摘要:采用真空蒸发镀膜技术设计制作了以云母为基片的薄膜热传感器,传感器包括一个用于热流测量的热电堆和一个用于温度测量的热电偶。综合测试发现:云母基片薄膜热传感器性能良好。封装后,薄膜热电偶的静态标定拟合直线相关系数均可以达到0.999。薄膜热流计的静态标定拟合直线的相关系数为0.99439,测头系数为8.78886 W/(m2·µV),灵敏度为0.11378 µV/(W/m2)。薄膜热电偶的动态响应时间是0.446 s 且具有良好的复现性。随着加载热流的增大,薄膜热流计的动态响应时间变大,阶跃热流值为600 W/m2时响应时间为0.483 s。
关键词:膜;测量;瞬态响应;传热;燃料电池
引 言
基于薄膜技术的瞬态热传感器对非稳态热流体过程研究有重要意义。物理法和化学法是薄膜制备工艺中常见的两类工艺方法。物理法制备薄膜如蒸镀、溅射、离子镀等技术成熟,可以很好地完成薄膜的制备。化学法包括化学气相沉积和电镀等工艺[1]。
Hsiao等[2]利用蒸镀法在聚酰亚胺基片上沉积了p型(Bi-Te-Sb)和n型(Bi-Te-Se)热电偶,选择合适的蒸发速率可以提升两种热电偶的性能。刘海军等[3]用掩膜图形化和射频磁控溅射的方法,在Al2O3陶瓷基片上制作了Pt/ITO 薄膜热电偶。Glatz 等[4]在190µm 厚的聚合物模块中用电镀的方法将Cu-Ni 热电偶对嵌入其中。Satish 等[5]采用真空镀膜技术,以镍基合金为基底制作了K 型热电偶(NiCr-NiMn)。Wang等[6]采用印刷电路工艺制作了用于瞬态高温热源测量的传感器,发现基于印刷电路工艺制作的传感器的响应比基于陶瓷的更快速。
