摘要:针对传统的电容式触觉传感器因存在信号耦合测量,导致切向灵敏度远低于法向灵敏度的问题,基于多层电容结构,设计了一种三轴力解耦测量的高灵敏触觉传感器。传感器分为切向和法向测量单元,切向测量单元采用对称分布的差分式指状结构保证切向高灵敏测量,并结合超薄弹性硅胶介质,提高切向介质层有效压缩刚度,以抑制法向信号的耦合干扰;法向测量单元的介质层采用一种弹性稀疏网状微结构,用于法向高灵敏测量,并通过拓展法向接地极消除切向信号的耦合干扰。在对电容结构参数化设计的基础上,完成触觉传感器的制备,并搭建三轴力测试系统进行测试。结果显示,传感器的切向X,Y以及法向的测量灵敏度为0.206 pF/N, 0.251 pF/N,0.148 pF/N;切向X-Y以及切向-法向之间的最大静态耦合比分别为7.636%,1.051%。本传感器实现了三轴力的解耦测量及切向、法向相同量级的高灵敏特性。
关 键 词:触觉传感器;多层电容结构设计;解耦测量;高灵敏
1 引 言
近年来,随着电子产品精密化和微小化的发展,柔性电路板(Flexible Printed Circuit Board, FPCB)的应用领域越来越广泛。其中,吸附搬运技术是柔性电路板集成过程中的重要一环,针对传统的真空吸附方式难以实现对多孔柔性电路板的可靠搬运的问题,有科学家根据壁虎的仿生学原理,提出一种基于范德华力的仿生壁虎脚掌黏附手段[1],该方法对目标物表面无特殊要求,损伤小,有望解决可靠搬运这一难题。值得指出的是,仿生壁虎脚掌通过切向加载实现法向黏附,其中法向和切向载荷力的分布不均或超越极限值极易造成仿生壁虎脚掌黏附的失败,因此在黏附过程中,目标附着界面的法向力与切向力的高灵敏触觉传感技术就显得至关重要。
现有的用于载荷力测量的触觉传感器,根据工作原理可分为压阻式[2]、压电式[3]、光纤式[4-5]以及电容式[6],其中电容式触觉传感器与其他传感器相比[7],具有体积小、灵敏度高、稳定性好等特点,是目前触觉传感器研究的主流方向。但是,现有的多轴电容式触觉传感器,一般都是采用法向和切向信号耦合测量的设计方案[8],在法向力和切向力作用下,通过同一组阵列电容敏感单元的极距和正对面积的改变影响电容的输出,最后通过解析该组单个电容之间的输出差异,实现对法向力和切向力的测量[9-11]。该方案虽然结构简单,工艺要求低,但普遍存在切向灵敏度远低于法向灵敏度的问题。为解决这一问题,日本东北大学的Asano S等人[12]和中国浙江大学的G.Liang等人[13]设计了相似的突起结构,通过变极距的原理实现切向力的高灵敏感测。该结构在切向力作用下可使介质层产生弯曲形变,使得一侧电容的极距增加,另一侧电容的极距减小,最后通过两侧电容差值变化表征切向力。该设计为有效弥补切向灵敏度不足提供了重要参考,使切向与法向灵敏度保持相同量级的高灵敏特性,但这类带有突起结构的触觉传感器并不适用于仿生壁虎脚掌这类分布式载荷力的测量,相关研究亟待深入。
