首先消除衬管与基管之间的初始间隙,衬管发生塑性变形;其次衬管和基管共同沿径向向外扩张,基管变形常常处于弹性范围内;最后撤去衬管内压力,基管和衬管共同沿径向向内收缩,由于基管的回弹量大于衬管的回弹量,使得基管和衬管复合在一起,此时由于复合工艺基管和衬管会产生环向复合应力。液压成型工艺如图1(a),由制作工艺产生的环向复合应力如图1(b)。
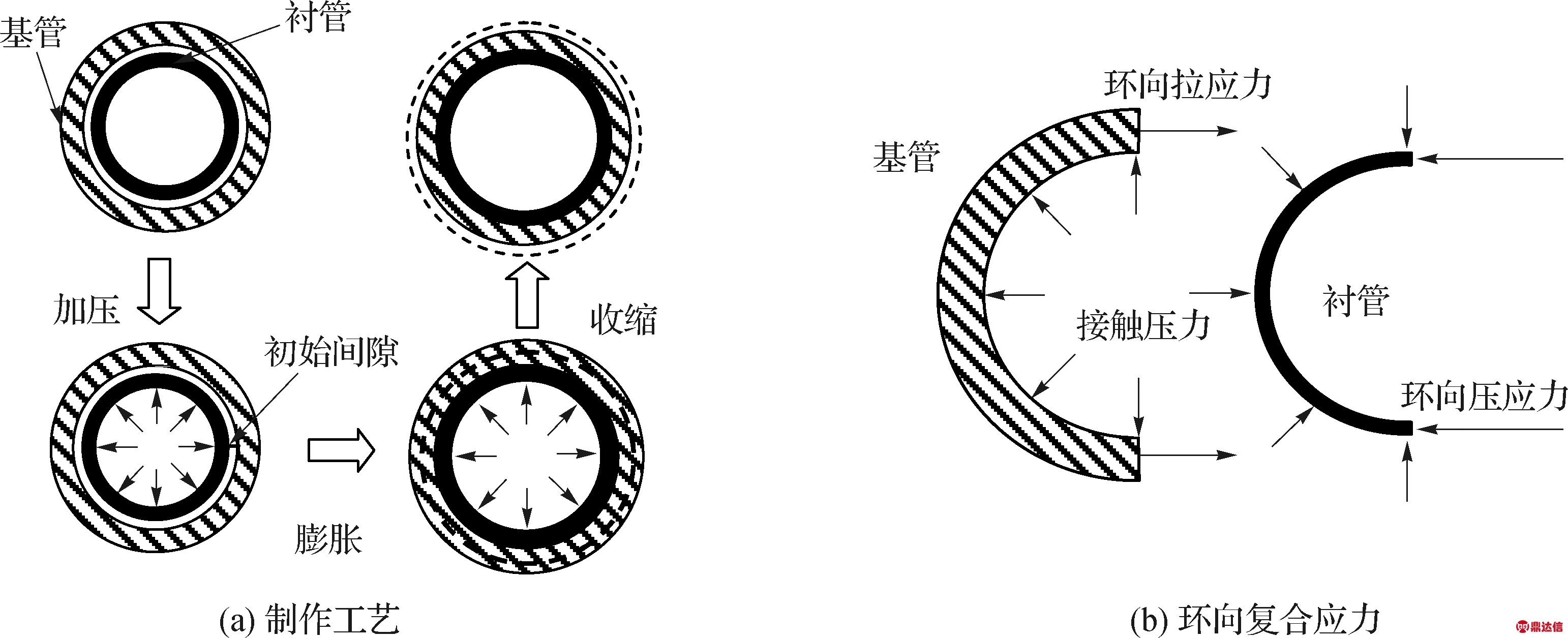
图1 双金属复合管
Fig.1 Lined pipe
其中不锈钢衬管的应力—应变曲线非线性特征明显并常伴有较大的应力强化,设计中广泛采用的不锈钢本构关系是经Gardner和Nethercot修正的两阶段Ramberg-Osgood模型(简称G-N模型),模型关系式为:

(1)
式中:E0表示弹性模量;σ0.2为塑性应变为0.2%时对应的应力;σ1.0为残余应变为0.01时对应的应力;n表示材料系数;代表应变硬化指数;E0.2为在屈服强度处的切线模量;εt0.2为在0.2%弹性极限应力处的总应变。
对外径D=168.3 mm,基管为API 5L X65无缝钢管,衬管为316L不锈钢焊管的双金属复合管进行了材性试验,基管壁厚to=12.7 mm,衬管壁厚ti=3 mm。依据《金属材性拉伸试验:室温试验方法》(GB/T228.1—2010)制作标准材性试件,试件直接从双金属复合管衬管中切取3个试样加工成纵向弧形,试件编号为CTI-1、CTI-2和CTI-3,编号定义如下:CT为Coupon Test的首字母缩写,I代表衬管,数字代表试件编号,并利用设计的夹具进行拉伸试验,试验采用位移控制加载,加载速率为2 mm/min,材性试验如图2所示。通过式(1)的G-N模型模拟3个不锈钢试件材料的应力—应变结果进行对比,试验结果与G-N模型模拟值对比图见图3。
