摘 要: 通过腐蚀试验、恒电流加速试验以及耦合性能试验,研究了铝合金和锌合金作为牺牲阳极材料在高温稠油输送管道中的适用性。结果表明:随着温度升高,两种阳极材料的腐蚀速率增大,实际电容量和电流效率减小,消耗率增大,使用寿命降低。在80 ℃条件下,铝阳极的腐蚀速率和消耗率均低于锌阳极的,且与T/S-52K管线钢的耦合电位更负,耦合电流更大,阴极保护作用更显著,而锌阳极在80 ℃下的工作电位高于最小保护电位,不满足GB/T 21448-2017标准的要求。铝合金较锌合金更适合作为高温稠油输送管道的牺牲阳极材料。
关键词: 稠油输送管道;内嵌牺牲阳极;铝合金;锌合金
稠油是黏度较高,密度较大的原油。因稠油黏度较高,在输送过程中需要加热,并采取保温措施,这使得管体温度较高,钢制管材腐蚀加剧。由于防护保温层的屏蔽作用,目前常用的外加电流阴极保护技术无法对其实现有效保护[1-7]。因此,改进稠油输送管道的阴极保护技术显得尤为重要。
常用的稠油输送管道阴极保护技术改进措施主要有三种:① 使用固体电解质以实现外加电流阴极保护,但该方法施工维修程序复杂、成本高,在长距离管线上的适用性较差,仅适用于短距离管段的腐蚀防护(如穿越管线套管内的管道防护);② 喷涂牺牲阳极涂层,然而涂层质量难以控制,使用寿命较短,价格较高;③ 直接将牺牲阳极安装在保温层内,该方法可对进水后的保温管线进行阴极保护,适合安装在保温层内的牺牲阳极包括带状阳极和片状阳极,带状阳极可沿管线轴向铺设,保护距离长[8-10]。受到油井套管使用的手镯式牺牲阳极的启发,本工作拟通过将牺牲阳极安装在保温层内对稠油输送管道进行防护。目前,常用的牺牲阳极材料有铝合金、锌合金和镁合金三大类。由于镁阳极电流效率低,消耗快,且容易析氢和诱发火花,不适合作为高温稠油输送管道保温层下长寿命牺牲阳极。因此,选择铝合金阳极和锌合金阳极,通过腐蚀试验、恒电流加速试验以及耦合性能试验等,综合探讨不同阳极材料在高温条件下的适用性,以期筛选出适合保护稠油输送管道的阳极材料。
