摘 要:针对动车组头罩端盖强度既应该满足日常运行要求,又要保证在碰撞事故发生时不妨碍相邻两车端部车钩有效连挂,即要求端盖用GFRP材料在一定撞击条件下可以发生穿透损伤。利用大质量低速冲击试验,探究纤维含量、纤维长短、铺层方向对复合材料层合板的抗冲击性能影响,基于被动安全防护角度提出动车组头罩端盖结构破损性能评价方法。研究结果表明:编织纤维层合板受冲击作用产生的破损形貌可以满足头罩端盖要求。利用编织纤维材料试制动车组端盖样件并进行大质量冲击试验,发现其在冲击过程中呈现大小可容车钩穿过的破损形貌,碎屑尺寸细小不影响车钩连挂。
关键词:玻璃纤维复合材料;层合板;车辆端盖;冲击试验
目前,我国铁路投入运营的动车组已有 2 470组,动车组运能大、速度高,一旦发生碰撞事故后果不堪设想。国内外针对列车事故开展车辆碰撞研究[1−3],提出车辆结构“耐撞性”设计需求以满足在列车碰撞事故发生后将损失降到最小[4−6]。欧洲标准EN15227:2008+A1[7]认为要求车体结构在任何碰撞情况下都保证乘客安全不现实,车辆设计应采取措施降低爬车风险,并且以可控方式吸收冲击能量保证救生空间及乘客区域结构完整性,同时降低碰撞过程减速度来实现被动安全防护。英国、法国、德国和美国等国家均采用多级能量吸收系统来满足车体被动安全防护要求,只是具体结构不同[8−13]。铁道车辆多级能量吸收系统包括车钩缓冲器,压溃管及车端碰撞吸能结构[2],在碰撞发生时,列车头部车钩自动连挂是保证车钩缓冲器作为一级吸能系统发挥作用的必要先决条件。为保证动车组高速运行时具有良好的气动性能,动车组头部一般采用流线型端盖将传统列车上车钩等外露设备包裹起来。端盖一般设计为可开闭式,在调车作业,救援抢险及重联作业时端盖开启露出车钩钩头,在高速运行时通过开闭机构闭合自锁保证车体头罩外形平整美观[14]。碰撞事故发生瞬间通过主动控制打开端盖露出车钩是不现实的,因此探究动车组头罩端盖的耐撞性有助于改善动车组被动安全性能。