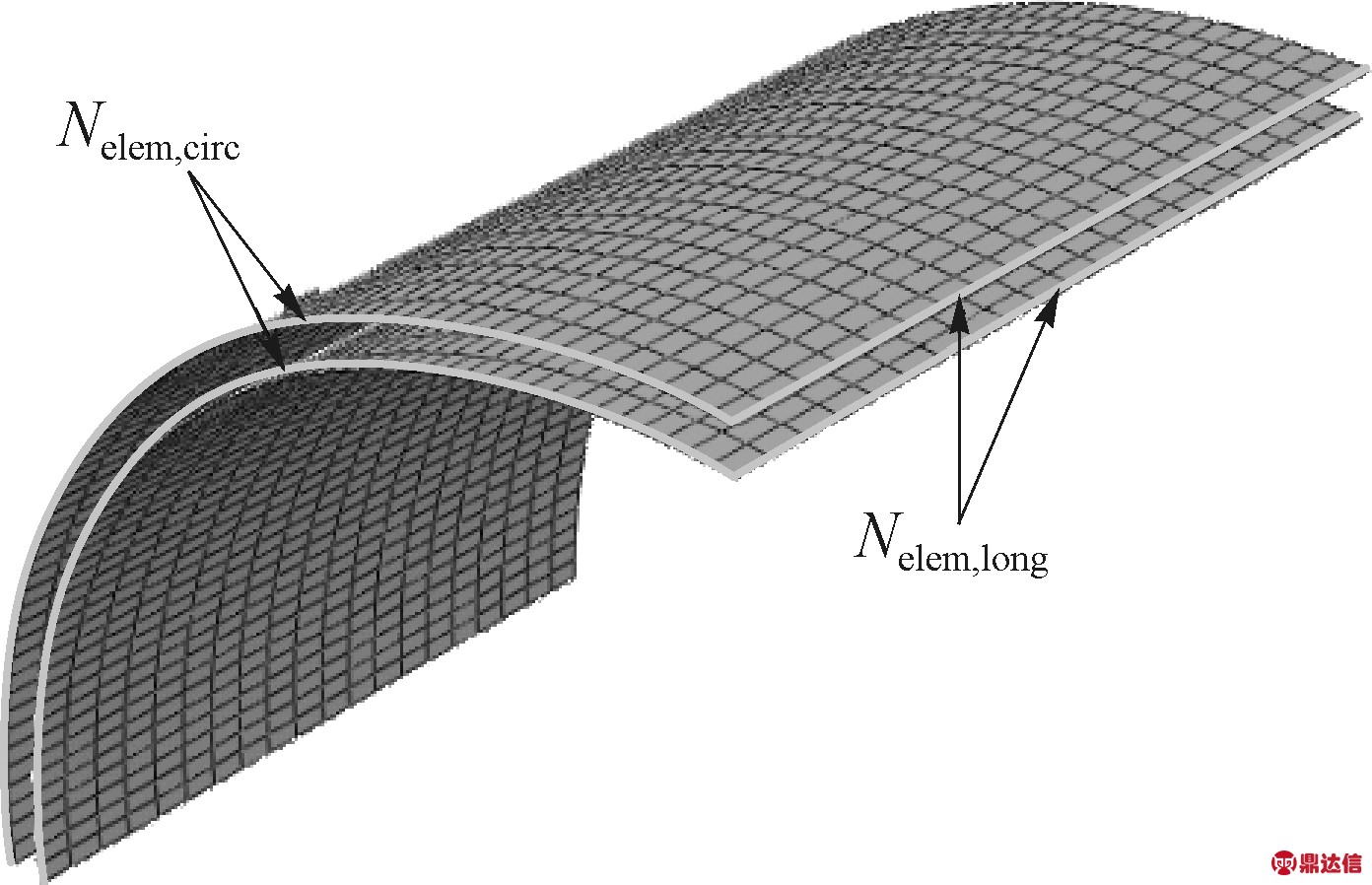
图2 材性试验
Fig.2 Coupon test
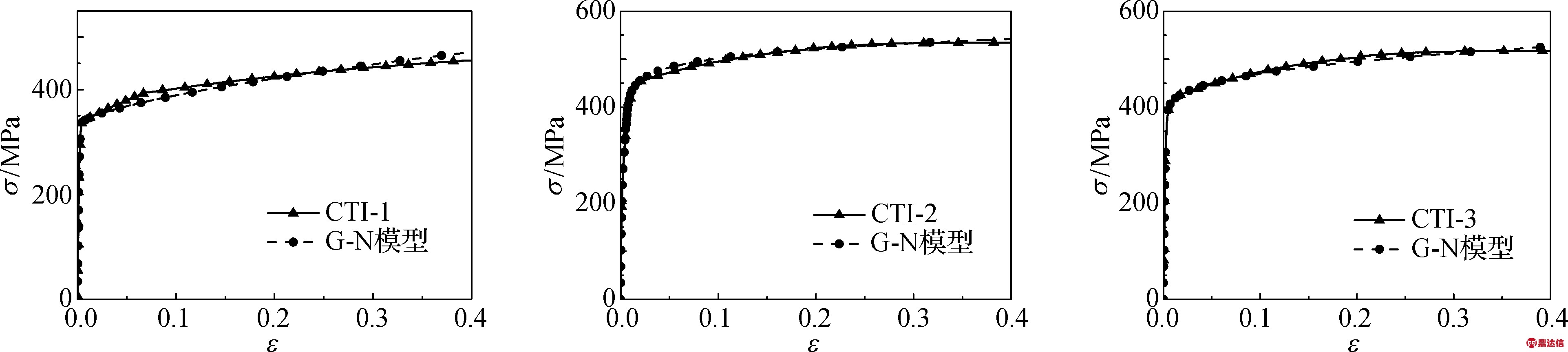
图3 试验曲线与G-N模型对比
Fig.3 Stress-strain curves from test and G-N model
由图3可知:316L不锈钢衬管的应力—应变曲线具有明显的非线性特征,Gardner和Nethercot修正的R-O 模型能够很好地描述不锈钢衬管的本构关系,对比结果显示在双金属复合管轴压模型中采用G-N模型是合理的。
2 有限元模型建立
2.1 分析对象
对管长L=200 mm,D=273.1 mm,to=9.3 mm,ti=2.45 mm的双金属复合管[10]进行轴压模拟。考虑到模型、边界条件和加载方式的对称性,有限元中将原结构简化为八分之一模型,采用对称边界条件,有限元模型如图4所示。内外钢管均采用壳单元(S4R),法向接触采用硬接触,切向采用库仑摩擦,钢材泊松比均取0.3。管道材料强度参数采用Focke等[14]所得试验数据,基管为API 5L X65级钢管,强度参数屈服强度fy=552 MPa,E0=200 000 N/mm2,采用带屈服平台的材料本构模型;衬管为AISI 304L不锈钢,材料本构关系采用G-N模型,强度参数E0和σ0.2分别取值为193 190 N/mm2和308 MPa;n和分别取[15]4.7和3.1。
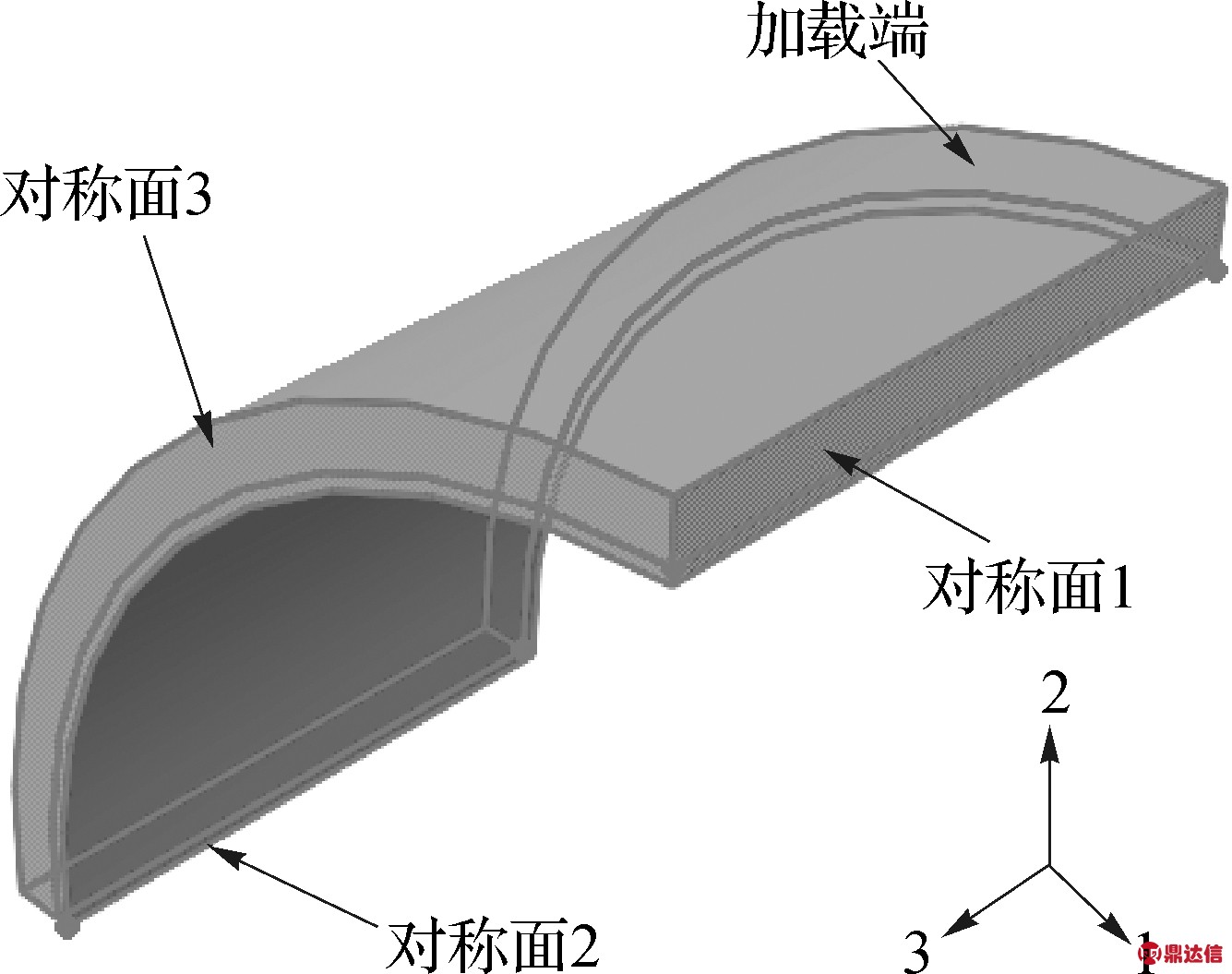
图4 八分之一有限元模型