1 试验
1.1 试验材料及试验条件
试验用铝合金阳极为Al-Zn-In系,锌合金阳极为Zn-Al-Cd系,化学成分见表1和表2。管线钢为T/S-52K钢,化学成分见表3。试验介质为模拟稠油管道服役环境的土壤溶液,化学成分见表4。试验温度分别为20,50,80 ℃。
表1 铝合金阳极的化学成分
Tab. 1 Chemical composition of aluminum alloy anode %

表2 锌合金阳极的化学成分
Tab. 2 Chemical composition of zinc alloy anode %

表3 T/S-52K钢试样的化学成分
Tab. 3 Chemical composition of T/S-52K steel sample

表4 土壤溶液的化学成分
Tab. 4 Chemical composition of the soil solution mg/kg

1.2 试验方法
1.2.1 腐蚀试验
将两种阳极试样加工成尺寸为50 mm×10 mm×3 mm的挂片试样。试验前采用砂纸(400~1 500号)逐级打磨试样表面后,用蒸馏水清洗,再用无水乙醇去除表面的油污,随后及时将试样放入烘箱,烘干30 min,烘箱温度为105±2 ℃,取出后尽快放入干燥器内,将阳极挂片自然冷却至室温后进行第一次称量。然后重复烘烤、称量步骤,直至两次称量结果差值小于0.4 mg,取两次称量结果的平均值为阳极挂片的试验前质量。将装有土壤溶液的锥形瓶放入恒温水浴中,水浴温度分别为20,50,80 ℃,将阳极试样置于土壤溶液中7 d进行腐蚀浸泡试验,试验结束后将试样取出,去除表面腐蚀产物,干燥后称量,参照式(1)计算试样的均匀腐蚀速率(vcorr)。
(1)
