摘 要:文章首先介绍了冷挤压内螺纹的特点及性能要求,并列举了挤压内螺纹与切削内螺纹的区别。其次介绍了国内外内螺纹冷挤压净成形工艺的发展史和研究现状,并阐述了内螺纹冷挤压技术的原理及内螺纹成形效果。最后,对内螺纹冷挤压净成形工艺未来的发展趋势进行了展望。
关键词:螺纹连接;内螺纹冷挤压;成形原理;高精度
前言
内螺纹冷挤压工艺是一种金属塑性变形加工,这种加工方式是在工件上预制好相应尺寸的底孔,将挤压丝锥导入工件预制底孔中,在扭矩的作用下,丝锥的挤压棱齿逐渐挤入预制底孔内壁,底孔内壁上的金属沿着挤压棱齿表面流动,堆积在丝锥的螺纹槽内,从而形成内螺纹[1-2]。
传统的内螺纹加工方式一般采用切削丝锥攻丝或者螺纹车刀车削[3]。在生产实践中,常用切削丝锥进行内螺纹攻丝,其原理是利用切削丝锥上按顺序排列的切削刃将工件预制底孔内壁上的金属依次切除,形成内螺纹廓形,属于连续切削工艺。但切削丝锥攻丝时,切削量的控制不容忽视,特别是在硬度低,粘性大和容易产生长条形切屑的材料上攻丝时,切屑极易在排屑槽内积聚,造成切削中断甚至丝锥折断。而车削加工则是在多轴机床或车床上,用螺纹车刀或小规格整体式镗刀车削螺纹,但车削方式不能加工出小直径内螺纹,且通常需要连续多次走刀才能获得精确尺寸的内螺纹[4-5]。
1 内螺纹冷挤压工艺的特点
挤压内螺纹相比于切削内螺纹具有以下优点:
1.1 提高内螺纹的强度
内螺纹冷挤压时,工件底孔内壁上的金属处于三向压应力状态,若此时金属发生塑性变形,材料内部的晶粒发生滑移,晶格扭曲,金属纤维呈连续的流线型,组织结构紧密,使螺纹的强度大幅提升,抗拉强度提高20%以上,抗剪强度提高5%~10%,内螺纹表面的冷作硬化层厚度约为0.15 mm,硬度提高40%以上[1]。