Fig.4 One eighth of finite model
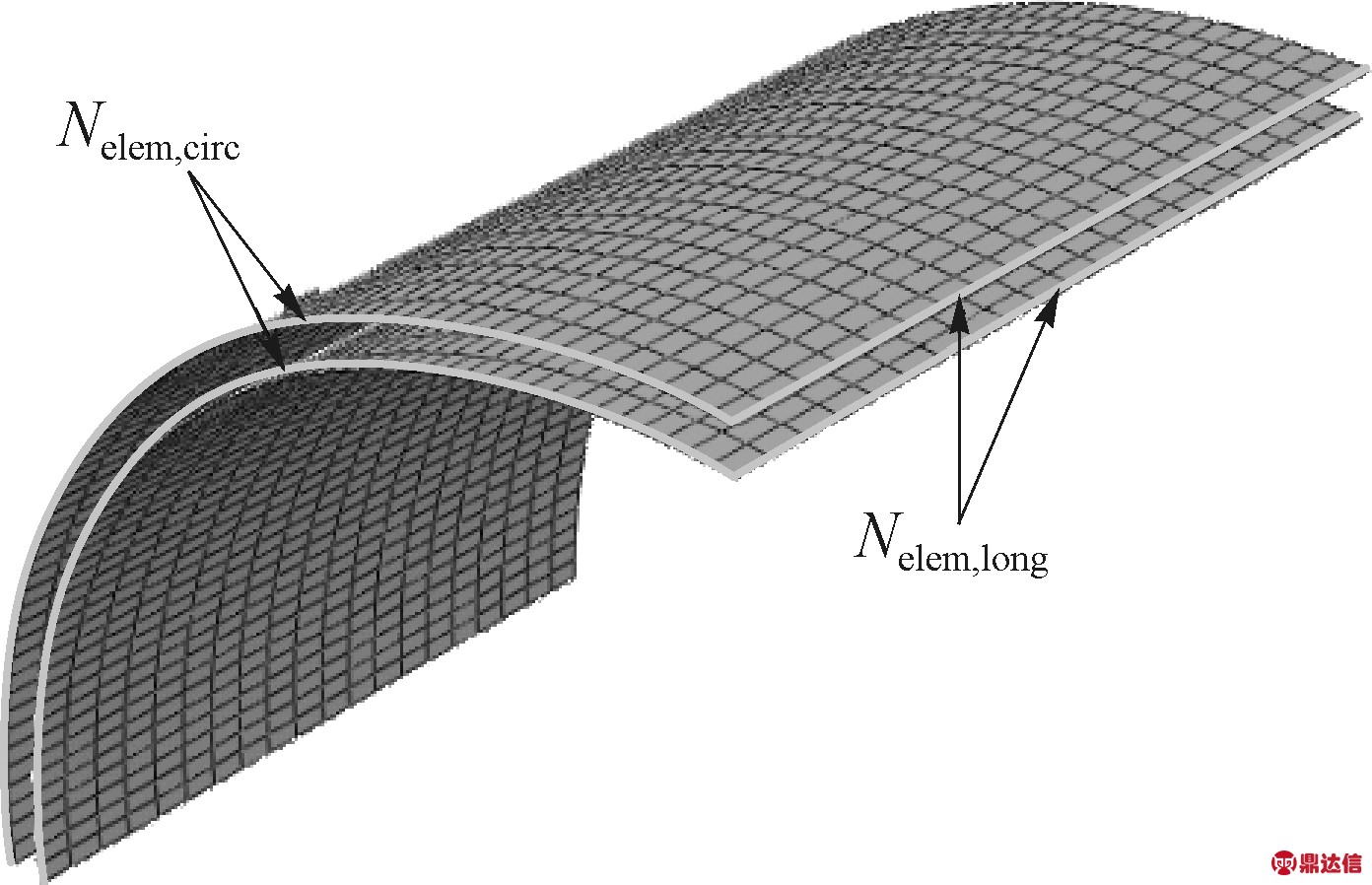
图5 网格划分
Fig.5 Mesh
2.2 网格划分
为保证模型的计算精度和效率,开展了收敛性分析;通过取轴压极限承载力Nu和完成位移加载时管道的轴力Nend,进行单元敏感性分析。定义网格比例参数m=Nelem,circ:Nelem,long(其中Nelem,circ为四分之一管端圆周长上的单元个数;Nelem,long为管道试件L/2上的单元个数),内外管之间不考虑摩擦,摩擦系数取为0,不考虑初始缺陷和环向复合应力,有限元模型中基管和衬管网格均采用比例参数m,取m=3、4、5;Nelem,long=5、7、10、15、20、25、30,单元网格划分示意图如图5所示,单元敏感性分析结果如图6所示。
那天,李桂明的妻子回娘家了,就他一个人在家。他想,这是极好的机会。一早,他父亲嘱咐他早点回来,为帮他家做活的亲戚朋友做饭。
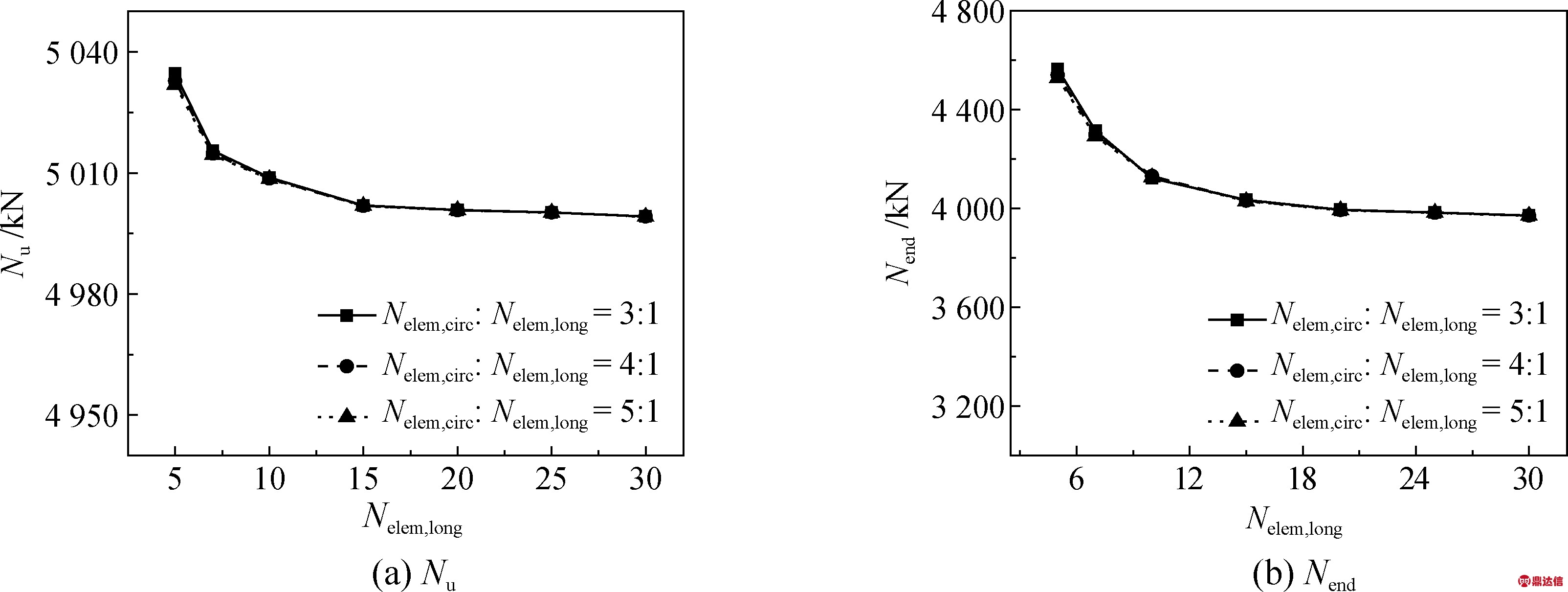
图6 单元敏感性
Fig.6 Sensitivity of different meshes
2.3 初始几何缺陷
探究初始缺陷对管道轴压作用下极限承载力影响的敏感性时,参考Yuan[16]提出的两种衬管初始缺陷类型,即衬管的两种局部曲屈模态(如图7所示),以10-1 mm幅值浮点形初始缺陷植入有限元模型,示意图如图8(a)所示。
图8(b)中实线为原初始缺陷沿管道试件轴向方向的剖面,点划线为植入衬管后的缺陷幅值。图8表明初始缺陷并未按原有形状植入衬管中,这是因为ABAQUS中衬管和基管之间存在接触,衬管无法穿透基管。衬管初始缺陷在复合之前就已经存在,复合过程中,因基管对衬管的约束作用,衬管初始缺陷会形成与图8(a)一致的状态。因此,有限元模型中初始缺陷的植入方法能够正确反映双金属复合管的真实初始缺陷状态。
