摘 要:金属丝材的电弧3D打印成形工艺因具有制造高效率、高柔性、低能耗、易于实现大尺寸等优点成为研究热点。研究了打印速度、电压和电流对成形零件打印层高和层宽的影响;开发出与打印工艺参数、CAD切面算法、零件成形匹配且界面友好的3D打印软件系统;利用自行开发的在线打印系统打印出典型的结构零件。打印件具有成形良好、精度较高、致密性高等优点,验证了打印软件算法的正确性、弧焊金属丝打印和修复结构件的可行性。
关键词:金属丝材;弧焊3D成形;打印软件
3D打印成型技术是上世纪80年代后期发展起来的一项崭新技术,其以增材制造为思想,综合数控、计算机、机械工程及材料科学技术等先进技术于一体,以降维制造为手段,是实现三维原件成形的先进技术。电弧成形增材制造技术采用电弧作为热源,将金属丝材熔化逐层沉积,从而制造出接近产品设计尺寸要求的三维金属胚件,再辅以少量机械加工,最终达到产品尺寸设计要求。与基于激光做热源的激光选区熔化(SLM)、激光近成形(LENS)等技术相比,具有制造效率高(几公斤/小时,为SLM技术的10~100倍)、高柔性(可以多维度曲面自由成形)、节能降耗(电-电弧转换率85%以上、激光电-光转换率小于10%)、易于实现大尺寸制造等优点[1-7]。由于无需粉末床等设施,可直接在原(损坏)金属零部件上直接成形,因此特别适合于破损零部件的在线式维修再制造。然而,基于金属材料的3D打印成型技术至今仍存在许多瓶颈问题,其中最突出的是两方面的问题:①金属3D打印技术可使用的材料种类较少,急需开发适合3D打印成型的金属丝材;②直接打印成型的金属零件尺寸难控制且表面质量低,一般需要1~5 mm的切削量。因此,非常有必要开展对金属丝材的3D打印工艺和打印精度的研究。
1 实验方法
1.1 实验设备和材料
1)实验设备:MOTOMAN-UP20弧焊机器人系统;MOTOWELD-S350 CO2自动焊机;Kempotig AC/DC 250氩弧焊机。
2)实验材料:YCJ501-1药芯焊丝,成分见表1,主要用于碳钢及500 MPa级高强钢的堆积;焊丝直径为Φ1.2 mm。本实验保护气体为20%氩气和80%二氧化碳的混合气体。
