摘要:建立矩形密封圈的混合润滑模型,分析工作压力、活塞杆运行速度和密封件粗糙度对轴向往复用矩形密封圈的摩擦力矩、泄漏量的影响。结果表明:过大的密封压力会对密封件造成损坏,使得摩擦力和净泄漏量极速增大;往复速度的增加会使摩擦力线性增大,直线往复密封的净泄漏量随着表面粗糙度的增大表现为越来越大的增量。利用田口实验设计方法对矩形密封圈操作压力、运行速度和密封件粗糙度进行正交试验,分析得到最优参数组合,并得到各影响因素对密封性能的影响程度由大到小依次为往复速度、粗糙度、密封压力。
关键词:矩形密封圈;运行参数;田口方法
矩形密封圈因结构简单、抗挤出能力强、密封压力大、工作寿命长等特点,在液压系统中得到广泛应用。对于矩形密封圈的研究最早可追溯到WHITE和DENNY[1]在1947年所进行的实验,他们对矩形密封圈的磨损和挤出机制、摩擦特性、润滑过程进行了探索。1972年FIELD和NAU[2]确立了矩形密封圈泄漏率、摩擦力和油膜厚度与压力、速度操作运行参数间的关系。但这些都是在假设密封件表面光滑且润滑条件为全油膜润滑的基础上进行的研究。 2010年NIKAS[3]在考虑矩形密封圈粗糙度的前提下,建立了矩形密封圈的弹性动力润滑方程,在耦合流体压力对密封圈弹性变形影响的情况下,用数值计算方法,求得矩形密封圈的油膜分布、操作压力、摩擦力及泄漏量等密封性能参数,为接近实际情况下矩形密封圈的数值计算提供了理论基础。但这些研究并没有确立矩形密封圈的增效操作运行参数间的最佳匹配关系。
为了探索矩形密封圈不发生泄漏和减少摩擦磨损所需要的密封件粗糙度、运行速度和操作压力间的最佳匹配关系,本文作者利用田口实验设计方法对矩形密封圈操作压力、运行速度和密封件粗糙度进行正交试验[4],分析得到各影响因素对密封性能的影响程度,得到最优参数组合。
1 矩形弹性密封圈的数值计算模型
1.1 矩形密封圈的流体力学分析
矩形密封结构示意图如图1所示。将活塞杆与密封圈空气侧边缘延伸线间的交点设为直角坐标系的原点O,圆周方向、轴向和径向坐标分别由X、Y、Z表示。图2为矩形密封圈密封接触区域示意图。文中在以下假设基础上建立数值计算模型[5]。
