摘要:为了实现滚珠螺母型面的快速精确测量,提出了激光测量方法并设计测量装置。首先,基于经直角棱镜反射的点激光轴向扫描的测量原理设计了螺母滚道型面检测装置,并根据滚道的数学模型提出轴法向转换的数据处理方法。然后,对直角棱镜的平移和转角误差、激光偏移误差、激光倾斜误差建立模型进行分析。最后,设计工装对标准钢球和圆槽进行扫描,并对螺母滚道开展实际测量。结果显示,完成误差标定后,经棱镜反射的点激光扫描圆弧轮廓的测量误差在3.1 m以内,标准差在2.2
m以内。对螺母滚道的扫描图像完整有效,总体精度满足螺母滚道型面的测量要求。
关 键 词:型面检测;螺母型面参数;点激光扫描;数据处理;误差分析
1 引 言
随着数控机床在装备制造业的广泛应用,加工过程中对速度和精度的要求越来越高,对高精度滚珠丝杠副的需求越来越大。螺母作为滚珠丝杠副的滚珠循环承载装置,其滚道的精度对滚珠丝杠副的接触刚性、摩擦特性、精度保持性等均有较大的影响[1]。
滚珠螺母的型面是由具备滚道法向设计截形的砂轮水平移动伴随回转加工所形成的三维螺旋曲面,滚道型面的滚道半径、接触角、偏心距等参数是螺母滚道型面研究的重点[2]。对于螺母的型面检测,生产线上通常采用三针法测量螺母滚道中径,检测参数单一。由于螺母内部空间的局限性,在企业计量室内通常将它沿法向截面剖开,利用投影仪将图像与样板进行对比,判断是否在允许误差范围内;或使用专用粗糙度轮廓仪沿法向滚道逐个进行接触扫描,该方法需要专业人员安装调整,难以满足高效率的要求[3]。类似于滚珠螺母滚道,在对梯形螺纹等普通螺母的滚道测量中,2012年陈曼龙[4]采用垂直投影法对外螺纹进行测量,出现由螺旋升角造成的牙型失真现象,后期使用算法对遮挡点进行恢复,但效果欠佳。2011年,丁亮亮[5]设计了高精度单针接触式轮廓仪测量螺纹,但其测量对象为普通螺纹,不存在法向和轴向测量的要求。2013年,Rao等人[6]使用工业照相机对内螺纹进行多角度成像,然后对获取的影像完成多步骤的图像处理,最终得到螺纹中径等参数,但是该方法的测量精度受设备和测量环境的影响较大,且算法对几何尺寸的图像处理精度相对较低。2015年,要义勇等人[7]使用光纤伸入螺母内部完成对滚道的扫描,但该方法对于光纤头部的角度有较高要求,且当螺母导程较大时,不可避免地发生传感器与被测物的碰撞。2017年,王瑞等人[8]提出了相关的点激光检测方法,但缺少滚道建模和完善的数据处理,对轴向数据直接拟合误差较大,且没有涉及系统误差的标定补偿。
对于激光测量过程的误差研究,现阶段主要为激光测量本身存在的原理性问题以及由激光测头安装产生的误差影响,缺乏对滚珠螺母进行激光测量时系统误差的分析。2007年王世峰等人[9]在测量普通螺纹时,分析了检测系统中激光位移传感器的测距范围变化带来的能量分布误差,以及光栅尺的电信号频率引起的测量误差,但对系统误差的分析较少。2007年,吕东方等人[10]提出了利用双向倾斜扫描法去补偿激光三角法测量时的误差,但其测头结构较大,无法适应小尺寸和大范围型面的测量。2016年,张丽艳等人[11]研究了激光测量中测头的安装位置和姿态带来的误差,并提出了标定补偿方法。
本文综合对比前人的研究,提出了螺母滚道型面测量方法,并根据测量原理设计了针对滚珠螺母型面检测的自动化装置,同时建立了轴法向数据转换的测量模型。在此基础上,对直角棱镜安装误差、偏移误差、激光倾斜误差等主要系统误差进行了分析,还设计工装对标准圆弧和实际的螺母进行测量,在准确性和重复性两方面验证了方案的可行性。
2 测量方案
2.1 基于点激光的非接触测量方案
根据JB/T 17587.3-1998中对滚珠丝杠副的验收条件,针对螺母滚道型面的检测项目是其螺旋滚道的法向截形误差[12]。在滚珠丝杠副实际的传动中,滚珠同时与丝杠滚道和螺母滚道接触,而滚道接触部分的加工精度对产品的整体性能有重要影响,本文主要测量的部分为图1中经过高精度磨削的螺母滚道。

