摘 要 针对柔性舱为密封舱在太空环境中存在密封可靠性不足问题,文章提出了一种柔性舱O型密封结构,建立了柔性舱密封结构的非线性有限元仿真模型。通过柔性舱O型密封圈的Von Mises应力及最大接触应力来判定柔性舱密封可靠性,探讨柔性舱内气压、预压缩率、压条与舱门法兰间是否添加薄膜等因素对柔性舱密封性能的影响状况。ANSYS仿真分析结果表明:随着预压缩率及柔性舱内压增加,最大接触应力与Von Mises应力增大;当柔性舱密封结构添加薄膜时将增强密封性能,预压缩率为10%且舱内气压在0.1~0.6MPa范围内时可实现自密封,从而保证柔性舱密封性能。
关键词 柔性舱密封 O型密封圈 有限元分析 接触应力 航天器机构
0 引言
载人深空探测是扩展人类活动领域及开发利用资源的有效途径,大型空间柔性舱体作为载人深空探测的典型设备,不仅可用于空间站的建设,同时还能为后续月球基地的探测和建设奠定基础[1-2]。为了保证深空探测安全进行,在发射前需对柔性舱密封等结构进行可靠性试验,检验其在太空环境中能否工作正常,而密封技术又是评定柔性舱可靠性关键因素之一[3]。
密封技术对航天器正常工作至关重要,历史上曾发生数起因密封装置失效而造成的航天事故,如1986年美国“挑战者”号[4],由于右侧推进器O型密封结构设计问题导致密封圈失效,燃气泄漏造成航天飞机爆炸;2007年美国“奋进号”航天飞机因船舱泄漏问题导致无法按期发射[5]。针对密封可靠性不足问题现阶段密封结构大多采用O型密封圈形式[6],业内对于此类密封结构已开展了大量研究工作,例如:文献[7]中提出了O型密封圈的接触应力的经验公式,可用于解决密封结构摩擦、泄露及其耐用性问题。文献[8]对大型真空容器的密封结构进行有限元研究,得出密封槽宽度对密封圈压缩量的影响规律。文献[9]对载人飞船舱门及主轴密封结构进行有限元分析,得出结构参数对密封性能的影响规律、分析摩擦系数及温度对密封失效的影响规律。