由于复合材料轻质高强,可设计性及整体成型性好,将其应用在高速动车组上可以满足列车轻量化高速化的发展要求[15−16]。日本新干线高速列车、法国TGV高速列车和意大利ETR500型高速列车均大量采用复合材料(FPR)[17−18]。中国“韶”系列、“蓝箭”、“中华之星”及上海明珠二号线地铁列车头罩均应用了复合材料。玻璃纤维复合材料(GFRP)因其易腐蚀、耐磨损、易成型的特点通常被用来制造高速列车头罩端盖,克服了传统金属头罩高成本、低精度、易磨损、难维修的缺点[19−20]。国内外针对动车组头罩端盖耐撞性开展的研究较少,多数研究集中在复合材料层合板抗冲击性能。Schoeppner等[21]通过试件冲击实验发现载荷绝对值的突然下落与脱层的发展相对应, 证明了脱层阈值载荷的存在。Matemilola等[22]通过复合材料压力容器受球头落锤冲击实验发现第一个载荷绝对值的下落的基本原因是脱层,不同材料和结构的形式存在对应的阈值载荷。Hirai等[23]等针对编织的玻璃纤维层板展开实验,发现初始损伤载荷导致界面失效或者层板后表面附近基体裂纹。徐宝龙等[24]通过层板横向冲击试验发现脱层失稳载荷与试件铺层结构有关,发生脱层的界面具有相同的细观剪切强度。依据EN12663-2000[25]中对铁道车辆结构的冲击试验要求,展开玻璃纤维层合板低速冲击试验,比选出最优类型。通过动车组头罩端盖样件试制及冲击试验,验证材料选型可行性,为动车组端盖制作提供工程参考。
1 GFRP层合板低速冲击试验
1.1 GFRP层合板铺层
通常情况下纤维增强复合材料结构形式一般为层合板(Laminate)的构型[26],每个单层由纤维和基体材料构成,最终按照需要将一定数量的单层堆积固化形成层合板。通过改变单层纤维含量,纤维铺层方向及各层间的相对角度可以改善层合板的力学性能。在复合材料层合板铺层设计中,优先采用对称层合板,这样可以消除层合板面内与面外之间的耦合,并获得较大的面内刚度和面外扭转刚度,而且易于成型。