本文面向多自由度高灵敏触觉传感技术的实际应用需求,为解决电容式触觉传感器因信号耦合测量,导致切向灵敏度远低于法向灵敏度的问题,设计了一种基于多层电容结构的三轴力解耦测量的高灵敏触觉传感器。首先,建立传感器基于多层结构的三轴力测量模型,模型分为切向测量单元和法向测量单元,切向测量单元的感测电极采用对称分布的新型差分式指状结构设计,该设计无需借助突起结构,只需增加指状结构数量,即可实现切向的高灵敏测量,介质层采用一种超薄的硅胶弹性体以提高其有效压缩刚度,从而抑制法向耦合干扰。法向测量单元采用一种硅胶材质的稀疏网状微结构,实现法向高灵敏测量,并拓展法向接地极面积以消除切向的耦合干扰。然后,通过多层PCB层叠设计结合硅基MEMS工艺,实现传感器采集信号中杂散电容的屏蔽和介质层微结构的加工,并通过层间粘合工艺研究完成触觉传感器的集成。最后,搭建实验测试系统,对传感器的灵敏度和解耦性能进行了系统测试。
2 三轴力高灵敏触觉传感器结构设计
本文设计的三轴力解耦测量的高灵敏触觉传感器的整体结构如图1所示。切向测量单元基于变面积原理测量切向力,电极形状设置为X/Y向独立分布的差分式指状结构,分别用于切向X,Y测量,并采用一种超薄的硅胶弹性体作为切向介质层。法向测量单元基于变极距原理测量法向力,介质层采用硅胶材质的稀疏网状微结构,并适当拓展法向接地极面积以实现解耦,其中法向感应极采用阵列式分布,有助于提高传感器的空间分辨力。此外,传感器嵌有电容数字转化电路,不仅为传感器提供数字转换接口,还增添有源屏蔽输出,用于消除杂散电容的干扰。

图1 触觉传感器的结构组成
Fig.1 Structural composition of tactile sensor
2.1 传感器切向测量单元设计
切向测量单元的力-电容测量结构,如图2所示。
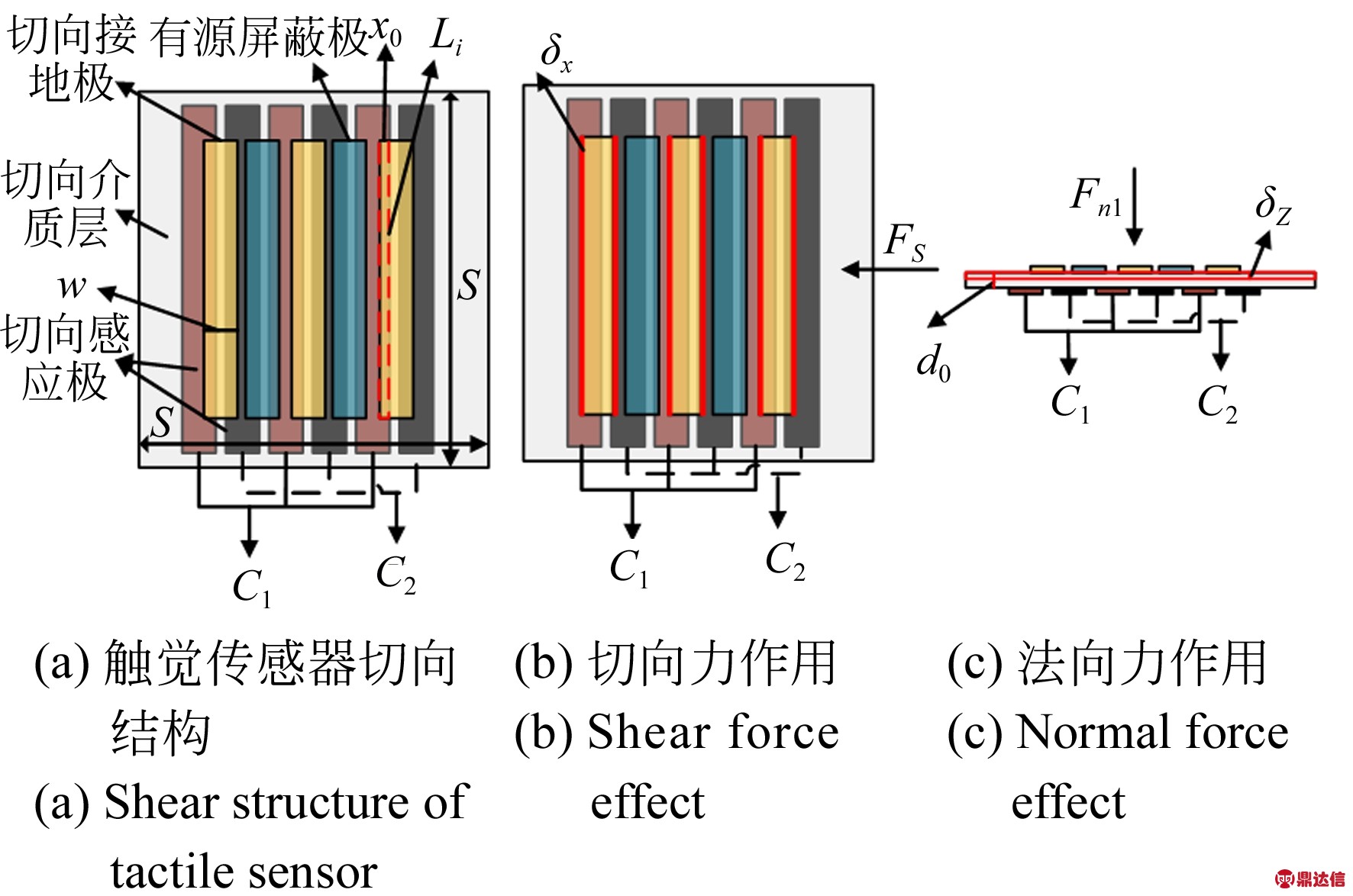
图2 切向测量单元
Fig.2 Shear direction measuring unit
当受切向力Fs作用时,切向介质层产生X向/Y向变形,如图2(b)所示,切向位移δx为:
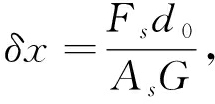
(1)
其中:d0为切向介质层初始厚度,As=s2为介质层面积,s为介质宽度,G为切向介质层剪切模量。
结合电容公式,得出电容C1和C2与切向位移δx的关系式为:
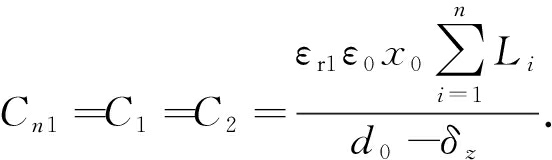