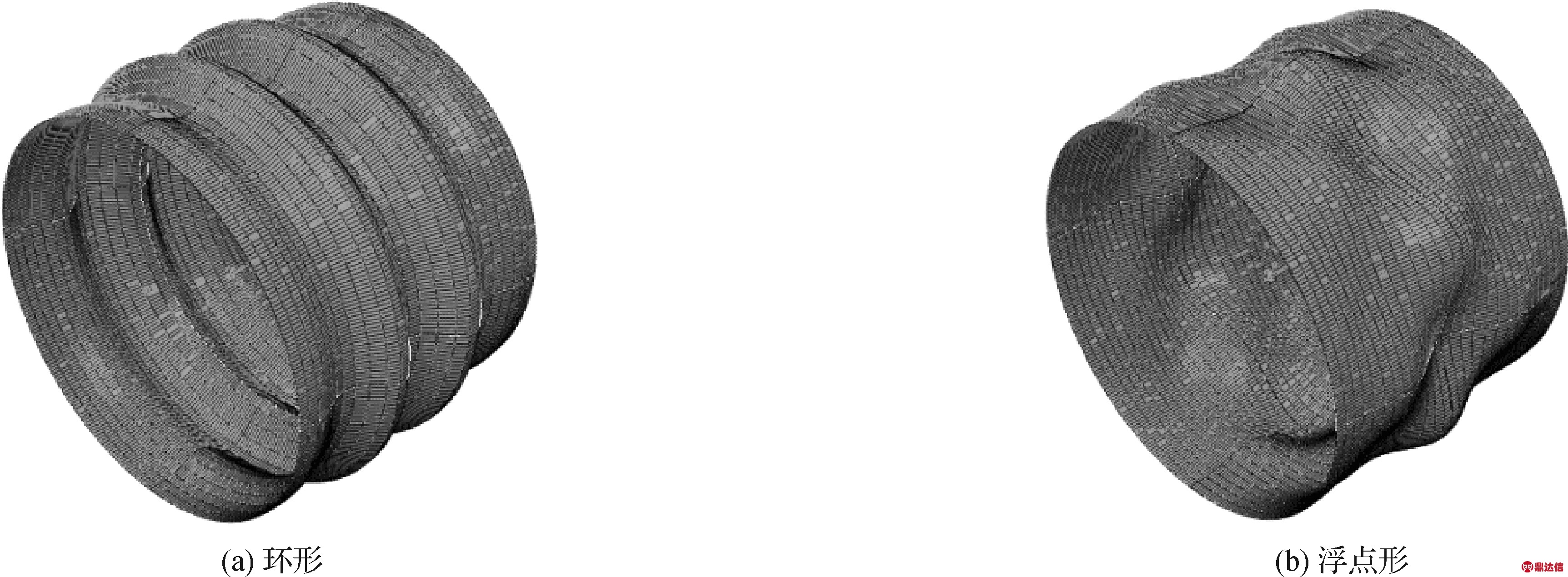
图7 初始缺陷示意
Fig.7 Imperfection patterns

图8 初始缺陷植入衬管前后变化
Fig.8 Comparison of profiles of imperfections initially and after application
有限元模型中不考虑环向复合应力和内外管之间的摩擦,两种初始缺陷幅值分别取10-3 mm、10-2 mm、10-1 mm和1 mm分析得到的轴力—轴向应变(N-ε)变化关系如图9所示。
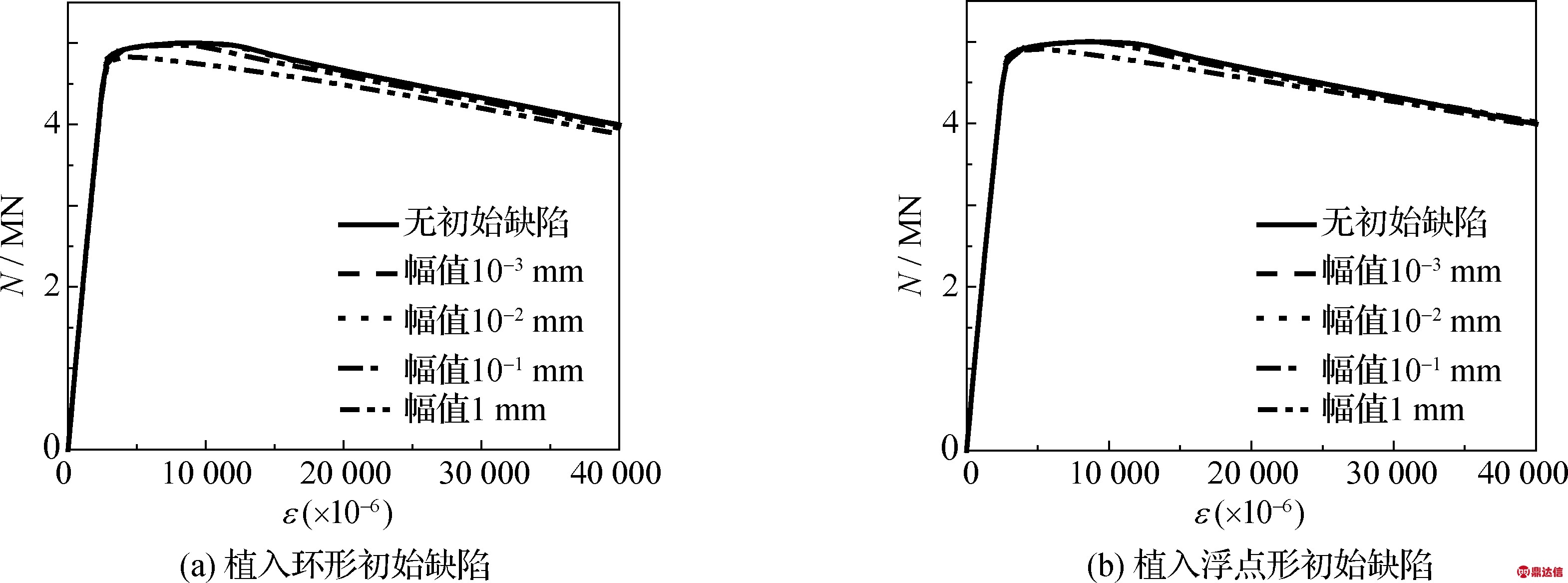
图9 不同初始缺陷下N-ε
Fig.9 N-ε of different imperfections
图9结果表明:随着衬管初始缺陷幅值的增大,初始缺陷对双金属复合管轴压结构的影响也随之增大,当初始缺陷幅值为1 mm时,对双金属复合管轴压结构的影响较大;当初始缺陷幅值小于1 mm时,初始缺陷对双金属复合管轴压结构的影响可忽略不计。
2.4 环向复合应力和摩擦系数
探究环向复合应力对轴力的影响时,不考虑初始缺陷和内外管之间的摩擦。利用ABAQUS中的预定义场功能(predefined field)设定环向应力,之后有限元模型通过基管和衬管之间的相互作用经自平衡得到与图1(a)第四步环向应力状态相同的管道,其中环向复合应力正值为拉应力,负值为压应力。不同环向复合应力状态下管道极限承载力结果见表1。由表1分析可得不同环向复合应力下管道的极限承载力变化范围在0.5%之内。