图1 测量对象(钢球与丝杠、螺母滚道的接触)
Fig.1 Measuring objects (steel balls with screw and nut raceway)
为了获取完整的滚道轮廓,如图2所示,采用激光三角结合直角棱镜的测量方案。刚性连接传感器与直角棱镜,并保持直角棱镜反射面与发射光线呈45°关系,使发射透镜出射的激光经过镜面反射后垂直射向内部滚道,经过滚道反射的光线会再次照射到镜面,并反射回到接收透镜。通过反射光线沿螺母轴向的移动扫描,得到滚道完整的轴向截面,再经过数据转化,最终获取滚道的法向型面参数。
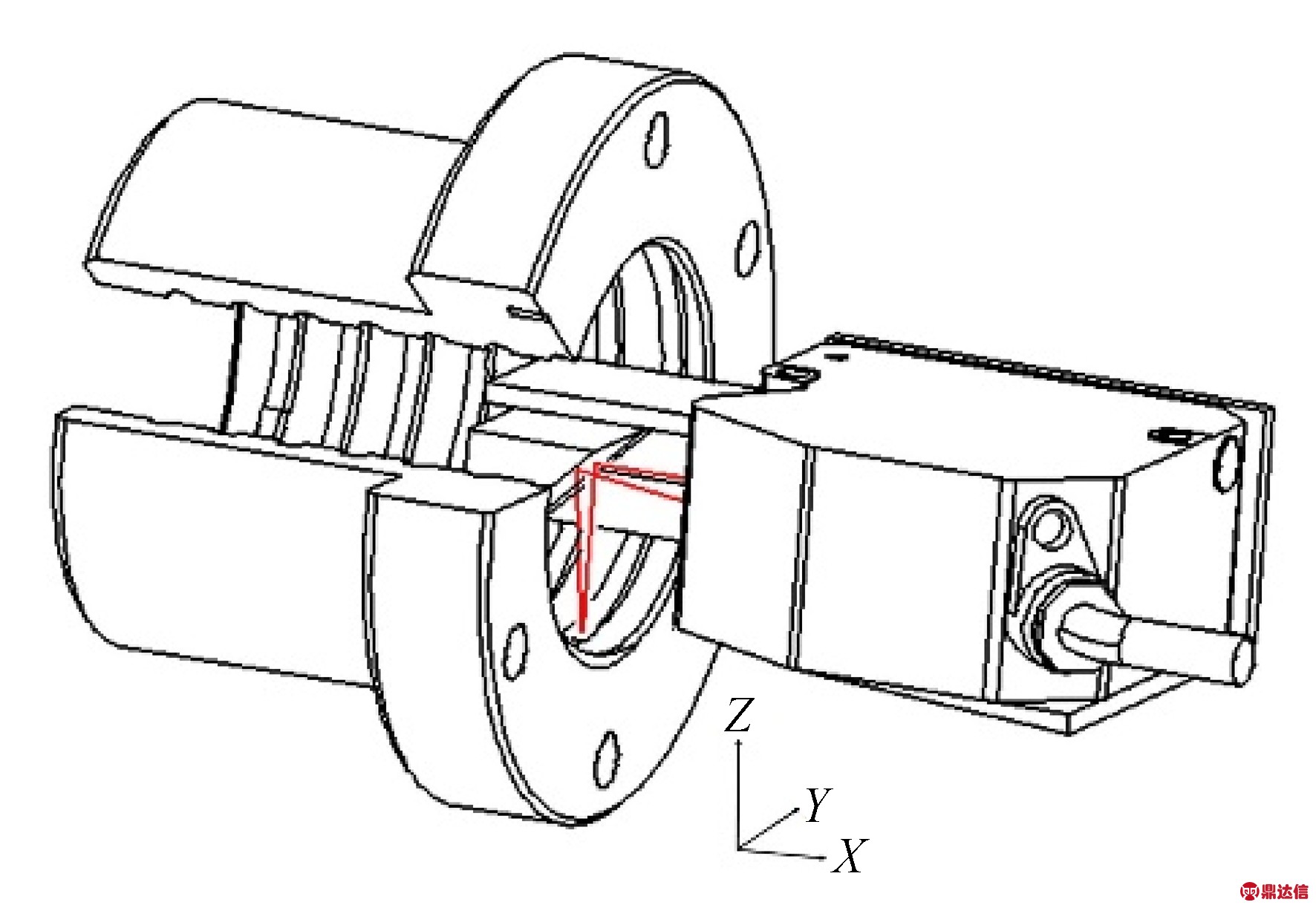
图2 螺母型面测量方案的传感器布局
Fig.2 Sensors layout in nut profile measurement scheme
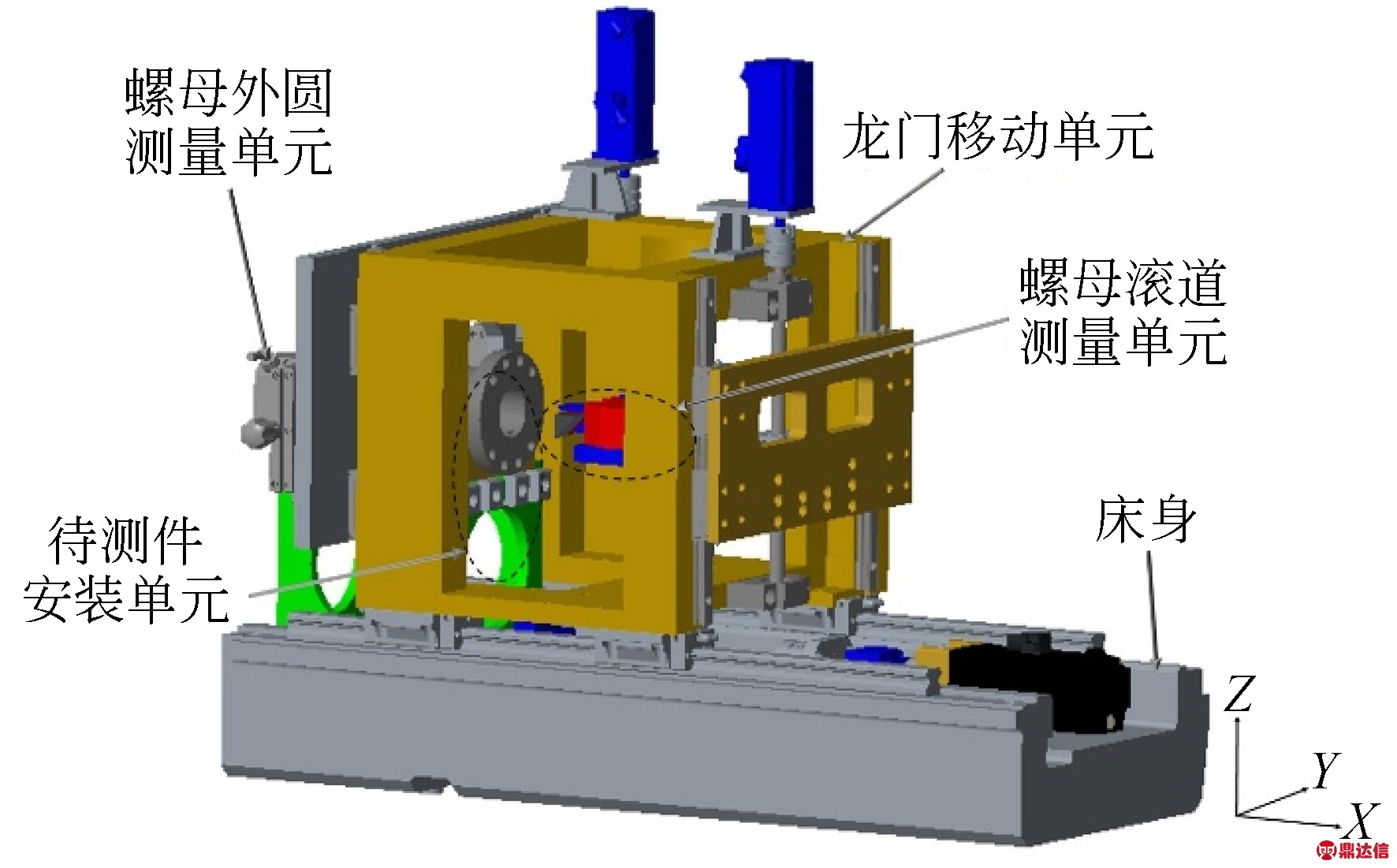
图3 螺母型面检测装置
Fig.3 Nut surface detecting device
根据所提出的测量原理,设计的专用检测装置如图3所示。在全局坐标系下,仿照三坐标测量仪结构,在底座上搭建龙门移动单元,固定待测件安装单元,由螺母滚道测量单元、螺母外圆测量单元的移动完成测量。主要的传动方式采用伺服电机驱动高精度滚珠丝杠副,运动部件由高精度直线导轨副搭载。3个伺服电机分别控制龙门移动单元沿X向移动,螺母滚道测量单元和螺母外径测量单元沿Z向移动。由激光位移传感器和直角棱镜组成的螺母滚道测量单元,调节好Z轴高度和Y轴位置后伸入螺母内部沿轴向扫描滚道,螺母外圆测量单元对称布置的两个传感器通过Z向移动完成螺母外径部分的扫描,最终经过多传感器数据融合处理获得滚珠螺母的型面精度。
综合考虑各种型号激光位移传感器的量程和精度,本方案选择基恩士高精度激光位移传感器LK-H050完成对螺母滚道和外圆的轮廓测量,具体传感器参数如表1所示。同时,在X轴安装海德汉光栅尺记录滚道测量单元移动的位置。
表1 激光传感器参数
Tab.1 Parameters of laser sensor
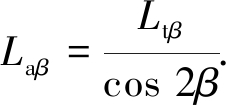
2.2 螺母滚道测量模型分析
本测量方案中,对螺母外径的测量可以简化为对圆棒的轮廓扫描,误差较易控制,难点在于对螺旋滚道的测量。由于滚道的型面参数在法向平面内描述,轴向扫描螺母内滚道,无法直接得到法向截形,需要进行坐标的转化。考虑到螺母内滚道与丝杠外滚道同为对称哥特式圆弧螺旋滚道,为了方便描述,以丝杠外滚道为目标建立轴法向转换模型。如图4所示,以中间滚道为研究对象,b平面为轴向截面,a平面为以滚道最低点为旋转中心旋转后的法向截面,需要将b平面内的数据点转化到a平面。
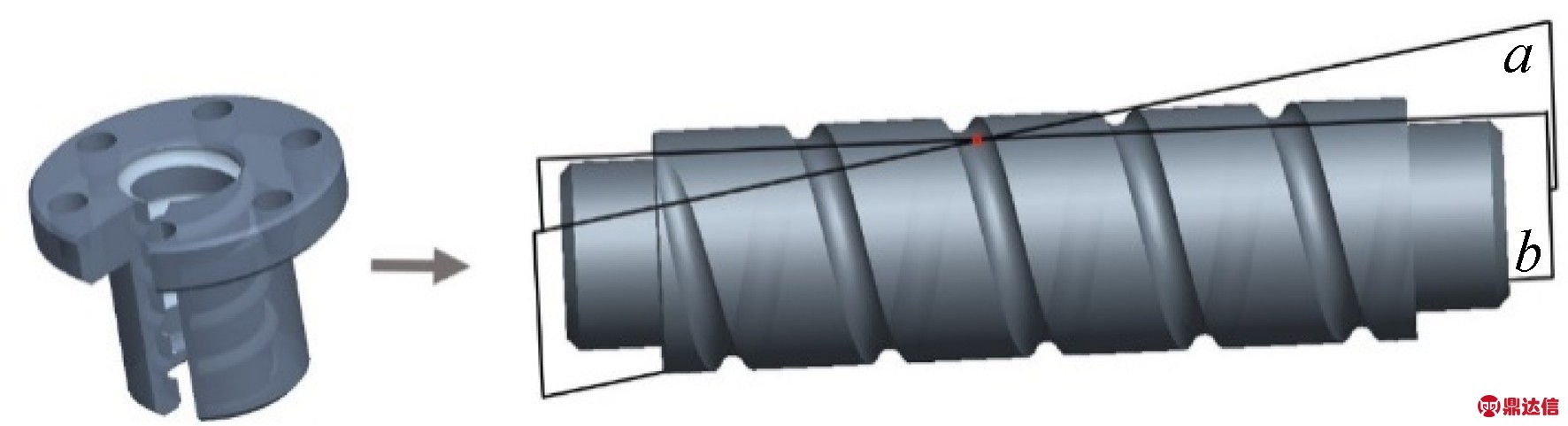
图4 螺母滚道测量模型分析
Fig.4 Analysis of nut traceway measurement model
2.3 螺母滚道测量数据处理
简化图4中的目标滚道截形,绘制相交的轴向平面和法向平面,两平面夹角为螺母滚道的导程角,主要是将轴向平面内的圆弧滚道坐标转换到法向平面内。考虑到滚道是由具有法向截形的砂轮磨削加工而成,砂轮旋转伴随着工件移动,形成螺旋滚道[2]。因此,轴向滚道上的任一点都处在一簇半径不同的螺旋线上,与法向平面相交,交点即为轴向平面数据点对应在法向平面内的坐标点,即将圆弧上的坐标点转换到圆弧
上。
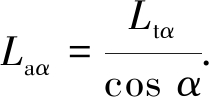
