摘 要:阀门执行器是工业控制中大量使用的用于阀门启闭的自动化器件,当其在爆炸极限工况下使用时,容器内产生的压力会使端盖产生变形,造成端盖的结构应力和变形分布不均,其中端盖厚度参数对其变形的影响尤为显著。本文通过公式计算和经验数据的数值缩比,对端盖厚度取2 个极限值,利用有限元软件ANSYS 对极限值区间内的不同端盖厚度进行静态受力分析,选取3 mm 作为设计厚度。为更好地验证设计的合理性,对整个端盖进行建模和爆炸数值模拟,结果显示最大应力值小于端盖材料的抗拉强度255 MPa,端盖最大位移量小于1 mm,变化范围较小。结果表明,设计具有一定的可行性。
关键词:阀门执行器;端盖设计;有限元分析
工业过程控制系统用隔爆型阀门执行器广泛用于工程中的排水、通风、抽采、洒水等管道中。隔爆型阀门执行器的端盖装在阀门执行器控制端,阀门执行器在爆炸极限工况下使用时,腔内压力会迅速增大,导致端盖损坏,必须符合GB/3836.2-2010《爆炸性环境第2 部分:由隔爆型“d 保护的设备”》的标准要求[1]。为最大程度地避免和减少这些不可控因素造成的危险,本研究对阀门执行器端盖进行了设计。
本文经公式计算,利用有限元分析进行数值模拟[2],为设计提供更为准确的理论依据。
1 隔爆型阀门执行器端盖设计及计算
1.1 三维模型设计
阀门执行器主要由箱体、传动部分、端盖等组成,如图1 所示是执行器的箱体和传动部分,其端盖在结构上考虑与箱体的连接及轴的安装位置,模型设计如图2 所示。阀门执行器端盖的耐压设计是其核心技术之一[3],这对材料提出了严格要求,目前一般选取铸铝。
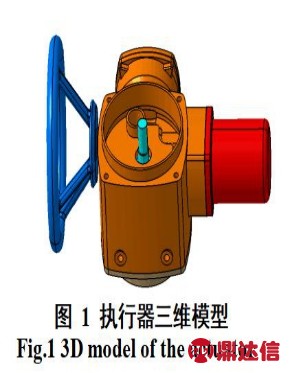
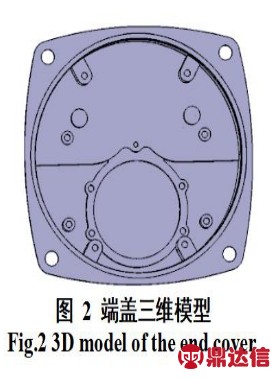
1.2 端盖壁厚确定
端盖在爆炸极限工况下使用需要满足防爆安全要求,根据材料设计端盖壁厚,其计算公式为:

式中:Dc 为端盖直径,m;Pε为理论计算压力,Pa;σ为材料的许用应力,Pa。
理想计算压力即为所需的等效静载荷,采用动力系数法进行计算[4]:Pe=PmCd (2)