表1 YCJ501-1的熔敷金属化学成分

3)堆积基板:280 mm×140 mm×12 mm的Q235钢。为了使基板具有良好的导电性,使用前必须去除表面的铁锈和氧化层,将基板用砂轮机进行打磨。
1.2 打印工艺参数
3D打印工艺参数(电流、电压和速度)直接影响结构件的成形。本实验分别选取8个不同打印速度20,40,60,80,100,115,130,150 cm/min进行实验,堆积电流为100,160,220,280,340 A,电压为:14,21,35,42 V,打印成型时保持1种参数变化,另2种参数保持不变,且每组参数堆一个成形件。
2 堆积速度对直壁堆积成形工艺的影响
按照给定的打印工艺参数,每个成形件堆积8层,前2层打底,后面6层用于测量不同打印层的熔高和熔宽,每层测量点在同一个位置。依此,通过测量电弧堆积层的熔宽和熔高来研究打印工艺参数对打印件壁厚和层高的影响。每层分别测量层高和层宽,每个数据测量3次,取平均值。记录实验所得数据,并采用OriginPro对相关数据进行分析处理,得到不同工艺参数下打印件层高、层宽随打印层变化的折线图。
2.1 打印速度对堆积件层高、层宽的影响
不同速度下打印层高与打印层数关系见图1。由图1可以得出不同打印速度下,打印件的层高随堆积道次的增加均增高,而且呈现明显的正相关性。在同一打印速度下,一般每增加一层,堆积件的层高都会有明显的变化,而层宽基本不变化;打印电流和电压不变时,随着堆积速度的增加,熔高、熔宽均减小。
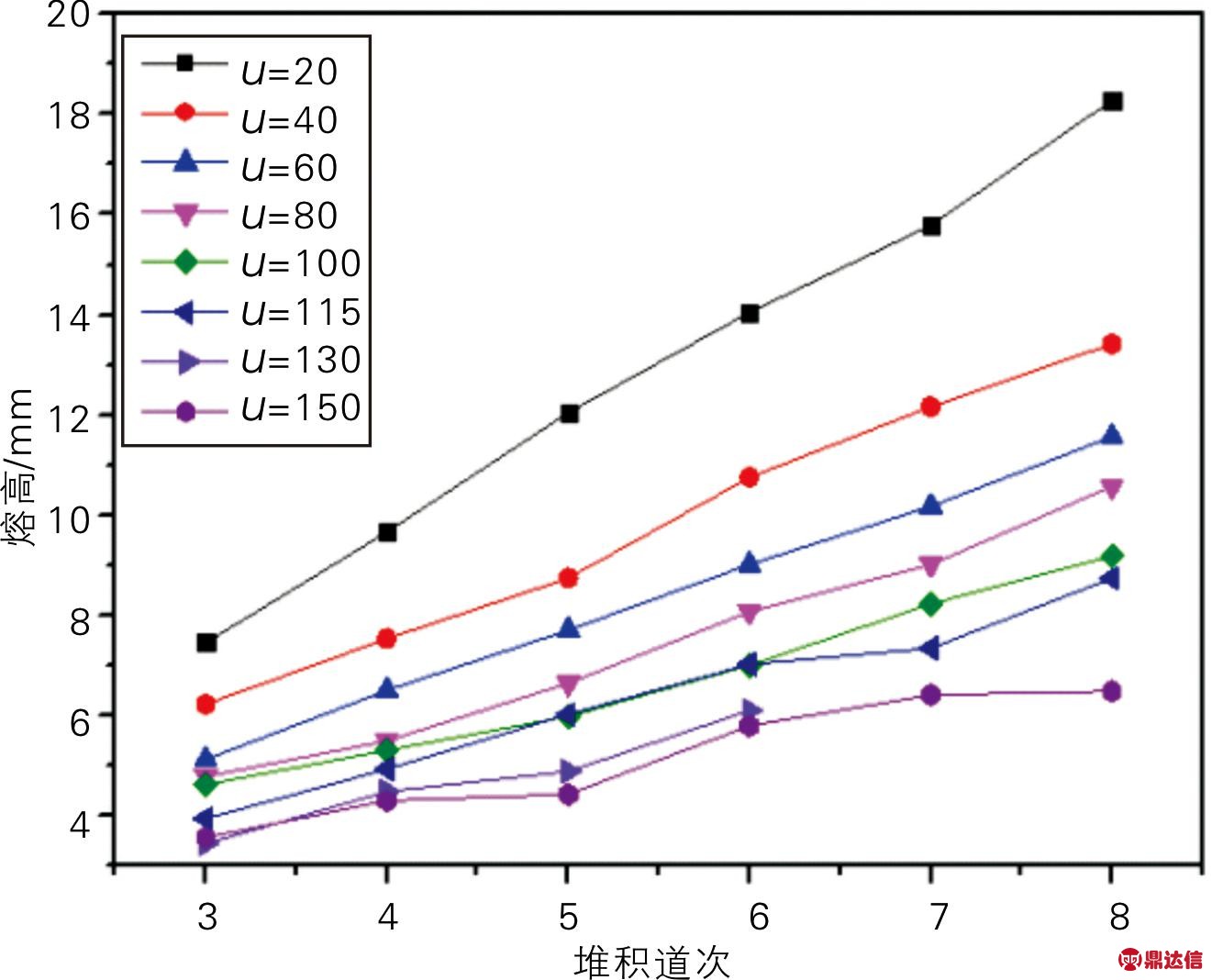
图1 不同速度下打印层高与打印层数关系
单道多层层高与打印速度关系见图2,单道多层层宽与打印速度关系见图3。图2和图3表明其他打印参数不变情况下,打印件层高和层宽随打印速度增加而减少,呈负相关性。
单道多层层宽与打印电流关系见图4。图4表明在其他参数不变的情况下,层宽随打印电流的增加而增加,呈正相关性,因此编写弧焊3D打印成型分层软件时对层高要逐层分析,而对层宽只分析某一打印速度下层宽的平均值即可。