图5 轴向滚道测量坐标转换
Fig.5 Coordinate transformation in measurement of axial receway
建立全局笛卡尔坐标系O-XYZ,丝杠轴线与X轴重合,Z轴经过滚道最低点O′。以点A为例进行转换分析,将激光位移传感器和光栅尺测量得到的二维相对坐标点转换到三维空间坐标系中,则经过A点(xA,yA,zA)的螺旋线方程可以表示为:
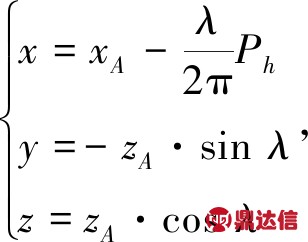
(1)
式中:λ为点A所属螺旋线在此点对应的旋转角(以X轴正向为基准,逆时针为正),Ph为丝杠导程。
轴向平面以滚道最低点为基准旋转导程角后,得到法向平面,则该平面内的点坐标之间存在三角函数关系,将螺旋线的坐标点对应到法向平面,得:
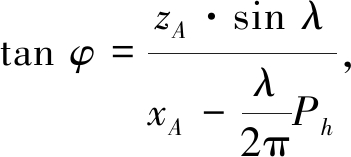
(2)
式中:φ为导程角,对螺旋线方程的参数的限制范围为
即可得到与法向平面的唯一交点。
此转换模型同样适用于滚珠螺母滚道的数据处理,基于此坐标转换,对轴向截面轮廓的测量提出了更高的要求,即滚道测量单元在扫描滚道之前,必须将它反射激光点的运动轨迹调整至经过螺母滚道最低点所在的轴线方向上。如果偏离此轴线,会产生激光偏移误差,使得扫描所得的轮廓偏小,即使经过坐标转化也无法得到真实的法向截形。在得到法向截面轮廓后,根据双圆弧滚道的特点,利用滚道中心线分割左右滚道,再根据滚道倒角和底部沟槽形状,设置分割线1和2,从而将滚道分为左右两段,如图6所示。
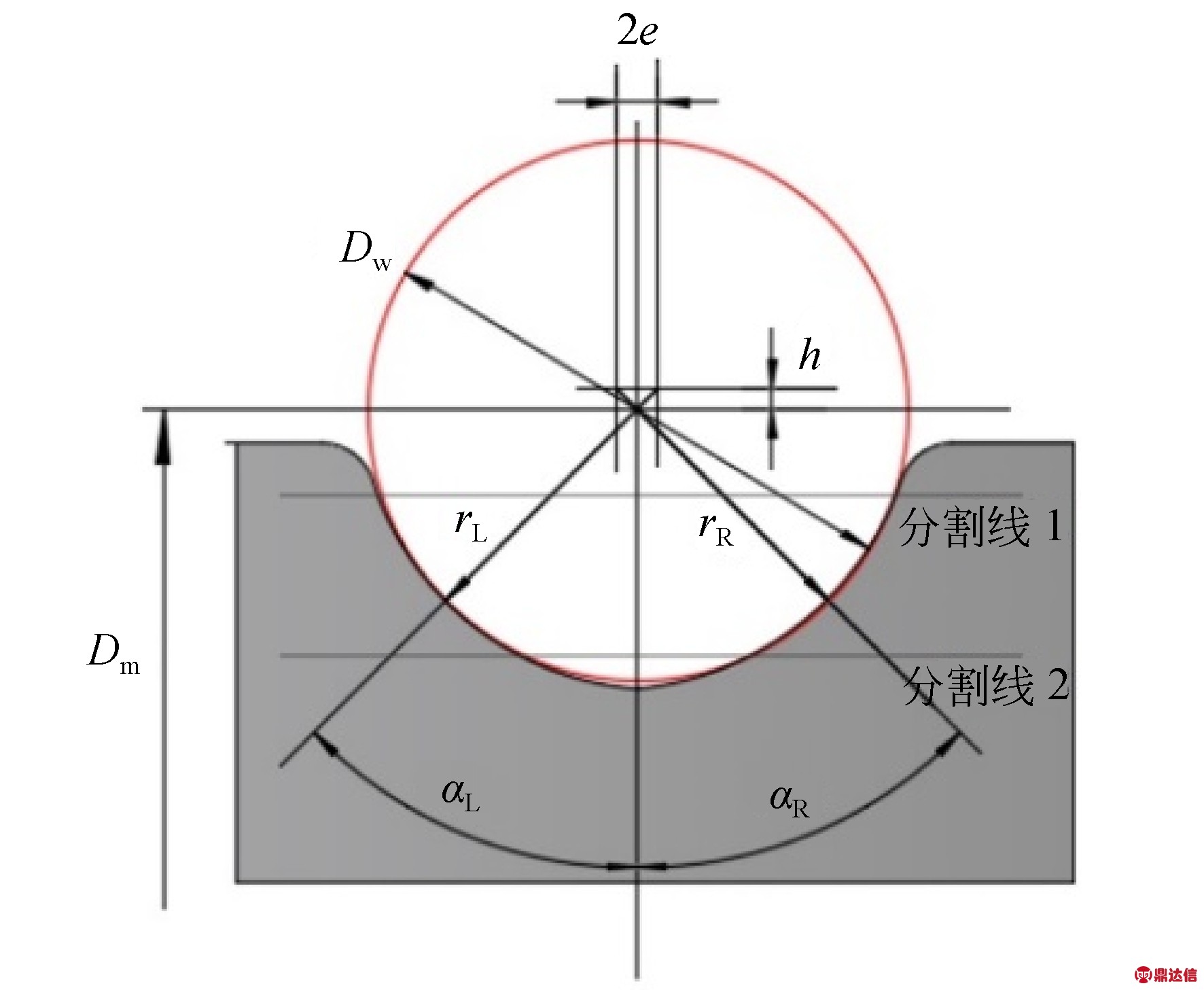
图6 滚道法向截面
Fig.6 Cross section of raceway
图6中,滚珠与滚道在法向截面接触,rL和rR为滚道左右圆弧半径,αL和αR为滚珠与滚道左右圆弧的接触角,e为轴向偏心距,h为径向偏心距,Dw为滚珠直径,Dm为滚道中径。
然后采用最小二乘法拟合圆弧:
f(xc,zc,r)=

(3)
式中:(xsi,zsi)为经过转换的左右滚道轮廓数据,i=1,2,…n,n为数据点的个数,(xc,yc)为经过拟合的圆心,r为拟合半径。同时,对圆弧数据点进行去噪点处理,将距离圆心较远的点认定为噪点,即有:

(4)
式中:(x′,z′)为噪点坐标,c为设定距离阈值。将式(3)计算出的圆心和半径代入式(4),设定阈值后去除圆弧上到圆心距离大的噪点,并重新利用式(3)拟合圆弧,得到相关参数。
结合目前工厂执行的抽样检测标准,对单个滚珠螺母内滚道检测项目为其法向截面误差,不同精度等级下允差值如表2所示。
表2 检测指标允差
Tab.2 Test indicator tolerance

可以看出,对1、2级和3、4级滚珠丝杠副的螺母其法向截面允差分别为12
m和
16
m,相关的检测方法精度需要在允差范围内。
3 误差分析
根据以上分析,法向截面经过拟合可以得到型面参数,但要保证测量数据的准确性,即将滚道测量单元调整至与螺母中轴线在同一垂直平面,且要保证反射激光垂直水平面照射到滚道上。直角棱镜的安装、激光照射位置、激光与被测物表面的角度,以及一些其他因素,都会对测量数据产生影响,下面对主要的系统误差进行分析。
3.1 直角棱镜安装误差分析
3.1.1 平移误差
直角棱镜的安装位置决定了激光照射的距离。如图7所示,当棱镜沿着X方向移动ΔX距离时,会使光线沿相应方向产生等距位移,相当于棱镜沿轴向的前后移动,不会对得到的轮廓图像产生影响;当棱镜沿着Z方向移动ΔZ距离时,会使光线沿相应方向产生等距位移,会改变激光的成像距离,只要保证在量程范围内移动且不与螺母内壁碰撞,不会对轮廓图像产生影响。