目前,国内大多数飞行器大多使用O型密封圈进行密封,O型密封圈具有体积小、结构紧凑、密封性能好、摩擦阻力小等优势,可广泛应用于端面及其零件内外径结构切合面[10-11]。影响密封圈密封性能的因素包括:舱内气压、O型密封圈预压缩率、槽口倒角等因素[12-13]。本文以大型空间柔性舱体密封结构的O型密封圈为例,利用ANSYS软件研究各影响因素下O型密封圈的接触应力及Von Mises应力,分析O型密封圈的受力和密封性能,对O型密封圈各个影响因素下进行有限元仿真分析,为柔性舱的密封性能提供科学的理论依据。
1 柔性舱密封结构及密封性能判定
柔性舱舱体的密封性能主要取决于舱门的密封结构,结构例如图1所示。柔性舱舱门共设置两处密封结构,一处为舱门与舱门法兰之间设置O型密封圈,夹层间增加薄膜,舱门与舱门法兰由螺钉连接;另一处为舱门法兰与蒙皮之间设置O型密封圈,中间夹层增加薄膜,舱门法兰与压条由螺钉连接,对柔性舱蒙皮实施压力起到固定作用。为提高柔性舱密封性能,在舱门法兰与蒙皮间设置两道密封圈增强密封可靠性。柔性舱的密封结构通过O型密封圈进行径向密封为轴对称结构,将其简化为二维模型如图2(a)所示。柔性舱蒙皮刚化后弹性模量远大于密封圈[17],因此,可将柔性舱蒙皮及压条简化为单个刚体。图2(b)为径向密封结构简化后O型密封圈的几何模型,柔性舱舱门两处密封结构可用该简化模型进行计算。柔性舱O型密封圈直径为7mm,密封槽尺寸为9.7mm×5.72mm,槽口半径为1mm,槽底半径0.2mm。
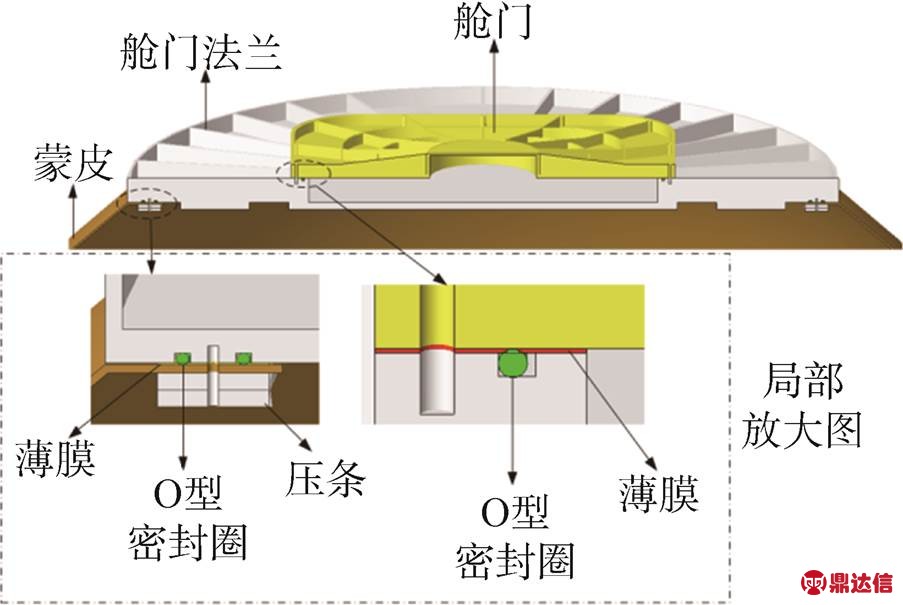
图1 柔性舱舱门密封结构例
Fig.1 Flexible cabin door sealing structure
