摘 要:针对塑件注射成型自动化实施困难问题,设计了一副单点潜浇口、两板式2次开模注射模来解决这一难题。模具布局为1模2腔。模具中单腔的机构设置情况为:(1)定模侧,设计了一个油缸驱动的定模顶出机构;动模侧,设置了2个特殊的斜顶+滑块复合机构、1个万能斜顶机构、1个隧道滑块机构、及1个顶针顶出机构;(2)定模顶出机构由油缸驱动定模顶出板以驱动6根斜顶杆来对6个倒扣特征进行自动脱模;(3)2个特殊的复合机构分别为:双滑块+斜顶3次复合抽芯机构、单滑块斜顶两次抽芯机构;此2个机构的作用是,通过斜导柱驱动滑块,从而2次驱动滑块内的斜顶实施2次抽芯,来到达塑件局部区域多次多向抽芯的目的;(4)机构中,使用万能斜顶机构能有效减小模具高度尺寸;使用隧道滑块斜抽芯机构,动模一侧增加1次模板开模打开来驱动隧道滑块实施斜抽芯,能有效利用模具开模动力,降低模具制造成本。
关 键 词:斜顶滑块复合机构;隧道滑块;注射模;自动化;机构设计;模具结构
0 前言
塑件在型腔内的外壁成型时,如有一处或者多处倒扣使用定模斜顶顶出时,需要在定模一侧设置定模同步顶出机构[1-3]。塑件外壁侧壁上,侧抽芯槽内设置有垂直于槽侧抽芯方向的单个或者多个二级侧孔时,一般使用需要使用多层多次侧抽芯机构[4-7],其中较为实用的是,在滑块上设置二级斜顶侧抽芯机构-即滑块式斜顶机构。塑件内壁上的直面倒扣多使用斜顶机构来抽芯,斜顶使用时,若侧抽芯距离较长,一般使用万能斜顶机构来实施侧抽芯[8-9]。塑件内壁上有斜孔倒扣多使用T型块驱动的内藏式斜抽芯机构来实施斜抽芯脱模,机构动作的执行,需要增加一次模板的打开来进行驱动[10]。因而,针对塑件上同时存在上述4种特征的塑件,机构的设计、模具结构的设计都需要做较大程度的创新设计。本文结合某端盖塑件的结构特点,设计了一副这样的模具,模具中,使用了1个定模斜顶机构、2个滑块式斜顶创新机构、1个万能斜顶机构、1个模板驱动的T型块斜顶机构,来实现塑件的自动化注射成型。