1.2 提高内螺纹精度
使用挤压方式加工的内螺纹,螺纹孔扩张量极小,挤压过程中内螺纹的形位误差小,内螺纹的成形精度较高,成形质量稳定[6]。
1.3 提高内螺纹表面质量
内螺纹冷挤压过程中,挤压丝锥的挤压棱齿表面对内螺纹表面产生挤光作用,成形后的内螺纹表面光洁度极好,表面粗糙度可以达到Ra0.4~0.8 [7]。
1.4 节约材料
内螺纹冷挤压工艺是利用金属的塑性变形从而形成内螺纹,加工过程中没有切屑产生,所以又称为“无屑攻丝”,大幅提升材料的利用率[8]。
1.5 适合深孔和盲孔加工
由于挤压过程中不需要清除切屑,从而避免了因排屑困难或切屑拥塞而导致的丝锥崩刃、折断[9]。
挤压内螺纹与切削内螺纹表面形貌的区别如图1所示,挤压内螺纹因金属沿着丝锥挤压棱齿表面向中间流动聚拢,牙顶存在U形口,螺纹截面金属组织结构紧密;切削内螺纹是利用切削刃将多余金属切除,螺纹截面整齐,牙顶的形态由底孔直径决定。

图1 挤压内螺纹与切削内螺纹表面形貌
2 内螺纹冷挤压技术的研究现状
内螺纹冷挤压工艺的发展空间巨大,在航空航天、汽车、精密仪器制造等领域应用前景广泛,其主要研究内容包括以下几个方面[10-13]:
(1)挤压丝锥结构参数的进一步优化、设计及制造。
(2)挤压加工过程中的工艺参数,例如挤压丝锥的结构参数、工件预制底孔直径、挤压速度、润滑液种类和工件材料等。
(3)在有色金属及其合金,低碳钢及硬度较低的调质钢、合金钢、不锈钢以及合金工具钢等材料上挤压中小直径的内螺纹。