表1 不同环向复合应力下管道极限承载力
Tab.1 Nu of different residual hoop stresses

分析摩擦系数μ的影响时,模型中不考虑初始缺陷和环向复合应力,内外管之间摩擦系数μ分别取0、0.3、0.5、1.0和1.5,得到不同摩擦系数下管道的极限承载力变化范围在0.3%之内。分析结果表明:忽略环向复合应力和摩擦系数对双金属复合管轴压极限承载力结构影响较小。
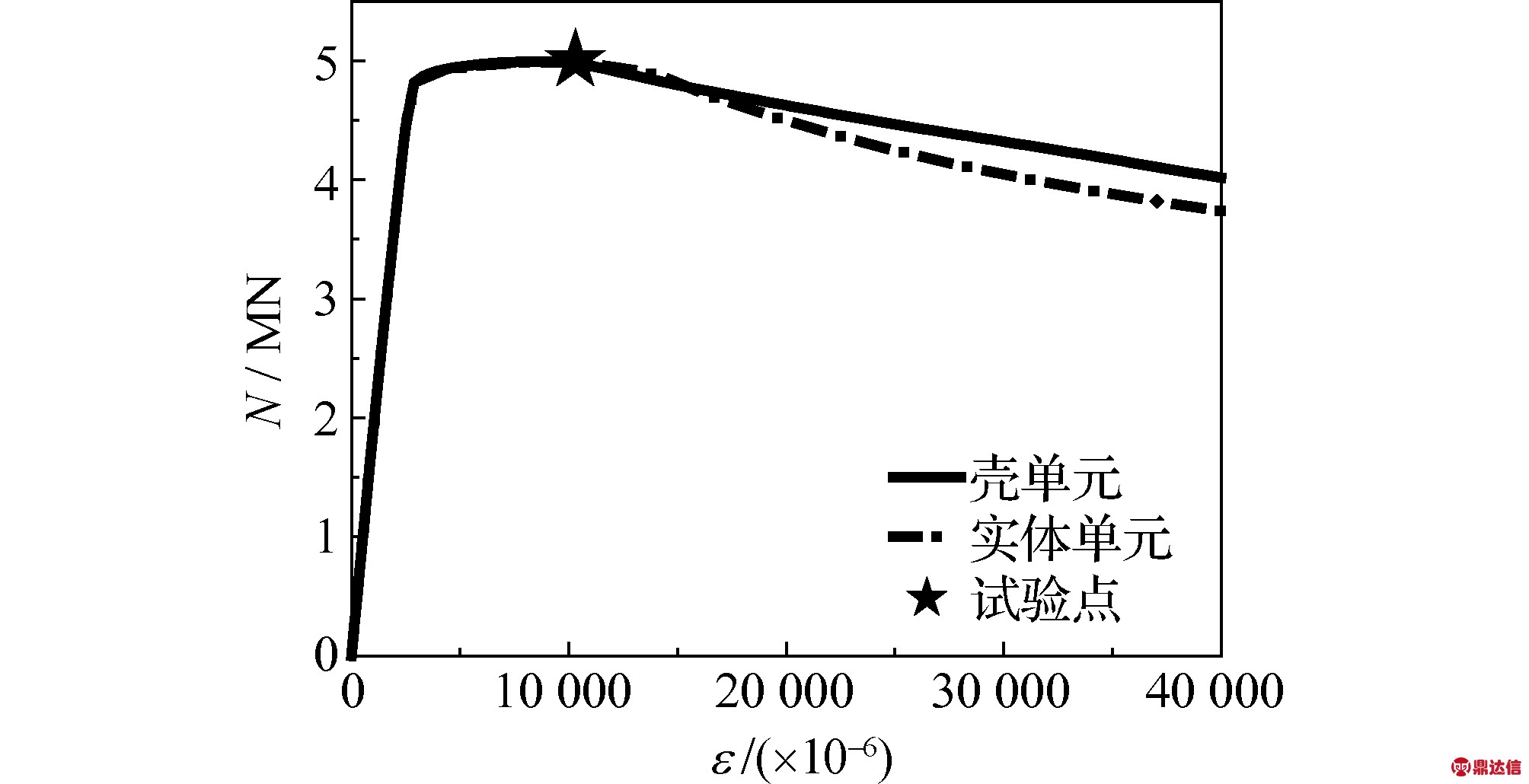
图10 N-ε
Fig.10 N-ε
2.5 模型验证
首先建立无环向复合应力,无摩擦,衬管植入0.1 mm幅值浮点形初始缺陷的双金属复合管实体单元和壳单元轴压有限元模型进行对比分析。结果表明两者失效形态相同,N-ε变化关系图如图10所示,二者最大误差为6.8%,同时考虑到管道结构特性和壳单元选取原则,选取壳单元模型进行验证及分析。由图10可知,当达到极限承载力Nu时有限元模型结果与试验值分别为4 995 kN和5 007 kN,误差为0.24%;对应的轴向应变εu与试验值分别为0.87%和1.03%,误差为15.53%。
轴压作用下双金属复合管失效形态,有限元模拟与试验中基管均表现为管道中部略向外鼓曲如图11(a)、(b)所示;衬管则产生向内部的褶皱,模型中衬管失效形态为对称分布如图11(c),试验中衬管失效形态为非对称如图11(d)所示,这是因为有限元模型管道、材料和几何尺寸均为理想;而试验中管道为非理想,故导致出现非对称褶皱,但二者的局部褶皱形态可以很好吻合。因此通过极限承载力、轴向应变和失效形态三方面的对比验证了所建立有限元模型的准确性。