1 端盖塑件
端盖塑件结构如图1所示,端盖为圆盘状塑件,直径φ162 mm。
塑件的正面中央部位A2区域,设置有K1~K6共6个倒扣。侧边上,在A1区域的铰接板上,设置有H1、H2这2个对向侧盲孔。在A3区域的侧板上,设置有凹槽B1,B1内设置有2个垂直筋位J1、J2,J1为直壁筋,J2为“十”筋;在B1槽的两个侧壁,分别设置有侧孔H3、H4这2个盲孔。
塑件反面的内壁上,设置有多个槽位B2。反面上,在A4区域,设置有直的矩形通孔D1,在D1的出口边上,设置有3处J3斜筋。塑件材料使用丙烯腈-丁二烯-苯乙烯共聚物(ABS),收缩率为4.8%~5.5%。
本塑件模具设计的最难点在于A1区域H1、H2孔的脱模,及A3区域H3、H4孔的脱模。
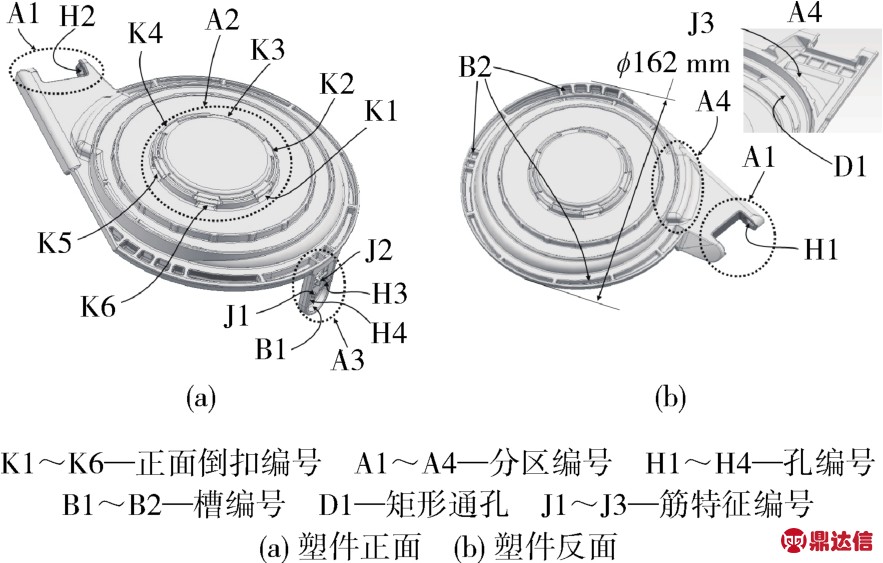
图1 塑件形状
Fig.1 Shape of plastic parts
2 模腔分型
2.1 单腔分型设置
单个塑件模腔的分型设置如图2所示,分型线使用塑件的最大外沿轮廓线,用分型线在水平面内进行延拓,而获得如图2中所示的平面水平分型面,这样有利于简化成型件的加工[11-12]。单腔模腔的打开拟按Z-方向来进行打开。
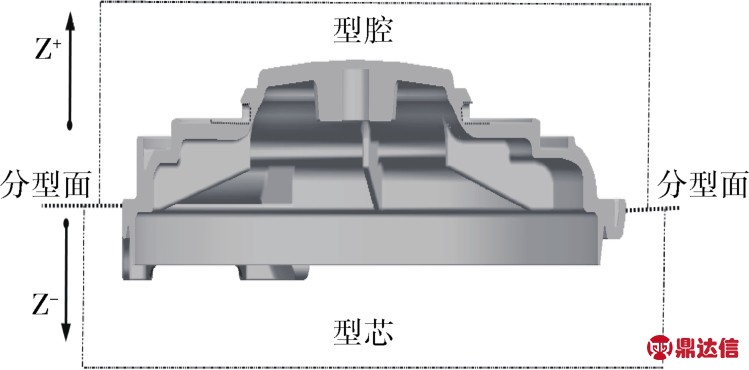
图2 单腔分型面设置
Fig.2 Parting surface setting of single chamber
2.2 单腔成型件设置