对于薄膜热电偶的动态标定目前为止还没有统一的方法。祁漫宇等[7]用激光脉冲装置对薄膜热电偶进行动态标定。周川等[8]对薄膜热电偶进行标定之后,运用人工神经网络模型对结果进行了处理,使动态特性曲线有了更好的拟合精度。Chu等[9]设计了金/镍薄膜热电偶并用脉冲激光对热电偶的动态特性进行研究,测量了响应时间和下降时间两个动态响应参数。蒋均颖[10]、聂志华[11]采用阶跃响应法对自制的薄膜热电偶传感器进行了标定。
曾祥森等[12]建立了一维非稳态导热模型,通过仿真得出了传感器的动态响应;对薄膜热电偶进行动态标定实验。Jin等[13]对自制的ITO薄膜热电偶进行了标定和实测,加入的保护层可以提高热电偶在高温下的稳定性。Zhang等[14]设计制作了一种钨-铼薄膜热电偶,并针对此种热电偶的特性进行了建模与仿真分析。杨丽红等[15]对自制的薄膜热电偶进行了静态标定实验,发现Cu/CuNi 薄膜热电偶的灵敏度受厚度影响。
在薄膜热流计相关领域,Ewing等[16]设计了包含一个特殊的信号放大器的薄膜热流计阵列,该阵列采用镍/铜作为电极材料,聚酰亚胺薄膜作为基片。Jasperson 等[17]基于微加工和微铣削技术在铜基片上制作了薄膜热流计,用于测量微通道热沉的热通量。Azerou 等[18]研制了薄膜热阻式热流计。Ammar等[19]研制了一种用于测量微通道的温度和热流的分布热传感器。Frankel 等[20]用理论分析的方法对薄膜热流计的标定结果进行分析。
作为一种高效、环境友好的发电装置,燃料电池直接将存储在燃料与氧化剂中的化学能转化为电能[21]。温度在电池运行中扮演着重要的角色。小尺寸的薄膜热传感器植入电池后对电池性能影响小,在燃料电池热测试中会起到更大的作用。