20世纪50年代,内螺纹冷挤压技术刚刚兴起,由于缺少实践应用和深入研究,挤压内螺纹时扭矩极大,且挤压过程中产生大量的热,挤压丝锥的寿命很低。70年代后,英国BAJ Vickers Ltd公司在铬钼钢上尝试挤压小直径内螺纹,随着高性能材料的出现,挤压丝锥的性能也得到有效提升,国外的内螺纹冷挤压技术不再局限于加工抗拉强度小于600 MPa、延伸率大于12%的有色金属和合金钢[14]。
20世纪60年代,日本的隈部淳一郎开始系统研究振动攻丝技术,由于其可以大幅降低挤压扭矩和挤压温度,很快引起其他学者的关注,随后俄罗斯、美国等也在此项技术中开展研究,直到60年代末,我国才开始对该技术进行初步探索。梁瑜轩等人[15-17]设计了一套如图2所示的低频振动攻丝系统,其振动方向沿螺纹升角方向,并且在Q460高强度钢材料上进行了初步试验,研究了激振频率和激振力对挤压扭矩的影响,研究结果表明:振动挤压攻丝时挤压扭矩较低,螺纹成形质量较高,表面形貌规整,并且振动攻丝可改善内螺纹表面的冷作硬化均匀程度,使其机械强度得到有效提高。
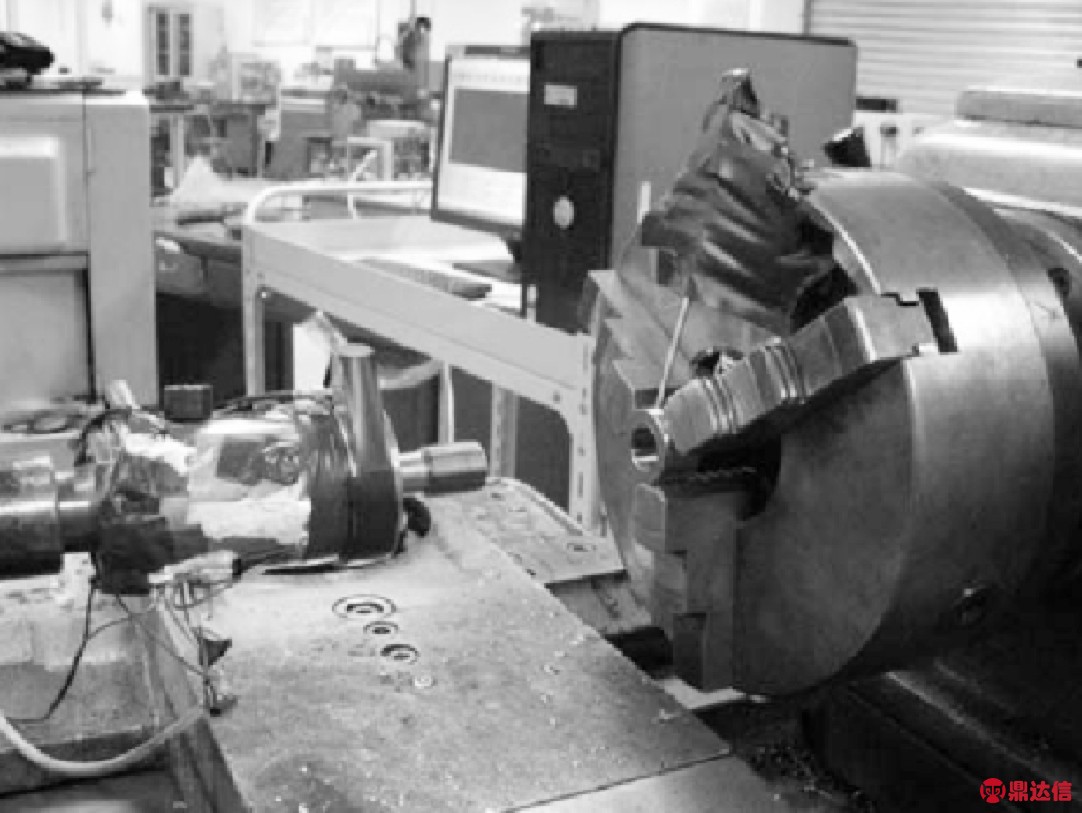
图2 振动攻丝系统
Yongyi Li、黄小龙等人[18-22]简化了内螺纹挤压的有限元模型,如图3所示,分析了金属流动规律和振动辅助技术对挤压攻丝的影响机理,并基于数值模拟技术对内螺纹冷挤压成形的工艺参数进行了优化,结果表明:预制底孔直径和摩擦系数对挤压扭矩的影响最大,攻丝速度对挤压温度的影响最大,振动挤压攻丝技术可以有效降低挤压扭矩,提高螺纹加工精度和表面质量。
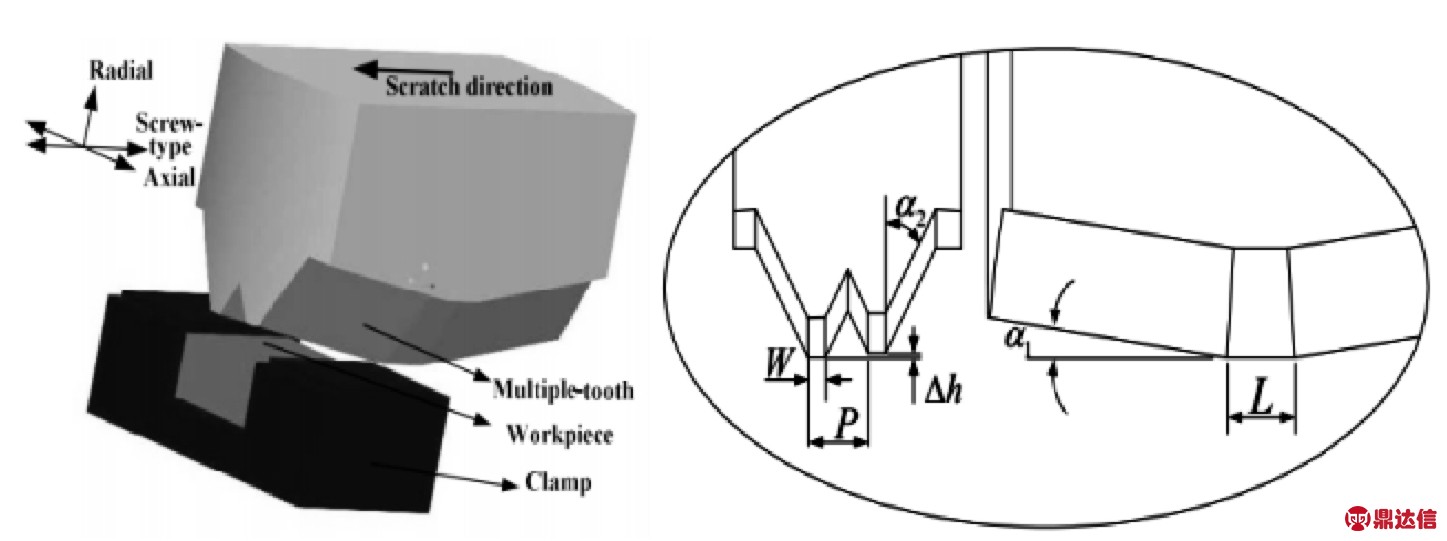