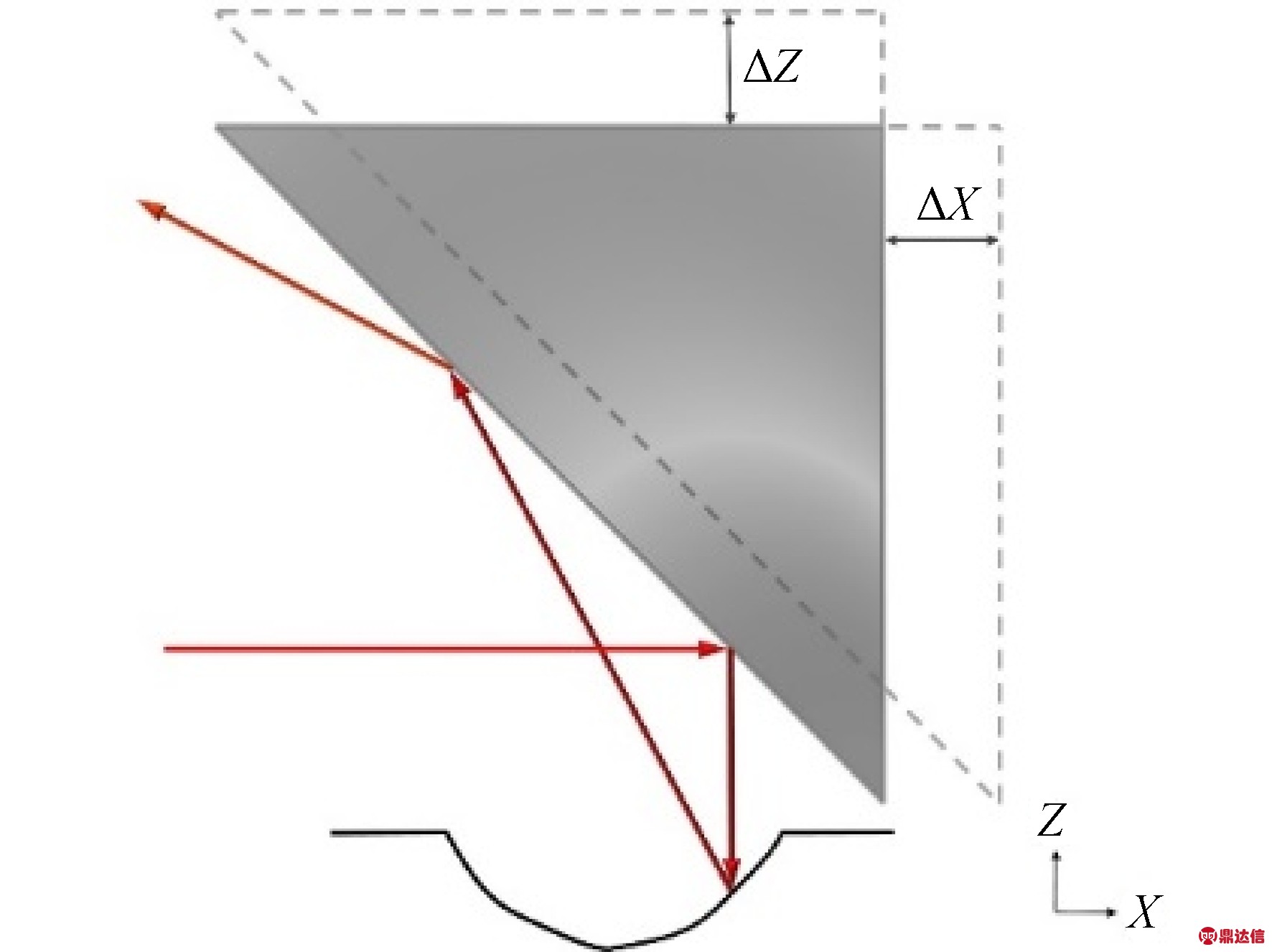
图7 直角棱镜平移误差
Fig.7 Translation error of rectangular prism
当棱镜沿着Y方向移动ΔY距离时,会改变激光照射在直角棱镜反射面上的位置,为了保证经滚道反射的光线可以更多地射入传感器的感光元件上,要保证入射激光尽量照射在棱镜边缘,否则会对测量点的数据产生影响。
3.1.2 转角误差
直角棱镜的安装角度决定了激光照射的角度,会对测量结果产生影响。当直角棱镜绕着X轴转过角度α,如图8所示,此时实际测量值会偏大,实际距离Laα与理论距离Ltα的关系为:
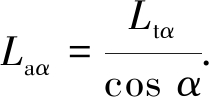
(5)
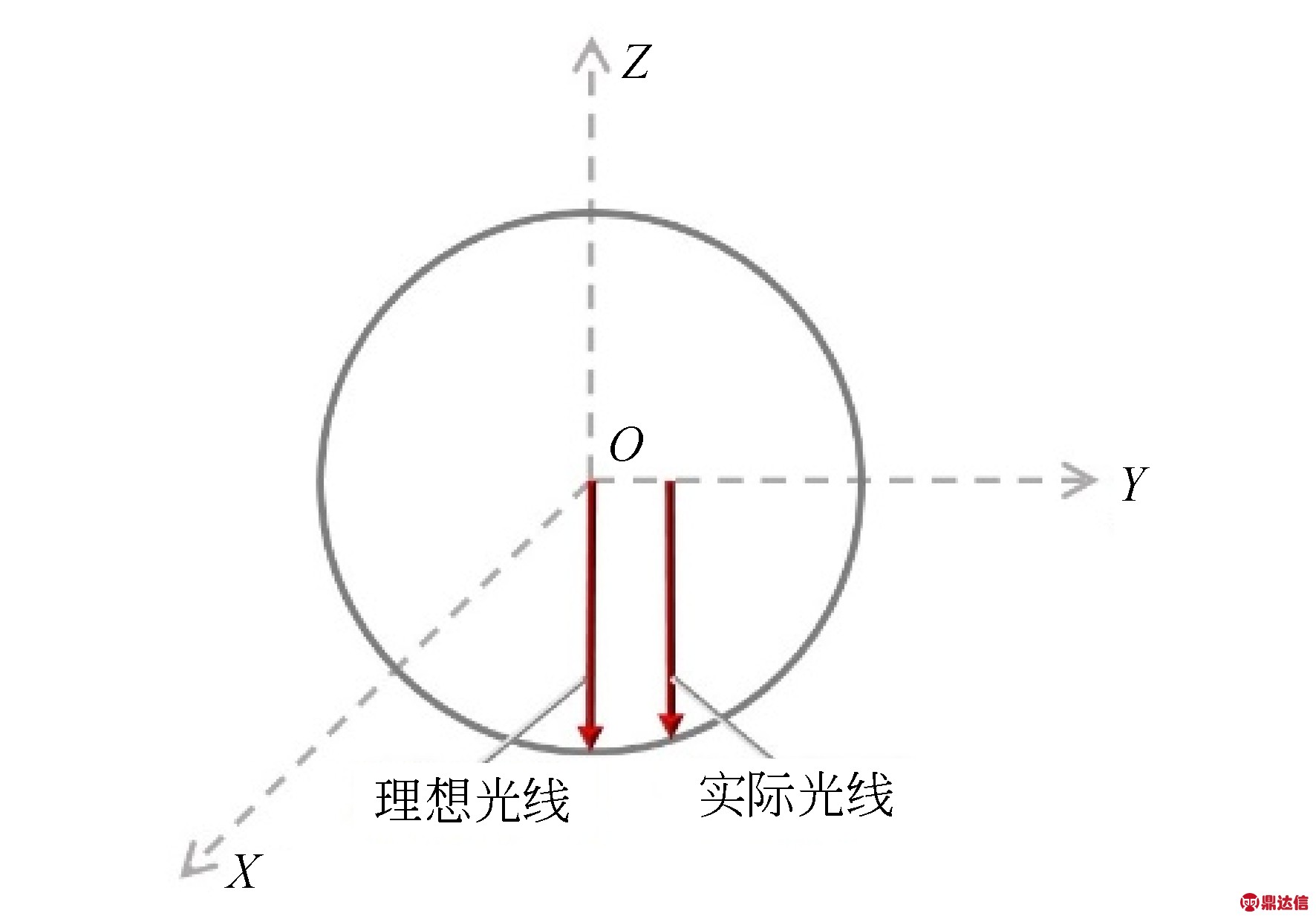
图8 直角棱镜转角误差(绕X轴)
Fig.8 Rotation error of rectangular prism around X axis
当直角棱镜绕着Y轴转过角度β,如图9所示,也相当于传感器存在转角误差,实际距离Laβ与理论距离Ltβ的关系为:
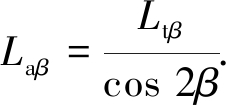
(6)
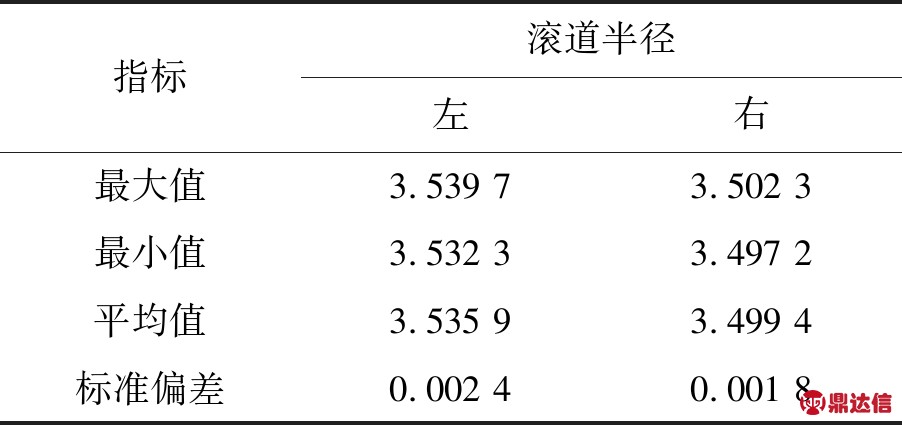
图9 直角棱镜转角误差(绕Y轴)
Fig.9 Rotation error of rectangular prism around Y axis
当直角棱镜绕着Z轴旋转时,不会影响到光线照射到滚道面的距离,不会影响测量结果。
3.2 激光偏移误差分析
为了保证激光扫描的轮廓为轴向滚道截面,本测量方案要求激光照射点在螺母上的移动轨迹与螺母的中轴线都处于XOZ平面内。当滚道测量单元未能调整至合适位置,经过直角棱镜的反射光线会发生偏移,如图10所示。考虑到螺母滚道为三维螺旋结构,偏移后扫描得到的图像虽形状相似,但尺寸相差较大,没有实际意义。
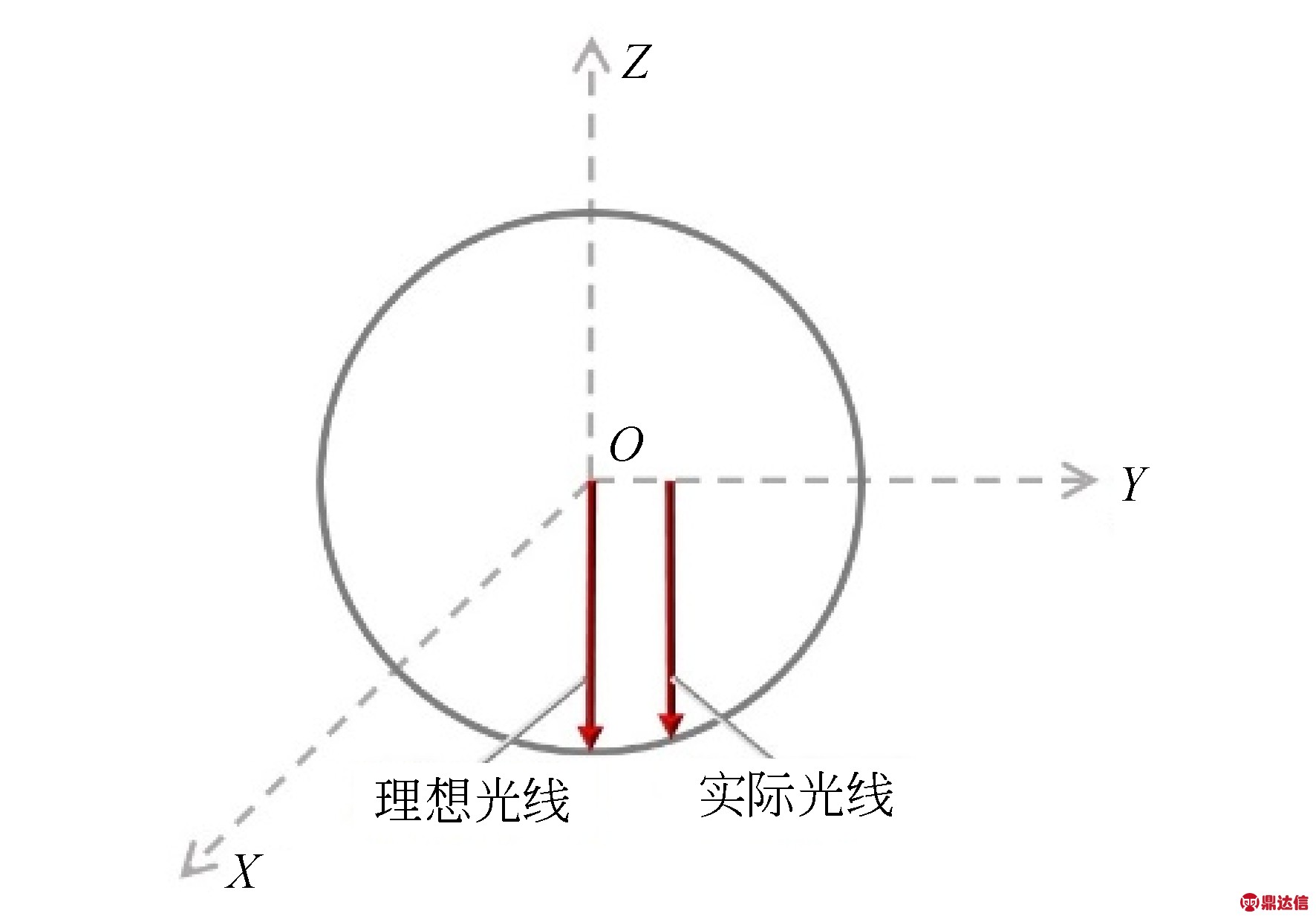
图10 激光偏移误差
Fig.10 Laser offset error
3.3 激光倾斜误差分析
3.3.1 激光倾斜照射模型建立
三角反射式激光位移传感器的测量原理是发射激光与物体表面保持垂直,此时接收光线可以全部返回接收透镜。如果发射光线与物体表面存在夹角,传感器接收透镜无法全部接收反射光线的能量,会改变感光元件上光斑所处的空间位置,而其内部的测量算法是计算光能质心的变化,使得测量值和实际值可能产生偏差[13]。
为了便于分析测量过程,对测量单元和激光的位置关系进行简化,将螺母滚道视为圆柱形曲面。激光在沿着轴向竖直扫描圆柱曲面的过程中,激光与滚道面的夹角在不断变化,因此假想出倾角时刻变化的平面作为圆柱面的切平面。还原实际测量过程,如图11所示,激光垂直于水平面扫描,当光线照射到圆柱面侧轮廓时,在照射点处圆柱的切平面可以近似看作垂直面。随着光线向圆柱面中心移动,照射点处圆柱的切平面与水平面的夹角γ在90°~0°内不断变化,对应的,光线与圆柱表面的夹角θ也在0°~90°内变化。
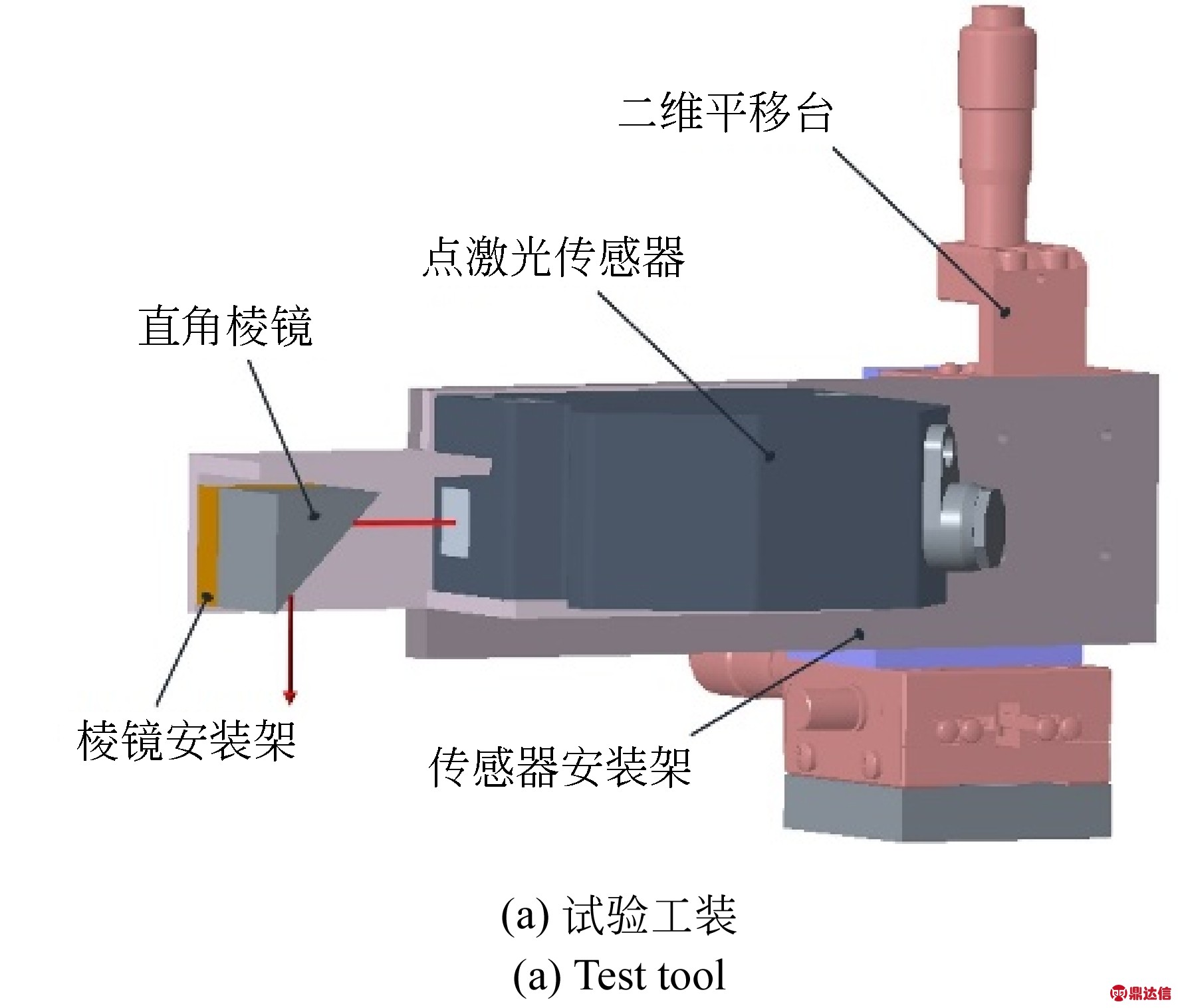
图11 光线倾斜模型
Fig.11 Light oblique irradiation model
考虑到实际的螺母滚道并非完整圆柱轮廓,不存在接触点切平面近乎与水平面垂直的情况,可避免光线大幅度散射。在通常情况下,光线与切平面的夹角可以保证接收透镜中入射的光能量,即光的能量中心的偏移程度很小,测量值与真实值较为接近。
3.3.2 照射表面的倾斜角分析