刘佳兴[22]利用真空蒸发镀膜技术制作薄膜热流计,自制的热流计基片采用二氧化硅,电极材料是钴和锑,薄膜热流计线性度好,时间常数为0.66044 s。He 等[23]设计制作了铂金热敏电阻传感器,并将其嵌入Nafion 膜中测量电解质层的温度,与传统薄膜热电偶传感器的灵敏度接近。吴铄等[24]设计并制作了基于二氧化硅、聚酰亚胺薄膜和氧化铝陶瓷3种不同基片材料的复合薄膜热传感器。Lee 等[25]采用微机电系统技术将易弯曲的微型传感器集成到燃料电池里在线测量温度和电压分布。他们还利用微机电系统技术在不锈钢箔片基板上制作了多功能微型传感器,并将其植入到质子交换膜燃料电池中[26]。Lee 等还利用微型传感器对发光二极管接点的温度[27]、微型重整器内温度[28-29]进行测量。
本文采用真空蒸发镀膜技术,制作了可以实现温度和热流同步测量的薄膜热传感器。之后通过静态和动态的标定实验,以及对传感器进行复现性研究,测试验证了传感器的性能。
1 薄膜传感器的制作
热阻式热流计是应用较为广泛的一类热流计,当有热流通过传感器时,热阻层上下两侧会产生温差ΔT,这个温差使得热阻层覆盖的差分热电堆产生一定的温差电动势E。在一维稳态的情形下,由傅里叶定律可知

式中,q为热通量,W/m2;λ为热阻层材料的热导率,W/(m·K);ΔT 为热阻层两侧的温差,K;ΔX 为热阻层的厚度,m。
本文采用真空蒸发镀膜技术,在云母基片(性质见表1)上按一定顺序蒸镀热电堆和热阻层。制成后的薄膜传感器整体长50 mm,宽2 mm。热电堆的电极材料为纯度99.999%的铜和镍,厚度均为0.1µm。热阻层材料为二氧化硅,厚热阻层厚度为0.8µm,薄热阻层厚度为0.2µm。补偿导线采用的是与金属膜层材料相对应的纯铜丝和纯镍丝,直径均为0.2 mm。