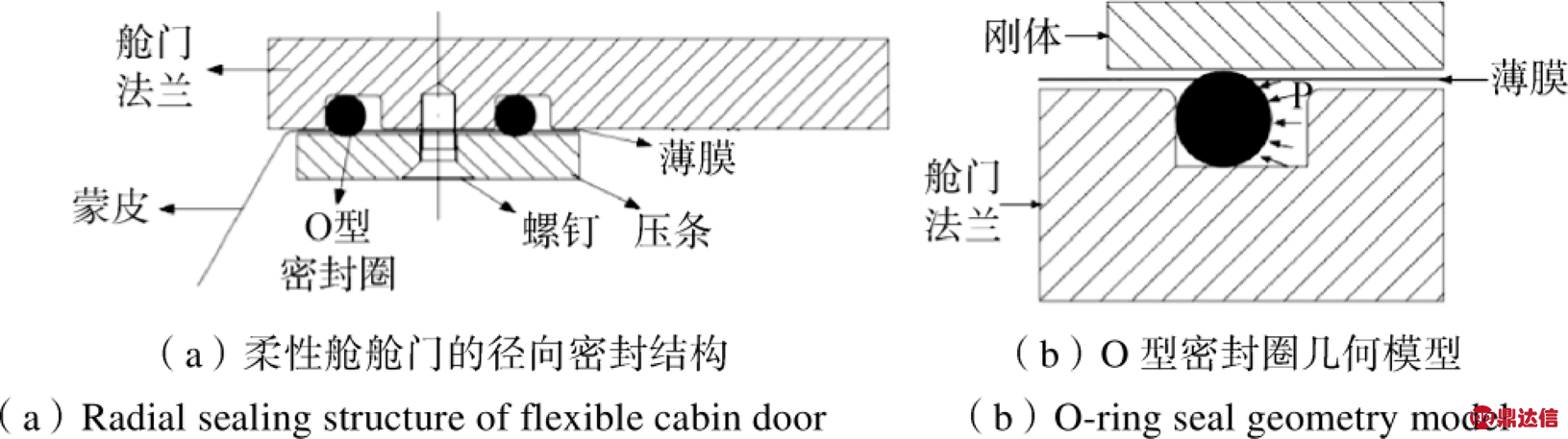
图2 柔性舱密封结构二维模型
Fig.2 Two-dimensional model of flexible cabin sealing structure
柔性舱O型密封圈密封面的接触应力及Von Mises应力影响密封结构的密封特性,柔性舱密封性能的优劣取决于舱门法兰与O型密封圈的最大接触应力,密封圈接触面最大接触应力大于柔性舱内气压时可实现密封效果,最大接触应力越大,柔性舱密封性能越好[14]。同时,需考虑密封圈的最大Von Mises应力,具体计算公式为

式中 σ1、σ2、σ3为单元体三个方向的主应力;σ为Von Mises应力,大小可判定密封圈的破坏失效及疲劳失效概率;其等效应力主要反映密封圈某点的Von Mises应力,Von Mises应力越大,O型密封圈越易出现材料蠕变及应力松弛现象[15]。
O型密封圈的最大接触应力越大密封性能越好,而Von Mises应力越大材料易失效,因此,最大接触应力与最大Von Mises应力相互限制,可利用柔性舱O型密封圈密封面接触应力及Von Mises应力判定柔性舱密封结构的密封性能[16]。
2 计算模型
2.1 O型密封圈材料模型
对柔性舱O型密封圈进行有限元分析时,将O型密封圈视为超弹性体,具有材料非线性及几何非线性的力学特性[17]。现假设O型密封圈材料具有不可压缩或近似不可压缩、各向同性的特性,Rivlin提出不可压缩或近似压缩及各向同性橡胶材料的应变能函数由应变张量的2个不变量I1、I2所表示[18],并推导出Mooney-Rivlin模型的应变能函数模型W

式中 Cij,N,dk为Mooney-Rivlin模型常数;J为初始和终止状态的体积比。
应变不变量I1、I2为
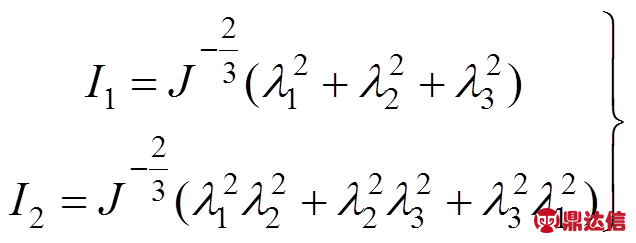