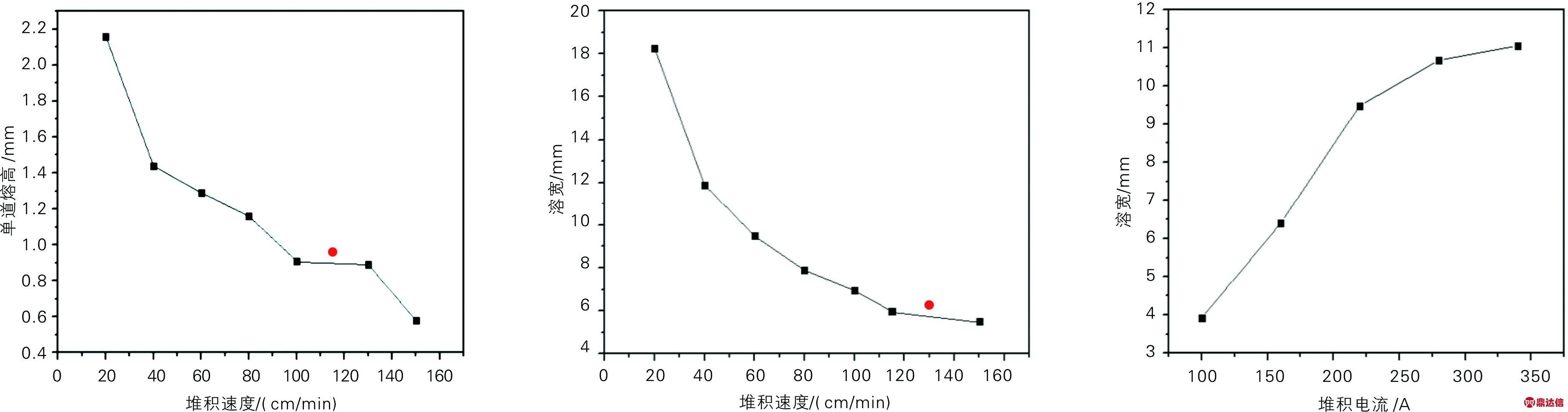
图2 单道多层层高与打印速度关系 图3 单道多层层宽与打印速度关系 图4 单道多层层宽与打印电流关系
2.2 打印电压和电流对堆积件层高的影响
不同打印电压和电流下层高与打印层的关系见图5。由图5可见,随着电压的增大,层高的变化趋势并不明显,影响程度非常轻微;随着堆积电流的增大,电流对熔高的影响越来越小。
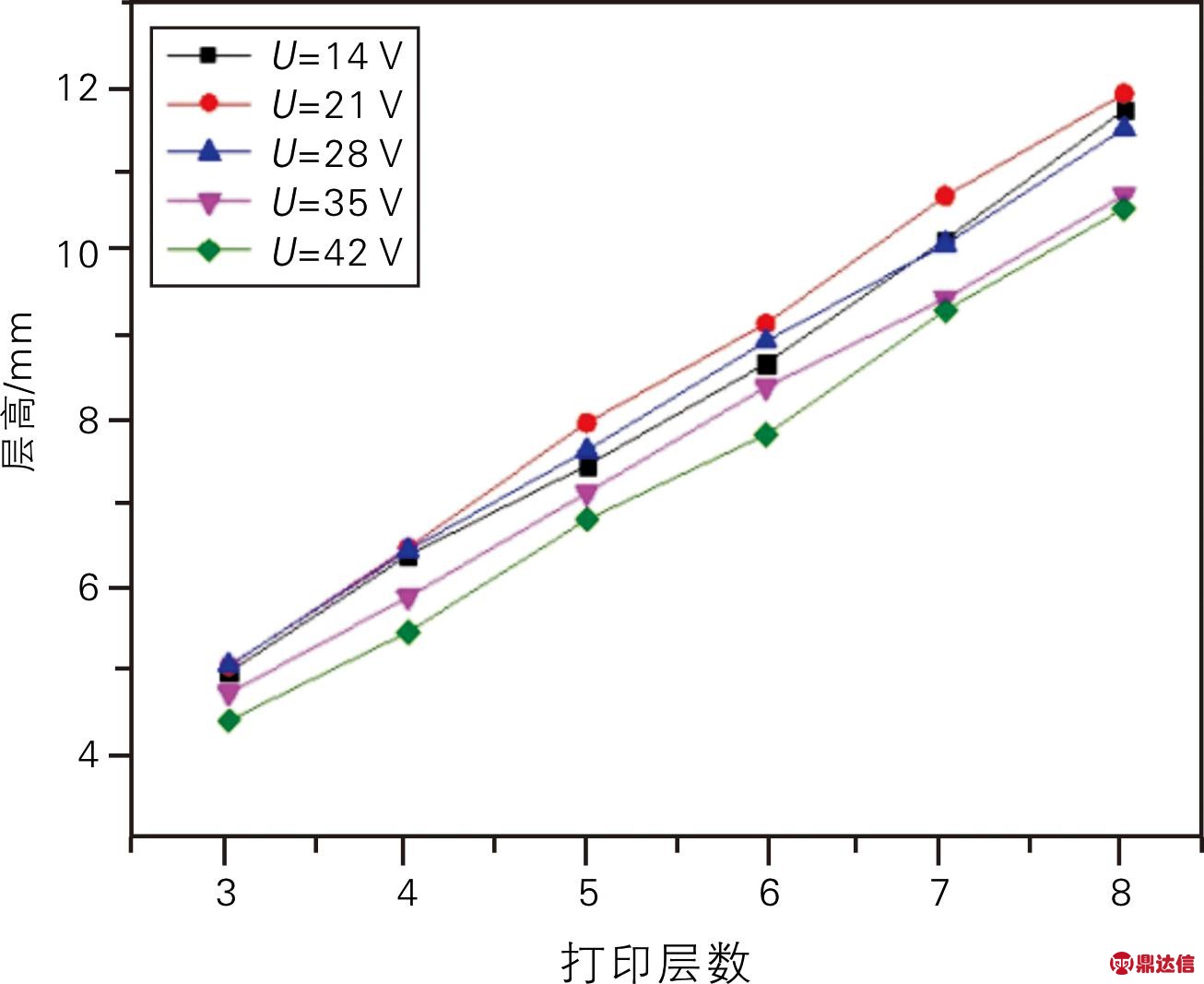
(a) 速度为60 cm/min,电流为220 A
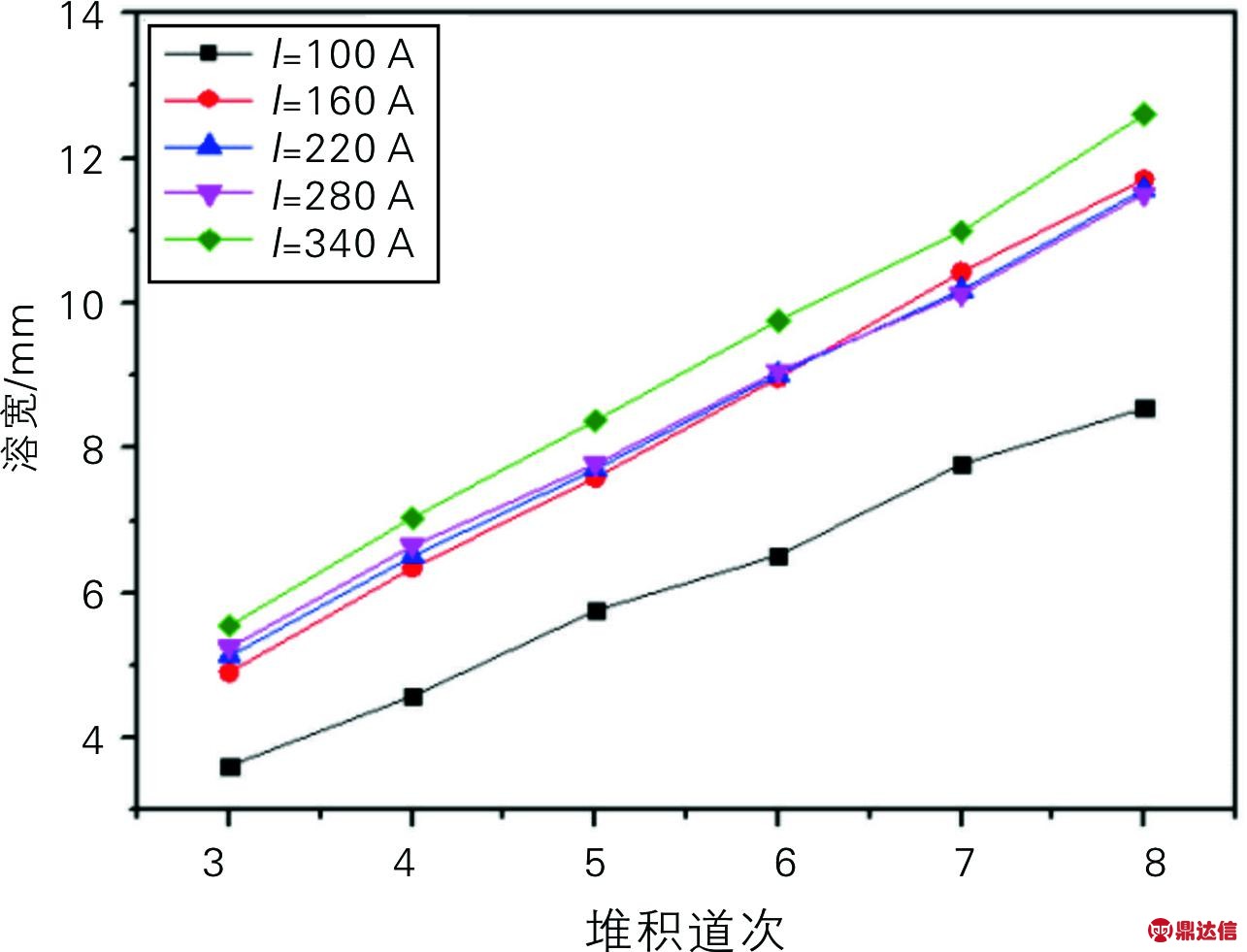
(b) 速度为60 cm/min,电压为28 V
图5 不同打印电压和电流下层高与打印层的关系
3 金属丝3D打印专用工艺规划软件研发
金属丝材3D打印软件开发的关键是从零件模型到3D打印制造技术接口的数据转换和处理软件。基于零件模型的3D打印软件系统一般由3个部分组成[1-4] :零件模型获取软件(系统)、模型处理软件和监控软件。