薄膜传感器的结构如图1所示。热流计是由22个热电偶结点串联成11对的差分热电堆,两端结点分别通过两条铜镀层引线连接。通过在热电偶的结点处上方蒸镀不同厚度的二氧化硅热阻层,使上下两侧热电偶结点产生温度差,进而实现热通量的测量;中间区域设计了一个单结点的热电偶用于温度测量,热电偶结点两端分别通过铜镀层引线和镍镀层引线连接。图2 为制成的传感器实物图。图3所示为传感器引线方案实物图,传感器制作完成后,将其插入连接器的接口内,传感器引线和连接器内接线柱相连,压紧连接器接口的盖子将传感器固定。连接器另一端通过导线与数据采集器相连用于测量输出热电势。
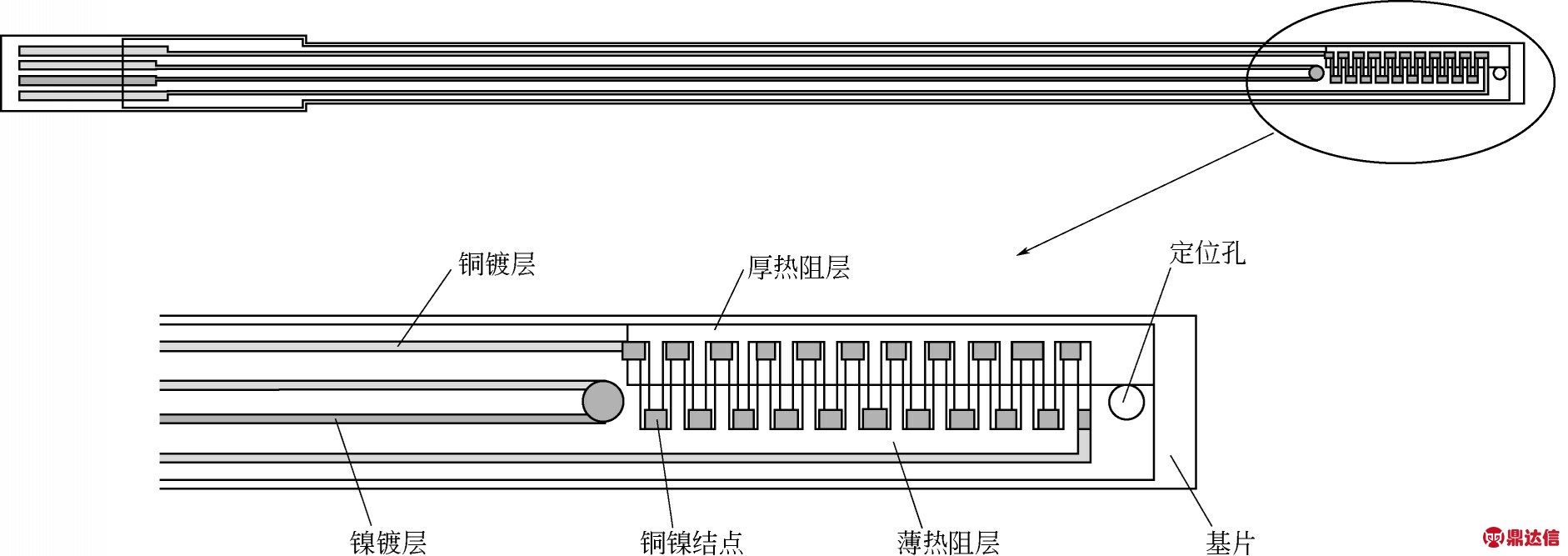
图1 薄膜传感器结构图
Fig.1 Structure map of thin film sensor
表1 云母基片的厚度和物理性质
Table 1 Thickness and physical properties of mica substrate

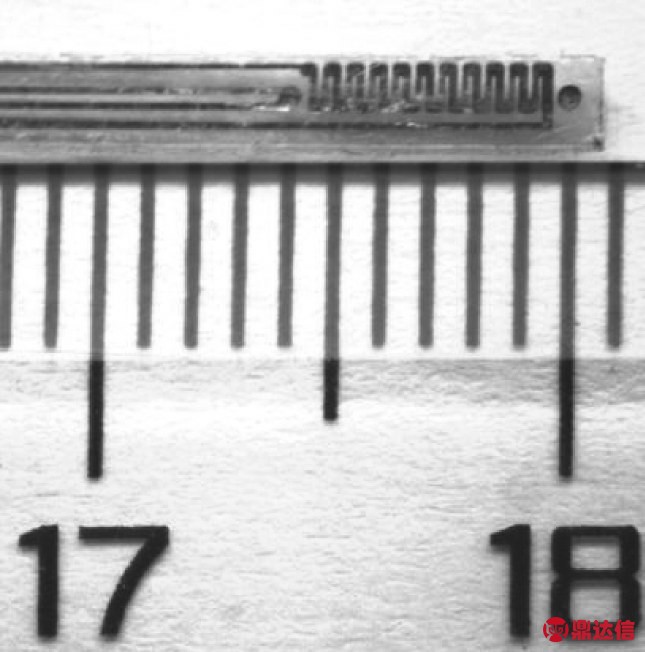
图2 薄膜传感器实物图
Fig.2 Physical map of thin film sensor
2 实验结果与讨论
2.1 静态标定
温度静态标定采用的方案是:云母基片传感器的温度测头固定在表面温度校验仪的控温表面。表面温度校验仪的温度由30℃升高到80℃,每隔10℃进行一次测量,共有6 个实验测点。考虑到将传感器放入燃料电池内部后,产生的水容易使传感器失效,因此在实际使用条件下用三防漆对传感器进行封装。图4 为封装前后温度标定结果的比较。封装前传感器的相关系数为:0.99863,0.99591。