摘要:为了解决微特电机端盖焊缝焊接难度较大,人工焊接效率低且易焊偏等问题,设计了一种旋转式电机端盖全自动焊接装置,包括机架、工件夹具、输送装置、检测装置、焊接装置和上下料装置等。工人只需将工件放在上料工位的夹具上,输送装置将工件输送至焊接工位自动完成焊接和检测工序,最后下料装置自动将焊接好的工件移出,整个过程无需人工介入,有效提高了生产效率和产品质量。同时驱动装置使工件夹紧装置转动,实现端盖的连续焊接,有效防止焊接偏离,且由于焊枪不需要转动,其电源线也不易出现卷绕问题。设备已用到实际生产中,生产节拍达6s/件,焊接同轴度达到0.08,报废率低于0.5‰,效果较好,达到技术要求。
关键词:电机端盖;自动焊接;工件转动;连续焊接
0 引言
微特电机的生产加工过程中,需要将机壳与端盖焊接在一起,目前的焊接作业由人工手动完成,工人首先将机壳和端盖安装固定在相应的夹具上,再人工将机壳和端盖焊接在一起,工人的工作环境较差和劳动强度较大,且人工固定和焊接容易出现失误和工艺不一致等问题,难以保证产品质量。另外,焊接过程中产生的焊烟、高温焊渣易对工人造成伤害,存在一定的安全隐患。针对此问题,国内很多文献提出不同的解决方式主要有:①采用数控焊接方式[1-2],造价高;②焊接专机[3],编程复杂后期升级改造难;③夹具的改造设计[4-6],有一定的借鉴作用,但无法实现柔性生产。
为了解决以上问题,设计了一种电机端盖全自动焊接装置,包括机架、工件夹具、输送装置、检测装置、焊接装置和上下料装置等。工人只需将工件放在上料工位的夹具上,输送装置将工件输送至自动焊接工位和检测工位,最后下料装置自动将焊接好的工件移出,整个过程无需人工介入,有效提高了生产效率和产品质量。同时驱动装置使工件夹紧装置转动,实现端盖的连续焊接,有效防止焊接偏离,且由于焊枪不需要转动,其电源线也不易出现卷绕问题。设备已用到实际生产中,生产节拍达6s/件,焊接同轴度达到0.08,报废率低于0.5‰,效果较好,达到技术要求。
1 整体机械结构设计
电机端盖全自动焊接装置,包括机架、工件夹具、输送装置、焊接装置、检测装置和上下料装置等,如图1所示。工件安装在夹具上并由输送装置输送,依序经过上料工位、焊接工位、检测工位和下料工位。