式中 λ1,λ2,λ3为三方向主伸长比;O型橡胶圈视为不可压缩材料或近似不可压缩材料时J=1。
Mooney-Rivlin模型一般有2、5、9种材料参数的材料模型[19],本文选取两个材料参数的两项式Mooney-Rivlin模型,即:

式中 I1、I2为应变张量的2个主不变量;C10、C01为Mooney-Rivilin模型常数。
柔性舱的O型密封圈选取硬度为80、泊松比为0.499、的丁腈橡胶,薄膜材料采用弹性模量为255MPa、泊松比为0.15的线弹性材料。
2.2 有限元模型
柔性舱O型密封圈为轴对称模型,其受力为轴对称,因此,传统密封结构如图3(a)所示。对O型密封圈仿真时,建立O型密封圈、舱门法兰、刚体的二维轴对称模型。在图3(a)密封结构基础上,在舱门法兰与刚体之间添加薄膜,用于仿真柔性舱在有薄膜工况下的密封性能,增加薄膜的密封结构如图3(b)所示。柔性舱O型密封圈两种模型均采用自由划分网格技术。
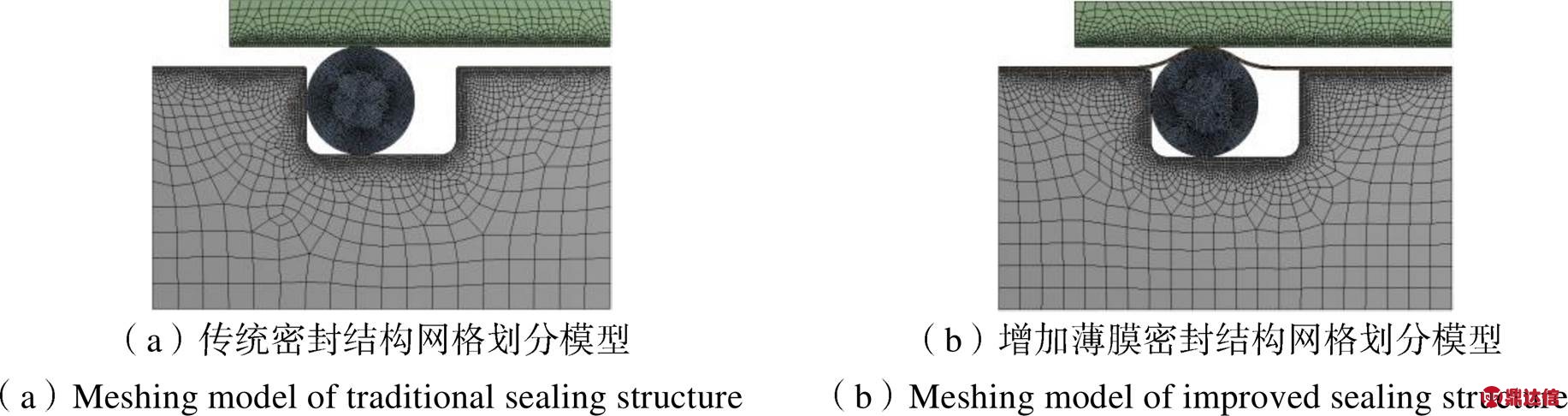
图3 柔性舱密封结构网格划分
Fig.3 Meshing of flexible cabin sealing structure
柔性舱O型密封的工作过程可分为三步:第一步为刚体与舱门法兰的安装过程,即先将刚体移动一段距离,使密封圈有一个预压缩率;第二步为对柔性舱进行充气加压过程,即O型密封圈添加均布压力过程;第三步为柔性舱法兰与刚体之间增加薄膜进行装配及加压过程。仿真模拟柔性舱密封圈的密封过程,将刚体移动一定距离,使其缓慢移动到安装位置,实现刚体与舱门法兰的安装过程模拟。对柔性舱进行充气加压,在密封圈一侧添加压力,仿真在一定压缩率下的加压过程,此过程有三组接触对:1)舱门法兰与密封圈接触;2)密封圈与薄膜接触;3)薄膜与刚体接触。