本文针对玻璃纤维提出3种不同构造形式的层合板:单向纤维层合板、正交编织纤维层合板和短纤维层合板,层合板厚度均为 8 mm,层数为 8层。单向纤维层合板每单层纤维主方向一致,单层间纤维主方向成 90°夹角,铺层方式为:(0°/90°/0°/90°);编织纤维层合板每一层的纤维都是 0°/90°正交编织,横向和纵向纤维量相当;短纤维层合板每层纤维在工艺成形过程中随机散列,单层间纤维主方向不同。
1.2 低速冲击试验
低速冲击试验在中南大学轨道交通安全实验室车辆部件碰撞试验台上进行,碰撞试验台由刚性墙、试验线路、试验台车、驱动系统(牵引回拉装置)、制动系统、电气控制系统和数据采集系统构成。根据欧盟的铁道车辆车体结构要求标准 EN12663—2000中的冲击试验要求[4],结合碰撞事故场景统计数据,低速冲击试验设计速度为9.0 km/h,试验台车前端焊装长500 mm的钢管带车钩钩头结构模拟实际车钩形态。考虑到层合板非承载结构,台车调整配重至2.3 t,在工装固定端焊接吸能圆管保证实验安全性。表1所示为层合板试件及冲击试验参数。
表1 层合板冲击试验参数
Table 1 Impact test parameters of composite laminates
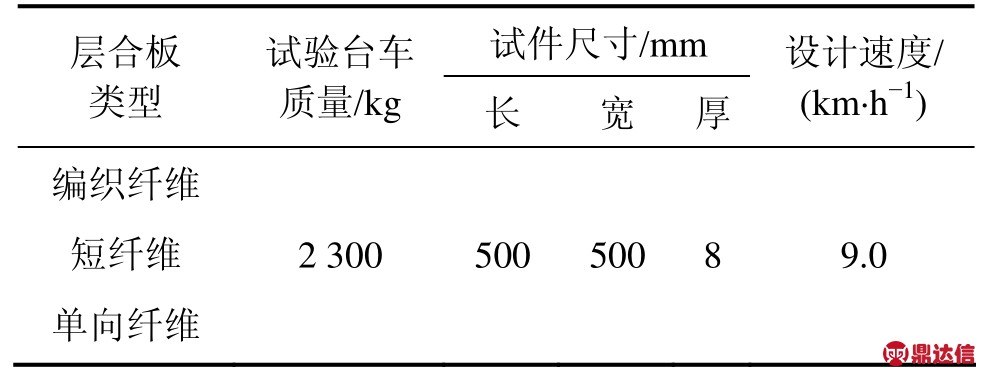
冲击试验的数据采集部分由测力系统采集整个撞击过程中撞击力−时间曲线,高速摄影系统采集撞击过程图像序列。测力系统由美国 Endevco 9393A压电式测力传感器及电荷放大器和数据采集器等主要设备组成,高速摄影系统由 2台正交的高速摄影机(MEMRECAM HXlink-3)组成,试验过程中以5 000帧/秒的速度捕捉碰撞过程序列图。
2 破损性能评定方法