为了准确分析入射光线与被测物表面的夹角,需求出入射光线的方向向量,以及照射点所处单位曲面的法向量,对两个向量求向量积得到夹角。由于被测表面可视为圆柱形表面,且测量方式为激光沿直线扫描,选取圆柱表面上一微小曲面,对所研究入射点沿激光移动方向前后各取一个点,平行圆柱轴线方向前后各取一个点,组成十字形五点形式,如图12所示。

图12 圆柱表面5点分布
Fig.12 Five-points distribution on cylindrical surface
在圆柱曲面上分布有十字式相交曲线,过P0,P1,P2的曲线和过P3,P1,P4的两条曲线相交于P1,其交点处的法向量可通过u方向切向量和w方向切向量求外积获得[14]。在十字形五点组成的曲面上,通过3个点的Bezier曲线可以表示为:
P(u)=(1-u)2B0+2u(1-u)B1+u2B2,
(7)
其中:B0,B1,B2是Bezier曲线的控制点,当u=u0=0时,B0=P0;当u=u1时,当u=u2=1时,B2=P2。
求Bezier曲线的切线,对其表达式进行微分,得到:

(8)
因此对Bezier曲线中点处的切向量当u=u1时,有:
,
(9)


(10)
选用固定参数,令u0=0,u1=0.5,u2=1,此曲线可以化简为也可按照比例法,依据各点间弧长的比例来决定参数,则参数为:

(11)
通过扫描曲面后的数据处理,可以得到在曲线上3个点的坐标,代入式(11)求出Bezier曲线所含的参数和表达式,进一步得到该曲线在中心点处的方向向量。结合圆柱曲面的轴线方向坐标,求出过P3,P1,P4点的曲线在中心点处的方向向量,从而通过两向量的外积得到该微小曲面在中心点处的法向量n。考虑实际测量过程,入射光线的角度可以根据传感器的位姿标定得到,通过以上分析求解出入射光线与被测物表面的倾斜角。通过入射光线的移动,求解出入射光线在不同位置时与被测物表面的倾斜角,从而可以分析倾斜角的变化趋势。
3.4 其他误差分析
除了以上的主要系统误差外,还存在一些随机误差。测量环境的光照、温度,传感器发射光强及它到物体的距离导致的激光光点直径的变化,被测物的表面粗糙度和光泽、表面颜色等都会对测量结果产生影响,应尽量在调试阶段加以控制[15-16]。
激光测量试验应在温度为(200.5)℃、湿度为50%的恒温环境下进行,由白炽灯或荧光灯提供充足的环境照明(最大10 000 lux);传感器启动时要检查信号灯的发光强度,并静置一段时间以使激光发射器工作稳定,这些都可以有效降低传感器自身的误差。被测螺母滚道的金属表面对红光吸收能力较弱,且在试验准备阶段使用酒精擦拭螺母滚道灰尘。测量过程控制激光照射距离在50 mm左右,由于滚道半径本身较小,被测曲率半径远大于光斑直径,可以提高测量精度。
4 试 验
在检测的实际案例中,利用激光进行螺纹精密测量的应用较多,但研究对象大多为常见的普通螺纹和管螺纹,它们在几何形状和加工精度要求等方面与滚珠螺母滚道差别较大。为了验证所提出的测量方案,本文设计相关试验对利用激光扫描螺母滚道的检测精度进行验证。
4.1 试验装置
为了实现螺母滚道型面测量装置的运动关系,按照提出的测量方案开展预实验,设计的试验工装如图13(a)所示。实验工装由二维手动平移台、传感器安装架、棱镜安装架及直角棱镜等组成;二维手动平移台可使滚道测量单元在Y,Z方向移动以实现位置调节,将该测试工装安装在移动测量平台上,如图13(b)所示,可以实现滚道测量单元X方向的扫描。移动测量平台下方布置有直线光栅尺,以得到移动测量平台准确的位移信息。
试验前,对螺母导程角进行标定,根据“三针法”原理,测出置于滚道中的钢球到外壁基准面的距离Dbo、钢球直径Db及螺母外径Do,即可求出螺母的中径,进而求出螺母滚道的螺旋角。螺母中径的计算公式为:
Dm=Do-2×Dbo+Db.