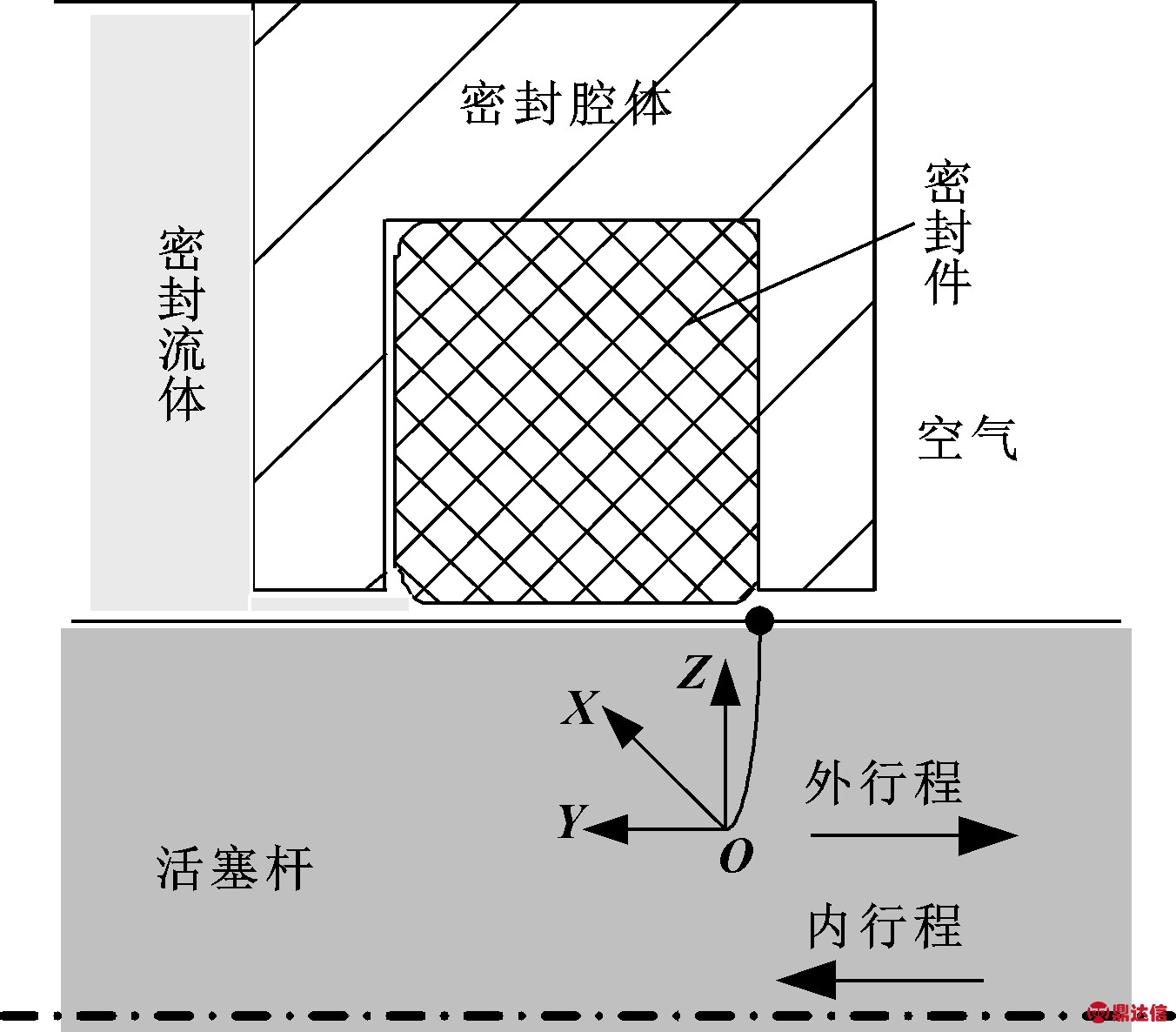
图1 矩形密封圈的结构组成
Fig 1 Basic assembly of the rectangular seal

图2 密封接触区域示意
Fig 2 Sealed contact area
(1)活塞杆表面绝对光滑,密封面粗糙,活塞杆为刚性体,密封件是弹性体;
(2)密封件是轴对称的,沿油膜厚度方向不考虑压力的变化;
(3)流体是牛顿流体,由于往复速度不高,流体在杆与密封接处的黏性剪切力忽略不计;
(4)密封件是弹性材料,流体润滑剂的黏压效应忽略不计,由于密封件相比活塞杆较薄和较软,不能看作半空间体。
矩形密封圈密封区域流体力学分析通过雷诺方程求解:


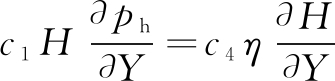
(1)
其中:
A≡ca/{(1+cbp)[1+(ca+cb)p]}-α

式中:φ为圆周坐标;Y为轴向坐标;H为膜厚;ph为油膜压力;η为液压油的动力黏度;p为密封与活塞杆接触处压力,p=pcon+ph,pcon为预加载荷接触压力与密封压力总和;ca、cb为流体常数;Drod为活塞杆的外径。
文中通过超松弛迭代的方法对油膜压力ph进行计算。迭代计算的边界条件为:空气侧ph为0,液压油侧为1-pcon/pcyl,pcyl为密封压力,循环计算连续两次迭代之间压力最大差值小于0.001后,得出收敛解ph。
1.2 矩形弹性密封圈的接触力学分析
密封圈初始安装时的接触压力p0和在介质压力作用下的接触压力pcon,按式(2)计算。

αseal(θ-θ0)-νsealεx-εz]
(2)
pcon=p0+pcylνseal/(1-νseal)
式中:νseal为密封圈泊松比;εx、εz为密封圈x、z方向应变[6]。
液压缸工作时密封圈与活塞杆的实际接触宽度Wc按式(3)计算,yc为公式(4)的根,εy为密封圈y方向上的应变[6],r为密封圈安装前的圆角半径。
Wc=(1+εy+λαsealΔθ)W-2yc
(3)