当冲击物开始接触玻璃纤维层合板前表面时,就会产生层合板厚度方向上的压缩应力波,压缩应力波会沿着层合板的厚度方向传播到层合板的背面,应力波在层合板背面反射后又形成拉伸应力波。这时,如果冲击能量足够大,拉伸应力波产生的层间剪切应力就会超过层合板结构的层间剪切强度而产生分层破坏,与此同时,层合板变形形成的弯曲应力波致使层间应力的增大,形成明显的分层损伤;如果冲击能量大到使层合板内纤维发生大规模断裂失效,在冲击接触区域会形成明显的损伤破坏区域,这时层合板材料结构就会发生撕裂或穿透性破坏;当层合板结构在板平面内各向性能差异明显时容易产生撕裂破坏,当各向性能接近时则容易产生穿透性破坏,并在冲击后层合板结构上留下明显的穿透破坏孔。在轨道车辆领域,暂时还没有关于复合材料动车组端盖被动安全评价标准。基于实际运行中被动安全防护要求,动车组端盖头罩在碰撞发生时需呈现良好的破损形貌,不能影响列车车钩连挂。本文针对上述要求提出复合材料层合板及动车组端盖的复合材料结构破损性能评定方法:
1) 破损模式主要通过碰撞过程中材料的动态破坏状态和材料最终的破坏形态来评定。主要从以下几种模式来分析:穿透性破坏、撕裂性破坏、基体剪切、纤维断裂、分层破坏以及上述各种破坏模式的耦合破坏等;同时要分析碰撞过程中材料在厚度方向上的弯曲变形幅度,因为过大的弯曲变形容易造成破坏的碎片大量进入车钩的钩体凹锥孔内,影响车钩连挂。
2) 破损形貌通过材料碰撞破坏后呈现的最终形态来评定,评定内容有:是否有穿透孔,穿透孔形状、大小,散落的碎片大小,层合板破坏处纤维形态。层合板和动车组端盖结构在碰撞后出现较大的穿透孔、散落细小的碎片、破坏处纤维断裂彻底并无杂乱的纤维束缠绕等破损形貌是比较理想的材料结构。
3) 材料破坏的难易程度主要通过等能量撞击下材料破坏过程中撞击力动态响应情况来评定,同等能量撞击下撞击力峰值越大材料越难发生破坏,撞击响应时间越长说明材料越难发生破坏且材料弯曲变形越大。
3 层合板破损性能评价
层合板冲击试验中以相同冲击能量分别撞击 3种不同构造形式的玻璃纤维层合板,试验参数记录于表2中。
3.1 破损模式分析