3 O型密封圈仿真分析
3.1 无气压下不同预压缩率对柔性舱密封特性的影响
模拟无气压下不同预压缩率对柔性舱密封性能的影响,逐步移动刚体到指定位置,O型密封圈的压缩率分别为5%,10%,15%,20%。O型密封圈不同预压缩率的Von Mises应力分布云图如图4所示,可以看出:随着压缩率的增加,密封圈上下截面变形,应力也对应增加,出现两个峰值区,分别为O型密封圈靠近法兰及刚体接触位置,呈现“哑铃”状,红色区域Von Mises应力较大由上下两端向中间靠拢;当预压缩率达到20%时,红色区域贯穿,此时O型密封圈出现应力集中,易出现裂纹现象。
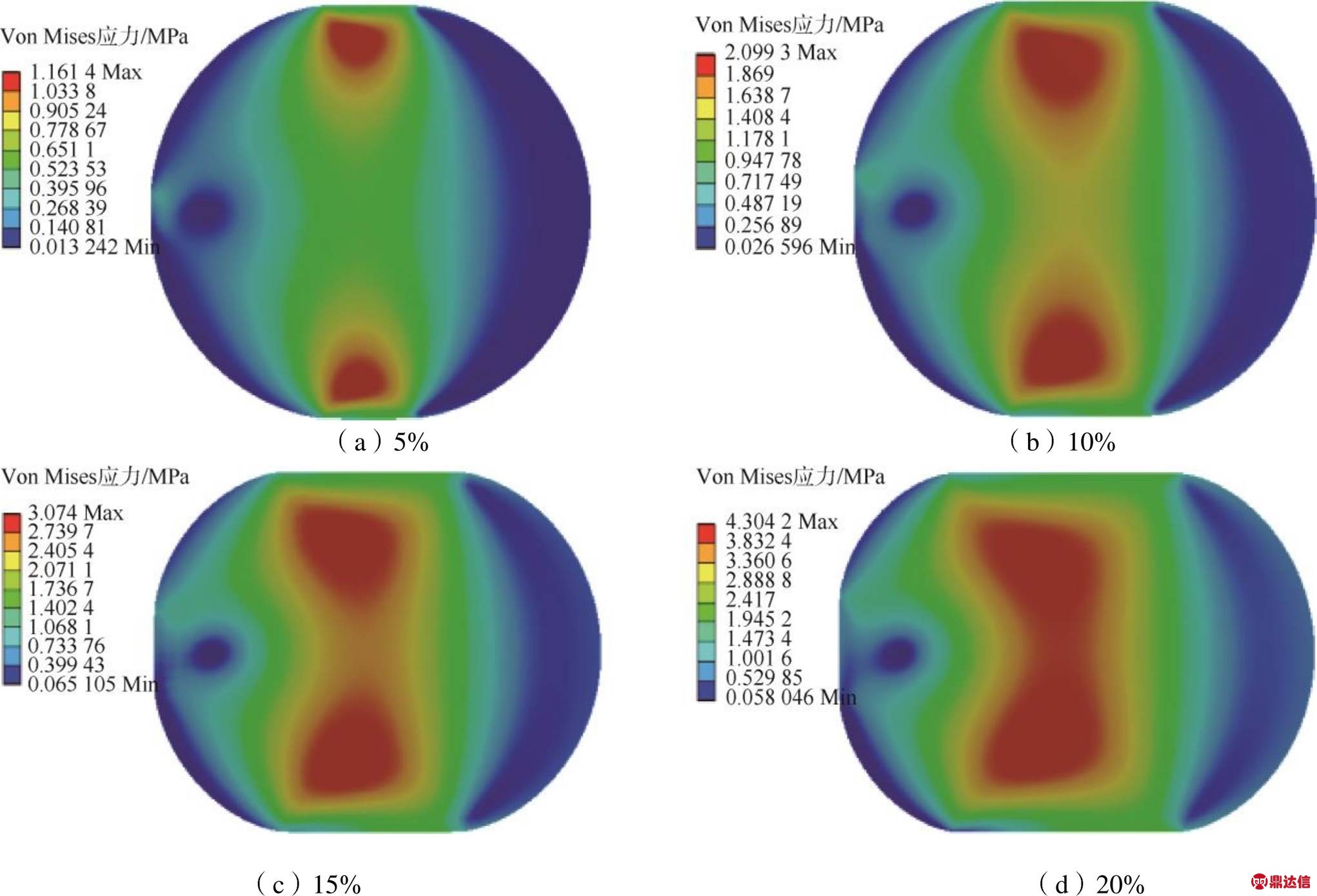
图4 不同预压缩率下Von Mises应力分布
Fig.4 Von Mises stress distribution at different pre-compression rates
接触应力分布状况如图5所示,由图可知O型密封圈与刚体及密封槽的接触面积增大,上下接触应力对称分布;随着预压缩率的增大,密封圈与刚体最大接触应力增大,与Hertz接触理论相符合[20]。
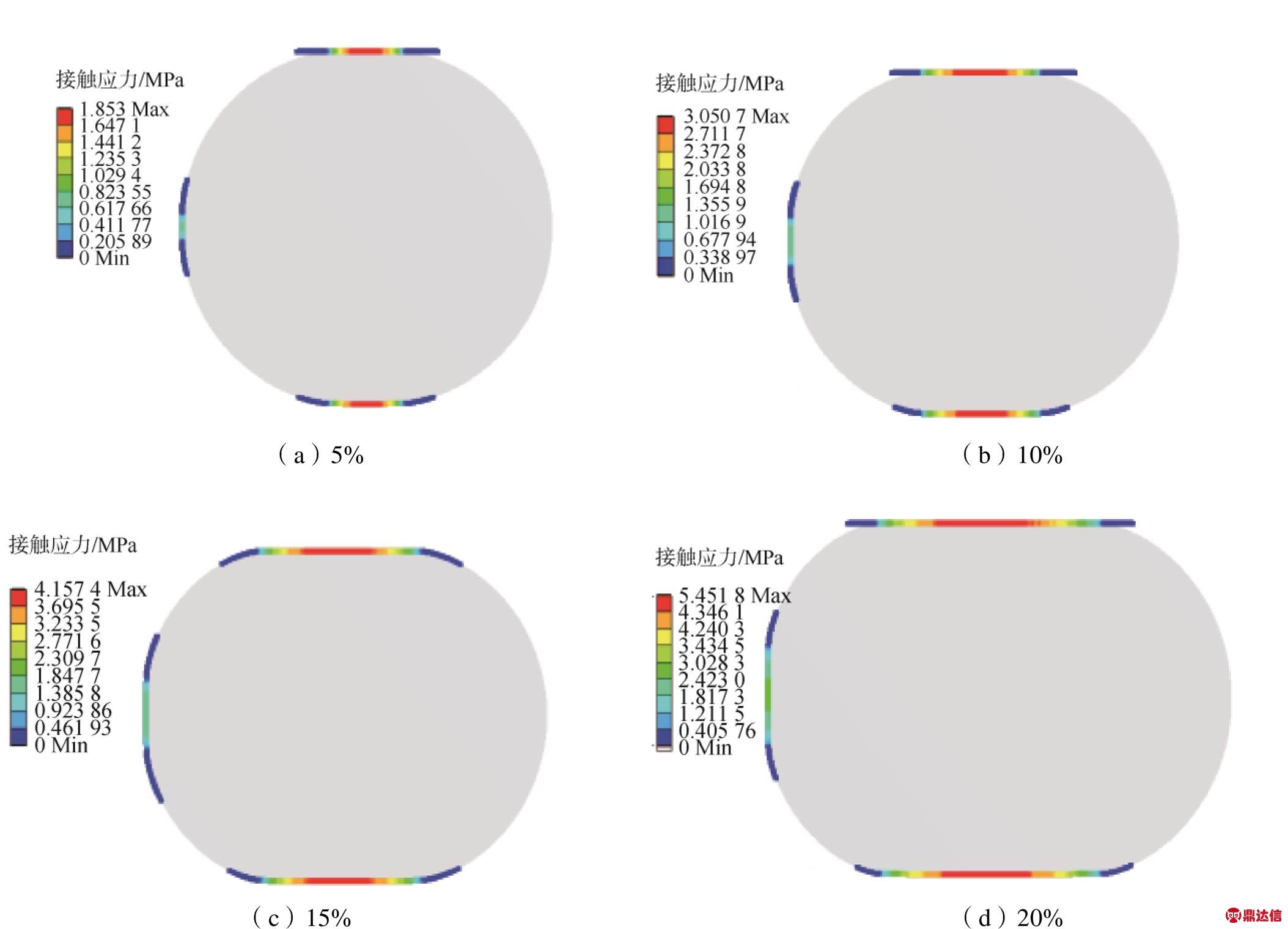
图5 不同预压缩率下接触应力分布
Fig.5 Contact stress distribution diagram at different pre-compression rates
当柔性舱在无内压条件下,不同预压缩率下最大接触应力及最大Von Mises应力分布如图6所示,最大接触应力由1.15MPa增加至5.45MPa,最大Von Mises应力随着预压缩率的增大而增大,但增加至20%时,密封圈出现应力集中现象,此时O型密封圈易出现裂纹,导致密封失效。