图3 Yongyi Li简化的有限元模型
B.M.明沙柯夫[22]系统地介绍了挤压丝锥的结构参数设计、理论计算以及工艺参数的确定方法,为研究者提供了理论依据。国内王珉等人[23]根据内螺纹冷挤压的成形机理对底孔直径的计算公式进行了修正,并分析了冷挤压内螺纹的抗疲劳性能和增寿机理,得到了内螺纹牙高率与螺纹强度的关系。
Bratan P N和刘志峰等人[24-25]基于有色金属和纯铝材料的塑性变形实现内螺纹冷挤压工艺,介绍了这些材料的优点,并优选了加工工艺参数。徐九华、王珉等人[26-27]在300M高强度钢和35CrMo钢上应用内螺纹冷挤压工艺,搭建了挤压扭矩和挤压温度的在线监测系统和螺纹成形质量测量系统,并对冷挤压内螺纹的抗疲劳机理进行了研究。杨名大等[28-29]针对钛合金材料的内螺纹加工困难的问题开发了切削-挤压复合攻丝技术,解决了抗疲劳制造在钛合金连接构件上的应用难的问题。
目前,国内外对于内螺纹冷挤压工艺的研究主要集中在高强度材料、底孔直径的计算方法、挤压丝锥结构参数的设计优化以及加工过程工艺参数优化等方面,主要在一些高强度钢、特种金属、有色金属及其合金等材料上进行小直径或超大直径内螺纹冷挤压试验探究。
3 内螺纹冷挤压工艺简介
3.1 挤压丝锥
内螺纹冷挤压工艺是利用挤压丝锥在工件预制底孔上进行挤压,图4为挤压丝锥的结构。
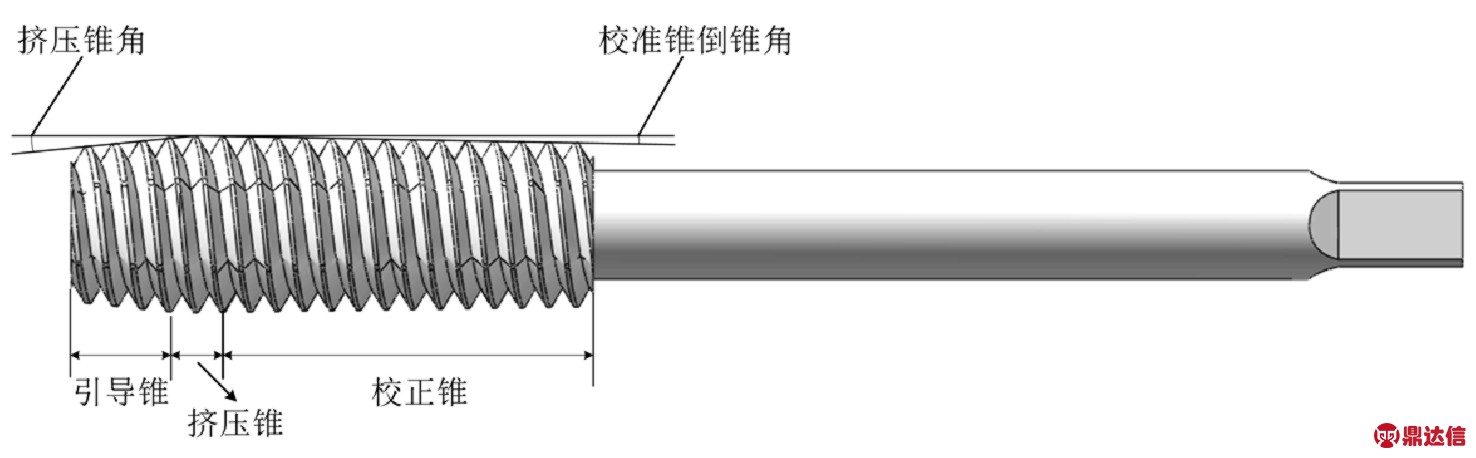
图4 挤压丝锥的结构
挤压丝锥的种类有很多,通常按照不同的使用场合选择挤压丝锥,当挤压材料强度较高、螺纹尺寸较大时,挤压过程较为困难,通常选择带润滑油槽的六棱挤压丝锥;当材料塑性较好,螺纹尺寸较小时,挤压过程相对容易,通常选择带引导锥的无槽挤压丝锥。图5为几种常见的挤压丝锥。