式中:vcorr为均匀腐蚀速率,mm/a;m0和m1分别为试验前后试样的质量,g;S为试样的总面积,cm2;t为试验时间,h;ρ为试样的密度,g/cm3。
1.2.2 恒电流加速试验
根据GB/T 17848-1999《牺牲阳极电化学性能试验方法》,对铝阳极和锌阳极进行电化学性能测试。铝阳极试样尺寸为φ28 mm×16 mm,锌阳极试样尺寸为φ50 mm×9 mm。电化学性能测试采用Corrtest310H电化学工作站,辅助电极和参比电极分别采用铂金片状电极和饱和甘汞电极(SCE)。试验结束后,计算阳极实际电容量、电流效率以及消耗率,并对阳极表面腐蚀形貌进行观察。
1.2.3 耦合性能试验
耦合性能测试采用Corrtest310H电化学工作站,使用尺寸为φ15 mm×3 mm的圆形试样,将导线焊接在试样一个端面,用环氧树脂和截取的PVC管对试样进行密封并使其固化,保留一个工作面积为1.75 cm2的圆形工作面,用水砂纸(400~1 500号)逐级打磨试样工作面,最后依次用蒸馏水、丙酮、无水乙醇清洗去油脱水,冷风吹干待用。管线钢试样工作面积为30 cm2,阳极与阴极面积之比为1∶17。工作电极与阳极试样连接,参比电极采用饱和甘汞电极,将铝阳极、锌阳极分别与管线钢试样用导线连接,接地线与管线钢试样连接,测定阳极耦合电位和耦合电流。
2 结果与讨论
2.1 腐蚀试验
由图1可见:随着土壤溶液温度的升高,两种阳极试样的腐蚀速率均增大,当温度为20 ℃和50 ℃时,两种阳极试样的均匀腐蚀速率均较小且相差不大;当温度升至80 ℃,锌阳极试样的均匀腐蚀速率为0.326 6 mm/a,而铝阳极试样的仅为0.179 3 mm/a。这说明铝合金适合作为管道内嵌牺牲阳极材料。
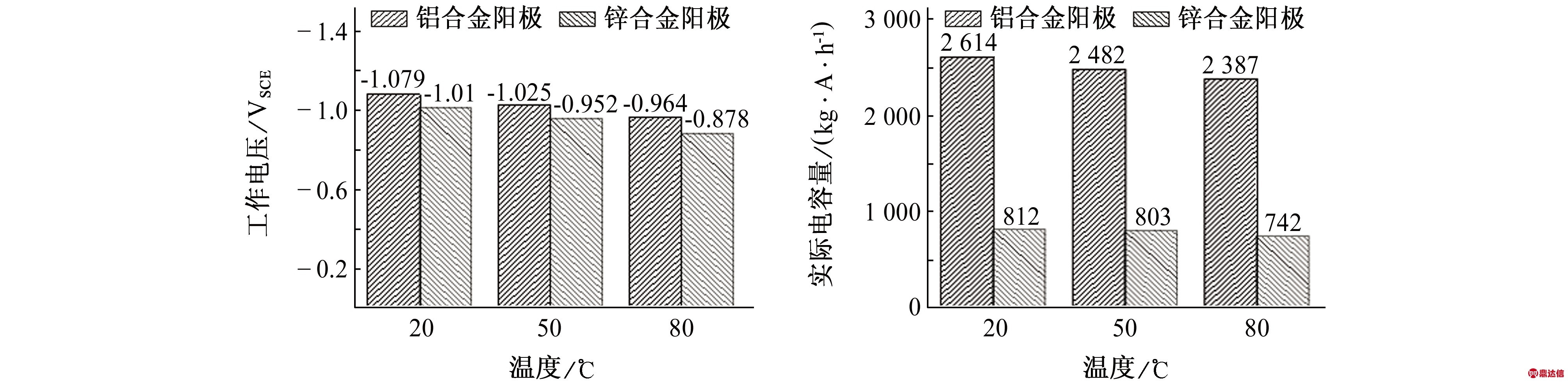
图1 两种阳极试样在不同温度试验溶液中浸泡7 d后的腐蚀速率