(2)
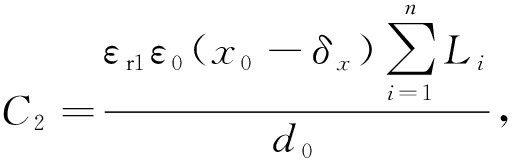
(3)
其中:n为指状结构总数量,Li为第i个电极长度,x0为电容初始正对宽度,εr1为切向介质层的相对介电常数,ε0为真空介电常数。
结合式(1)~式(3),得出电容差分变化量Cs与切向力FS之间的关系式为:
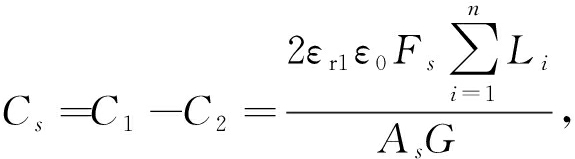
(4)
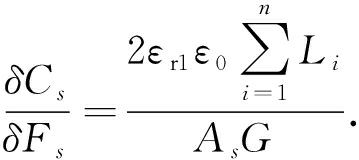
(5)
差分式指状结构相当于几个电容的并联,灵敏度更高,由公式(5)可以看出,在相同面积下,通过增加指状结构数量,降低单个分支单元的面积,能增大切向力作用下的正对面积增量,有效提高切向测量灵敏度。
在切测量单元的解耦设计中,本文对切向弹性介质层的参数设计开展研究。考虑到当连接在两个刚性体中的弹性材料很薄时,该材料的有效压缩刚度急剧增加而其剪切刚度基本不发生变化[14],利用此原理,将切向介质层设计为一种微米级的超薄弹性结构,以保证测量单元对切向力有较好的响应,而对正压力无明显响应,从而实现对法向信号的有效抑制,即切向测量单元单个电容对切向和法向力的测量灵敏度的比值要尽可能的大:

(6)
其中测量单元中单个电容对切向的灵敏度为:
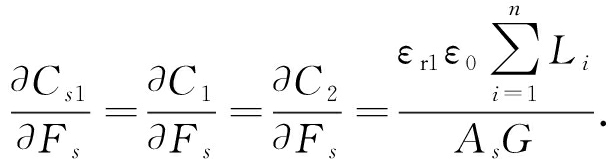
(7)
如图2(c)所示,当法向力作用于超薄介质层作用时,基于不可压缩性假设获得有效的弹性模量如式(8)[14]:

(8)
其中η=2d0/s为介质的纵横比。
根据应力与应变的概念,导出法向力Fn1与切向介质层法向位移δz表达式:
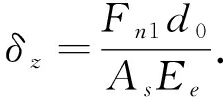
(9)
假定式(9)中的切向位移为0,受法向力Fn1作用时,切向测量单元电容值Cn1为:
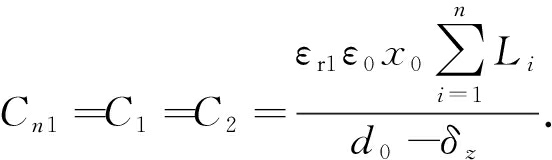
(10)
联立式(8)~式(10)得:
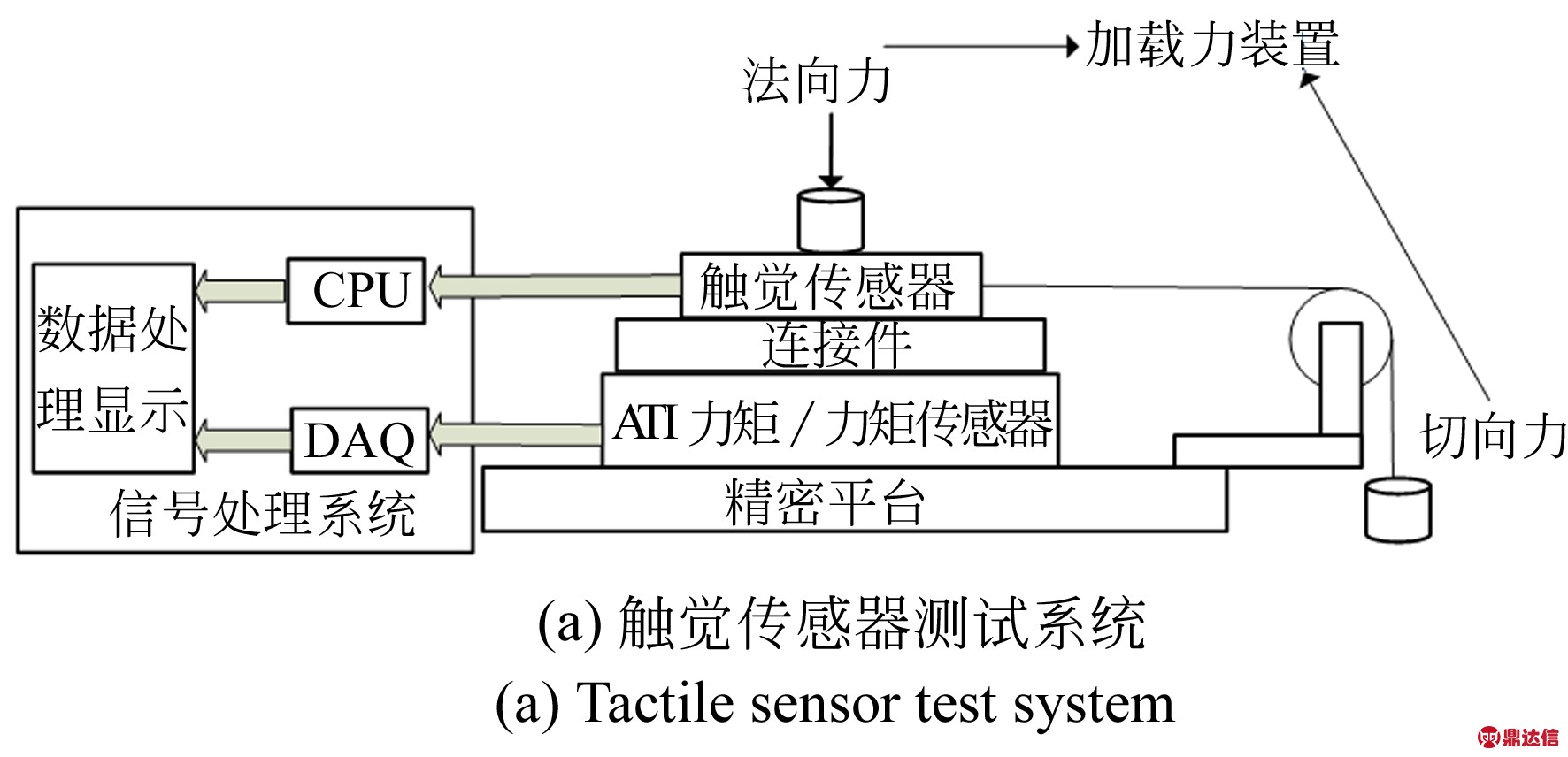
(11)
式(11)对Fn1求偏导,即可得到切向测量单元电容对法向力的测量灵敏度:
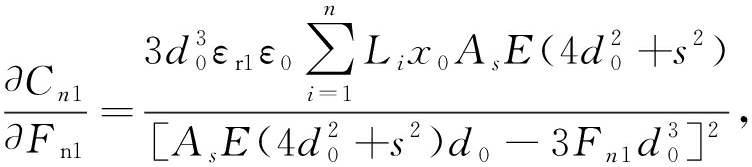
(12)
联立公式(7),公式(12),得出切向测量单元电容对切向力和法向力的测量灵敏度近似比:
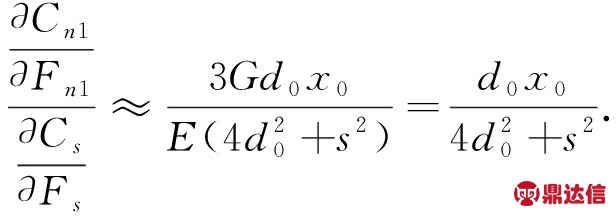
(13)
对于超薄弹性体G=E/3,从式中可以发现,当s2≫d0x0时,即切向介质宽度的平方远大于介质厚度与电极初始正对宽度的乘积,能有效抑制法向的测量灵敏度。因此,选用超薄的硅胶弹性体作为电容的介质层,能有效抑制切向测量通道中法向力的作用,同时结合差分式结构,实现切向测量单元对法向信号的高效解耦。