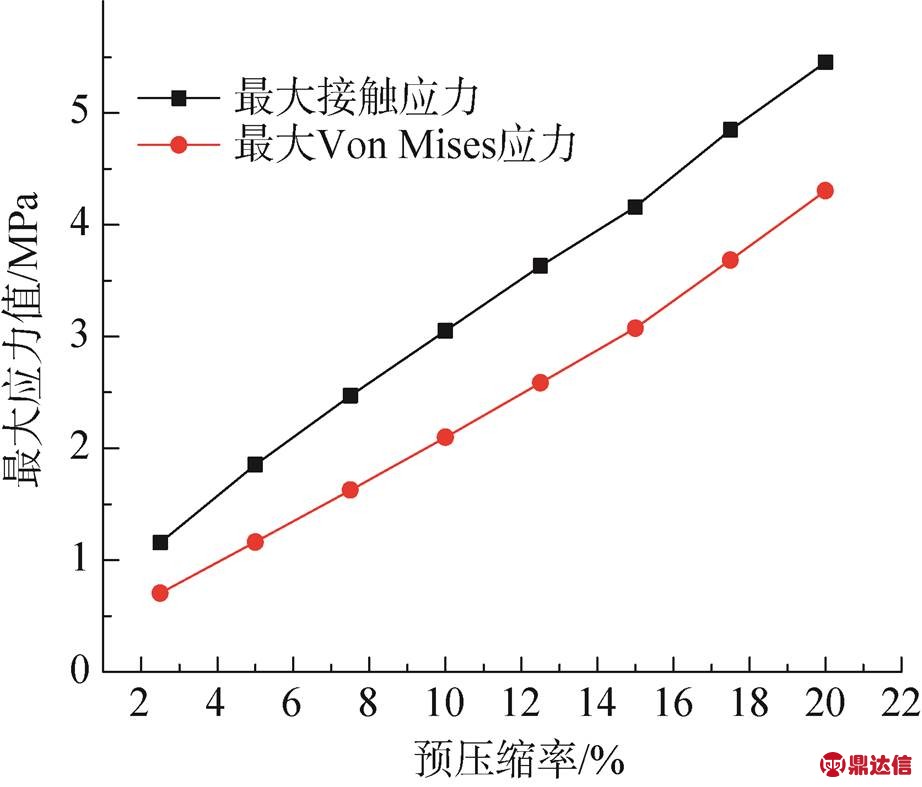
图6 不同预压缩率下最大接触应力及最大Von Mises应力
Fig.6 Maximum contact stress and maximum Von Mises stress at different precompression rates
3.2 柔性舱内不同气压对柔性舱密封特性的影响
柔性舱内无气压、压缩率为10%时,O型密封圈未出现应力集中现象。选取预压缩率为10%,并逐步增加柔性舱内压由0.1MPa至0.6MPa进行仿真分析。结果显示,最大接触应力由3.07MPa增至3.55MPa,远大于柔性舱内气压,说明柔性舱在此状况下能实现自密封,并在内压作用下,O型密封圈向左挤压移动,柔性舱内气压增大,接触应力增大。
保持O型密封圈压缩率为10%,逐步增加柔性舱内压,最大Von Mises应力及最大接触应力变化趋势如图7所示。可以看出,预压缩率一定,增大柔性舱内压,最大Von Mises应力的变化较小近似为一条直线,而最大接触应力则呈显著增大的趋势。
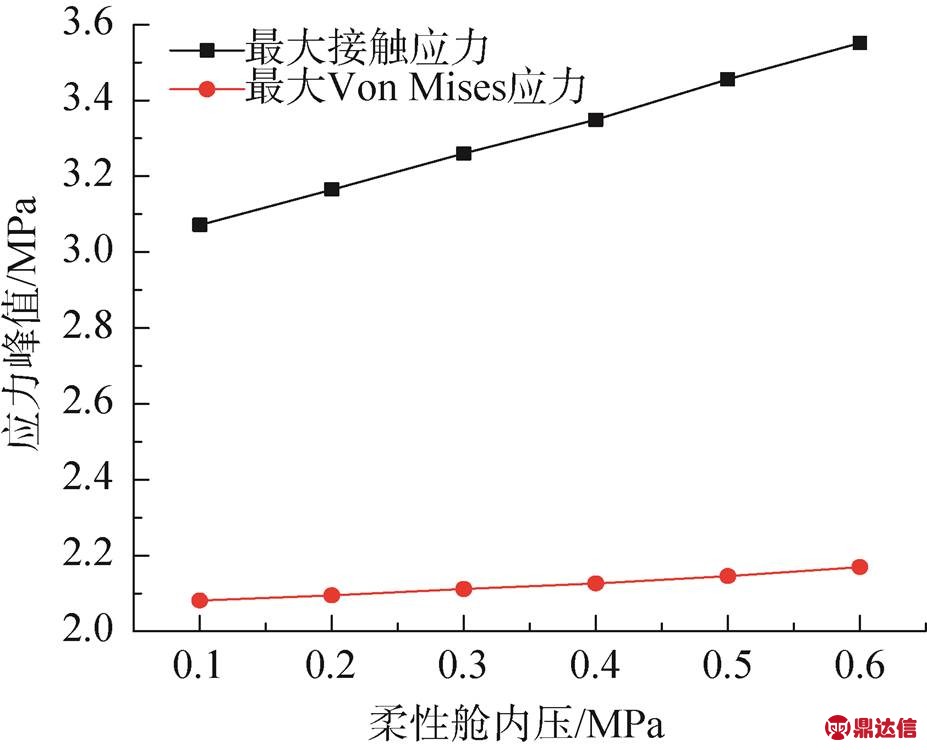
图7 最大Von Mises应力及最大接触应力随柔性舱内压的变化趋势
Fig.7 Maximum Von Mises stress and maximum contact stress under different internal pressures
3.3 柔性舱刚体与舱门法兰之间添加薄膜对柔性舱密封特性的影响
当柔性舱刚体与舱门法兰之间增加薄膜,在柔性舱内无气压状况下,预压缩率分别为5%,10%,15%,20%时,O型密封圈的Von Mises应力分布如图8所示。可以发现,随着压缩率的增加,O型密封圈Von Mises应力也对应增加,出现上下两个峰值区,当预压缩率达到20%时,O型密封圈易出现裂纹。随着预压缩量的增大,O型密封圈最大接触应力由1.403MPa增至5.134MPa,最大Von Mises应力在一定范围内和预压缩率近似成线性增长,具体变化趋势如图9所示。