(4)
1.3 矩形弹性密封圈的变形力学分析
矩形密封圈的弹性变形大小不仅与密封圈的尺寸、所受载荷状况、密封耦合面的微观表面形貌及油膜厚度有关,还受到活塞杆、缸体的变形影响。因此通过对矩形弹性密封圈的微单元体进行受力分析,可由式(5)计算其径向变形

(5)
式中:b为密封件的厚度,b=(dcyl-Drod)/2;Q为密封腔体与密封件间的局部压力;pc为密封件与活塞杆间局部压力;Gseal为密封件的剪切模量,为活塞杆弹性径向位移[7],由式(6)计算。

(6)
式中:drod为活塞杆的内径;Erod为活塞杆的弹性模量;νrod为活塞杆的泊松比;αrod为活塞杆的热膨胀系数;θ为工作温度;θ0为密封圈安装时的室温。
活塞杆和密封圈的黏性剪切应力由式(7)、式(8)计算。

(7)

(8)
活塞杆局部法向位移由式(9)计算。

(9)
活塞杆与密封圈接触处的油膜厚度公式为
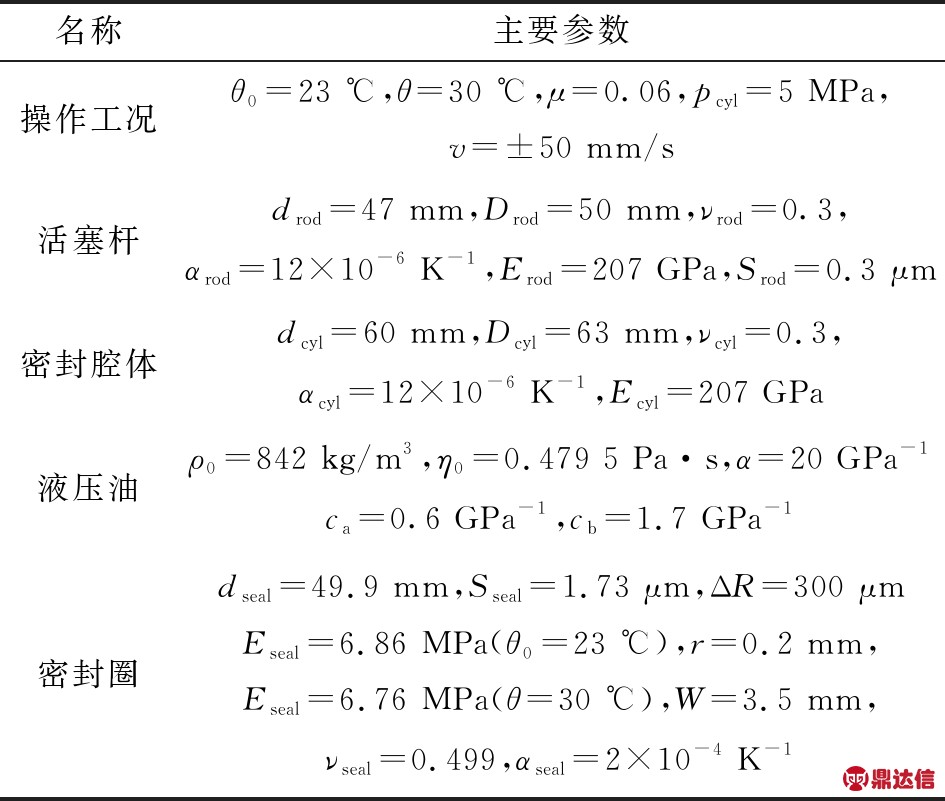
(10)
式中:Srod、Sseal分别为活塞杆和密封圈的粗糙度;是密封圈安装时对活塞杆表面造成的法向位移,为式(9)由p0计算出的
1.4 矩形密封圈数值计算流程
文中通过MatLab编程[8-10]的方式实现对方程的建立与求解,数值计算流程[11]如图3所示。
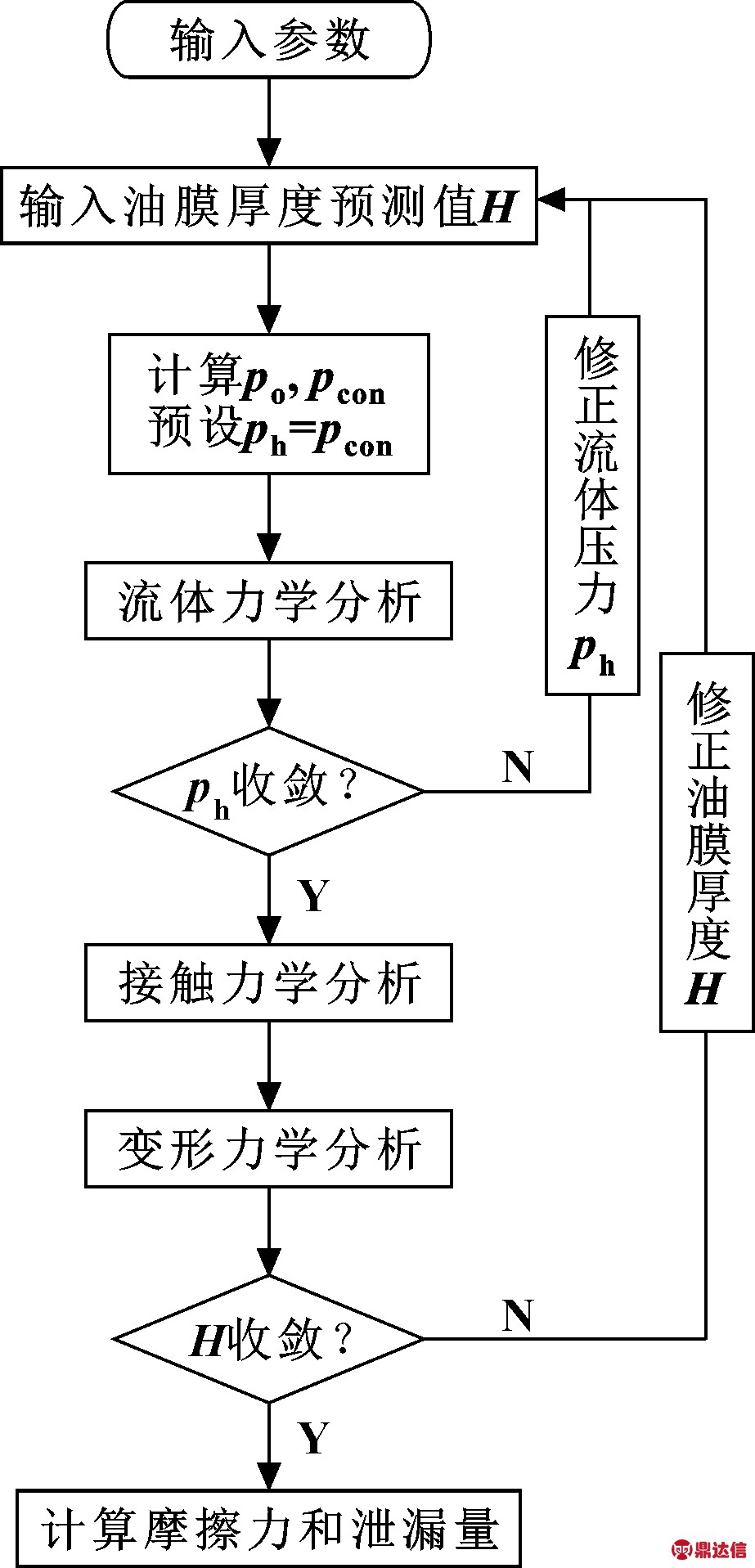
图3 数值计算流程
Fig 3 Flow of numerical calculation
假设初始时p=pcon(p为密封接触压力),对往复运动时密封区实际接触宽度进行计算,并预设合理的期望膜厚;通过流体力学分析求得收敛解ph,根据活塞杆的弹性径向位移,计算密封圈的弹性径向变形,再根据式(7)、式(8)计算密封圈与活塞杆间的黏性边界剪切力,求得活塞杆的局部法向位移,最后得到油膜厚度;通过反复迭代至收敛求得密封区域膜厚分布。最后,若计算出的膜厚可接受(将连续两次迭代求得膜厚差值在0.001之内),再由式(11)、式(12)计算密封圈的泄漏量q以及密封圈与活塞杆接触处的摩擦力Fseal。