Fig. 1 Corrosion rates of two anode samples immersed in test solutions at different temperatures for 7 days
由图2可见,在80 ℃试验溶液中腐蚀7 d后,铝合金表面腐蚀均匀,且由图3(a)可见其未出现晶间腐蚀,说明铝合金阳极在高温条件下,其生成的钝化膜阻隔了Zn和In等活化元素及其“溶解-再沉积”的过程,进而使活化作用减弱。此外,根据热力学规律,铝合金在高温下也更易钝化,这一结果也说明铝阳极在高温下钝化反应更明显[11]。许多研究表明合金的耐蚀性与晶界的状态密切相关[12],由图3可见,温度达到80 ℃时,锌合金表面发生晶间腐蚀,试样表面明显粗糙,颜色加深,腐蚀程度加剧,并且由图3(b)也可以发现其晶间腐蚀,表明铝合金阳极在高温环境中的使用性能更好。
2.2 恒电流加速试验
由图4可见:随着温度的升高,铝阳极和锌阳极的工作电位均正移,且在测试温度范围内,铝阳极的工作电位均低于GB/T 21448-2017标准要求的最小保护电位(20 ℃时:-0.777 V;50 ℃时:-0.825 V;80 ℃时:-0.881 V。锌阳极在20 ℃和50 ℃时的工作电位满足标准要求,但温度升至80 ℃,其工作电位为-0.878 V),高于最小保护电位,不能满足标准要求。由图5可见:两种阳极试样在不同温度条件下,均以均匀溶解为主,未出现局部溶解显现。随着温度的升高,两种阳极试样表面腐蚀加剧。相较于锌阳极,铝阳极试样表面随着温度上升腐蚀更为严重。这说明锌阳极电位随温度升高而正移,与上述工作电位结论吻合,说明锌阳极表面覆盖层结构发生了变化,当温度超过55~60 ℃时,锌阳极表面覆盖层中Zn(OH)2变为ZnO,后者具有电子导电性,使锌阳极电位随温度升高而正移[13-15]。