分型所得的单腔成型件构成如图3所示。单腔成型件中,型腔、型芯都使用镶件方式[13-15],型腔材料使用合金钢S136、S136为退火状态,粗加工后需进行真空淬火及回火处理,热处理硬度至HRC48~50。型腔的成型面须抛光至Ra0.8。型芯使用预硬态合金钢2738。针对塑件正面6个倒扣,设置了X1~X6共6个斜顶镶件,以及针对正面多处凹槽特征,设置了多个小镶件,以便于这些地方的成型件加工,如图3(a)所示。型芯一侧的成型件除型芯镶件外,使用了S1、S2这2个滑块机构、机构D1的斜顶杆、机构D2的斜滑块来参与成型,如图3(b)所示。
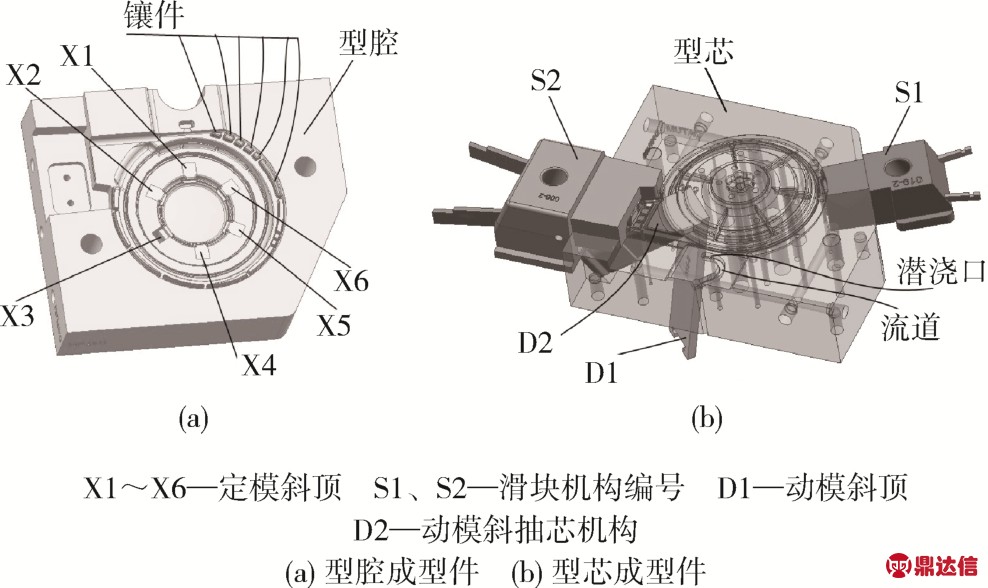
图3 成型件设计
Fig.3 Design of formed parts
2.3 浇注
单腔模腔的浇注使用潜伏式单点浇口进行浇注,浇口开设于顶针上。流道使用图3(b)中所示的“S”形流道,以提高浇口的进口温度。
2.4 冷却
模腔的冷却是模具设计中的一个重点,针对型腔镶件,鉴于其内需要开设6个斜顶的缘故,水路的布局空间变得狭小,因而设置了如图4(a)中所示的单一“Z”形水路W1,管道直径使用φ12 mm,以加大冷却效果。型芯镶件的边沿部位使用W2、W4这2条φ8 mm水路,中央部位使用5个水井构成的水路W3进行冷却。水井直径φ14 mm,如图4(b)所示。
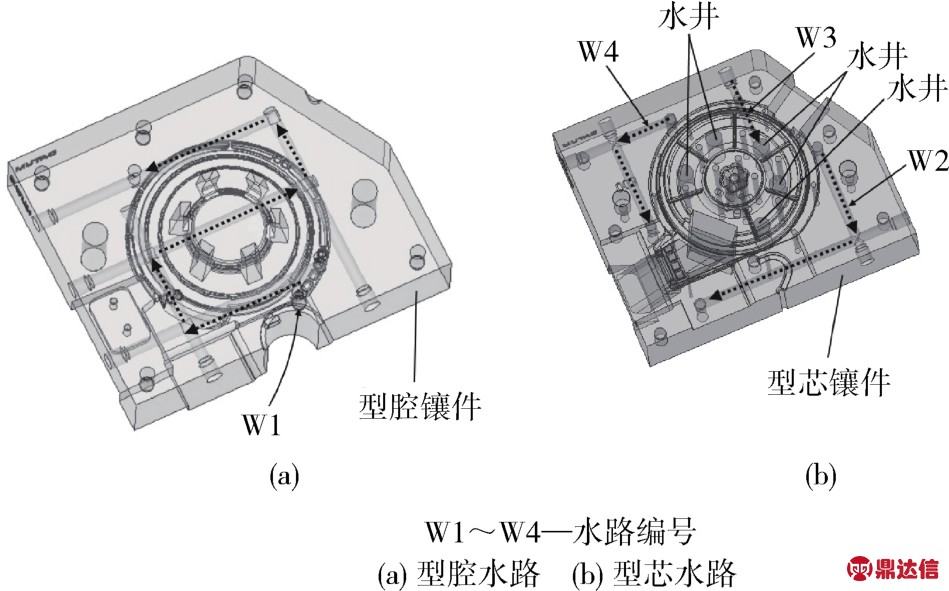
图4 成型件冷却水路
Fig.4 Cooling water path of formed parts
3 机构设计
为实现塑件的成型和自动脱模,模具单腔中,需要设置以下5个机构来解决此问题。5个机构分别为:
(1)针对塑件正面A1区域6个倒扣K1~K6自动脱模而设置的定模斜顶顶出机构。(2)针对塑件侧面A1区域特征脱模而设置的滑块机构S2。(3)针对塑件侧面A3区域特征脱模而设置的滑块机构S1。(4)针对塑件反面A4区域矩形通孔D1而设置的动模斜顶机构D1。(5)针对塑件反面A4区域3处J3斜筋而设置的动模斜抽芯机构D2。机构设计的难点在于机构S1、机构S2的设计。5个机构的具体设计分别如下。
3.1 定模斜顶顶出机构
如图5所示,定模斜顶顶出机构主要针对K1~K6倒扣特征,X1~X6这6个斜顶杆的顶出而设置,X1~X6这6个斜顶杆通过各自的斜顶销6安装在斜顶盖板2的槽内,并由定模斜顶推板1压住。油缸3用于驱动定模斜顶推板1和斜顶盖板2沿导柱4运动,从而来推动X1~X6这6个斜顶杆向下将塑件从型腔镶件9中顶出。斜顶销6主要限制6个斜顶杆在开模方向上的移动,而垂直于开模方向的平面内,斜顶销6可以移动。
3.2 机构S1的设计
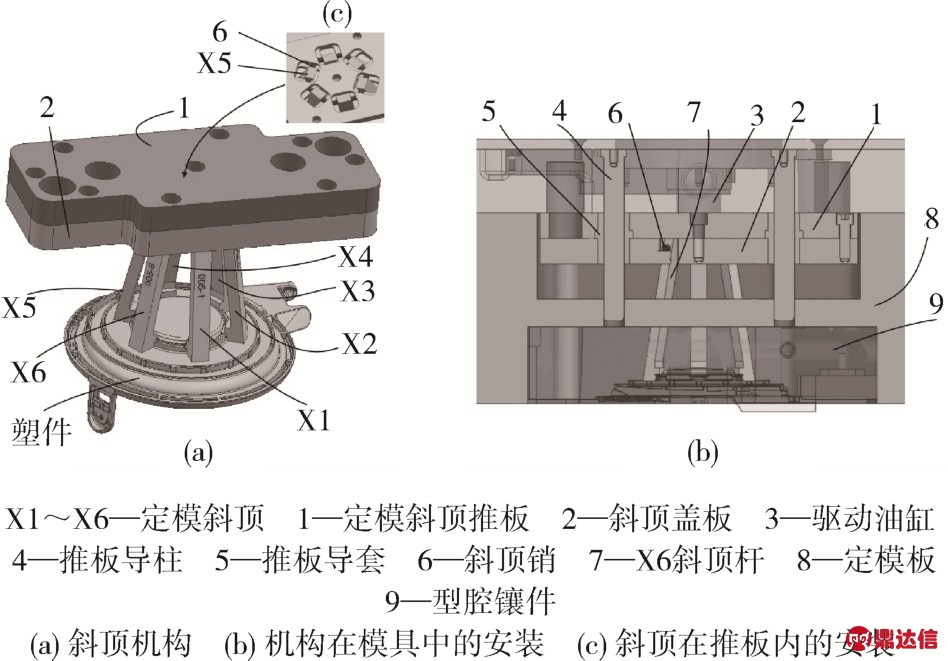
图5 定模斜顶机构
Fig.5 Fixed mould lifter mechanism
针对塑件A3区域C2槽及其内结构特征的特点,使用如图6所示的双滑块+斜顶3次复合抽芯机构来实施成型与自动抽芯脱模。机构S1按以下方案来设计:在型芯镶件上,以P1侧分型面分割出S1滑块11的成型头部,并设计S1滑块11,S1滑块11由S1斜导柱10驱动,S1滑块11通过其两侧边的S1压条12安装在S1副滑块15内,能跟随S1副滑块15一起移动,S1副滑块15再通过其两侧的S1副压条16安装在模具动模板上。S1副滑块15的滑出行程由S1螺钉18限制,S1滑块11在S1副滑块15上的滑出行程由S1副滑块15尾部的凸台限制。S1滑块11内部开设有2个斜顶杆孔以用于安装H3孔斜顶杆13和H4孔斜顶杆14。