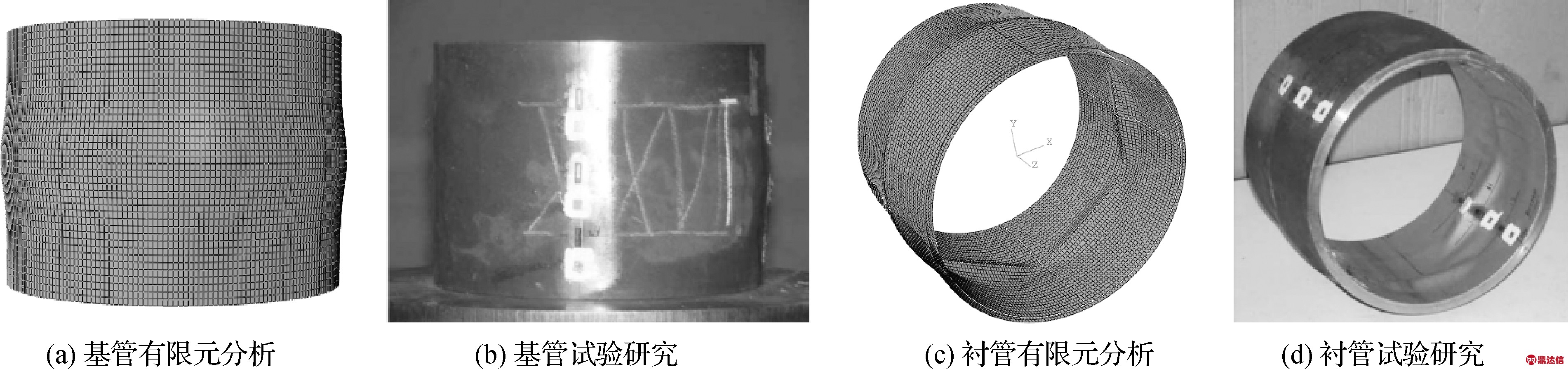
图11 失效形态对比图
Fig.11 Comparison of the failure model
3 参数分析
3.1 径厚比
基于验证的有限元模型,内外管之间设置无摩擦,无环向复合应力,衬管植入0.1 mm幅值的浮点形初始缺陷,分析径厚比对轴力的影响,保持双金属复合管总壁厚t(to=9.3 mm,ti=2.45 mm)和长细比λ不变,改变管道外径D,径厚比参考挪威船级社规范[17]取15<D/t<45。管道模型参数见表2,ε-N变化关系如图12所示。
表2 管道几何参数
Tab.2 Geometrical parameters of finite model

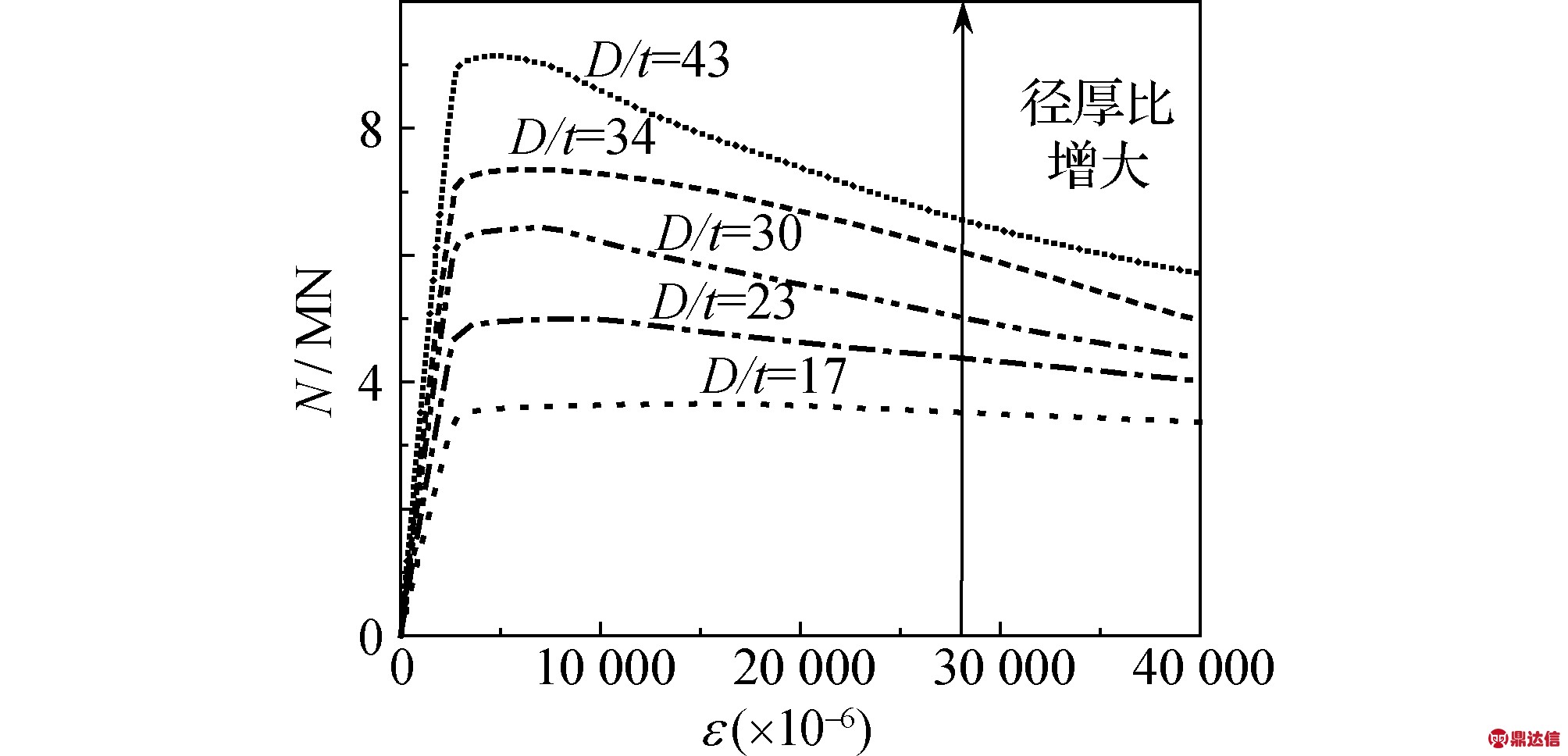
图12 不同径厚比N-ε
Fig.12 Effect of D/t on N-ε of curve
图12表明,保持双金属复合管的长细比不变时,随着径厚比的增大,管道极限承载力随之增大。当径厚比大于等于23时,随着径厚比的增大,管道达到屈服后承载力下降加快,这是因为随着径厚比的增大,管道壁局部屈曲发展较快,导致管道后期承载力迅速退化;当径厚比为17时,管道横截面钢管面积与中部空心面积之比为28.4%,在管道屈服后,后期承载力下降缓慢,这对于长期处于海流冲击下的海底管道可起到延缓破坏的作用,因此建议双金属复合管道的径厚比不宜过大。
3.2 材料强度
考虑材料强度对极限承载力Nu的影响时,基于验证的有限元模型,内外管之间设置无摩擦,无环向复合应力,衬管植入0.1 mm幅值的浮点形初始缺陷。只改变基管或者衬管的屈服强度,基管的屈服强度fy分别取350 MPa、400 MPa、450 MPa、500 MPa、550 MPa、600 MPa和650 MPa;衬管屈服强度σ0.2分别取250 MPa、300 MPa和350 MPa,管道模型参数见表3。不同材料强度下双金属复合管的极限承载力Nu,如图13所示。