通过分析冲击试验动态响应过程(如图1),发现编织纤维层合板主要以变形为主并向内凹陷,内部结构逐渐失效破坏,结构强度刚度退化,T=20 ms时模拟车钩钩头已完全侵入层合板,层合板被冲击区域材料结构完全失效,发生穿透破坏;短纤维层合板主要以变形为主,伴有表面可见的组织脆裂,内部结构也逐渐发生失效破坏,结构强度刚度退化,T=20 ms时大部分侵入层合板,层合板被冲击区域材料结构完全失效,发生穿透破坏;单向纤维层合板主要以变形为主并向内凹陷,内部结构也逐渐发生失效破坏,结构强度刚度退化,T=20 ms时模拟车钩钩头部分侵入层合板,层合板被冲击区域沿一侧撕裂,同时层合板上侧边角发生层裂现象;层合板被穿透后,上下侧都发生明显的层裂,冲击接触区域板材呈现中心发散状散裂现象。对比3种层合板材料的破坏模式,表明编织纤维层合板和短纤维层合板能满足动车组端盖材料的被动安全要求。
表2 试验参数
Table 2 Test parameters
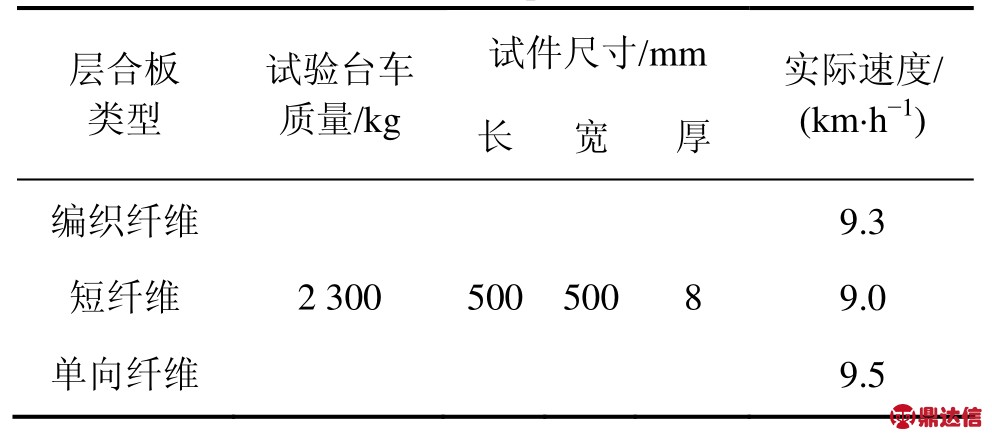
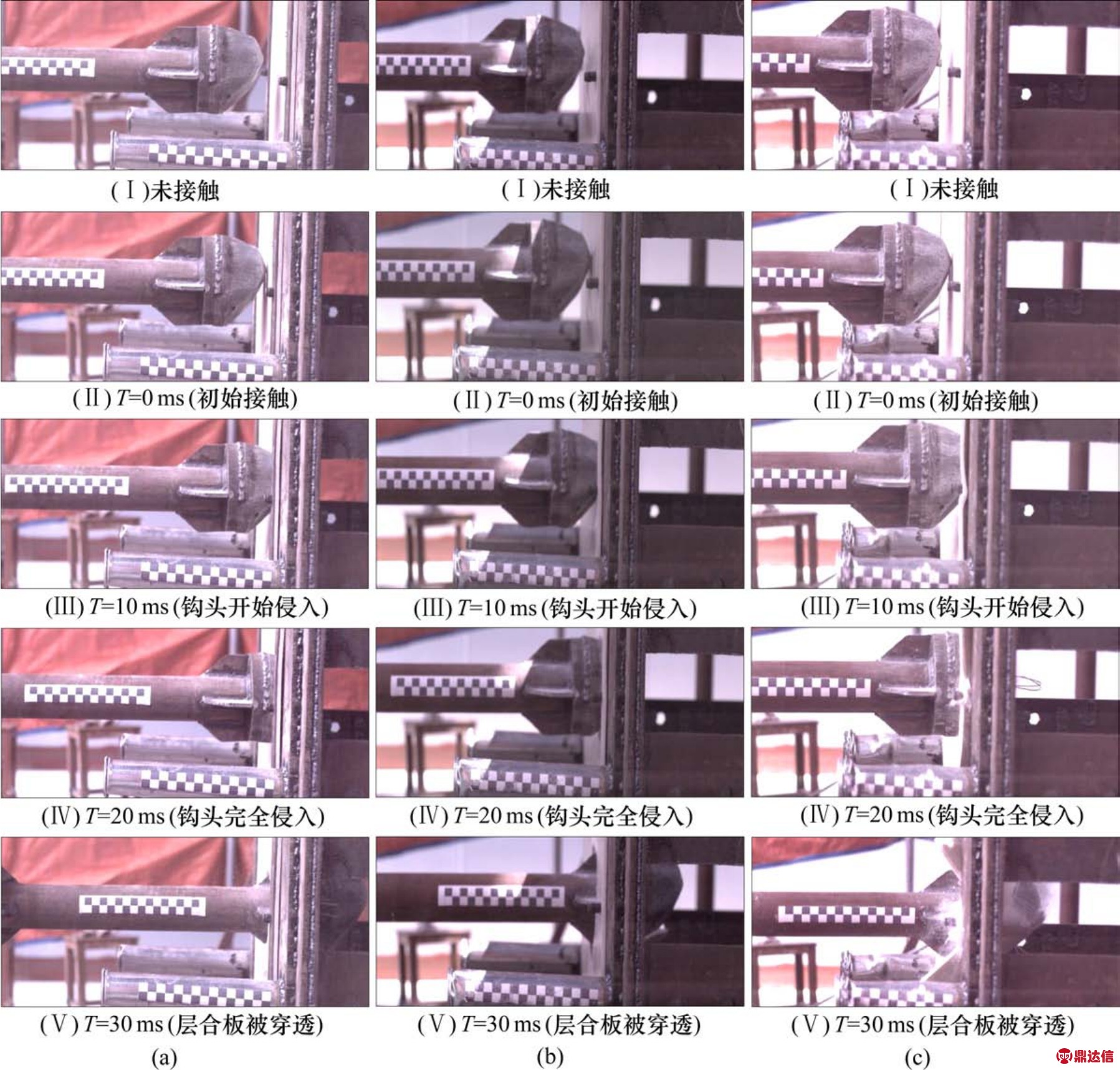
图1 不同类型纤维层合板受冲击动态响应过程
Fig. 1 Collision responses of different composite laminates
(a) 编织纤维层合板;(b) 短纤维层合板;(c) 单向纤维层合板
3.2 破损形貌分析
冲击试验后3种不同玻璃纤维构造形式层合板的破损形貌如图2所示。编织纤维层合板受冲击后呈现出210 mm左右的圆形穿透孔,孔径稍大于台车模拟车钩钩头直径,穿透孔周边纤维断裂比较规整,穿透破坏孔面积仍大于冲头端部横截面积,破坏区域的材料结构受冲击形成细小碎屑;短纤维层合板受冲击后基体剪切现象明显,呈现出类正方形破孔,破孔边长为200 mm,左右方向对角线长为250 mm,穿透部分散裂为5片较大尺寸碎片,最大碎屑面积约为穿透破坏孔面积的 1/2。单向纤维层合板被模拟车钩撞穿撕裂,冲击过程中未产生破孔,仅从碰撞点向右侧扩展为严重的撕裂现象,同时向四周散裂开来,层合板表面出现层裂剥皮现象,部分纤维被扯出,形成大尺寸纤维断头,有交织缠绕现象,无法规整剥离。