本研究自行开发的软件界面友好,支持单道多层和多道多层成形、自适应搭接量技术和尺寸误差补偿。对金属直接成形过程的控形技术研究,是提高成形精度的技术研究。影响成形进度的因素包括功率大小、扫描方式、电流大小(弧焊成形)等工艺参数,应选取合适的扫描方式,降低成形过程中应力的累积,减小成形变形;研究工艺参数对成形精度的影响规律,优化出最佳的工艺参数使成形精度达到最高。
本研究利用 OpenGL 自身图形操作函数,在 VC++环境下进行金属丝材打印成型编程和软件模块设计。金属丝3D打印软件模块图见图6。
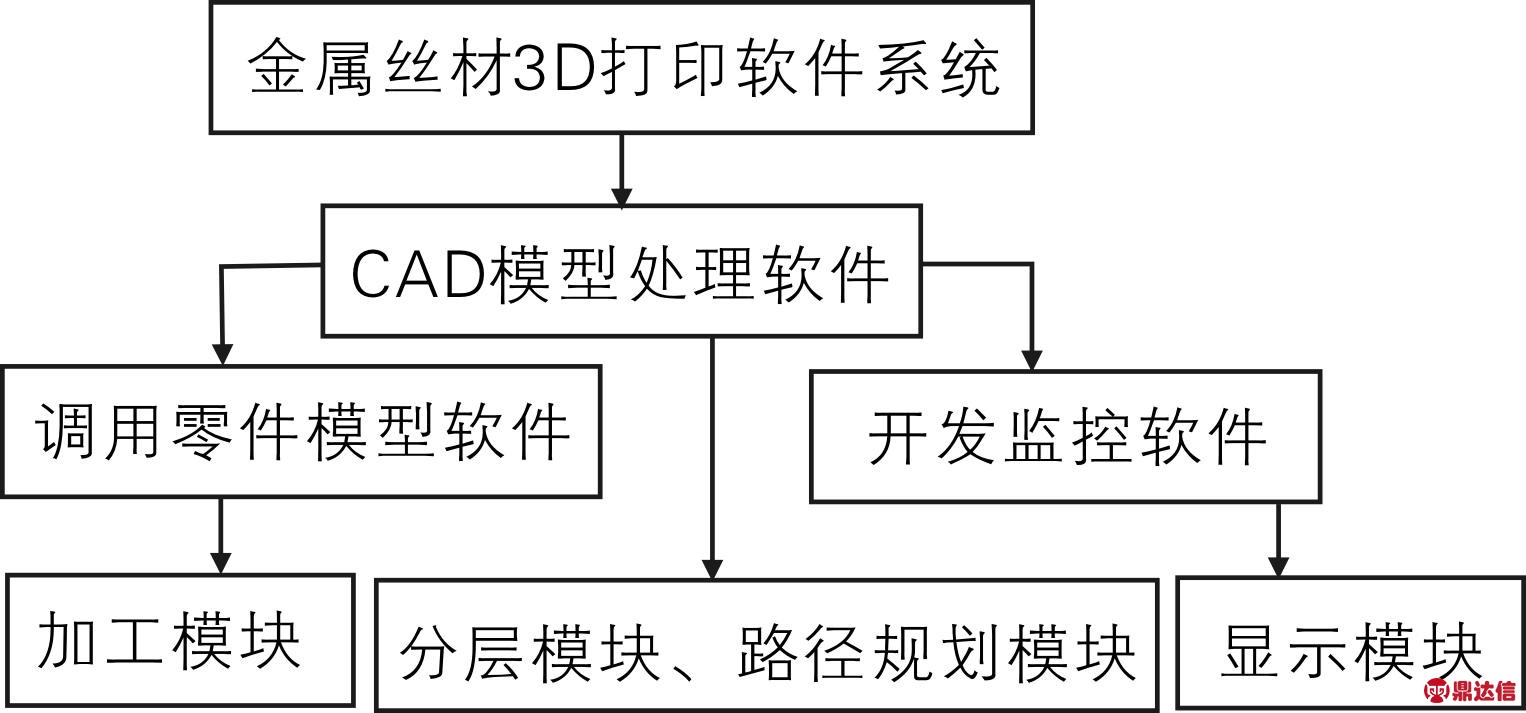
图6 金属丝3D打印软件模块图
在开发本打印软件时,针对相关参数设置,对堆焊路径做一些单独的优化处理,具体包括以下几个方面:水平方向尺寸补偿、高度方向补偿、焊接路径规划和旋转、支持打印参数监控及修改的功能等。基于上述打印参数对层高和层宽影响研究的数据支持,在线金属弧焊3D打印系统重叠界面如图7所示。