表3 模型参数
Tab.3 Parameters of finite model

由图13分析可知,当保持衬管材料的屈服强度不变时,每当基管材料屈服强度提高50 MPa,双金属复合管的极限承载力提高约390 kN,极限承载力随着基管材料屈服强度的提高而增大,二者呈现出明显的线性关系;当保持基管材料的屈服强度不变时,每当衬管材料屈服强度提高50 MPa,双金属复合管的极限承载力提高约110 kN,极限承载力随着衬管材料屈服强度的提高而增大,两者间存在明显的线性变化关系。因此可以通过提高管道材料的屈服强度来改善管道轴压承载性能。
4 组合作用分析
双金属复合海底管道中基管和衬管在轴压作用下共同承担轴力,为探究轴压过程中双金属复合管基管和衬管之间的组合作用,作者分析了全过程构件、基管和衬管轴力的N-ε曲线,如图14所示。
双金属复合管道的N-ε全过程变化曲线可大致分为三个阶段:1)构件整体表现为弹性的OA段;2)构件整体表现为弹塑性的AB段;3)构件整体表现为塑性的BC段。OA弹性阶段,此时基管处于弹性阶段,衬管处于弹塑性阶段,但构件整体轴力—应变曲线表现为线性关系,由ABAQUS输出基管和衬管A点处的von Mises应力,二者也同时达到了各自材料的屈服强度,表明基管和衬管在此之前并未发生局部屈服;AB弹塑性阶段,基管进入了弹塑性阶段,对基管截面屈服荷载Ny=Afy(A为管道截面面积)与模拟得到的基管轴力进行比较[18],由于碳素钢往往伴有较长的屈服平台,两者基本相等,表明虽然基管达到了屈服强度,但其整体承载力并未出现下降。