(12)
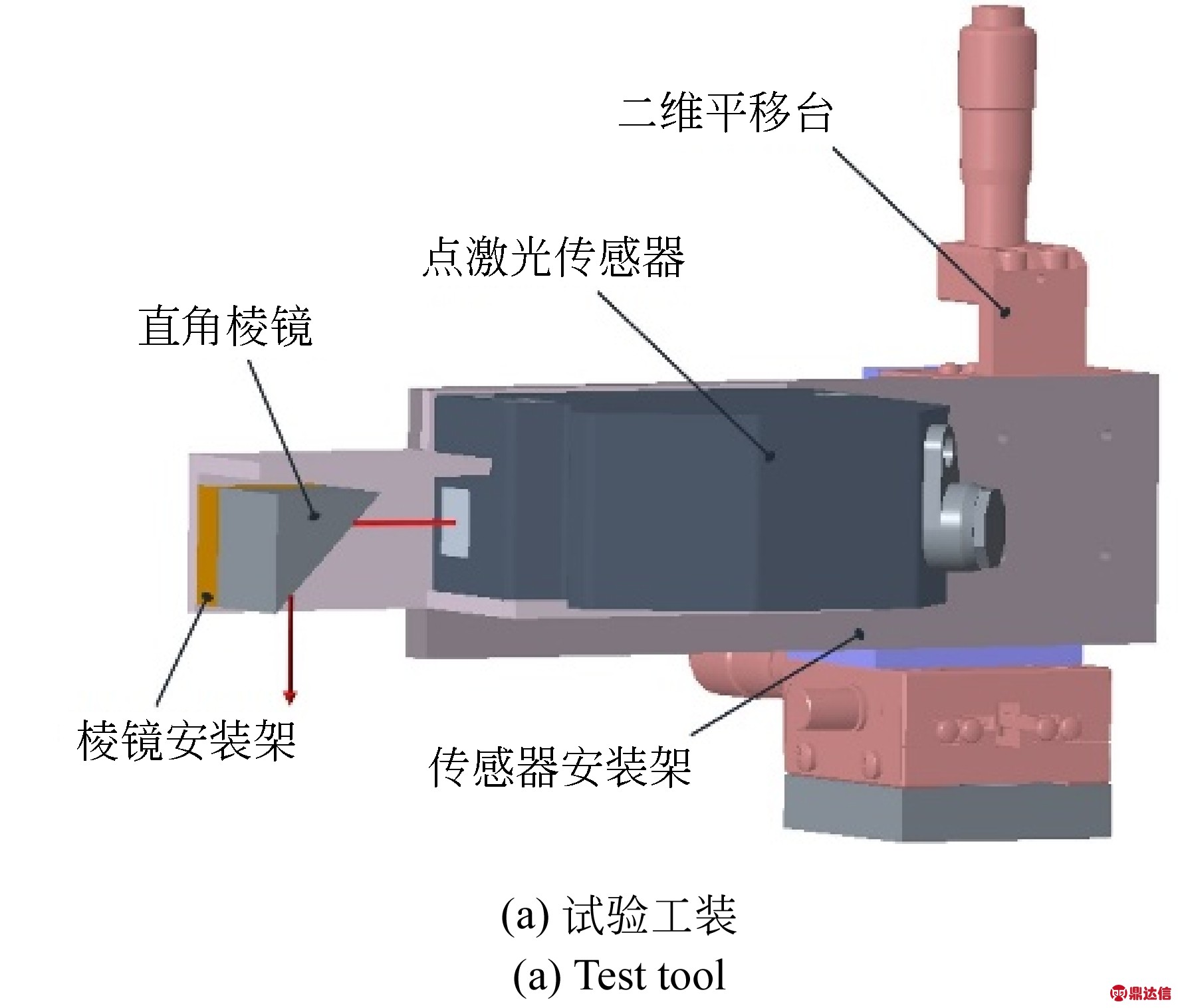
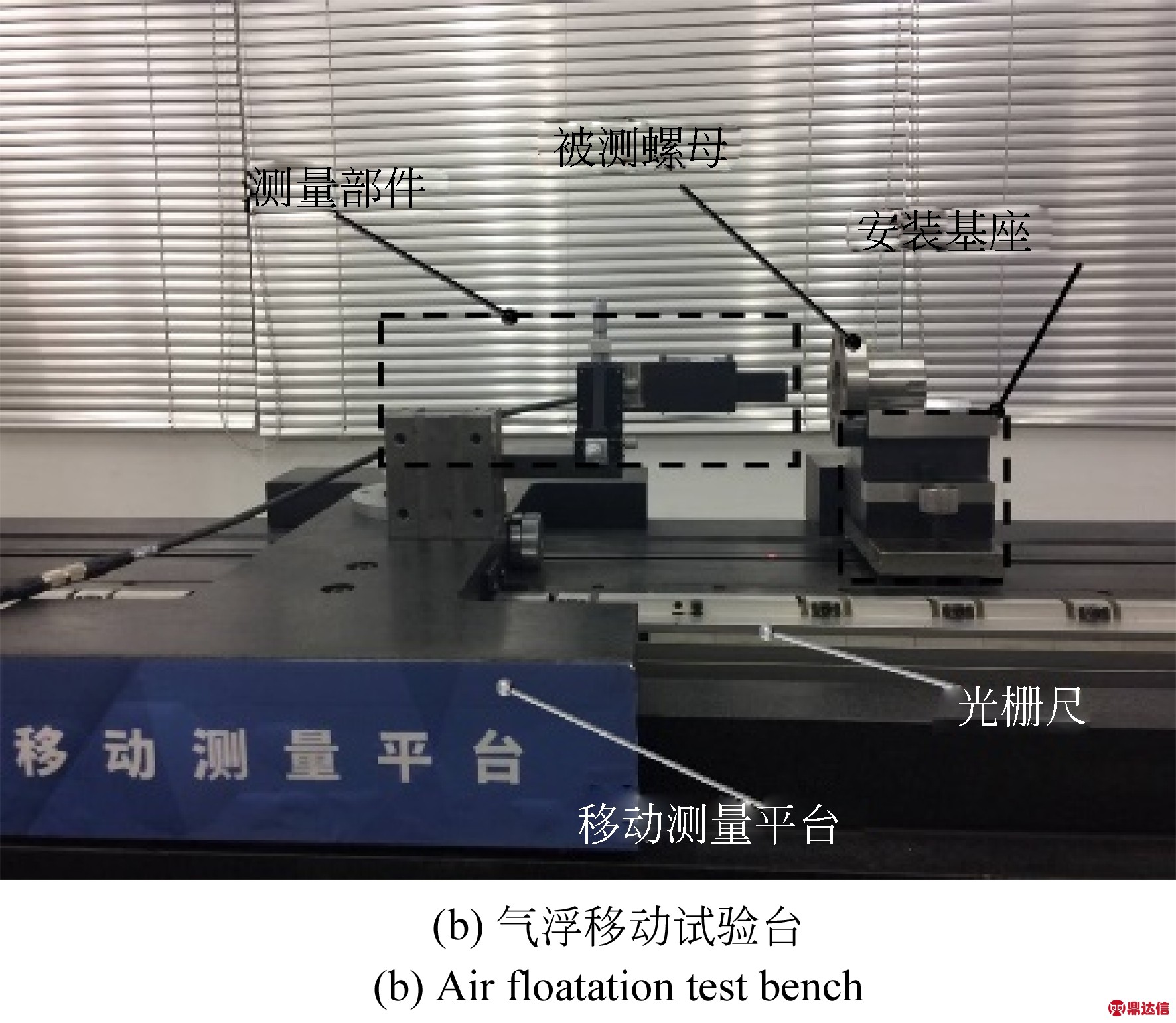
图13 螺母滚道型面测量试验装置
Fig.13 Test device for profile measurement of nut raceway
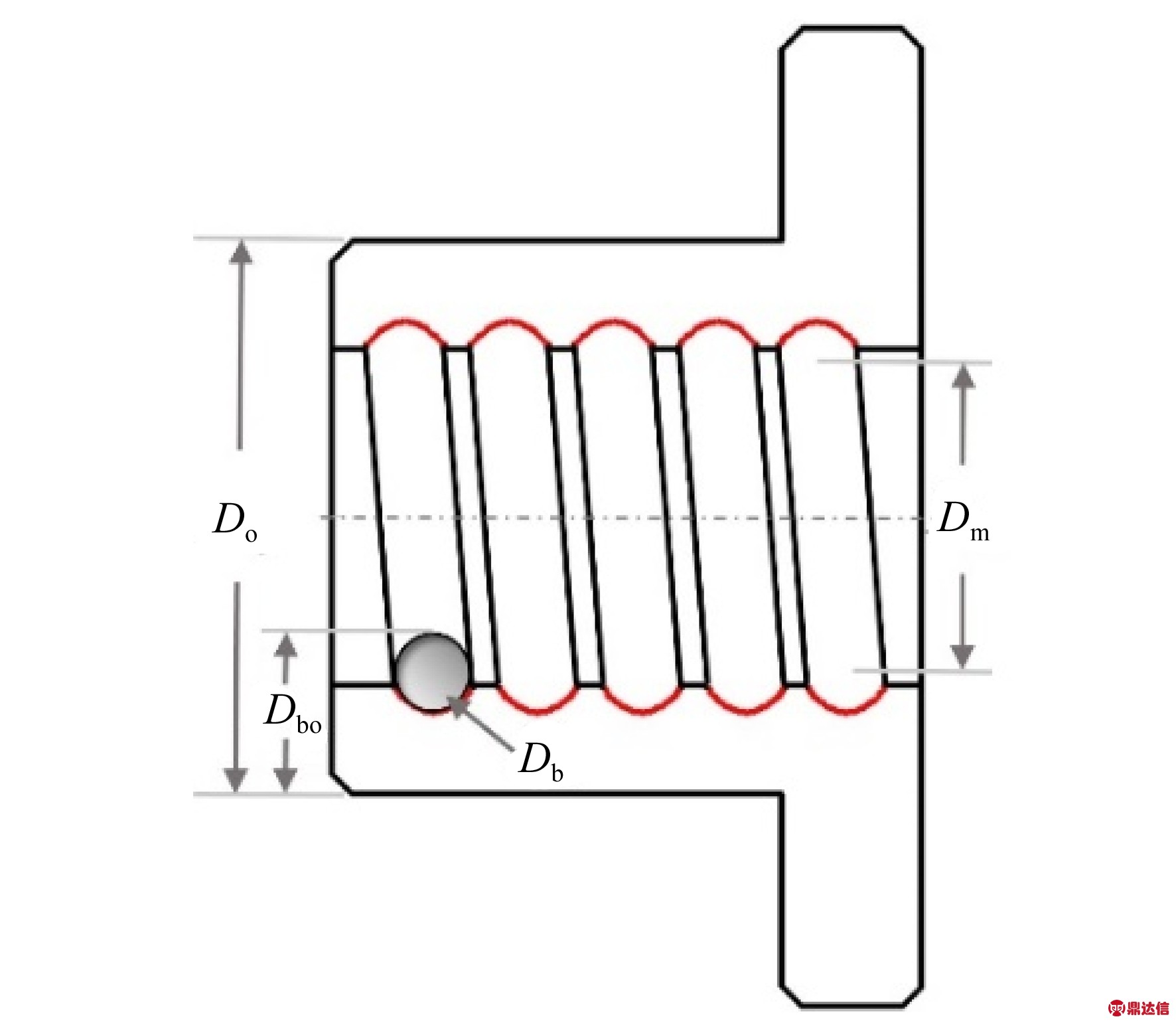
图14 螺母中径测量原图
Fig.14 Principle for measurement of nut′s diameter
螺母安装基座由V型块和高度调节平板组成,将螺母安装基座置于床身的平V轨上,使用千分表调节安装基座直线度,以保证螺母轴线与移动测量平台平行。将通过法兰面定位的螺母固定于V型块上,选择适合滚道尺寸的钢球放置于靠近法兰面的滚道上,此时钢球会在自身重力的影响下在滚道上来回滑动,最终稳定在XOZ平面上,接下来对系统误差进行校准。
为了尽可能减小直角棱镜的转角误差,对棱镜的安装板进行高精磨削提高平面度,以保证它绕X轴旋转的安装精度;激光照射直角棱镜面,通过调节它绕Y轴旋转,当测距值为最小时激光为垂直照射状态,可保证绕Y轴旋转方向的安装精度。调整好直角棱镜转角误差后,通过二维手动平移台调节装置沿Y轴方向移动,扫描标准钢球的轮廓。由于钢球中心处在XOZ平面上,当扫描钢球截面的测距值为最小时,光线正好处于XOZ平面,此时固定平移台位置,可保证激光沿Y轴方向的安装精度,以减小偏移误差。
以上校准需要重复3次,以保证测量数据真实可靠。
4.2 准确性试验
由于螺母滚道的检测方法不完善,难以找到经认定具有标准尺寸的螺旋滚道。为了验证本方案测量圆弧轮廓的准确性,利用激光扫描高精度钢球的最大圆轮廓和高精度圆槽的内轮廓。标准钢球为凸形轮廓,圆槽为凹形轮廓,可以全面反映该测量方案扫描圆弧轮廓的精度。
本测量方案中对结果影响较大的系统误差是直角棱镜的转角误差和激光偏移误差,考虑到钢球形状规则,激光扫描角度和轨迹不同会得到不同的结果,因此对误差校准前后钢球的测量结果进行分析。将经过光学标定的φ22.235 mm的钢球放置于V型块上,将激光移动到钢球上进行扫描测量;测量完成后,按照3.1中所述对系统误差进行校准,再次扫描钢球轮廓,各测量8次,经过拟合得到圆弧后对测量结果进行分析,拟合结果对比如图15所示。