柔性舱内无气压、压缩率为10%时,O型密封圈未出现应力集中现象,在此预压缩率下逐步增加柔性舱内压由0.1MPa至0.6MPa,最大接触应力和最大Von Mises应力的变化趋势如图10所示。可以发现,随着内压增大,最大接触应力由2.967MPa增加至3.703MPa,主密封界面的接触应力均值为3.28MPa,远大于柔性舱内压,故O型密封圈能够实现自密封;在柔性舱内压推动下,O型密封圈向左偏移,内压的增大对最大Von Mises应力影响较小。
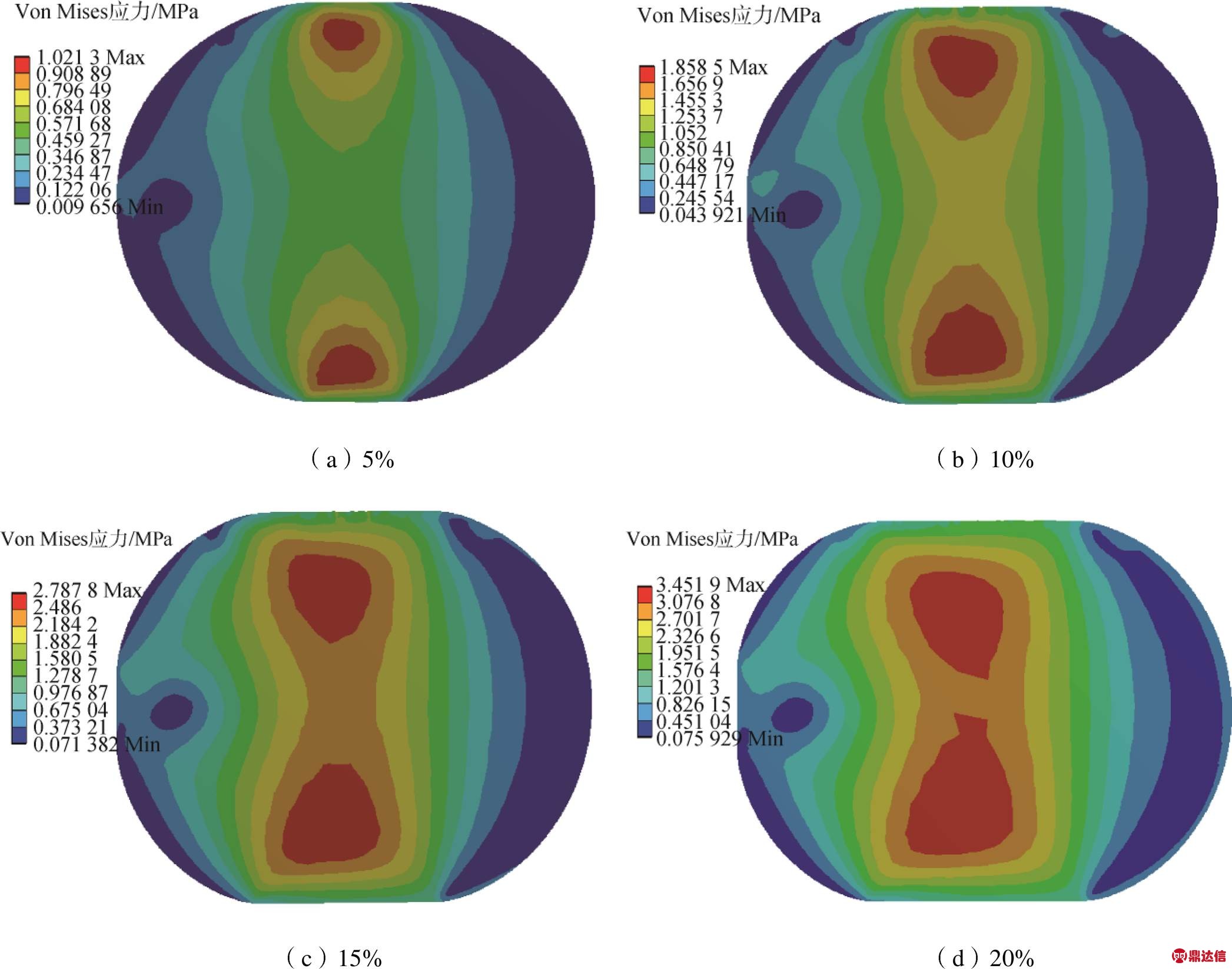
图8 不同压缩率下Von Mises应力分布
Fig.8 Von Mises stress cloud at different compression ratios
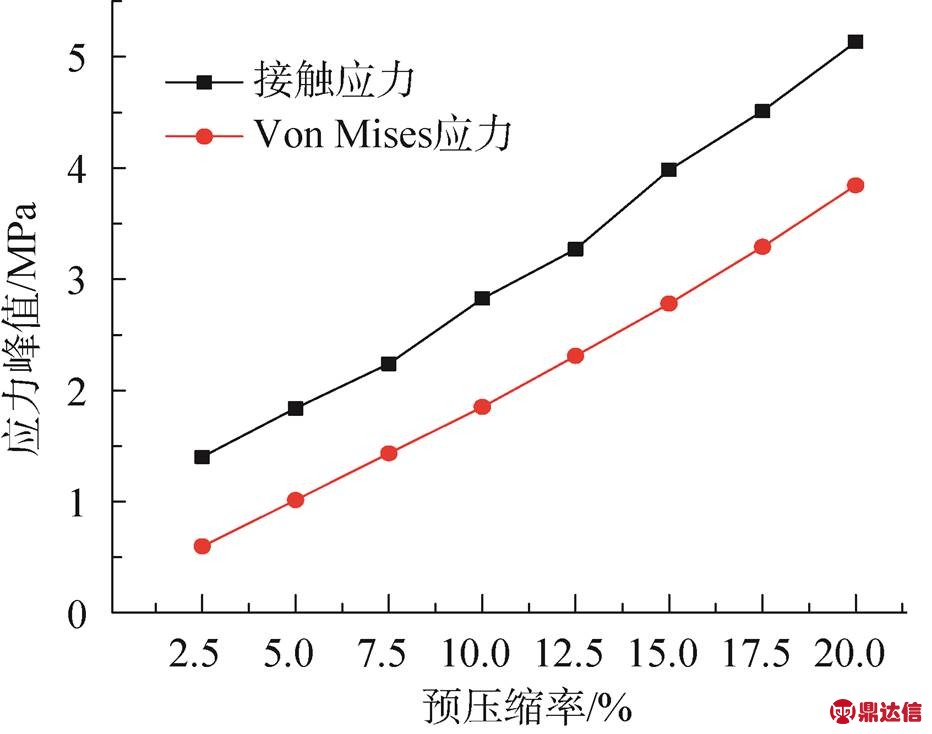
图9 不同压缩率下最大Von Mises应力及最大接触应力
Fig.9 Maximum Von Mises stress and maximum contact stress at different compression rates
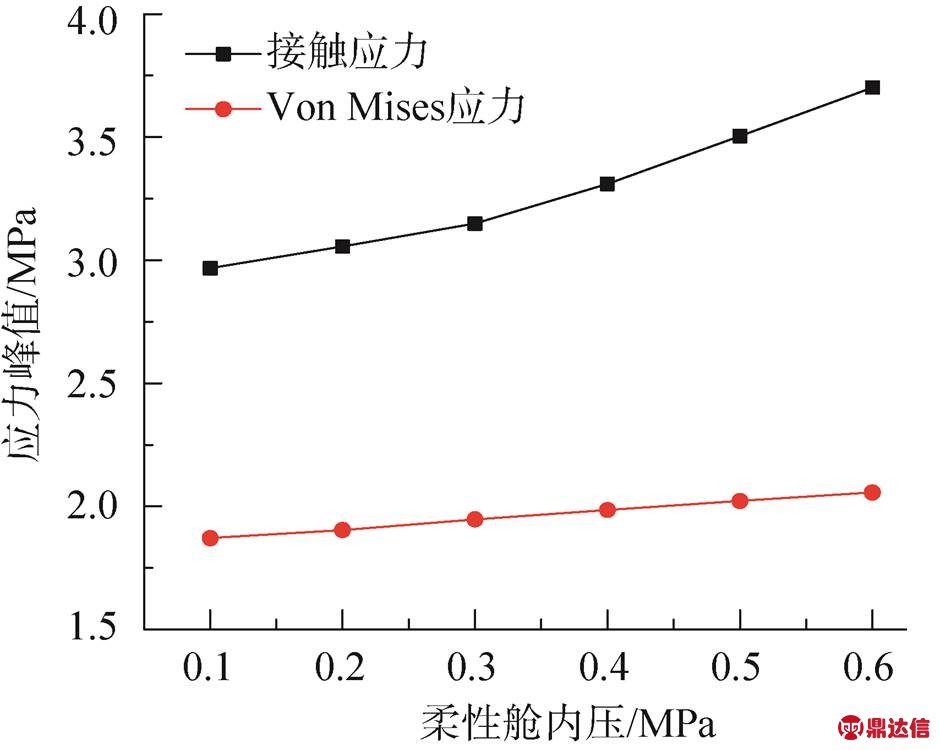
图10 不同内压下最大接触应力及最大Von Mises应力
Fig.10 Maximum Von Mises stress and maximum contact stress under different internal pressures