式中:Pe 为等效静压力,MPa;Pm 为反射超压,MPa;P+为入射压力,MPa;P0 为初始大气压力,MPa;Cd 为动力系数。
P+的经验公式有Henrych 公式、Sadovskyi 公式等[5,6],本文以应用较广泛的Henrych 公式来计算。
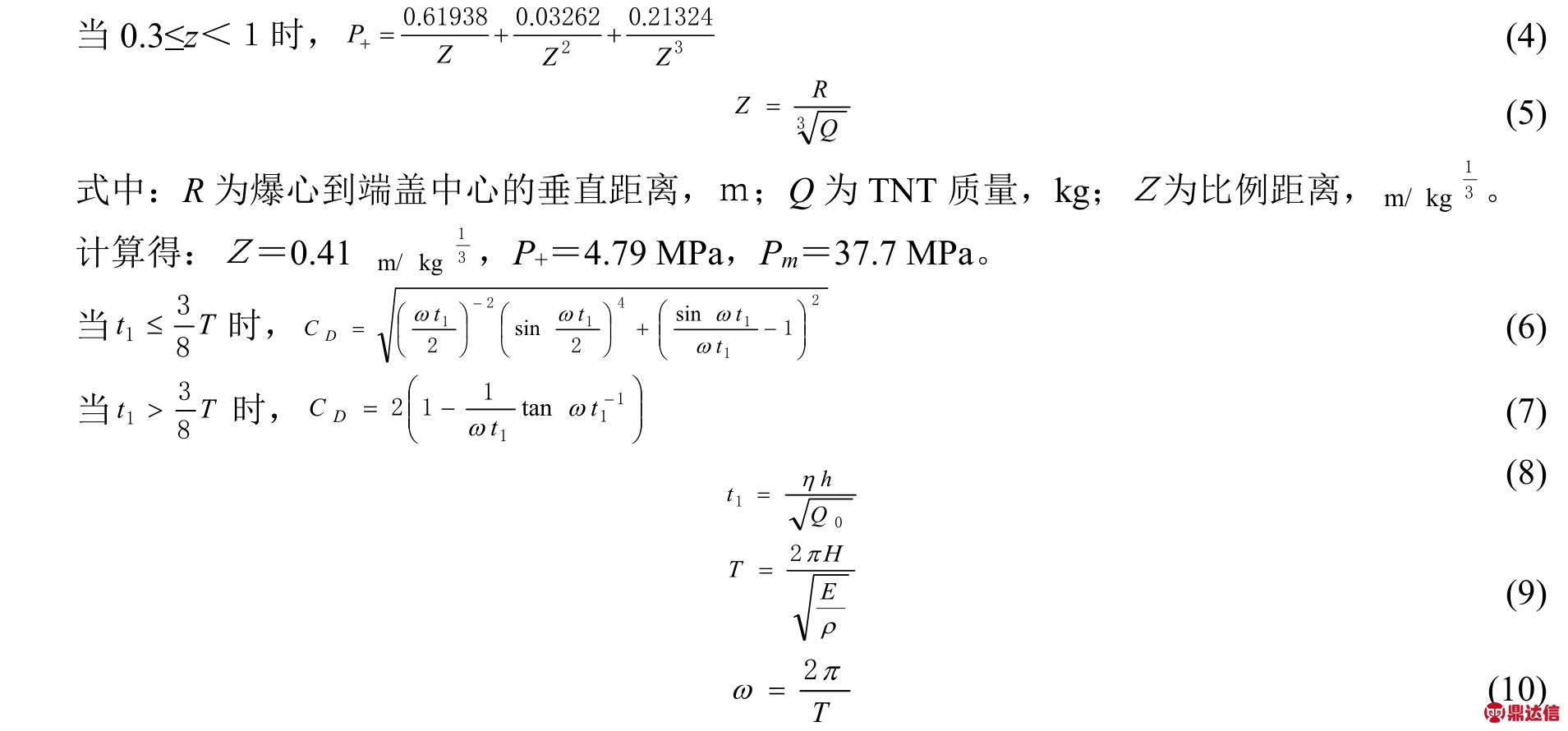
式中,t1 为等效作用时间,s;h 为引爆点到端盖的距离,m;Q0 为单位质量爆热,TNT 的Q0值为4860874.8 J/kg;η为经验系数0.5;ρ为材料密度,kg/m3;E 为材料的弹性模量,MPa。
根据公式计算可得:t1=0.02×10-3 s,T=0.126×10-3 s,Cd=0.21,δ=2 mm。
表1所示为早期苏联科学院[7]设计的防爆容器的部分尺寸,本设计实际模型尺寸接近第1行数据中按比例缩减至10%后的值。以第1行数据的10%计算δ=4.5 mm 为上限值,以计算厚度δ=2 mm为下限值,在上下值间每隔0.5 mm 取厚度值,利用有限元分析软件对不同壁厚的端盖进行初步静态力分析,选取位移和应力值合适的端盖壁厚来进行更为精准的动态力分析[8]。
表1 不同规格防爆容器设计的部分参数
Table 1 Partial design parameters of explosion-proof containers