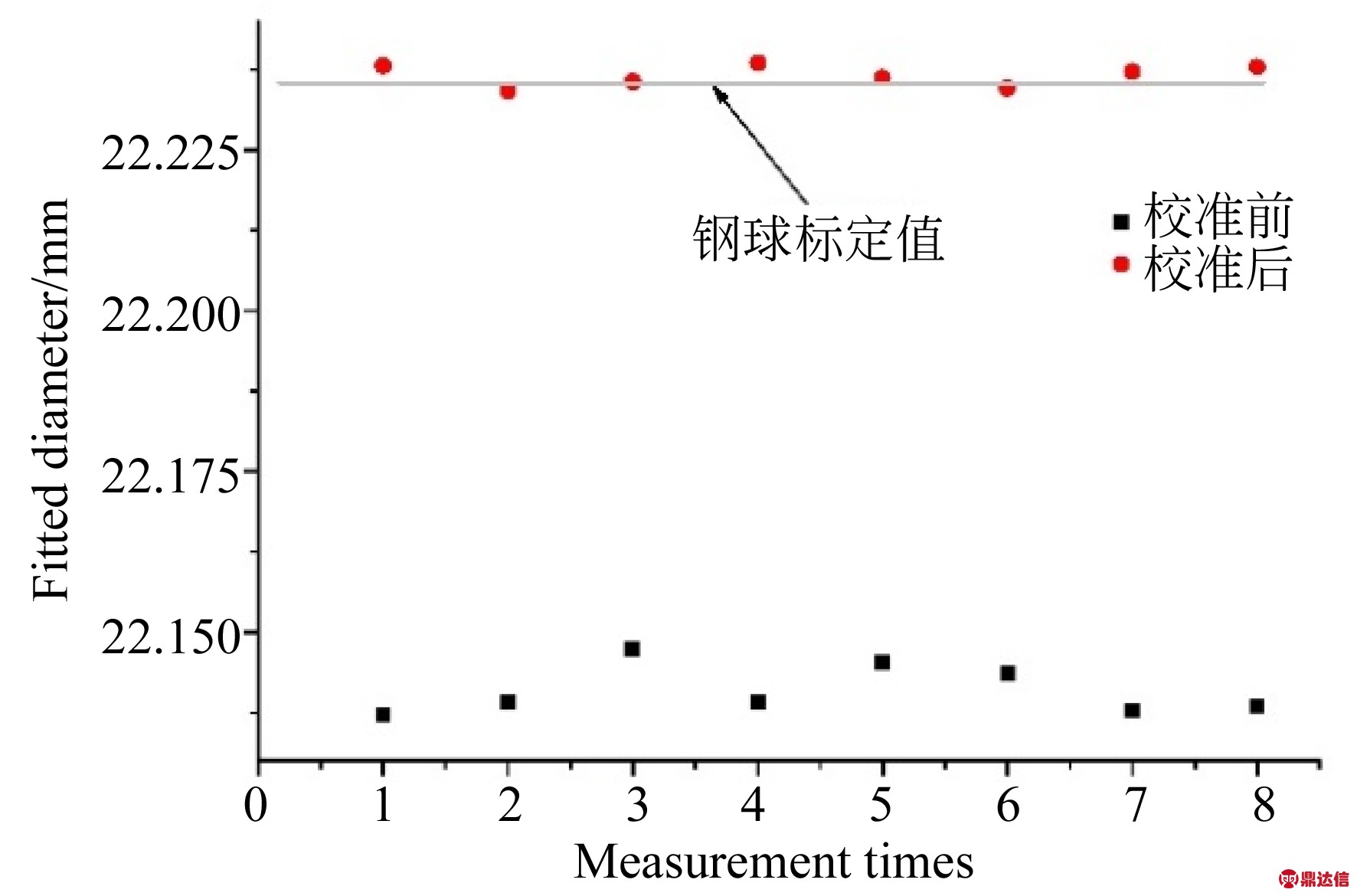
图15 误差校准前后钢球测量比较
Fig.15 Comparison of steel ball measurement before and after error calibration
根据数据分析可以得出,误差校准前的均值为22.141 1 mm,标准偏差为0.003 6 mm;误差校准后的均值为22.236 5 mm,标准偏差为0.001 5 mm,误差校准之后测量值更加接近真实值,且结果更加稳定,测量精度有明显提高。误差校准前的测量结果偏小,可能是实际测量轨迹与中轴线偏离,使得测量轨迹并非最大圆轮廓所致。
同时,将经过标定的直径为20.004 mm的圆槽工件放置于工作台,调整合适后测量8次,经过拟合圆弧得到圆槽直径。
表3 准确性试验结果
Tab.3 Accuracy test result (mm)
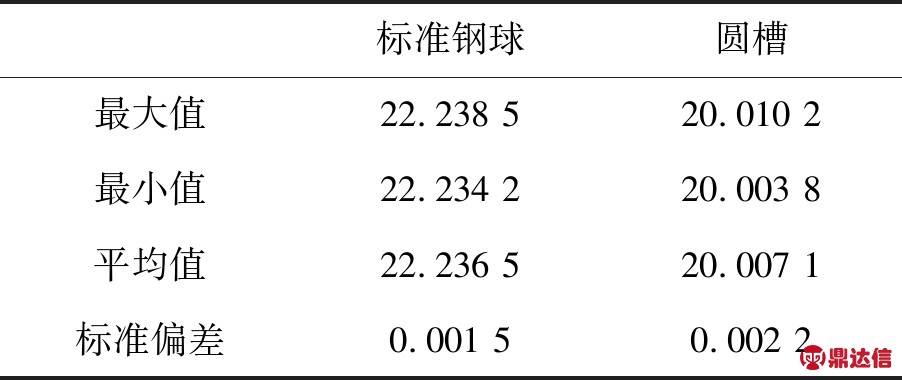
以上计算标准偏差的公式为:
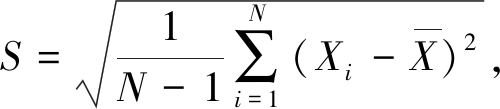
(13)
式中:S为标准偏差,N为样本的个数,Xi为第i个样本,为样本均值。
比较拟合直径与标准直径,结果如表3所示。标准钢球直径的平均值为22.236 5 mm,标准偏差为1.5 m;标准圆槽直径的平均值为20.007 1 mm,标准偏差为2.2
m。根据测量值,结合被测件标定尺寸可以得出,利用设计工装测量钢球时的偏差为1.5
m,测量圆槽时的偏差为3.1
m。测量标准圆槽的数据波动较大,可能由于表面加工精度所致。
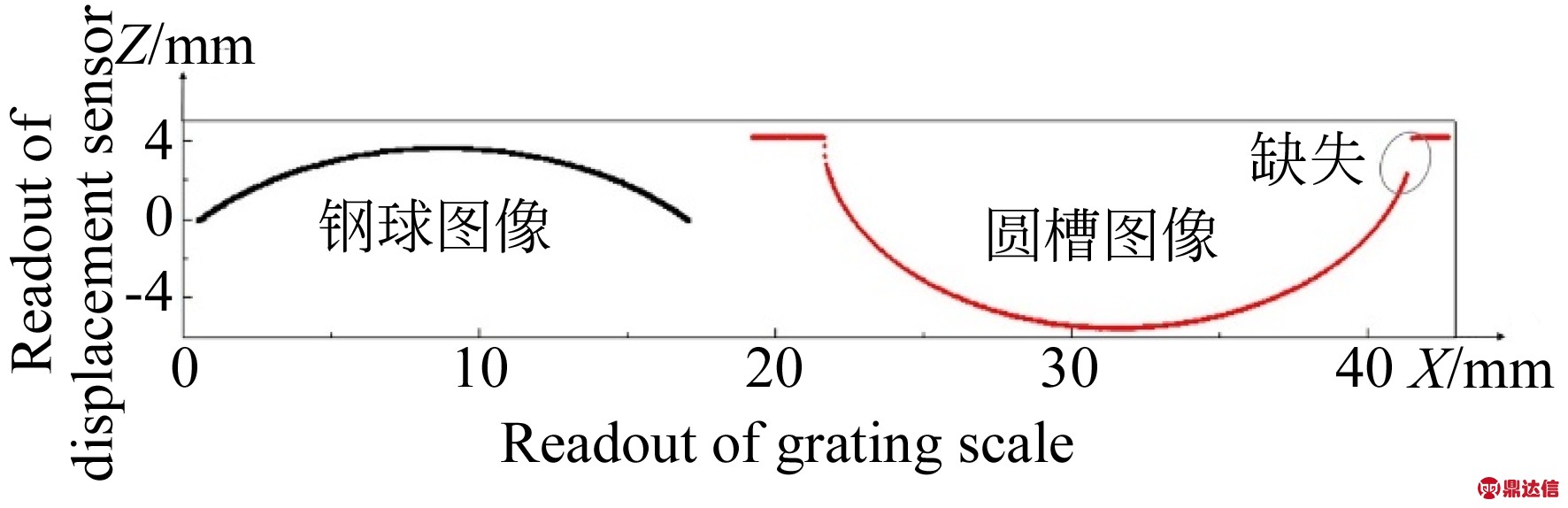
图16 钢球和圆槽测量图像
Fig.16 Scanning images of steel balls and circular grooves