焊接装置由4台焊枪组成,共同完成工件的焊接作业。为了保证端盖的同轴度,要求4台焊枪同时进行;检测装置用于检测位于检测工件的焊高和漏焊情况;最后下料装置将位于下料工位夹具上的工件从夹上取下并移出。整个过程,工人只需将工件放置在位于上料工位的夹具上,设备依次自动完成夹紧、焊接、检测和下料等工序,有效提高了生产效率和保证产品质量。
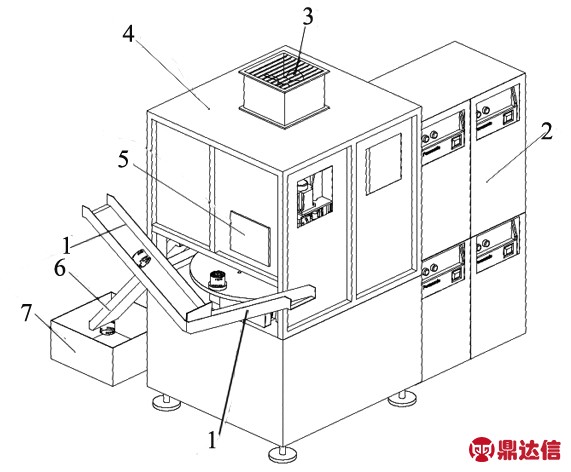
(a)外部结构图
1.上料滑道 2.焊接系统 3.排气系统 4.机架 5.控制面板 6.下料滑道 7.收料器
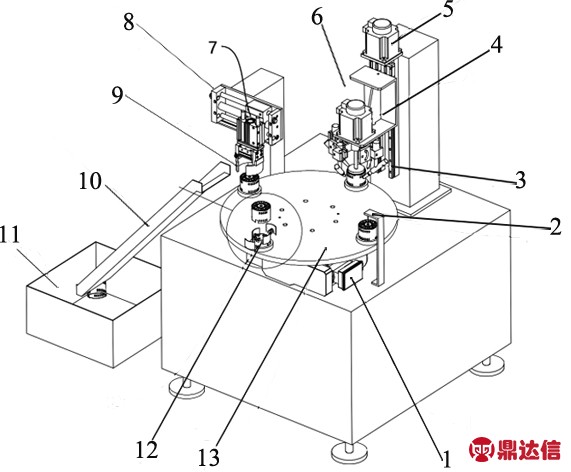
(b)内部结构图
1.第一驱动装置 2.检测装置 3.焊枪 4.第三驱动装置 5.第二驱动装置 6.焊接装置 7.行走机构 8.下料装置 9.机械爪 10.下料滑道 11.收料器 12.夹具 13.转盘
图1 整体机械结构图
机架上设置有靠近上料工位的两个上料滑道,和靠近下料工位的下料滑道,两个上料滑道分别用于输送存放电机的机壳和端盖,工人从两个上料滑道中取料拼装成待焊工件,并将其放在夹具上,下料装置将下料工位上的工件移出到下料滑道上,通过下料滑入相应的收料容器内。
输送装置包括转盘和用于驱动转盘的第一驱动装置,夹具设置在转盘上可随转盘转动,对夹具上的工件进行输送,实现循环作业,便于工人上料和回收加工好的工件,并能有效减小设备体积。
检测装置包括机械式检测机构、传感器和摄像器等检测结构,在机架上设置有控制器,可以记录每个工件的检测结果,同时利用控制器来协调控制各部件的动作以实现自动化运行,其中控制面板用于工人设定各项参数和对工作状态进行监控。
2 工装夹具的设计
如图2所示为工装夹具结构图,工装夹具包括卡盘、卡爪和卡板等。工件由机壳和端盖组成,卡盘插设在机壳的内腔中,卡盘的卡爪上具有与机壳内壁相适配的卡板,卡爪张开将卡板压紧在机壳的内壁上,最终将工件固定在夹具上,夹具能适用于多种不同尺寸规格的机壳,适用范围广。
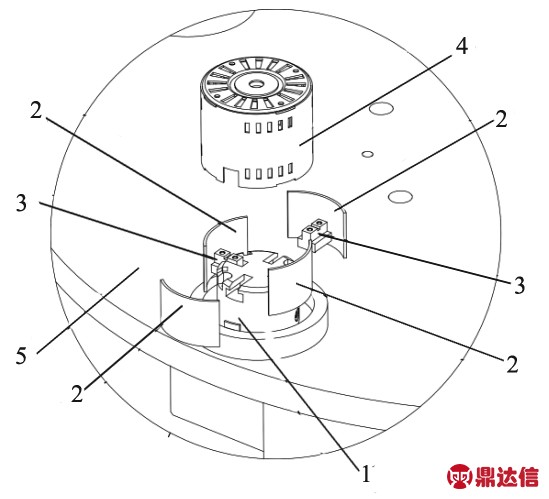
1.工装夹具 2.卡板 3.卡爪 4.工件 5.转盘
图2 工装夹具结构图