由图4还可见:随着温度的升高,两种阳极的实际电容量以及电流效率均呈减小趋势,这表明温度升高,阳极的使用时间减少,寿命降低。三种温度条件下,铝阳极的消耗率更低,表明铝阳极的使用时间更长。目前使用微电偶模型来阐述牺牲阳极消耗率高的原因,但当材料发生晶间腐蚀时,仅用微电偶模型解释就不够完整[16-18]。由图3可知,锌阳极在80 ℃时发生晶间腐蚀,晶间腐蚀引起晶粒脱落,锌阳极基体无法分解为离子提供保护电流,白白浪费材料。该结果表明铝阳极在高温环境中使用的时间更长。

(a) 铝合金,20 ℃ (b) 铝合金,50 ℃ (c) 铝合金,80℃
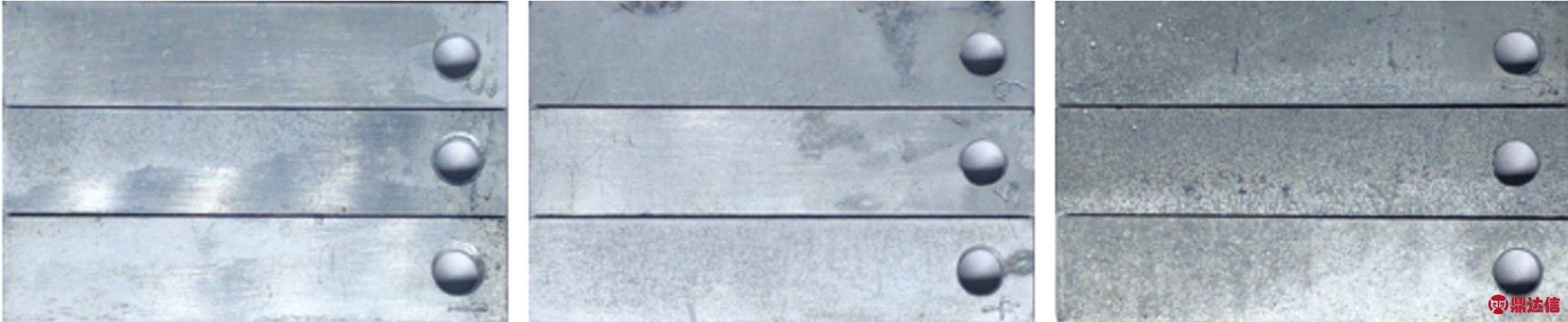
(d) 锌合金,20 ℃ (e) 锌合金,50 ℃ (f) 锌合金,80℃
图2 两种阳极试样在不同温度试验溶液中浸泡7 d后的表面宏观形貌
Fig. 2 Surface macro morphology of aluminum anode samples (a,b,c) and zinc anode samples (d,e,f) immersed in test solution at different temperatures for 7 days
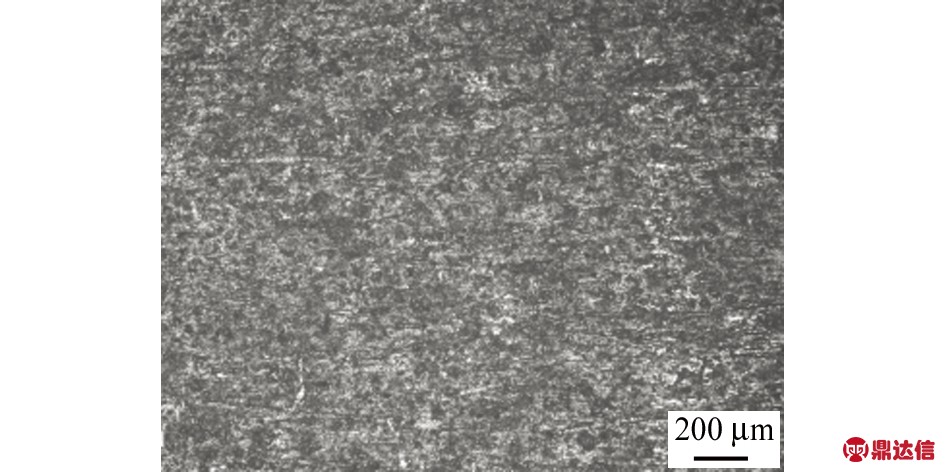
(a) 铝合金
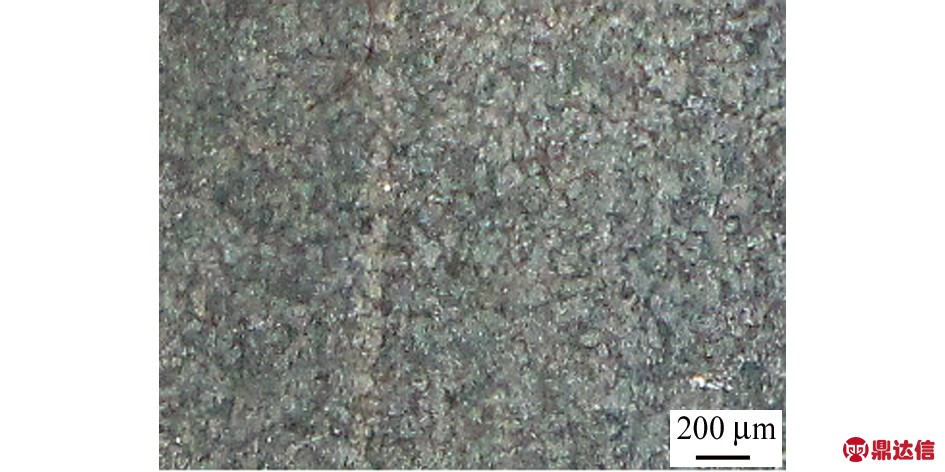
(b) 锌合金
图3 两种阳极试样在80 ℃试验溶液中腐蚀7 d后的表面微观形貌
Fig. 3 Surface micromorphology of Al alloy (a) and Zn alloy (b) samples after corrosion in 80 ℃ test solution for 7 days
2.3 耦合性能试验测试结果分析与讨论