由图16可以看出,钢球轮廓图像正常,圆槽轮廓图像右侧有一段缺失,可能是由于入射光线在该段倾斜角度大导致传感器感光元件接收到的漫反射光线较弱,造成该段图像丢失,经过该段后,图像又恢复正常。这也反映出点激光测量中常见的入射角度问题,图像缺失使得拟合点减少,可能会影响圆弧的拟合精度,最终产生测量误差。
4.3 螺母滚道测量应用
基于上述理论验证,激光测量圆弧轮廓具有可行性。对国内某厂家生产的R40-10型滚珠丝杠配套螺母的滚道进行测量,将它固定在V型块上,经过调试准备后,通过气浮移动试验台搭载试验工装以5 mm/min的速度扫描螺母滚道,得到的图像如图17所示。
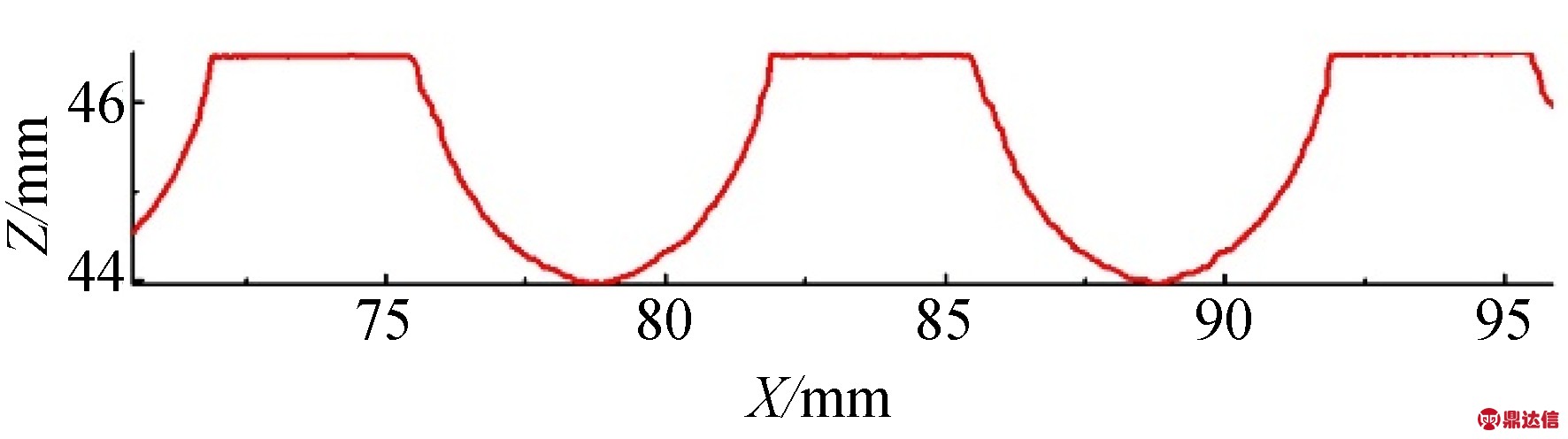
图17 螺母滚道测量图像
Fig.17 Nut raceway measurement image
对滚道数据点完成预处理、坐标转换、图像分割和圆弧拟合,得到左右圆弧半径和圆心坐标。重复测量5次,对测量数据的范围、均值和标准偏差进行分析,结果如表4所示。
表4 螺母滚道测量结果
Tab.4 Measurement results of nut raceway (mm)
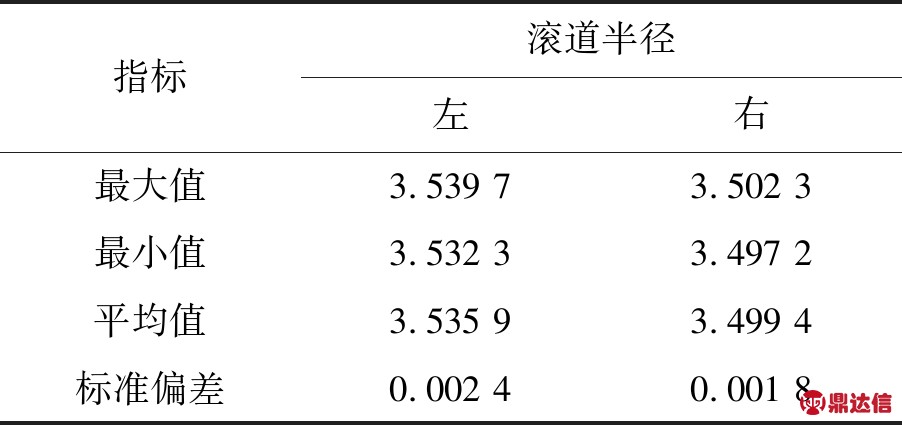
经过计算分析对比,被测螺母左右滚道圆弧半径的平均值分别为3.535 9 mm和3.499 4 mm,可以看出左右滚道数据在对称性上存在问题;左右滚道圆弧半径的标准偏差分别为2.4 m和1.8
m,标准偏差反映了测量数据的重复性,综合测量结果和图17可以得出,利用直角棱镜反射激光测量的滚道数据存在一定程度的波动,这与测量单元的行走精度有关。
5 结 论
本文建立了螺母内滚道的轴法向测量转换模型,并对滚珠螺母型面激光测量方案中的误差进行分析,通过调整直角棱镜和激光光路对钢球外轮廓进行测量,结果表明误差校准后的测量精度明显提高,结合扫描圆槽的试验验证激光测量圆弧轮廓的误差在3.1 m以内,对螺母滚道的扫描图像完整有效,总体精度满足螺母滚道型面的测量要求。与传统的测量单个滚道法向截面对比,本检测方案能够一次性获得全部滚道的轴向截面,经过数据处理得到法向型面参数,操作难度小,检测效率高,但该方案的数据稳定性还有待提高。该方法还可以应用到螺杆、转子等其他零部件的轮廓测量,具有一定的推广价值。