H3孔斜顶杆13和H4孔斜顶杆14的尾端都设有导槽,通过该导槽,对应的,安装于S1副滑块15尾端的H3导轨块20和H4导轨块19,通过其底面的导轨对H3孔斜顶杆13和H4孔斜顶杆14进行导向。S1滑块11的成型面用于C2槽、J1、J2筋位的成型与抽芯脱模,H3孔斜顶杆13和H4孔斜顶杆14则分别用于H3孔和H4孔的成型与侧抽芯脱模。

图6 机构S1的结构组成
Fig.6 Structure of mechanism S1
机构S1的动作原理为:当S1斜导柱10驱动S1滑块11按F1向向外抽芯移动t1距离后,S1滑块11被S1副滑块15尾端的凸台挡住,在此过程中,由于H3孔斜顶杆13和H4孔斜顶杆14的尾端在F1方向上,被H3导轨块20和H4导轨块19挡住,故而,两者只能沿H3导轨块20和H4导轨块19上的导轨,被迫分别做N1向、N2向所示的相向内收抽芯运动,从而实现H3孔斜顶杆13和H4孔斜顶杆14的头部从H3孔、H4孔内的抽芯抽出,此动作,刚好在S1滑块11被S1副滑块15挡住时完成。S1斜导柱10继续驱动S1滑块11向外移动时,将推动S1滑块11、S1副滑块15、H3孔斜顶杆13和H4孔斜顶杆14同步向外抽出,为塑件A3区域在开模方向上的出模让出空间,直到S1副滑块15被螺钉18挡住。复位时,S1滑块11先按F1向的反向移动推动H3孔斜顶杆13和H4孔斜顶杆14向N1、N2向的反向外侧移动,通过移动t1距离后,S1滑块11通过此两根斜顶杆拉动S1副滑块15复位。最后,闭模时,由S1锁紧块对2个滑块的尾端进行锁紧。
3.3 机构S2的设计