封装后传感器的相关系数为:0.99989,0.99953。封装前薄膜热电偶的灵敏度为:13.3654 µV/℃,15.0557µV/℃。封装后的灵敏度为:18.4332µV/℃,15.9236µV/℃。通过对比发现,封装后灵敏度下降,线性度有所增加。
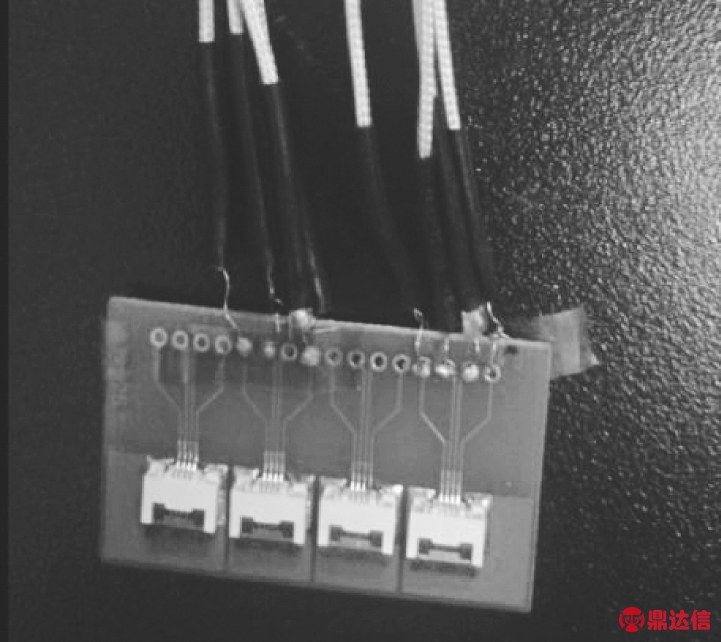
图3 引线方案实物图
Fig.3 Physical map of lead wire
同样地,将自制的薄膜传感器热流测头紧贴在表面温度校验仪的控温表面,把标准热流计放置在相同位置接收热流,记录下标准热流计的热流输出值。图5 给出的是热通量静态标定结果,拟合直线的相关系数为0.99439。薄膜热流计的测头系数为8.78886 W/(m2·µV),灵敏度为0.11378 µV/(W/m2)。此时,薄膜热流计静态标定的拟合直线方程为

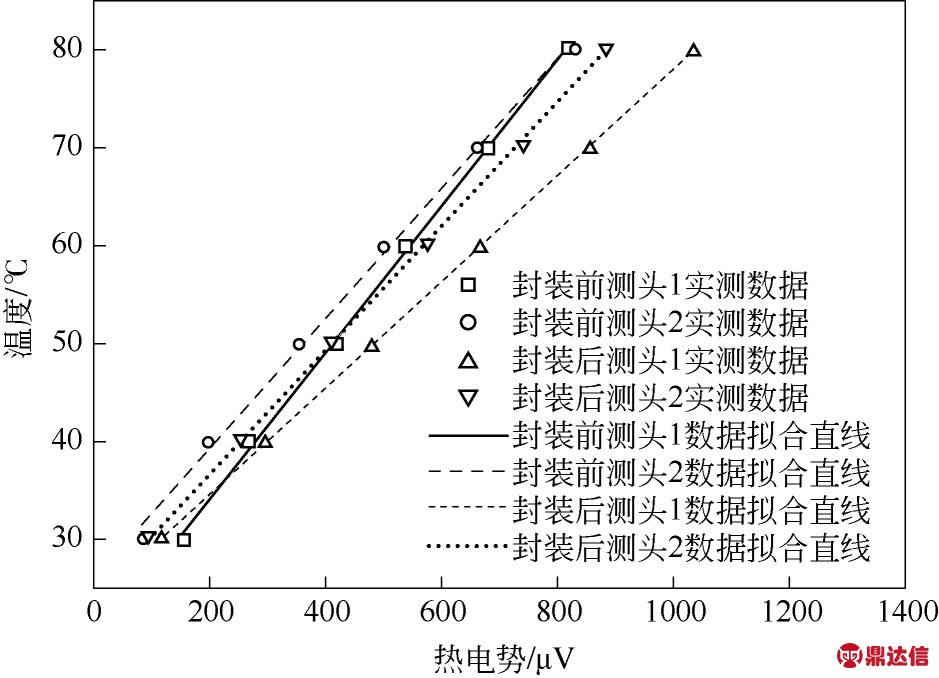
图4 云母基片传感器封装前后温度标定结果比较
Fig.4 Calibration results comparison of temperature on mica substrate sensor
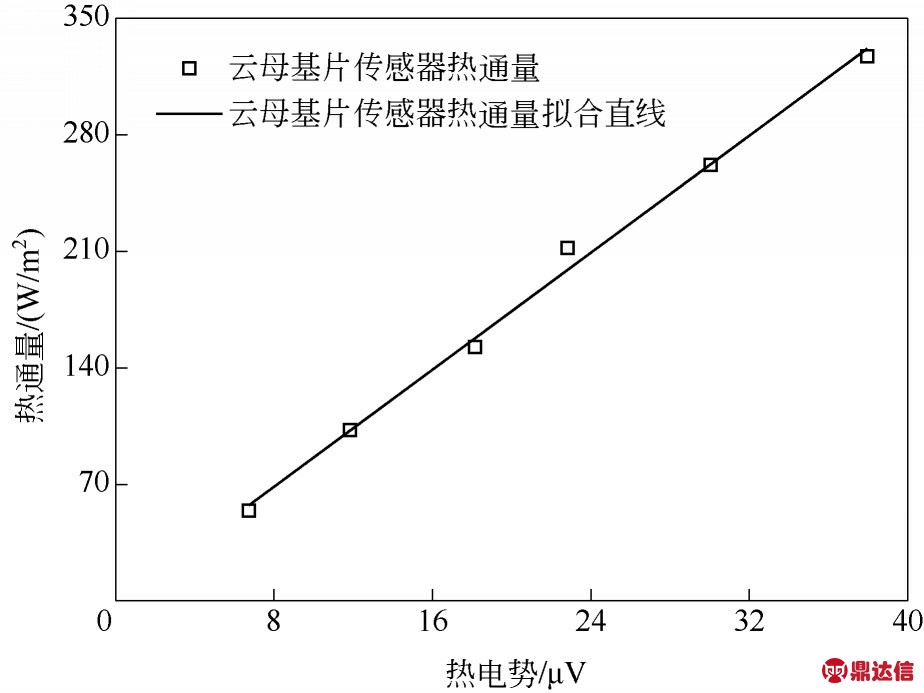
图5 基于表面温度校验仪的云母基片传感器热通量的标定结果
Fig.5 Calibration result of heat flux on mica substrate sensor with surface temperature calibrator