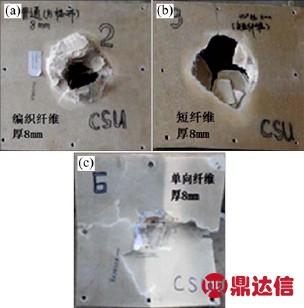
图2 层合板的破损形貌
Fig. 2 Morphology of composite laminates
(a) 编织纤维;(b) 短纤维;(c) 单向纤维
对比3者破损形貌发现,单向纤维的撕裂破坏及纤维断头会影响车钩连挂;短纤维层合板受冲击产生碎屑尺寸较大,如果飞溅到车钩钩体凹锥孔内对车钩连挂影响较大;编织纤维产生的碎屑尺寸很小,即使进入到车钩钩体锥孔内对车钩连挂影响相对较小,编织纤维受冲击形成的穿透孔的大小和规则程度较短纤维层合板更好,此外,从结构轻量化设计角度来考虑,同等厚度的层合板编织纤维的强度比短纤维的更大,满足相同运行强度时,采用编织纤维层合板更符合结构轻量化设计趋势。
3.3 破损难易程度分析
冲击试验采用空气炮作为驱动装置,试验设计速度为9.0 km/h,实际速度最大偏差6%,在允许范围内。试验结果及相关量计算值记录在表3中。
表3 不同类型纤维层合板冲击试验结果
Table 3 Impact test results of different composite laminates
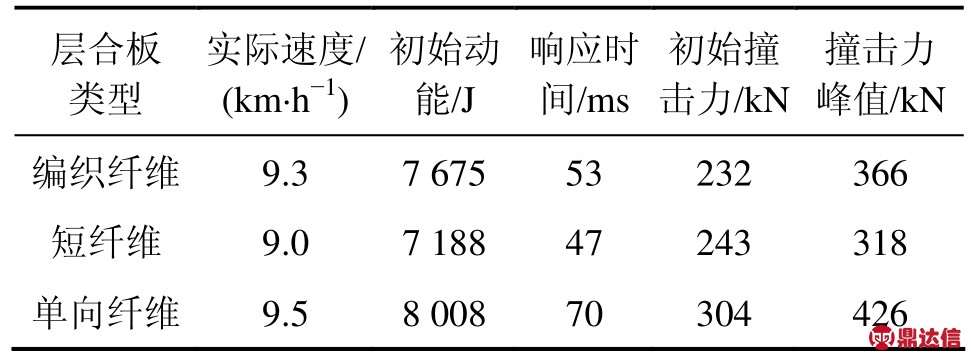
单向纤维层合板初始破坏撞击力为304 kN,明显大于编织纤维(232 kN)和短纤维层合板(243 kN),编织纤维和短纤维层合板的初始破坏撞击力值大小相当;层合板受冲击响应过程中,单向纤维层合板峰值撞击力为 426 kN,编织纤维层合板次之为366 kN,短纤维层合板最小为318 kN,因此短纤维最容易被撞穿,编织纤维次之,单向纤维强度刚度最大。
对比 3种层合板受冲击作用下撞击力-时间响应曲线(图 3(a)所示),发现编织纤维层合板响应时间稍大于短纤维层合板均在50 ms左右,单向纤维层合板撞击力响应时间为70 ms。整个冲击过程,模拟车钩最先接触层合板形成第1个波动区域,撞击力迅速上升至第一个峰值,此时层合板接触区域发生部分穿透;随后穿透孔继续扩大,模拟车钩穿过层合板与工装内置蜂窝夹芯三明治吸能结构接触形成第2个波动区域;最后在第3个波动区域,台车前端与工装预置吸能圆管接触,撞击力逐渐下降为0 kN,撞击过程基本完成。