由于卡爪上设置了与机壳内壁相适配的卡板,能增大与机壳内壁的接触面,分摊受力,防止机壳变形,能够有效保证产品质量,实际应用中,夹具可采用弹性夹等其他常用结构。
3 焊接装置的设计
焊接装置是本设备中最重要也是最关键的部分,直接决定整个设备的生产效率和质量。焊接装置包括可纵向移动的移动座、在移动座上的转动座、压块和设置在转动座上的焊枪组成,如图3所示。移动座由第二驱动装置驱动而可相对机架上下移动,转动座由第三驱动装置驱动而可绕纵向的旋转轴转动;在工件到达焊接工位后,第二驱动装置驱动移动座下移,压块将端盖压紧在机壳上并驱动焊枪对准工件的焊接点,随后第三驱动装置驱动转动座旋转,焊枪对工件的弧形焊接点进行焊接作业,结构精密可靠,能够有效保证产品质量。
其中,压块设置在转动座上,第二驱动装置和第三驱动装置采用伺服电机驱动,能方便准确的对移动座和焊枪进行定位,移动座通过滑轨机构滑动设置在了机架上,第二驱动装置通过丝杆机构驱动移动座上下移动,能够有效提高移动座上下移动的平稳度,防止移动座出现偏移,转动座和压块则设置在了第三驱动装置的输出轴上,能保证焊枪的平稳移动并能准确对焊枪进行定位,有效保证焊接质量。另外,在机架外还设置了与焊枪相配套的焊接系统,焊接系统包括电源转换器、水冷器等。
多个焊枪并环绕旋转轴周向均匀分布,实际焊枪数量根据工件型号灵活调整,各焊枪能同时进行焊接作业,可减小每个焊枪所需的焊接长度,能够有效提高生产效率。
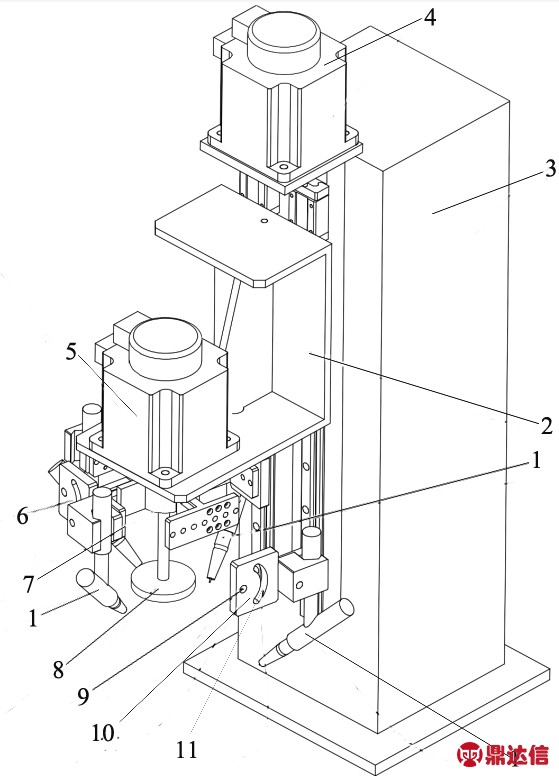
1.焊枪 2.移动座 3.机架 4.第二驱动装置 5.第三驱动装置 6.调节座 7.转动座 8.压块 9.枢接轴 10.调节座 11.调节槽
图3 焊接装置的结构图
设计中还包括与焊枪对应的调节座,调节座通过一横向的枢接轴枢设在转动座上并可由一锁紧装置锁紧固定在转动座上,焊枪设置在调节座上,能方便的调节焊枪的位置,使焊枪能够准确的与焊接位对齐,保证产品质量,并且能根据不同尺寸规格的工件灵活调节焊枪位置,有效提高了设备的适用范围。调节座上设置有环绕在枢接轴外的调节槽,锁紧装置包括设置在转动座上的锁紧件,锁紧件滑动插设在调节槽内,可与转动座一起将调节座夹紧,结构简单可靠,便于对焊枪进行调节,锁紧件采用螺接在转动座上的螺栓。实际应用中,锁紧装置也可采用插销等其他常用结构,调节座上沿调节槽设置相应的标识,便于对焊枪的位置进行准确调节。