对于静态标定,用表面温度校验仪标定温度和热通量时,传感器的灵敏度更好,可以推测,将传感器布置在被测物体表面时能快速监测温度和热通量的变化。另外,用表面温度校验仪进行温度和热通量的标定时,测头紧贴于控温表面的这种布置方式与传感器布置在被测物体表面时的情况比较类似,因此,采用这种方法进行标定时,测量数据更准确。
2.2 动态测试
薄膜热电偶属于一阶系统,根据一阶系统对阶跃响应的理论,时间常数τ 是薄膜热电偶输出值与初始温度之差达到温度阶跃值63.2%时所用的时间。它与热电偶搭接处两种不同金属材料的薄膜厚度、薄膜材料与基片材料的匹配度都有关。τ 越小,则响应越快,测量精度越高。时间常数的计算如下[30]

式中,T 为热电偶的指示温度,T0为热端点的初始温度,Te为阶跃温度,t为对阶跃温度的响应时间,τ为时间常数。当t=τ时,代入式(3)得

对于薄膜热电偶的动态测试,采用的是迅速投掷法:开始记录实验数据后,先将传感器置于室温下,之后迅速投入到恒温的热水中,用数据采集系统以10 Hz 的频率采集传感器温度测量单元的响应情况。图6是云母基片传感器的响应曲线。由响应曲线得到:薄膜热电偶的输出值快速上升,达到新的平衡需要0.7057 s,由此可知时间常数τ 为0.7057 s×63.2%≈0.446 s。为了进一步检测薄膜热电偶的复现性,在两个不同日期的同一时间进行了同样的测试,验证传感器的响应性能。热水温度80℃,室温为18℃。从图7 可以看出:薄膜热电偶对于温度变化能够较快响应,输出温度波形有较好的复现性。
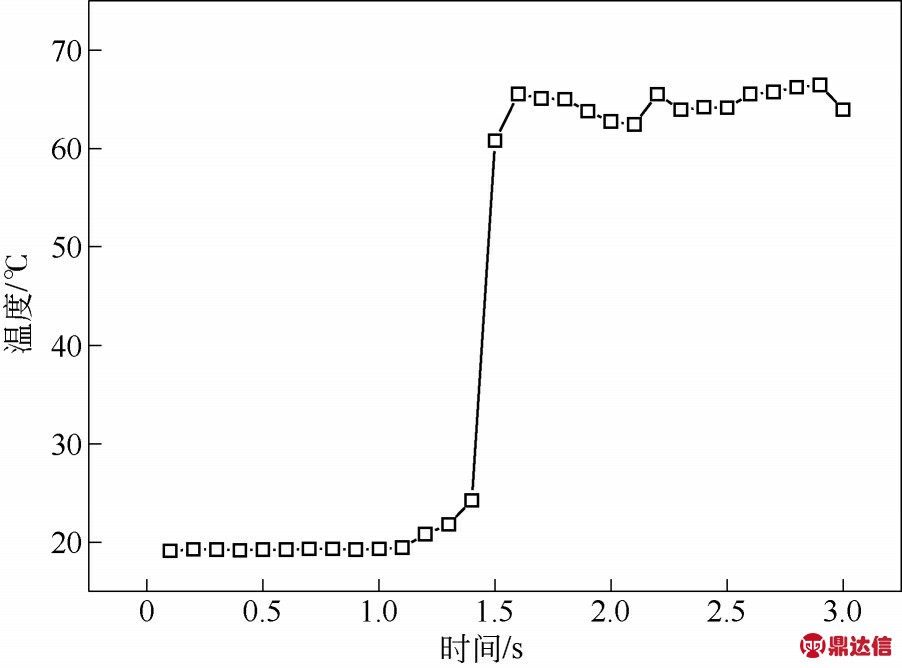
图6 云母基片传感器温度动态响应曲线
Fig.6 Temperature dynamic response of thin film sensor on mica substrate