2.2 传感器法向测量单元设计
法向测量单元基于稀疏网状介质的力-电容测量结构,如图3所示。
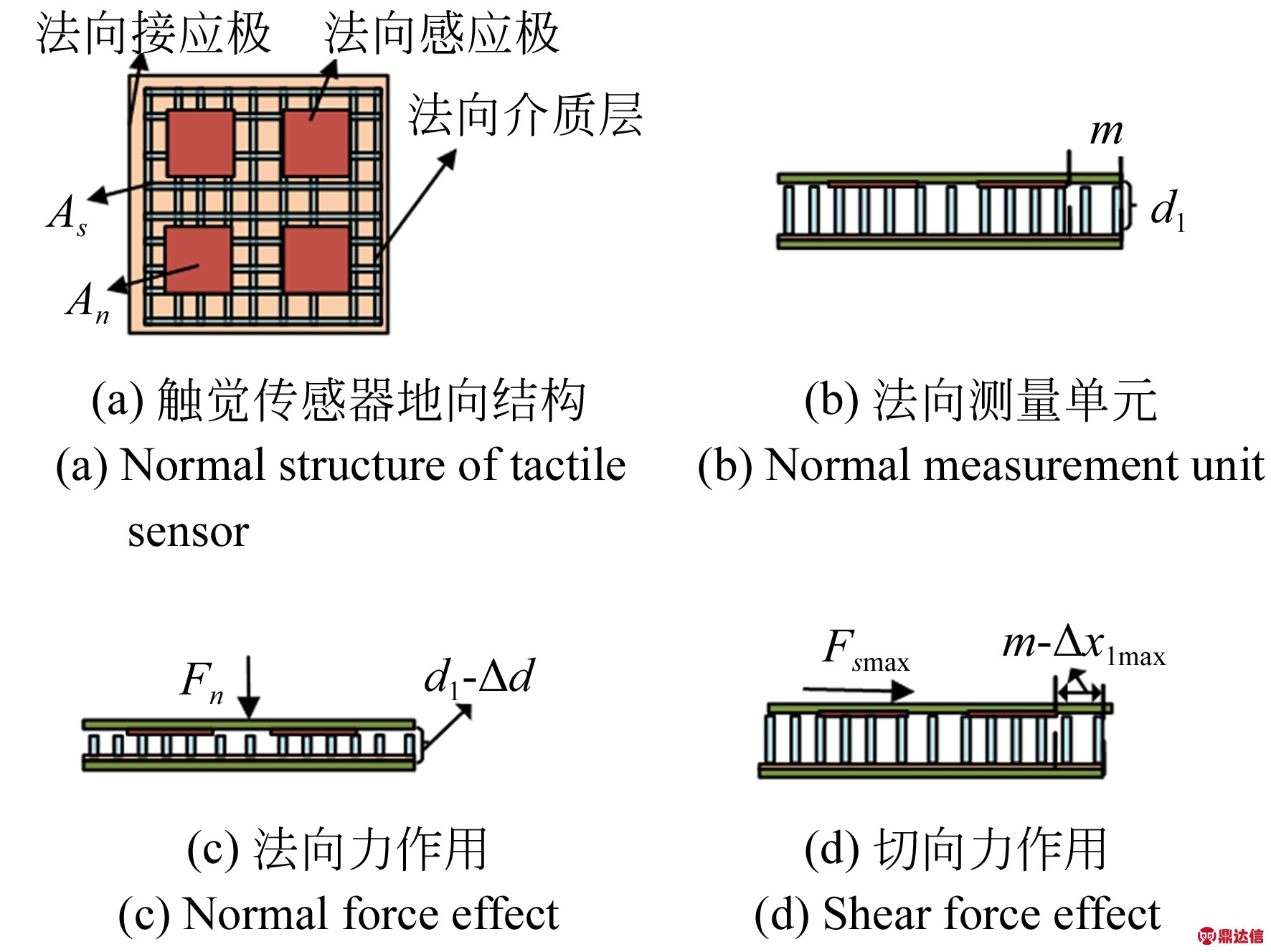
图3 法向测量单元
Fig.3 Normal direction measuring unit
如图3(c)所示,受法向力Fn时,介质层伸缩变化量Δd为[15]:
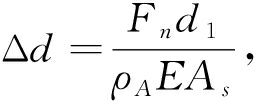
(14)
其中:d1为法向介质初始厚度,As为介质层面积,E为介质弹性模量,ρA为介质填充率。
法向测量单元电容值Cn与法向力Fn的关系为:
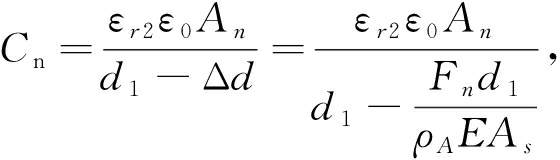
(15)
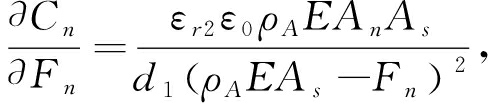
(16)
其中:An为单个法向感应电极面积,εr2为介质的相对介电常数。
检测压力Fn相对于ρAEAs很小,忽略Fn对法向灵敏度的影响,此时法向灵敏度为:
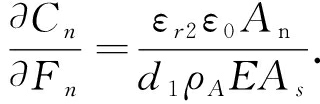
(17)
稀疏网状结构在两个传感电极间形成一种弹性体和空气气隙的组合体,从公式(17)可以看出,通过降低弹性介质的填充率,可以有效提高法向测量灵敏度。
为实现法向测量单元的解耦性能,本文通过拓展法向接地极尺寸,在受切向力作用时,保证法向测量单元的有效正对面积不变,从而消除切向信号的耦合影响。如图3(d)所示,首先认为法向测量单元承受的极限切向力为切向测量单元承受的最大切向力,设为FSmax,法向介质层的有效剪切模量为Ge,由切向力公式(1),得出法向介质层最大切向偏移量Δx1max:
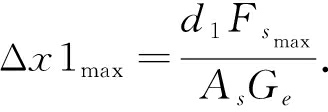
(18)
为便于计算法向介质层的最大偏移量,假设Ge=E/3,设法向接地极宽度超出法向感应电极宽度为m。若要取得较好的解耦效果,设计中要保证m>Δx1max,即法向接地极超出法向感应电极的宽度大于法向介质层的最大切向偏移量。
3 三轴力高灵敏触觉传感器的制备
传感器由三层平面PCB板与两层介质交替堆叠构成,整体大小为30 mm×30 mm。如图4(a)所示,传感电极由绘制在PCB板上的铜导线组成,顶层PCB板印制切向接地极与有源屏蔽的指状交错结构,切向指状结构数量n=15,指状宽度w=305 μm,指状重叠正对宽度x0=76 μm。底层PCB板放置传感器的法向接地极,接地极尺寸为30 mm×30 mm。