2 有限元分析
2.1 静态力学分析
2.1.1 模型建立 建立阀门执行器端盖三位模型如图2 所示。按照表2在前处理中输入材料属性。
表2 材料属性
Table 2 Material properties

执行器端盖接触面添加固定约束,如图3 所示;爆炸极限工况下阀门执行器端盖最大要承受2.5 MPa 的压强,因此端盖内表面加载荷2.5 Mpa,载荷设置如图4 所示,受力内表面如图5 所示;采用直接建立单元模型的网格直接生成法,最终得到有限元模型含有31790 个节点,16573 个网格单元,对网格质量进行检查,纵横比合适[9]。
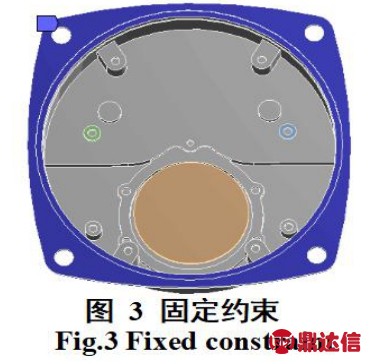
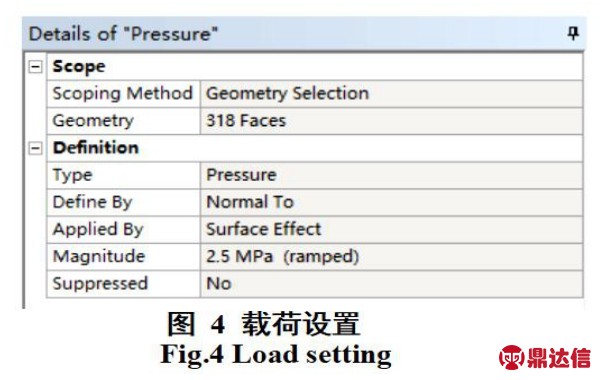
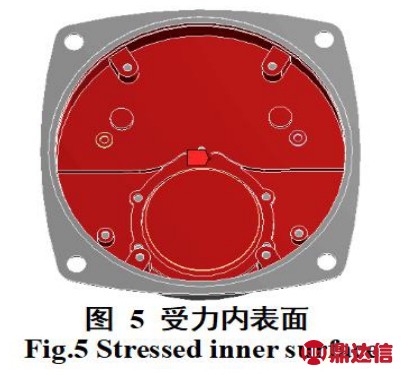
2.1.2 静态分析结果 由表3可知,端盖壁厚在2~2.5 mm 之间的应力和位移较3~4.5 mm 之间变化值大,说明端盖受到压力的影响在壁厚达到一定值后逐渐减小。当端盖厚度在2~2.5 mm 之间时,端盖的数值计算最大应力值大于材料的抗拉强度255 MPa,不满足要求,不能其作为设计厚度。选取δ=3 mm,σmas 近似于0.7 σs,在满足力学性能的前提下尽量满足了质量轻量化。
表3 不同壁厚端盖应力和位移最大值
Table 3 Maximum stress and displacement of end cover with different wall thickness