在薄膜热流计的动态测试中,通过迅速打开和关闭卤素灯和传感器之间的遮光板,可以让传感器获得一个突变的热流。此过程中可以得到传感器的动态响应曲线。图8是云母基片传感器在卤素灯输出电压分别为150、180 和210 V 时热通量测量单元的动态响应曲线。由图可知,突然打开遮光板后,薄膜热流计表现出了较快的响应速度,并且输出热流值在一定范围内上下波动,当关闭遮光板时出现类似的响应情况。薄膜热流计在不同电压下都有着较快的响应速度。卤素灯电压升高,输出热流值增大。在不同阶跃热流值下,动态响应时间不同。通过计算得到:阶跃热流值为260、350、600 W/m2时,响应时间分别为0.158、0.316、0.483 s。由此可见,阶跃热流值越大,响应时间越长。
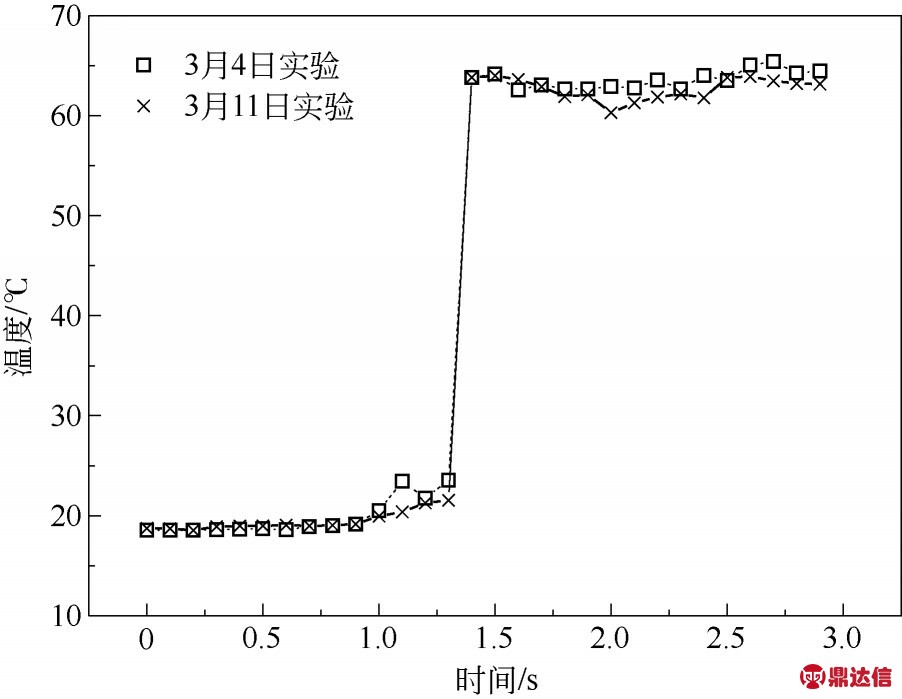
图7 云母基片薄膜传感器温度动态响应复现图
Fig.7 Reproducibility of dynamic response of temperature on mica substrate sensor
设定卤素灯的输入电压,对传感器加载周期为10 s 的动态热流。图9 显示了不同输入电压下周期性加载热流时,云母基片传感器动态响应曲线。薄膜热流计对周期性热流有较快的响应:在加载不同热流的情况下,薄膜热流计都能快速响应,并且很快达到稳定状态。而在突然遮挡了卤素灯辐射后,输出值立刻下降,也能快速达到稳定。三个周期内热流输出都呈现了同样的变化趋势。随着辐射热流周期性加载和卸载,传感器的输出总体也随之呈现阶梯状变化。但是从图9 中也可以看到,当电压增加到180 V 时,在最后一个卤素灯加载功率周期时,传感器的输出热流相比之前整体升高。