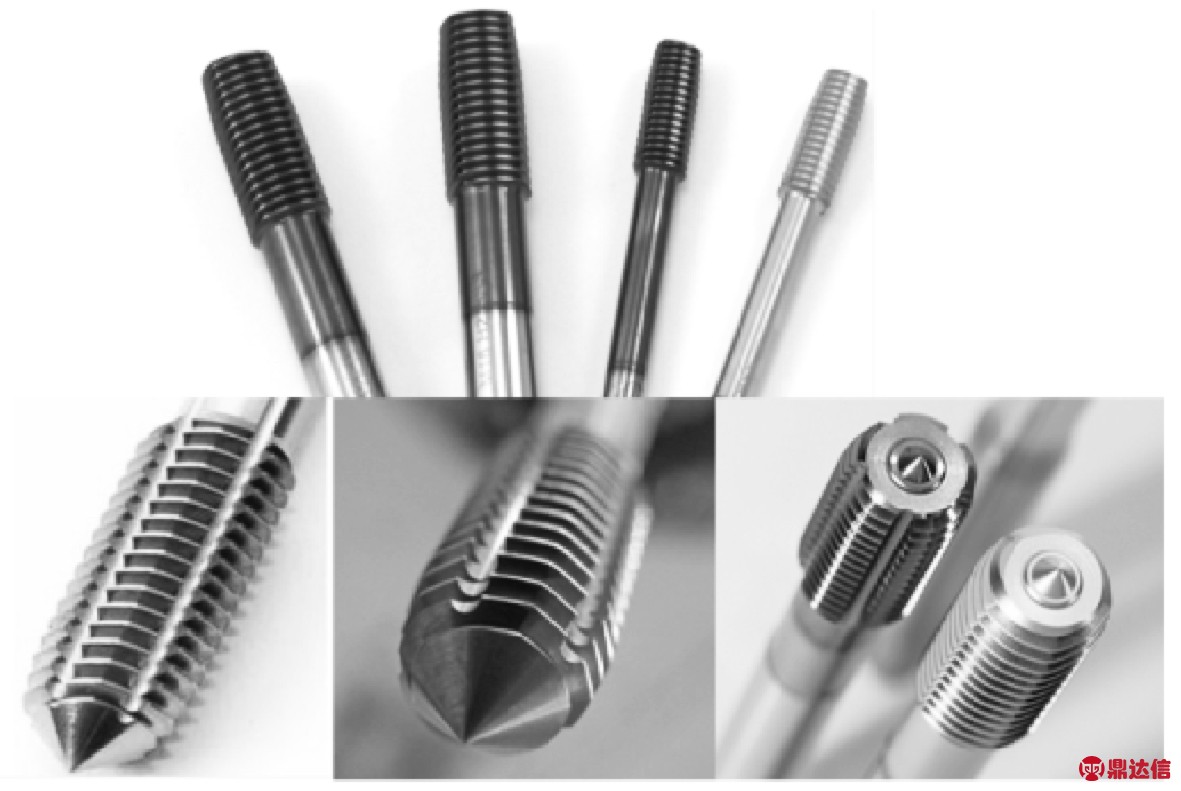
图5 几种常见的挤压丝锥
3.2 内螺纹冷挤压原理
内螺纹冷挤压成形过程如图6所示,由于挤压丝锥的横截面是一种特殊的曲边棱形,所以在挤压过程中,工件底孔内壁上的变形区金属承载周期性变化的负荷,变化频率与丝锥的棱数和机床转速有关。当挤压丝锥最前端的挤压棱齿挤入时,底孔内壁上的金属产生弹塑性变形,当这个挤压棱齿离开后,材料产生一部分的弹性恢复,塑性变形则被保留;随着丝锥旋转,第二个挤压棱齿再次对此处进行挤压,材料再次发生弹塑性变形,此棱齿离开后,材料再次产生一部分弹性恢复,保留塑性变形,以此类推,当挤压丝锥的所有棱齿全部离开后,底孔内壁上形成了完整的内螺纹牙形。
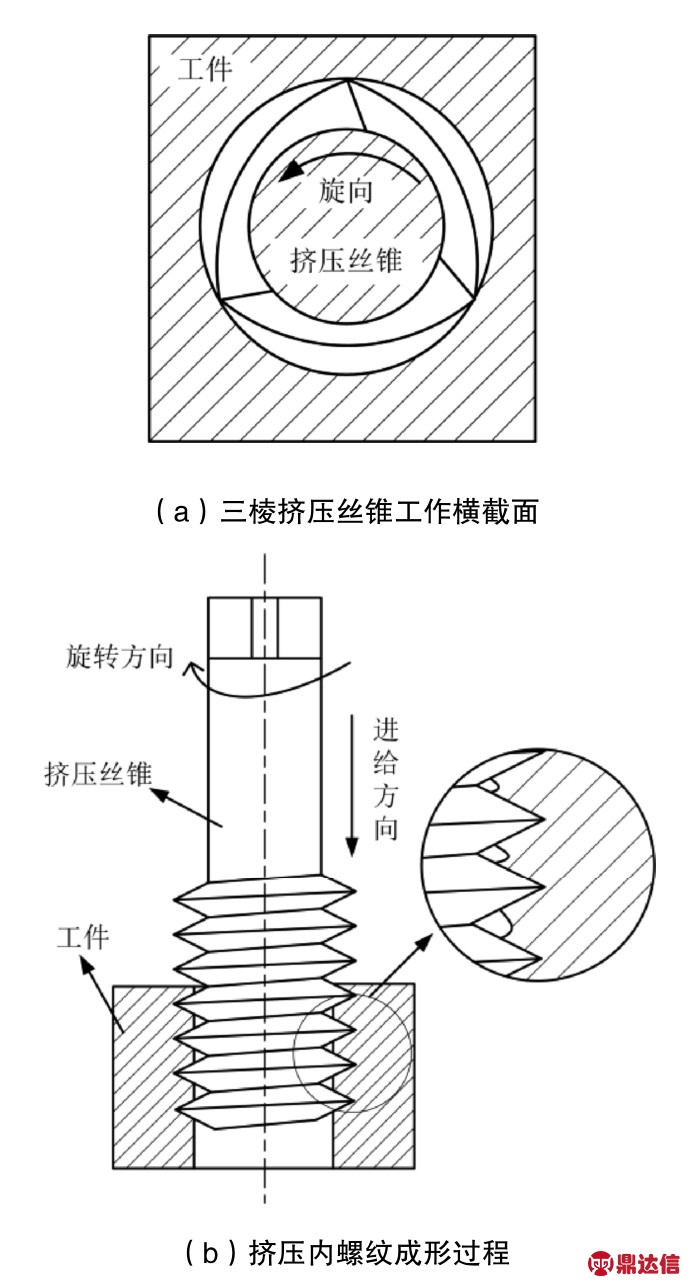
图6 内螺纹挤压成形原理
4 内螺纹冷挤压技术的发展趋势
由于我国制造业的迅猛发展,内螺纹冷挤压工艺的应用领域越来越广,挤压丝锥、工装夹具等的市场也越来越大。现代科技的不断发展对内螺纹冷挤压技术产生了极大的影响,例如计算机对内螺纹冷挤压技术中的工艺分析、制造及工艺过程的控制及丝锥设计的影响。未来内螺纹冷挤压净成形工艺的发展趋势应包含以下几点:
4.1 扩大应用范围
目前,内螺纹冷挤压工艺通常应用在航空航天、汽车、精密仪器制造等领域,一般工厂中,若无特殊加工要求,内螺纹的加工仍然是以切削攻丝为主。内螺纹冷挤压技术是一种绿色、无污染的加工方式,螺纹使用寿命长,符合“绿色制造”理念。因此,扩大内螺纹冷挤压技术的应用范围势在必行[30]。