通过第Ⅰ个波动区域的撞击力−时间曲线(图3(b)所示),发现3种层合板材料弹性变形时间区间基本相等;从材料屈服到材料穿透或撕裂破坏时间区间长度来看,编织纤维和短纤维层合板基本相等,单向纤维层合板最长。
对比3种层合板各项性能评价结果(表4所示),发现单向纤维层合板在破坏模式、破损形貌以及破坏难易程度等方面的性能均较差,编织纤维及短纤维在破坏模式和响应时间方面两者性能基本相当,但短纤维层合板的破损时碎屑尺寸较大,进入车钩钩体凹锥孔内会严重影响车钩连挂。编织纤维层合板的各方面性能均为优良或一般,满足要求。
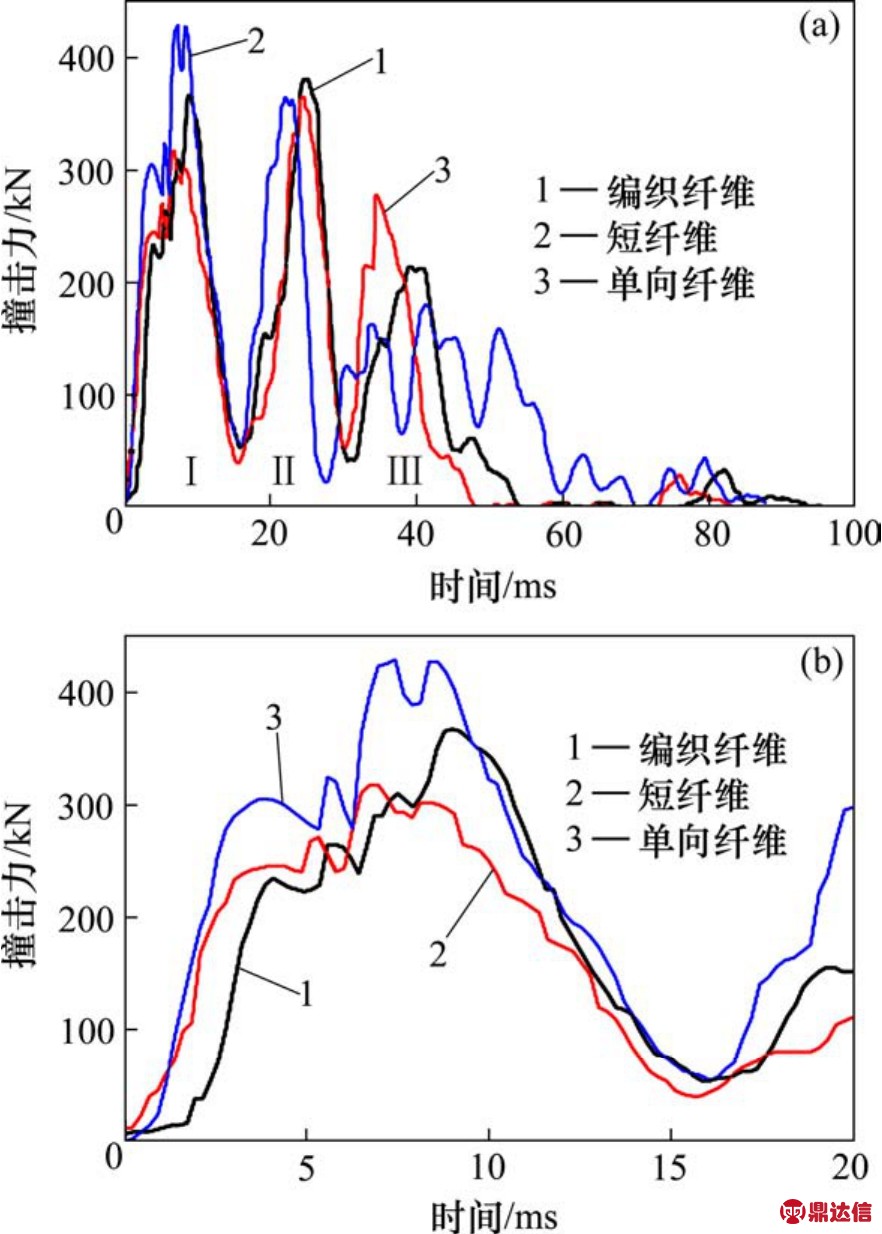
图3 3种层合板撞击力-时间响应曲线
Fig. 3 Force-time response of different composite laminates
(a) 整体响应曲线;(b) 第Ⅰ个波动区域的响应曲线
表4 层合板各项性能评价结果
Table 4 Various property targets comparison of different composite laminates
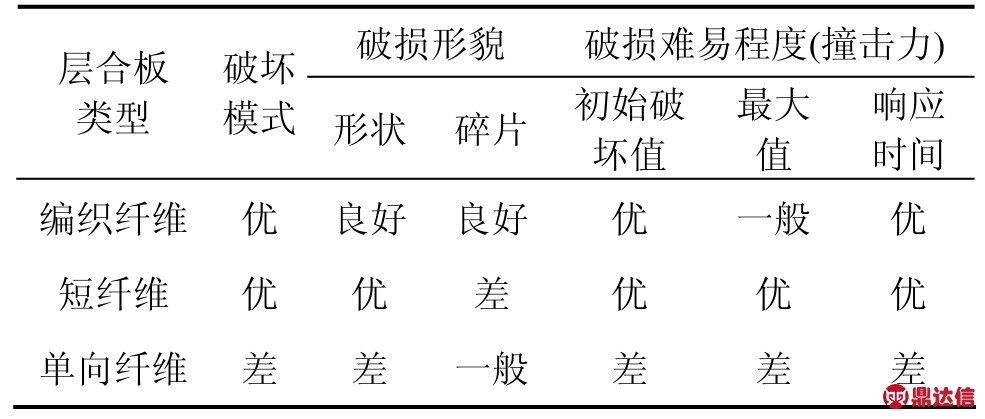
4 动车组端盖样件试验验证
动车组端盖样件验证试验装置如图4(a)所示,试验台车质量25 t,台车前端焊接动车组端盖样件,端盖将车钩封闭在内模拟碰撞事故情景(图 4(b))。刚性墙处加装特制工装(图 5(c)所示)模拟对撞端车钩形态,数据采集系统与层合板低速冲击试验相同。
冲击试验实际速度为7.2 km/h,冲击动能为50 kJ。通过撞击力−时间响应曲线(图5)发现,初始撞击力为396 kN,最大撞击力峰值为860 kN,整体响应时间约为150 ms。