尤其为使传感器结构紧凑,将传感器的切向感测电极、法向感测电极和电容数字转换电路集成在中间层PCB板,其中法向感应电极尺寸An=11 mm×11 mm,法向接地极尺寸超出法向感应电极的尺寸m=2.5 mm。由于中间层PCB板的高度集成,为防止感应电极之间的相互影响,并消除杂散电容,中间层采用四层PCB板层叠设计,切向感测电极和电容数字转换电路放置在PCB板上表层,法向感测电极放置于中间PCB下层;PCB板中间增设一层有源屏蔽,用于消除法向和切向感测电极之间的干扰;此外,为了将法向输出端信号引入电容数字转换电路接口,在PCB板有源屏蔽层和上表层之间设计一层走线层,用于法向信号的传输。同时,为防止同层信号之间的干扰,每个感应电极和走线周围都设置有源屏蔽,实现与周围环境隔离。
为保证传感器的高灵敏和解耦特性,切向超薄介质和法向低填充率网格介质的制备与粘合工艺起着至关重要的作用。本文采用硅基MEMS工艺实现介质层微结构的制备,其中切向介质层选用延展性较好,抵抗剪切能力强的柔性较高的铂催化硅橡胶Smooth-On Ecoflex® 00-50(混合比例A∶B=1∶1),该硅胶固化后非常柔软,抗拉撕性能和恢复性好,剪切模量G=100 kPa[14],相对介电常数εr1=2.7,切向介质层宽度s=30 mm,厚度d0=100 μm。法向介质层采用弹性较好的弹性较好的室温硫化型硅橡胶TAP® Silicone RTV(混合比例A∶B=1∶1),该材料具备较好的弹性,抗压性能好,良好的尺寸稳定性和伸长率,线性收缩率低,弹性模量E=840 kPa[14],法向介质层的填充率ρA=13%(硅胶网格宽度为235 μm),高度d1=130 μm,网格的相对介电常数εr1=~2[15],真空介电常数ε0=8.854×10-12 F/m。首先,通过硅基MEMS工艺分别制备相应要求的硅模具;然后在硅模具上沉淀一层parylene,用以降低模具与硅胶之间的粘附性,使模具与硅胶能够较为顺利的分离;最后经浇注,抽气,匀胶,常温固化,脱模等一系列加工工艺,完成介质层的制备,最终制备的切向和法向介质层如图4(b)所示。
传感器集成过程中,由于介质层的柔性和微小尺寸,使其在粘合过程中易产生卷曲或褶皱,造成传感器集成失败。为了解决这一难题,本文采用PET硬质塑料作为介质层转移的中间媒介,集成过程如图4(c)所示,一方面PET为介质层提供刚性支撑,用以介质层的转移并保证平整度,另一方面,PET还具有一定的柔性,便于介质层与PCB板粘合时夹杂气泡的排除。为了使PCB板与已经固化的硅胶介质固连在一起,在切向测量单元的粘合中,将未固化的硅胶滴入底漆预处理过的PCB板上,经真空抽气后,旋涂出薄层作为连接层;对于法向测量单元,本文采用硅胶粘合剂作为连接层,以实现介质层与PCB板的可靠粘合。粘合过程中,在每层PCB板上设有定位孔,可通过销钉定位保证三层PCB板的对准精度。