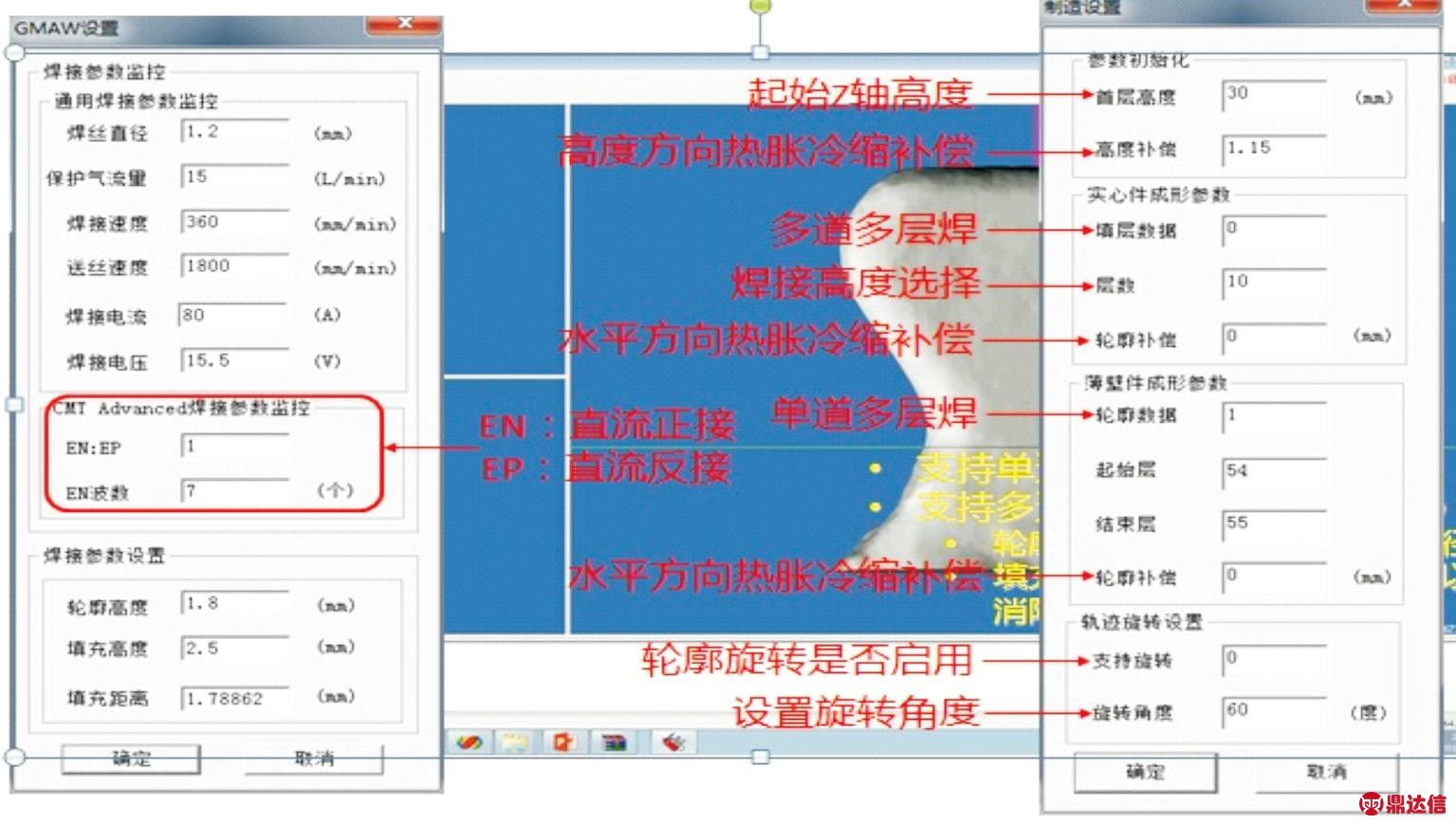
图7 在线金属弧焊3D打印系统重叠界面
4 不同形状薄壁构件3D打印堆积实例
本实验堆积了一U形件和回转件,气流量q=18 L/min(100%Ar)。U型件工艺参数:电压28 V,电流220 A,速度60 cm/min;回转件工艺参数为:电压12.6 V ,电流76 A,速度36 cm/min。在线金属弧焊3D打印系统本体及打印件见图8。
由图8可以看出,U形件和回转件均成形良好,没有咬边、气孔等缺陷,而且飞溅小,同时过渡处也没有出现塌陷等缺陷。层宽与堆积形状无关,而成形件的表面精度与形状有关。无论是U形还是圆行,熔宽的标准差都小于熔高,这说明内外壁的精度高于上壁。同时,打印件的角度也会对精度造成一定影响,U形时,角度为90°,转角处的熔高与直壁处没什么区别;而三角形在小角度30°处的层高达到48 mm,与直壁处相差较大。这说明,角度过小时在转角处会发生比较大的尺寸偏差。实验结束后,每个堆积件随机测量15个点的堆积熔高以及其熔宽,并进行统计分析,结果如表2所示。由表2中数据可知,堆积件的壁高和壁宽的尺寸标准差值控制在1 mm范围内。