根据图6 仿真结果,阀门执行器端盖在承受内压时,有两部位有应力集中现象,其一是中心部位,另一处是边缘拐角处。端盖中心部位的应力分布区间为21.111~99.771 MPa;由于边缘拐角处有较大的向外的撕裂应力,形成了应力集中,应力分布区间为64.125~189.91 MPa。如图7 所示,端盖最大位移在中心部位为196.27µm,小于端盖和阀体的配合预留量1 mm,位移值沿着中心向边缘逐渐减小。对边缘拐角和端盖中心两处危险点进行动态力学分析,为后续设计提供更充分的理论依据。
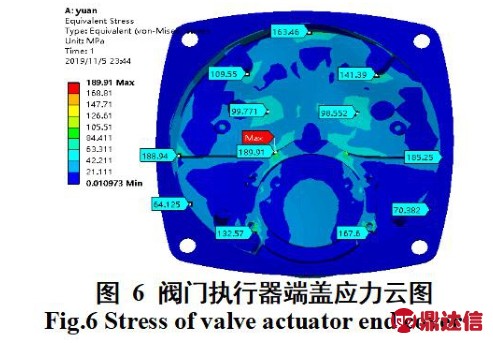
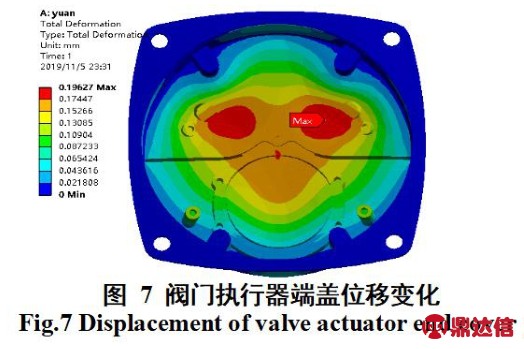
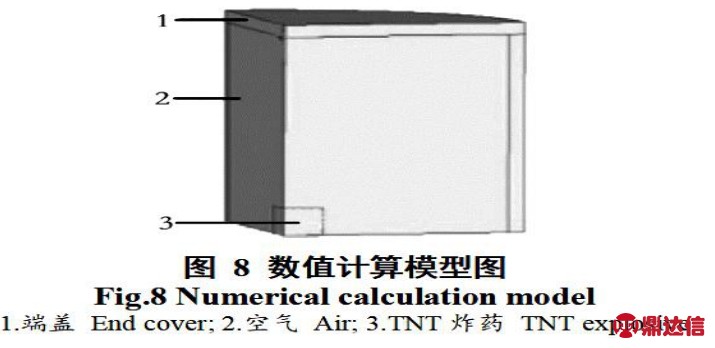
2.2 动态力分析
2.2.1 建模 利用Dyna 对容器内爆炸情况进行动态模拟,重点观边缘拐角和测端盖中心处的动态响应。端盖和炸药结构均设置为柱形,呈轴对称分布,如图8 所示。分别建立端盖、炸药和空气模型,在模型对称面施加对称约束,并进行网格划分[10]。为节约计算时间,取模型的1/4 进行计算。
2.2.2 材料模型和状态方程确定 炸药采用MAT_HIGHEXPLOSIVE_BURN 材料模型和JWL 状态方程描述炸药做功[11],其表达式为:

式中:A、B、R1、R2 和ω为输入参数;E0 为爆轰产物的比内能;V为爆速,相关参数见表4。
表4 TNT 炸药参数
Table 4 Parameters of TNT explosive

空气采用MAT_NULL 材料模型和EOS_LINEAR_POLYNOMIAL 多项式方程描述理想气体,其一般形式为:P=(γ-1)ρe0(12)
式中,γ为气体的比热;e0 为单位质量内能;ρ为气体密度,相关参数如表5 所示。
表5 空气参数
Table 5 Parameters of air

铸铝阀体和端盖采用MAT_ELSTIC 各向同性材料模型。材料性能参数如表6 所示。
表6 铸铝阀体和端盖材料参数
Table 6 Parameters of Cast Aluminum valve and end cover