4.2 提高精度与表面质量
虽然冷挤压内螺纹的尺寸精度和表面质量相比于切削螺纹已经有了很大的提高,但是在一些超高精度的应用场合,使用冷挤压技术加工的内螺纹还要经过二次精磨和表面处理[31]。因此,要对内螺纹冷挤压净成形工艺进行合理规划,以满足超高精度的加工要求,并对加工后处理内螺纹表面毛刺、金属粘连的方法进行改善,提高加工表面质量。
4.3 扩大加工材料的范围
目前内螺纹冷挤压技术只适用于加工塑性较大的金属,例如铜、铝合金、低碳钢等断裂延伸率大于7%、抗拉强度小于1200 N·mm-1的材料;对于一些脆性材料如灰铸铁、AZ91(镁合金)或硅含量大于12%的金属则较难加工[32]。随着工业技术的发展,各种新型材料在高端制造领域的应用越来越广泛,为了满足构件之间的螺纹连接强度,内螺纹冷挤压技术必须在材料应用范围方面实现技术突破。
4.4 优化挤压丝锥结构参数
挤压丝锥的结构复杂、结构参数计算繁琐,而且对于内螺纹挤压加工,挤压丝锥必须要根据螺纹的规定参数、性能要求等条件进行结构的定制设计[11]。在内螺纹挤压过程中,工件金属变形区会产生大量的热,挤压丝锥也承载着极大扭矩,挤压温度和扭矩直接影响着丝锥的使用寿命以及内螺纹的成形质量。挤压丝锥的结构参数是影响挤压温度和扭矩的关键因素之一,对其进行合理的优化可大幅提高丝锥的耐用度,降低生产成本。
4.5 工件预制底孔直径的计算