(11)

(12)
2 弹性矩形密封圈密封性能及其影响参数
文中通过一驱动装置的矩形密封圈作为实例,探索运行参数与矩形密封圈密封性能之间的关系,该矩形密封圈的基本参数如表1所示。Eseal为密封圈的弹性模量;Grod、Gseal为活塞杆、密封圈的剪切模量;νseal为密封圈的泊松比;dseal、Dseal为密封圈的内径、外径;r为密封圈安装前的圆角半径;μ为边界摩擦因数,ρ为在(p,θ)条件下的流体密度;ΔR为θ0时的初始径向干涉;Srod、Sseal分别为活塞杆和密封圈的粗糙度。
表1 矩形密封圈的基本数据
Table 1 The data of the rectangular seal example
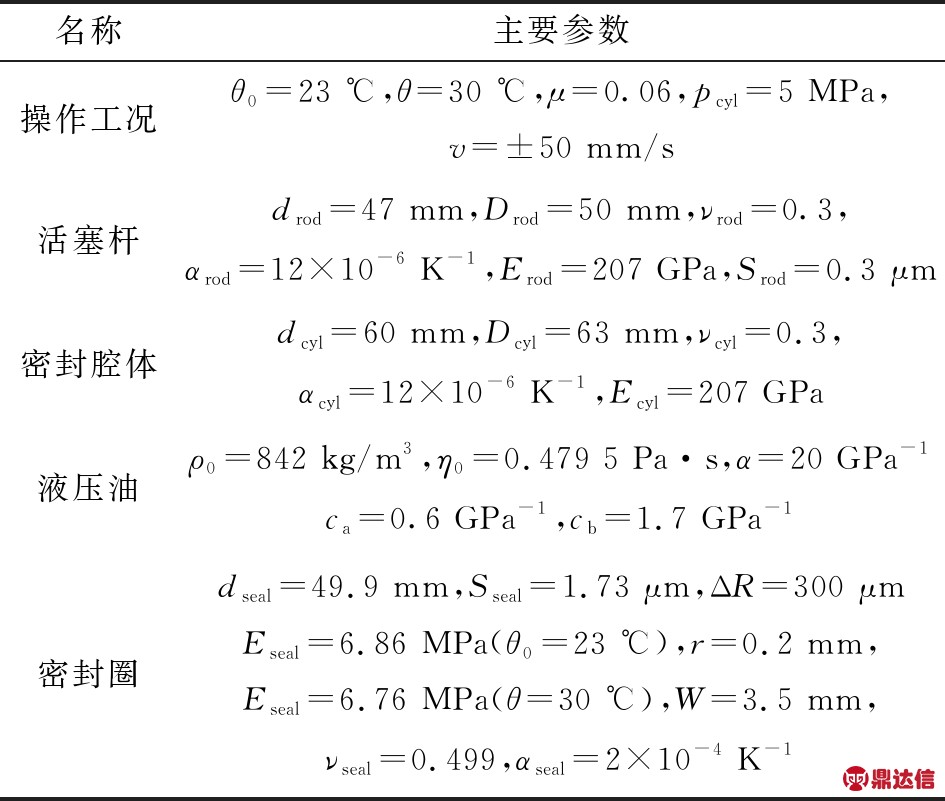
2.1 矩形密封圈的密封性能
往复密封圈的密封性能主要通过压力分布曲线及泄漏量来衡量。根据接触压力密封失效准则,为避免介质的泄漏,接触压力应大于等于最大密封压力。文中通过上述计算过程,得出矩形密封圈内、外行程的压力分布,将密封接触宽度划分为50×50的网格,耦合面压力分布如图4所示,内外行程压力均大于密封压力5 MPa,可实现有效密封。将数值计算结果与实验结果进行比较,如图5所示,压力分布与WHITE和DENNY[1]所作实验数据变化趋势一致,证明此计算结果是合理可靠的。
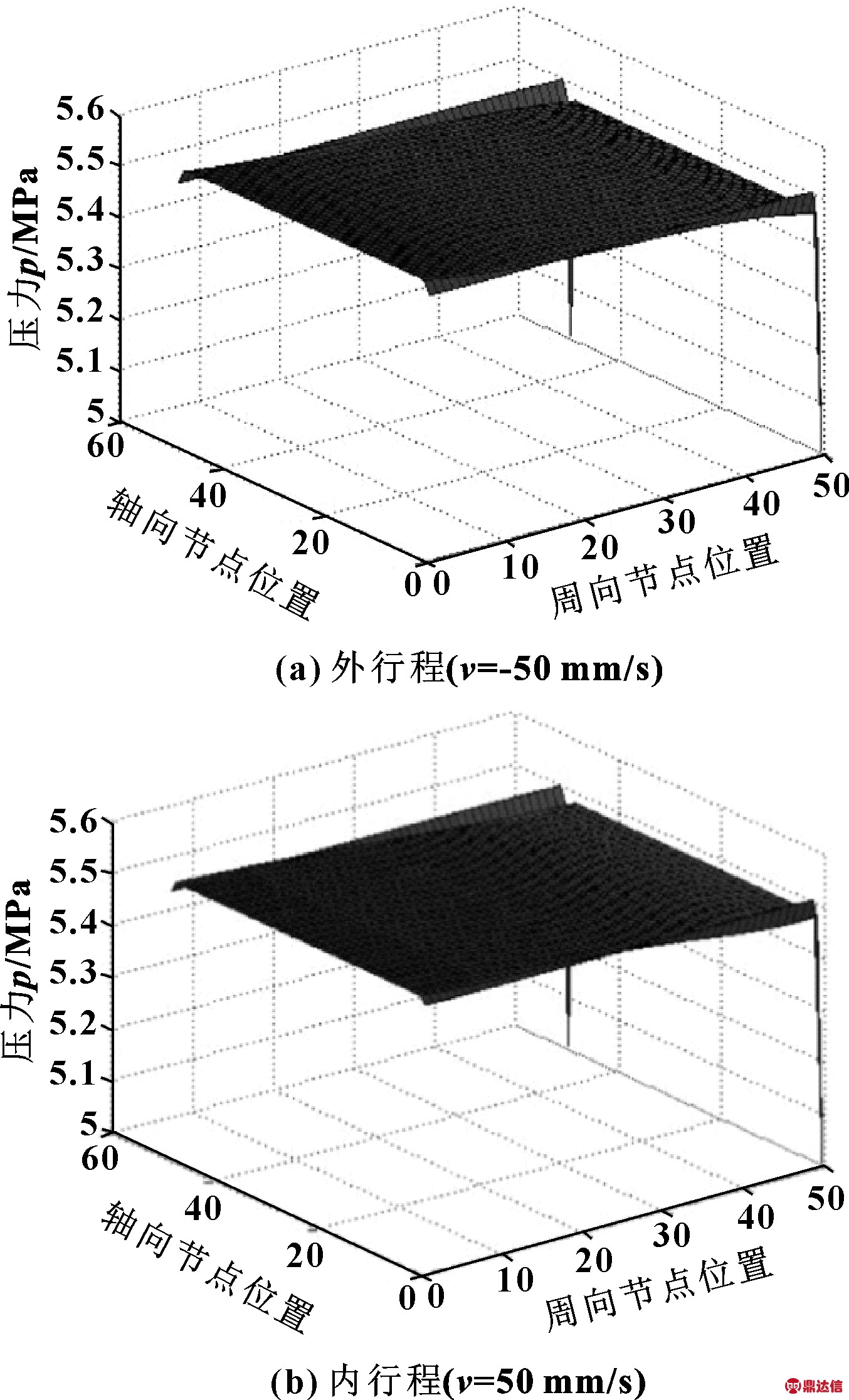
图4 内外行程密封耦合面压力分布
Fig 4 Pressure distribution between coupling surfaces of outstroke and instroke (a) outstroke(v=-50 mm/s);(b) instroke(v=50 mm/s)
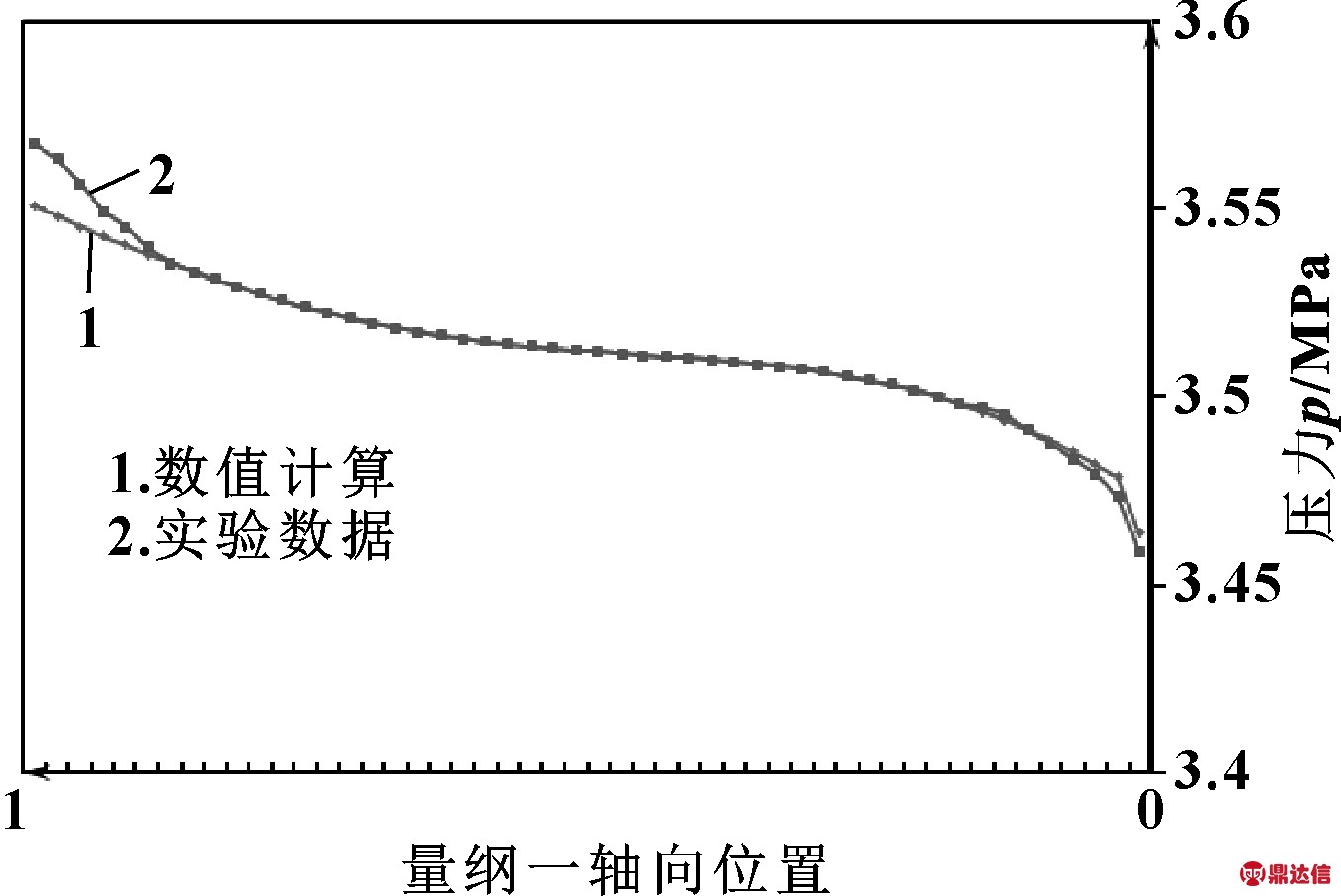
图5 压力分布计算结果与实验结果比较
Fig 5 Comparison of calculation results and experimental results of pressure distribution