不同内压状况下对比传统密封结构和增加薄膜的密封结构的最大接触应力,如图11(a)所示,可以看出,当柔性舱内压达到0.4MPa后,增加薄膜的密封结构比传统密封结构最大接触应力大,密封结构密封性能更好。最大Von Mises应力变化如图11(b)所示,可以发现有薄膜状况下密封圈的应力峰值始终小于传统密封结构结果,这可有效减小密封圈出现裂纹及永久变形状况,因此添加薄膜可增加O型密封圈的使用寿命。
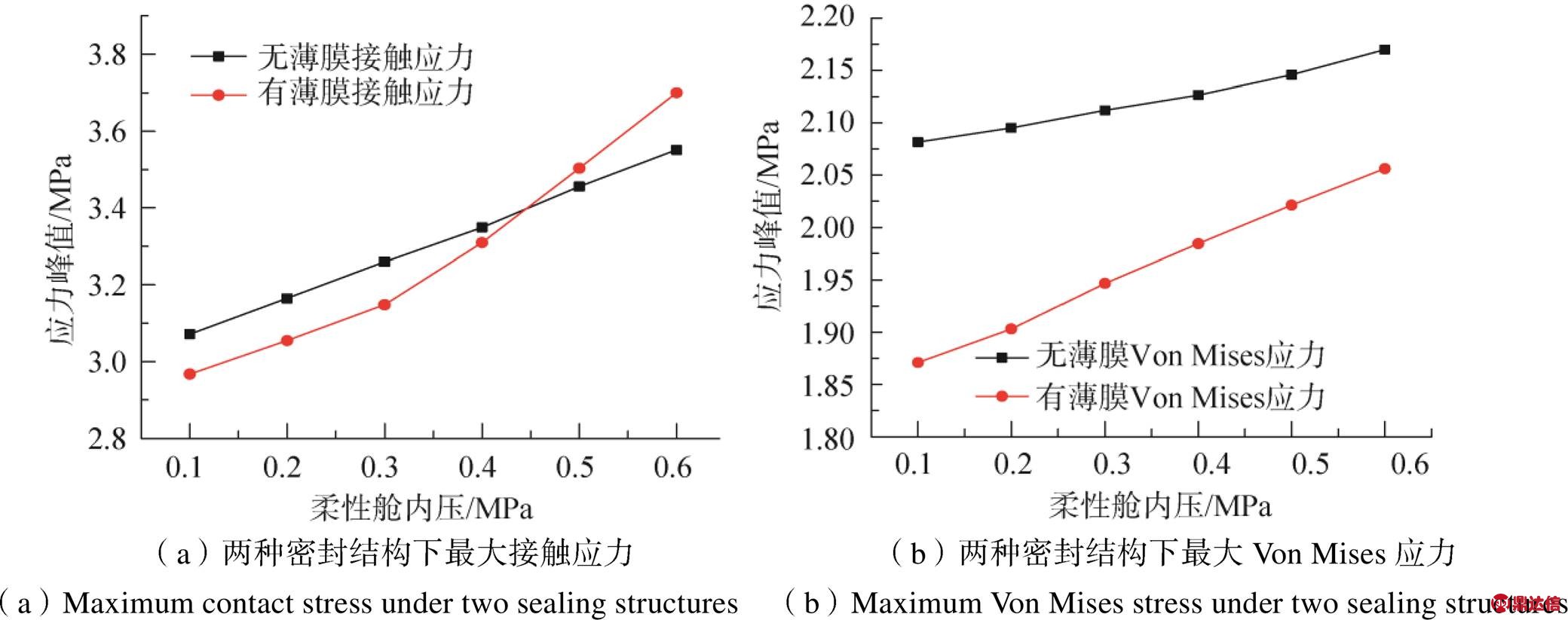
图11 两种密封结构下O型密封圈的最大接触应力和最大Von Mises应力
Fig.11 Maximum contact stress and maximum Von Mises stress of O-rings under two sealing structures
4 结束语
基于柔性舱舱门结构的密封性能需求,本文提出一种柔性舱舱门密封结构,并对该密封结构建立有限元模型,通过最大接触应力及最大Von Mises应力来判定柔性舱的密封性能,研究预压缩率及柔性舱充气压力对O型密封圈密封性能影响,得到以下结论:
1)当柔性舱内气压为0 MPa时,增大密封圈预压缩率,使密封圈与法兰的接触面积增大,增加密封效果,但预压缩率较大时密封圈易出现应力松弛,造成永久变形,导致密封失效。因此,在保证有效密封的状况下适当选择预压缩率。
2)预压缩率一定时,柔性舱加压过程中,密封圈与法兰接触面积及接触应力逐渐增大,增加密封性能。满足柔性舱蒙皮及舱门结构强度下,柔性舱在0.1至0.6 MPa压力范围内,最大接触应力始终远大于舱内压,可实现密封效果。
3)增加薄膜的柔性舱密封结构O型密封圈的最大接触应力始终远大于舱内充气压力,Von Mises应力始终小于传统密封结构的数值,能够有效保障柔性舱在轨密封可靠性。