机构S2主要针对A1区域的H1、H2这2个孔而设置,机构S2同机构S1类似,不同的是该机构为单滑块斜顶2次抽芯机构。机构S2的结构如图7所示。机构中,H1插条28、H2插条31安装于模具定模板上,与S2斜导柱21保持同步运动;H1挡板27、H2挡板30安装于模具动模板上,两者有2个作用,其一是对S2滑块22的F2向抽芯滑出进行限位,其二是,两者上端开设的导向槽用于H1孔斜顶杆26、H2孔斜顶杆29的内收抽芯导向。S2滑块通过两侧的S2压条25安装于动模板上,其内部设置有H1孔斜顶杆26、H2孔斜顶杆29用于塑件H1孔、H2孔特征的成型与抽芯脱模。S2滑块内同时还装有一个驱动销24,用于H1孔斜顶杆26、H2孔斜顶杆29分别按N3向、N4向内收抽芯完毕后,被S2滑块带动一起向F2移出,以让出塑件A1区域的出模空间。
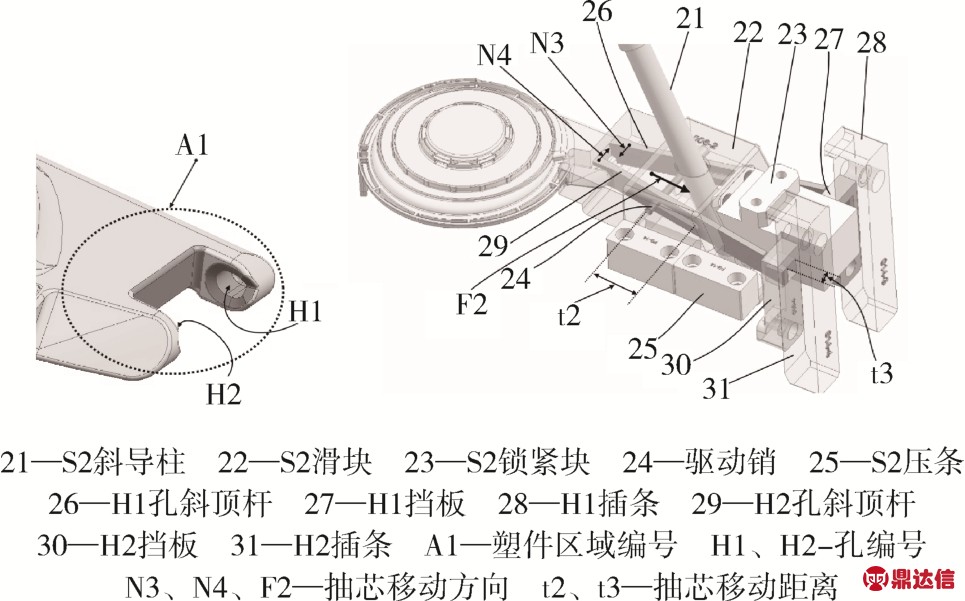
图7 机构S2结构组成
Fig.7 Structure of mechanism S2
机构S2的动作原理为:当模具动模下行时,S2斜导柱21驱动S2滑块22按F2向抽芯抽出,此时,由于H1插条28、H2插条31的阻挡,H1孔斜顶杆26、H2孔斜顶杆29被迫只能分别按N3向、N4向左内收抽芯移动,内收距离为t3,其尾端由H1挡板27、H2挡板30导向。当H1孔斜顶杆26、H2孔斜顶杆29抽芯完毕,此时,H1插条28、H2插条31失去对H1孔斜顶杆26、H2孔斜顶杆29的限制,S2滑块22滑出t2距离后,S2滑块22通过驱动销24带动H1孔斜顶杆26、H2孔斜顶杆29继续向外滑出,为塑件A1区域的出模让出空间。闭合时,过程相反,闭合后,由S2锁紧块对S2滑块22进行锁紧。
3.4 动模斜顶机构D1和动模斜抽芯机构D2