图4 触觉传感器的制备
Fig.4 The manufacturing of tactile sensor
最终集成制备的高灵敏触觉传感器实物样机如图4(d)所示,本触觉传感器样机采用AD7148芯片作为电容数字转换芯片,其测量范围为±8 pF,分辨力为±0.1 fF;触觉传感器与外界通信采用I2C总线,外部控制器可通过I2C总线实现对触觉传感器的寄存器配置及三轴力数据信息的读取;此外,触觉传感器集成了有源屏蔽端口,便于传感器的干扰屏蔽设计。
最后根据上述设计参数进行了切向和法向测量单元的理论计算。首先是切向测量单元,由式(5)可得到切向测量灵敏度的理论值为0.194 pF/N;公式(13)可得出法向和切向测量灵敏度的理论比值为8.4×10-6,由此可以看出,在切向测量单元检测中,法向相较于切向的测量灵敏几乎可以忽略不计,从而获得了较好的解耦效果。关于法向测量单元,根据公式(17)得到法向的测量灵敏度为0.167 pF/N;联立公式(1)和公式(18)可得出法向测量单元切向最大偏移量Δx1max=0.035 mm,本文中设计的法向测量单元的接地极超出感应电极的尺寸m为2.5 mm,满足m>Δx1max要求,可以保障法向测量单元的解耦性能。
4 触觉传感器性能测试
4.1 测试系统的搭建
为了验证传感器的灵敏度和解耦性能,搭建了如图5(a)所示的传感器静态加载测试系统,系统主要由加载力装置,标准的商用型号为 ATI Gamma SI-65-5的六轴力/力矩传感器,信号处理系统,连接件等部分组成,测试系统的结构图如图5所示,加载力装置对传感器施加三轴力,商用ATI传感器作为标准参考,其性能如表1所示,通过信号处理系统进行数据的采集与处理,测试触觉传感器的灵敏度与解耦性能。
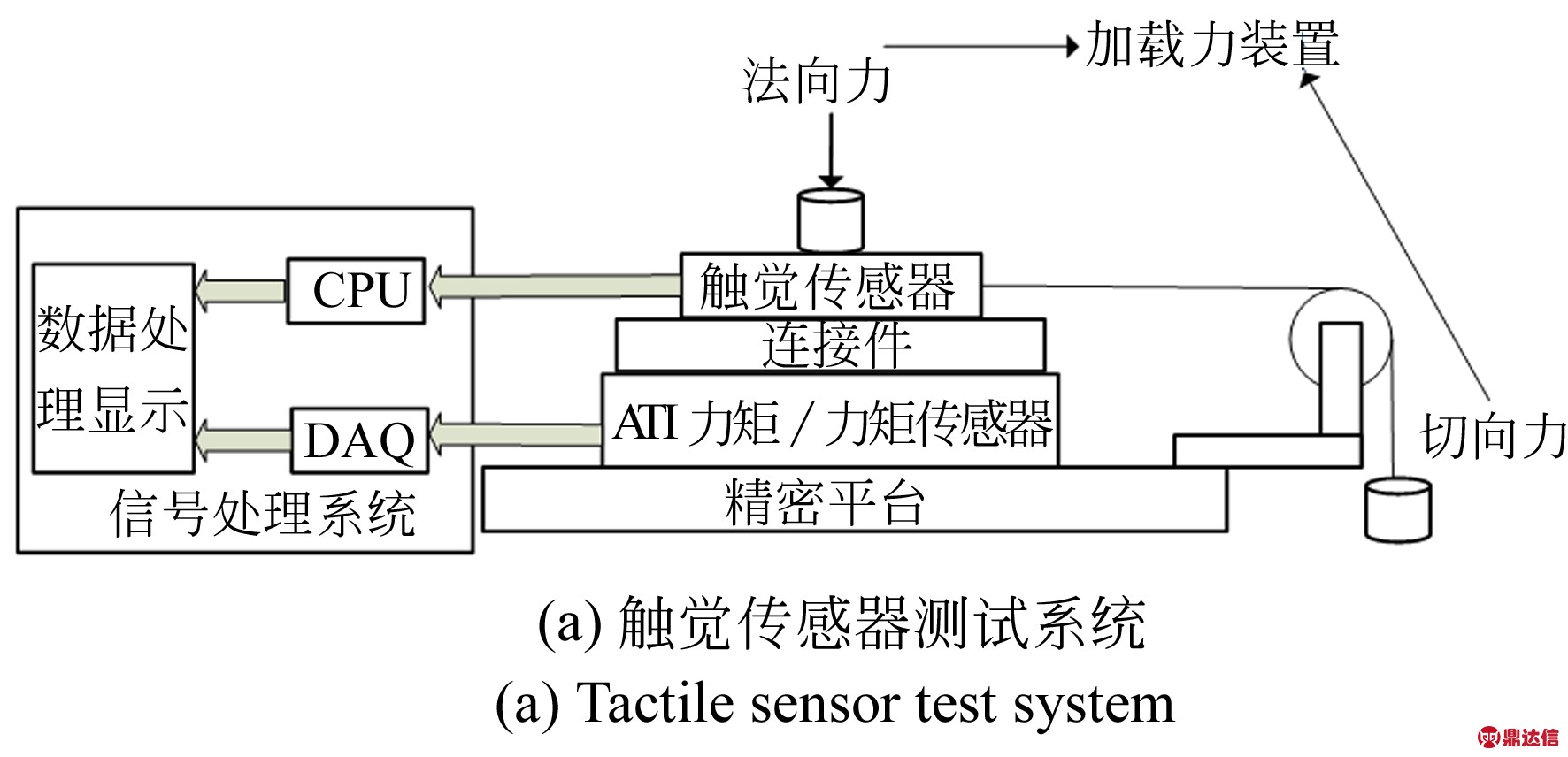
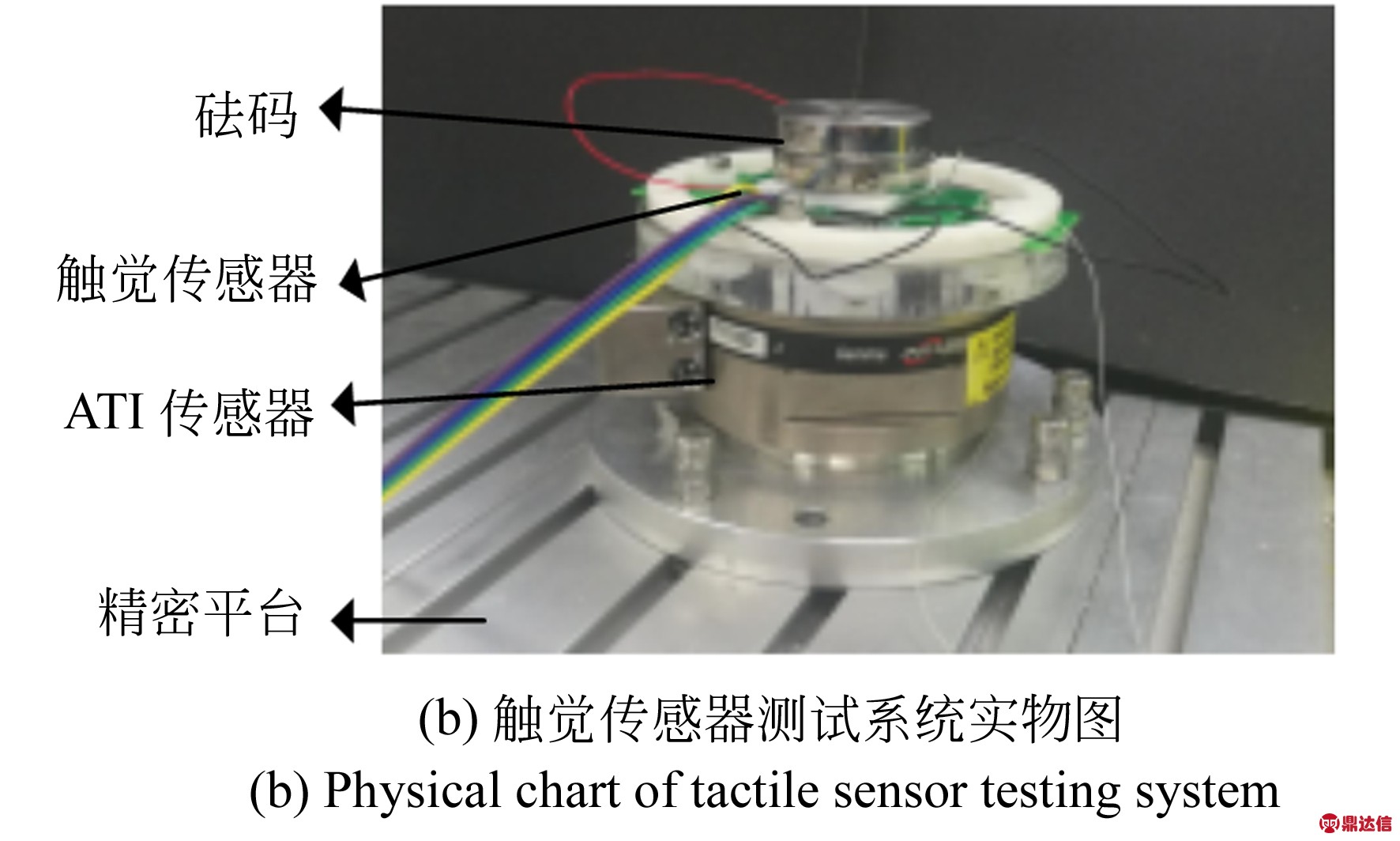
图5 传感器静态加载测试实物配合图
Fig.5 Static load test material diagram of the sensor
表1 触ATI六轴力/力矩传感器性能参数
Tab.1 Performance parameters of the ATI six-axis force sensor
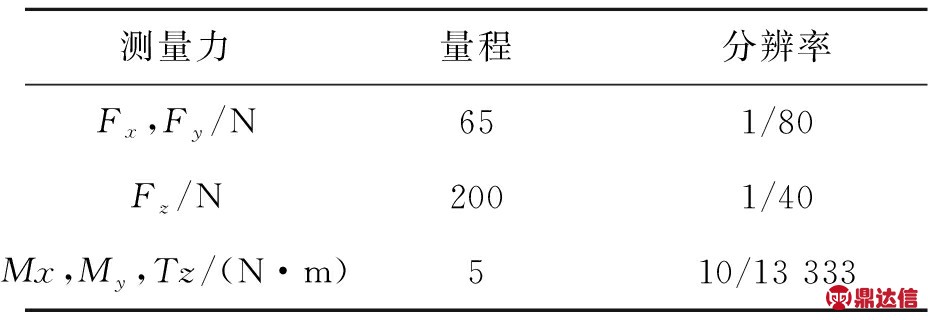
4.2 传感器灵敏度和解耦性能测试