图6给出了往复速度v=50 mm/s时密封圈内外行程的流量,可以看出内外行程流量的分布差别较大,内行程流量的变化较外行程平稳。若要保证密封不发生泄漏,内行程流量需要大于外行程流量。泄漏量为外行程流量的绝对值减去内行程流量,若泄漏量大于0,则表示发生了外泄漏,相反则表示密封性良好。图7给出了外行程流量绝对值与内行程流量的比较,可以看出此工况下液压缸未发生泄漏。
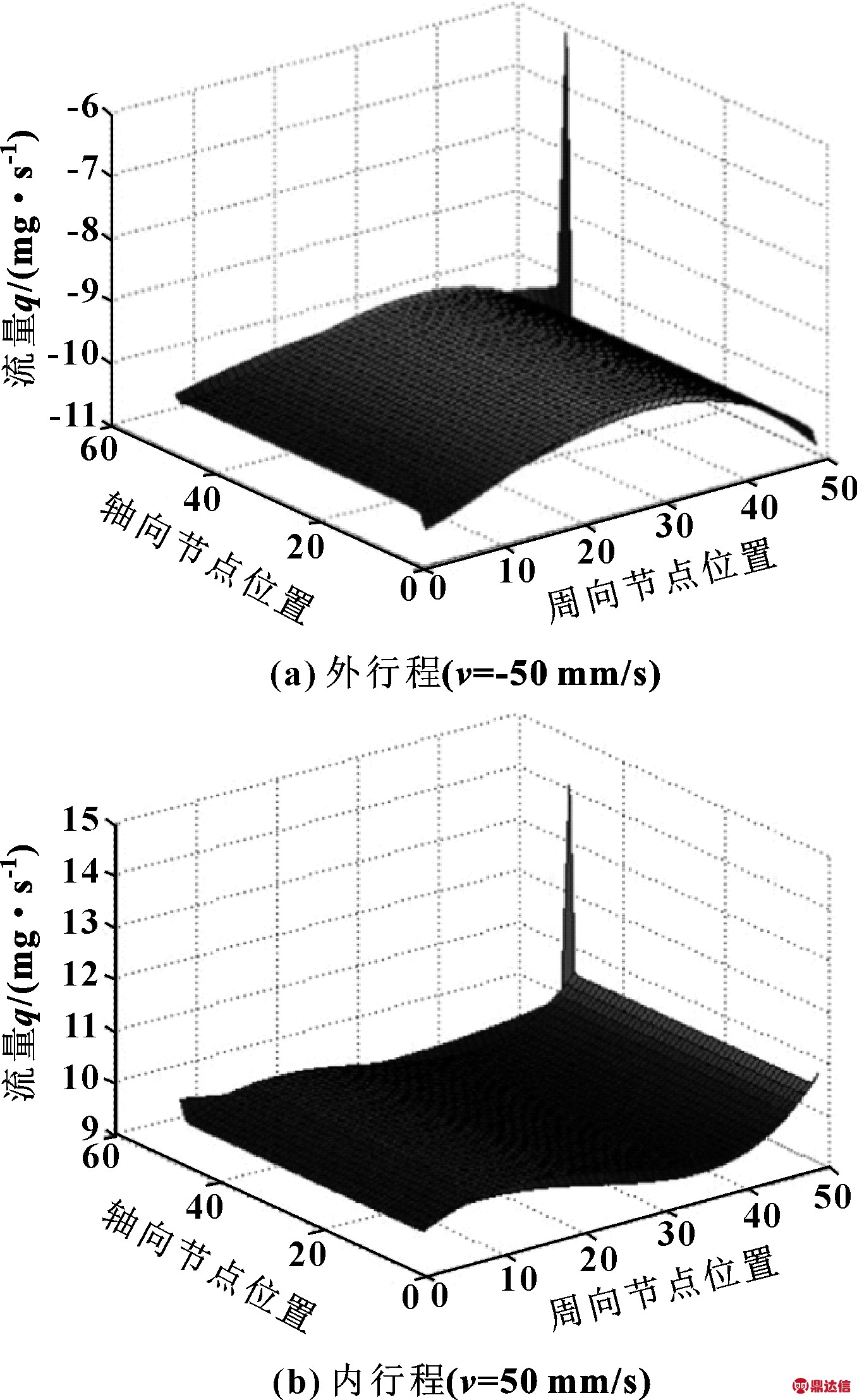
图6 矩形密封圈内外行程流量分布
Fig 6 Flow distribution of rectangular seals of outstroke and instroke (a) outstroke(v=-50 mm/s);(b) instroke(v=50 mm/s)
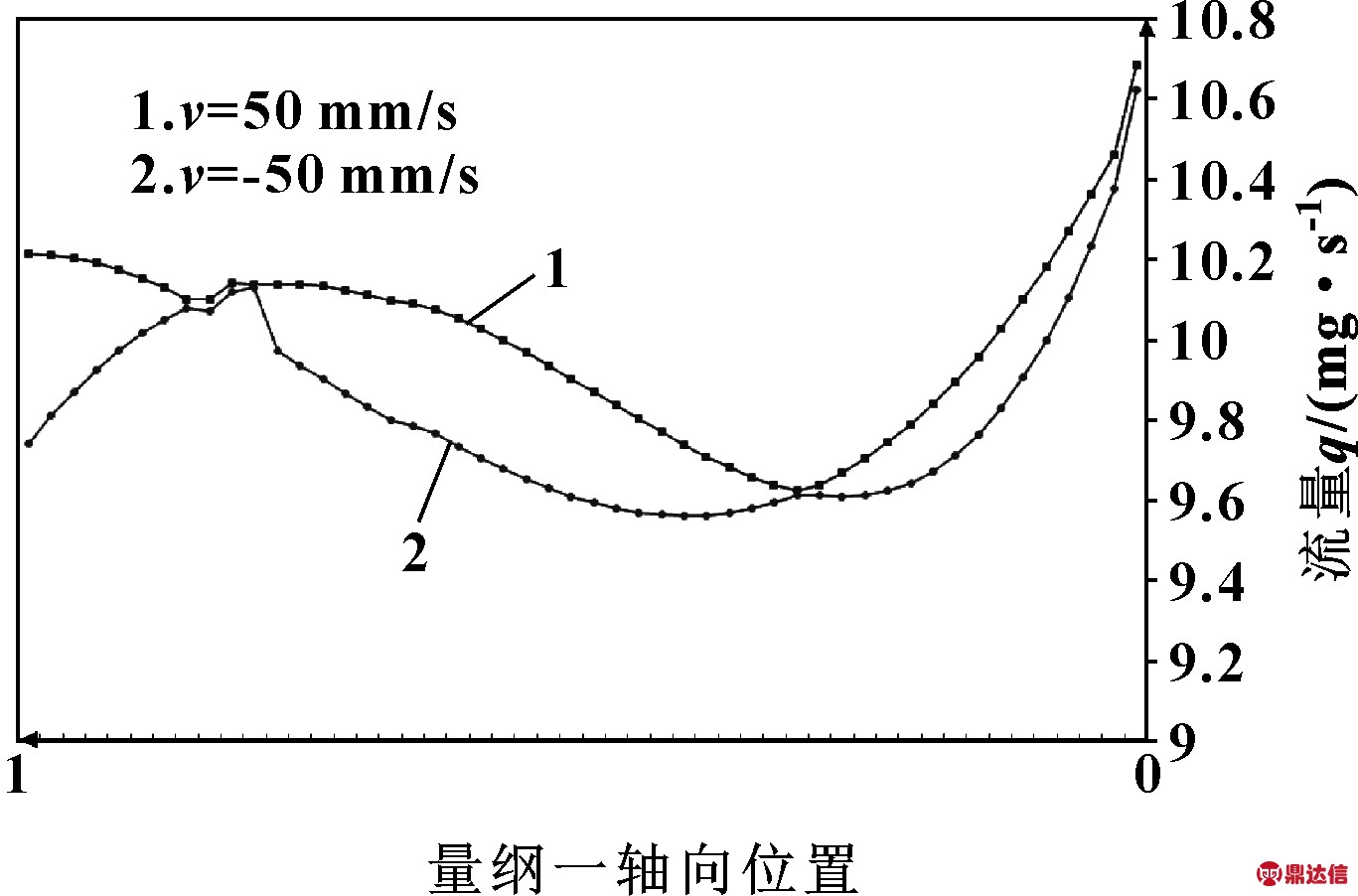
图7 内外行程流量
Fig 7 The leakage of the rectangular seal under the instroke and outstroke
2.2 密封压力的影响
当Sseal=1.73 μm,v=50 mm/s时改变密封介质的压力值,通过数值计算矩形密封圈的泄漏量和摩擦力,得到图8所示的曲线。如图8(a)所示,当活塞杆的运行速度与密封件粗糙度一定时,密封圈与活塞杆间的摩擦力随着密封压力的增加而增大。当密封压力达到一定数值后,摩擦力随着密封压力的增加而增大的速率变大,这是由于当密封处于允许压力范围内时,密封圈与活塞杆间可保持稳定的油膜厚度及摩擦力,确保密封圈有较长的使用寿命;若密封压力持续增大,密封圈则会发生挤出现象,被挤出到密封间隙中的边缘部分被撕裂甚至剪断,随着活塞杆的往复运动在密封间隙中流动,从而导致摩擦力的突然增加。
图8(b)表明,当密封压力低于5 MPa时,密封圈泄漏量为0,随着密封压力的进一步增加,密封圈出现挤出现象,使得泄漏量也线性增大。由此可以看出密封介质的压力对矩形密封圈的密封性能起着决定性的作用,通过该曲线可以确定某粗糙度和速度下不发生泄漏的最大工作压力。