如图8所示,针对塑件反面A4区域的矩形通孔D1,及其末端边的3处J3斜筋,使用动模斜顶机构D1来对D1孔实施侧抽芯脱模,机构使用万能斜顶方式,即将D1斜顶杆32缩短,由安装于模具推板上延长顶杆33来推动,两者之间使用T型导轨方式联结,即将延长顶杆33的顶端设置成T型导轨形式,这样做的好处是能有效缩短斜顶杆32的长度,减小模架模脚的使用高度,节省模架成本。顶出时,延长顶杆33推动斜顶杆32边沿其上端导轨移动,边按F4向斜向顶出。
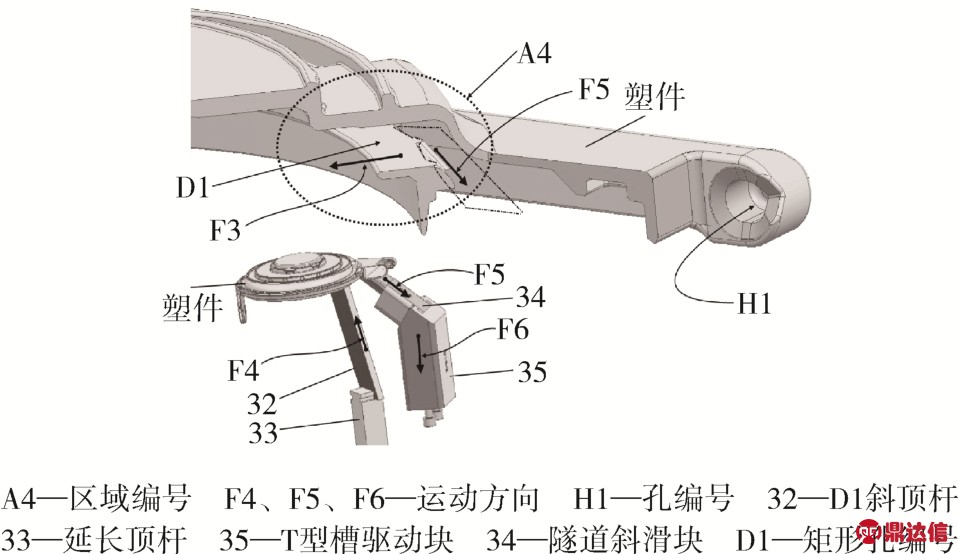
图8 机构D1、D2结构组成
Fig.8 Structure of mechanism D1 and D2
针对3处J3斜筋,使用动模斜抽芯机构D2来实施斜抽芯,机构中,T型槽驱动块35安装于模具动模垫板上,而隧道斜滑块34则安装于动模板内相应的隧道槽内,当动模板、动模垫板分离时,驱动块35按F6向移动,将通过T型槽驱动隧道斜滑块34按F5向实施抽芯。
4 模具
4.1 结构布局
模具的结构布置如图9所示,模具为1模2腔布局,结构形式为两板冷流道结构形式,分2次分型打开,1次定模顶出和1次动模顶出。模具2次打开顺序由4个扣机39进行控制。
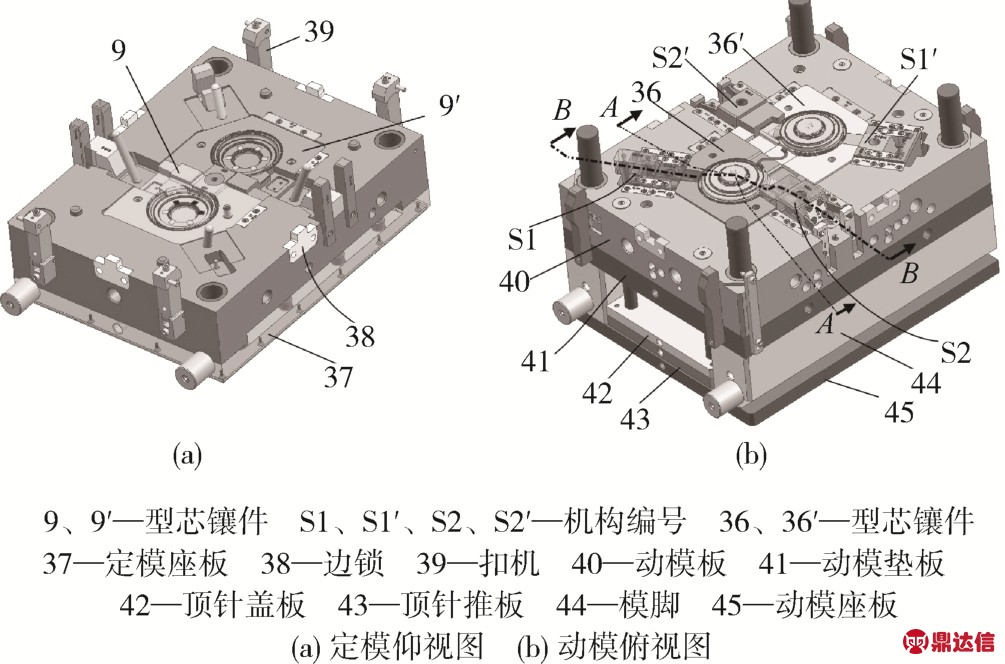
图9 模具结构
Fig.9 Structure of the mould
4.2 工作原理
模具装配于注塑机上后,工作时,随着注塑机动模板的驱动运动,及模板开闭顺序控制机构扣机39、动模板定距拉杆46的协同控制下,模具按以下动作顺序来实施其自动注塑功能,如图10所示。
(1)模具闭合完成注塑后,准备开模。
(2)K1面打开,注塑机动模板拉动K3面以下的动模按Z-方向下行,模具开始打开,由于扣机39的定序控制,模具首先在K1面处打开,打开距离为t4后,动模板40被拉住,此时,扣机39解除动模板40与定模板38之间的锁闭,K3面准备打开。此过程中,T型槽驱动块35拉动隧道斜滑块34完成斜孔抽芯动作。K1面打开距离t4。