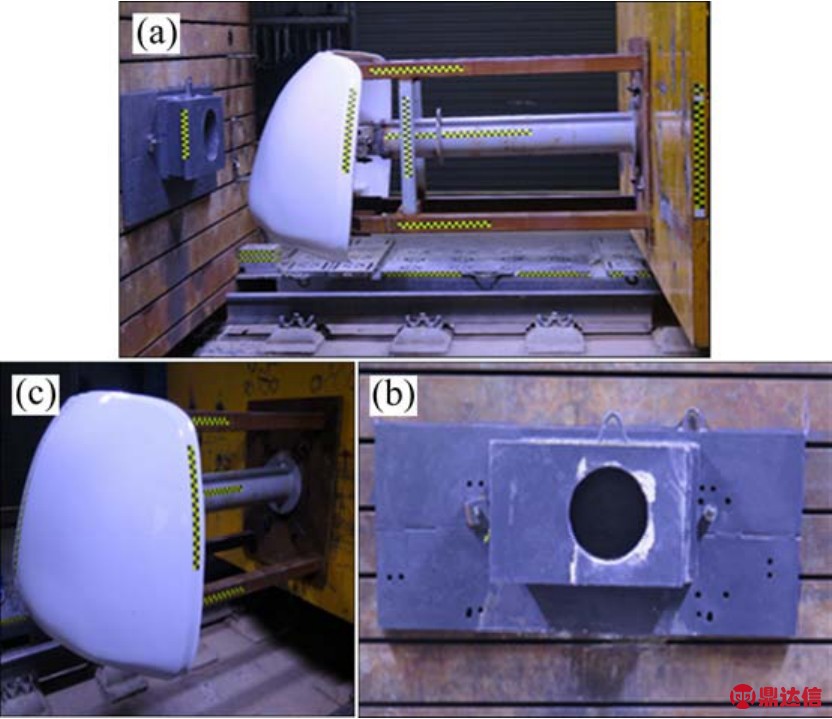
图4 试验装置
Fig. 4 Test device
(a) 端盖样件试验整体;(b) 试制端盖样件;(c) 模拟撞击端车钩工装
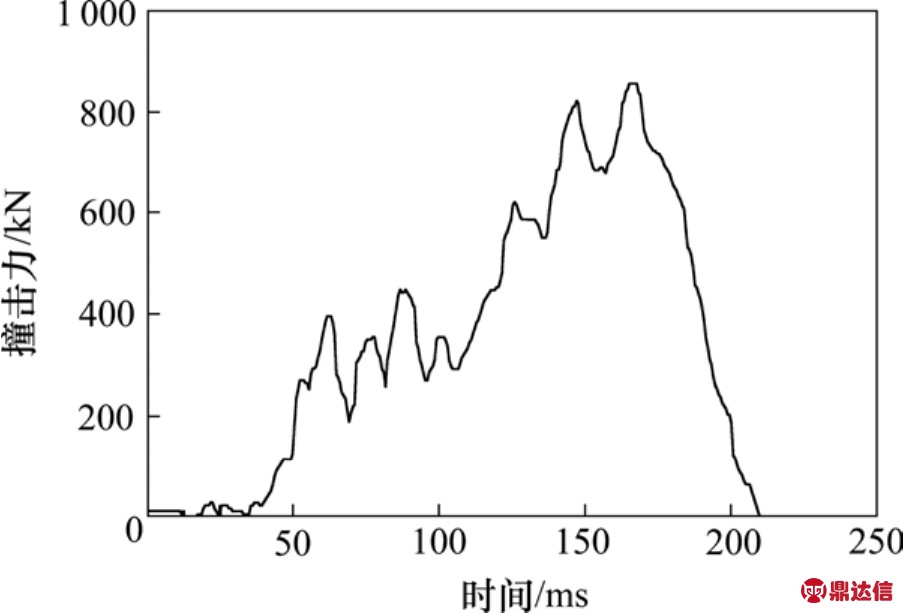
图5 撞击力−时间曲线
Fig. 5 Force-time response
动车组端盖样件受低速冲击作用后产生类似矩形的穿透破坏孔(图 6(a)),碎屑尺寸细小,穿透破坏孔孔边轮廓规整(图 6(b)),破孔边界缠绕的纤维束很少,孔边其他区域发生了部分基体剥离现象(图 6(c)),结构刚度发生退化。低速冲击实验后,车钩钩头凹锥孔结构及模拟工装内均为发现大尺寸碎屑进入(图 6(d))。整个冲击过程端盖样件未产生大挠度弯曲就发生穿透现象,满足动车组端盖被动安全防护要求。
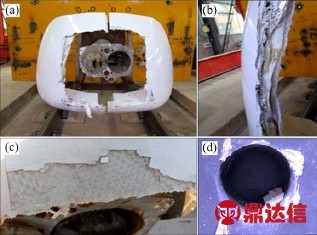
图6 端盖样件冲击试验结果
Fig. 6 Impact test results of sample parts
(a) 端盖样件整体形貌;(b) 左侧边局部放大;(c) 局部表面剥离形貌;(d) 冲击试验碎屑
5 结论
1) 结合复合材料层板及端盖样件冲击试验结果,提出以复合材料端盖的破损形貌,破损难易程度及穿透破坏响应时间等参数作为其耐撞性评价指标,为动车组头罩端盖选材设计提供参考。
2) 通过 3种构造形式复合材料层合板低速冲击试验,发现编织纤维层合板受冲击作用时,整体响应时间短,可以保证材料未发生大挠度变形时就产生穿透损伤形貌。同时,穿透形貌轮廓规整,无纤维交织缠绕,碎屑尺寸细小,满足动车组端盖被动安全要求。
3) 利用编织纤维材料试制动车组端盖头罩。通过端盖样件低速冲击实验表明:动车组以7.2 km/h速度撞击静止列车时,端盖可以产生大小允许车钩穿过的损伤破孔,且碎屑尺寸细小不影响车钩连挂。