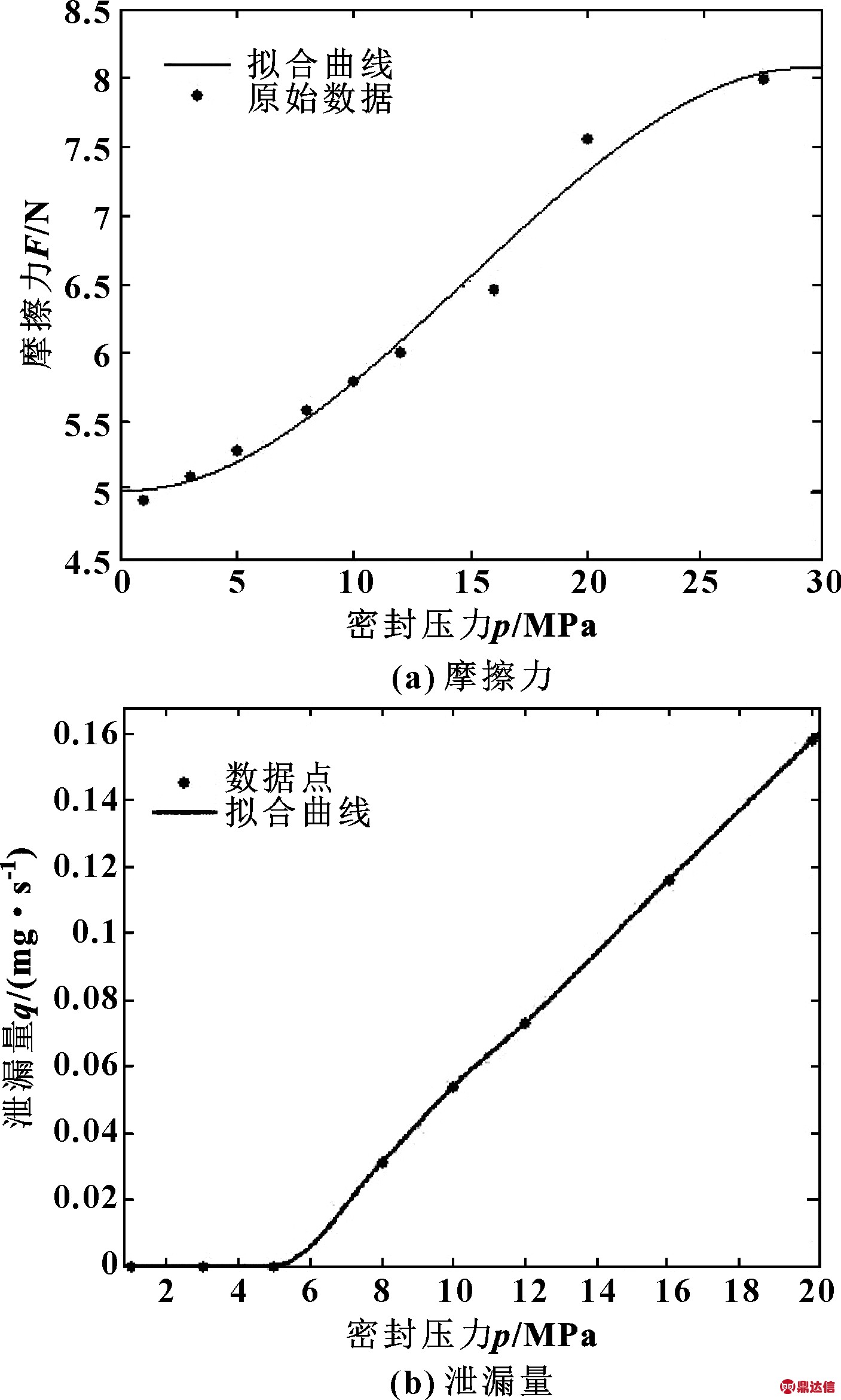
图8 密封压力对密封性能的影响(v=50 mm/s,Sseal=1.73 μm)
Fig 8 Effect of sealing pressure on sealing performances (v=50 mm/s,Sseal=1.73 μm) (a) friction;(b)leakage
2.3 往复速度的影响
当p=5 MPa,Sseal=1.73 μm时,图9给出了不同活塞杆往复运动速度下密封圈摩擦力和泄漏量的变化规律。文中将内外程往复速度设置为相同值。从图9(a)中可以看出,随着往复速度的增加,密封圈与活塞杆间的摩擦力线性增大;从图9(b)中可以看出,当活塞杆的运动速度小于某一值(v=53.73 mm/s)时,密封未发生泄漏;当活塞杆往复运动速度超过这一临界值后,随着往复运动速度的增加,泄漏量急剧增大。这是由于当运动速度增加后,润滑油膜厚度随之增大,往复循环的加快更促使泄漏量的急剧增加。通过该曲线可以确定一定密封压力下不发生泄漏的临界运动速度值。
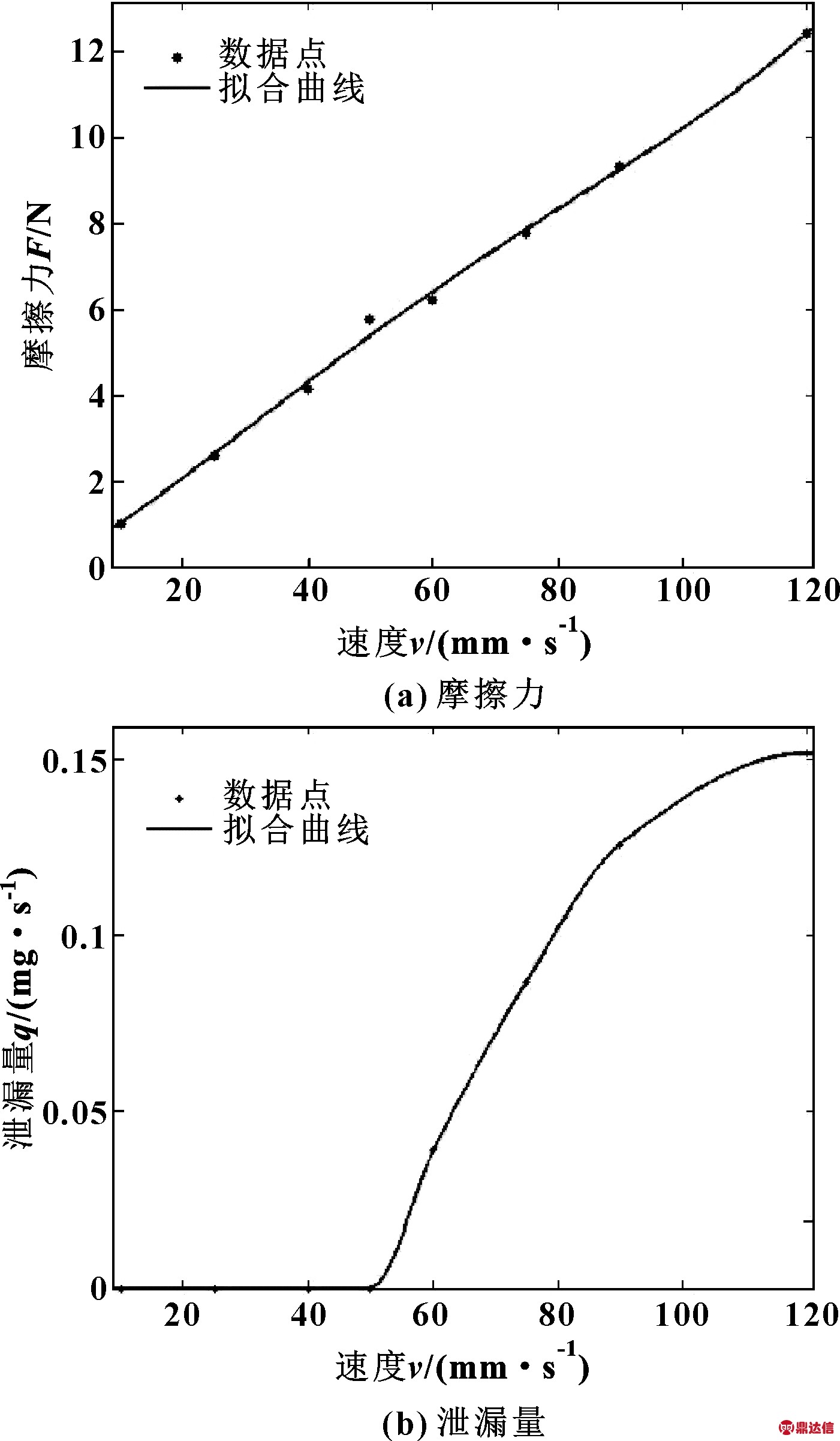
图9 往复速度对密封性能的影响(p=5 MPa,Sseal=1.73 μm)
Fig 9 Influence of piston rod moving speed on sealing performances(p=5 MPa,Sseal=1.73 μm) (a)friction;(b)leakage
2.4 密封圈粗糙度的影响
图10所示为当p=5 MPa,v=50 mm/s时,不同粗糙度下的摩擦力和泄漏量曲线。由图10(a)可以看出,密封圈与活塞杆间的摩擦力随着密封件粗糙度的增加而变大,当密封件粗糙度增大到某一值时,摩擦力迅速增大,矩形密封圈的润滑状态恶化,这会对密封圈产生较严重的磨损。由图10(b)可以看出,当密封件的粗糙度小于某一值时(Sseal=1.8 μm),密封表现出良好的防泄漏能力;当密封件的粗糙度大于这一临界值时,随着粗糙度的增大,摩擦和润滑条件恶化导致密封件损坏,使得泄漏量呈现指数增大。通过该曲线可以确定一定密封压力和活塞杆运动速度下不发生泄漏的临界粗糙度值。