用挤压丝锥加工内螺纹之前,必须要确定适当的预制底孔直径,底孔直径的合适与否直接影响到内螺纹的成形[30]。如图7所示,若底孔直径过大,螺纹成形不完整,工件报废;若底孔直径过小,则容易造成挤压扭矩陡增、金属流动阻塞,使挤压丝锥卡死甚至折断。由于工件材料的变形量与其本身的塑性有关,即使相同大小的底孔直径在不同材料上的成形效果也不一样。目前在生产实践中一般根据经验公式对预制底孔直径进行大概估计,再进行多次加工调整。根据材料的塑性推导出合适的底孔直径计算公式,减小加工误差是内螺纹冷挤压工艺中的一项重要研究内容。
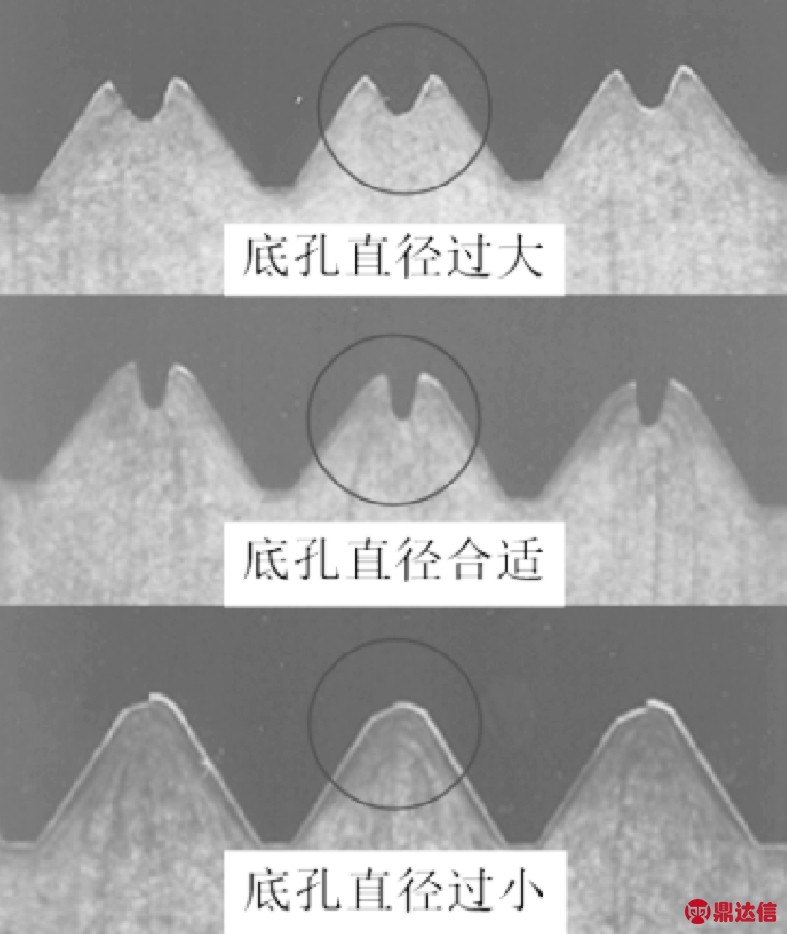
图7 底孔直径与内螺纹成形效果
4.6 发展热挤压、高速挤压等技术
由于一些特种金属材料强度极高,对挤压丝锥的使用寿命影响较大,所以发展热挤压工艺对特殊材料进行预热处理,再进行等温加工,会大幅降低挤压难度。虽然内螺纹冷挤压的加工效率已经是切削攻丝的2~3倍,但是生产节奏日渐高速化,内螺纹冷挤压的加工速度也需要提高[33]。
5 结语
随着制造业对加工精度、螺纹连接强度等的要求越来越高,内螺纹冷挤压净成形工艺将被应用到更多的领域。与切削内螺纹相比,冷挤压内螺纹的强度更高、精度更好、使用寿命更长,内螺纹的加工效率也更高,经济效益明显。冷挤压内螺纹的高强度、高精度、高寿命等一系列的优点可以满足大多数工作场景的需求。
许多国外的生产厂家在挤压丝锥的制造技术方面已经积累了大量的经验,其生产的高性能挤压丝锥几乎占据了国际市场的所有份额。国内的内螺纹冷挤压技术起步较晚,总体水平落后于国外,但随着越来越多的中国学者对此技术进行研究,内螺纹冷挤压技术已经逐渐接近先进水平。
由于内螺纹冷挤压技术在众多场合应用广泛,将会有越来越多的学者对其进行研究、开发。内螺纹冷挤压净成形工艺将会朝向宽应用、高精度、高质量、高效率的方向发展。