3 结 论
基于真空蒸发镀膜技术制作了可以同时监测温度和热通量的薄膜热传感器,测试了传感器的静态和动态特性,研究了传感器的复现性。得到以下结论。
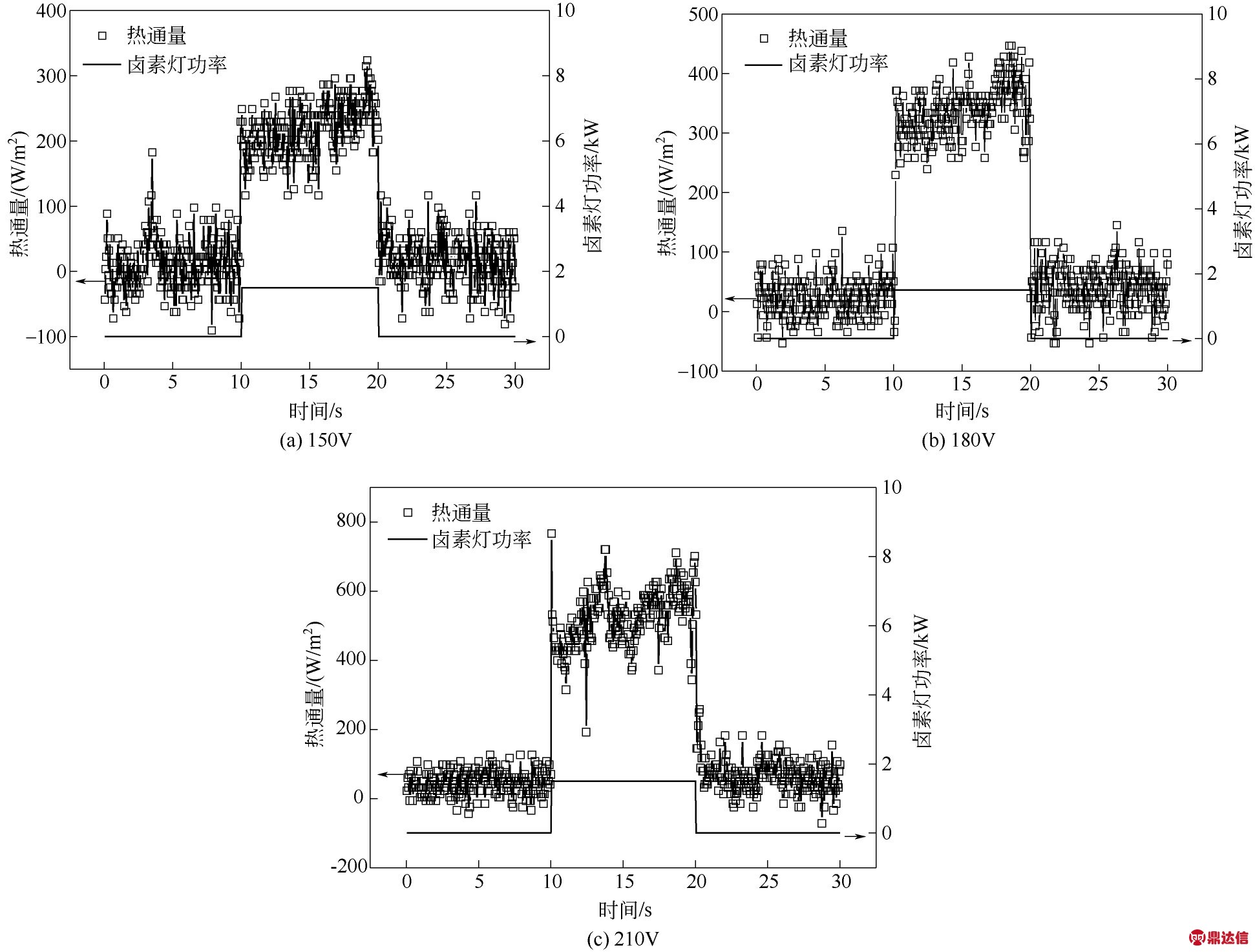
图8 不同电压时云母基片传感器的动态响应曲线
Fig.8 Dynamic response of sensor on mica substrate at different outputs
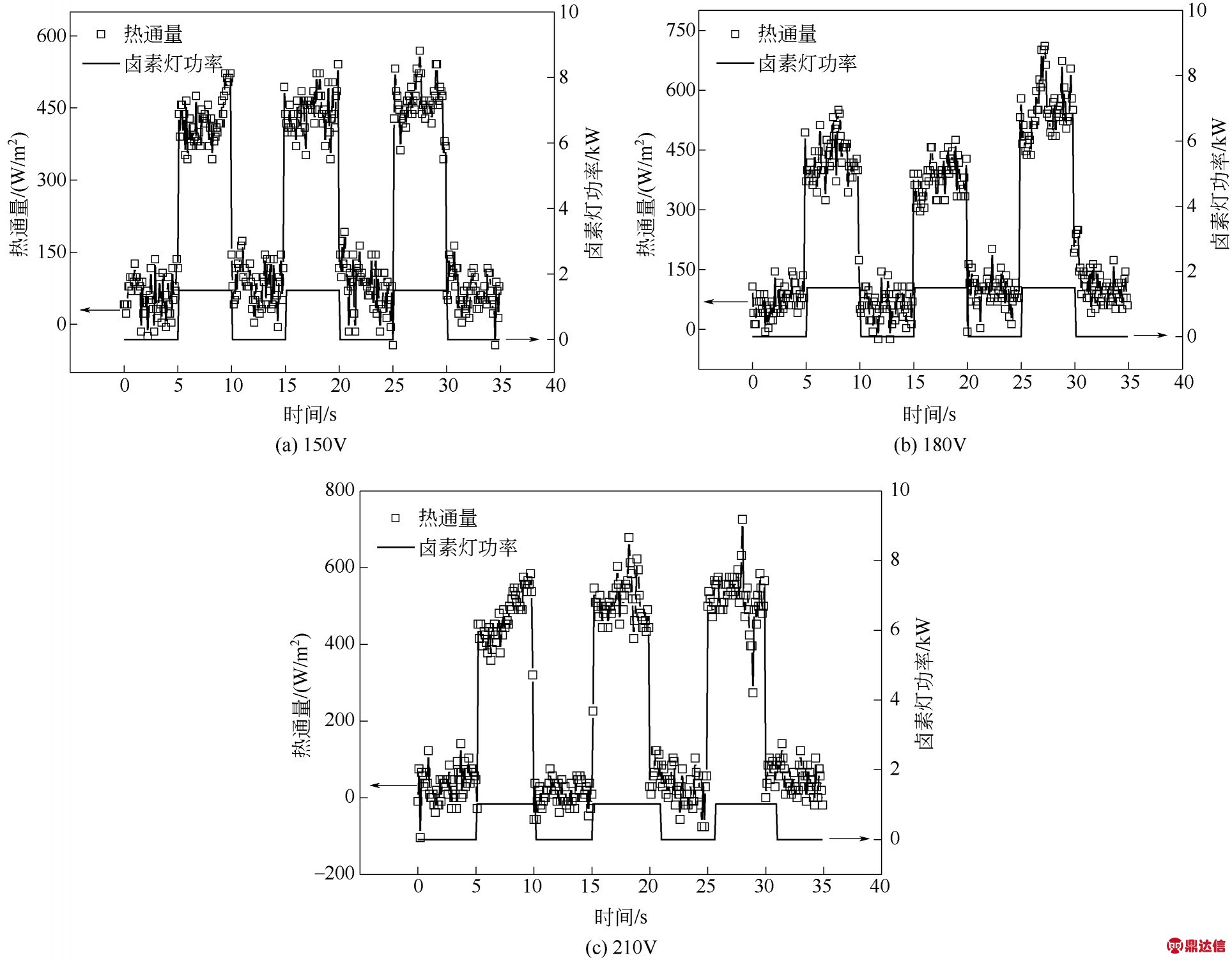
图9 不同输入电压下周期性加载热流时云母基片传感器的动态响应曲线
Fig.9 Dynamic response of sensor on mica substrate to period heat flux at different outputs
(1)封装前,薄膜热电偶的静态标定拟合直线的相关系数为:0.99863,0.99591。薄膜热流计静态标定拟合直线的相关系数为0.99439,测头系数为8.78886 W/(m2·µV),灵敏度为0.11378 µV/(W/m2)。用三防漆对传感器封装后,薄膜热电偶线性度增大,相关系数均达到0.999,而灵敏度有所下降。
高考报名,误打误撞进入北京印刷学院;放弃舒服的国企工作,进入民营企业;背水一战,选择“下海”创业……当庄浩向我们讲述自己的创业经历之时,闽南人特有的“爱拼才会赢”的精神,以及与生俱来的果断、有主见的性格,逐渐显现。其自己也坦然,“我从小就很有想法”“我做每件事,一定要做出个结果,遇到问题,会打破沙锅问到底,而且还得问问砂锅是怎么破的”。或许,正是骨子中的那股执着,成就了厦门吉宏的几年一跨步式的前进。