图9是齿轮件轮廓原件及打印修复件对比图,两零件相似度极高,可见3D打印技术可以在零件的修复中发挥巨大作用;利用实验所得参数进行3D打印堆焊熔积成形时,所得成形件成形良好,精度较高。
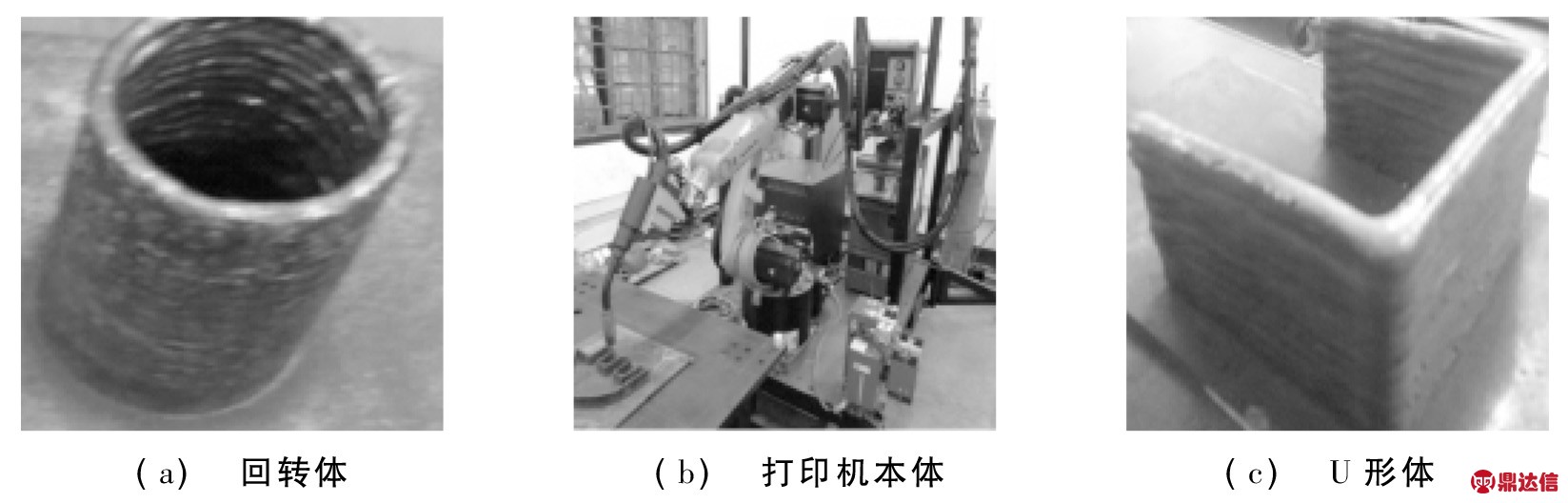
图8 在线金属弧焊3D打印系统本体及打印件
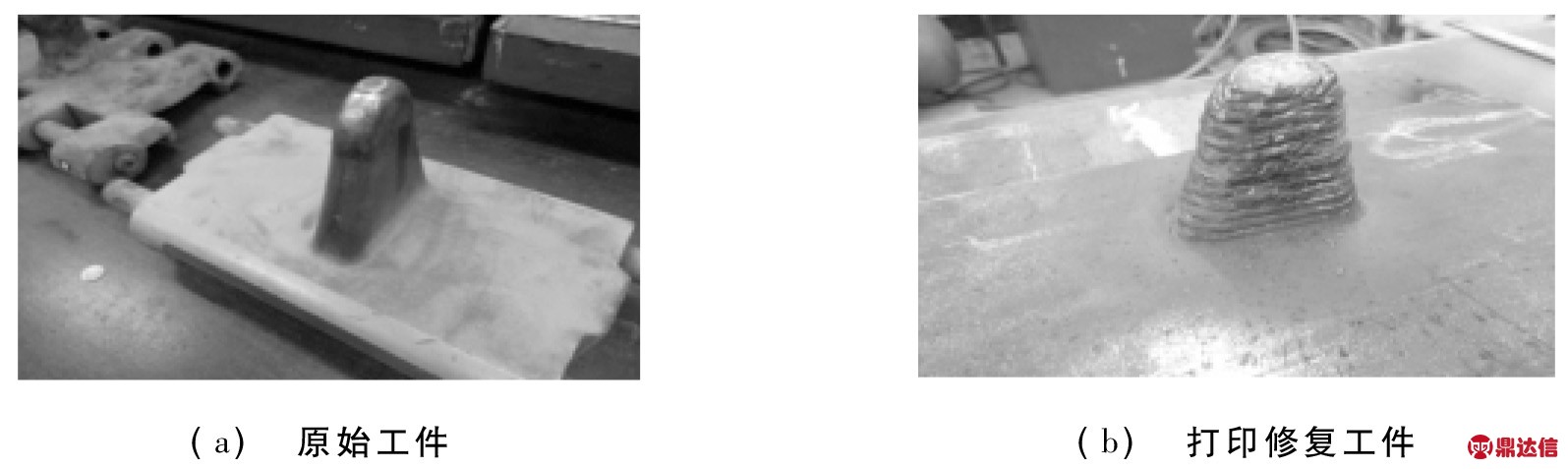
图9 齿轮件轮廓原件及打印修复件图
表2 不同形状打印层高、层宽数据测量值 mm
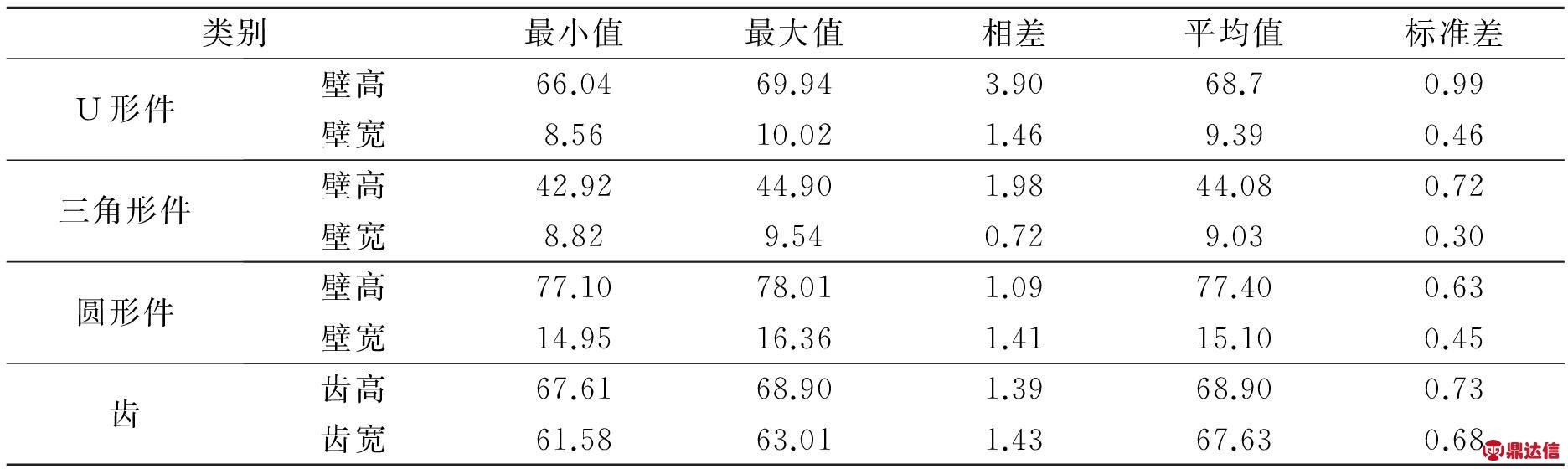
5 结论
针对不同制件应采用不同的工艺参数,以此实现对打印件质量的实时控制;可以在同一制件的不同地方采用不同分层参数提高零件的形状和尺寸精度;通过进一步优化速度、电压和电流等打印工艺参数,可以得到一套能保证尺寸精度的工艺参数数据库。