由图6可见:当温度为20,50,80 ℃时,铝阳极与管线钢的耦合电位分别为-1.109 V,-1.095 V和-1.054 V,锌阳极与管线钢的耦合电位分别为-1.045 V,-1.020 V和-1.013 V,铝阳极与管线钢的耦合电位比锌阳极的更负。由图7可见:当温度为20,50,80 ℃时,铝阳极与管线的钢耦合电流分别为0.425,0.263,0.25 6 mA,锌阳极与管线钢的耦合电流分别为1.000,0.225,0.168 mA。综合对比发现,在80 ℃高温条件下,铝阳极与管线钢的耦合电位更负,耦合电流更大,表明铝阳极更适合高温稠油输油管道服役环境。这是因为在高温条件下,铝合金表面会生成一层致密的钝化膜,阻碍腐蚀阴离子(如Cl-、SO42-等)的进入,进而减缓腐蚀进程,致使耦合电位发生负移。并且耦合阴极金属表面的还原反应仅仅发生在钝化膜的薄弱处,增大了活性点的数量,使得耦合电流变大[19]。
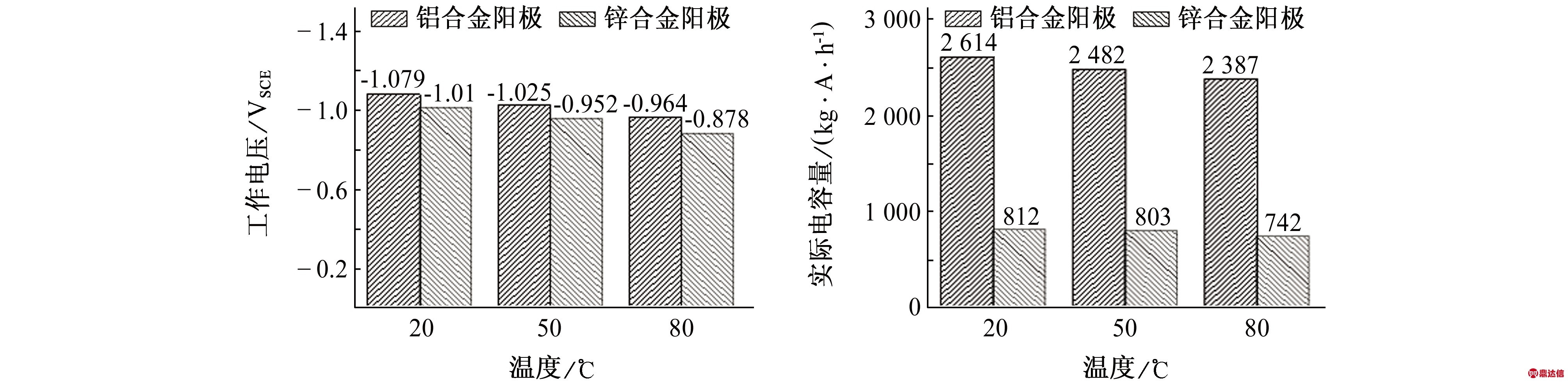
(a) 工作电位 (b) 实际电容量
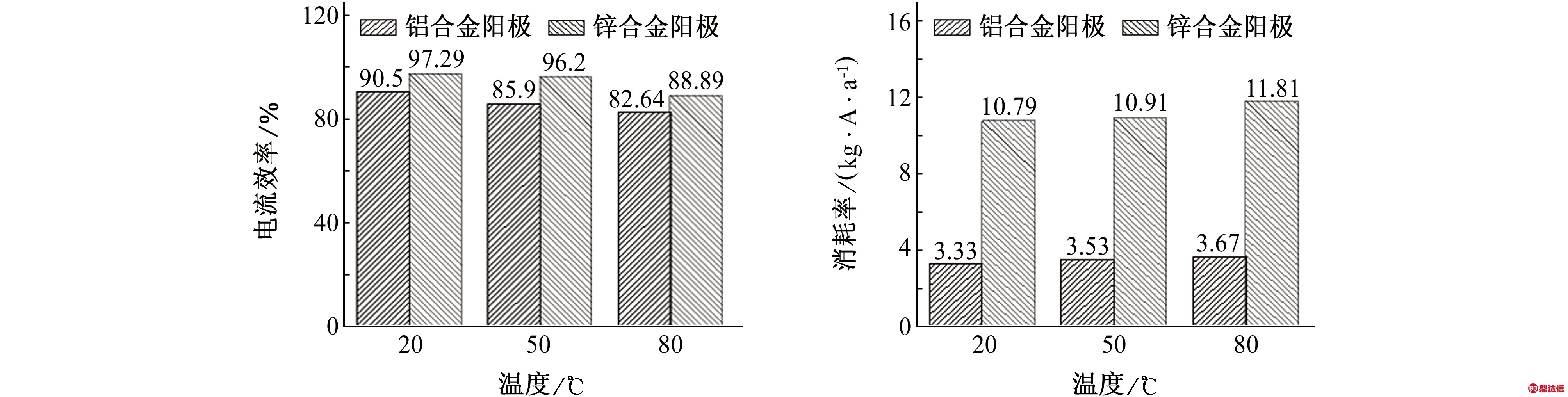
(c) 电流效率 (d) 消耗率
图4 不同温度条件下,两种阳极的恒电流加速试验结果
Fig. 4 Constant current acceleration test results of two anodes under different temperature conditions: (a) working potential; (b) actual capacitance; (c) current efficiency; (d) consumption rate

(a) 20 ℃铝合金 (b) 50 ℃铝合金 (c) 80 ℃铝合金

(d) 20 ℃锌合金 (e) 50 ℃锌合金 (f) 80 ℃锌合金
图5 不同温度条件下,两种阳极试样经恒电流加速试验后的表面宏观腐蚀形貌