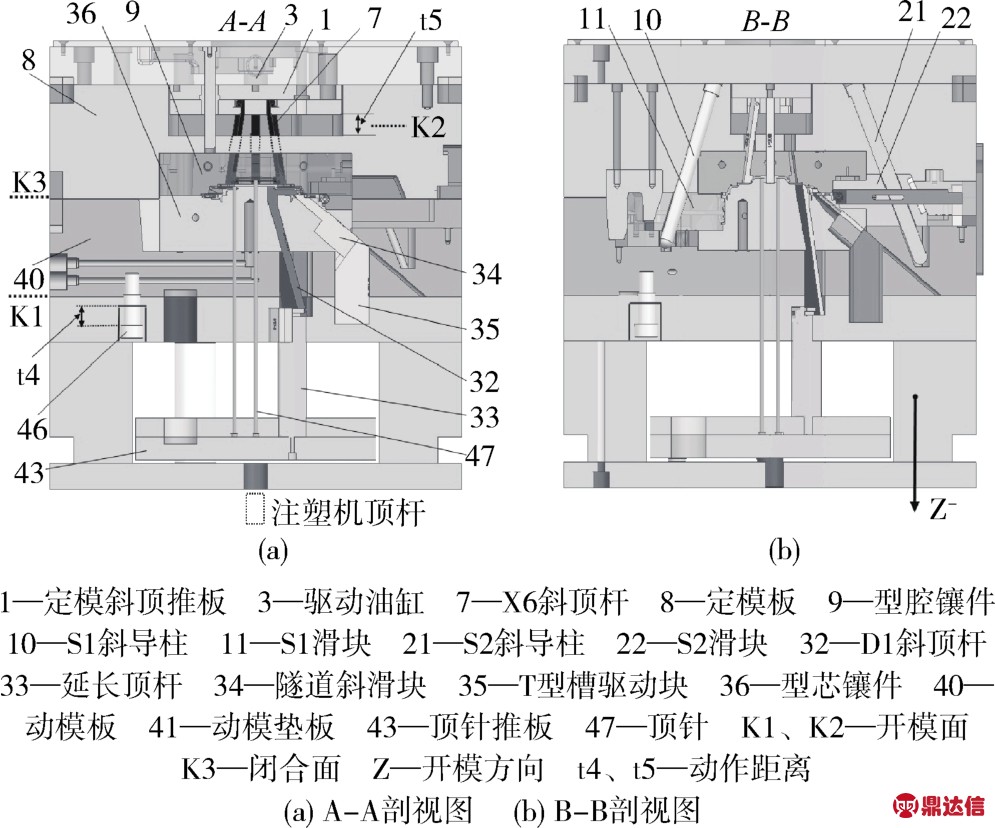
图10 模具工作原理
Fig.10 Working principle of the mould
(3)K3面打开,(K2)面闭合,动模继续下行,模具在K3面处打开,打开时,S1斜导柱10驱动S1滑块11、S2斜导柱21驱动S2滑块22同步完成机构S1、机构S2的抽芯功能。同步地,定模推出机构的油缸3驱动定模的6根斜顶杆同步顶出,将塑件从型腔镶件9中推出(K2面闭合,闭合距离为t5),而留于型芯镶件36上。
(4)顶出,模具打开完毕,注塑机顶杆顶住推板43,使其保持不动,动模继续下行,塑件将被顶针47、D1斜顶杆从型芯镶件36上顶出,而实现完全脱模。
(5)模具复位,模具的复位过程与开模过程完全相反。
5 结论
(1)设计了一副两板单点潜伏式浇口注射模具用于端盖塑件的注射成型;
(2)模具中,为解决塑件生产自动化生产问题,在机构设计和模具结构布置方面做了以下6个设计措施来进行保证:①塑件正面的6个倒扣特征,使用油缸驱动的定模顶出机构驱动6根斜顶杆来实施成型和侧抽芯脱模;②侧面的侧板特征,使用了一种双滑块+斜顶3次复合抽芯机构实施成型和3次侧抽芯脱模;③侧面铰接板上侧孔特征,使用了一种单滑块斜顶2次抽芯机构来实施成型和2次侧抽芯脱模;④塑件反面的矩形通孔,使用了一种万能斜顶机构来实施成型和侧抽芯脱模;⑤针对3处斜筋特征,使用了一种隧道滑块斜抽芯机构来实施成型和斜抽芯脱模;⑥对两板模架进行了三板式改造,在动模一侧增加1次模板开模打开来驱动,以满足隧道滑块斜抽芯机构的驱动需要。