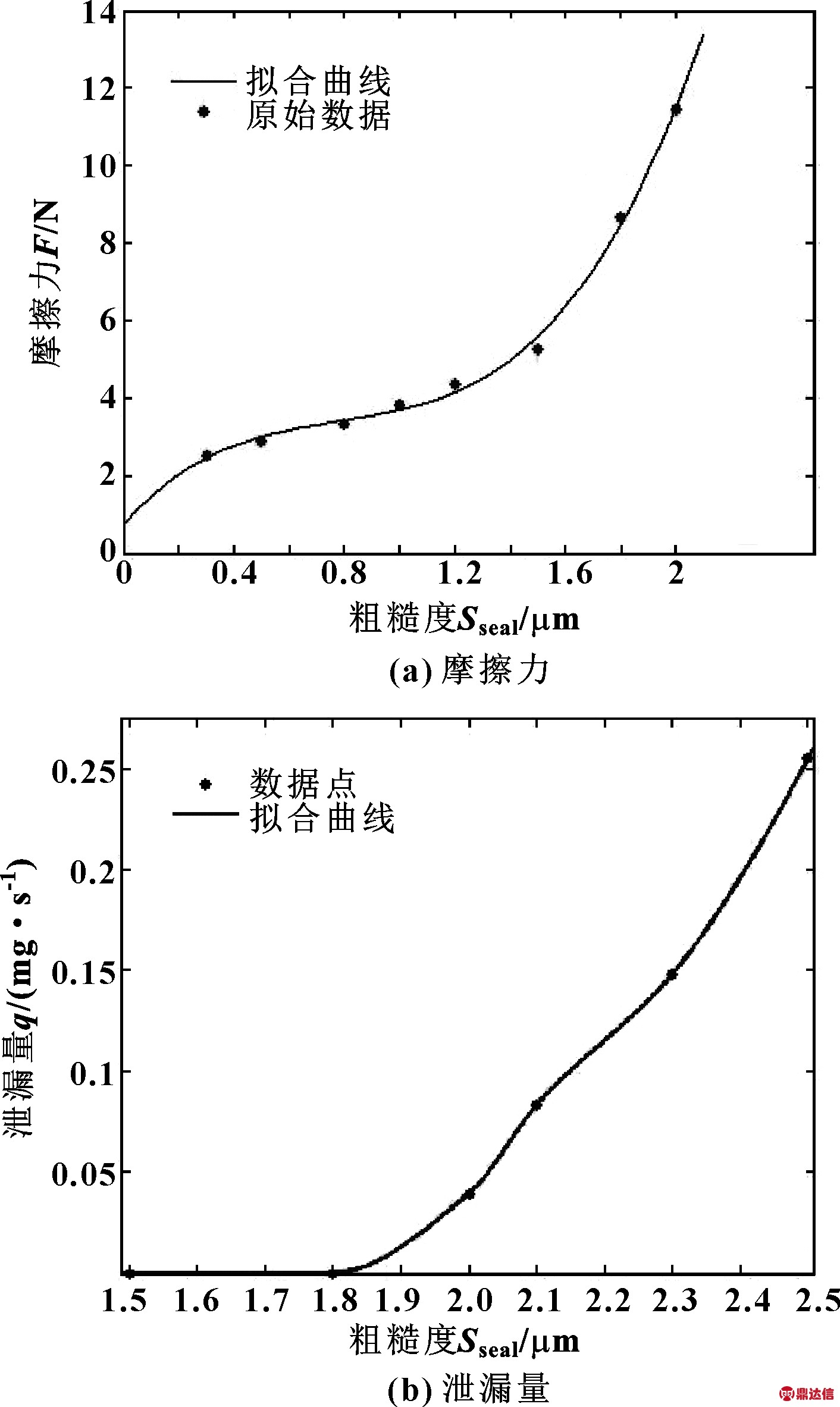
图10 密封件粗糙度对密封性能的影响(p=5 MPa,v=50 mm/s)
Fig 10 Influence of seal roughness on sealing performances(p=5 MPa,v=50 mm/s)(a) friction;(b) leakage
3 弹性矩形密封圈的最佳运动参数匹配关系
田口方法是一种通过正交试验,采用少量试验数据和较小的计算量得到最优参数组合的计算方法[12-13]。通过上节的分析发现,密封件的粗糙度、活塞杆的往复速度和密封介质压力对密封性能具有重要的影响。为了探索弹性矩形密封圈不发生泄漏的最佳运动参数匹配关系,设计4因子3水平正交试验,试验因素水平表如表2所示,相应数值模型试验仿真结果如表3所示。
表2 因素水平设计
Table 2 Factors level design
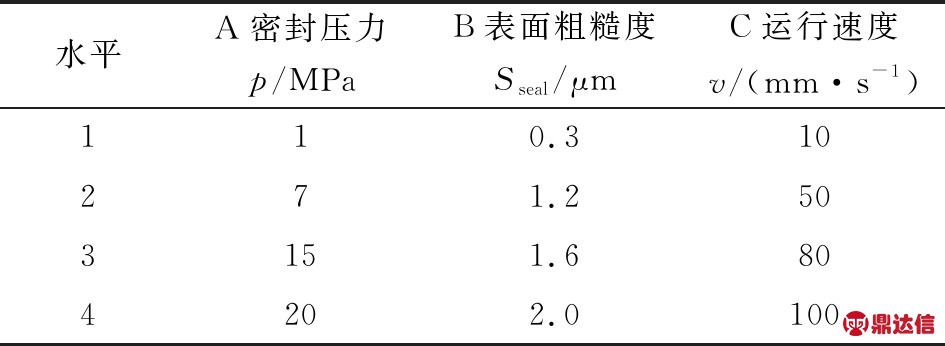
表3 正交试验方案及结果
Table 3 The orthogonal experiment scheme and the results
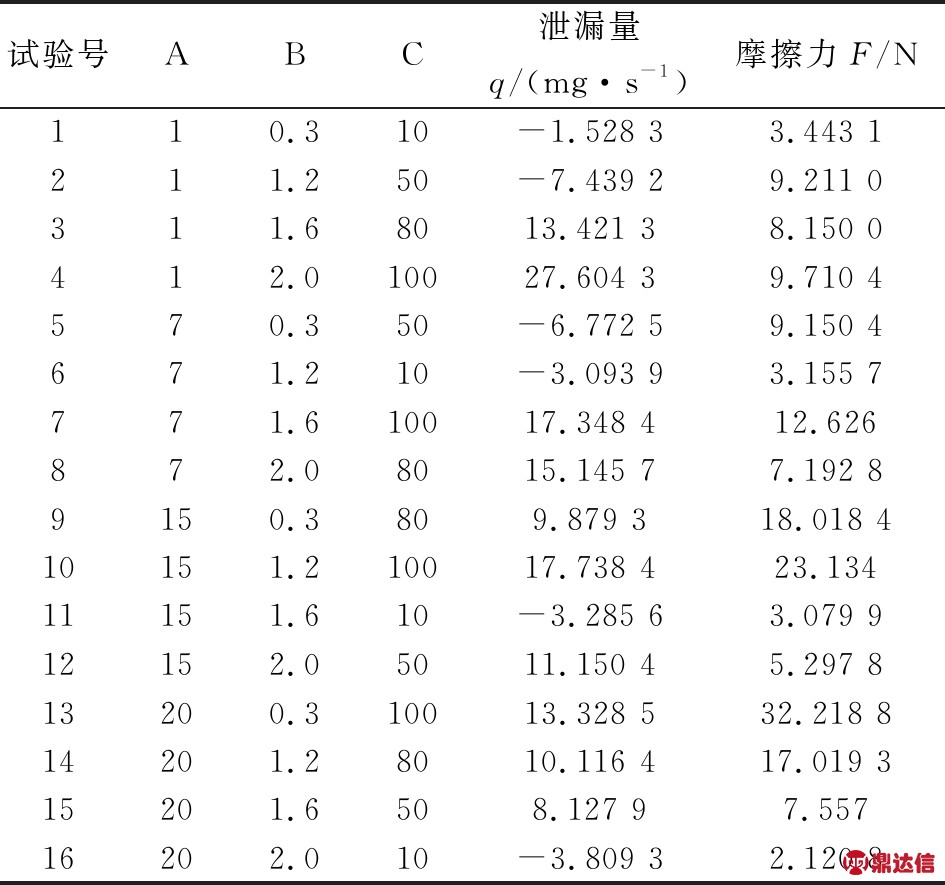
田口算法中,将静态特性分为望大特性、望目特性、望小特性3种,望小特性是希望测试结果越小越好。根据密封性能与泄漏量、摩擦力间的关系,文中利用Minitab软件,采用望小特性进行相关计算[14-15],在运算过程中,信噪比SN越大,表明该参数水平下的产品功能越稳定,密封性能越好。为了进一步求得密封性能最佳的参数组合,计算各参数组合所得信噪比如表4所示。由表4可以看出,矩形往复密封具有最佳密封性能的参数组合为p=1 MPa,Sseal=0.3 μm,v=10 mm/s,此时的信噪比为最大值-3.684 2。