Fig. 5 Under different temperature conditions, surface macro corrosion morphology of aluminum anode samples (a,b,c) and zinc anode samples (d,e,f) after constant current acceleration test
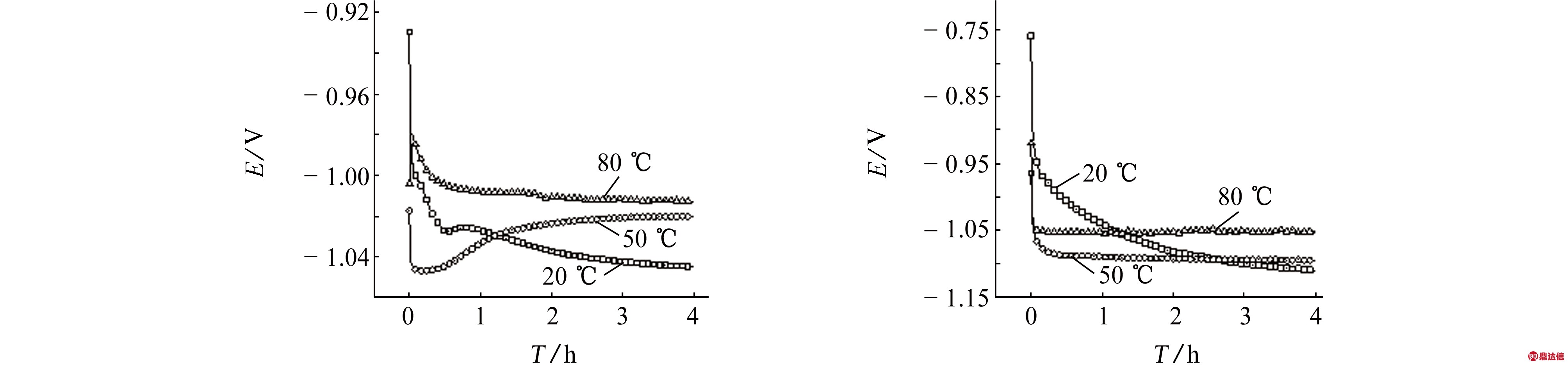
(a) 铝合金 (b) 锌合金
图6 不同温度下的耦合电位测试曲线
Fig. 6 Coupling potential test curves at different temperatures: (a) aluminium alloy; (b) zinc alloy
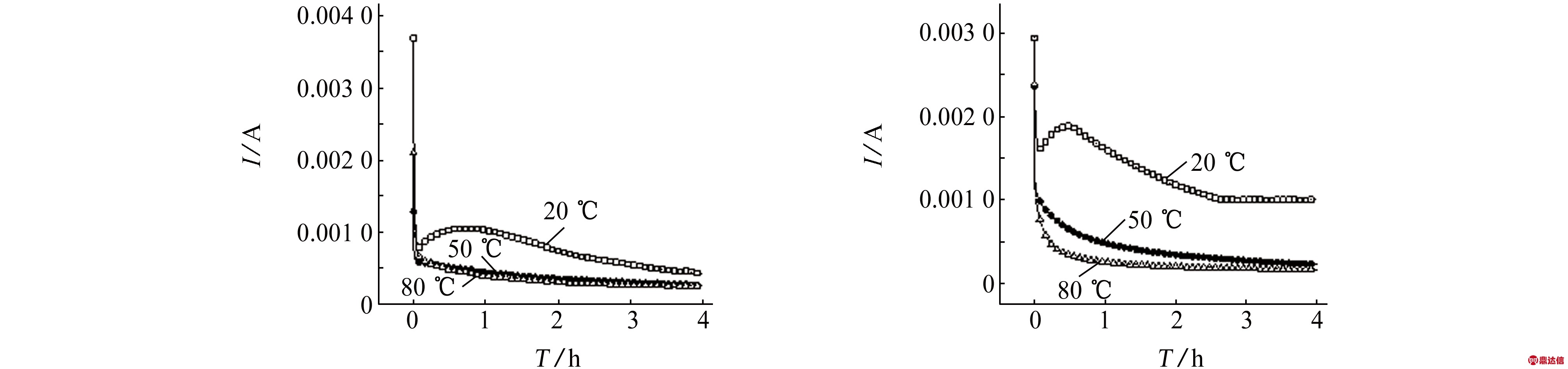
(a) 铝合金阳极 (b) 锌合金阳极
图7 不同温度下耦合电流测试曲线
Fig. 7 Coupling current test curves at different temperatures: (a) aluminium alloy; (b) zinc alloy
3 结论
(1) 随温度升高,铝阳极和锌阳极的腐蚀速率均增大,较低温度下(20 ℃和50 ℃),两种阳极的均匀腐蚀速率相差不大,但当温度达到80 ℃时,锌阳极的均匀腐蚀速率明显高于铝阳极的,并且发生晶间腐蚀。
(2) 锌阳极在80 ℃高温条件下,工作电位高于最小保护电位,不满足GB/T 21448-2017标准要求,无法提供有效阴极保护。铝金阳极在测试温度范围内的工作电位均符合标准,而且消耗率更小,使用时间更长。
(3) 在测试温度范围内,铝阳极与T/S-52K管线钢的耦合电位比锌阳极的更负,而且在80 ℃高温度条件下,铝阳极与管线钢的耦合电流更大,阴极保护作用更显著。
(4) 综合两种阳极材料自腐蚀性能,电化学性能和耦和性能,铝合金更适合作为高温稠油输送管道的牺牲阳极材料。