为测试传感器三轴的灵敏度特性,在传感器的测量范围内,对传感器的三轴进行3次正负行程压力循环加载/卸载测试。为实现X/Y方向切向力的加载/卸载,通过加载线绕过水平转向滑轮静态悬挂砝码,测试范围为0~600 g,每次加载/卸载间隔为100 g,共取7点;法向加载/卸载方案通过在传感器的中心位置静置砝码而实现,其测量范围是0~300 g,每次加载/卸载间隔为50 g,共取7个点。实验中传感器输出至稳定状态时,记录触觉传感器和ATI传感器的1 000个数据点取均值,作为每次加载/卸载的实验数据。所得的数据经处理后采用最小二乘线性拟合,最终得到触觉传感器输出电容相对初始电容变化量与输入力之间的关系,如图6所示。
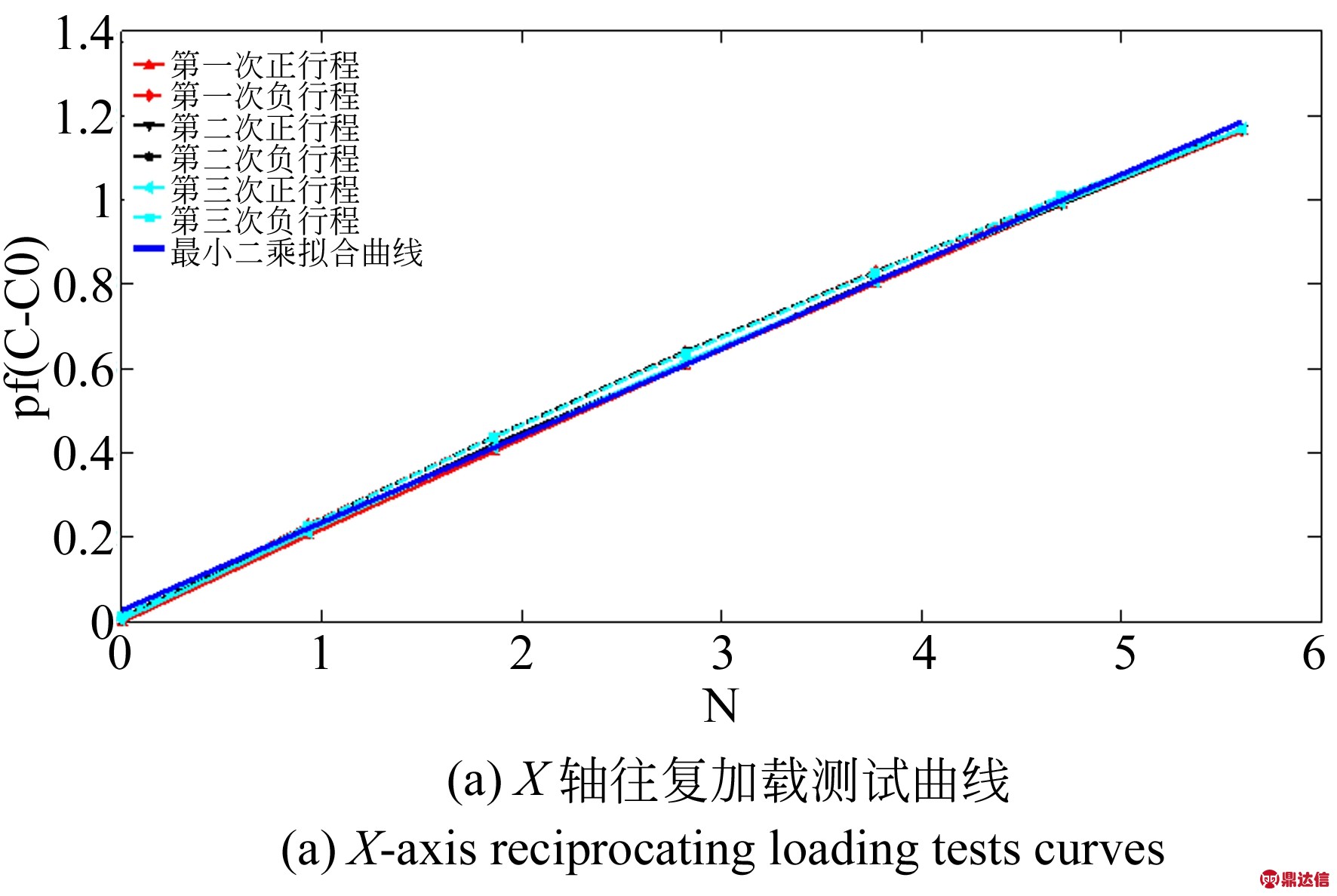
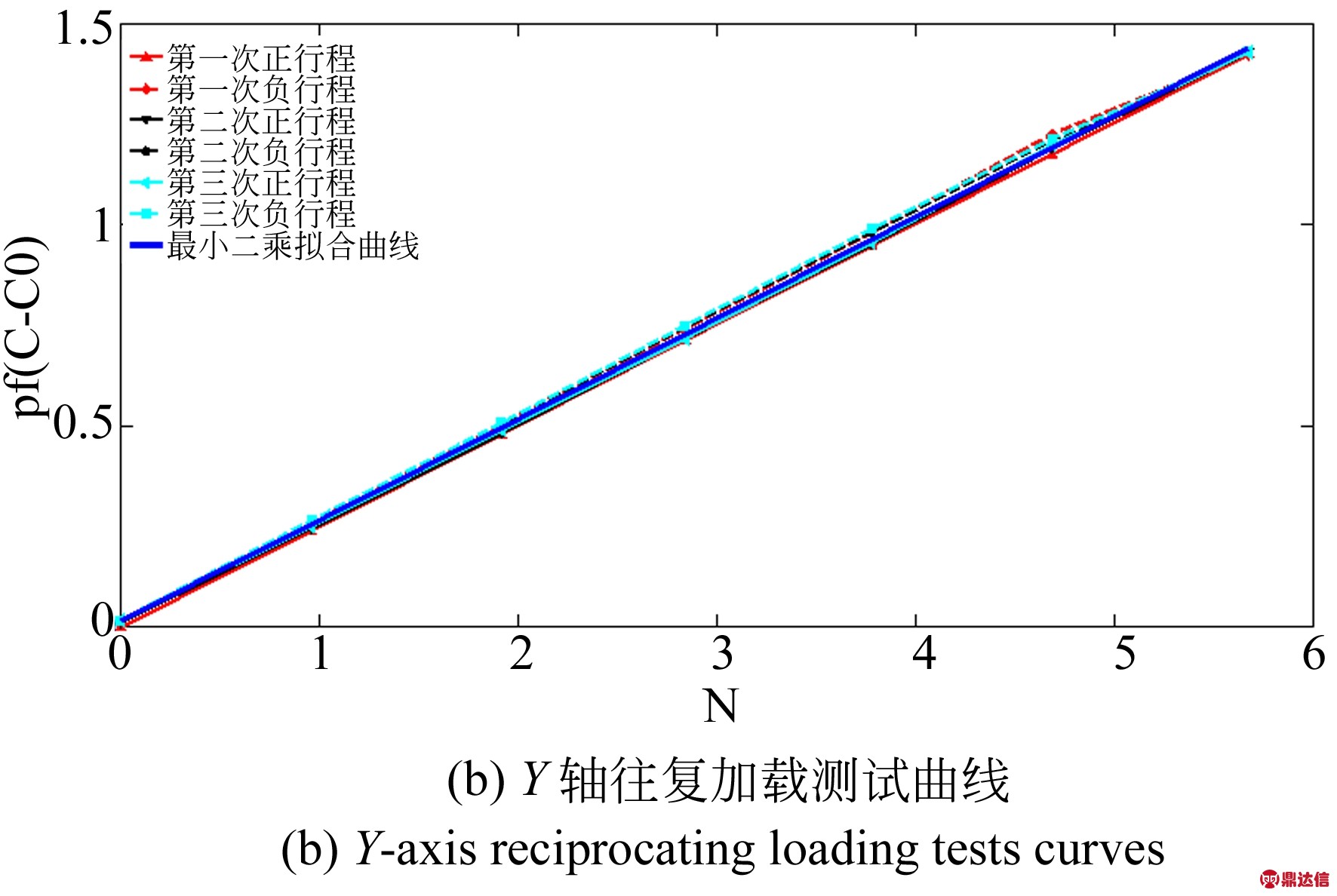
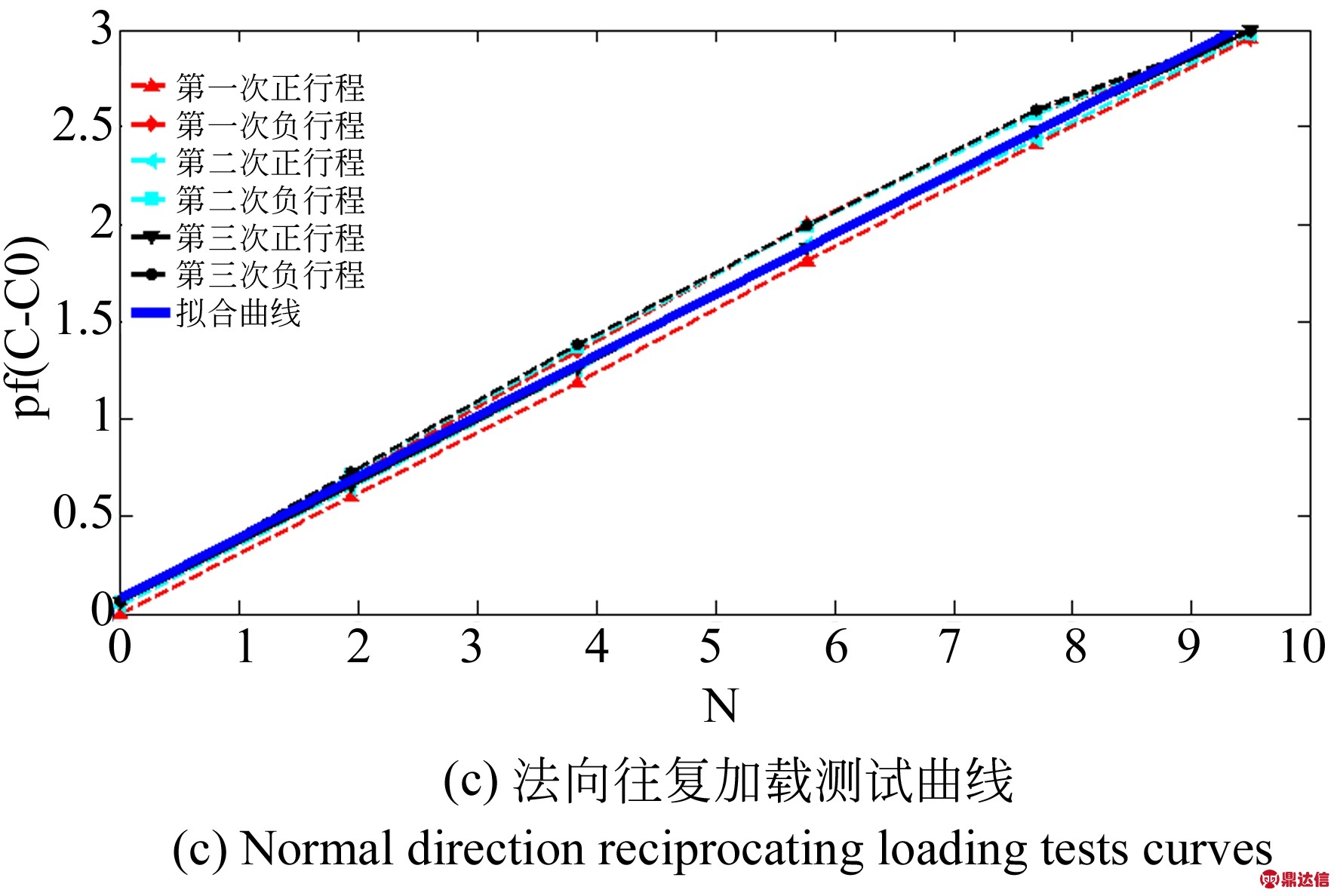
图6 传感器三轴往复加载特性曲线
Fig.6 Triaxial reciprocating loading characteristic curves of the sensor
计算出的触觉传感器各项静态特性指标如表2所示,切向X最小二乘拟合公式:Cx=0.206Fx+0.028,测量灵敏度为0.206 pF/N;切向Y最小二乘拟合公式:Cy=0.251 Fy+0.014,测量灵敏度为0.251pF/N。法向最小二乘拟合公式:Cz=0.148Fn+0.038,测量灵敏度为0.148 pF/N。从测试结果可以看出,实际输出与理论结算结果较为接近,证明了参数化设计的正确性,同时法向和切向灵敏度量级相当,且均具有较高的灵敏度。关于灵敏度的实际值与理论值之间存在的偏差来源,主要是PCB板和介质之间粘合过程中夹杂的气泡及网格被一定粘结剂填充引起的。
表2 触觉传感器静态性能指标
Tab.2 Tactile sensor static performance index
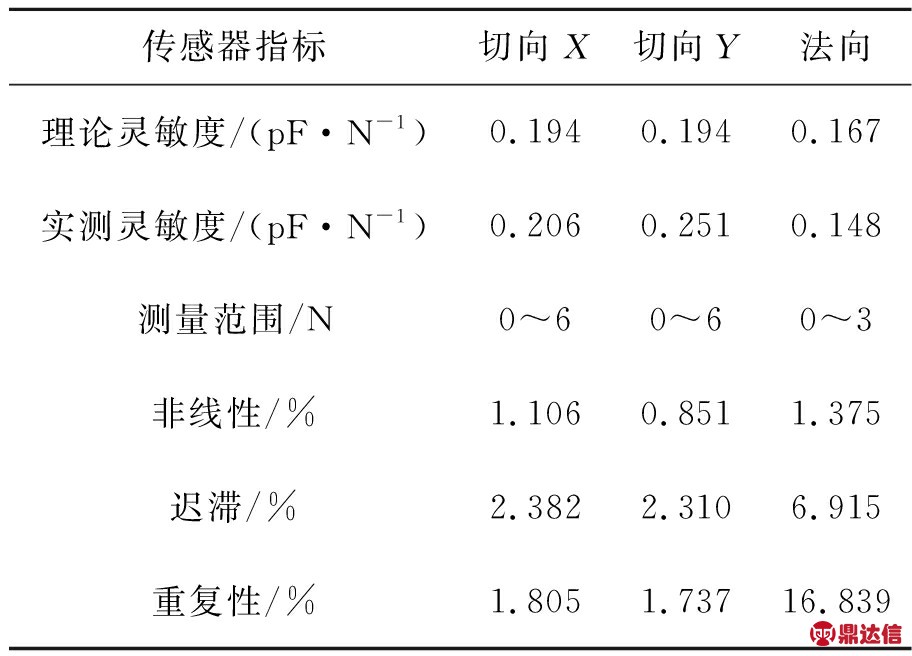
在验证解耦的测试中,耦合程度用多维力之间的静态耦合比表示[16],其表达式为:
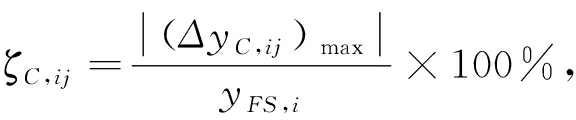
(19)
其中,yFS,i表示传感器在i方向加载时的满量程输出,|(ΔyC,ij)max|表示传感器在j方向加载时i方向的最大变化量。从公式看ξC,ij越小,解耦效果越好。
静态耦合的测试方法为分别对传感器各轴进行静态加载,每次单轴加载至满量程,记录传感器三轴力的输出变化量,进而分析各轴的静态耦合比。其中,触觉传感器切向满量程为0~600 g,测试每次间隔100 g加载,法向满量程为0~300 g,每次间隔50 g。数据获取方法与灵敏度测试相同。最后得到的传感器三轴的输出变化结果,如图7所示。