2.2.3 动态分析结果 数值计算结果如图9所示,端盖中心的应力最大值发生在在1.2 ms 附近,约为240 MPa,分别在1.6 ms 和2.4 ms 时出现2 次波峰,约为220 MPa,均低于材料抗拉强度。随着时间推移,应力振动幅度逐渐下降且趋于稳定,由于容器内部静压力作用,4 ms 后应力波振荡稳定却没有迅速消失。
端盖边缘拐角处应力变化如图10 所示。这是由于炸药引爆后冲击波发生端盖中心处,随即向外传播,在遇到壁面时发生反射形成反射波,而执行器端盖内长径比接近1:1,反射波沿着轴向和纵向几乎同时传播至端盖边缘拐角处,引爆中心的冲击波也在向该处传播,三波集中,因此边缘拐角处平均应力值略高于中心处。
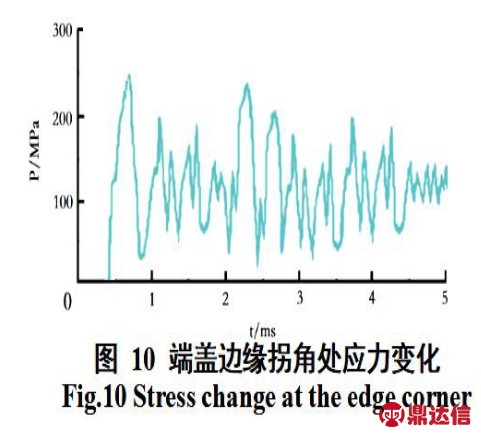
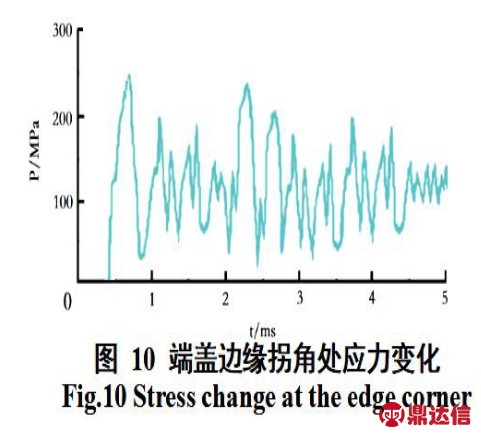
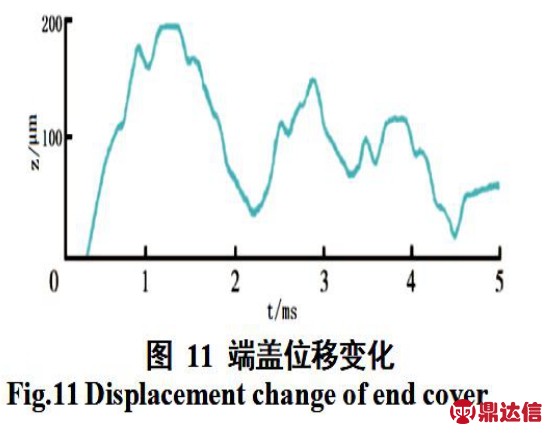
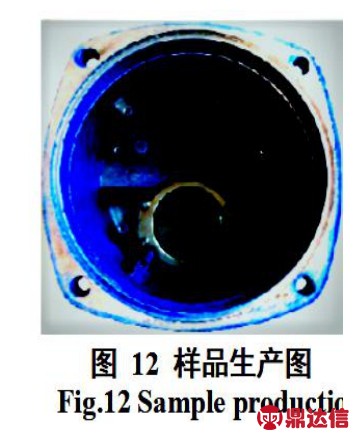
由端盖位移随时间的变化曲线,可见在模拟爆炸冲击时,端盖中心部位产生初始径向最大位移190µm 左右,与静态模拟结果一致,随后曲线呈振动态势,偏移量随时间逐渐减小,最终为60µm左右,没有回到位移零点,说明端盖产生了一定塑性变形,这在保证安全的前提下可以发生(图11)。
选择合适的端盖厚度后经过静态以及动态力学分析满足设计要求后进行了实物加工(图12)。
3 结论
1)隔爆型阀门执行器在爆炸极限工况下使用时,容器内产生的压力会使端盖产生变形,造成端盖的结构应力和变形分布不均,影响变形量的主要因素是端盖厚度。通过公式计算和经验数据缩比对端盖厚度取2 mm 下极限值和4.5 mm 上极限值的理论值区间;
2)利用有限元对理论值区间内的不同壁厚端盖进行静态受力分析,在满足力学性能的前提下尽量满足轻量化,选取3 mm 作为设计厚度;
3)为更好地验证设计的合理性,对整个端盖进行动态力学模拟表明,最大应力值小于端盖材料的抗拉强度255 MPa,端盖最大位移量小于1 mm,变化范围较小,设计具有一定的可行性。