表4 信噪比
Table 4 Signal to noise ratio
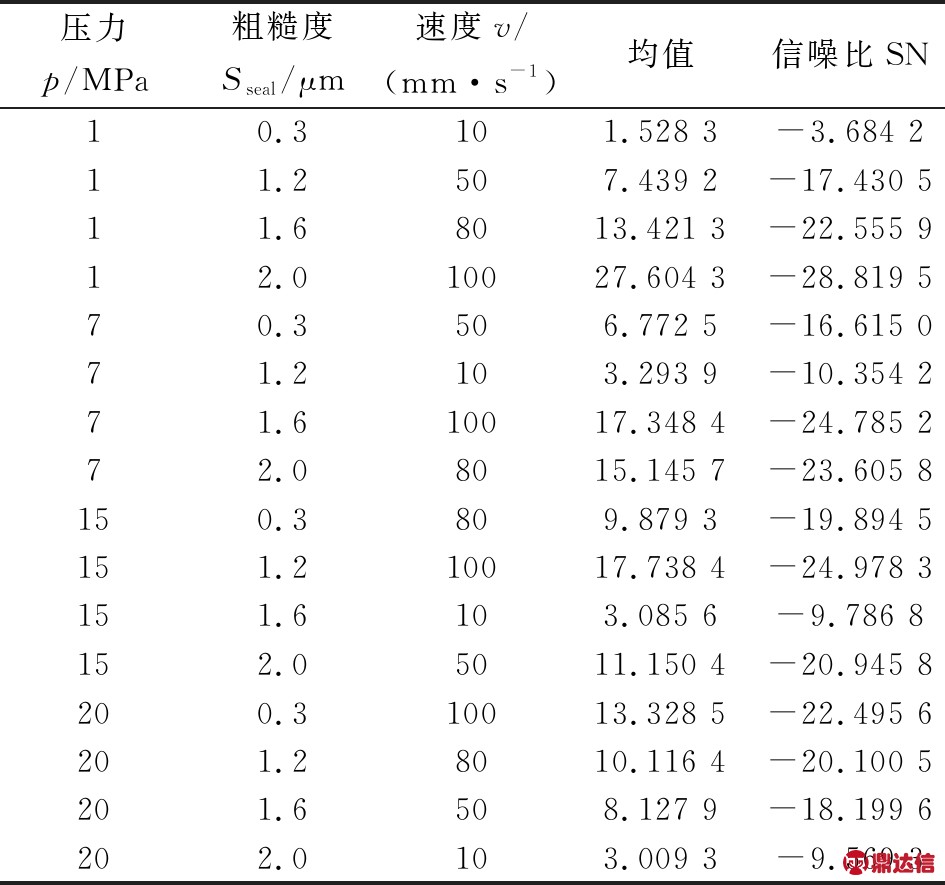
Delta为SN比的极差值。极差值反映控制因子的重要程度,极差值越大表明该因子对指标的影响越大越重要,秩的排序则越靠前。信噪比响应表如表5所示。在此例中,秩的排序表明,对于密封性能的影响程度由大到小依次为往复速度、粗糙度、密封压力,即往复速度的影响最为显著。由表3的正交试验结果也可看出,当往复速度为10 m/s时,密封压力和表面粗糙度无论取多大值,所对应的泄漏量绝对值和摩擦力的数值都相对较小。再次证明活塞杆往复速度是影响密封性能的最主要因素。因此,在实际应用中应在较低的运行速度下综合质量成本等因素对密封压力及表面粗糙度进行选择。
表5 信噪比响应表(望小)
Table 5 Signal-to-noise ratio response table (looking for the small)
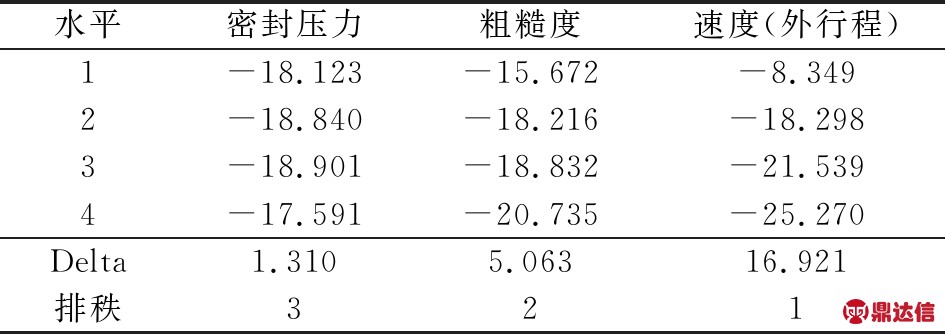
4 结论
(1)在轴用矩形往复密封中,过大的密封压力会对密封件造成损坏,使得摩擦力和净泄漏量极速增大,从而导致密封失效。不发生泄漏的临界速度则随着密封压力的增加呈现出先增大后减小的情况。
(2)在轴用矩形往复密封中,随着往复速度的增大,摩擦力呈线性增长趋势。当运动速度大于53.73 mm/s后,随着速度的增大,泄漏量也随之增大,且增大的速率逐渐减小。
(3)在轴用矩形往复密封中,随着表面粗糙度的增大,直线往复密封的净泄漏量表现为越来越大的增量。不发生泄漏的临界速度则随着密封压力的增加而降低。
(4)数值分析表明,密封压力、密封件粗糙度和往复运动速度是影响矩形密封性能的重要因素。利用田口算法分析证明,密封参数的最优组合为p=1 MPa,Sseal=0.3 μm,v=10 mm/s。各试验因素对于密封性能影响显著程度顺序依次为往复速度、粗糙度、密封压力。