4 下料装置的设计
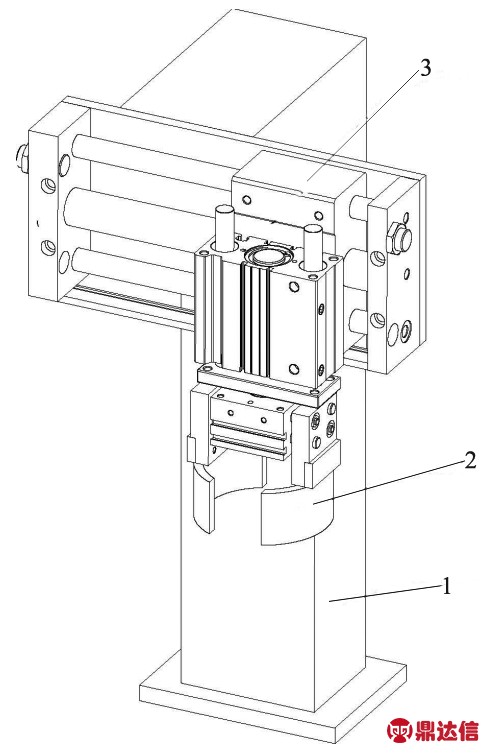
1.机架 2.机械爪 3.行走机构
图4 下料装置结构图
为了提高生产效率,在本设计中增加了简易灵活的下料装置,如图4所示。下料装置包括通过行走机构和机架上的机械爪,机械爪可从位于下料工位的夹具上夹取工件,通过行走机构将夹取的工件移出,行走机构和机械爪具有多种不同的结构和类型,也可应用到其他设备上,行走机构采用XZ双轴行走机构,结构简单可靠,易于装配和使用。
5 试用验证
为了验证设计的可行性,完成了设备的制造,并应用到中山市某电机制造公司,经过试运行,获得的改造前后对比数据如表1所示。
表1 改造前后对比数据
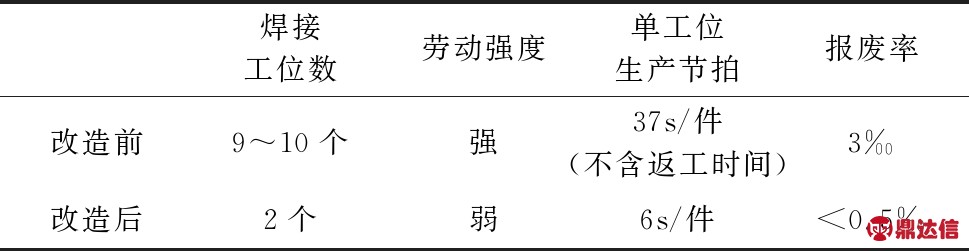
从数据表看出,改造前,要满足生产要求,必须配备9个以上的焊接工位,每个工位配1名焊接工人,完成工件的上下料、固定和焊接工作,劳动强度大,且另需额外1名工人进行焊接工艺的检测,效率低下;改进后,焊接速度大幅度提高,所需焊接工位大幅度降低,每个工位只需1名工人负责上下料,劳动强度较低,且保证焊接工艺的一致性。生产节拍达到6s/件,设备稼动率大于95%;同轴度达到0.08,焊高低于0.2mm,报废率小于0.05%,换模时间小于15min,完全满足客户的技术要求。
6 总结
为了解决微特电机端盖焊缝焊接难度较大,人工焊接效率低且易焊偏等问题,设计了一种电机端盖全自动焊接装置,包括机架、工件夹具、输送装置、检测装置、焊接装置和上下料装置等。工人只需将工件安装在上料工位的夹具上,输送装置将工件输送至自动焊接工位和检测工位,最后下料装置自动将焊接好的工件移出,整个过程无需人工介入,有效提高了生产效率和产品质量。同时驱动装置使工件夹紧装置转动,实现端盖的连续焊接,有效防止焊接偏离,且由于焊枪不需要转动,其电源线也不易出现卷绕问题。
经过实际应用,效果明显,生产节拍达6s/件,设备稼动率大于95%;同轴度达到0.08,焊高低于0.2mm,报废率小于0.05%,效果较好,达到技术要求。目前存在的缺点是仍需要人工上下料,后期将进一步改造成自动上下料。