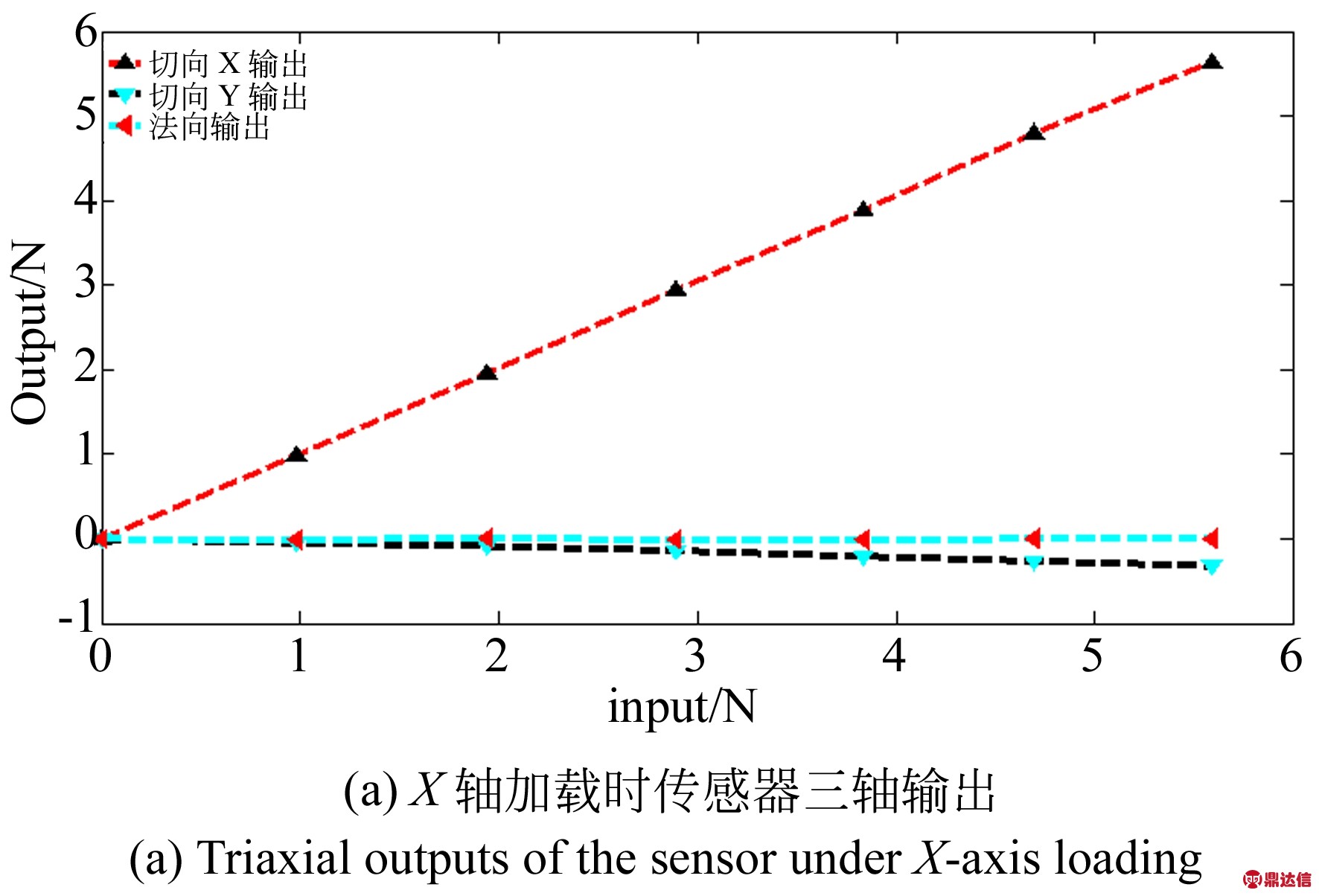
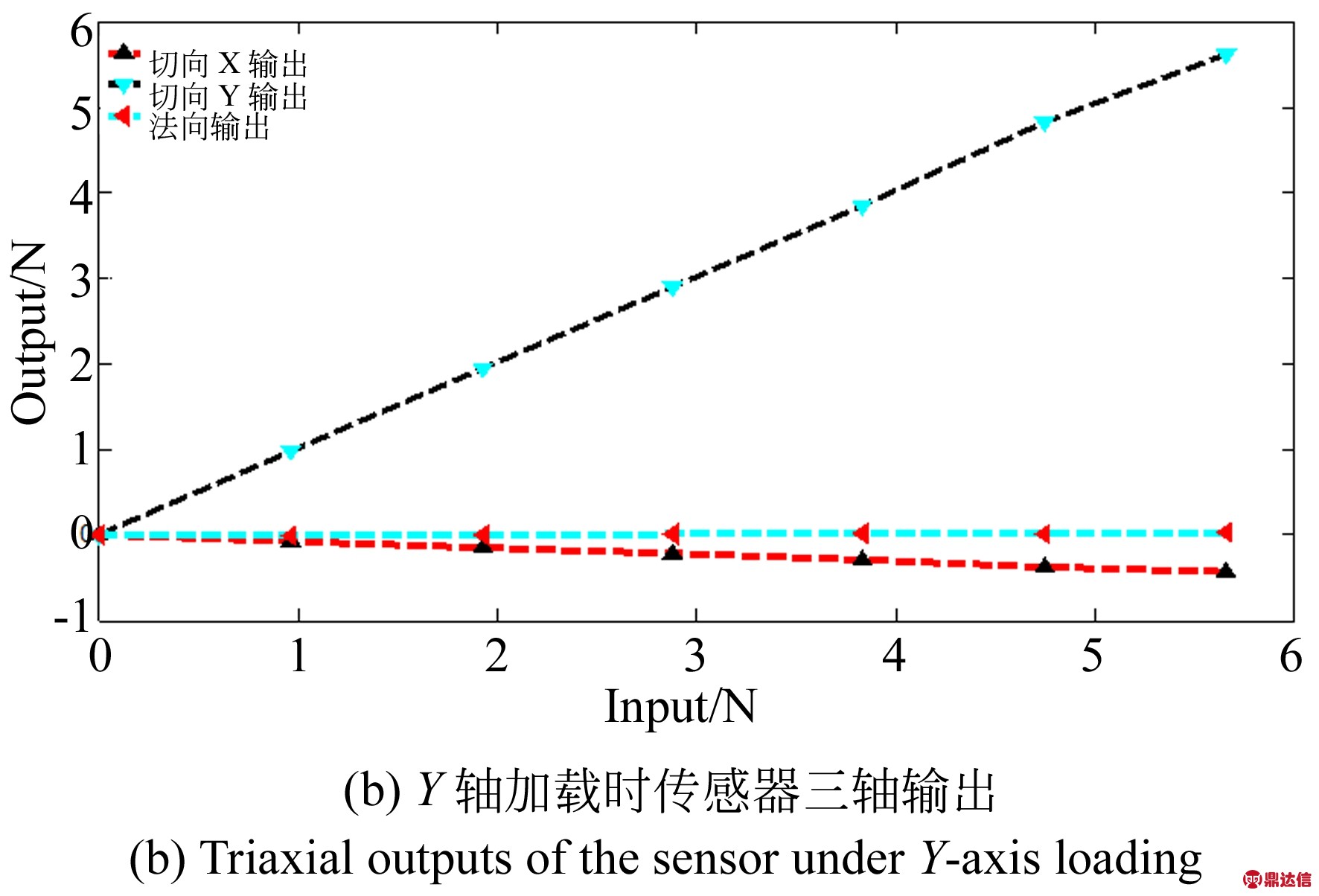
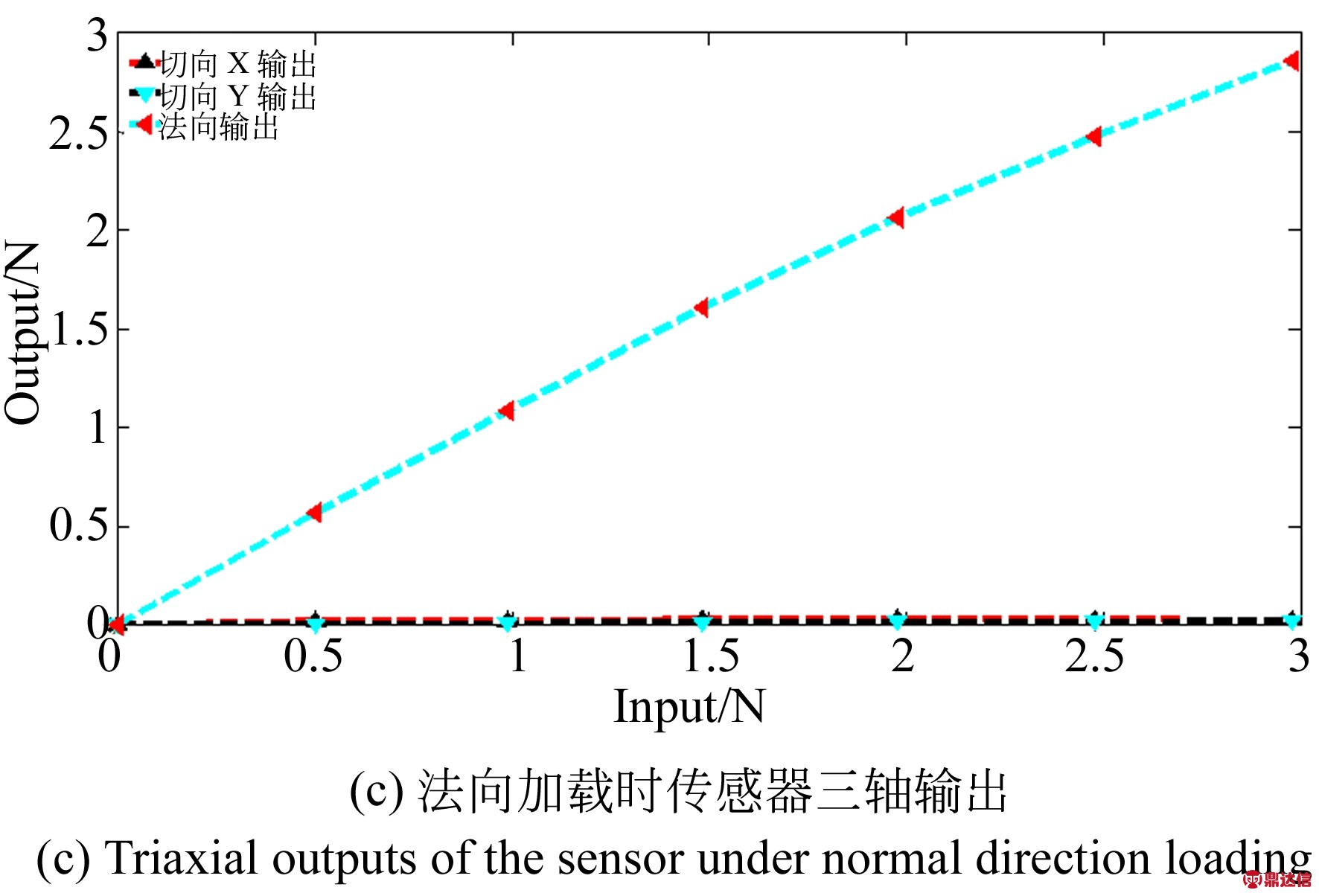
图7 传感器三轴加载输出
Fig.7 Outputs of the sensor under Triaxial loading
其耦合结果如表3,从表中可以看出法向-切向之间通过传感器结构的参数化设计取得了较好的解耦效果,静态耦合比最大为1.051%;另外,通过进一步分析发现切向X-Y的最大静态耦合比为7.636%,相较于切向-法向解耦结果稍微偏大,这是由于切向X,Y共用切向介质层的原因,当介质层产生横向位移变化时,其纵向也会发生微小的形变,因此切向X,Y输出之间会存在微弱的耦合。
表3 触觉传感静态耦合比
Tab.3 Static coupling ratio of the tactile sensor
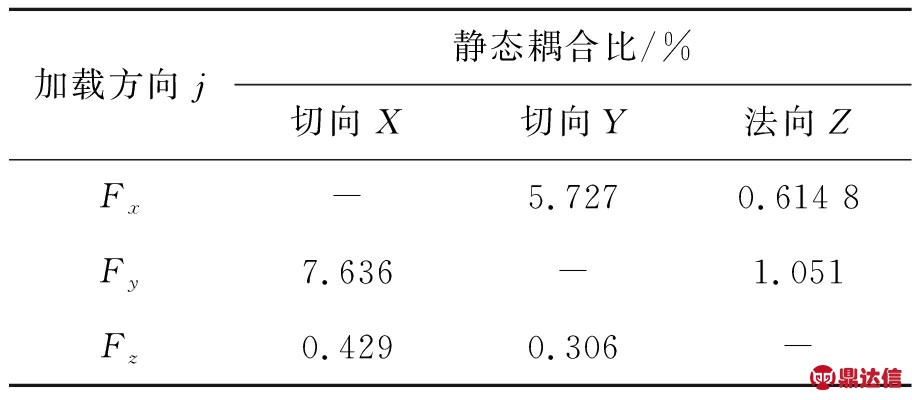
最后,将本传感器与公开报道的多维触觉传感器进行对比,如表4所示。通过对比分析表明在切向和法向相同量级的测量范围情况下,本文设计的触觉传感器具备三轴相同量级且高灵敏的测量特性,测量灵敏度均高于0.1 pF/N,无突起结构。此外本传感器还表现出了优良的解耦效果,三轴耦合比最大不超过8%。
表4 公开报道的触觉传感器与本文触觉传感器性能对比
Tab.4 Tactile sensor performance of publicly reported compared with this paper
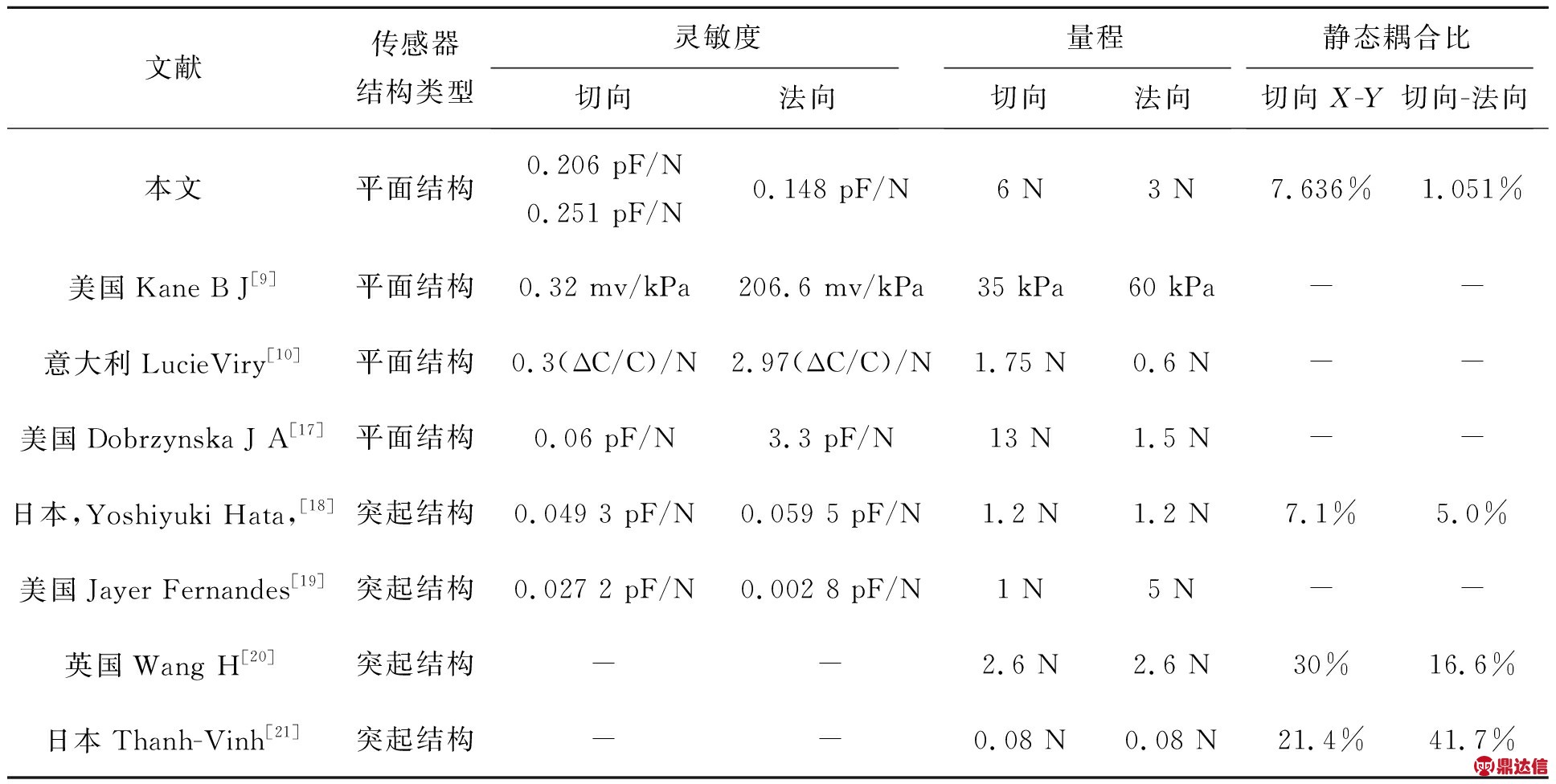
5 结 论
本文基于多层电容结构,设计了一种可实现三轴力解耦测量的高灵敏触觉传感器,开展了各层的高灵敏和解耦测量原理分析及参数化设计研究,完成工艺制备并搭建测试系统进行测试。结果显示本传感器切向X,Y和法向的灵敏度分别为0.206 pF/N, 0.251 pF/N,0.148 pF/N;切向X-Y之间的最大静态耦合比为7.636%,切向-法向之间的最大静态耦合比为1.051%。最后通过与已有的部分传感器对比,证明了本文研制的触觉传感器不仅达到了三轴相同量级的高灵敏测量目的,还具有较好解耦特性;并且无突起结构,适用于分布式载荷力的高灵敏测量。
在传感器的测试结果中也发现,传感器对法向信号测量的迟滞性和重复性相对切向较差,后续将对传感器中法向测量单元的介质层稀疏网格参数优化及粘合工艺开展进一步研究,以降低法向测量单元的迟滞和重复性误差。