同时衬管依然处于弹塑性阶段,由于不锈钢的应变强化特性和基管对衬管的约束作用,限制了衬管局部屈曲现象的发展,延缓并提高了衬管极限承载力的出现,使得双金属复合管在AB段的轴力持续增大,避免了双金属复合管承载力的退化,这对于防止海底管道的破坏十分有利;进入BC塑性阶段,基管和衬管大面积发生屈服,基管对衬管的约束作用也减弱,衬管褶皱屈曲向内部快速发展,此时双金属复合管的承载力进入下降阶段。
由图14可知当双金属复合管达到极限承载力时,基管和衬管各承担了荷载的85.6%和14.4%,由此可见基管承担了大部分荷载,这与Focke等[10]得到的结论一致,因此通过改变基管的截面面积和提高基管承载力可有效提高双金属复合管的极限承载能力。
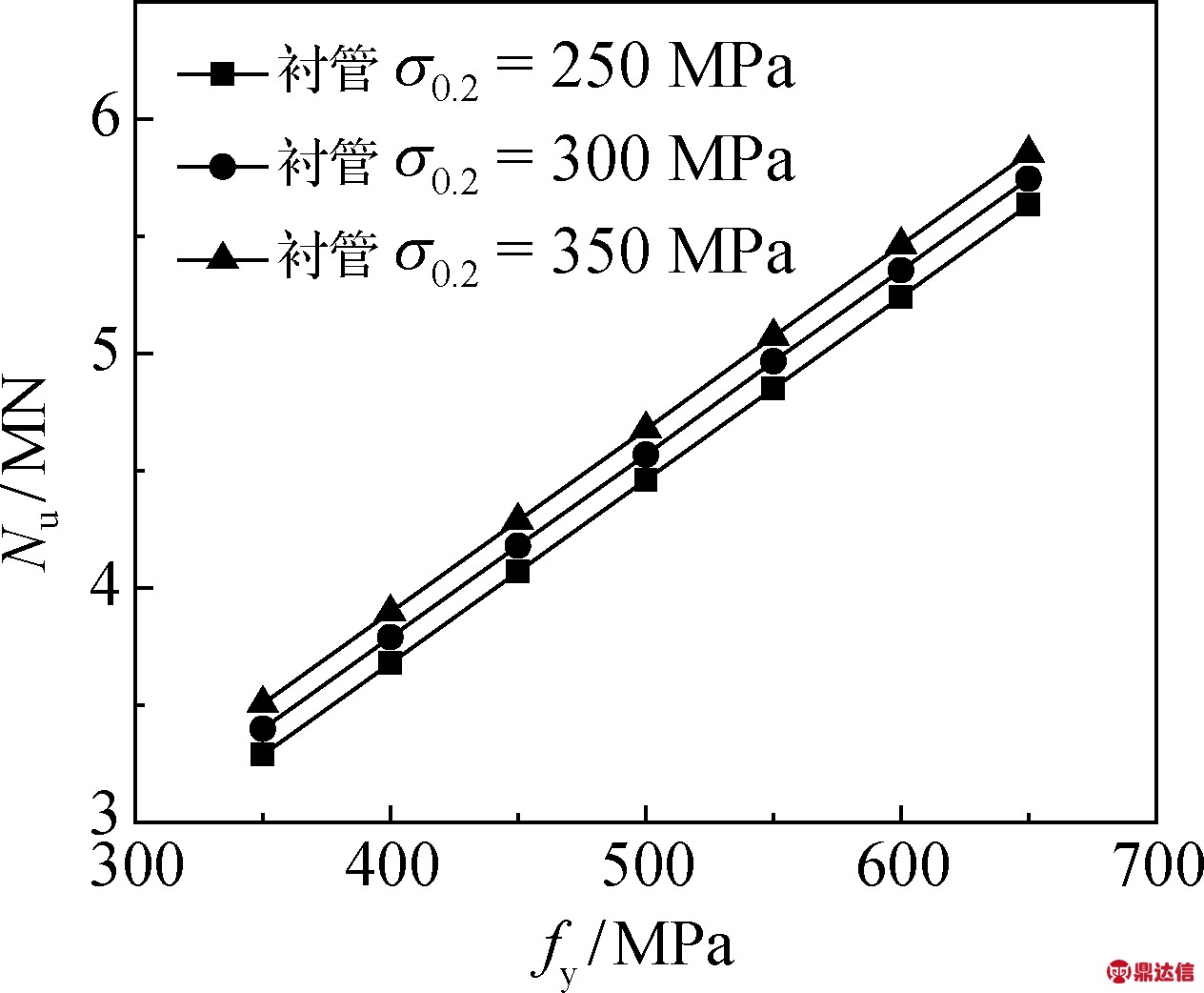
图13 Nu-fy
Fig.13 Nu-fy
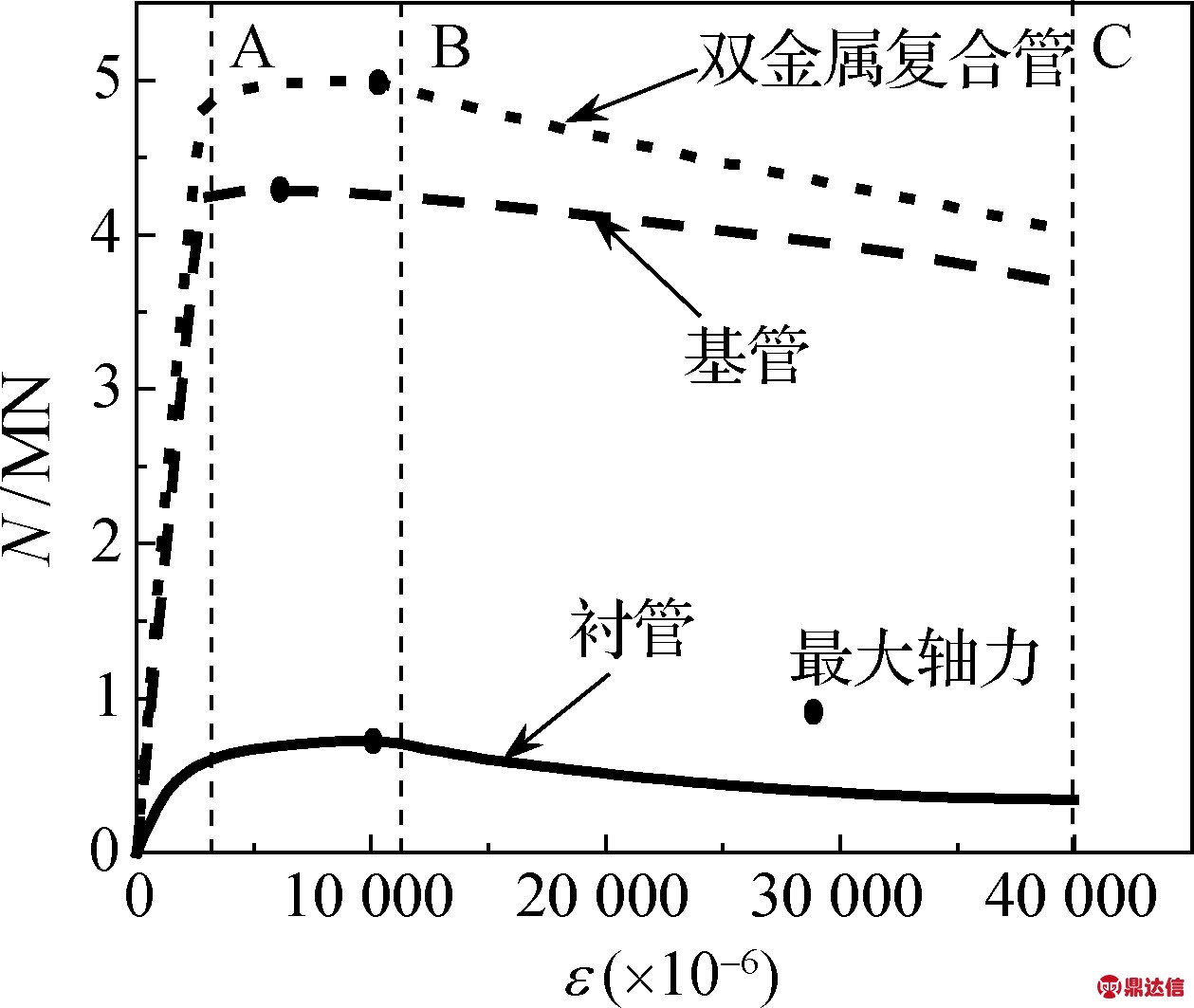
图14 N-ε
Fig.14 N-ε
5 结 语
进行了双金属复合海底管道不锈钢衬管的材性试验,建立了精细化的双金属复合管轴压有限元模型并进行了轴压试验分析。
1)通过双金属复合海底管道不锈钢衬管材性试验,验证了Gardner和Nethercot修正的R-O模型可以很好描述不锈钢衬管的本构关系。
2)建立了考虑不锈钢材料非线性计算精度较高的双金属复合管轴压有限元模型,与已有双金属复合管轴压试验结果的对比验证了数值模型的准确性。
3)基于验证的有限元模型分析,双金属复合管的极限承载力随管径和材料强度的提高而增大;在轴压过程中基管承担了绝大部分的轴压荷载,同时由于衬管的存在延缓了双金属复合管承载力的下降。